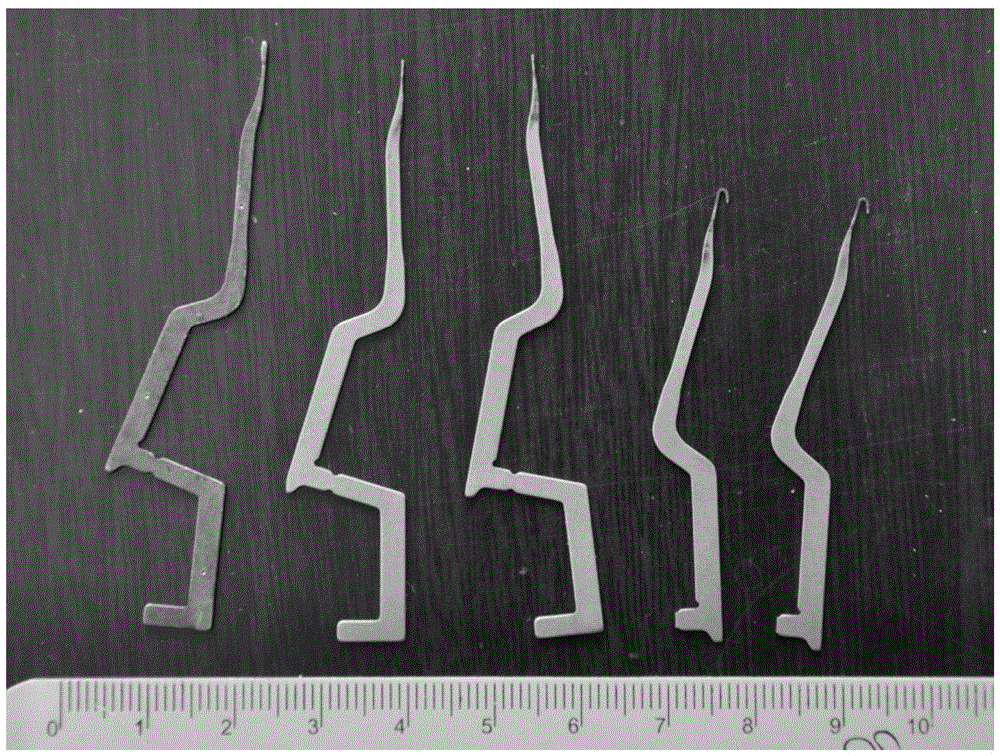
本發(fā)明屬于合金鋼領(lǐng)域,具體提供一種超高強(qiáng)高韌馬氏體時(shí)效鋼及其制備方法和應(yīng)用。
背景技術(shù):
:對于紡織鉤針、撞針等高強(qiáng)度結(jié)構(gòu)件的制備,高強(qiáng)度低合金鋼憑借材料成本的優(yōu)勢,始終成為企業(yè)的首選。與高強(qiáng)度低合金鋼相比,馬氏體時(shí)效鋼具有明顯的強(qiáng)韌性優(yōu)勢,但一直無法得到企業(yè)的認(rèn)可而實(shí)現(xiàn)產(chǎn)業(yè)化應(yīng)用。在馬氏體時(shí)效鋼的發(fā)展過程中,強(qiáng)韌性匹配與使用成本是影響馬氏體時(shí)效鋼應(yīng)用前景的兩個(gè)核心問題,一方面,在保證韌性的前提下實(shí)現(xiàn)馬氏體時(shí)效鋼強(qiáng)度的提高,迎合產(chǎn)品的輕量化、節(jié)能減排以及安全環(huán)保等設(shè)計(jì)宗旨,是決定馬氏體時(shí)效鋼應(yīng)用前景的關(guān)鍵因素;另一方面,與普通的高強(qiáng)度低合金鋼相比,馬氏體時(shí)效鋼的強(qiáng)韌性優(yōu)勢明顯,但由于其高含量的合金元素,馬氏體時(shí)效鋼的材料成本同樣很高,如何充分利用馬氏體時(shí)效鋼的性能優(yōu)勢,降低結(jié)構(gòu)材料使用成本,是影響馬氏體時(shí)效鋼應(yīng)用前景的關(guān)鍵。技術(shù)實(shí)現(xiàn)要素:為解決上述技術(shù)問題,本發(fā)明提供一種超高強(qiáng)高韌的馬氏體時(shí)效鋼及其制備方法和應(yīng)用,本發(fā)明的整體技術(shù)方案為:本發(fā)明在現(xiàn)有的高強(qiáng)度馬氏體時(shí)效鋼基礎(chǔ)上,適量提高合金元素的含 量并優(yōu)化合金元素配比,開發(fā)出抗拉強(qiáng)度達(dá)到3000MPa的新型超高強(qiáng)度馬氏體時(shí)效鋼,同時(shí)通過優(yōu)化冶煉工藝,將鋼中雜質(zhì)元素含量降到較高級(jí)別,保證馬氏體時(shí)效鋼具有高強(qiáng)度的同時(shí)兼顧良好的韌性。根據(jù)上述設(shè)計(jì)思想,本發(fā)明的具體技術(shù)方案為:超高強(qiáng)高韌馬氏體時(shí)效鋼的化學(xué)成分為(wt.%):C:≤0.008%,Ni:18.0-20.0%,Co:15.0-18.0%,Mo:7.0-8.0%,Ti:1.5-2.5%,O≤0.01%,N≤0.01%,P≤0.01%,S≤0.01%,F(xiàn)e:余量。優(yōu)選為:C:≤0.005%,Ni:18.5-19.5%,Co:15.5-16.5%,Mo:7.0-7.5%,Ti:1.5-1.8%,O+N≤0.004%,P≤0.005%,S≤0.005%,F(xiàn)e:余量。