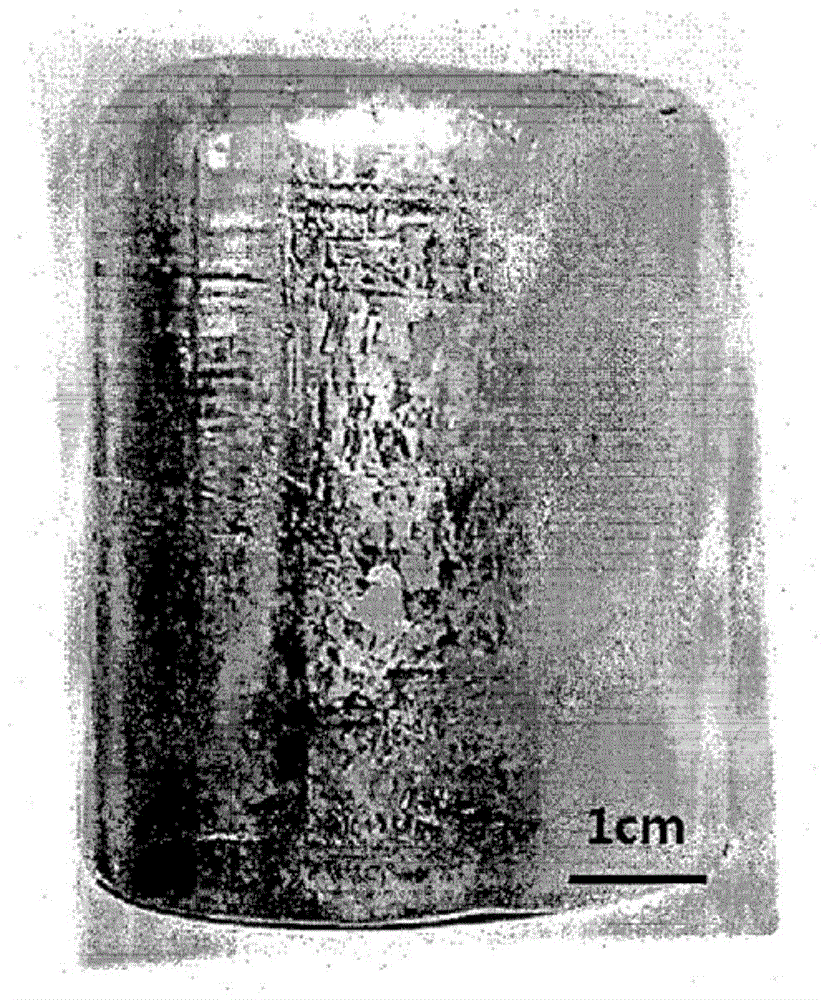
本發(fā)明涉及合金材料,特別是涉及具有改善的機(jī)械性能和耐腐蝕性能的合金材料(如Mg合金)及其制造方法。更具體而言,本發(fā)明涉及通過不同于常規(guī)構(gòu)思的經(jīng)均勻化熱處理而具有改善的機(jī)械性能和耐腐蝕性能等的合金材料(如Mg合金)及其制造方法。
背景技術(shù):Mg是環(huán)境友好型材料,具有1.74g/cm3的密度,這一密度僅為Fe密度的1/5和Al密度的2/3,通常具有優(yōu)異的強(qiáng)度,并可容易地回收利用。Mg也被評為超輕質(zhì)結(jié)構(gòu)材料,Mg的比強(qiáng)度和彈性系數(shù)與其它輕質(zhì)材料(例如Al)相當(dāng)。此外,Mg對減震(absorbvibration)、沖擊和電磁波等顯示出優(yōu)異的能力,并具有優(yōu)異的導(dǎo)電性和導(dǎo)熱性。然而,盡管具有上述的出色性能,Mg和Mg合金存在耐腐蝕性能差的根本性問題。由于已知Mg因其高反應(yīng)性而在電動(dòng)勢(EMF)下和在電鍍反應(yīng)中迅速腐蝕,Mg的應(yīng)用局限于腐蝕環(huán)境條件不嚴(yán)苛的內(nèi)部或者對強(qiáng)度、耐熱性能或耐腐蝕性能要求不高的區(qū)域。因此,盡管仍需要從根本上改善Mg和Mg合金耐腐蝕性能的技術(shù),但是現(xiàn)有技術(shù)并不能滿足這種需要。同時(shí),通過向Mg材料中加入氧化物顆粒(例如,鈣氧化物),嘗試彌補(bǔ)Mg的這些缺陷(例如,韓國專利公開號(hào)No.10-2009-78039)。然而,當(dāng)強(qiáng)力攪拌鈣氧化物或?qū)⑵溟L時(shí)間暴露于熔融金屬中時(shí),氧漂浮在該熔融金屬的表面上,由此形成雜質(zhì)。必須去除這些有問題的雜質(zhì)。當(dāng)向Mg中加入鈣氧化物時(shí),已知Mg和Ca形成復(fù)合物,且O與Mg鍵合形成雜質(zhì)。此類雜質(zhì)(如MgO)降低了Mg的耐腐蝕性能。此外,在制造材料時(shí)通常進(jìn)行熱處理。即,當(dāng)進(jìn)行均勻化熱處理如O-回火時(shí),隨著共晶結(jié)構(gòu)消失,延伸率增加。通過此類均勻化熱處理結(jié)合低溫?zé)崽幚懋a(chǎn)生沉淀(沉淀硬化),由此改善了材料的機(jī)械性能,例如強(qiáng)度或硬度。同時(shí),雖然均勻化熱處理增加了延伸率,但是由于第二相消失,強(qiáng)度降低。在相關(guān)的技術(shù)中,由于均勻化熱處理而在強(qiáng)度方面的降低被視為正常的事而被接受,并未嘗試改善這一強(qiáng)度。
技術(shù)實(shí)現(xiàn)要素:技術(shù)問題本發(fā)明是為了解決現(xiàn)有技術(shù)中的上述問題,因此本發(fā)明的目的是提供合金材料,其中,使用金屬氧化物顆粒改善基質(zhì)金屬的機(jī)械性能和耐腐蝕性能。本發(fā)明的另一目的是提供合金材料,其中,使用金屬氧化物納米顆粒通過均勻化熱處理可改善所述合金材料的機(jī)械性能和耐腐蝕性能,以及所述材料的制造方法。技術(shù)方案為實(shí)現(xiàn)上述目的,本發(fā)明提供了包含基質(zhì)金屬的鑄造材料,其中,氧化物顆粒在基質(zhì)金屬中分解,從而使作為該氧化物構(gòu)成成分的金屬元素和氧(O)原子分散于所述基質(zhì)金屬中,并且所述氧原子不與所述基質(zhì)金屬形成氧化物。