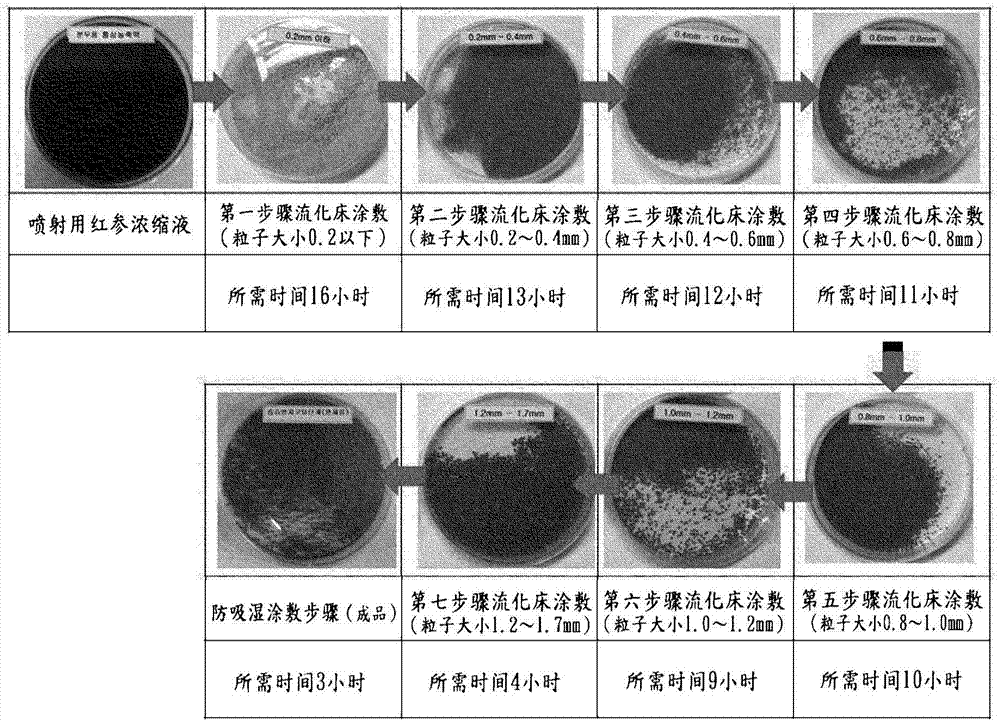
本發(fā)明涉及紅參濃縮液顆粒及其制備方法,更詳細(xì)地,涉及利用干燥后的紅參濃縮液粉末使以往的經(jīng)過7~8個步驟的流化床涂敷工序縮減為3~4個步驟,來縮短紅參濃縮液顆粒的制備時間,并大幅度增加每個時間的生產(chǎn)量,從而提高價格競爭力的紅參濃縮液顆粒、利用紅參濃縮液粉末和流化床涂敷機(jī)的紅參濃縮液顆粒的制備方法。
背景技術(shù):
:當(dāng)前所銷售的紅參產(chǎn)品有原形紅參、紅參粉末、紅參切片、紅參濃縮液等,在這些產(chǎn)品中,最受消費(fèi)者歡迎的產(chǎn)品為紅參濃縮液。但是,紅參濃縮液具有飲用時的不便、使用容器的管理上的困擾及液相產(chǎn)品的流通問題,因此,為了解決這些問題,正在銷售通過“不添加稀釋劑而利用人參濃縮液來制備流動性及儲存性優(yōu)秀的人參濃縮液丸的方法”(韓國授權(quán)專利公報第10-0813387號,專利文獻(xiàn)1)、“利用超微紅參粉末的紅參濃縮液顆粒的制備方法”(韓國授權(quán)專利公報第10-1357169號,專利文獻(xiàn)2)使紅參功能成分得到高濃縮,從而因每日攝取量非常小,以顆粒形態(tài)便于攜帶,且很好地溶解于水而可以容易地攝取的被稱為100%紅參濃縮液顆粒(紅參丹)產(chǎn)品的新的紅參產(chǎn)品類型,由此,通過促進(jìn)紅參在韓國國內(nèi)的消費(fèi)來增大農(nóng)業(yè)收入,并增大出口,從而大大貢獻(xiàn)于高麗紅參的地位的提高。在上述專利文獻(xiàn)1、專利文獻(xiàn)2的情況下,在排除異物或其他添加物的添加的情況下,既維持100%紅參成分,又便于攝取及攜帶管理。而且,為了提高消費(fèi)者偏好度而以這種方式制備的顆粒呈圓形的球形狀。為了滿足這種條件而使用流化床涂敷機(jī)來進(jìn)行制備工序。若觀察專利文獻(xiàn)1所公開的人參濃縮液丸的大小,則所制備的人參濃縮液丸的大小為700~5000μm。并且,專利文獻(xiàn)2所公開的紅參濃縮液顆粒的大小也為700~5000μm,可知非常小。實(shí)質(zhì)上,優(yōu)選地,這種大小與水之類的液相相混合來進(jìn)行攝取。這是因?yàn)椋蛄W哟笮∵^小而在以粉末狀直接攝取的情況下,即使是很小的風(fēng),也可導(dǎo)致一不小心通過鼻子或嘴來進(jìn)入到呼吸器官,并引發(fā)咳嗽等。因此,如專利文獻(xiàn)1、專利文獻(xiàn)2,有必要制備成因呈固相而具有即使在用勺子舀著吃,也不會飄散的重量,且具有容易用手拿著吃的大小,而且,以用于此的粒子大小滿足消費(fèi)者嗜好的方式具有規(guī)定大小。但是,在利用流化床涂敷機(jī)使液相實(shí)現(xiàn)粒子化,并對粒子重新進(jìn)行涂敷來實(shí)現(xiàn)規(guī)?;矫嫘枰芏鄷r間或設(shè)施費(fèi)用。觀察作為與流化床裝置相關(guān)的技術(shù)的“流化床的組裝涂敷裝置及流化床的組裝涂敷方法”(韓國公開專利公報第10-2003-0007568號,專利文獻(xiàn)3)所公開的內(nèi)容,公開有便于進(jìn)行批量生產(chǎn)的連續(xù)式流化床的組裝機(jī)因分級效果不完整而使排泄產(chǎn)品的粒度分布變得不均衡的問題,而在間歇式流化床的組裝機(jī)的情況下,公開有很難進(jìn)行批量生產(chǎn)的問題。當(dāng)通常所使用的流化床的組裝機(jī)并非為連續(xù)式時,在專利文獻(xiàn)1、專利文獻(xiàn)2中,為了使流化床涂敷機(jī)所制備的濃縮液顆粒具有規(guī)定大小且以mm單位以上實(shí)現(xiàn)規(guī)?;枰喈?dāng)多的時間。作為一例,作為100kg生產(chǎn)標(biāo)準(zhǔn)的底噴方式的流化床涂敷機(jī)的每臺的銷售價格通常為10億韓元左右,而這種流化床涂敷機(jī)在使初期的紅參濃縮液粒子化為0.2mm以下粒徑的微細(xì)粉末時需要16小時左右,在使小于0.2mm的粒徑規(guī)模化為0.2~0.4mm大小時需要13小時,而將此重新規(guī)模化為0.4~0.6mm時需要12小時,在規(guī)?;癁?.6~0.8mm時需要11小時,在規(guī)?;癁?.8~1.0mm時需要10小時,在規(guī)?;癁?.0~1.20mm時需要9小時,在規(guī)?;癁?.2以上時需要4小時。