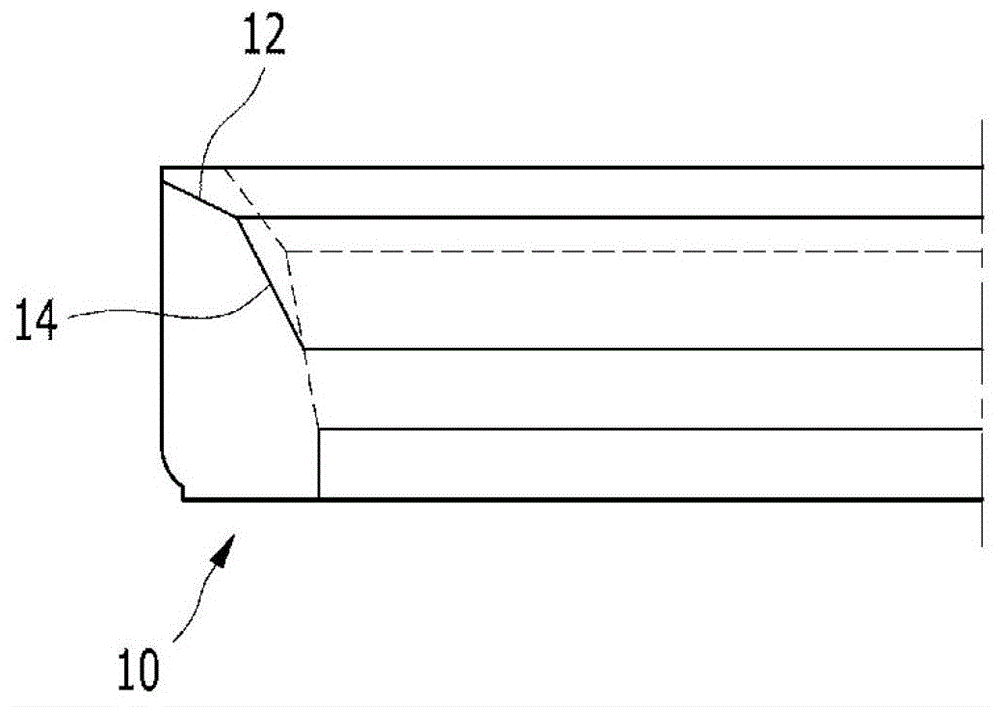
用于閥座的燒結(jié)合金和使用該合金制造排氣閥座的方法相關(guān)申請(qǐng)的交叉引用本申請(qǐng)要求2012年4月2日提交的韓國專利申請(qǐng)第10-2012-0033989號(hào)的優(yōu)先權(quán),該申請(qǐng)的全部內(nèi)容結(jié)合于此,以用于通過該引用的所有目的。技術(shù)領(lǐng)域本發(fā)明涉及閥座。更特別地,本發(fā)明涉及用于閥座的燒結(jié)合金以及利用該燒結(jié)合金制造閥座的方法,其中添加MnS用于改善機(jī)械加工性和回火性。
背景技術(shù):用于車輛的發(fā)動(dòng)機(jī)部件的閥座是一種接觸閥表面并且保持燃燒室中的氣密性的部件。所述閥座受到反復(fù)撞擊,所以需要將其制造為其不會(huì)由于受到反復(fù)撞擊而遭到破壞。用于閥座的傳統(tǒng)的耐磨燒結(jié)合金具有作為其主要成分的鐵(Fe),并且含有0.4-1.0重量%的碳(C)、0.1-1.0重量%的硅(Si)、0.5-2.0重量%的鉻(Cr)、6.0-10.0重量%的鉬(Mo)、6.0-15.0重量%的鈷(Co)和6.0-18.0重量%的鉛(Pb)。其制造過程如下。首先,將除鉛以外的所述成分的金屬粉末混合,并且其通過4-8噸/平方厘米的表面壓力形成。將其在減壓條件下,于750-800℃的范圍內(nèi)預(yù)燒結(jié)40分鐘,并且其通過7-10噸/平方厘米的表面壓力鍛造。然后,在氫氣氛中,于1110-1140℃的范圍進(jìn)行主燒結(jié),持續(xù)30-50分鐘,將樹脂浸漬以改善可加工性,并且進(jìn)行轉(zhuǎn)桶提金法處理(barrelprocess)以制造用于閥座的耐磨燒結(jié)合金。然而,通過成分和含量制造的用于閥座的燒結(jié)合金引起工具的過度磨耗和撕裂,并且可加工性不好。因此,需要改進(jìn)。公開于本發(fā)明背景部分的信息僅僅旨在增加對(duì)本發(fā)明的總體背景的理解,而不應(yīng)當(dāng)被視為承認(rèn)或以任何形式暗示該信息構(gòu)成已為本領(lǐng)域一般技術(shù)人員所公知的現(xiàn)有技術(shù)。
技術(shù)實(shí)現(xiàn)要素:本發(fā)明的各個(gè)方面提供了用于閥座的燒結(jié)合金和使用其的排氣閥座的制造方法,所述用于閥座的燒結(jié)合金具有的優(yōu)點(diǎn)在于通過由于加入MnS和進(jìn)行回火而形成Co-Mo-Cr-Si硬質(zhì)相來改善固體潤滑、閥座的粗糙度和表面條件。根據(jù)各個(gè)方面,本發(fā)明提供了用于閥座的燒結(jié)合金,并且將MnS添加到燒結(jié)合金中,所述燒結(jié)合金包括0.8-1.2重量%的C、2.0-4.5重量%的Ni、3.0-5.0重量%的Cr、16.0-20.0重量%的Mo、9.0-13.0重量%的Co,0.05-0.15重量%的V、0.2-0.8重量%的S、Fe和額外的不可避免的雜質(zhì)。