根據(jù)本發(fā)明,所述鑄造材料不包含所述氧化物顆粒。根據(jù)本發(fā)明,所述氧化物顆粒的氧原子可優(yōu)先分散于所述基質(zhì)金屬中,并且所述氧化物顆粒的金屬元素可隨后分散于所述基質(zhì)金屬中,由此與所述基質(zhì)金屬混合。根據(jù)本發(fā)明的實(shí)施方式,所述基質(zhì)金屬可以是Mg或Mg合金,所述氧化物顆??梢允沁x自如下氧化物中的至少一種氧化物的顆粒:鈦氧化物(TiOx)、錳氧化物(MnOx)、鋯氧化物(ZrOx)、鉻氧化物(CrOx)和鐵氧化物(FeOx)。本發(fā)明另一方面提供了制造鑄造材料的方法,所述方法包括如下步驟:制備基質(zhì)金屬的熔融金屬;將氧化物顆粒加入到所述熔融金屬中,分解所述氧化物顆粒,從而使作為所述氧化物顆粒構(gòu)成成分的氧原子首先分散于所述基質(zhì)金屬中,并且使作為所述氧化物顆粒構(gòu)成成分的金屬元素隨后分散于所述基質(zhì)金屬中,由此制造出所述氧原子和所述金屬元素分散于所述基質(zhì)金屬中的鑄造材料,其中,所述氧原子不與所述基質(zhì)金屬形成氧化物。根據(jù)本發(fā)明的實(shí)施方式,所述鑄造材料可不包含所述氧化物顆粒。本發(fā)明又一方面提供了鑄造合金材料。所述鑄造合金材料包含基質(zhì)金屬和合金元素。納米級(jí)的氧化物顆粒在所述基質(zhì)金屬中分解,從而使包含金屬元素(所述氧化物顆粒的構(gòu)成成分)和所述合金元素的新相形成帶狀結(jié)構(gòu)或網(wǎng)狀結(jié)構(gòu)。所述金屬元素和所述合金元素具有負(fù)混合熱關(guān)系。由所述氧化物顆粒分解形成的氧原子分散于所述基質(zhì)金屬中,并且不與所述基質(zhì)金屬形成氧化物。根據(jù)本發(fā)明的實(shí)施方式,所述金屬元素和所述基質(zhì)金屬可具有正混合熱關(guān)系或負(fù)混合熱關(guān)系,所述負(fù)混合熱的絕對值小于所述金屬元素和所述合金元素之間的負(fù)混合熱的絕對值。根據(jù)本發(fā)明的實(shí)施方式,所述金屬元素(所述氧化物顆粒的構(gòu)成成分)與所述基質(zhì)金屬不會(huì)形成復(fù)合物。根據(jù)本發(fā)明的實(shí)施方式,可在均勻化熱處理過程中形成所述新相,從而與所述熱處理前相比,機(jī)械性能和耐腐蝕性能得到改善。所述均勻化熱處理可為O-回火。根據(jù)本發(fā)明的實(shí)施方式,所述基質(zhì)金屬可為Mg,合金元素可為Al,所述氧化物顆??梢允沁x自如下氧化物中的至少一種氧化物的顆粒:鈦氧化物(TiOx)、錳氧化物(MnOx)、鉻氧化物(CrOx)、鋯氧化物(ZrOx)和鐵氧化物(FeOx)。進(jìn)一步地,本發(fā)明另一方面提供了制造鑄造合金材料的方法。所述方法包括如下步驟:制備基質(zhì)金屬的熔融金屬;加入合金元素,該合金元素與所述基質(zhì)金屬具有負(fù)混合熱關(guān)系;將納米級(jí)的氧化物顆粒加入到所述熔融金屬中,該氧化物顆粒包含與所述合金元素具有負(fù)混合熱關(guān)系的金屬元素,從而分解所述氧化物顆粒,由此制造出所述金屬元素優(yōu)先分布于所述合金元素周圍的鑄造材料;以及對所述鑄造材料進(jìn)行均勻化熱處理,從而由包含所述金屬元素和所述合金元素的新相形成帶狀結(jié)構(gòu)或網(wǎng)狀結(jié)構(gòu),與未經(jīng)歷所述均勻化熱處理的鑄造材料相比,由此改善了鑄造材料的機(jī)械性能和耐腐蝕性能。