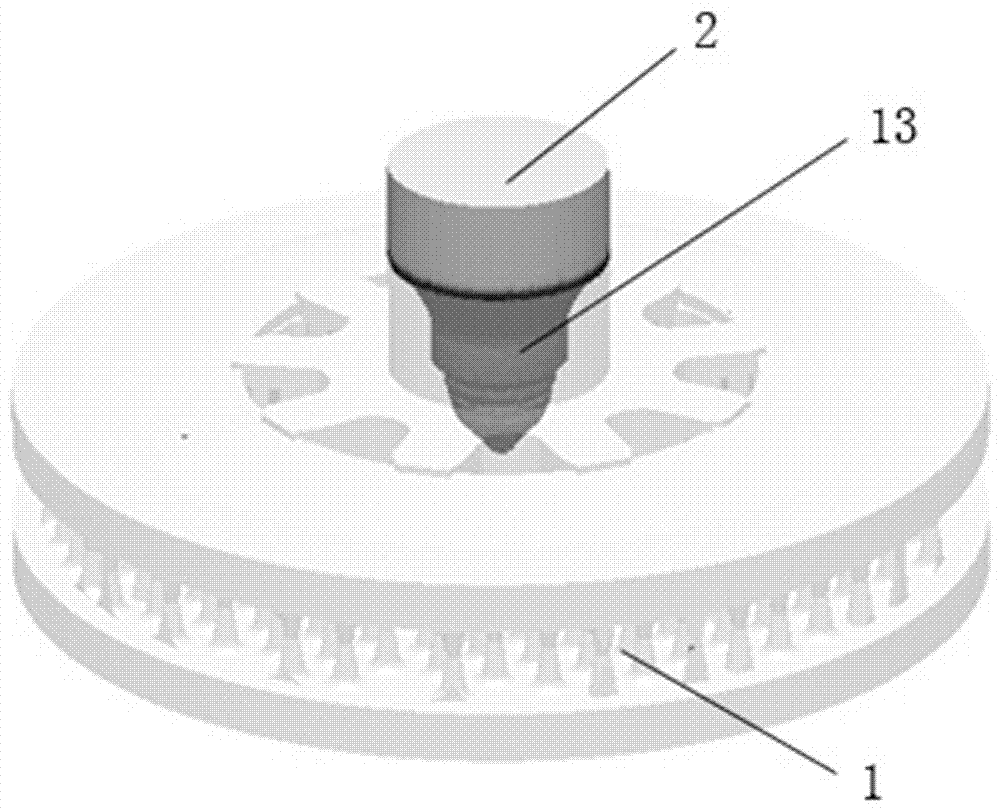
本發(fā)明涉及一種鑄造方法,尤其涉及一種適用于高速列車鑄鋼制動(dòng)盤盤體的鑄造方法和裝置,及由此制得的制動(dòng)盤盤體。
背景技術(shù):制動(dòng)盤盤體是高速列車的關(guān)鍵部件,在列車制動(dòng)時(shí)起重要作用。由于其工作環(huán)境復(fù)雜惡劣,維修更換不便。要求制動(dòng)盤產(chǎn)品必須有穩(wěn)定的質(zhì)量和較長的使用壽命。大量研究表明,在材質(zhì)一定的情況下,鑄造制動(dòng)盤盤體失效的主要原因是盤體中存在縮孔、縮松、砂孔、裂紋等鑄造缺陷。250km/h以上速度的高速列車,對(duì)制動(dòng)盤盤體的質(zhì)量提出了更高的要求,對(duì)縮孔、縮松、砂孔、氣孔、渣孔、裂紋等鑄造缺陷的容忍度進(jìn)一步降低,同時(shí),對(duì)材質(zhì)中的氣體及夾雜物的含量也做出了嚴(yán)格的限制。這都要求必須有相應(yīng)合理的澆注系統(tǒng)和補(bǔ)縮系統(tǒng)來保證,因此,開發(fā)一種能夠穩(wěn)定生產(chǎn)高速列車鑄鋼及其他合金的制動(dòng)盤盤體的鑄造工藝是一個(gè)很迫切的問題。公布號(hào)為CN102069148A的發(fā)明專利公開了一種高速機(jī)車用制動(dòng)盤的鑄造方法,包括如下步驟:凝固模擬、設(shè)計(jì)砂芯、芯盒制作、制芯、組芯、熔煉澆注、打箱落砂和清理,該發(fā)明采用無箱疊芯組合澆注的方式,一次造型澆注4-8件,生產(chǎn)效率高,但是生產(chǎn)的鑄件仍然存在大量的鑄造缺陷。公告號(hào)為CN202097365U的實(shí)用新型專利公開了一種汽車制動(dòng)盤鑄造澆道機(jī)構(gòu),包括直澆道、橫澆道、冒口和鑄件,直澆道和橫澆道之間設(shè)有集渣包I和集渣包II,橫澆道和冒口之間設(shè)有集渣包III,該實(shí)用新型設(shè)計(jì)了三道集渣道,能濾去鐵液中50%以上的夾渣,但是生產(chǎn)的鑄件仍然存在大量的鑄造缺陷。
技術(shù)實(shí)現(xiàn)要素:為克服上述現(xiàn)有技術(shù)中存在的問題,本發(fā)明提供一種制動(dòng)盤盤體的鑄造方法,其按照先后順序包括以下步驟:(1)通過計(jì)算機(jī)模擬軟件對(duì)所述制動(dòng)盤盤體的鑄造工藝和鑄造裝置進(jìn)行模擬分析,確定澆注系統(tǒng)和補(bǔ)縮系統(tǒng)的位置,所述補(bǔ)縮系統(tǒng)的冒口中心置于鑄件內(nèi)側(cè)壁至鑄件幾何中心的任一位置;在進(jìn)行模擬分析前,首先對(duì)鑄件需要達(dá)到的技術(shù)要求做分析,根據(jù)技術(shù)要求模擬制動(dòng)盤盤體的鑄造工藝和鑄造裝置。本發(fā)明選用的模擬軟件包括適用于材料加工工程及制造領(lǐng)域中的任何模擬軟件,如Magma、ProCast、NovaCast、AnyCast、Flow3D、華鑄CAE、Ansys、Abaqus、Marc等。