本發(fā)明所述馬氏體時(shí)效鋼的制備工藝,其特征在于,包括以下步驟:真空熔煉—真空自耗—均勻化處理—鍛造—熱處理,其中:真空熔煉:合金元素均以高純度純金屬的形式加入,將配料置于真空感應(yīng)爐中進(jìn)行真空熔煉、Ca處理和真空脫氣,嚴(yán)格控制鋼中雜質(zhì)元素含量,之后澆鑄成鑄錠。真空自耗:將真空熔煉并澆鑄成的鋼錠加工成自耗電極,之后將自耗電極置于真空自耗電弧爐中完成真空自耗結(jié)晶重熔工藝過程。均勻化處理:將自耗重熔以后澆鑄成的鋼錠置于熱處理爐中,將熱處理爐升溫至1000-1200℃,保溫15-25h。鍛造處理:均勻化處理后的鋼錠進(jìn)行鍛造加工,鍛造初始溫度為1000-1250℃,終鍛溫度為700-900℃。熱處理:固溶處理830-870℃保溫1-2h,空冷到室溫;深冷處理:液氮 中保溫5h以上;時(shí)效處理:480-520℃保溫1-6h,空冷。本發(fā)明所述馬氏體時(shí)效鋼的制備工藝,其特征在于:所述超純金屬原材料中的雜質(zhì)元素總含量(Si+Mn+P+S+O+N)%<0.1wt%。真空感應(yīng)爐和真空自耗電弧爐的真空度均小于10-4Pa。所述鍛造過程中的鍛造比>10。本發(fā)明還提供了一種適用于所述馬氏體時(shí)效鋼的最優(yōu)化的熱處理工藝,其特征在于:850℃保溫1.5h,空冷到室溫,液氮中保溫6h,500℃保溫2h,空冷。本發(fā)明所述馬氏體時(shí)效鋼可以用于制備紡織鉤針,包括以下步驟:真空熔煉—真空自耗—均勻化處理—鍛造—熱軋—冷軋—深冷處理—粗加工成型—時(shí)效處理—精加工成型。采用上述方法制得的紡織鉤針,不僅具有優(yōu)異的強(qiáng)韌性匹配,而且具有優(yōu)異的耐摩擦磨損性能,可以很好的滿足紡織工業(yè)的需求。本發(fā)明所述馬氏體時(shí)效鋼還可以用于制備撞針,包括以下步驟:真空熔煉—真空自耗—均勻化處理—鍛造—熱軋—深冷處理—粗加工—時(shí)效處理—精加工成型。采用上述方法制得的撞針,具有優(yōu)異的抗疲勞性能和耐高溫軟化性能,可以很好的滿足撞針服役條件對材料的性能要求。本發(fā)明所述馬氏體時(shí)效鋼具有高的強(qiáng)韌性匹配,其σb≥3000MPa,σ0.2≥2600MPa,δ≥9%,ψ≥30%,適用于對結(jié)構(gòu)材料的強(qiáng)韌性要求苛刻的環(huán)境。本發(fā)明所述馬氏體時(shí)效鋼已成功應(yīng)用于紡織鉤針的制備中,制得的紡織鉤針具有優(yōu)異的使用性能,與傳統(tǒng)材料制備的鉤針相比,具有更低的使用成本。采用本發(fā)明所述馬氏體時(shí)效鋼制備的撞針其使用壽命是傳統(tǒng)材料 撞針的10倍,具有優(yōu)異的使用性能,具備廣闊的應(yīng)用前景。附圖說明圖1為實(shí)施例8制備得到的高性能鉤針示意圖。圖2為實(shí)施例9制備得到的高性能撞針示意圖。具體實(shí)施方式實(shí)施例1按下述名義成分(wt.