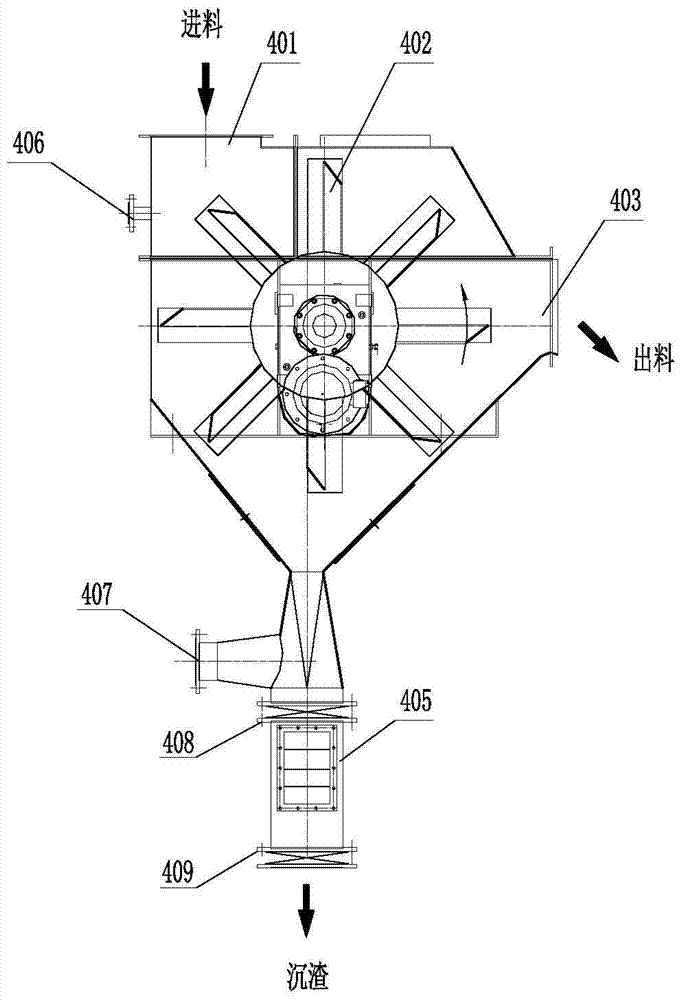
本發(fā)明涉及一種制漿系統(tǒng)和制漿方法,具體涉及一種廢紙回收再利用化學(xué)機械制漿系統(tǒng)和制漿方法。
背景技術(shù):廢紙是重要的造紙纖維原料,各國都很重視廢紙資源的回收利用,世界廢紙回收量由2005年的1.826億噸提高到2010年的2.234億噸;回收率由49.8%提高到56.6%,發(fā)達國家普遍超過60%,韓國、德國超過80%。我國廢紙制漿由2005年的2810萬噸增至2010年的5305萬噸,占總用漿量比重由54.0%提升至62.7%,其中國內(nèi)廢紙漿的比重由27.8%提升至38.0%。至“十二五”期間,廢紙漿增量約為1400萬噸。國內(nèi)廢紙回收率將提高至46.7%,同時,仍要充分利用境外廢紙資源,使我國造紙工業(yè)廢紙利用率提高至72.1%。目前,受國內(nèi)廢紙質(zhì)量較低和廢紙回收率偏低等因素的影響,廢紙資源供給對外依存度較高,美廢、歐廢和日廢的可出口資源基本都進入中國,且質(zhì)量在逐年下降,價格卻在逐年提高,供需矛盾日益加劇。廢紙的再生利用可以節(jié)約大量的原生纖維資源、節(jié)約能源的消耗、減輕環(huán)境的污染,而且相比于商品紙漿,廢紙的再制漿具有明顯的成本優(yōu)勢。隨著人們生活水平的提高,對紙和紙板的要求也越來越高,很多紙種特別是包裝類紙板為了能在潮濕或有水存在的情況下仍具有一定的強度,在生產(chǎn)時經(jīng)常使用濕強劑。這些具有濕強度的廢紙的數(shù)量呈逐年增加趨勢。不含濕強劑的普通紙,纖維連接依靠氫鍵形成的范德華力,水可以打破氫鍵連接,使紙張碎解。濕強劑樹脂可與纖維素、半纖維素形成交聯(lián)、不溶水和共價鍵的網(wǎng)絡(luò)結(jié)構(gòu)。通常情況下,經(jīng)濕強樹脂處理的紙在用水完全潤濕后仍將維持原干強度的30%以上,可保持紙張完整度,而無濕強劑處理的普通紙僅能維持2~7%的原干強度。因此,濕強度高的廢紙回收利用很困難,碎漿時存在高篩渣含量、低得率和高電耗等技術(shù)問題難以解決,這主要是因為用常規(guī)的制漿疏解設(shè)備和工藝不能將其充分分散成紙漿。進口的廢紙中往往夾雜有一些很難疏解的濕強廢紙,特別是使用了高含量濕強劑的永固性濕強廢紙,疏解極為困難,即使延長打漿時間或增加打漿強度也難以獲得好的效果。很多濕強度較高的廢紙作為固體廢棄物被填埋,或作為垃圾焚燒,這既造成了環(huán)境的污染,也浪費了可用于造紙的廢紙資源。許多濕強紙含有高質(zhì)量漂白化學(xué)纖維或高質(zhì)量長纖維漿料,有很高的利用價值,當前造紙纖維原料的短缺促使造紙行業(yè)對濕強廢紙的再生利用必須進行大的技術(shù)改進。目前濕強廢紙再制漿方法和技術(shù)主要分為兩類:機械法和化學(xué)法,且均處于研究階段試制階段?!?】機械法濕強廢紙再制漿方法。杜永等(杜永,王中原.廢濕強紙的處理【J】.中國造紙,2009,28(7):68~69)利用機械法處理濕強廢紙,處理過程中不需蒸汽,僅需純機械式打漿、磨漿把廢紙疏解為合格的纖維漿料。廢紙首先通過高濃碎漿機碎解,碎漿濃度12~15%,碎漿時間25~30min,間歇式工作,每鍋放料后,積存的較大紙片因無法通過碎漿機底部篩板篩孔,被留存鍋內(nèi),留作下次打漿;高濃碎漿機每打完一鍋漿料,就由螺旋輸送機輸送到中間緩沖漿罐,罐內(nèi)漿料濃度稀釋至8~10%;緩沖漿罐內(nèi)漿料利用高位差,自流至雙螺旋擠漿機濃縮至漿濃25~30%;濃縮后漿料經(jīng)斜螺旋輸送機輸送至高濃盤磨磨漿機磨漿,高濃磨磨漿濃度20~30%,磨漿過程采用兩臺串聯(lián)方式,磨漿后漿料打漿度可達到原成漿時的打漿度。此技術(shù)的不足之處在于(1)高濃碎漿生產(chǎn)不連續(xù),時間較長;(2)電耗較高;(3)濕強劑未經(jīng)化學(xué)處理,會造成后序制漿造紙過程中再絮凝,影響紙張抄造;(4)濕強劑的存在會影響紙張抄造時其它駐留助劑等化學(xué)品的使用效果?!?】堿法化學(xué)蒸煮濕強廢紙再制漿方法。王建等(王建,齊亮,白鐵軍,華開開.PAE增濕強本色廢紙的再制漿工藝【J】.紙和造紙,2008,27(5):47-49)用化學(xué)蒸煮的方法處理本色廢紙,將廢紙裝入蒸球,液比1:6,添加1%的燒堿和0.05%的AQ進行蒸煮,蒸煮后再通過水力碎漿機碎解。在最高蒸煮溫度160℃,保溫30min的條件下,粗漿得率可達到82.7%,再制漿損失率17.3%。曹慶福等(曹慶福,張元彬,張桂蘭.濕強廢紙最佳處理方法選擇【J】.中華紙業(yè),1998(4):45)用自制蒸煮器處理含濕強劑的紗管封面紙,在裝入廢紙的蒸煮器中加入7.5%的硫酸鋁蒸煮2h,然后經(jīng)水力碎漿機碎解,每噸廢紙較原來利用水力碎漿機和打漿機設(shè)備處理的機械法,噸漿電耗由原來的1232kw.h降至146kw.h,降低費用1148元,取得了較好的效果。堿法化學(xué)蒸煮可以分解濕強劑或破壞濕強劑與紙漿纖維的化學(xué)結(jié)合,解離濕強紙。存在問題:(1)廢紙漿得率較低,大量的纖維原料降解后進入到制漿廢水中,增加了廢水處理的難度和成本;(2)如果不對解離的廢紙漿漂白,紙漿白度很低,只能用于一些對白度要求不高的紙板中,紙漿用途受到限制;(3)化學(xué)蒸煮方法對廢紙漿的化學(xué)作用比較強烈,造成纖維素聚合度下降,而導(dǎo)致成漿的物理強度下降?!?】氧化劑處理濕強廢紙再制漿方法。聚酰胺多胺環(huán)氧氯丙烷(PAE)樹脂是目前造紙工業(yè)中占主導(dǎo)的濕強劑,因而,很多關(guān)于濕強廢紙再生利用的研究都是針對PAE類濕強廢紙的。氧化劑可以破壞PAE在紙頁中產(chǎn)生的網(wǎng)絡(luò)結(jié)構(gòu)或者直接破壞它與紙漿纖維的化學(xué)鍵,解離濕強紙。主要有:(1)次氯酸鹽處理法。在濃度為5%左右的濕強紙漿中,緩緩加入NaOH溶液調(diào)PH值至11,再加入NaCIO漂液,,在反應(yīng)溫度下處理一定時間。待反應(yīng)結(jié)束,將紙料混合液轉(zhuǎn)移至高速分散機中剪切幾分鐘,漿料經(jīng)洗滌再進行抄紙。研究表明:NaCIO用量對濕強紙的疏解影響最大,當用量達到0.5~0.8g/L時,疏解較容易,疏解率較高;PH值對NaCIO法影響較為特殊,PAE樹脂在較寬的PH值(4~10)范圍內(nèi),具有良好的穩(wěn)定性,特別是PH值在6.5~8.0之間時,其性質(zhì)最為穩(wěn)定,酰胺環(huán)氧化物間的交聯(lián)鍵最不易破壞,疏解最困難,所以應(yīng)避開樹脂的穩(wěn)定范圍,選擇在PH<6.5或強堿(PH>11)的條件下進行疏解;溫度也是影響再制漿的一個重要因素,用次氯酸鈉或次氯酸鈣處理PAE濕強紙時,較高的處理溫度不利于再制漿;機械剪切處理對再制漿的作用與打漿和精漿的原理相似,能增加纖維潤張,從而有利于提高紙頁的強度。