在所述鑄造合金材料中,由氧化物顆粒分解形成的氧原子分散于所述基質(zhì)金屬中,并且不與所述基質(zhì)金屬形成氧化物。根據(jù)本發(fā)明的實(shí)施方式,隨所述熱處理時(shí)間的增加,所述機(jī)械性能可得到進(jìn)一步改善。根據(jù)本發(fā)明的實(shí)施方式,所述均勻化熱處理可為O-回火。根據(jù)本發(fā)明的實(shí)施方式,所述金屬元素和所述基質(zhì)金屬可具有正混合熱關(guān)系或負(fù)混合熱關(guān)系,所述負(fù)混合熱的絕對值小于所述金屬元素和所述合金元素之間的負(fù)混合熱的絕對值。根據(jù)本發(fā)明的實(shí)施方式,所述基質(zhì)金屬可為Mg,所述合金元素可為Al,所述氧化物顆??梢允沁x自于如下氧化物中的至少一種氧化物的顆粒:鈦氧化物(TiOx)、錳氧化物(MnOx)、鉻氧化物(CrOx)、鋯氧化物(ZrOx)和鐵氧化物(FeOx)。本發(fā)明另一方面提供了包含Mg基質(zhì)金屬和合金元素的Mg合金材料,所述合金元素與所述Mg基質(zhì)金屬具有負(fù)混合熱關(guān)系。納米級(jí)的氧化物顆粒包含金屬元素,該金屬元素與所述Mg具有正混合熱關(guān)系,并與所述合金元素具有負(fù)混合熱關(guān)系,使所述氧化物顆粒分解,從而由包含所述金屬元素(所述氧化物顆粒的構(gòu)成成分)和所述合金元素的新相形成帶狀結(jié)構(gòu)或網(wǎng)狀結(jié)構(gòu)。由所述氧化物顆粒分解形成的氧原子分散于所述Mg基質(zhì)金屬中,并且不與所述Mg形成氧化物。有益效果根據(jù)本發(fā)明,可通過使熔融金屬中的氧化物顆粒分解,由此使構(gòu)成所述氧化物的金屬元素和氧原子分散于基質(zhì)金屬中,從而制造出鑄造材料。與其它合金相比,由于使氧原子分散,所述鑄造材料顯示出優(yōu)異的機(jī)械性能和耐腐蝕性能。此外,即使進(jìn)行均勻化熱處理,但是包含合金元素和金屬元素(由氧化物顆粒分解形成)的新相形成帶狀結(jié)構(gòu)或網(wǎng)狀結(jié)構(gòu),由此改善了所述鑄造合金材料的機(jī)械性能(如強(qiáng)度)和耐腐蝕性能。附圖說明圖1是示出本發(fā)明實(shí)施方式所述的鑄造材料制造過程的流程圖;圖2是示出根據(jù)本發(fā)明實(shí)施方式制造的鑄造材料的照片;圖3是對根據(jù)本發(fā)明實(shí)施方式制造的鑄造材料的表面進(jìn)行觀察獲得的光學(xué)顯微照片;圖4是根據(jù)本發(fā)明實(shí)施方式制造的鑄造材料的蝕刻狀態(tài)照片及其放大圖;圖5是顯示根據(jù)本發(fā)明實(shí)施方式制造的鑄造材料的X射線能量色散譜(EDS)組分分析結(jié)果的圖;圖6是示出本發(fā)明另一實(shí)施方式所述的鑄造合金材料制造過程的流程圖;圖7是示出本發(fā)明實(shí)施方式所述的鑄造合金材料的微觀結(jié)構(gòu)的圖,所述鑄造材料通過向熔融金屬中添加二氧化鈦(在該熔融金屬中,已經(jīng)以6%、9%和12%的質(zhì)量比將Al加入到Mg基質(zhì)中),并經(jīng)分解和分散制造;圖8是Mg-Al相圖;圖9是示出本發(fā)明實(shí)施方式所述的鑄造合金材料在400℃下熱處理12小時(shí)后的微觀結(jié)構(gòu)的圖,所述鑄造合金材料通過向熔融金屬中添加二氧化鈦(在該熔融金屬中,已經(jīng)以6%、9%和12