而且,在收集每個工序的中間制備的顆粒后,需要重新經(jīng)過篩選步驟并經(jīng)過噴射及流動化涂敷步驟,因此,工序之間的時間也需要消耗很多。在此,在實(shí)施如專利文獻(xiàn)2的吸濕涂敷的情況下,若考慮還需要3小時左右,則在利用10億韓元左右的流化床涂敷機(jī)來生產(chǎn)100kg需要78小時左右,因此,存在生產(chǎn)率顯著下降的問題。像這樣,以紅參濃縮液之類的液相為起始點(diǎn),需要研發(fā)不僅具有容易用勺子或手來攝取最終生產(chǎn)品的程度的充分大小,而且形成外觀上的品質(zhì)優(yōu)秀的圓球形態(tài),尤其,可排除生產(chǎn)成本的過度增加的工序。像這樣,以往的制備100%紅參濃縮液顆粒的工序利用流化床涂敷機(jī)從紅參濃縮液中經(jīng)過7~8個步驟的流化床涂敷制備工序來制備平均1.5mm大小的球形形態(tài)的紅參濃縮液顆粒,而這種方式不僅需要過多的顆粒制備時間,而且因作為相當(dāng)高價的裝備的流化床涂敷機(jī)的最佳生產(chǎn)量少而成為紅參丹產(chǎn)品的價格上升因素,并且,即使為了提高價格競爭力,也需要研發(fā)可以大大減少流化床涂敷制備工序步驟的技術(shù)?,F(xiàn)有技術(shù)文獻(xiàn)(專利文獻(xiàn)1)kr10-0813387(2008年03月06日)(專利文獻(xiàn)2)kr10-1357169(2014年01月23日)(專利文獻(xiàn)3)kr10-2003-0007568(2003年01月23日)技術(shù)實(shí)現(xiàn)要素:技術(shù)問題本發(fā)明的紅參濃縮液顆粒、利用紅參濃縮液粉末和流化床涂敷機(jī)的紅參濃縮液顆粒的制備方法用于解決在如上所述的現(xiàn)有技術(shù)中發(fā)生的問題,本發(fā)明的目的在于,提供紅參濃縮液顆粒的制備方法,上述紅參濃縮液顆粒的制備方法在對紅參濃縮液進(jìn)行干燥及粉碎來粉末化為大小小于最終生成產(chǎn)品對象的無定形后,利用流化床涂敷機(jī)并經(jīng)過流動化及噴射步驟來向上述無定形的粉末涂敷噴射型紅參濃縮液,從而縮短紅參濃縮液顆粒的流化床涂敷制備工序步驟,節(jié)約紅參濃縮液顆粒的流化床涂敷時間,并增加流化床涂敷機(jī)的最佳生產(chǎn)量,從而使價格競爭力變得優(yōu)秀。并且,經(jīng)過粉碎及篩選的無定形紅參濃縮液粉末的大小使之后利用流化床涂敷機(jī)的涂敷工序形成反復(fù)進(jìn)行2~3次,從而可以同時滿足縮短工序和維持適合消費(fèi)者嗜好的球形狀兩種目標(biāo)。尤其,干燥和粉碎以使費(fèi)用增加最小化,且藥理成分的改性可能性小的真空干燥及輥式粉磨方式構(gòu)成,而且,在輥式粉磨方式中,通過使輥之間的間隔逐漸縮小的多次粉碎方式進(jìn)行粉碎,并在兩個輥之間的表面形成半球形的槽,從而使因粒度差異而分離的篩選率最小化,使得粉碎后的無定形紅參濃縮液粉末最大限度呈接近球形狀的形狀,從而在之后的涂敷工序中可以順暢地制備球形狀的紅參濃縮液顆粒。解決問題的手段本發(fā)明的利用紅參濃縮液粉末和流化床涂敷機(jī)的紅參濃縮液顆粒的制備方法為了解決如上所述的問題而包括:濃縮液干燥步驟,對紅參濃縮液進(jìn)行干燥來制備干燥濃縮膏;粉碎步驟,對在上述濃縮液干燥步驟中制備的干燥濃縮膏進(jìn)行粉碎來制備無定形紅參濃縮液粉末;篩選步驟,在上述無定形紅參濃縮液粉末中僅篩選粒子大小為0.2~0.8mm的粉末;球形化涂敷步驟,在流化床涂敷機(jī)的內(nèi)部,在流化床涂敷條件下,以底噴方式向被篩選的無定形紅參濃縮液粉末噴射噴射用紅參濃縮液,并實(shí)施流動化,以多個步驟反復(fù)實(shí)施噴射和流動化,使得粒子大小按不同的步驟變大,并經(jīng)過最后的噴射及流動化步驟來使粒子大小大于上述無定形紅參濃縮液粉末,來制備球形狀的紅參濃縮液顆粒;以及防吸濕流化床涂敷步驟,在流化床涂敷條件下,在流化床涂敷機(jī)內(nèi)以底噴方式向球形化的上述紅參濃縮液顆粒噴涂噴射用超微紅參粉溶液,從而制備防止吸濕的紅參濃縮液顆粒。