存在問題:次氯酸鹽處理法可以有效的處理漂白的PAE濕強紙,且成本較低,但是它不能將非漂白濕強紙完全再制漿,而且,會增加排放污水中氯仿、四氯乙烷等可吸附有機鹵化物(AOX)的負荷,這也是限制次氯酸鹽使用的不利因素。(2)過氧化二硫酸鹽處理濕強廢紙。王麗娟等(王麗娟,楊汝男,章海濤,等.濕強紙再制漿的的研究【J】.中國造紙,2004,23(4):63-64)采用過硫酸鉀處理廢人民幣紙,較適宜的處理條件為過硫酸鉀用量6%,酸處理PH值3,時間30min,制漿濃度13%。成漿率可控制在94%以上。Stephen.AFicher等(Ficher,S.A..Repulpingwet-strengthpaper【J】.TappiJ1997,80(11):141-147)用過硫酸鈉處理含有PAE濕強劑的本色??垺.斶^硫酸鈉的用量為1%,預(yù)處理PH值11,疏解時間70min的條件下,本色???PAE用量0.6%)的再制漿得率達到66%。當進一步增加過硫酸鈉的用量到10%,預(yù)處理PH值和時間不變的情況下,處理另一種本色???PAE用量0.4%),再制漿得率可以達到74%。結(jié)果表明,過硫酸鹽在堿性條件下對含有PAE的濕強廢紙的處理效果較差。過氧化二硫酸鹽的模型化合物反應(yīng)機理:氧化劑易進攻PAE樹脂聚合物的叔胺或酰胺-環(huán)氧化合物間的仲酰胺鍵,使PAE樹脂發(fā)生分解反應(yīng),從而導(dǎo)致濕強紙失去濕增強功能。過氧化二硫酸鹽處理濕強廢紙再制漿受處理溫度、反應(yīng)時間、氧化劑用量、PH值和機械剪切等因素的影響較大。溫度升高有利于再制漿,在中堿性條件下,處理后的紙漿強度略高于NaCIO法,但需要稍高的溫度,且反應(yīng)速度稍慢,再制漿白度略低;過氧化二硫酸鹽再制漿廢液中可吸附有機鹵的含量極低;再制漿不經(jīng)洗滌重新添加等量的濕強劑,殘留的過氧化二硫酸鹽對再抄紙的紙張的濕強度影響遠低于殘留NaCIO產(chǎn)生的影響,可節(jié)省大量洗滌水。存在問題:在中性或堿性再制漿過程中,由于過氧化二硫酸鹽分解產(chǎn)生的自由基能提取木質(zhì)素上的氫形成無反應(yīng)活性的自由基,而使大部分濕強樹脂未被氧化,所以,過氧化二硫酸鹽對未漂硫酸鹽漿、化學(xué)熱磨機械漿及OCC濕強紙不太有效,難于再制漿。雖過量的過氧化二硫酸鹽可以克服這種副反應(yīng),但是價格太昂貴,效率不高,而且對纖維有損害。
技術(shù)實現(xiàn)要素:發(fā)明目的:為了克服現(xiàn)有技術(shù)中存在的不足,本發(fā)明提供一種濕強廢紙回收再利用化學(xué)機械制漿系統(tǒng),進而提供一種濕強廢紙回收再利用化學(xué)機械制漿方法。技術(shù)方案:為解決上述技術(shù)問題,本發(fā)明提供的濕強廢紙回收再利用化學(xué)機械制漿系統(tǒng),按物料工序運行方向,該系統(tǒng)包括第一輸送設(shè)備、碎料機、第二輸送設(shè)備、轉(zhuǎn)鼓式洗滌機、斜螺旋脫水機、汽蒸倉、第三螺旋輸送機、第一雙螺桿浸漬機、第一反應(yīng)倉、第四螺旋輸送機、第二雙螺桿浸漬機、第二反應(yīng)倉、第五螺旋輸送機、消潛漿池、漿泵、纖維分離機、凈化篩選濃縮裝置、貯漿裝置;所述第一輸送設(shè)備的出料口正對碎料機的進料口,所述碎料機的出料口正對第二輸送設(shè)備的進料口,所述第二輸送設(shè)備的出料口正對轉(zhuǎn)鼓式洗滌機的進料口,所述轉(zhuǎn)鼓式洗滌機的出料口與斜螺旋脫水機的進料口連通,所述斜螺旋脫水機的出料口與汽蒸倉的進料口連通,所述汽蒸倉的出料口與第三螺旋輸送機進料口連通,所述第三螺旋輸送機的出料口與第一雙螺桿浸漬機的進料口連通,所述第一雙螺桿浸漬機的出料口與第一反應(yīng)倉的進料口連通,所述第一反應(yīng)倉的出料口與第四螺旋輸送機的進料口連通,所述第四螺旋輸送機的出料口與第二雙螺桿浸漬機的進料口連通,所述第二雙螺桿浸漬機的出料口與第二反應(yīng)倉的進料口連通,所述第二反應(yīng)倉的出料口與第五螺旋輸送機的進料口連通,所述第五螺旋輸送機的出料口連通至消潛漿池,所述漿泵設(shè)于消潛漿池與纖維分離機之間,漿泵的輸入端與消潛漿池的容積腔連通,漿泵的輸出端與纖維分離機的進料口連通,所述纖維分離機的出料口與凈化篩選濃縮裝置的進料口連通,所述凈化篩選濃縮裝置的出料口與貯漿裝置相連。優(yōu)選的,本系統(tǒng)還包括料片泵,所述轉(zhuǎn)鼓式洗滌機的出料口與斜螺旋脫水機的進料口的連通方式為:在轉(zhuǎn)鼓式洗滌機的出料口下方設(shè)有容器,所述料片泵設(shè)于該容器與斜螺旋脫水機之間,料片泵的輸入端設(shè)置在該容器的容積腔內(nèi),料片泵的輸出端與斜螺旋脫水機的進料口連通。優(yōu)選的,所述碎料機為撕碎機或水力碎漿機;所述第一輸送設(shè)備和第二輸送設(shè)備為鏈板輸送機或皮帶輸送機;所述凈化篩選濃縮裝置包括順序連接的壓力篩、除渣器和濃縮設(shè)備,所述纖維分離機的出料口與壓力篩的進料口連通,所述壓力篩的出料口與除渣器的進料口連通,所述除渣器的出料口與濃縮設(shè)備的進料口連通,所述濃縮設(shè)備的出料口與貯漿裝置相連。優(yōu)選的,所述轉(zhuǎn)鼓式洗滌機包括機體,轉(zhuǎn)鼓、轉(zhuǎn)鼓驅(qū)動裝置;所述機體一側(cè)上部設(shè)有進料口,其另一側(cè)設(shè)有出料口,機體內(nèi)設(shè)有洗滌腔,所述轉(zhuǎn)鼓設(shè)于洗滌腔內(nèi)并受轉(zhuǎn)鼓驅(qū)動裝置驅(qū)動旋轉(zhuǎn);所述轉(zhuǎn)鼓位置下方的機體底部形狀呈倒錐臺形;所述機體鄰近進料口的一端設(shè)有上進水口,所述機體底部的倒錐臺形的下錐臺口的下方設(shè)有與下錐臺口連通的管體,管體側(cè)壁設(shè)有下進水口;所述管體的下方設(shè)有沉渣管,所述沉渣管的上端設(shè)有上卸渣閥,下端設(shè)有下卸渣閥。采用本結(jié)構(gòu)的轉(zhuǎn)鼓式洗滌機可通過下進水口進水形成上行水流,上行水流的推力將有效減少比重較輕的物料向下沉淀,僅使得比重較重的重雜質(zhì)如金屬物、石子等沉入沉渣管,可以有效的清除物料中的重雜質(zhì),且極大的減少了物料在洗滌分離雜質(zhì)的過程中易造成的損耗。優(yōu)選的,所述斜螺旋脫水機包括螺旋外殼,螺旋外殼內(nèi)設(shè)有受螺旋驅(qū)動裝置驅(qū)動旋轉(zhuǎn)的螺旋,所述螺旋外殼及其內(nèi)部的螺旋沿物料輸送方向由低到高傾斜設(shè)置,所述螺旋外殼的較低的一端為外殼斜下端,較高的一端為外殼斜上端,所述外殼位于外殼斜下端的上部設(shè)有進料口,位于外殼斜下端的下部設(shè)有排水口,位于外殼斜上端的下部設(shè)有出料口,所述螺旋外殼內(nèi)位于螺旋的下部平行設(shè)有濾網(wǎng)板。本系統(tǒng)中的汽蒸倉可選用本領(lǐng)域常規(guī)汽蒸倉如振動式卸料汽蒸倉。