%的質(zhì)量比將Al加入到Mg基質(zhì)中),并經(jīng)分解和分散制造;圖10是示出如下Mg合金的硬度值隨處理時(shí)間變化的圖:以9%和12%的質(zhì)量比添加Al并以2%的體積比添加二氧化鈦的Mg合金;以12%的質(zhì)量比添加Al并以3%的體積比添加二氧化鈦的Mg合金;以及可商購的AZ91Mg合金;圖11是針對如下鑄造合金材料進(jìn)行腐蝕試驗(yàn)所得到的腐蝕曲線之間的比較圖:通過以3%的體積比將二氧化鈦加入到熔融金屬中(在該熔融金屬中,已經(jīng)以12%的質(zhì)量比將Al加入到Mg基質(zhì)中)制造,并進(jìn)行熱處理(氧化)后的鑄造合金材料;現(xiàn)有的AZ91合金;熱處理前的該鑄造合金材料。圖12是示出通過對根據(jù)本發(fā)明實(shí)施方式制造的鑄造材料進(jìn)行軋制而獲得的軋制材料的照片;以及圖13是示出對上述軋制材料進(jìn)行的拉伸試驗(yàn)的圖。具體實(shí)施方式下面將詳細(xì)地參考本發(fā)明的各種實(shí)施方式以及附圖。在本發(fā)明的以下描述中,將省略對公知技術(shù)的詳細(xì)描述。然而,下述實(shí)施方式將使本領(lǐng)域技術(shù)人員易于理解本發(fā)明的特征性組成和效果,并能夠沒有明顯困難地將本發(fā)明付諸實(shí)踐。實(shí)施例實(shí)施例1圖1是示出本發(fā)明實(shí)施例1所述的材料制造過程的流程圖。本發(fā)明人選擇Mg和二氧化鈦(TiO2,50nm)分別作為金屬基質(zhì)和納米氧化物顆粒,根據(jù)如下過程制造材料,并評價(jià)該材料的性能。首先,本發(fā)明人使用慣常的鑄造方法通過將氧化物顆粒分解/分散于基質(zhì)金屬中,實(shí)現(xiàn)了溶解氧原子的出乎預(yù)料的結(jié)果。具體而言,使用電熔融爐對純Mg進(jìn)行熔融,然后以1%的體積比將二氧化鈦(TiO2,50nm)加入到熔融金屬中。此時(shí),在室溫下以壓塊(compact)的形式制備二氧化鈦粉末,從而可將二氧化鈦顆粒加入到熔融金屬中。將熔融金屬的溫度升至820℃,并維持30分鐘,使所述顆粒能夠分解。隨后進(jìn)行鑄造,由此制造出圖2所示的鑄造材料。在制造過程中全程使用保護(hù)氣體(SF6+CO2)以防止氧化。同時(shí),雖然本實(shí)施例中使用了純Mg,但是還可如下文所述使用Mg合金。為分析上述制造的Mg材料的微觀結(jié)構(gòu),使用光學(xué)顯微鏡觀察蝕刻前后的Mg材料,結(jié)果在圖3和圖4中示出。首先,關(guān)于刻蝕前的照片(圖3),這是使用光學(xué)顯微鏡觀察由上述過程制造的鑄造材料而獲得的照片。可確認(rèn)在鑄造材料內(nèi)部實(shí)質(zhì)上不存在缺陷。雖然慣常的Mg鑄造材料在其中通常含有相當(dāng)大量的雜質(zhì),但是從本發(fā)明的Mg合金的表面觀察不到此類缺陷。在使用苦味酸對鑄造材料進(jìn)行蝕刻后,使用光學(xué)顯微鏡觀察鑄造材料的表面。結(jié)果在圖4的左側(cè)部分示出;通過在高放大倍數(shù)下對結(jié)果進(jìn)行觀察而獲得的照片在圖4的右側(cè)部分示出。由圖4可知,通過TiO2的分解在顆粒內(nèi)部形成新相。如果TiO2是簡單地分散而非分解,考慮到它們的尺寸(約50nm),必定會(huì)發(fā)現(xiàn)顆粒的團(tuán)聚物(clusters)。然而,并未發(fā)現(xiàn)團(tuán)聚物,并且觀察到圖4中所示的不同的相。