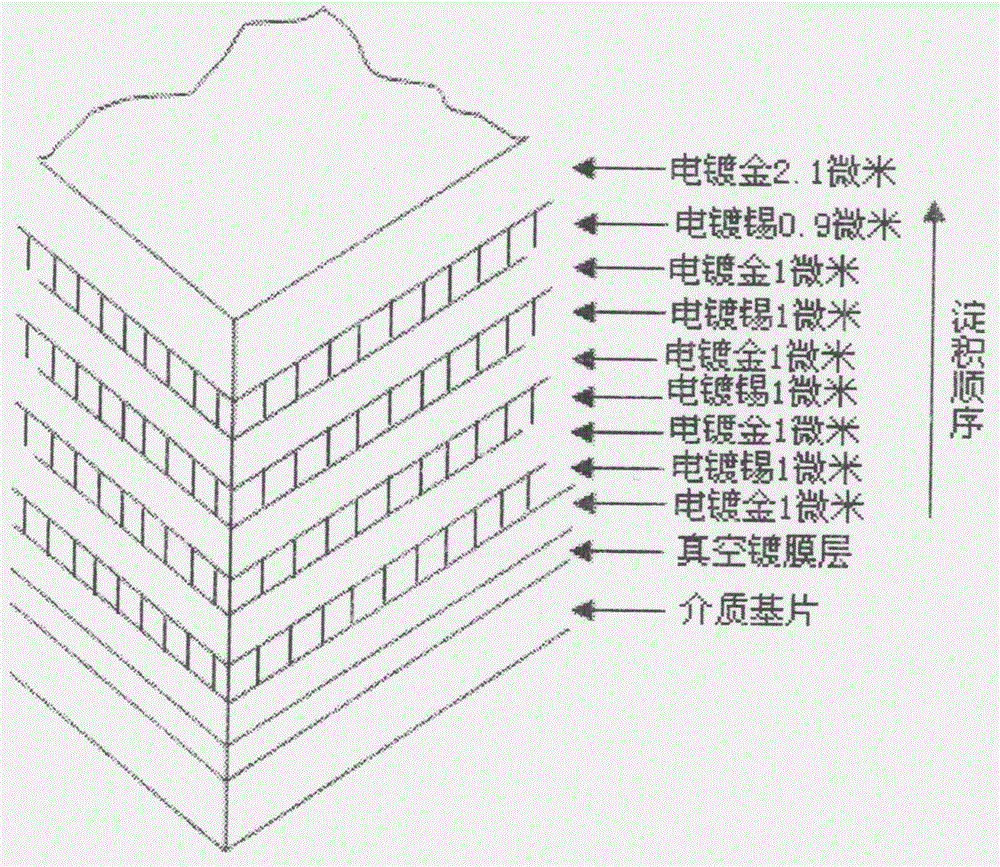
本發(fā)明涉及混合集成電路的釬焊組裝領(lǐng)域,特別涉及一種釬焊層預(yù)淀積方法。
背景技術(shù):當前,混合集成電路在高可靠性、高導(dǎo)熱和高導(dǎo)電方面的應(yīng)用日益廣泛,混合集成電路的釬焊組裝技術(shù)也越來越受到重視,混合集成電路的釬焊貼片質(zhì)量,直接影響到電路是否具有高可靠性、高導(dǎo)熱和高導(dǎo)電性能。混合集成電路的釬焊工藝,一種方法是焊膏涂覆到焊接位置,然后用貼片機將混合集成電路放置在焊膏上,通過加熱將焊膏熔焊,冷卻后實現(xiàn)釬焊連接;另一種方法是采用焊料片,將焊料片裁剪成跟混合集成電路的外形一樣大小或略小于混合集成電路外形,采用貼片機依次將焊料片和混合集成電路放置在焊接位置處,經(jīng)過加熱將混料片熔化,冷卻后實現(xiàn)釬焊連接。這些方法,都存在定位精度低、焊料或焊膏熔化程度均勻性差等問題。無論采用焊膏還是采用焊料片的釬焊連接,焊膏的涂覆量或焊料片的大小、形狀及厚度都無法精確控制,相同焊接參數(shù)下,焊膏或焊料熔化程度均勻性差,造成模塊或組件中各處的焊接質(zhì)量一致性差;焊膏或焊料片焊接,都存在焊接位置、焊膏或焊料片、被焊接混合集成電路片三者之間的位置對準問題,無論采用設(shè)備對準,還是采用手工對準,對準精度都無法滿足高精度、高密度焊接的需求,尤其在對準后轉(zhuǎn)入加熱過程時,會因為周轉(zhuǎn)或移動而造成三者之間的相對位移,最終造成因?qū)什痪_引起的廢品。因此,現(xiàn)有技術(shù)存在缺陷,需要改進。
技術(shù)實現(xiàn)要素:本發(fā)明所要解決的技術(shù)問題是針對現(xiàn)有技術(shù)的不足,提供了在混合集成電路的焊接面上預(yù)淀積一層與焊料成份相當?shù)暮噶蠈拥姆椒ǎ浜穸染鶆蛐詷O高,外形可與混合集成電路外形嚴格一致,焊接時僅考慮混合集成電路與焊接位置兩者間的對準即可,采用定位標記或?qū)蕣A具均可實現(xiàn)精確對準。本發(fā)明的技術(shù)方案如下:一種釬焊層預(yù)淀積方法,其中,包含以下步驟:A:真空濺射鍍膜種子層;B:以金層和錫層依次交替電鍍的方式沉積各層。所述的方法,其中,所述步驟A中,采用磁控濺射的方法,在電路介質(zhì)基片上依次淀積粘附層和電鍍種子層。所述的方法,其中,所述電路介質(zhì)基片為混合集成電路介質(zhì)基片。所述的方法,其中,所述步驟B中,金的密度為19.3g/cm3;錫的密度為7.31g/cm3。所述的方法,其中,所述步驟B中,金和錫的重量比是80.4∶19.6。所述的方法,其中,所述步驟B中,所述金層與錫層總厚度比為1.55∶1。