在上述結(jié)構(gòu)中,本發(fā)明的特征在于,在上述紅參濃縮液干燥步驟中,利用選自真空干燥、熱風(fēng)干燥、冷凍干燥及常溫通風(fēng)干燥中的一種對紅參濃縮液進(jìn)行干燥,來制備干燥濃縮膏。并且,本發(fā)明的特征在于,在上述粉碎步驟中,利用輥式粉磨機(jī)對上述干燥濃縮膏進(jìn)行粉碎,來制備無定形紅參濃縮液粉末。并且,本發(fā)明的特征在于,在上述流化床涂敷條件中,吸入空氣量為5~15m3/秒、投入管溫度為80~150℃、噴射壓力為1.0~5.0巴(bar)、噴射速度為1~10kg/小時。而且,本發(fā)明的特征在于,在上述噴射用紅參濃縮液中,固體成分含量為噴射用紅參濃縮液的總重量的10~50重量百分比。而且,本發(fā)明的特征在于,利用超微粉碎機(jī)來配制粒子大小為5~100μm的紅參粉末后,溶解于水,從而制備上述噴射用超微紅參粉溶液。并且,本發(fā)明的特征在于,上述噴射用超微紅參粉溶液的涂敷含量為紅參濃縮液顆粒的總重量的1~10重量百分比?;蛘?,本發(fā)明包括:濃縮液干燥步驟,以向托盤倒入紅參濃縮液的狀態(tài)向真空干燥機(jī)投入后,進(jìn)行真空干燥來制備干燥濃縮膏;粉碎步驟,在輥式粉磨機(jī)中粉碎在上述濃縮液干燥步驟中制備的干燥濃縮膏,來制備無定形紅參濃縮液粉末;篩選步驟,使上述無定形紅參濃縮液粉末通過篩選機(jī),來僅篩選粒子大小為0.6~0.8mm的粉末;球形化涂敷步驟,包括第一球形化涂敷步驟、第二球形化涂敷步驟及第三球形化涂敷步驟,在上述第一球形化涂敷步驟中,在吸入空氣量為5~15m3/秒、投入管溫度為80~150℃、噴射壓力為1.0~5.0巴、噴射速度為1~10kg/小時的流化床涂敷條件下,在流化床涂敷機(jī)內(nèi)部,以底噴方式向被篩選的無定形紅參濃縮液粉末噴射固體成分含量為10~50重量百分比的噴射用紅參濃縮液,并實(shí)施流動化,來制備粒子大小為0.8~1.0mm的第一顆粒,在上述第二球形化涂敷步驟中,在與第一球形化涂敷步驟相同的流化床涂敷條件下,在流化床涂敷機(jī)內(nèi)以底噴方式向上述第一顆粒噴射固體成分含量為10~50重量百分比的噴射用紅參濃縮液,并實(shí)施反復(fù)的流動化,來制備粒子大小為1.0~1.2mm的第二顆粒,在第三球形化涂敷步驟中,在與第一球形化涂敷步驟相同的流化床涂敷條件下,在流化床涂敷機(jī)內(nèi)以底噴方式向上述第二顆粒噴射固體成分含量為10~50重量百分比的噴射用紅參濃縮液,并實(shí)施反復(fù)的流動化,來制備粒子大小為1.2~1.7mm的球形狀的紅參濃縮液顆粒;以及防吸濕流化床涂敷步驟,在流化床涂敷條件下,在流化床涂敷機(jī)內(nèi)以底噴方式向球形化的上述紅參濃縮液顆粒噴涂粒子大小為5~100μm,且紅參濃縮液顆粒的總重量的1~10重量百分比的超微紅參粉末的噴射用超微紅參粉溶液,從而制備防止吸濕的紅參濃縮液顆粒。在上述結(jié)構(gòu)中,本發(fā)明的特征在于,在上述粉碎步驟中,朝向兩個輥相向的方向,向以能夠向前、后移動的方式形成的輥式粉磨機(jī)的兩個輥之間投入上述干燥濃縮膏來進(jìn)行粉碎,一邊逐漸縮小兩個輥之間的間隔,一邊多次反復(fù)進(jìn)行粉碎,并在兩個輥的表面形成有分別以格子形進(jìn)行陽刻的圖案,在圖案的內(nèi)部形成有半球形的槽,從而在兩個輥相接近來進(jìn)行粉碎時,向半球形的槽之間引導(dǎo)干燥濃縮膏來進(jìn)行粉碎。而且,本發(fā)明的紅參濃縮液顆粒的特征在于,如圖5所示,包括:芯部30,包含無定形的紅參濃縮液粉末,上述芯部30的粒子大小為0.6~0.8mm;紅參濃縮液涂敷部40,在上述芯部30與芯部形成一體,并使噴射用紅參濃縮液以多層方式進(jìn)行流動化涂敷而成;以及防吸濕涂敷部50,由噴射用超微紅參粉溶液在上述紅參濃縮液涂敷部的外圍進(jìn)行流動化涂敷而成,上述紅參濃縮液顆粒的粒子大小為1.2~1.7mm。發(fā)明的效果本發(fā)明的紅參濃縮液顆粒的制備方法與以往的制備方法相比,減少流化床涂敷制備工序步驟,從而縮短工序時間,并增加流化床涂敷機(jī)的生產(chǎn)能力,因而大大提高紅參濃縮液顆粒產(chǎn)品的價格競爭力,由此,通過促進(jìn)紅參在韓國國內(nèi)的消費(fèi)來增大農(nóng)業(yè)收入,并增大出口,從而大大貢獻(xiàn)于高麗紅參的地位的提高。