根據(jù)本發(fā)明的各個(gè)方面,添加相對(duì)于100重量份的所述燒結(jié)合金的量為0.2-2.5重量份的MnS,MnS的粒徑小于12μm,并且MnS包括60-65重量%的Mn和35-40重量%的S。本發(fā)明的各個(gè)方面提供了一種方法,其包括以下步驟:混合MnS和用于閥座的合金粉末,所述用于閥座的合金粉末包括0.8-1.2重量%的C、2.0-4.5重量%的Ni、3.0-5.0重量%的Cr、16.0-20.0重量%的Mo、9.0-13.0重量%的Co,0.05-0.15重量%的V、0.2-0.8重量%的S、Fe和額外的不可避免的雜質(zhì);通過形成混合的物料來制備一次形狀;對(duì)一次成形的形狀進(jìn)行預(yù)燒結(jié);通過再次擠壓一次預(yù)燒結(jié)的形狀來制備二次形狀;對(duì)二次形狀進(jìn)行主燒結(jié);并且對(duì)主燒結(jié)的二次形狀進(jìn)行回火。根據(jù)本發(fā)明的各個(gè)方面,MnS相對(duì)于100重量份的合金粉末的量為從0.2至2.5重量份,回火溫度為從180℃至220℃,并且回火時(shí)間為從100分鐘到150分鐘。本發(fā)明的各個(gè)方面提供的方法包括以下步驟:使油滲透到回火的二次形狀中,并且對(duì)油滲透的二次形狀進(jìn)行加工和轉(zhuǎn)桶提金法處理(barreling)。閥座可以由上述燒結(jié)合金制造。通過由于加入MnS和進(jìn)行回火而形成Co-Mo-Cr-Si硬質(zhì)相可以改善固體潤滑、閥座的粗糙度和表面條件。此外,可以改善閥座的耐磨性而不增加咬合磨耗損失,并且防止撕裂現(xiàn)象。本發(fā)明的方法和裝置具有其他的特性和優(yōu)點(diǎn),這些特性和優(yōu)點(diǎn)從并入本文中的附圖和隨后的具體實(shí)施方式中將是顯而易見的,或者將在并入本文中的附圖和隨后的具體實(shí)施方式中進(jìn)行詳細(xì)陳述,這些附圖和具體實(shí)施方式共同用于解釋本發(fā)明的特定原理。附圖說明圖1A-1C是根據(jù)閥座的處理順序的本發(fā)明的各個(gè)方面的示意圖。圖2是根據(jù)本發(fā)明的示例性閥座表示粗糙度的曲線圖。圖3A-3D顯示出根據(jù)比較例和本發(fā)明的示例性實(shí)施例的示例性金屬結(jié)構(gòu)在腐蝕之前和腐蝕之后的照片。圖4是用于根據(jù)本發(fā)明的示例性閥座的制造過程的流程圖。具體實(shí)施方式現(xiàn)在將具體參考本發(fā)明的各個(gè)實(shí)施例,在附圖中和以下的描述中示出了這些實(shí)施例的實(shí)例。雖然本發(fā)明與示例性實(shí)施例相結(jié)合進(jìn)行描述,但是應(yīng)當(dāng)了解,本說明書并非旨在將本發(fā)明限制為那些示例性實(shí)施例。相反,本發(fā)明旨在不但覆蓋這些示例性實(shí)施例,而且覆蓋可以被包括在由所附權(quán)利要求所限定的本發(fā)明的精神和范圍之內(nèi)的各種替換、修改、等效形式以及其它實(shí)施例。