本發(fā)明人使用掃描電子顯微鏡(SEM)觀察微觀結(jié)構(gòu),并通過X射線能量色散譜(EDS)進(jìn)行組分分析,以對微觀結(jié)構(gòu)進(jìn)行詳細(xì)分析,結(jié)果在圖5中示出。由圖5中示出的EDS照片可發(fā)現(xiàn),O原子和Ti原子均勻地分散于Mg基質(zhì)中。此外,由于氧原子密集地分布于新相所在區(qū)域,還可明白的是,形成了包含氧原子的新相。從現(xiàn)有的公知常識(shí)來看,可認(rèn)為這是相當(dāng)出乎預(yù)料的結(jié)果。即,認(rèn)為二氧化鈦分成Ti原子和氧原子,從而使O原子和Ti原子分散于Mg基質(zhì)中,由此形成了單獨(dú)的新相。實(shí)施例2圖6是示出本發(fā)明實(shí)施例2所述的鑄造合金材料的制造過程的流程圖。本發(fā)明人選擇Mg、Al和二氧化鈦(TiO2,50nm)分別作為金屬基質(zhì)、合金元素和納米氧化物顆粒,根據(jù)如下過程制造材料,并評價(jià)該材料的性能。同時(shí),本發(fā)明人從混合熱的角度對所選擇的金屬基質(zhì)、合金元素和納米氧化物顆粒進(jìn)行了分析?;旌蠠崾潜硎井?dāng)兩種不同的成分以液態(tài)形式存在時(shí),這兩種成分各自的焓之間的差值的參數(shù)。當(dāng)處于液態(tài)的兩種不同成分之間的焓差為負(fù)(–)時(shí),通過這兩種成分的分子間相互反應(yīng)實(shí)現(xiàn)混合。該差值越大,越容易混合(即,兩種不同的成分傾向于聚集在一起)。與此相反,當(dāng)焓差為正(+)時(shí),由于兩種成分彼此之間不反應(yīng),因此并不會(huì)發(fā)生混合(即,兩種不同成分傾向于保持彼此分開)。Mg和Ti之間的混合熱差是+16,Al和Ti之間的混合熱差是–30,Mg和Al之間的混合熱差是–2。因此可以說,Ti傾向于優(yōu)先與Al而非Mg鍵合。首先,本發(fā)明人使用慣常的鑄造方法通過將氧化物顆粒分解/分散于基質(zhì)金屬中,實(shí)現(xiàn)了溶解氧原子的出乎預(yù)料的結(jié)果。具體而言,使用電熔融爐對純Mg進(jìn)行熔融,以6%、9%、12%的質(zhì)量比加入Al,然后以1%的體積比將二氧化鈦加入到各熔融金屬中。此時(shí),在室溫下以壓塊的形式制備二氧化鈦粉末,從而可將二氧化鈦顆粒加入各熔融金屬中。將熔融金屬的溫度升至820℃,并維持30分鐘,使所述顆粒能夠得以分解。隨后進(jìn)行鑄造,由此制造出鑄造合金材料。在制造過程中全程使用保護(hù)氣體(SF6+CO2)以防止氧化。同時(shí),在本發(fā)明中,所加入的氧化物顆粒的粒徑處于納米級(jí)(本實(shí)施例中為50nm),將納米級(jí)的氧化物顆粒的壓塊加入到熔融金屬中。雖然未在本申請文件中特別示出,但是根據(jù)本發(fā)明人的觀察,當(dāng)氧化物顆粒的尺寸超出納米級(jí)時(shí),例如,當(dāng)氧化物顆粒尺寸增大至微米級(jí)時(shí),即使將氧化物顆粒加入到熔融金屬中,也觀察不到如下文所述的氧化物被分成金屬元素和氧原子的現(xiàn)象。為分析上述制造的Mg材料的微觀結(jié)構(gòu),使用光學(xué)顯微鏡觀察蝕刻前后的Mg合金材料,結(jié)果在圖7中示出。如該圖所示,顯然形成了不同的新相,而非添加有Al的現(xiàn)有Mg合金可見的第二相。也就是說,認(rèn)為通過TiO2的分解在顆粒內(nèi)部形成新相。