作為本發(fā)明的進一步改進,本系統(tǒng)中的汽蒸倉優(yōu)選旋轉(zhuǎn)撥料式汽蒸倉,所述旋轉(zhuǎn)撥料式汽蒸倉,包括倉體、旋轉(zhuǎn)撥料裝置、排料裝置,倉體內(nèi)設(shè)有蒸腔,倉體上部設(shè)有進料口;所述旋轉(zhuǎn)撥料裝置包括設(shè)在倉體底部的撥料盤,所述撥料盤包括底盤和可在底盤上旋轉(zhuǎn)的撥料片;所述排料裝置包括殼體和排料電機,殼體內(nèi)設(shè)有排料螺旋,所述排料螺旋包括螺旋軸和設(shè)置在螺旋軸上的螺旋葉片,該螺旋軸與設(shè)在殼體一側(cè)的排料電機傳動連接,殼體另一側(cè)下部設(shè)有出料口;排料裝置位于撥料盤下方,撥料盤的底盤與排料裝置的殼體對接的部位設(shè)有落料開口。作為本發(fā)明的進一步改進,本旋轉(zhuǎn)撥料式汽蒸倉中,旋轉(zhuǎn)撥料裝置還包括撥料電機和中心軸,所述底盤中心設(shè)有通孔,所述中心軸穿過該通孔一端與撥料片固定連接,另一端通過聯(lián)軸器與撥料電機傳動連接;所述底盤為圓形底盤,所述落料開口位于底盤的偏心位置上,且位于撥料片旋轉(zhuǎn)覆蓋的底盤區(qū)域內(nèi),為由與圓形底盤同圓心的兩段圓弧和兩條弦構(gòu)成四條邊的落料開口;所述蒸腔內(nèi)壁位于撥料盤的上部周向均布防滑條;所述倉體為圓柱形或圓臺形;所述倉體底部設(shè)有蒸汽進管,所述倉體上部設(shè)有蒸汽回流口和蒸汽排放口;所述排料裝置的殼體上鄰近出料口的部位設(shè)有蒸汽輸出口;還包括回氣管,所述回氣管的一端管口與所述排料裝置的蒸汽輸出口對接,另一端與所述倉體上部的蒸汽回流口對接;所述排料電機為可調(diào)速齒輪減速電機,所述排料螺旋的螺旋軸由軸承和軸承座支撐,兩端設(shè)有密封函,所述螺旋葉片為沿螺旋軸輸送方向螺距逐漸由小變大的變螺距螺旋葉片。當倉體內(nèi)物料達到一定料位并滿足充足停留汽蒸時間后,本旋轉(zhuǎn)撥料式汽蒸倉通過旋轉(zhuǎn)撥料裝置,連續(xù)將制漿原料分層并按先進先出原則通過落料開口撥入排料裝置,然后由排料裝置計量送出。一方面可消除因物料受熱、壓實和體積膨脹導(dǎo)致倉內(nèi)出現(xiàn)的架橋現(xiàn)象,提高倉容利用率;另一方面物料得到充足的汽蒸軟化,會有效提升后序工藝中的擠壓化學(xué)預(yù)漬效果和水溶性有色物質(zhì)及樹脂物質(zhì)的脫除率,降低化學(xué)品消耗,從而提高漂白化學(xué)機械漿漿料的白度和物理性能;當物料短暫中斷時,還能作為一個緩沖容器,確保給系統(tǒng)提供均勻、可控的物料。保證物料汽蒸效果的同時,很好的維持了正常連續(xù)生產(chǎn)的穩(wěn)定性。更進一步,上述蒸汽回路設(shè)計,可充分利用蒸汽能效,在進一步提高物料汽蒸軟化效果的同時,節(jié)能環(huán)保。更進一步,物料在倉體內(nèi)呈塞式垂直下落,本旋轉(zhuǎn)撥料式汽蒸倉通過防滑條有效防止了物料隨撥料裝置打滑旋轉(zhuǎn)的問題。更進一步,排料螺旋螺旋軸上的螺旋葉片采用變螺距設(shè)計,一方面保證了落料開口下方的螺旋軸螺槽內(nèi)物料呈充滿狀態(tài),另一方面使得物料在輸送過程中沿螺旋軸輸送方向由充滿狀態(tài)逐漸過渡到松散狀態(tài),提高效率,降低了螺旋運轉(zhuǎn)負載和磨損,實現(xiàn)連續(xù)計量出料的同時,提高了系統(tǒng)的穩(wěn)定性。其中的第一反應(yīng)倉和第二反應(yīng)倉可選用本領(lǐng)域常規(guī)反應(yīng)倉,作為本發(fā)明的進一步改進,優(yōu)選均勻落料式反應(yīng)倉。所述均勻落料式反應(yīng)倉,包括倉體和均勻落料裝置,倉體頂部設(shè)有進料口,倉體底部設(shè)有落料口;所述均勻落料裝置,包括殼體,殼體內(nèi)設(shè)有排料螺旋,殼體一側(cè)下部設(shè)有反應(yīng)倉的出料口,該均勻落料裝置的進料口即為反應(yīng)倉倉體底部的落料口;所述排料螺旋包括螺旋軸和設(shè)置在螺旋軸上的螺旋葉片,所述螺旋軸位于出料口上方的部位固定設(shè)有均勻落料環(huán),所述均勻落料環(huán)與所述螺旋軸的中心軸線一致;所述均勻落料環(huán)包括管體和多線螺紋葉片,所述多線螺紋葉片固定連接在管體的外壁上,所述管體固定環(huán)繞套接在螺旋軸上,所述多線螺紋葉片的旋向與所述排料螺旋上的螺旋葉片旋向一致。作為本發(fā)明的進一步改進,本均勻落料式反應(yīng)倉的倉體為梯形方倉;所述均勻落料裝置包括兩根以上的排料螺旋,每根排料螺旋均包括螺旋軸和螺旋葉片,所述螺旋葉片為沿輸送方向螺距逐漸由小變大的變螺距螺旋葉片;每根排料螺旋的螺旋軸位于出料口上方的部位均固定設(shè)有均勻落料環(huán),每個均勻落料環(huán)與其對應(yīng)的螺旋軸中心軸線一致,每個均勻落料環(huán)上的多線螺紋葉片與其對應(yīng)的排料螺旋上的螺旋葉片旋向一致;所述兩根以上的排料螺旋分別獨立驅(qū)動,相鄰排料螺旋的螺旋軸反向旋轉(zhuǎn)。本均勻落料式反應(yīng)倉通過均勻落料環(huán)可實現(xiàn)均勻下料,有利于下游制漿設(shè)備穩(wěn)定生產(chǎn),負載波動幅度由原來的一倍以上降低至10~15%之內(nèi),降低了設(shè)備故障率,提高了設(shè)備可靠性,穩(wěn)定了漿料質(zhì)量。在此基礎(chǔ)上,進一步可通過兩根以上的排料螺旋反向旋轉(zhuǎn),使得物料在鄰近排料螺旋上的兩個反向旋轉(zhuǎn)尤其是反內(nèi)向旋轉(zhuǎn)的螺旋葉片的共同推動下,更加均衡的往前推移,然后經(jīng)均勻落料環(huán)的攪拌打散,連續(xù)均勻得從出料口下落至下游設(shè)備。排料螺旋上螺旋葉片的變螺距設(shè)計可以使得物料在輸送過程中沿螺旋軸輸送方向由充滿狀態(tài)逐漸過渡到松散狀態(tài),提高效率,降低螺旋運轉(zhuǎn)負載和磨損。優(yōu)選的,本系統(tǒng)中的第一、第二雙螺桿浸漬機,如在2012年9月11日提交的申請?zhí)枮?01210332112.8、公開號為CN102864669A的名為“一種雙螺桿浸漬機”的中國專利申請中所描述的,其全部內(nèi)容通過引用結(jié)合于此。也可以如2012年9月11日提交的授權(quán)號為ZL201220458032.2的名為“一種雙螺桿浸漬機”的中國專利申請中所描述的,其全部內(nèi)容通過引用結(jié)合于此。上述的雙螺桿浸漬機包括機架以及設(shè)置在機架上的電機、齒輪變速箱、可移式鼓形齒聯(lián)軸器、機筒和兩根螺桿,所述電機通過齒輪變速箱以及可移式鼓形齒聯(lián)軸器與兩根螺桿傳動連接,所述兩根螺桿互相平行且可轉(zhuǎn)動地設(shè)置在所述機筒內(nèi),所述機筒一端設(shè)有進料口,另一端設(shè)有出料口;所述螺桿沿輸送方向依次套設(shè)有第一輸送螺旋套、第一擠壓螺旋套、第二輸送螺旋套、第二擠壓螺旋套、第三輸送螺旋套以及第三擠壓螺旋套,所述第一、第二、第三輸送螺旋套的螺旋方向與所述第一、第二、第三擠壓螺旋套的螺旋方向相反,所述第一輸送螺旋套的螺距沿輸送方向逐漸減??;所述機筒上部設(shè)有與第三輸送螺旋套對應(yīng)的液體加入孔,所述機筒下部設(shè)有廢液孔;所述第一、第二、第三擠壓螺旋套的螺棱上開有豁槽;所述機筒為上下剖分式機筒,包括對稱連接的固定設(shè)置在機架上的上半機筒和可啟閉的連接在機架上的下半機筒。