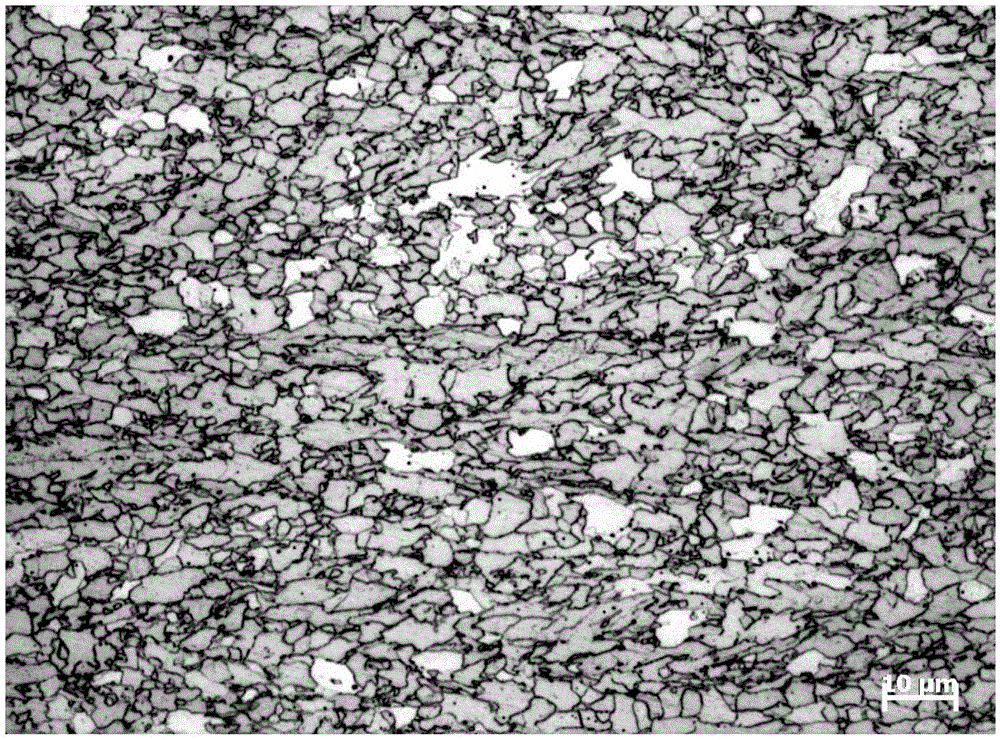
本發(fā)明涉及高強度微合金控軋控冷鋼,特別提供一種石油天然氣輸送用新型含Cu高強韌性兼具抗硫化氫腐蝕管線鋼。
背景技術:
:管道運輸工程是油氣采運發(fā)展的前提和基礎,處于油氣產(chǎn)業(yè)價值鏈的核心環(huán)節(jié),市場前景廣闊。隨著人類不斷對石油、天然氣兩大主要能源的消耗,正迫使油氣開采向著極端環(huán)境發(fā)展。相應地,對石油開采、油氣運輸所用的油管鋼材質的選擇帶來一系列問題。硫化氫腐蝕便是管線鋼所面臨的一個嚴峻問題。如何在保證高強韌性以及節(jié)約成本的前提下仍然保持較好的抗硫化氫腐蝕性能對管線鋼的發(fā)展將具有重要指導意義。Cu合金化元素在鋼中具有三大主要作用:1)提高基體強度;2)提高耐腐蝕性能;3)改善加工性能。這為含Cu鋼的開發(fā)提供了潛能。早期含Cu低合金高強度(HSLA)鋼的開發(fā)證實了Cu合金化元素加入到鋼結構材料的可行性,這種含銅HSLA鋼不僅具有優(yōu)良的焊接性能,而且在不影響韌性的同時還能大幅度提高其強度,這為Cu合金化元素在微合金管線鋼中的應用指明了思路。在含Cu高強度低合金結構鋼的研究中可以看到,以往的研究者也認識到了Cu合金化元素在鋼中所起到的強化作用,然而在他們所報道的實施例中,極少注意到含Cu鋼中經(jīng)過強化熱處理后富Cu析出相的“氫陷阱”作 用,從而在保證高強度的同時仍具有較好的抗硫化氫腐蝕性能。技術實現(xiàn)要素:本發(fā)明的目的在于提供一種在保證高強韌性的同時具有優(yōu)異的耐硫化氫腐蝕性能的新型含Cu管線鋼,以使材料滿足不斷發(fā)展的綜合性能指標的更高要求。本發(fā)明的技術方案是:本發(fā)明經(jīng)過前期實驗研究,提出了一種新型具有高強韌性的含Cu管線鋼,Cu合金化元素對該管線鋼的強化起到關鍵性作用。其特征在于,在軋后或重新再加熱時效熱處理過程中,通過Cu的析出沉淀強化,不僅能大幅度提高強度,而且細小彌散析出的富Cu相可成為氫陷阱,同時提高管線鋼的抗硫化氫腐蝕性能。根據(jù)上述構思所提出的含Cu管線鋼,其微觀組織包括多邊形鐵素體和針狀鐵素體,合金成分及重量百分比為:C:0.015~0.035%;Si:0.10~0.20%;Mn:0.8~1.1%;Cu:1.0~2.0%;Ni:0.30~0.40%;Mo:0.30~0.40%;Cr:0.30~0.40%;Nb:0.04~0.06%;余量為Fe和其他不可避免的雜質。優(yōu)選的化學成分如下:C:0.020~0.030%;Si:0.10~0.15%;Mn:0.9~1.1%;Cu:1.0~2.0%;Ni:0.30~0.35%;Mo:0.30~0.35%;Cr:0.30~0.35%;Nb:0.045~0.055%;余量為Fe和其他不可避免的雜質。