從現(xiàn)有的公知常識(shí)來看,可以認(rèn)為這是相當(dāng)出乎預(yù)料的結(jié)果。即,在Mg熔融金屬中,二氧化鈦分解成Ti原子和氧原子,并且Ti原子和氧原子均勻分散于熔融金屬中。在固化過程中,氧原子并不會(huì)形成Mg氧化物,而是以準(zhǔn)平衡態(tài)存在于Mg-Al基質(zhì)中。還認(rèn)為,Ti原子分散于合金基質(zhì)中,并傾向于優(yōu)先與Al鍵合,由此形成單獨(dú)的新相。此外,不僅是Ti,而且Zr、Mn、Cr和Fe也顯示出如下類似的傾向:隨著Mg濃度梯度的增大,液相線升高。從混合熱的角度描述,Ti和Mn等顯示出對于Mg的正(+)混合熱,以及對于Al的負(fù)(–)混合熱。因此,Ti和Mn等并不會(huì)與Mg形成復(fù)合物,而是優(yōu)先與Al鍵合,由此形成新相。這一結(jié)果相當(dāng)出乎預(yù)料。已知的是,由于Mg在液相/固相時(shí)實(shí)質(zhì)上并不能溶解氧,氧原子在Mg中的分散不可能處于熱力學(xué)穩(wěn)定態(tài)。此外,從熱力學(xué)的角度來看,當(dāng)強(qiáng)行溶解氧時(shí),必定會(huì)直接形成MgO。然而,根據(jù)本發(fā)明,實(shí)際上觀察到在固化期間和在熔融金屬中,氧原子分散于Mg中而并未形成MgO,該結(jié)果在圖7中示出。認(rèn)為這是由于在制造Mg合金時(shí)使用了不同于現(xiàn)有技術(shù)方法的獨(dú)特方法。具體而言,在嘗試通過將氧化物顆粒加入到Mg熔融金屬中來形成MgO時(shí),可認(rèn)為,當(dāng)氧形成數(shù)個(gè)團(tuán)聚物且MgO成核并生長至預(yù)定尺寸以上時(shí),形成MgO顆粒。出于移除氧以防止其存在于熔融金屬中的目的,相關(guān)現(xiàn)有技術(shù)涉及在將氧化物顆粒加入到熔融金屬中的同時(shí),強(qiáng)力攪拌熔融金屬。該強(qiáng)力攪拌形成團(tuán)聚物,從而形成了氧化物,例如MgO。與廣泛使用的相關(guān)現(xiàn)有技術(shù)方法不同,本發(fā)明人僅僅是加入處于穩(wěn)定態(tài)的氧化物顆粒。即,本發(fā)明人僅通過向熔融金屬中加入上述制備的二氧化鈦顆粒,并且在加入二氧化鈦顆粒時(shí)并沒有為了使所述顆?;烊肴廴诮饘僦卸鴮θ廴诮饘龠M(jìn)行強(qiáng)力攪拌操作,就可將二氧化鈦顆粒分成Ti原子和氧原子。據(jù)此可認(rèn)為,由于未滿足從二氧化鈦分出的氧原子可形成團(tuán)聚物的條件,使得并未發(fā)生MgO晶體的成核。因此,最終制造的Mg合金中不含有MgO。同時(shí),本發(fā)明人對上述制造的材料進(jìn)行熱處理。即,在材料的通用生產(chǎn)過程中,進(jìn)行熱處理(例如O-回火;參見圖8),從而緩和應(yīng)變硬化并改善延展性。已知的是,均勻化熱處理(如O-回火)降低機(jī)械性能(如強(qiáng)度)。從圖8的Mg-Al相圖中明顯可見的是,通過將400℃下的熱處理溫度維持12小時(shí)進(jìn)行熱處理,從而在基質(zhì)中形成單一的相。使用光學(xué)顯微鏡觀察熱處理材料的微觀結(jié)構(gòu),并在圖9中示出。如圖9中所示,不同于在添加有Al的常見Mg合金熱處理過程中所見的微觀結(jié)構(gòu),首次發(fā)現(xiàn),根據(jù)Al的量,新形成的相形成帶狀結(jié)構(gòu)或網(wǎng)絡(luò)結(jié)構(gòu)。