打開模擬軟件,建立實(shí)體模型,在模型上劃分網(wǎng)格,設(shè)定參數(shù),進(jìn)行模擬分析;根據(jù)模擬結(jié)果調(diào)試參數(shù),然后使用新的參數(shù)再次進(jìn)行模擬分析;經(jīng)過不斷的調(diào)試參數(shù),得到能夠達(dá)到鑄件技術(shù)要求的鑄造工藝和鑄造裝置。本發(fā)明經(jīng)過大量模擬,最終確定了澆注系統(tǒng)和補(bǔ)縮系統(tǒng)的位置,其中當(dāng)補(bǔ)縮系統(tǒng)的冒口中心置于鑄件內(nèi)側(cè)壁至鑄件幾何中心的任一位置時(shí),模擬結(jié)果顯示,制動(dòng)盤盤體中的縮孔、縮松、砂孔、氣孔、渣孔、裂紋等鑄造缺陷最少,甚至沒有缺陷。從模擬分析結(jié)果看,只有當(dāng)澆注系統(tǒng)和補(bǔ)縮系統(tǒng)的位置設(shè)計(jì)合理,且相互配合,才能有效地防止制動(dòng)盤盤體在鑄造過程中出現(xiàn)缺陷,使得鑄件充型均勻密實(shí),其綜合性能和整體質(zhì)量大幅度提高。本發(fā)明的澆注系統(tǒng)能有效確保金屬液平穩(wěn)均衡充型,排氣順暢,防止金屬液在充型過程中因紊流飛濺和對(duì)型腔的沖蝕等原因而使鑄件產(chǎn)生砂孔、渣孔、氣孔等鑄造缺陷,同時(shí)能強(qiáng)化鑄件的順序凝固趨勢,提高冒口的補(bǔ)縮效率;補(bǔ)縮系統(tǒng)中的冒口與補(bǔ)貼配合能實(shí)現(xiàn)鑄件的順序凝固,同時(shí)確保其在凝固過程中實(shí)現(xiàn)完全補(bǔ)縮,防止鑄件出現(xiàn)縮孔、縮松等缺陷,保證鑄件性能各向同性,防止鑄件發(fā)生變形。(2)根據(jù)步驟(1)的模擬分析結(jié)果,制定所述制動(dòng)盤盤體的鑄造工藝,采用底返引入金屬液的方式進(jìn)行底澆,其中金屬液由整流過濾裝置底部進(jìn)入型腔;在制動(dòng)盤盤體的實(shí)際鑄造過程中,金屬液進(jìn)入型腔的方式、位置、流速等各個(gè)參數(shù)均要符合模擬結(jié)果。(3)制作鑄造裝置,其澆注系統(tǒng)和補(bǔ)縮系統(tǒng)的位置符合步驟(1)中模擬分析的結(jié)果;在實(shí)際的鑄造裝置中,澆注系統(tǒng)和補(bǔ)縮系統(tǒng)的位置、形狀、尺寸、冒口的形狀及數(shù)量等各個(gè)參數(shù)均要符合模擬結(jié)果;(4)制作型芯;(5)合箱;(6)熔煉澆注;(7)打箱落砂并清理,切除冒口部分;(8)對(duì)鑄件進(jìn)行粗加工和熱處理;(9)對(duì)鑄件進(jìn)行調(diào)質(zhì)處理和精加工。熱處理的目的是消除鑄件組織中的柱狀晶、粗大的等軸晶和樹枝狀偏析,消除殘余應(yīng)力和部分缺陷,改善鑄件的力學(xué)性能。