%):C:0.008%,Ni:21.5%,Co:17.0%,Mo:7.5%,Ti:1.7%,O:0.01%,N:0.01%,P:0.01%,S:0.01%,F(xiàn)e:余量,配料和混料后在真空感應(yīng)熔煉爐中熔煉,澆鑄成鑄錠以后進(jìn)行真空自耗以及均勻化處理,并按下述工藝進(jìn)行熱加工和熱處理:(1)在奧氏體單相區(qū)鍛造,鍛造初始溫度為1150℃,終鍛溫度為850℃,鍛造比為12,鍛造之后空冷到室溫;(2)熱處理制度按如下步驟進(jìn)行,固溶處理(850℃保溫1.5h,空冷到室溫),深冷處理(液氮中保溫6h),時(shí)效處理(500℃保溫2h,空冷)。顯微組織觀察以及XRD分析表明,該合金成分的馬氏體時(shí)效鋼,經(jīng)過熱處理后的殘余奧氏體含量較多。對其熱處理態(tài)的材料進(jìn)行力學(xué)性能檢測,其力學(xué)性能為抗拉強(qiáng)度2755MPa,屈服強(qiáng)度為2532MPa,延伸率為9%,斷面收縮率為35%。該合金成分的馬氏體時(shí)效鋼中的Ni含量高于權(quán)利要求1中Ni含量的上限值(20.0%),造成了鋼中殘余奧氏體含量過高,進(jìn)而導(dǎo)致強(qiáng)度較低。實(shí)施例2按下述名義成分(wt.%):C:0.008%,Ni:19.0%,Co:14.0%,Mo:7.5%,Ti:1.7%,O:0.01%,N:0.01%,P:0.01%,S:0.01%,F(xiàn)e:余量,配料和混料后在真空感應(yīng)熔煉爐中熔煉,澆鑄成鑄錠以后進(jìn)行真空自耗以及均勻化處理,并按實(shí)施例1所述的工藝進(jìn)行熱加工和熱處理。對其熱處理態(tài)的材料進(jìn)行力學(xué)性能檢測,其力學(xué)性能為抗拉強(qiáng)度2975MPa,屈服強(qiáng)度為2814MPa,延伸率為8%,斷面收縮率為33%。材料的斷裂韌性為K1C=23MPa.m1/2。該合金成分的馬氏體時(shí)效鋼的Co含量低于權(quán)利要求1中的鈷含量的下限值15.0%,導(dǎo)致鋼中的析出強(qiáng)化作用減弱,最終導(dǎo)致其強(qiáng)度降低。實(shí)施例3按下述名義成分(wt.%):C:0.008%,Ni:19.0%,Co:17.0%,Mo:7.5%,Ti:1.4%,O:0.01%,N:0.01%,P:0.01%,S:0.01%,F(xiàn)e:余量,配料和混料后在真空感應(yīng)熔煉爐中熔煉,澆鑄成鑄錠以后進(jìn)行真空自耗以及均勻化處理,并按實(shí)施例1所述的工藝進(jìn)行熱加工和熱處理。對其熱處理態(tài)的材料進(jìn)行力學(xué)性能檢測,其力學(xué)性能為抗拉強(qiáng)度2915MPa,屈服強(qiáng)度為2794MPa,延伸率為9%,斷面收縮率為35%。材料的斷裂韌性為K1C=20MPa.m1/2。該合金成分的馬氏體時(shí)效鋼的Ti含量低于權(quán)利要求1中的鈦含量的下限值1.5%,Ti是馬氏體時(shí)效鋼最主要的強(qiáng)化元素,其含量的降低會(huì)導(dǎo)致鋼的強(qiáng)度降低。實(shí)施例4在實(shí)施例1-3的基礎(chǔ)上,調(diào)整了Cr當(dāng)量與Ni當(dāng)量的比值,重新優(yōu)化了合金成分。