所述的方法,其中,所述步驟B中,所述金層和錫層間隔電鍍,每層1微米。所述的方法,其中,所述步驟B中,所述金層和錫層共計電鍍9層。所述的方法,其中,所述步驟B中,所述第8層為錫層電鍍0.9微米。所述的方法,其中,所述步驟B中,所述第9層為金層電鍍2.1微米。采用上述方案,本發(fā)明不僅解決了現(xiàn)有技術(shù)存在的問題,而且明顯具有以下優(yōu)勢:1、針對采用釬焊的混合集成電路,對傳統(tǒng)焊接中采用焊膏或焊料片這一工藝方式進行改進,在電路焊接面(一般指背面)上淀積一層各成份重量比相當?shù)暮噶蠈樱附訒r可直接將電路放置在焊接位置上,經(jīng)過加熱實現(xiàn)焊接。這種技術(shù)不但可以減小焊料片成型的加工工作量,而且可以減少因焊接時焊接位置、焊料片、待焊接電路三者之間的位置偏移造成的廢品。2、相比現(xiàn)有焊料、焊膏的裁剪或涂覆技術(shù),采用本發(fā)明制作得到的焊料預(yù)淀積層,厚度均勻性極高,外形可與混合集成電路外形嚴格一致,焊接時僅考慮混合集成電路與焊接位置兩者間的對準即可,采用定位標記或?qū)蕣A具均可實現(xiàn)精確對準,對準精度高、焊料的融化程度均勻性好,焊接質(zhì)量大大提高。3、該發(fā)明借鑒了混合集成電路工藝技術(shù)中的電鍍技術(shù),在電路基片的種子層上預(yù)淀積一層焊料,替代采用裁剪焊料片或涂覆焊膏的裝配方法。4、該發(fā)明專利的技術(shù)創(chuàng)新主要體現(xiàn)在:利用電鍍技術(shù)預(yù)淀積焊料層,焊料層成份按重量比與焊料片的成份相當,經(jīng)過理論計算,最終體現(xiàn)在焊料層中各成份的厚度比例上;根據(jù)實際需要,預(yù)淀積層采用多層結(jié)構(gòu),每層厚度不超過1微米,以期各成份均勻性盡量接近焊料片的成份均勻性;預(yù)淀積層的最外層采用化學穩(wěn)定性好的金層,以防止電路的預(yù)淀積層在焊接前氧化,影響焊接效果。附圖說明圖1是淀積種子層結(jié)構(gòu)示意圖;圖2是依次電鍍沉積各層金錫層結(jié)構(gòu)示意圖。具體實施方式以下結(jié)合附圖和具體實施例,對本發(fā)明進行詳細說明。實施例一如圖1至圖2所示,本發(fā)明的技術(shù)方案,以混合集成電路中常用的金錫共晶焊料的電鍍預(yù)淀積為例,方案采用了電鍍多層金層和錫層的方案,以使金錫兩種成份的均勻性盡量接近合金成份的均勻性,方案中的實現(xiàn)流程如下:真空濺射鍍膜種子層:本方案中混合集成電路焊接面的粘附層和電鍍種子層的淀積,采用磁控濺射的方法,分別在混合集成電路介質(zhì)基片上依次淀積粘附層(例如TiW層)和電鍍種子層(例如Au層),如圖1所示;依次電鍍沉積各層金錫層:以預(yù)淀積10微米金錫焊料層為例,金錫共晶焊料中金和錫的重量比是80.4∶19.6,金的密度是19.3g/cm3,錫的密度是7.31g/cm3,因此金層與錫層總厚度比大約是1.55∶1。