顯而易見的是,新相在整個(gè)區(qū)域上均勻形成,新相的形狀隨Al添加量的增加而變得更加致密。具體而言,當(dāng)將二氧化鈦粉末加入到Mg熔融金屬中時(shí),該二氧化鈦粉末開始分解并分成Ti原子和氧原子。此時(shí),由于Ti原子不會(huì)與Mg形成復(fù)合物(+16的正混合熱),因此并未形成由Mg和Ti組成的相。本發(fā)明人向先添加了Al的Mg熔融金屬中加入二氧化鈦粉末。與Mg的情況不同,Ti原子與Al具有負(fù)混合熱,因此所分出的Ti原子將優(yōu)先分布在Al原子周圍。認(rèn)為當(dāng)對Ti原子分布在Al周圍的材料進(jìn)行上述熱處理時(shí),形成含有Mg、Al、Ti和氧原子的新相,由此構(gòu)成的相形成如圖9所示的帶狀結(jié)構(gòu)或網(wǎng)狀結(jié)構(gòu)。本發(fā)明人對Al和二氧化鈦的量不同的材料以及AZ91Mg合金(可商購合金)的硬度值與熱處理時(shí)間的關(guān)系進(jìn)行了比較,結(jié)果在圖10中示出。如圖10中所示,對如下合金的硬度值與熱處理時(shí)間的關(guān)系進(jìn)行了比較:以9%和12%的質(zhì)量比添加Al并以2%的體積比添加二氧化鈦的Mg合金;以12%的質(zhì)量比添加Al并以3%的體積比添加二氧化鈦的Mg合金;以及AZ91Mg合金。熱處理溫度為420℃。明顯的是,當(dāng)熱處理3小時(shí)后,所有材料的硬度值均降低。這一現(xiàn)象的發(fā)生是由于材料中的共晶相擴(kuò)散入基質(zhì)中。然而,在添加有二氧化鈦的三種材料中,3小時(shí)后可觀察到強(qiáng)度的改善。這可能是由于形成了具有如圖9所示的帶狀結(jié)構(gòu)或網(wǎng)狀結(jié)構(gòu)的相。因此,可證實(shí)與熱處理的現(xiàn)有結(jié)果不同的結(jié)果,即所述結(jié)果為,隨熱處理時(shí)間的增加,硬度值增加而非降低??烧J(rèn)為這是由于隨熱處理時(shí)間的增加,構(gòu)成網(wǎng)狀的相在貫穿材料的整個(gè)內(nèi)部形成。因此,在通過利用本發(fā)明來制造塊狀材料(bulkmaterial)的情況下,如果熱處理進(jìn)行足夠長的時(shí)間,能夠形成在整個(gè)區(qū)域具有均勻的機(jī)械性能的合金材料,并不存在所述機(jī)械性能(如硬度或強(qiáng)度)隨材料位置不同而不同的非均勻性。此外,本發(fā)明人通過拋光上述制造的鑄造合金材料的表面并隨后在420℃下熱處理24小時(shí),進(jìn)行腐蝕測試,結(jié)果在圖11中示出。上述的熱處理過程(氧化)是一種通過在鑄造材料或加工材料表面上形成氧化膜來改善腐蝕評分的方法。然而,即使進(jìn)行表面處理(如熱處理),在表面上形成的氧化膜也不均勻,因此難以改善Mg的腐蝕評分,這很成問題。與之相反,就根據(jù)本發(fā)明進(jìn)行熱處理的鑄造合金材料的情況而言,在該鑄造材料的表面上形成均勻的氧化膜。因此可理解的是,相對于AZ91合金(可商購合金)的腐蝕曲線以及熱處理前的鑄造合金材料的腐蝕曲線,該鑄造合金材料的腐蝕曲線得到顯著改善。如下將對圖11的結(jié)果進(jìn)行更詳細(xì)地描述。金屬發(fā)射電子的時(shí)間(腐蝕發(fā)生的時(shí)間)稱為極化電位Ecorr。如圖11所示,電子發(fā)射的時(shí)間是反應(yīng)由還原轉(zhuǎn)變?yōu)檠趸臅r(shí)間??