按下述名義成分(wt.%):C:0.008%,Ni:19.0%,Co:16.0%,Mo:7.2%,Ti:1.7%,O+N:0.004%,P:0.005%,S:0.005%,F(xiàn)e:余量,配料和混料后在真空感應(yīng)熔煉爐中熔煉,澆鑄成鑄錠以后加工成自耗電極并進(jìn)行自耗重熔工藝以及均勻化處理,之后按實(shí)施例1所述的工藝進(jìn)行熱加工和熱處理,并測試了不同時(shí)效處理?xiàng)l件下的室溫拉伸性能,拉伸力學(xué)性能測試結(jié)果如表1所示。表1實(shí)施例4拉伸力學(xué)性能測試結(jié)果時(shí)效工藝抗拉強(qiáng)度,MPa屈服強(qiáng)度,MPa延伸率,%面縮,%480℃2h293328559.535480℃4h297428969.435480℃6h299229109.432500℃1h299428329.636500℃2h301529119.234500℃4h295228969.037根據(jù)表1所示的力學(xué)性能結(jié)果,得出該合金的最優(yōu)化熱處理工藝為:850℃保溫1.5h,空冷到室溫,液氮處理6h,500℃保溫2h,空冷。經(jīng)過最優(yōu)化熱處理工藝得到的峰時(shí)效態(tài)樣品的斷裂韌性為K1C=80MPa.m1/2。實(shí)施例5以實(shí)施例4的合金成分為基礎(chǔ),但與實(shí)施例4不同的是,在真空感應(yīng)熔煉過程中的真空度高于權(quán)利要求5中要求的10-4Pa,且不進(jìn)行后續(xù)的自耗 重熔工藝,最終會(huì)導(dǎo)致鋼中的雜質(zhì)元素P、S、O、N的含量偏高。按下述名義成分(wt.%):C:0.008%,Ni:19.0%,Co:16.0%,Mo:7.2%,Ti:1.7%,O:0.02%,N:0.02%,P:0.015%,S:0.015%,F(xiàn)e:余量,配料和混料后在真空感應(yīng)熔煉爐中熔煉,澆鑄成鑄錠以后直接進(jìn)行均勻化處理,并按實(shí)施例1所述的工藝進(jìn)行熱加工和熱處理。該合金成分的馬氏體時(shí)效鋼的雜質(zhì)元素含量超過了權(quán)利要求1中雜質(zhì)元素含量的上限值。在實(shí)施例4所述的最優(yōu)化熱處理工藝條件下,其力學(xué)性能為抗拉強(qiáng)度3020MPa,屈服強(qiáng)度為2920MPa,延伸率為9%,斷面收縮率為30%,材料的斷裂韌性為K1C=8MPa.m1/2。其拉伸性能與實(shí)施例4的拉伸性能相當(dāng),而斷裂韌性遠(yuǎn)低于實(shí)施例4的斷裂韌性,說明雜質(zhì)元素含量過高會(huì)大大惡化材料的韌性。實(shí)施例6按下述名義成分(wt.%):C:0.008%,Ni:18.0%,Co:16.0%,Mo:7.0%,Ti:1.5%,O+N:0.004%,P:0.005%,S:0.005%,F(xiàn)e:余量,配料和混料后在真空感應(yīng)熔煉爐中熔煉,澆鑄成鑄錠以后加工成自耗電極并進(jìn)行自耗重熔工藝以及均勻化處理,之后按實(shí)施例1所述的工藝進(jìn)行熱加工和熱處理。