根據(jù)本發(fā)明的各個(gè)方面,通過將MnS添加到燒結(jié)合金中來制造用于閥座的燒結(jié)合金,所述燒結(jié)合金包括0.8-1.2重量%的C、2.0-4.5重量%的Ni、3.0-5.0重量%的Cr、16.0-20.0重量%的Mo、9.0-13.0重量%的Co,0.05-0.15重量%的V、0.2-0.8重量%的S、Fe和額外的不可避免的雜質(zhì)。含有相對(duì)于100重量份的燒結(jié)合金的0.2-2.5重量份的MnS,并且采用含有MnS的燒結(jié)合金來制造閥座。在下文中解釋對(duì)于根據(jù)本發(fā)明的各種實(shí)施方案的數(shù)值的限制原 因。首先,將碳添加到鐵(Fe)中,以便根據(jù)強(qiáng)度和硬度的增量的耐磨性得到改善并且基體的強(qiáng)度得到增強(qiáng)。如果碳的量小于0.8重量%,則過量形成珠光體(pearlite)和鐵素體(ferrite),使得所述基體軟化并且強(qiáng)度和耐磨性較差,如果碳的量大于1.2重量%,則在形成珠光體之后保留的碳形成網(wǎng)絡(luò)結(jié)構(gòu)的滲碳體,使得所述基體強(qiáng)度減弱。因此,本發(fā)明的各種實(shí)施方案中碳的含量被限制在0.8-1.2重量%。當(dāng)將Ni添加并擴(kuò)散到基體金屬中時(shí),其改善了耐熱性和高溫特性。如果Ni的量小于2.0重量%,則上述效果略有顯示,而如果Ni的量大于4.5重量%,基體結(jié)構(gòu)被改變?yōu)轳R氏體(martensite)和富Ni奧氏體(Ni-richaustenite),從而結(jié)構(gòu)是不穩(wěn)定的,并且硬度過量增加進(jìn)而使機(jī)械加工性變差。因此,本發(fā)明的各種實(shí)施方案中Ni的含量被限制在2.0-4.5重量%。Cr與Co、Mo和Si成分一起形成Co-Mo-Cr-Si相(其為硬質(zhì)相),以至于耐磨性得到改善,并且Cr通過在基體中沉淀CrS來發(fā)揮潤滑劑的作用。如果Cr的含量小于3.0重量%,則略微形成所述Co-Mo-Cr-Si相(其為硬質(zhì)相)和所述CrS(其為固體潤滑劑),從而耐磨性較差。當(dāng)Cr的含量大于5.0重量%時(shí),過量形成Co-Mo-Cr-Si相和CrS,從而使金屬基體的強(qiáng)度減弱。因此,本發(fā)明的各種實(shí)施方案中Cr的含量被限制在3.0-5.0重量%。在Co-Mo-Cr-Si相中,成分的量分別為50重量%的Mo、9重量%的Cr、3重量%的Si和作為余量的Co。然而,上述量的成分對(duì)于優(yōu)化效果而言是示例性的,因此其含量不限于所述用量。Mo與Co共同形成Co-Mo-Cr-Si相(其為硬質(zhì)相),從而通過借助于在Fe基體中的擴(kuò)散的Fe-Mo相來提高和改善耐磨性。如果Mo的量小于16.0重量%,則略微形成Co-Mo-Cr-Si相和Fe-Mo相,使得耐磨性較差,而如果Mo的量大于20.0重量%,則過量形成Co-Mo-Cr-Si相和Fe-Mo相,從而使基體金屬的強(qiáng)度減弱。因此,本發(fā)明的各種實(shí)施方案中Mo的含量被限制在16.0-20.0重量%。Cr與Mo共同形成Co-Mo-Cr-Si相(其為硬質(zhì)相),使得耐磨性得到提高。