其中的第一反應(yīng)倉和第二反應(yīng)倉也可以與上述汽蒸倉結(jié)構(gòu)組成相同,因為經(jīng)雙螺桿浸漬機擠壓揉搓的物料,其摩擦熱溫度已滿足反應(yīng)倉反應(yīng)所需,所以當反應(yīng)倉使用與汽蒸倉一樣的結(jié)構(gòu)時,可以不通過蒸汽管注入蒸汽加熱,當然在需要的情況下,也可以選用蒸汽加熱的方式。為解決上述技術(shù)問題,本發(fā)明提供的一種強廢紙回收再利用化學(xué)機械制漿方法,其使用上述的濕強廢紙回收再利用化學(xué)機械制漿系統(tǒng),該方法中各藥劑組分的百分量是占絕干原料重量的百分量,該濕強廢紙回收再利用化學(xué)機械制漿方法包括:①備料工段:將原料輸送至碎料機破解成料片后,輸送至轉(zhuǎn)鼓式洗滌機加水調(diào)整濃度為3~5%進行洗滌、沉渣去除混雜在物料中的雜質(zhì),洗滌后的物料和水由料片泵泵送至斜螺旋脫水機進一步清除殘余雜質(zhì)并完成脫水;殘余雜質(zhì)和水通過斜螺旋脫水機的篩網(wǎng)網(wǎng)孔排出;②汽蒸工段:將備料工段輸出的脫水后的物料輸送至汽蒸倉,在0.3~0.6MPa的蒸汽壓力范圍內(nèi)汽蒸15~30分鐘使得物料汽蒸軟化;③第一擠壓浸漬化學(xué)機械處理段:將汽蒸工段輸出的蒸后物料由螺旋輸送機輸送至本段雙螺桿浸漬機內(nèi)被擠壓揉搓為絲團狀并濃縮至35~45%濃度,其后在本段雙螺桿浸漬機內(nèi)與計量加入的第一化學(xué)浸漬藥劑高濃混合,并加水調(diào)整漿濃至25~35%,實現(xiàn)均質(zhì)化化學(xué)浸漬處理后排出至反應(yīng)倉,在80~95℃的溫度范圍內(nèi),停留35~60分鐘進行反應(yīng);④第二擠壓浸漬化學(xué)機械處理段:將第一擠壓浸漬化學(xué)機械處理段反應(yīng)倉輸出的漿料,由螺旋輸送機輸送至本段雙螺桿浸漬機中被進一步擠壓揉搓為纖維束和單根纖維混合物狀并濃縮至35~45%濃度,其后在本段雙螺桿浸漬機內(nèi)與計量加入的第二化學(xué)浸漬藥劑高濃混合,并加水調(diào)整漿濃至25~35%,實現(xiàn)均質(zhì)化化學(xué)浸漬處理后排出至反應(yīng)倉,在80~95℃的溫度范圍內(nèi),停留35~60分鐘進行反應(yīng);⑤消潛和再疏解段:將第二擠壓浸漬化學(xué)機械處理段反應(yīng)倉輸出的漿料,由螺旋輸送機輸送至消潛漿池內(nèi)使得球團狀纖維分散伸展消除內(nèi)應(yīng)力,加水調(diào)整漿濃至3~5%,調(diào)整漿料溫度范圍為60~70℃,其后通過漿泵泵送至纖維分離機進行再疏解,分離出輕、重雜質(zhì)和粗大廢料和濕強紙纖維;⑥凈化、篩選和濃縮段:將消潛和再疏解段分離得到的濕強紙纖維,經(jīng)除渣器凈化、壓力篩篩選、濃縮設(shè)備濃縮后存貯在貯漿裝置中備抄。優(yōu)選的,所述①備料工段中轉(zhuǎn)鼓式洗滌機洗滌后得到的沉渣雜質(zhì)進入固廢處理系統(tǒng),通過斜螺旋脫水機的濾網(wǎng)板網(wǎng)孔排出的殘余雜質(zhì)和水進入水處理系統(tǒng),經(jīng)沉淀凈化后循環(huán)回用于洗滌過程。優(yōu)選的,按照占絕干原料的重量百分比,所述②汽蒸工段中,脫水后的物料輸送至汽蒸倉汽蒸時加入0.1%~0.15%的再濕劑,所述再濕劑包含線性或直連乙氧基化物或丙氧基化物的醇,以及消泡劑如硅氧烷基膠乳;所述③第一擠壓浸漬化學(xué)機械處理段中第一化學(xué)浸漬藥劑為1~2%的NaOH或Na2CO3,通過堿處理的漿料PH值控制在11.5~12.5范圍內(nèi);所述④第二擠壓浸漬化學(xué)機械處理段中的第二化學(xué)浸漬藥劑為氧化劑,通過氧化劑處理的漿料PH值控制在11.5~12.5范圍內(nèi);所述氧化劑包含1~3%的NaOH、2~6%的H2O2、1~2%的Na2SiO3和0.2~0.5%的螯合劑;所述螯合劑為DTPA或EDTA的任意一種。作為進一步的優(yōu)選,所述②汽蒸工段中,脫水后的物料輸送至汽蒸倉汽蒸時加入0.1%的再濕劑;所述③第一擠壓浸漬化學(xué)機械處理段中第一化學(xué)浸漬藥劑為1%的NaOH;所述④第二擠壓浸漬化學(xué)機械處理段中的第二化學(xué)浸漬藥劑包含1%的NaOH、2%的H2O2、1%的Na2SiO3和0.2%的DTPA。作為另一種優(yōu)選方案,按照占絕干原料的重量百分比,所述②汽蒸工段中,脫水后的物料輸送至汽蒸倉汽蒸時加入0.1%~0.15%的再濕劑;所述③第一擠壓浸漬化學(xué)機械處理段中的第一化學(xué)浸漬藥劑為1~1.5%的H2SO4或3~6%的明礬,通過酸處理的漿料PH值控制在4.5~6范圍內(nèi);所述④第二擠壓浸漬化學(xué)機械處理段中的第二化學(xué)浸漬藥劑為氧化劑,通過氧化劑處理的漿料PH值控制在11.5~12.5范圍內(nèi);所述氧化劑包含1~3%的NaOH、2~6%的H2O2、1~2%的Na2SiO3和0.2~0.5%的螯合劑;所述螯合劑為DTPA或EDTA的任意一種。作為另一種優(yōu)選方案的更進一步優(yōu)選,所述②汽蒸工段中,脫水后的物料輸送至汽蒸倉汽蒸時加入0.12%的再濕劑;所述③第一擠壓浸漬化學(xué)機械處理段中的第一化學(xué)浸漬藥劑為1.2%的H2SO4;所述④第二擠壓浸漬化學(xué)機械處理段中的第二化學(xué)浸漬藥劑包含2%的NaOH、4%的H2O2、1.5%的Na2SiO3和0.35%的DTPA。作為另一種優(yōu)選方案的另一種更進一步優(yōu)選,所述②汽蒸工段中,脫水后的物料輸送至汽蒸倉汽蒸時加入0.15%的再濕劑;所述③第一擠壓浸漬化學(xué)機械處理段中的第一化學(xué)浸漬藥劑為1.5%的H2SO4;所述④第二擠壓浸漬化學(xué)機械處理段中的第二化學(xué)浸漬藥劑包含3%的NaOH、6%的H2O2、2%的Na2SiO3和0.5%的EDTA。有益效果:本發(fā)明提供的化學(xué)機械制漿系統(tǒng)和制漿方法中,采用碎料機靠機械剪將廢紙剪切成紙片,然后利用雙螺桿浸漬機作為纖維機械解離和化學(xué)預(yù)處理設(shè)備,靠雙螺桿浸漬機螺桿的機械揉搓作用,在濕強廢紙片外形尺寸逐步變小和分步逐漸解離纖維的同時,進行化學(xué)處理,實現(xiàn)化學(xué)助劑與漿料的高濃混合和均質(zhì)化浸漬,提高化學(xué)反應(yīng)效率,降低化學(xué)品消耗20~30%。更進一步的,本發(fā)明提供的化學(xué)機械制漿系統(tǒng),可采用轉(zhuǎn)鼓式洗滌機通過下進水口進水形成上行水流,有效減少比重較輕的物料向下沉淀,僅使得比重較重的重雜質(zhì)如金屬物、石子等沉入沉渣管,可以有效的清除物料中的重雜質(zhì),且極大的減少了物料在洗滌分離雜質(zhì)的過程中易造成的損耗。