調(diào)質(zhì)處理為淬火和高溫回火的雙重?zé)崽幚?,其目的是保證鑄件具有優(yōu)良的綜合機(jī)械性能,既具有較高的強(qiáng)度又具有較高的塑性和韌性。對(duì)鑄件進(jìn)行無損檢測,同時(shí)滿足了射線探傷I級(jí)、超聲探傷I級(jí)和磁粉探傷I級(jí)的檢驗(yàn)要求。通過上述鑄造方法制備的制動(dòng)盤盤體,其屈服強(qiáng)度σ0.2≥950MPa。優(yōu)選的是,所述冒口的數(shù)量為一個(gè),且冒口中心置于鑄件幾何中心的位置。在上述任一方案中優(yōu)選的是,所述冒口的數(shù)量為一個(gè),且冒口中心置于距離鑄件幾何中心為10-15mm的位置。當(dāng)冒口為一個(gè)時(shí),冒口底部對(duì)應(yīng)一個(gè)內(nèi)澆口,冒口中心和內(nèi)澆口中心均置于鑄件幾何中心或鑄件幾何中心附近的位置。金屬液由內(nèi)澆口向四周流動(dòng),實(shí)現(xiàn)平穩(wěn)均衡的充型,所制備的制動(dòng)盤盤體中沒有縮孔、縮松、砂孔、氣孔、渣孔、裂紋等鑄造缺陷。在上述任一方案中優(yōu)選的是,所述冒口的數(shù)量至少為兩個(gè),且均勻分布在以鑄件幾何中心位置為中心的同一個(gè)圓周上。在上述任一方案中優(yōu)選的是,所述冒口的數(shù)量至少為兩個(gè),且冒口中心置于鑄件內(nèi)側(cè)壁的位置。在上述任一方案中優(yōu)選的是,所述冒口的數(shù)量至少為兩個(gè),且冒口中心置于距離鑄件幾何中心為(1/2)R的位置,其中R為鑄件內(nèi)側(cè)壁至鑄件幾何中心的距離。當(dāng)冒口為多個(gè)時(shí),并不是每一個(gè)冒口底部都對(duì)應(yīng)一個(gè)內(nèi)澆口,可以分段設(shè)置內(nèi)澆口。冒口中心和內(nèi)澆口中心均置于鑄件內(nèi)側(cè)壁或距離鑄件幾何中心一定距離的位置。金屬液由各個(gè)內(nèi)澆口向四周流動(dòng),實(shí)現(xiàn)平穩(wěn)均衡的充型,所制備的制動(dòng)盤盤體中沒有縮孔、縮松、砂孔、氣孔、渣孔、裂紋等鑄造缺陷。在上述任一方案中優(yōu)選的是,所述冒口的數(shù)量為六個(gè)或八個(gè)。在上述任一方案中優(yōu)選的是,內(nèi)澆口置于所述冒口的底部,并與鑄件相連。內(nèi)澆口位于補(bǔ)縮鑄件的冒口之下,與冒口連接為一體,提高補(bǔ)縮效率。在上述任一方案中優(yōu)選的是,所述金屬液在內(nèi)澆口的流速為20-60cm/s,確保金屬液平穩(wěn)均衡的充型。在上述任一方案中優(yōu)選的是,所述金屬液在鑄件中的上升速度為15-35mm/s,確保金屬液平穩(wěn)均衡的充型。本發(fā)明的制動(dòng)盤盤體的鑄造方法能實(shí)現(xiàn)鑄件的順序凝固和完全補(bǔ)縮,有效防止鑄件在鑄造過程中出現(xiàn)縮孔、縮松、砂孔、氣孔、渣孔、裂紋等缺陷,確保鑄件性能各向同性,保證具有高質(zhì)量制動(dòng)盤盤體的生產(chǎn)。