如果Cr的量小于9.0重量%,則略微形成Co-Mo-Cr-Si相,使得耐磨性較差,而如果Cr的量大于13.0重量%,則過量形成Co-Mo-Cr-Si相,從而使基體金屬的強(qiáng)度減弱。因此,本發(fā)明的各種實(shí)施方案中Cr的含量被限制在9.0-13.0重量%。在本發(fā)明的各種實(shí)施方案中,將V(釩)與碳結(jié)合并形成顆粒狀碳化物,以至于耐磨性和高溫強(qiáng)度得到改善。如果V的量小于0.05重量%,則影響是輕微的,而如果V的量是大于0.15重量%,則容易形成V2O5氧化物。由于所述氧化物的蒸汽壓較高,因此易于在高溫下蒸發(fā)。因此,本發(fā)明的各種實(shí)施方案中V的含量被限制在0.05-0.15重量%。此外,添加硫(S)作為固體潤滑劑并將其與Cr結(jié)合,并在顆粒內(nèi)部形成CrS。如果S的量小于0.2重量%,則固體潤滑劑的沉淀量較小,以至于影響是輕微的,而如果S的量大于0.8重量%,則CrS的量是過量的,使得基體的強(qiáng)度變差。因此,本發(fā)明的各種實(shí)施方案中S的含量被限制在0.2-0.8重量%。此外,在本發(fā)明的各種實(shí)施方案中,用于閥座的燒結(jié)合金含有作為主要成分的鐵(Fe)并且將MnS添加到用于閥座的合金粉末中,以改善工具磨損性和機(jī)械加工性。在本發(fā)明的各種實(shí)施方案中,MnS存在于孔中并且不與相鄰的元素反應(yīng),因此能夠改善機(jī)械加工性和固體潤滑。在本發(fā)明的各種實(shí)施方案中,MnS(具有小于或等于12μm的粒徑)是均勻分布的,MnS的含量是60-65重量%,并且S的含量是35-40重量%。MnS在高溫下不分解成化合物并且是穩(wěn)定的,因此MnS保留在燒結(jié)體的孔中作為燒結(jié)之后的MnS。因此,在機(jī)械加工過程中,通過減小咬合摩擦系數(shù)能夠獲得燒結(jié)體,其中所述燒結(jié)體的機(jī)械加工性是良好的。此外,因?yàn)镸nS發(fā)揮了作為固體潤滑劑的作用,所以MnS能夠 減少金屬之間的撞擊和摩擦力。如果MnS相對(duì)于100重量份的燒結(jié)合金(合金粉末)的量小于0.5重量份,則效果是輕微的,而如果MnS相對(duì)于100重量份的燒結(jié)合金的量大于2.5重量份,則基體的強(qiáng)度減小,以至于在將閥座擠壓到氣缸蓋中的過程中能夠容易地發(fā)生斷裂。因此,在本發(fā)明的各種實(shí)施方案中,MnS相對(duì)于100重量份的燒結(jié)粉末(合金粉末)的含量被限制在0.5-2.5重量份。下文中將描述本發(fā)明的各種實(shí)施方案中的閥座的制造方法。圖4是根據(jù)本發(fā)明的各種實(shí)施方案的閥座的制造過程的流程圖。參照?qǐng)D4,將相對(duì)于100重量份的合金粉末的1.0~2.0重量份的MnS添加到合金粉末中,所述合金粉末由0.8-1.2重量%的C、2.0-4.5重量%的Ni、3.0-5.0重量%的Cr、16.0-20.0重量%的Mo、9.0-13.0重量%的Co,0.05-0.15重量%的V、0.2-0.8重量%的S、Fe和額外的不可避免的雜質(zhì)組成。在步驟S100中,考慮到通過一次成形所需密度和整體長度,將混合的合金粉末和MnS制備成一次形狀。