附圖說明圖1為表示在本發(fā)明中的真空干燥機(jī)中得到干燥的干燥濃縮膏的照片。圖2為表示在本發(fā)明的詳細(xì)說明中作為現(xiàn)有技術(shù)的比較例3的制備步驟中收獲的樣品的照片。圖3為表示本發(fā)明的實(shí)施例3的制備步驟中收獲的樣品的照片。圖4為表示在本發(fā)明的粉碎步驟中所使用的輥式粉磨機(jī)的結(jié)構(gòu)的照片。圖5為以概念性的方式表示本發(fā)明的實(shí)施例3的紅參濃縮液顆粒的結(jié)構(gòu)的剖視圖。圖6為放大表示通過本發(fā)明來制備的紅參濃縮液顆粒的照片。標(biāo)號說明10:圖案20:槽30:芯部40:紅參濃縮液涂敷部50:防吸濕涂敷部具體實(shí)施方式以下,參照附圖對本發(fā)明的紅參濃縮液顆粒、利用紅參濃縮液粉末和流化床涂敷機(jī)的紅參濃縮液顆粒的制備方法進(jìn)行詳細(xì)說明。本發(fā)明的利用紅參濃縮液粉末和流化床涂敷機(jī)的紅參濃縮液顆粒的制備方法大致包括濃縮液干燥步驟、粉碎步驟、篩選步驟、球形化涂敷步驟、防吸濕流化床涂敷步驟。1.濃縮液干燥步驟對紅參濃縮液進(jìn)行干燥來制備干燥濃縮膏。干燥方式可以選擇性地使用真空干燥、熱風(fēng)干燥、冷凍干燥及常溫通風(fēng)干燥中的一種。其中,優(yōu)選為真空干燥方式。真空干燥方式可以使用干燥裝置,上述干燥裝置包括:托盤,用于收容紅參濃縮液;以及真空干燥機(jī),上述托盤以多層方式收容于上述真空干燥機(jī)的內(nèi)部。與熱風(fēng)干燥方式相比,真空干燥方式具有有效成分的損失少的優(yōu)點(diǎn),而與常溫通風(fēng)干燥方式相比,真空干燥方式具有干燥時間短的優(yōu)點(diǎn)。并且,與冷凍干燥方式相比,具有干燥費(fèi)用少的優(yōu)點(diǎn)。2.粉碎步驟對在上述濃縮液干燥步驟中制備的干燥濃縮膏進(jìn)行粉碎來制備無定形紅參濃縮液粉末。此時,粉碎裝置可以使用公知的多種粉碎裝置,但優(yōu)選地,利用由兩個輥相互并列配置的輥式粉磨機(jī)來進(jìn)行粉碎。更具體地,朝向兩個輥相向的方向,向以能夠向前、后移動的方式形成的輥式粉磨機(jī)的兩個輥之間投入上述干燥濃縮膏來進(jìn)行粉碎。此時,起初設(shè)定成使被固化為托盤形狀的干燥濃縮膏粉碎為大塊的間隔,來使干燥濃縮膏粉碎為小塊,接著,逐漸縮小輥之間的間隔,并逐漸粉碎為小塊,最終以使兩個輥之間的間隔達(dá)到0.2~0.8mm左右的程度來進(jìn)行粉碎。像這樣,進(jìn)行多次粉碎是為了防止被粉碎為過小的小塊,使得今后的篩選步驟中的紅參濃縮液粉末的回收率最大化。尤其,如圖4所示,在兩個輥的表面分別形成有被陽刻為格子形的圖案10,而在格子形圖案10的內(nèi)部形成有半球形的槽20,因此,優(yōu)選地,當(dāng)兩個輥相接近來進(jìn)行粉碎時,干燥濃縮膏向半球形的槽之間引導(dǎo),并進(jìn)行粉碎。3.篩選步驟在上述無定形紅參濃縮液粉末中篩選粒子大小為0.2~0.8mm的粉末。篩選可以通過公知的網(wǎng)狀的篩子之類的篩選機(jī)來進(jìn)行篩選,或者可以在輥式粉磨機(jī)的出口側(cè)設(shè)置振動的網(wǎng)體來方便地進(jìn)行篩選。在粒子大小小于0.2mm的情況下,當(dāng)與通過現(xiàn)有的制備方法制備的紅參濃縮液顆粒相比較時,在制備成本方面無法呈現(xiàn)出較大的差異,因而降低實(shí)效性,相反,在粒子大小大于0.8mm的情況下,很難制備球形的紅參濃縮液顆粒,從而降低外觀上的產(chǎn)品品質(zhì)。因此,為了制備既具有價格競爭力,又具有優(yōu)秀的紋理功能及防吸濕功能的紅參濃縮液顆粒,優(yōu)選地,在0.2~0.8mm的范圍選擇所篩選的大小。此時,最優(yōu)選地,更優(yōu)選的篩選粒子大小為0.6~0.8mm。4.球形化涂敷步驟向流化床涂敷機(jī)內(nèi)投入所篩選的無定形紅參濃縮液粉末后,在流化床涂敷條件下,以底噴方式對噴射用紅參濃縮液實(shí)施噴射及流動化,以多個步驟反復(fù)實(shí)施噴射和流動化,使得粒子大小按不同的步驟變大,并經(jīng)過最后的噴射及流動化步驟來制備粒子形態(tài)為球形形態(tài)的紅參濃縮液顆粒。