赏ㄟ^腐蝕試驗(yàn)測定該反應(yīng),并且極化電位和腐蝕速率(Icorr,腐蝕電流密度)(Tefal曲線)可如圖11所示。參考Tefal曲線,可能確定施加電壓時(shí)發(fā)生腐蝕的量。例如參考圖11,當(dāng)通入–1.3V的電壓時(shí),添加有TiO2的樣品和AZ91樣品之間的腐蝕速率差是10-2。這表明,添加有TiO2的樣品比起AZ91樣品在腐蝕方面要更慢約100倍。此外可理解的是,當(dāng)對經(jīng)過熱處理(氧化)的樣品通入–1.3V的電壓時(shí)未發(fā)生腐蝕,而在更高的電壓–0.2V下發(fā)生腐蝕。該速率與未經(jīng)熱處理的樣品和AZ91樣品相比分別顯示出10-3和10-5的速率差。這表明,腐蝕發(fā)生分別減慢約1000和100,000倍,且耐腐蝕性能得到顯著改善。本發(fā)明人將前述實(shí)施例中提出的溶解有氧原子的鑄造材料在380℃下進(jìn)行熱軋制,所得到的軋制材料在圖12中所示。具體而言,以1%的體積比將二氧化鈦(TiO2)加入到熔融金屬中,該熔融金屬通過以3%的質(zhì)量比將Al熔融到純Mg中得到。將所得到的熔融金屬在恒溫下維持30分鐘,隨后進(jìn)行鑄造。在制造過程中全程使用保護(hù)氣體(SF6+CO2)以防止氧化。這與前述實(shí)施例中所述的相同。在380℃下,以15%的壓下率將上述制造的鑄造材料從10mm的初始厚度熱軋制至0.8mm,由此制造出Mg軋制材料,并在室溫和200℃下進(jìn)行拉伸試驗(yàn)。在圖13中示出了在室溫下和在200℃下由拉伸試驗(yàn)獲得的標(biāo)稱應(yīng)變-標(biāo)稱應(yīng)力圖。在室溫下,以10-4s-1的拉伸速率以及在200℃下以10-3s-1的拉伸速率進(jìn)行拉伸試驗(yàn)。如圖13所示,顯然的是,所述材料在室溫和高溫下均顯示出優(yōu)異的延伸率。雖然上文中已參考優(yōu)選的實(shí)施方式對本發(fā)明進(jìn)行了描述,但應(yīng)當(dāng)理解的是,本發(fā)明不限于前述實(shí)施方式。雖然通過例舉的方式將前述實(shí)施方式描述為使用陶瓷顆粒即二氧化鈦(TiO2),但是本發(fā)明并不僅限于此。例如,還可將基于金屬元素的氧化物顆粒用于本發(fā)明,所述金屬元素對于基質(zhì)金屬具有正混合熱,且對于合金元素具有負(fù)混合熱。例如,所述氧化物選自:錳氧化物(MnOx)、鉻氧化物(CrOx)、鋯氧化物(ZrOx)和鐵氧化物(FeOx)。此外,即使氧化物(例如鈣氧化物(CaOx)、鍶氧化物(SrOx)、鋇氧化物(BaOx)、鋅氧化物(ZnOx)、硅氧化物(SiOx)、鋁氧化物(AlOx)、釔氧化物(YOx)、稀土氧化物(REOx)和錫氧化物(SnOx))可溶于基質(zhì)金屬,當(dāng)通過本發(fā)明前述生產(chǎn)方法加入氧化物時(shí)(即以靜態(tài)放入而不強(qiáng)力攪拌),可根據(jù)本發(fā)明所述對該氧化物進(jìn)行分解和熱處理,從而形成新相,所述新相構(gòu)成貫穿整個(gè)基質(zhì)金屬的帶狀結(jié)構(gòu)或網(wǎng)狀結(jié)構(gòu),由此改善合金材料的機(jī)械性能。如上所述,可在不脫離所附權(quán)利要求書范圍的情況下,對本發(fā)明進(jìn)行各種變化和修改,并且這些變化和修改全部落入本發(fā)明的范圍內(nèi)。因此,本發(fā)明僅由權(quán)利要求書及其等同物限定。