更進一步的,本發(fā)明提供的化學(xué)機械制漿系統(tǒng),可采用均勻落料式反應(yīng)倉以通過均勻落料環(huán)實現(xiàn)均勻下料,有利于下游制漿設(shè)備穩(wěn)定生產(chǎn),負載波動幅度由原來的一倍以上降低至10~15%之內(nèi),降低了設(shè)備故障率,提高了設(shè)備可靠性,穩(wěn)定了漿料質(zhì)量;更進一步的,本發(fā)明提供的化學(xué)機械制漿系統(tǒng),可采用旋轉(zhuǎn)撥料式汽蒸倉以通過旋轉(zhuǎn)撥料裝置將物料連續(xù)分層地撥入排料裝置,通過防滑條防止物料打滑旋轉(zhuǎn),消除了因物料受熱體積膨脹導(dǎo)致的架橋現(xiàn)象,提高了倉容利用率,物料得到了充足汽蒸軟化,有效提升了后序化學(xué)擠壓浸漬效果和水溶性有色及樹脂物質(zhì)的脫除率,降低化學(xué)品消耗。更進一步的,本發(fā)明提供的化學(xué)機械制漿方法中,可在兩段串聯(lián)的擠壓浸漬化學(xué)機械處理段,先對濕強廢紙經(jīng)過酸處理控制PH值范圍為4.5~6,再對濕強廢紙經(jīng)過氧化劑處理控制PH值范圍為11.5~12.5,避開濕強廢紙中濕強劑性質(zhì)最穩(wěn)定的PH值范圍,并通過雙PH值處理的方法,首先在酸性條件下氧化廢紙中的濕強劑,然后在堿性條件下進一步促進水解,更有效的破壞濕強劑分子間以及濕強劑與紙漿纖維之間的化學(xué)結(jié)合,獲得濕強紙纖維96%甚至98%以上的高解離率或完全解離,有效提高了纖維解離率和再制漿得率。整體而言,本發(fā)明提供的化學(xué)機械制漿系統(tǒng)和制漿方法依靠機械強力作用和化學(xué)處理作用在低(電)能耗下,不降低原紙漿強度甚至有所提高的同時,實現(xiàn)濕強廢紙纖維解離再制漿;采用環(huán)保型氧化劑在漿料濃度25~35%下再制漿,降低噸漿水耗,節(jié)約用水,實現(xiàn)無污染環(huán)保制漿;并可針對不同的濕強廢紙?zhí)匦?,采用不同的氧化劑、不同的工藝條件,更有效的破壞濕強劑分子間以及濕強劑與紙漿纖維之間的化學(xué)結(jié)合,實現(xiàn)含漂白化學(xué)漿、化學(xué)機械漿或未漂漿的各類濕強紙的再制漿回收利用。整體解決了濕強廢紙回收制漿纖維離解率低、紙漿強度大幅下降的問題,且可實現(xiàn)連續(xù)、規(guī)?;?、低水耗、低能耗的無污染環(huán)保制漿。附圖說明圖1是濕強廢紙回收再利用化學(xué)機械制漿系統(tǒng)的整體結(jié)構(gòu)示意圖;圖2是轉(zhuǎn)鼓式洗滌機的結(jié)構(gòu)示意圖;圖3是圖2的左視圖;圖4是斜螺旋脫水機的結(jié)構(gòu)示意圖;圖5是旋轉(zhuǎn)撥料式汽蒸倉的結(jié)構(gòu)示意圖;圖6是圖5的俯視圖;圖7是圖5的左視圖;圖8是均勻落料式反應(yīng)倉的結(jié)構(gòu)示意圖;圖9是均勻落料式反應(yīng)倉中均勻落料環(huán)的結(jié)構(gòu)示意圖;圖10是均勻落料式反應(yīng)倉中的均勻落料裝置配置兩根排料螺旋的結(jié)構(gòu)示意圖。具體實施方式下面結(jié)合附圖、系統(tǒng)的實施方式和方法的實施例對本發(fā)明作更進一步的說明。如圖1所示,本濕強廢紙回收再利用化學(xué)機械制漿系統(tǒng),按物料工序運行方向,包括第一輸送設(shè)備1、碎料機2、第二輸送設(shè)備3、轉(zhuǎn)鼓式洗滌機4、料片泵5、斜螺旋脫水機6、汽蒸倉7、第三螺旋輸送機8、第一雙螺桿浸漬機9、第一反應(yīng)倉10、第四螺旋輸送機11、第二雙螺桿浸漬機12、第二反應(yīng)倉13、第五螺旋輸送機14、消潛漿池15、漿泵16、纖維分離機17、凈化篩選濃縮裝置18、貯漿裝置19;所述第一輸送設(shè)備1的出料口正對碎料機2的進料口,所述碎料機2的出料口正對第二輸送設(shè)備3的進料口,所述第二輸送設(shè)備3的出料口正對轉(zhuǎn)鼓式洗滌機4的進料口,所述轉(zhuǎn)鼓式洗滌機4的出料口下方設(shè)有容器(圖中未示出),所述料片泵5設(shè)于該容器與斜螺旋脫水機6之間,料片泵5的輸入端設(shè)置在該容器的容積腔內(nèi),料片泵5的輸出端與斜螺旋脫水機6的進料口連通,所述斜螺旋脫水機6的出料口與汽蒸倉7的進料口連通,所述汽蒸倉7的出料口與第三螺旋輸送機8進料口連通,所述第三螺旋輸送機8的出料口與第一雙螺桿浸漬機9的進料口連通,所述第一雙螺桿浸漬機9的出料口與第一反應(yīng)倉10的進料口連通,所述第一反應(yīng)倉10的出料口與第四螺旋輸送機11的進料口連通,所述第四螺旋輸送機11的出料口與第二雙螺桿浸漬機12的進料口連通,所述第二雙螺桿浸漬機12的出料口與第二反應(yīng)倉13的進料口連通,所述第二反應(yīng)倉13的出料口與第五螺旋輸送機14的進料口連通,所述第五螺旋輸送機14的出料口連通至消潛漿池15,所述漿泵16設(shè)于消潛漿池15與纖維分離機17之間,漿泵16的輸入端與消潛漿池15的容積腔連通,漿泵16的輸出端與纖維分離機17的進料口連通,所述纖維分離機17的出料口與凈化篩選濃縮裝置18的進料口連通,所述凈化篩選濃縮裝置18的出料口與貯漿裝置19相連。所述貯漿裝置19中貯漿備抄。具體的,所述凈化篩選濃縮裝置18可包括順序連接的壓力篩20、除渣器21和濃縮設(shè)備22,所述纖維分離機17的出料口與壓力篩20的進料口連通,所述壓力篩20的出料口與除渣器21的進料口連通,所述除渣器21的出料口與濃縮設(shè)備22的進料口連通,所述濃縮設(shè)備22的出料口與貯漿裝置19相連。其中的碎料機2為撕碎機或水力碎漿機,第一輸送設(shè)備1和第二輸送設(shè)備3為鏈板輸送機或皮帶輸送機。所述撕碎機的破碎機械結(jié)構(gòu)由固定于機殼上的定刀和兩根相對逆向旋轉(zhuǎn)的刀輥組成,物料進入撕碎機后,依靠兩刀輥之間的若干刀盤以及刀盤與定刀之間組成的剪切副,將物料剪切破碎成一定尺寸的料片,刀輥由中間為花鍵或六方形截面的軸和串裝于軸上的刀盤構(gòu)成,可以通過調(diào)整刀盤厚度來調(diào)整剪切后物料的尺寸;撕碎機可以根據(jù)需要配置單刀輥結(jié)構(gòu),也可以采用雙刀輥或多刀輥結(jié)構(gòu)。其中的轉(zhuǎn)鼓式洗滌機4可選用本領(lǐng)域常規(guī)轉(zhuǎn)鼓式洗滌機,此處給出一種具體實現(xiàn)形式,如圖2和圖3所示,該轉(zhuǎn)鼓式洗滌機包括機體,轉(zhuǎn)鼓402、轉(zhuǎn)鼓驅(qū)動裝置404;所述機體一側(cè)上部設(shè)有進料口401,其另一側(cè)設(shè)有出料口403,機體內(nèi)設(shè)有洗滌腔,所述轉(zhuǎn)鼓402設(shè)于洗滌腔內(nèi)并受轉(zhuǎn)鼓驅(qū)動裝置404驅(qū)動旋轉(zhuǎn);所述轉(zhuǎn)鼓402位置下方的機體底部形狀呈倒錐臺形;所述機體鄰近進料口401的一端設(shè)有上進水口406,所述機體底部的倒錐臺形的下錐臺口的下方設(shè)有與下錐臺口連通的管體,管體側(cè)壁設(shè)有下進水口407;所述管體的下方設(shè)有沉渣管405,所述沉渣管405的上端設(shè)有上卸渣閥408,下端設(shè)有下卸渣閥409。