球形化的紅參濃縮液顆粒的平均粒子大小優(yōu)選為1.5mm,但并不局限于此,以1.2~1.7mm左右的范圍為佳。此時,流化床涂敷條件優(yōu)選為吸入空氣量5~15m3/秒、投入管溫度(吸入空氣溫度)80~150℃、噴射壓力1.0~5.0巴、噴射速度1~10kg/小時,但并不局限于此。最優(yōu)選地,吸入空氣量10m3/秒、投入管溫度90℃、噴射壓力2.5巴、噴射速度5kg/小時。并且,上述噴射用紅參濃縮液的固體成分含量可以為噴射用紅參濃縮液的總重量的10~50重量百分比。優(yōu)選地,在上述篩選步驟中篩選的粒子大小為0.6~0.8mm的情況下,這種球形化涂敷步驟適合包括下述的第一球形化涂敷步驟、第二球形化涂敷步驟及第三球形化涂敷步驟。在第一球形化涂敷步驟中,在吸入空氣量5~15m3/秒、投入管溫度80~150℃、噴射壓力1.0~5.0巴、噴射速度1~10kg/小時的流化床涂敷條件下,在流化床涂敷機(jī)的內(nèi)部,以底噴方式向被篩選的0.6~0.8mm的無定形紅參濃縮液粉末噴射固體成分含量為10~50重量百分比的噴射用紅參濃縮液,并實(shí)施流動化來制備粒子大小為0.8~1.0mm的第一顆粒。而且,在第二球形化涂敷步驟中,在流化床涂敷機(jī)的內(nèi)部,在與第一球形化涂敷步驟相同的流化床涂敷條件下,以底噴方式向上述第一顆粒噴射固體成分含量為10~50重量百分比的噴射用紅參濃縮液,并實(shí)施反復(fù)的流動化來制備粒子大小為1.0~1.2mm的第二顆粒。而且,在第三球形化涂敷步驟中,在流化床涂敷機(jī)的內(nèi)部,在與第一球形化涂敷步驟相同的流化床涂敷條件下,以底噴方式向上述第二顆粒噴射固體成分含量為10~50重量百分比的噴射用紅參濃縮液,并實(shí)施反復(fù)的流動化來制備粒子大小為1.2~1.7mm的球形狀的紅參濃縮液顆粒。這種球形化涂敷步驟可以在篩選步驟中的粒子大小為0.2mm以上且小于0.6mm的情況下還可以包括球形化涂敷步驟來反復(fù)進(jìn)行。5.防吸濕流化床涂敷步驟在流化床涂敷條件下,以底噴方式向在流化床涂敷機(jī)內(nèi)以上述1.2~1.7mm大小實(shí)現(xiàn)球形化的紅參濃縮液顆粒噴涂噴射用超微紅參粉溶液,從而制備防止吸濕的紅參濃縮液顆粒。此時,優(yōu)選地,上述噴射用超微紅參粉溶液為利用超微粉碎機(jī)來配制粒子大小為5~100μm的紅參粉末后,溶解于水來制備而成的。更加優(yōu)選地,限制于10~30μm為佳。并且,上述噴射用超微紅參粉溶液的涂敷含量為紅參濃縮液顆粒的總重量的1~10重量百分比。在這種情況下,最佳重量以2~4重量百分比為佳。此時,流化床涂敷條件可以成為與上述的球形化涂敷步驟形態(tài)的條件。即,在吸入空氣量為5~15m3/秒、投入管溫度為80~150℃、噴射壓力為1.0~5.0巴、噴射速度為1~10kg/小時的流化床涂敷條件下進(jìn)行為佳。最佳條件為吸入空氣量為13m3/秒、投入管溫度為80℃、噴射壓力為2.0巴、噴射速度為6kg/小時。這種防吸濕流化床涂敷步驟如專利文獻(xiàn)2所公開,起到利用超微紅參粉溶液來提高防吸濕功能的作用。如圖5所示,通過如上所述的工序來制備的本發(fā)明的紅參濃縮液顆粒包括芯部30、紅參濃縮液涂敷部40及防吸濕涂敷部50。芯部30通過基于輥式粉磨機(jī)的粉碎及篩選來由無定形的紅參濃縮液粉末形成,且粒子大小為0.6~0.8mm。而且,紅參濃縮液涂敷部40在上述芯部30的外圍與芯部30形成一體,并根據(jù)流化床涂敷的反復(fù)次數(shù)來以多層方式流動化涂敷有噴射用紅參濃縮液。而且,防吸濕涂敷部50在上述紅參濃縮液涂敷部的外圍流動化涂敷有噴射用超微紅參粉溶液。以這種方式形成的紅參濃縮液顆粒的粒子大小為1.2~1.7mm,以便于用手抓取或用勺子舀著攝取。以下,通過實(shí)施例來對本發(fā)明進(jìn)行具體的說明,但下述的實(shí)施例及實(shí)驗(yàn)例僅為例示出本發(fā)明的一形態(tài),本發(fā)明的范圍并不局限于以下的實(shí)施例及實(shí)驗(yàn)例。實(shí)施例11.