將金、錫電鍍成多層結(jié)構(gòu),金錫間隔電鍍,每層1微米,形成“三明治”結(jié)構(gòu)的預(yù)淀積焊料,本方案采用鍍膜層上先電鍍1微米金,然后是1微米錫,然后依次間隔電鍍,第四層錫只鍍0.9微米,最后以2.1微米金結(jié)束金錫焊料的淀積,如圖2所示。實施例二在上述實施例的基礎(chǔ)上,進一步,本發(fā)明一種釬焊層預(yù)淀積方法,其中,包含以下步驟:A:真空濺射鍍膜種子層;B:以金層和錫層依次交替電鍍的方式沉積各層。優(yōu)選的,所述步驟A中,采用磁控濺射的方法,在電路介質(zhì)基片上依次淀積粘附層和電鍍種子層,此為現(xiàn)有技術(shù)可實現(xiàn)的方案實施即可。優(yōu)選的,所述電路介質(zhì)基片為混合集成電路介質(zhì)基片。優(yōu)選的,所述步驟B中,金的密度為19.3g/cm3;錫的密度為7.31g/cm3,此處,金的密度也可以為20.3g/cm3;錫的密度為8.31g/cm3。優(yōu)選的,所述步驟B中,金和錫的重量比是80.4∶19.6,此處重量比也可為80.7∶19.3,可以實施本發(fā)明的同樣優(yōu)選效果。優(yōu)選的,所述步驟B中,所述金層與錫層總厚度比為1.55∶1,此處也可為1.6∶1.1。優(yōu)選的,所述步驟B中,所述金層和錫層間隔電鍍,每層1微米,也可為每層0.9微米、0.8微米或0.5微米。優(yōu)選的,所述步驟B中,所述金層和錫層共計電鍍9層或11層。優(yōu)選的,所述步驟B中,所述第8層或第10層為錫層電鍍0.9微米,或者說最后一層錫層為小于每層設(shè)定1微米為佳,如設(shè)定每層為0.9微米時,最后一層錫層設(shè)定0.8微米,如設(shè)定每層為0.8微米時,最后一層錫層設(shè)定0.7微米,如設(shè)定每層0.5微米時,設(shè)定最后一層錫層為0.4微米。優(yōu)選的,所述步驟B中,所述第9層或第11層為金層電鍍2.1微米,或者說,最后一層金層為每層設(shè)定值的2.1倍。如設(shè)定每層為0.9微米時,最后一層金層設(shè)定1.89微米,如設(shè)定每層為0.8微米時,最后一層金層設(shè)定1.68微米,如設(shè)定每層0.5微米時,設(shè)定最后一層金層為1.05微米。應(yīng)當理解的是,對本領(lǐng)域普通技術(shù)人員來說,可以根據(jù)上述說明加以改進或變換,而所有這些改進和變換都應(yīng)屬于本發(fā)明所附權(quán)利要求的保護范圍。