工作時,經(jīng)碎料機破解成料片的物料進入轉(zhuǎn)鼓式洗滌機的進料口401,洗滌水由上進水口406和下進水口407加入,轉(zhuǎn)鼓402由轉(zhuǎn)鼓驅(qū)動裝置404驅(qū)動并連續(xù)緩慢旋轉(zhuǎn),料片進入洗滌區(qū)后,通過轉(zhuǎn)鼓402的旋轉(zhuǎn)連續(xù)將洗后料片通過出料口403撥出,重雜質(zhì)如金屬物、石子等沉入沉渣管405;正常工作時上卸渣閥408打開、下卸渣閥409關(guān)閉,以利于渣料沉淀入沉渣管405,當需要排渣時,上卸渣閥408關(guān)閉、下卸渣閥409打開,排出沉渣,然后上卸渣閥408再次打開,下卸渣閥409再次關(guān)閉,上、下卸渣閥交替關(guān)閉和打開實現(xiàn)沉渣,沉渣排出后進入固廢處理系統(tǒng)。在該結(jié)構(gòu)中,因為下進水口407進水會形成上行水流,上行水流的推力可以有效減少比重較輕的物料向下沉淀,但比重較重的重雜質(zhì)如金屬物、石子等依然會沉入沉渣管,可以有效的清除物料中的重雜質(zhì),且極大的減少了物料在洗滌分離雜質(zhì)的過程中易造成的損耗。其中的斜螺旋脫水機6可選用本領(lǐng)域常規(guī)斜螺旋脫水機,此處給出一種具體實現(xiàn)形式,如圖4所示,該斜螺旋脫水機包括螺旋外殼602,螺旋外殼602內(nèi)設(shè)有受螺旋驅(qū)動裝置604驅(qū)動旋轉(zhuǎn)的螺旋603,所述螺旋外殼602及其內(nèi)部的螺旋603沿物料輸送方向由低到高傾斜設(shè)置,所述螺旋外殼602的兩端分別為外殼斜下端和外殼斜上端,所述外殼位于外殼斜下端的上部設(shè)有進料口601,位于外殼斜下端的下部設(shè)有排水口607,位于外殼斜上端的下部設(shè)有出料口605,所述螺旋外殼602內(nèi)位于螺旋603的下部平行設(shè)有濾網(wǎng)板606。工作時,經(jīng)轉(zhuǎn)鼓式洗滌機洗滌后的物料和水由料片泵泵送至斜螺旋脫水機的進料口601,螺旋603由驅(qū)動裝置604驅(qū)動旋轉(zhuǎn),物料被螺旋603提升輸送至出料口605排出。洗滌水和殘余雜質(zhì)通過濾網(wǎng)板606的網(wǎng)孔排出并經(jīng)排水口607排入水處理系統(tǒng),經(jīng)沉淀凈化后循環(huán)回用于洗滌過程。其中的汽蒸倉7可選用本領(lǐng)域常規(guī)汽蒸倉如振動式卸料汽蒸倉,優(yōu)選旋轉(zhuǎn)撥料式汽蒸倉。如圖5、圖6、圖7所示,所述旋轉(zhuǎn)撥料式汽蒸倉包括倉體702、旋轉(zhuǎn)撥料裝置、排料裝置,倉體702內(nèi)設(shè)有蒸腔,倉體702上部設(shè)有進料口701;該旋轉(zhuǎn)撥料裝置包括撥料電機712、中心軸713和設(shè)在倉體底部的撥料盤,所述撥料盤包括底盤714和可在底盤上旋轉(zhuǎn)的撥料片715;底盤714中心設(shè)有通孔;中心軸713穿過該通孔一端與撥料片715固定連接,另一端通過聯(lián)軸器與撥料電機712傳動連接;該排料裝置包括殼體703和排料電機704,該排料電機704為可調(diào)速齒輪減速電機,殼體703內(nèi)設(shè)有排料螺旋,排料螺旋包括螺旋軸705和設(shè)置在螺旋軸上的螺旋葉片706;所述排料螺旋的螺旋軸705由設(shè)在兩側(cè)的第一軸承座707和第二軸承座708以及軸承支撐,兩端分別設(shè)有第一密封函709和第二密封函710,該螺旋軸705與設(shè)在殼體一側(cè)的排料電機704傳動連接,殼體703另一側(cè)下部設(shè)有出料口711,所述螺旋軸上設(shè)有的螺旋葉片706為沿輸送方向螺距逐漸由小變大的變螺距螺旋葉片;該排料裝置位于撥料盤下方,撥料盤的底盤714與排料裝置的殼體703對接的部位設(shè)有落料開口716,該落料開口716位于底盤714的偏心位置上,且位于撥料片715旋轉(zhuǎn)覆蓋的底盤714的區(qū)域內(nèi);上述撥料盤的底盤714為圓形底盤,排料裝置的殼體703為圓筒形,該落料開口716的邊為圓形底盤與排料裝置殼體的對接線,即為由與圓形底盤同圓心的兩段圓弧和兩條弦構(gòu)成四條邊的落料開口;所述蒸腔內(nèi)壁位于撥料盤的上部周向均布若干豎條形防滑條726;倉體702為圓臺形,當然也可以是圓柱形;在倉體中部設(shè)有觀察口718;在倉體702底部周向均布4個蒸汽進管,分別為第一蒸汽進管719、第二蒸汽進管720、第三蒸汽進管721、第四蒸汽進管722;所述倉體702上部設(shè)有蒸汽回流口和蒸汽排放口723;所述排料裝置殼體703上鄰近出料口711的部位設(shè)有蒸汽輸出口724;本汽蒸倉還包括回氣管725,所述回氣管725的一端管口與所述排料裝置的蒸汽輸出口724對接,另一端與所述倉體702上部的蒸汽回流口對接。工作時,將經(jīng)斜螺旋脫水機脫水后的物料自進料口701落入倉體702蒸腔內(nèi)。蒸汽通過外部蒸汽管道分別進入蒸汽進管,進而進入蒸腔底部,一部分向上蒸發(fā)汽蒸軟化物料,多余蒸汽從蒸汽排放口723輸出;另一部分向下經(jīng)落料開口716進入排料裝置,然后從排料裝置的蒸汽輸出口724輸出,通過回氣管725經(jīng)所述倉體上部的蒸汽回流口回流至倉體蒸腔內(nèi),受物料自然堆角影響,倉體蒸腔上部呈無料狀態(tài),可使蒸汽順利回流至蒸腔內(nèi)汽蒸軟化物料,多余蒸汽經(jīng)蒸汽排放口723回收利用或排放;當汽蒸倉倉體702內(nèi)物料達到一定料位并滿足充足停留汽蒸時間后,啟動旋轉(zhuǎn)撥料裝置的撥料電機712和排料裝置的排料電機704,撥料電機712通過中心軸713驅(qū)動撥料片715旋轉(zhuǎn),排料電機704驅(qū)動螺旋軸705旋轉(zhuǎn);因排料螺旋采用可調(diào)速齒輪減速電機驅(qū)動,此處可通過預(yù)先設(shè)置排料螺旋轉(zhuǎn)速達到計量輸送目的;撥料片715旋轉(zhuǎn)過程中,連續(xù)將物料分層并按先進先出原則通過落料開口716撥入排料裝置,物料在倉體702的蒸腔內(nèi)呈塞式垂直下落,防滑條726有效防止物料隨撥料裝置打滑旋轉(zhuǎn);此時位于落料開口716下方的螺旋軸705的螺槽內(nèi)物料呈充滿狀態(tài),在輸送過程中物料沿螺旋軸輸送方向由充滿狀態(tài)逐漸過渡到松散狀態(tài),并最終由排料裝置的排料螺旋計量送出,進入下游設(shè)備。