紅參濃縮液粉末的制備準(zhǔn)備多個長寬為50cm、高度為5cm的托盤后,在各托盤裝入紅參濃縮液,之后以多層方式在真空干燥機(jī)中投入多個托盤后,在40℃的溫度下過濾真空干燥機(jī)的內(nèi)部的真空,并對紅參濃縮液進(jìn)行干燥,從而制備干燥濃縮膏。接著,利用垂直將干燥濃縮膏粉碎為20cm3左右的塊后,向輥式粉磨機(jī)投入各塊。圖1為表示向輥式粉磨機(jī)投入之前的干燥濃縮膏的一部分的照片。如圖所示,可知干燥濃縮膏呈無定形的塊形狀。輥式粉磨機(jī)利用可以調(diào)節(jié)相互平行配置的兩個輥之間的間隔,并在輥的表面陽刻有格子形條紋的粉磨機(jī)。起初,使兩個輥之間的間隔成為2.5cm,接著,使兩個輥之間的間隔成為1cm、5mm、1mm、0.4mm,從而制備無定形的紅參濃縮液粉末。其中,通過篩選機(jī)來篩選并準(zhǔn)備大小為0.2~0.4mm的粉末。2.紅參濃縮液顆粒的制備向可用重量為100kg的流化床涂敷機(jī)內(nèi)投入上述粒子大小為0.2~0.4mm的無定形紅參濃縮液粉末后,一邊進(jìn)行流動化,一邊在吸入空氣量10m3/秒、投入管溫度90℃、噴射壓力2.3巴、噴射速度7kg/小時的流化床涂敷條件下,以底噴(bottomspray)方式噴射固體成分含量被調(diào)節(jié)為40重量百分比的噴射用紅參濃縮液,并制備出通過反復(fù)的涂敷及流動化步驟來球形化為1.2~1.7mm的粒子大小的球形狀的100%的純紅參濃縮液顆粒。更具體地,第一次在流化床涂敷機(jī)中經(jīng)過12小時的噴射及流動化步驟來形成粒子大小為0.4~0.6mm的顆粒后,第二次在流化床涂敷機(jī)中,在相同的流化床涂敷條件下噴射11小時的噴射用紅參濃縮液,并經(jīng)過11小時的噴射及流動化步驟來形成粒子大小為0.6~0.8mm的顆粒,第三次經(jīng)過10小時的相同步驟來形成粒子大小為0.8~1.0mm的顆粒,第四次經(jīng)過9小時的相同步驟來形成粒子大小為1.0~1.2mm的顆粒,第五次經(jīng)過4小時的相同步驟來形成粒子大小為1.2~1.7mm的球形狀的紅參濃縮液顆粒。3.防止吸濕的紅參濃縮液顆粒的制備向流化床涂敷機(jī)內(nèi)投入上述粒子大小為1.2~1.7mm的球形狀的紅參濃縮液顆粒后,一邊進(jìn)行流動化,一邊在吸入空氣量13m3/秒、投入管溫度80℃、噴射壓力2.0巴、噴射速度6kg/小時的流化床涂敷條件下,以底噴方式進(jìn)行噴射,使得在水中溶解有被粉碎為15~25μm大小的超微紅參粉末的噴射用超微紅參粉溶液成為紅參濃縮液顆粒的總重量的3%,并經(jīng)過涂敷及流動化步驟來制備防止吸濕的紅參濃縮液顆粒。紅參濃縮液顆粒因涂敷有微量的超微紅參粉溶液而不具有可識別的粒子大小的變化。實(shí)施例21.紅參濃縮液粉末的制備以與實(shí)施例1相同的方式進(jìn)行,在粉碎步驟中,使兩個輥之間的間隔最終成為0.6mm,而在篩選機(jī)中只篩選僅為0.4~0.6mm的來準(zhǔn)備無定形紅參濃縮液粉末。2.紅參濃縮液顆粒的制備以與實(shí)施例1相同的方式進(jìn)行,但不同于實(shí)施例1,反復(fù)進(jìn)行4個步驟。具體地,在第一球形化涂敷步驟中,以與實(shí)施例1相同的方式,以底噴方式向0.4~0.6mm的無定形紅參濃縮液粉末噴射11小時的噴射用紅參濃縮液并實(shí)施流動化,從而形成粒子大小為0.6~0.8mm的第一顆粒,在第二球形化涂敷步驟中,以相同方式,并以底噴方式向第一顆粒噴射10小時的噴射用紅參濃縮液并實(shí)施流動化,從而形成粒子大小為0.8~1.0mm的第二顆粒,在第三球形化涂敷步驟中,噴射9小時來形成粒子大小為1.0~1.2mm的第三次顆粒,在第四球形化涂敷步驟中,噴射4小時來制備粒子大小為1.2~1.7mm的球形狀的紅參濃縮液顆粒。3.防止吸濕的紅參濃縮液顆粒的制備以與實(shí)施例1的3個步驟相同的方式使粒子大小為1.2~1.7mm的球形狀的紅參濃縮液顆粒進(jìn)行流動化涂敷,從而制備防止吸濕的紅參濃縮液顆粒。實(shí)施例31.紅參濃縮液粉末的制備以與實(shí)施例1相同的方式進(jìn)行,而在粉碎步驟中,使兩個輥之間的間隔最終成為0.8mm,在篩選機(jī)中,只篩選0.6~0.8mm的來準(zhǔn)備無定形紅參濃縮液粉末。2.