本發(fā)明還提供一種制動(dòng)盤盤體的鑄造裝置,其包括澆注系統(tǒng)和補(bǔ)縮系統(tǒng),所述澆注系統(tǒng)包括澆口杯、直澆道、橫澆道、內(nèi)澆道和整流過濾裝置,所述補(bǔ)縮系統(tǒng)包括冒口和補(bǔ)貼,所述冒口中心置于鑄件內(nèi)側(cè)壁至鑄件幾何中心的任一位置。當(dāng)澆注系統(tǒng)和補(bǔ)縮系統(tǒng)的位置設(shè)計(jì)合理,且相互配合,才能有效地防止制動(dòng)盤盤體在鑄造過程中出現(xiàn)缺陷。澆注系統(tǒng)能有效確保金屬液平穩(wěn)均衡充型,排氣順暢,防止金屬液在充型過程中因紊流飛濺和對(duì)型腔的沖蝕等原因而使鑄件產(chǎn)生砂孔、渣孔、氣孔等鑄造缺陷,同時(shí)能強(qiáng)化鑄件的順序凝固趨勢,提高冒口的補(bǔ)縮效率;補(bǔ)縮系統(tǒng)中的冒口與補(bǔ)貼配合能實(shí)現(xiàn)鑄件的順序凝固,同時(shí)確保其在凝固過程中實(shí)現(xiàn)完全補(bǔ)縮,防止鑄件出現(xiàn)縮孔、縮松等缺陷,保證鑄件性能各向同性,防止鑄件發(fā)生變形。補(bǔ)縮系統(tǒng)的冒口中心置于鑄件內(nèi)側(cè)壁至鑄件幾何中心的任一位置時(shí),所制備的制動(dòng)盤盤體中沒有縮孔、縮松、砂孔、氣孔、渣孔、裂紋等鑄造缺陷。優(yōu)選的是,所述澆注系統(tǒng)還包括橫澆道溢流段。橫澆道溢流段是橫澆道的延伸部分,用來收集最初階段進(jìn)入澆注系統(tǒng)中的金屬液,這些金屬液因沖刷清洗澆注系統(tǒng)而溫度下降,同時(shí)變得不清潔,將其收集起來是為了避免該部分冷而不清潔的金屬液進(jìn)入型腔而影響鑄件質(zhì)量。在上述任一方案中優(yōu)選的是,所述澆注系統(tǒng)還包括集渣溢流片和集渣排氣棒。集渣溢流片用于收集充型時(shí)流程最長的冷而不清潔的金屬液;集渣排氣棒有利于充型時(shí)型腔的排氣,防止氣體在鑄件內(nèi)產(chǎn)生氣孔。在上述任一方案中優(yōu)選的是,所述澆口杯、直澆道、橫澆道和橫澆道溢流段依次相連,便于金屬液在進(jìn)入型腔前流通順暢,能夠平穩(wěn)的進(jìn)入內(nèi)澆道,進(jìn)而進(jìn)入型腔;所述冒口與補(bǔ)貼相連,補(bǔ)貼與鑄件相連,補(bǔ)貼可作為補(bǔ)縮通道,二者配合補(bǔ)償鑄件在凝固時(shí)的收縮,避免產(chǎn)生縮孔、縮松等缺陷。在上述任一方案中優(yōu)選的是,所述內(nèi)澆道置于冒口的下方和橫澆道的上方。在上述任一方案中優(yōu)選的是,內(nèi)澆口置于所述冒口的底部,并與鑄件相連。在上述任一方案中優(yōu)選的是,所述整流過濾裝置置于內(nèi)澆道與橫澆道之間。金屬液在橫澆道中穩(wěn)定后,先進(jìn)入整流過濾裝置進(jìn)行過濾,將夾渣、雜質(zhì)等使鑄件產(chǎn)生缺陷的物質(zhì)過濾掉,然后進(jìn)入內(nèi)澆道,進(jìn)而進(jìn)入型腔,有效防止鑄件產(chǎn)生渣孔、砂孔、裂紋等缺陷。