對其熱處理態(tài)的材料進(jìn)行力學(xué)性能檢測,其力學(xué)性能為抗拉強(qiáng)度3010MPa,屈服強(qiáng)度為2895MPa,延伸率為9.5%,斷面收縮率為36%,斷裂韌性K1C=85MPa.m1/2實(shí)施例7按下述名義成分(wt.%):C:0.008%,Ni:20.0%,Co:17.0%,Mo:7.5%,Ti:2.5%,O+N:0.004%,P:0.005%,S:0.005%,F(xiàn)e:余量,配料和混料后在真空感應(yīng)熔煉爐中熔煉,澆鑄成鑄錠以后加工成自耗電極并進(jìn)行自耗重熔工藝以及均勻化處理,之后按實(shí)施例1所述的工藝進(jìn)行熱加工和熱處理。對其熱處理態(tài)的材料進(jìn)行力學(xué)性能檢測,其力學(xué)性能為抗拉強(qiáng)度3025MPa,屈服強(qiáng)度為2905MPa,延伸率為8%,斷面收縮率為34%,斷裂韌性K1C=50MPa.m1/2實(shí)施例8按照實(shí)施例4設(shè)計(jì)的合金成分進(jìn)行配料,之后按如下步驟制備馬氏體時(shí)效鋼材料的高性能紡織鉤針。真空熔煉:合金元素均以高純度純金屬的形式加入,將配料置于真空感應(yīng)爐中進(jìn)行真空熔煉、Ca處理和真空脫氣,之后澆鑄成鑄錠,熔煉過程中的真空度≤10-4Pa。真空自耗:將真空熔煉并澆鑄成的鋼錠加工成自耗電極,之后將自耗電極置于真空自耗電弧爐中完成真空自耗結(jié)晶重熔工藝過程,真空自耗過程的真空度≤10-4Pa。均勻化處理:將自耗重熔以后澆鑄成的鋼錠置于400℃的熱處理爐中,將熱處理爐升溫至1200℃,保溫20h。鍛造處理:均勻化處理后的鋼錠經(jīng)鍛造加工成60mm厚的熱軋板坯, 鍛造初始溫度為1200℃,終鍛溫度為900℃。熱軋步驟:將鍛造后的熱軋板坯加熱到1150℃,首先在二輥軋機(jī)進(jìn)行粗軋,經(jīng)5道次軋制成7mm厚的中間坯;之后的精軋過程中,采用四輥軋機(jī),將中間坯軋制成4mm厚鋼板,終軋溫度為800℃。冷軋步驟:將熱軋得到的4mm厚熱軋鋼板在冷軋機(jī)上進(jìn)行軋制,冷軋采用20輥冷軋機(jī),經(jīng)7道次軋制,終軋至1mm厚的鋼帶。深冷處理:將冷軋鋼帶在液氮(-196℃)中保溫6h,然后將鋼帶從液氮中取出,恢復(fù)到室溫。粗加工成型:以深冷處理后的鋼帶為原材料,根據(jù)產(chǎn)品的設(shè)計(jì)尺寸,保證足夠的加工余量的前提下,將鋼帶粗加工成產(chǎn)品的坯料件。時(shí)效處理:將產(chǎn)品坯料件置于500℃的真空熱處理爐中保溫2h,取出恢復(fù)到室溫。精加工成型:時(shí)效處理后的坯料件,按照產(chǎn)品尺寸精加工即可得到高性能馬氏體時(shí)效鋼紡織鉤針。按上述工藝制備得到的馬氏體時(shí)效鋼紡織鉤針具有優(yōu)異的強(qiáng)韌性匹配,與傳統(tǒng)材料T8制備的紡織鉤針相比,服役壽命提高了5倍,其使用成本明顯低于T8,已經(jīng)成功替代傳統(tǒng)材料并實(shí)現(xiàn)批量生產(chǎn)。