紅參濃縮液顆粒的制備以與實(shí)施例1相同的方式進(jìn)行,并以第一球形化涂敷步驟、第二球形化涂敷步驟及第三球形化涂敷步驟的3個步驟進(jìn)行涂敷步驟。具體地,在第一球形化涂敷步驟中,向流化床涂敷機(jī)內(nèi)投入上述粒子大小為0.6~0.8mm的無定形紅參濃縮液粉末,并以與實(shí)施例1相同的方式在流化床涂敷條件下,以底噴方式噴射10小時并實(shí)施流動化,從而制備粒子大小為0.8~1.0mm的第一顆粒,在第二球形化涂敷步驟中,以與第一球形化涂敷步驟相同的方式噴射9小時的第一顆粒并實(shí)施流動化,從而形成粒子大小為1.0~1.2mm的第二顆粒,在第三球形化涂敷步驟中,以與第一球形化涂敷步驟相同的方式噴射4小時的第二顆粒并實(shí)施流動化,從而形成粒子大小為1.2~1.7mm的球形狀的紅參濃縮液顆粒。3.防止吸濕的紅參濃縮液顆粒的制備以與實(shí)施例1的3個步驟相同的方式使粒子大小為1.2~1.7mm的球形狀的紅參濃縮液顆粒實(shí)施流動化涂敷,來制備防止吸濕的紅參濃縮液顆粒。圖3示出了通過這種步驟來制備的不同的流化床涂敷步驟的粒子的大小及所需時間。實(shí)施例41.紅參濃縮液粉末的制備以與實(shí)施例1相同的方式進(jìn)行,利用在輥式粉磨機(jī)的輥的表面的格子形陽刻圖案的中央形成有半球形狀的槽的。而且,在粉碎步驟中,使兩個輥之間的間隔最終成為0.8mm,在篩選機(jī)中,只篩選0.6~0.8mm的來準(zhǔn)備無定形紅參濃縮液粉末。圖4為在輥的表面的圖案形成有半球形的槽的輥式粉磨機(jī)中進(jìn)行粉碎后篩選的無定形紅參濃縮液粉末的照片。如圖所示,由于形成有半球形的槽,因此,可知雖然為無定形,但整體上呈圓形的形態(tài),因而可以容易地涂敷加工為球形狀。2.紅參濃縮液顆粒的制備以與實(shí)施例3相同的方式按第一球形化涂敷步驟、第二球形化涂敷步驟及第三球形化涂敷步驟的3個步驟進(jìn)行流動化涂敷步驟,從而形成粒子大小為1.2~1.7mm的球形狀的紅參濃縮液顆粒。3.防止吸濕的紅參濃縮液顆粒的制備以與實(shí)施例1的3個步驟相同的方式使粒子大小為1.2~1.7mm的球形狀的紅參濃縮液顆粒實(shí)施流動化涂敷來制備防止吸濕的紅參濃縮液顆粒。如圖6所示,所制備的紅參濃縮液顆粒呈球形狀。比較例11.紅參濃縮液粉末的制備以與實(shí)施例1相同的方式進(jìn)行,通過調(diào)節(jié)輥之間的間隔來篩選并準(zhǔn)備粒子大小為0.2mm以下的無定形紅參濃縮液粉末。2.紅參濃縮液顆粒的制備以與實(shí)施例1相同的方式進(jìn)行,起初為了使0.2mm以下的粒子形成為0.2~0.4mm的大小的顆粒而以底噴方式還使噴射用紅參濃縮液噴射13小時并實(shí)現(xiàn)流動化,最終制備粒子大小為1.2~1.7mm的球形狀的紅參濃縮液顆粒。3.防止吸濕的紅參濃縮液顆粒的制備以與實(shí)施例1的3個步驟相同的方式使粒子大小為1.2~1.7mm的球形狀的紅參濃縮液顆粒流動化涂敷來制備防止吸濕的紅參濃縮液顆粒。比較例21.紅參濃縮液粉末的制備以與實(shí)施例1相同的方式進(jìn)行,通過調(diào)節(jié)輥之間的間隔來篩選并準(zhǔn)備粒子大小為0.8~1.0mm的無定形紅參濃縮液粉末。2.紅參濃縮液顆粒的制備以與實(shí)施例1相同的方式進(jìn)行,起初向流化床涂敷機(jī)內(nèi)投入0.8~1.0mm大小的粒子后,一邊進(jìn)行流動化,一邊以底噴方式使噴射用紅參濃縮液進(jìn)行9小時的噴射及流動化,來制備粒子大小為1.0~1.2mm的顆粒,第二次還進(jìn)行4小時的噴射及流動化,來制備粒子大小為1.2~1.7mm的紅參濃縮液顆粒。3.防止吸濕的紅參濃縮液顆粒的制備以與實(shí)施例1的3個步驟相同的方式使粒子大小為1.2~1.7mm的紅參濃縮液顆粒流動化涂敷來制備防止吸濕的紅參濃縮液顆粒。比較例31.噴射用紅參濃縮液的制備在固體成分含量為60重量百分比的紅參濃縮液中添加水后進(jìn)行攪拌,從而制備固體成分含量為40重量百分比的噴射用紅參濃縮液。2.紅參濃縮液顆粒的制備在吸入空氣量為10m3/秒、投入管溫度為90℃、噴射壓力為2.3巴、噴射速度為7kg/小時的流化床涂敷條件下,以底噴方式噴射上述噴射用紅參濃縮液,并通過反復(fù)的涂敷及流動化步驟來制備粒子大小為1.2~1.7mm的球形狀的100%純紅參濃縮液顆粒。