傳統(tǒng)的管線鋼主要通過兩種方式強化:一是通過提高合金化元素;二 是通過熱機械控制軋制和控制冷卻。提高合金化元素主要以提高Mn的含量為主,而Mn含量過高,對管線鋼的抗硫化氫性能不利。本發(fā)明通過采用超低C含量來保證管線鋼的高韌性及焊接性。本發(fā)明通過適當降低Mn含量,增加Cu含量,一方面Cu含量增加可以抵消Mn含量降低所損失的強度,另一方面,含Cu管線鋼通過強化熱處理后均勻彌散析出納米富Cu相起到“氫陷阱”作用,同時改善管線鋼的抗硫化氫腐蝕性能。本發(fā)明中Cu元素對該管線鋼的強化和抗硫化氫腐蝕性能起到關鍵性作用,其含量為1.0~2.0%,Cu在鋼中超過0.5%就可以通過沉淀強化提高鋼的強度和硬度,但Cu含量在1.0%以下以及2.0%以上銅鋼的沉淀硬化敏感性比較小,而且Cu含量過高會對鋼的沖擊韌性和熱加工性能產(chǎn)生不利影響。本發(fā)明通過加入適量的Cr、Ni、Mo元素來改善鋼中Cu的析出行為。本發(fā)明除延用傳統(tǒng)管線鋼生產(chǎn)過程中熱機械控制軋制和控制冷卻的優(yōu)勢外,增加Cu的析出強化熱處理后,充分發(fā)揮Cu合金化元素在鋼中的優(yōu)勢,同時大幅度提高鋼的強度和抗硫化氫腐蝕性能。本發(fā)明成分范圍內的含Cu管線鋼可采用如下方式生產(chǎn):原材料均采用合金元素以純金屬或中間合金的形式加入。經(jīng)配料、混料后,放入真空冶煉爐中熔煉,澆鑄成合金鑄錠。鑄錠在切除帽口、扒除表面氧化皮后,在1050℃左右開坯,開坯后沿長度方向下料,進入下一步熱加工工序。確定了材料的成分后,熱加工工藝和強化熱處理制度很重要,它決定 了材料的性能指標。本發(fā)明還提供了用于達到管線鋼最佳力學性能指標相應的強化熱處理工藝:(1)冶煉后奧氏體單相區(qū)加熱鍛造,鍛后空冷,奧氏體單相區(qū)加熱溫度不超過1080℃,鍛造過程中至少3次回爐,鍛造比≤4(優(yōu)選奧氏體單相區(qū)加熱溫度為1050℃,鍛造過程中回爐4次,鍛造比為3);(2)鍛后熱機械控制軋制(TMCP),初軋溫度為1000-1030℃,終軋溫度為≥800℃,軋后以20~30℃/s水冷,熱軋累積壓下量達到90%以上,終冷溫度為400~600℃(優(yōu)選420℃),而后空冷。熱軋過程中,分七道次進行熱軋,每道次壓下量不得大于35%;(3)熱軋后時效,時效后空冷。所述步驟(3)中,熱軋后溫度降至450~600℃或降溫后重新加熱到450~600℃,時效時間為10分鐘~10小時,時效后空冷。優(yōu)選的時效處理制度為:450℃時效6小時,空冷;或500℃時效1小時,空冷;或550℃時效1小時,空冷。最優(yōu)選的時效處理制度為:500℃時效1小時,空冷。本發(fā)明的有益效果是:1、本發(fā)明含1.0%Cu的管線鋼在強化熱處理后強度就高于傳統(tǒng)X80級別管線鋼,且韌性與傳統(tǒng)X80級別管線鋼相當,更高Cu含量的加入在強化熱處理后強度可達X120級別,并保持較好的韌性。