在上述任一方案中優(yōu)選的是,所述冒口的數(shù)量為一個(gè),且冒口中心置于鑄件幾何中心的位置。在上述任一方案中優(yōu)選的是,所述冒口的數(shù)量為一個(gè),且冒口中心置于距離鑄件幾何中心為10-15mm的位置。在上述任一方案中優(yōu)選的是,所述冒口的數(shù)量至少為兩個(gè),且均勻分布在以鑄件幾何中心位置為中心的同一個(gè)圓周上。在上述任一方案中優(yōu)選的是,所述冒口的數(shù)量至少為兩個(gè),且冒口中心置于鑄件內(nèi)側(cè)壁的位置。在上述任一方案中優(yōu)選的是,所述冒口的數(shù)量至少為兩個(gè),且冒口中心置于距離鑄件幾何中心為(1/2)R的位置,其中R為鑄件內(nèi)側(cè)壁至鑄件幾何中心的距離。在上述任一方案中優(yōu)選的是,所述冒口的數(shù)量為六個(gè)或八個(gè)。在上述任一方案中優(yōu)選的是,所述澆口杯、直澆道、橫澆道和橫澆道溢流段由耐火材料制成,比如陶瓷管和/或陶瓷磚等,因?yàn)槟突鸩牧暇哂辛己玫谋靥匦?。在上述任一方案中?yōu)選的是,所述內(nèi)澆道由耐火材料制成或由砂型形成。內(nèi)澆道可由陶瓷管和/或陶瓷磚等具有良好保溫特性的耐火材料制成,也可由砂型形成,砂型具有很好的保溫效果。在上述任一方案中優(yōu)選的是,所述冒口由砂型形成或冒口外側(cè)包覆一層保溫耐火材料。砂型也具有良好的保溫發(fā)熱效果,也可在冒口外側(cè)包覆一層耐火石棉、陶瓷纖維等具有良好保溫發(fā)熱效果的保溫耐火材料。在上述任一方案中優(yōu)選的是,所述補(bǔ)貼由金屬材料或保溫耐火材料形成。補(bǔ)貼是補(bǔ)縮的通道,與冒口配合,對(duì)鑄件起到補(bǔ)償?shù)淖饔?。補(bǔ)縮時(shí),若增加鑄件的形狀,則補(bǔ)貼由金屬材料形成,該金屬材料與鑄件的材料相同;補(bǔ)縮時(shí),若不增加鑄件的形狀,則補(bǔ)貼由保溫耐火材料形成,起到保溫發(fā)熱的作用。在上述任一方案中優(yōu)選的是,所述集渣溢流片置于鑄件外側(cè)的上下邊緣。在上述任一方案中優(yōu)選的是,所述集渣排氣棒置于鑄件外側(cè),并與上下邊緣的集渣溢流片相連。在上述任一方案中優(yōu)選的是,所述冒口的形狀為圓柱體、腰圓體或多面體。冒口橫截面可為圓形、腰圓形、梯形、五邊形、六邊形等。本發(fā)明的制動(dòng)盤盤體的鑄造裝置能實(shí)現(xiàn)鑄件的順序凝固和完全補(bǔ)縮,有效防止鑄件在鑄造過程中出現(xiàn)縮孔、縮松、砂孔、氣孔、渣孔、裂紋等缺陷,確保鑄件性能各向同性,保證具有高質(zhì)量制動(dòng)盤盤體的生產(chǎn)。本發(fā)明還提供一種制動(dòng)盤盤體,該盤體由上述任一種鑄造方法和鑄造裝置制成。所制備的制動(dòng)盤盤體沒有縮孔、縮松、砂孔、氣孔、渣孔、裂紋等鑄造缺陷,且性能各向同性,具有較高且均勻的力學(xué)性能。