此時,第一次噴射及流動化進(jìn)行16小時,從而形成0.2mm以下的第一顆粒,第二次噴射及流動化對第一顆粒進(jìn)行13小時的噴射及流動化來形成0.2~04mm的顆粒,第三次噴射及流動化進(jìn)行12小時,第四次噴射及流動化進(jìn)行11小時,第五次噴射及流動化進(jìn)行10小時,第六次噴射及流動化進(jìn)行9小時,從而按各不同的步驟來規(guī)?;癁?mm大小。而且,7個步驟在4小時內(nèi)進(jìn)行噴射及流動化,從而制備1.2~1.7mm大小的球形狀的100%純紅參濃縮液顆粒。3.防止吸濕的紅參濃縮液顆粒的制備以與實(shí)施例1的3個步驟相同的方式使粒子大小為1.2~1.7mm的紅參濃縮液顆粒流動化涂敷,從而制備防止吸濕的紅參濃縮液顆粒。圖2示出按這種現(xiàn)有制備方法的各不同的步驟來制備的多個顆粒的照片和基于此的時間。實(shí)驗(yàn)例1:紅參濃縮液顆粒的紋理及球形外觀的均勻度評價在紋理及球形外觀的均勻度評價中,選拔8名評價人員作為描述分析人員,并對在口中溶化的程度及球形外觀的均勻度,每隔30分鐘進(jìn)行四次訓(xùn)練,并將各術(shù)語的強(qiáng)度與標(biāo)準(zhǔn)品的分?jǐn)?shù)相比較來實(shí)施客觀評價。就對紋理的評價而言,對在口中放入0.3g的紅參濃縮液顆粒來溶化并吞咽時,在口中溶解的程度進(jìn)行評價,而在口中溶解的程度表示在將放入1g棉花糖來溶化的程度設(shè)定為9分時所感受到的強(qiáng)度。并且,球形外觀的均勻度評價表示在將2mm玻璃球的球形程度和均衡程度設(shè)定為9分時所呈現(xiàn)出的紅參濃縮液顆粒的程度。此時,使用9分量表法,1分被評價為非常弱的程度,5分被評價為中間程度,9分被評價為非常強(qiáng)的程度,而評價結(jié)果為收集8名的結(jié)果后實(shí)施平均的結(jié)果,其結(jié)果如以下表1所示。表1紋理球形外觀的均勻度實(shí)施例15.37.6實(shí)施例25.27.3實(shí)施例35.27.4實(shí)施例45.17.5比較例15.47.7比較例25.15.4比較例35.57.5從上述表1中可知,當(dāng)與通過現(xiàn)有的制備方法制備的比較例3相比較時,通過實(shí)施例1至4的制備方法制備的紅參濃縮液顆粒在紋理及球形外觀的均勻度方面幾乎相同。但是,可知在使用粒子大小被粉碎為0.8~1.0mm的紅參濃縮液粉末的比較例2的情況下,球形外觀的均勻度顯著降低,從而在可銷售性方面成為問題。實(shí)驗(yàn)例2:流化床涂敷的時間按不同的制備條件來測定使用100kg生產(chǎn)量的流化床涂敷機(jī)來制備100kg的防止吸濕的粒子大小為1.2~1.7mm的紅參濃縮液顆粒所需的時間,其結(jié)果如表2所示。表2流化床涂敷時間(小時)實(shí)施例149實(shí)施例237實(shí)施例326實(shí)施例426比較例162比較例216比較例378從上述表2中可知,使用粒子大小為0.2~0.8mm的無定形紅參濃縮液粉末的實(shí)施例1至實(shí)施例4的情況下,當(dāng)與通過現(xiàn)有的制備方法制備的比較例3的制備工序相比較時,流化床涂敷時間相當(dāng)縮短,從而節(jié)約制備成本。但是,當(dāng)與比較例3的現(xiàn)有工序相比較時,比較例1的工序雖然縮短制備時間,但若考慮到追加性的紅參濃縮液的干燥粉末的制備成本等,則被判斷為經(jīng)濟(jì)效果甚微。另一方面,比較例2的短的制備時間如上述所示的實(shí)驗(yàn)例1的結(jié)果,由于外觀均勻度的降低導(dǎo)致的可銷售性降低,因而判斷制備時間的縮短不具有多大意義。但是,在紋理及球形外觀的均勻度方面呈現(xiàn)出幾乎相等的水準(zhǔn)的實(shí)施例3、實(shí)施例4的情況下,具有作為現(xiàn)有工序的比較例3的1/3水準(zhǔn)的制備時間具有非常大的效果。產(chǎn)業(yè)上的可利用性本發(fā)明的紅參濃縮液顆粒能夠以如下多種方式進(jìn)行攝取,即,以顆粒狀態(tài)單獨(dú)攝取或與其他顆?;旌蠑z取或溶解于水或飲料等。當(dāng)前第1頁12