然后,在步驟S110中進(jìn)行預(yù)燒結(jié),并且該過程在2.5小時(shí)期間于750-800℃的范圍內(nèi)完成。預(yù)燒結(jié)過程是通過將少量的碳擴(kuò)散到用于在步驟S120中進(jìn)行再次擠壓(鍛造)的一次成形的形狀中來改善可鍛性的過程,所述再次擠壓(鍛造)是一個(gè)用于提高密度的過程。在預(yù)燒結(jié)過程之后,在步驟S120中將一次成形的形狀再次擠壓,從而通過施加10噸/平方厘米的力,實(shí)現(xiàn)二次形狀并增大密度。再次擠壓過程中的物料是物理結(jié)合的,而二次形狀能夠通過在步驟S130中的主燒結(jié)來化學(xué)結(jié)合。在主燒結(jié)過程中,將物料在1110-1140℃的范圍內(nèi)保持5小時(shí),并且特別是在高溫區(qū)保持50分鐘。在主燒結(jié)之后,二次形狀中出現(xiàn)殘余應(yīng)力,在步驟S140中進(jìn)行回火處理以除去殘余應(yīng)力,所述回火處理中的溫度在大氣中是恒定的。本發(fā)明的各種實(shí)施方案中的回火溫度在180-220℃的范圍內(nèi),并且回火時(shí)間在100-150分鐘的范圍內(nèi)。通過回火使結(jié)構(gòu)之間的應(yīng)力得以緩解。然后,進(jìn)行含油處理(oil-containingprocess),所述含油處理在真空狀態(tài)下將油混入二次形狀,以改善產(chǎn)品的機(jī)械加工性并防止生銹。在含油處理完成之后,對(duì)混入油的二次形狀的尺寸和形狀進(jìn)行機(jī)械加工處理,其不是通過粉末金屬(PM)的方法而實(shí)現(xiàn),在步驟S150中進(jìn)行轉(zhuǎn)桶提金法處理以保持最佳的表面狀態(tài),在該處理之后除去了毛刺和雜質(zhì)。當(dāng)所述轉(zhuǎn)桶提金法處理完成之后,早期檢測出產(chǎn)品表面上的缺陷并且最終檢查能夠找到它們,因此所述產(chǎn)品不會(huì)被遞送至客戶。下文中將更加詳細(xì)地描述本發(fā)明的各種實(shí)施方案。然而,本發(fā)明的范圍并不限制于此。實(shí)施例在本發(fā)明的各種實(shí)施方案中,將相對(duì)于100份的合金粉末的1.5重量份的MnS均勻地?fù)胶显诤辖鸱勰┲?,所述合金粉末?9.5重量%的Fe、3.15重量%的Ni、18.24重量%的Mo、4.27重量%的Cr、1.04重量%的C、11.6重量%的Co、0.95重量%的Mn、0.88重量%的S,0.1重量%的V和額外的不可避免的雜質(zhì)組成,并且將摻合的合金粉末擠壓以制造用于閥座的燒結(jié)合金,并且將擠壓的合金粉末成形、燒結(jié)并于200℃回火120分鐘。對(duì)通過上述方法制造的閥座的磨耗損失進(jìn)行測量。閥座10能夠分為座部分12、14和16以及非座部分,并且座部分12、14和16是本發(fā)明的各種實(shí)施方案中實(shí)驗(yàn)的焦點(diǎn)所在。本發(fā)明的各種實(shí)施方案中的非座部分指的是圖1A-1C中的座部分12、14和16的下部,其中與該閥的摩擦是微不足道的。