本發(fā)明的鑄造方法和/或鑄造裝置的澆注系統(tǒng)和補(bǔ)縮系統(tǒng)可適用于鑄鋼及其他合金的高速列車制動(dòng)盤盤體的生產(chǎn)。附圖說明圖1為按照本發(fā)明的制動(dòng)盤盤體的鑄造方法的工藝流程圖;圖2為按照本發(fā)明的制動(dòng)盤盤體的鑄造方法的一優(yōu)選實(shí)施例的縮孔縮松缺陷模擬顯示圖;圖3為按照本發(fā)明的制動(dòng)盤盤體的鑄造裝置的一優(yōu)選實(shí)施例的剖面圖;圖4為按照本發(fā)明的制動(dòng)盤盤體的鑄造裝置的另一優(yōu)選實(shí)施例的立體結(jié)構(gòu)圖;圖5為按照本發(fā)明的制動(dòng)盤盤體的鑄造裝置的圖4的優(yōu)選實(shí)施例的45°仰視立體結(jié)構(gòu)圖;圖6為按照本發(fā)明的制動(dòng)盤盤體的鑄造裝置的另一優(yōu)選實(shí)施例的立體結(jié)構(gòu)圖;圖7為按照本發(fā)明的制動(dòng)盤盤體的鑄造裝置的圖6的優(yōu)選實(shí)施例的45°仰視立體結(jié)構(gòu)圖。圖中標(biāo)注說明:1-鑄件,2-冒口,3-補(bǔ)貼,4-澆口杯,5-直澆道,6-橫澆道,7-橫澆道溢流段,8-內(nèi)澆道,9-內(nèi)澆口,10-整流過濾裝置,11-集渣溢流片,12-集渣排氣棒,13-縮孔縮松。具體實(shí)施方式為了更進(jìn)一步了解本發(fā)明的
技術(shù)實(shí)現(xiàn)要素:,下面將結(jié)合具體實(shí)施例詳細(xì)闡述本發(fā)明。實(shí)施例一:以時(shí)速350km/h的高速列車鑄鋼制動(dòng)盤軸盤盤體(外徑為600mm,內(nèi)徑為240mm,)為例,其鑄造方法的工藝流程如圖1所示,其按照先后順序包括以下步驟:(1)通過計(jì)算機(jī)模擬軟件對(duì)制動(dòng)盤盤體的鑄造工藝和鑄造裝置進(jìn)行模擬分析,確定澆注系統(tǒng)和補(bǔ)縮系統(tǒng)的位置,補(bǔ)縮系統(tǒng)的冒口2中心置于鑄件1幾何中心位置;(2)根據(jù)步驟(1)的模擬分析結(jié)果,制定所述制動(dòng)盤盤體的鑄造工藝,采用底返引入金屬液的方式進(jìn)行底澆,其中金屬液由整流過濾裝置10底部進(jìn)入型腔;(3)制作鑄造裝置,其澆注系統(tǒng)和補(bǔ)縮系統(tǒng)的位置符合步驟(1)中模擬分析的結(jié)果;(4)制作型芯;(5)合箱;(6)熔煉澆注;(7)打箱落砂并清理,切除冒口部分;(8)對(duì)鑄件進(jìn)行粗加工和熱處理;(9)對(duì)鑄件進(jìn)行調(diào)質(zhì)處理和精加工。選用Magma模擬軟件對(duì)鑄造工藝和鑄造裝置進(jìn)行模擬分析。根據(jù)最佳模擬結(jié)果,制定實(shí)際的鑄造工藝流程和實(shí)際的鑄造裝置。