2、本發(fā)明所述含Cu管線鋼顯微組織包括多邊形鐵素體和針狀鐵素體,與現(xiàn)有商用管線鋼相比能夠大幅度提高強度的同時具有優(yōu)異的抗硫化氫腐蝕性能。附圖說明圖1為本發(fā)明含1.5Cu管線鋼軋態(tài)顯微組織形貌。圖2為本發(fā)明含1.0Cu管線鋼在500℃時效1小時后的顯微組織形貌。具體實施方式下面將通過不同實施例和對比例的比較來描述本發(fā)明,這些實施例僅用于解釋的目的,本發(fā)明并不局限于這些實施例中。表1為實施例和對比例中各種鋼的化學成分。各種實施例鋼按照表2參數(shù)經(jīng)過熱機械控制軋制和控制冷卻制成鋼板,按照表3進行時效強化處理,對比例鋼的熱軋及冷卻參數(shù)按照傳統(tǒng)管線鋼生產(chǎn)工藝進行,表3同時列出了實施例和對比例鋼的力學性能。硫化氫腐蝕試驗只對氫致開裂實驗實施,參照NACETM0284-2003標準,實驗溶液選用標準溶液A。實施例及對比例的抗氫致開裂性能見表4。表1實施例和對比例化學成分(wt%)編號CSiMnMoCuCrNiNbVSP備注10.0300.141.090.311.060.320.320.04--0.00110.005實施例20.0200.121.030.311.460.310.310.05--0.00110.005實施例30.0230.131.060.302.000.300.300.06--0.00100.005實施例40.0250.170.930.341.700.330.320.05--0.00060.004實施例50.0350.190.860.351.250.370.370.05--0.00130.003實施例60.0170.201.100.381.870.400.400.05--0.00150.003實施例70.0280.281.900.220.20--0.290.0810.0310.00200.012對比例80.050.231.770.24--0.280.0160.079--0.00160.0076對比例90.050.221.920.290.250.410.440.0820.0090.00200.0078對比例表2熱機械控制軋制和控制冷卻參數(shù)表3強化熱處理工藝和力學性能*沖擊試樣為半尺寸:5mm×10mm×55mm表4抗氫致開裂參數(shù)從實施例1-6的材料綜合性能可以看出,按照本發(fā)明所給出的成分,含Cu管線鋼具有較高的強韌性兼具優(yōu)異的抗硫化氫腐蝕性能。上述實施例只為說明本發(fā)明的技術構思及特點,其目的在于讓熟悉此項技術的人士能夠了解本發(fā)明的內容并據(jù)以實施,并不能以此限制本發(fā)明的保護范圍。凡根據(jù)本發(fā)明精神實質所作的等效變化或修飾,都應涵蓋在本發(fā)明的保護范圍之內。當前第1頁1 2 3