圖1A-1C顯示出用于根據(jù)本發(fā)明的各種實(shí)施方式的閥座10的處理順序,其中在處理座部分12和14之后,處理座部分16。座部分16是閥座10與圖1C中的閥接觸的部分,并且座部分12和14是用于形成座部分16的輔助表面。圖1A-1C中的座部分12、14和16分別構(gòu)成表面A、B、C。實(shí)驗(yàn)方法為了測試根據(jù)本發(fā)明的各種實(shí)施方案的閥座的性能,在處理過程 中,以1100的每分鐘轉(zhuǎn)數(shù)(RPM)、124.4的進(jìn)給量(FEED)和0.11的進(jìn)給速率(FEEDRATE)來完成測試,對(duì)每一種物料的1000份產(chǎn)品進(jìn)行處理,并且在處理座部分12和14之后處理座部分16。測試結(jié)果如表1和表2中所示。在比較例中,添加MnS和樹脂,但不進(jìn)行回火。表1:機(jī)械加工性表2:物料屬性如表1所示,與比較例相比,根據(jù)各種實(shí)施方案的閥座的表面硬度得到改善。圖2顯示出根據(jù)本發(fā)明的各種實(shí)施方案的閥座的表面粗糙度,其中所述表面粗糙度(Rt)是每一種物料的1000份產(chǎn)品的5次測試平均值。另外,本發(fā)明的各種實(shí)施方案中的最大孔徑減小到比較例的最大孔徑的一半以下,并且大于100μm的氣孔的數(shù)目明顯減少。圖3A-3D顯示出腐蝕之前和之后金屬結(jié)構(gòu)的照片,并且所述照片被放大200倍。參照?qǐng)D3A-3D,圖3A和3B分別是腐蝕之前和之后的根據(jù)比較例和示例性實(shí)施方案的金屬結(jié)構(gòu)的照片,并且圖3C和3D分別是腐蝕之前和之后根據(jù)比較例和各種實(shí)施方案的金屬結(jié)構(gòu)的照片。如圖3A-3D所示,在腐蝕之后,比較例中有較大變化,而本發(fā)明的各種實(shí)施方案中幾無變化,因此,我們能夠知道,根據(jù)本發(fā)明的閥 座具有更好的耐腐蝕性。另外,少于300個(gè)孔能夠在比較例中被加工,而根據(jù)各種實(shí)施方案的閥座中多于1400個(gè)孔能夠被加工,并且在各種實(shí)施方案中不使用樹脂,以至于不會(huì)發(fā)生加工面的撕裂現(xiàn)象。因此,根據(jù)本發(fā)明的各種實(shí)施方案的閥座特別適合于與閥接觸的部分。為了方便解釋和精確限定所附權(quán)利要求,術(shù)語下等是用于參考圖中顯示的這些特征的位置來描述示例性實(shí)施方式的特征。前述對(duì)本發(fā)明的具體示例性實(shí)施方案的描述是為了說明和例證的目的。這些描述并非想窮盡本發(fā)明,或者將本發(fā)明限定為所公開的精確形式,并且很顯然,根據(jù)上述教導(dǎo),可以進(jìn)行很多改變和變化。對(duì)示例性實(shí)施例進(jìn)行選擇和描述的目的在于解釋本發(fā)明的特定原理及其實(shí)際應(yīng)用,從而使得本領(lǐng)域的其它技術(shù)人員能夠?qū)崿F(xiàn)并利用本發(fā)明的各種不同的示例性實(shí)施方案以及各種不同的選擇和改變。本發(fā)明的范圍意在由所附的權(quán)利要求書及其等同形式所限定。