在制動(dòng)盤盤體的鑄造過程中,金屬液進(jìn)入型腔的方式、位置、流速等各個(gè)參數(shù)均要符合模擬結(jié)果;鑄造裝置中澆注系統(tǒng)和補(bǔ)縮系統(tǒng)的位置、形狀、尺寸、冒口形狀及數(shù)量等各個(gè)參數(shù)也均要符合模擬結(jié)果。冒口2數(shù)量為一個(gè),其底部對(duì)應(yīng)一個(gè)內(nèi)澆口9。冒口2中心和內(nèi)澆口9中心均置于鑄件1幾何中心位置。金屬液由內(nèi)澆口向四周流動(dòng),實(shí)現(xiàn)穩(wěn)定均衡的充型。冒口2形狀為圓柱體,直徑為150mm,高度為150mm。通過Magma模擬軟件分析,冒口2為一個(gè),且冒口2中心置于鑄件1幾何中心位置時(shí),所制備的制動(dòng)盤盤體中沒有縮孔縮松13、砂孔、氣孔、渣孔、裂紋等鑄造缺陷。如圖2所示,鑄件1及冒口2在凝固后縮孔縮松缺陷的顯示,模擬表明,所有縮孔縮松13都集中在冒口2中,鑄件1內(nèi)部均勻致密,沒有縮孔縮松13。金屬液在內(nèi)澆口9的流速為20cm/s,金屬液在鑄件1中的上升速度為15mm/s。對(duì)鑄件進(jìn)行無損檢測,同時(shí)滿足了射線探傷I級(jí)、超聲探傷I級(jí)和磁粉探傷I級(jí)的檢驗(yàn)要求。制得的制動(dòng)盤盤體的屈服強(qiáng)度σ0.2=950MPa。如圖3所示,一種制動(dòng)盤盤體的鑄造裝置,其包括澆注系統(tǒng)和補(bǔ)縮系統(tǒng),澆注系統(tǒng)包括澆口杯4、直澆道5、橫澆道6、內(nèi)澆道8和整流過濾裝置10,補(bǔ)縮系統(tǒng)包括冒口2和補(bǔ)貼3,冒口2中心置于鑄件1幾何中心位置。澆注系統(tǒng)還包括橫澆道溢流段7、集渣溢流片11和集渣排氣棒12。澆口杯4、直澆道5、橫澆道6和橫澆道溢流段7依次相連,冒口2與補(bǔ)貼36相連。內(nèi)澆道8置于冒口2的下方和橫澆道6的上方。內(nèi)澆口9置于冒口2的底部,并與鑄件1相連。整流過濾裝置10置于內(nèi)澆道8與橫澆道6之間。冒口2數(shù)量為一個(gè),其形狀為圓柱體,直徑為150mm,高度為150mm。冒口2中心和內(nèi)澆口9中心均置于鑄件1幾何中心位置。澆口杯4、直澆道5、橫澆道6和橫澆道溢流段7均由耐火材料制成;內(nèi)澆道8由耐火材料制成;冒口2由砂型形成;補(bǔ)縮時(shí),需增加鑄件的形狀,所以補(bǔ)貼3由與鑄件材料相同的金屬材料形成。集渣溢流片11置于鑄件1外側(cè)的上下邊緣;有兩個(gè)集渣排氣棒12,均布于鑄件1外側(cè),并與上下邊緣的集渣溢流片11相連。一種制動(dòng)盤盤體,由上述的鑄造方法和鑄造裝置制備而成。所制備的制動(dòng)盤盤體沒有縮孔、縮松、砂孔、氣孔、渣孔、裂紋等鑄造缺陷,且性能各向同性,具有較高且均勻的力學(xué)性能。實(shí)施例二:以時(shí)速250km/h的高速列車鑄鋼制動(dòng)盤軸盤盤體(外徑為610mm,內(nèi)徑為240mm,)為例,其鑄造方法的工藝流程如圖1所示,其按照...