實(shí)施例9按照實(shí)施例4設(shè)計(jì)的合金成分進(jìn)行配料,之后按如下步驟制備馬氏體時(shí)效鋼材料的高性能撞針。真空熔煉:合金元素均以高純度純金屬的形式加入,將配料置于真空 感應(yīng)爐中進(jìn)行真空熔煉、Ca處理和真空脫氣,之后澆鑄成鑄錠,熔煉過程中的真空度≤10-4Pa。真空自耗:將真空熔煉并澆鑄成的鋼錠加工成自耗電極,之后將自耗電極置于真空自耗電弧爐中完成真空自耗結(jié)晶重熔工藝過程,真空自耗過程的真空度≤10-4Pa。均勻化處理:將自耗重熔以后澆鑄成的鋼錠置于400℃的熱處理爐中,將熱處理爐升溫至1200℃,保溫20h。鍛造處理:均勻化處理后的鋼錠經(jīng)鍛造加工成60mm厚的熱軋板坯,鍛造初始溫度為1200℃,終鍛溫度為900℃,鍛比為11。熱軋步驟:將鍛造后的熱軋板坯加熱到1150℃,首先在二輥軋機(jī)進(jìn)行粗軋,經(jīng)3道次軋制成20mm厚的中間坯;之后的精軋過程中,采用四輥軋機(jī),將中間坯軋制成17mm厚鋼板,終軋溫度為800℃。深冷處理:將熱軋鋼板在液氮(-196℃)中保溫6h,然后將熱軋鋼板從液氮中取出,恢復(fù)到室溫。粗加工成型:以深冷處理后的熱軋鋼板為原材料,根據(jù)產(chǎn)品的設(shè)計(jì)尺寸,保證足夠的加工余量的前提下,將熱軋鋼板粗加工成產(chǎn)品的坯料件。時(shí)效處理:將產(chǎn)品坯料件置于480-520℃的真空熱處理爐中保溫2h-4h,取出恢復(fù)到室溫。精加工成型:時(shí)效處理后的坯料件,按照產(chǎn)品尺寸精加工即可得到高性能馬氏體時(shí)效鋼撞針。按上述工藝制備得到的馬氏體時(shí)效鋼材料撞針,經(jīng)不同時(shí)效處理工藝后的性能差異較大,其實(shí)驗(yàn)測試結(jié)果如表2所示。表2實(shí)施例5撞針的測試結(jié)果時(shí)效處理工藝測試結(jié)果480℃2h60萬次后失效,撞針彎曲480℃4h350萬次后失效,撞針頭部斷裂500℃2h460萬次后失效,撞針頭部斷裂500℃4h800萬次后失效,撞針頭部斷裂520℃2h600萬次后失效,撞針頭部斷裂520℃4h90萬次后失效,撞針彎曲從表2可以看出,在時(shí)效處理工藝為500℃保溫4h的條件下得到的撞針具有最優(yōu)異的使用性能,其使用壽命是傳統(tǒng)材料S7制備的撞針的10倍,具有很大的應(yīng)用前景。上述實(shí)施例只為說明本發(fā)明的技術(shù)構(gòu)思及特點(diǎn),其目的在于讓熟悉此項(xiàng)技術(shù)的人士能夠了解本發(fā)明的內(nèi)容并據(jù)以實(shí)施,并不能以此限制本發(fā)明的保護(hù)范圍。凡根據(jù)本發(fā)明精神實(shí)質(zhì)所作的等效變化或修飾,都應(yīng)涵蓋在本發(fā)明的保護(hù)范圍之內(nèi)。當(dāng)前第1頁1 2 3