其中的雙螺桿浸漬機,如在2012年9月11日提交的申請?zhí)枮?01210332112.8、公開號為CN102864669A的名為“一種雙螺桿浸漬機”的中國專利申請中所描述的,其全部內(nèi)容包含附圖通過引用結(jié)合于此。也可以如2012年9月11日提交的授權(quán)號為ZL201220458032.2的名為“一種雙螺桿浸漬機”的中國專利申請中所描述的,其全部內(nèi)容包含附圖通過引用結(jié)合于此。該雙螺桿浸漬機包括機架以及設(shè)置在機架上的電機、齒輪變速箱、可移式鼓形齒聯(lián)軸器、機筒和兩根螺桿,所述電機通過齒輪變速箱以及可移式鼓形齒聯(lián)軸器與兩根螺桿傳動連接,所述兩根螺桿互相平行且可轉(zhuǎn)動地設(shè)置在所述機筒內(nèi),所述機筒一端設(shè)有進料口,另一端設(shè)有出料口;所述螺桿沿輸送方向依次套設(shè)有第一輸送螺旋套、第一擠壓螺旋套、第二輸送螺旋套、第二擠壓螺旋套、第三輸送螺旋套以及第三擠壓螺旋套,所述第一、第二、第三輸送螺旋套的螺旋方向與所述第一、第二、第三擠壓螺旋套的螺旋方向相反,所述第一輸送螺旋套的螺距沿輸送方向逐漸減??;每個輸送螺旋套與擠壓螺旋套之間都設(shè)有均化環(huán);所述機筒上部設(shè)有與第三輸送螺旋套對應(yīng)的液體加入孔,所述機筒下部設(shè)有與第一、第二輸送螺旋套的輸出端對應(yīng)的廢液孔,廢液孔處設(shè)有過濾蓖,即排水濾網(wǎng);所述第一、第二、第三擠壓螺旋套的螺棱上開有豁槽;所述機筒為上下剖分式機筒,包括對稱連接的固定設(shè)置在機架上的上半機筒和可啟閉的連接在機架上的下半機筒。工作時,物料通過兩根螺桿向出料口方向推進,輸送過程中由于第一輸送螺旋套的螺距逐漸減小,物料被逐漸壓縮并充滿螺槽;進入逆向擠壓區(qū)擠壓螺旋套前即第一均化環(huán)處,擠壓力達到最大,物料被強烈壓縮;在正向擠壓力的作用下,物料被強制通過第一擠壓螺旋套螺棱上的豁槽,受擠壓、搓揉的物料幾何尺寸變小并被壓潰,同樣自第二輸送螺旋套以及第二擠壓螺旋套再次擠壓均化后,物料依次通過了兩段擠壓揉搓段并被揉搓解離成絲團狀、束狀纖維狀和單根纖維狀;同時,物料所含水分和水溶物被擠出并通過機筒濾蓖和濾液排出孔排出并收集進入水處理系統(tǒng);在第二擠壓螺旋套的正向出料末端物料進入混合段前,通過機筒液體加入孔即加藥孔由計量加藥裝置計量加入化學(xué)浸漬藥劑和稀釋水,實現(xiàn)藥劑與纖維的高濃混合,調(diào)整漿濃至25~35%,再經(jīng)第三擠壓螺旋套高濃混合后排出。其中的第一反應(yīng)倉10和第二反應(yīng)倉13可選用本領(lǐng)域常規(guī)反應(yīng)倉,優(yōu)選均勻落料式反應(yīng)倉。如圖8所示,所述均勻落料式反應(yīng)倉包括倉體1010和均勻落料裝置,倉體1010為梯形方倉,倉體頂部設(shè)有反應(yīng)倉的進料口1020,倉體1010底部設(shè)有落料口;該均勻落料裝置包括殼體,殼體內(nèi)設(shè)有排料螺旋,所述排料螺旋包括螺旋軸1040和設(shè)置在螺旋軸上的螺旋葉片1050;該排料螺旋的螺旋軸1040與設(shè)在殼體一側(cè)的電機傳動連接,殼體另一側(cè)下部設(shè)有反應(yīng)倉的出料口1030,本均勻落料裝置的進料口即倉體1010底部的落料口;所述螺旋軸1040位于出料口1030上方的部位固定設(shè)有均勻落料環(huán)1060;均勻落料環(huán)1060的結(jié)構(gòu)示意圖如圖9所示,包括管體1061,管體1061的外壁固定連接有多線螺紋葉片1062;所述均勻落料環(huán)的管體1061通過焊接或螺栓緊固連接在所述螺旋軸1040上,均勻落料環(huán)1060與螺旋軸1040的中心軸線一致;所述多線螺紋葉片1062的旋向與所述排料螺旋上的螺旋葉片1050旋向一致。當然該反應(yīng)倉的均勻落料裝置中也可以包括兩根這樣的獨立驅(qū)動的排料螺旋,如圖10所示,每根排料螺旋均包括螺旋軸和螺旋葉片,所述螺旋葉片為沿輸送方向螺距逐漸由小變大的變螺距螺旋葉片;每根排料螺旋的螺旋軸位于出料口上方的部位均固定設(shè)有均勻落料環(huán),每個均勻落料環(huán)與其對應(yīng)的螺旋軸中心軸線一致,每個均勻落料環(huán)上的多線螺紋葉片與其對應(yīng)的排料螺旋上的螺旋葉片旋向一致;這兩根排料螺旋的螺旋軸反向旋轉(zhuǎn)。在這種配置下,物料在鄰近排料螺旋上的兩個反向旋轉(zhuǎn)尤其是反內(nèi)向旋轉(zhuǎn)的螺旋葉片的共同推動下,更加均衡的往前推移,然后經(jīng)均勻落料環(huán)的攪拌打散,連續(xù)均勻得從出料口下落至下游設(shè)備;排料螺旋上螺旋葉片的變螺距設(shè)計可以使得物料在輸送過程中沿螺旋軸輸送方向由充滿狀態(tài)逐漸過渡到松散狀態(tài),提高效率,降低螺旋運轉(zhuǎn)負載和磨損。工作時,漿料由上游輸送設(shè)備自反應(yīng)倉頂部的反應(yīng)倉入料口1020連續(xù)送入反應(yīng)倉倉體1010內(nèi),滿足工藝設(shè)計停留時間要求后,倉體內(nèi)物料充滿率為70~80%,此時排料螺旋填充物料呈充滿壓實狀態(tài),漿料在排料螺旋螺旋葉片1050之間的螺旋槽內(nèi)呈充滿塊團狀;當位于反應(yīng)倉底部的排料螺旋啟動并旋轉(zhuǎn)時,螺旋槽內(nèi)呈充滿塊團狀的物料被連續(xù)輸向排料螺旋接近出料口1030的一端;漿料接近排料螺旋尾端在下落前先經(jīng)過均勻落料環(huán)1060,經(jīng)均勻落料環(huán)1060上的多線螺紋葉片1062攪拌和打散后,連續(xù)均勻下落至下游設(shè)備。其中的第一反應(yīng)倉10和第二反應(yīng)倉13也可以與上述汽蒸倉7結(jié)構(gòu)組成相同,因為經(jīng)雙螺桿浸漬機擠壓揉搓的物料,其摩擦熱溫度已滿足反應(yīng)倉反應(yīng)所需,所以當反應(yīng)倉使用與汽蒸倉一樣的結(jié)構(gòu)時,可以不通過蒸汽管注入蒸汽加熱,當然在需要的情況下,也可以選用蒸汽加熱的方式。使用上述濕強廢紙回收再利用化學(xué)機械制漿系統(tǒng)的濕強廢紙回收再利用化學(xué)機械制漿方法,該方法中各藥劑組分的百分量是占絕干原料重量的百分量,其具體實施方式為:實施例1:漂白含濕強劑的紙機抄造損紙和邊角料再制漿回收損紙和邊角料由鏈板式輸送機輸送至水力碎漿機碎解成紙片后,輸送至轉(zhuǎn)鼓式洗滌機4加水調(diào)整濃度為3%進行洗滌除渣后,由料片泵5泵送至斜螺旋脫水機6脫水濃縮,然后輸送至汽蒸倉7汽蒸15分鐘,蒸汽壓力0.3MPa,按照占絕干原料的重量百分比,進入汽蒸倉時在進料口以霧狀噴入0.1%的再濕劑;蒸后料片由第三螺旋輸送機8送入第一雙螺桿浸漬機9擠壓搓揉成絲團狀并濃縮至35%濃度左右,其后按照占絕干原料的重量百分比,由計量泵加入1%的液體NaOH和適量清水,物料和化學(xué)浸漬藥劑在第一雙螺桿浸漬機9機內(nèi)高濃混合后,調(diào)整漿濃至25%左右、PH值控制在11.5左右送入第一反應(yīng)倉10,反應(yīng)溫度控制在80℃左右,停留時間35分鐘;反應(yīng)結(jié)束后由第四螺旋輸送機11送至第二雙螺桿浸漬機12擠壓搓揉解離成束狀纖維和單根纖維混合物狀并濃縮至35%濃度左右,其后按照占絕干原料的重量百分比,由計量泵加入1%的NaOH、2%的H2O2、1%的Na2SiO3、0.2%的螯合劑DTPA和適量清水,物料和化學(xué)浸漬藥劑在第二雙螺桿浸漬機12機內(nèi)高濃混合后,調(diào)整漿濃至25%左右、PH值控制在11.5左右送入第二高濃反應(yīng)倉13,反應(yīng)溫度控制在80℃左右,停留時間35分鐘;反應(yīng)結(jié)束后由第五螺旋輸送機14輸送至消潛漿池15。漿料在消潛漿池15內(nèi),加水稀釋漿濃至3%,溫度60℃,消除纖維在擠壓揉搓過程中產(chǎn)生的內(nèi)應(yīng)力,使球團狀纖維分散并充分伸展開,然后,通過漿泵16泵送至纖維分離機17進行再疏解,并分離清除輕、重雜質(zhì)和粗大廢料和濕強紙纖維,將分離得到的濕強紙纖維經(jīng)壓力篩20篩選,除渣器21凈化,濃縮設(shè)備22濃縮后存貯在貯漿裝置19中備抄。上述過程中,轉(zhuǎn)鼓式洗滌機洗滌后得到的沉渣進入固廢處理系統(tǒng),通過斜螺旋脫水機的濾網(wǎng)板網(wǎng)孔排出的殘余雜質(zhì)和水進入水處理系統(tǒng),經(jīng)沉淀凈化后循環(huán)回用于洗滌過程。本實施例中,根據(jù)損紙和邊角料的潔凈度,也可以省略洗滌步驟。實施例2:未漂白含濕強劑的紙機抄造損紙和邊角料再制漿回收損紙和邊角料由鏈板式輸送機輸送至水力碎漿機碎解成紙片,輸送至轉(zhuǎn)鼓式洗滌機4加水調(diào)整濃度為4%進行洗滌除渣后,由料片泵5泵送至斜螺旋脫水機6脫水濃縮,然后輸送至汽蒸倉7汽蒸25分鐘,蒸汽壓力0.45MPa,按照占絕干原料的重量百分比,輸送至汽蒸倉時在進料口以霧狀噴入0.12%的再濕劑;蒸后料片由第三螺旋輸送機8送入第一雙螺桿浸漬機9擠壓搓揉成絲團狀并濃縮至40%濃度左右,其后按照占絕干原料的重量百分比,由計量泵加入1.2%的H2SO4和適量清水,物料和化學(xué)浸漬藥劑在第一雙螺桿浸漬機9機內(nèi)高濃混合后,調(diào)整漿濃至30%左右、PH值控制在6左右送入第一反應(yīng)倉10,反應(yīng)溫度控制在90℃左右,停留時間45分鐘;反應(yīng)結(jié)束后由第四螺旋輸送機11送至第二雙螺桿浸漬機12擠壓搓揉解離成束狀纖維和單根纖維混合物狀并濃縮至40%濃度左右,其后按照占絕干原料的重量百分比,由計量泵加入2%的NaOH、4%的H2O2、1.5%的Na2SiO3和0.35%的DTPA和適量清水,物料和化學(xué)浸漬藥劑在第二雙螺桿浸漬機12機內(nèi)高濃混合后,調(diào)整漿濃至30%左右、PH值控制在12左右送入第二高濃反應(yīng)倉13,反應(yīng)溫度控制在90℃左右,停留時間45分鐘;反應(yīng)結(jié)束后由第五螺旋輸送機14輸送至消潛漿池15。漿料在消潛漿池15內(nèi),加水稀釋漿濃至4%,溫度65℃,消除纖維在擠壓揉搓過程中產(chǎn)生的內(nèi)應(yīng)力,使球團狀纖維分散并充分伸展開,然后,通過漿泵16泵送至纖維分離機17進行再疏解,并分離清除輕、重雜質(zhì)和粗大廢料和濕強紙纖維,將分離得到的濕強紙纖維經(jīng)壓力篩20篩選,除渣器21凈化,濃縮設(shè)備22濃縮后存貯在貯漿裝置19中備抄。上述過程中,轉(zhuǎn)鼓式洗滌機洗滌后得到的沉渣進入固廢處理系統(tǒng),通過斜螺旋脫水機的濾網(wǎng)板網(wǎng)孔排出的殘余雜質(zhì)和水進入水處理系統(tǒng),經(jīng)沉淀凈化后循環(huán)回用于洗滌過程。本實施例中,根據(jù)損紙和邊角料的潔凈度,也可以省略洗滌步驟。實施例3:未漂白含濕強劑的廢紙和廢紙箱板再制漿回收廢紙和廢紙箱板由鏈板式輸送機輸送至撕碎機碎解成紙片,輸送至轉(zhuǎn)鼓式洗滌機4加水調(diào)整濃度為5%進行洗滌除渣后,由料片泵5泵送至斜螺旋脫水機6脫水濃縮,然后輸送至汽蒸倉7汽蒸30分鐘,蒸汽壓力0.6MPa,按照占絕干原料的重量百分比,輸送至汽蒸倉時在進料口以霧狀噴入0.15%的再濕劑;蒸后料片由第三螺旋輸送機8送入第一雙螺桿浸漬機9擠壓搓揉成絲團狀并濃縮至45%濃度左右,其后按照占絕干原料的重量百分比,由計量泵加入1.5%的H2SO4和適量清水,物料和化學(xué)浸漬藥劑在第一雙螺桿浸漬機9機內(nèi)高濃混合后,調(diào)整漿濃至35%左右、PH值控制在4.5左右送入第一反應(yīng)倉10,反應(yīng)溫度控制在95℃左右,停留時間60分鐘;反應(yīng)結(jié)束后由第四螺旋輸送機11送至第二雙螺桿浸漬機12擠壓搓揉解離成束狀纖維和單根纖維混合物狀并濃縮至45%濃度左右,其后按照占絕干原料的重量百分比,由計量泵加入3%的NaOH、6%的H2O2、2%的Na2SiO3和0.5%的EDTA和適量清水,物料和化學(xué)浸漬藥劑在第二雙螺桿浸漬機12機內(nèi)高濃混合后,調(diào)整漿濃至35%左右、PH值控制在12.5左右送入第二高濃反應(yīng)倉13,反應(yīng)溫度控制在95℃左右,停留時間60分鐘;反應(yīng)結(jié)束后由第五螺旋輸送機14輸送至消潛漿池15。漿料在消潛漿池15內(nèi),加水稀釋漿濃至5%,溫度70℃,消除纖維在擠壓揉搓過程中產(chǎn)生的內(nèi)應(yīng)力,使球團狀纖維分散并充分伸展開,然后,通過漿泵16泵送至纖維分離機17進行再疏解,并分離清除輕、重雜質(zhì)和粗大廢料和濕強紙纖維,將分離得到的濕強紙纖維經(jīng)壓力篩20篩選,除渣器21凈化,濃縮設(shè)備22濃縮后存貯在貯漿裝置19中備抄。上述過程中,轉(zhuǎn)鼓式洗滌機洗滌后得到的沉渣進入固廢處理系統(tǒng),通過斜螺旋脫水機的濾網(wǎng)板網(wǎng)孔排出的殘余雜質(zhì)和水進入水處理系統(tǒng),經(jīng)沉淀凈化后循環(huán)回用于洗滌過程。對同等的PAE占比1.0%的原料分別進行上述實施例工藝條件和步驟下的實驗,結(jié)果顯示,在不降低原紙漿強度甚至有所提高的同時,均實現(xiàn)了濕強廢紙纖維解離再制漿;其中實施例1降低化學(xué)品消耗20%,負載波動幅度降低至15%以內(nèi),獲得的纖維解離率高達85%。實施例2降低化學(xué)品消耗25%,負載波動幅度降低至12%以內(nèi),獲得的纖維解離率高達96%。實施例3降低化學(xué)品消耗30%,負載波動幅度降低至12%以內(nèi),獲得的纖維解離率高達98%。以上實施例對本發(fā)明不構(gòu)成限定,相關(guān)工作人員在不偏離本發(fā)明技術(shù)思想的范圍內(nèi),所進行的多樣變化和修改,均落在本發(fā)明的保護范圍內(nèi)。