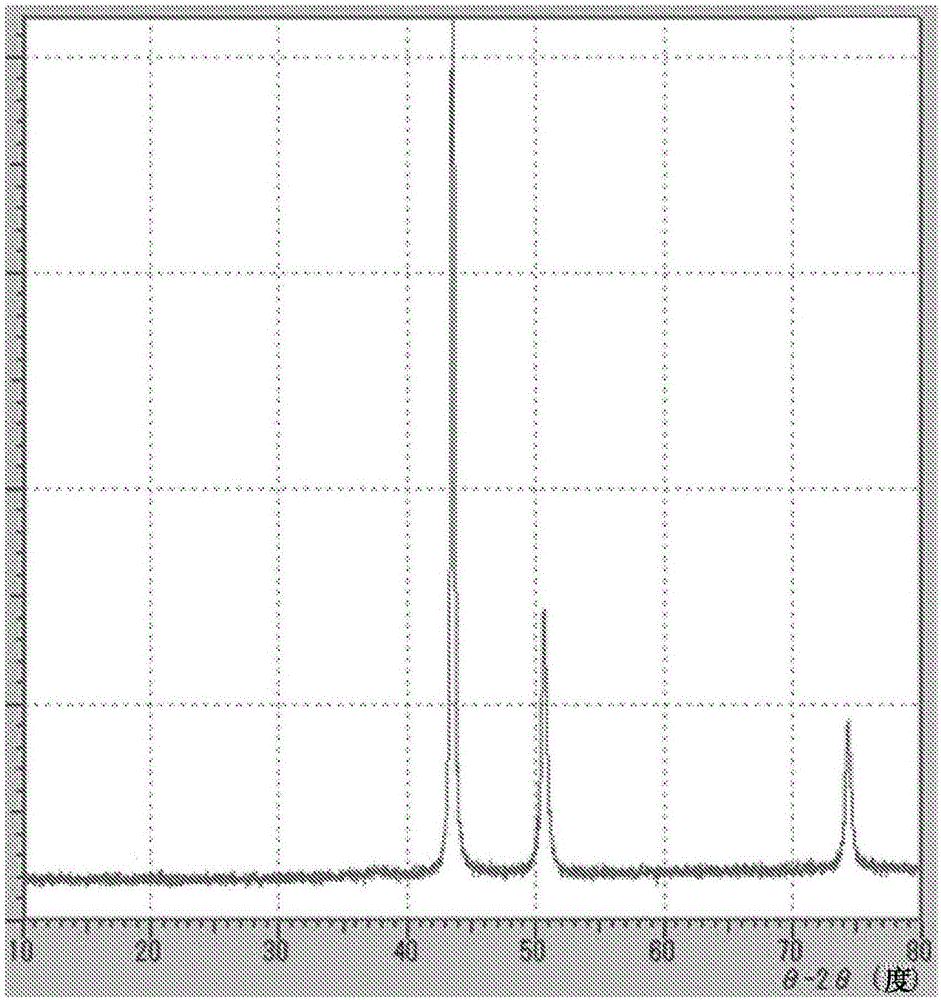
本發(fā)明涉及被覆銅顆粒及其制造方法。
背景技術(shù):
:在近年來的電子設(shè)備相關(guān)領(lǐng)域中,被稱為可印刷電子的
技術(shù)領(lǐng)域:
受到關(guān)注,該可印刷電子不需要利用曝光對配線或保護(hù)膜等進(jìn)行圖案化,而通過噴墨或印刷法直接形成微米級的微細(xì)配線。最初,金、銀等的微粒為中心,但金存在成本問題,銀存在電遷移的問題并且在硫化氣體等導(dǎo)致的腐蝕等耐腐蝕性方面存在課題。作為解決這些問題的手段,銅系材料受到關(guān)注。銅系材料除了與金、銀同樣地顯示出高導(dǎo)電性以外,在電遷移方面與銀相比格外優(yōu)異,耐腐蝕性也優(yōu)異。作為貴金屬的金、銀具有比較難以受到氧化的特性,因此,在制作金屬微粒分散液時(shí),容易維持所含有的金屬微粒而不使其表面形成氧化覆膜。與此相對,銅具有比較容易被氧化的特性,特別是若為粒徑在200nm以下的微細(xì)的銅微粒,則由于尺寸效應(yīng)和比表面積的關(guān)系,該傾向變得更為顯著。在制備銅微粒分散液時(shí),所含有的銅微粒在短時(shí)間內(nèi)形成其表面被氧化膜覆蓋的狀態(tài),進(jìn)而氧化覆膜的厚度也經(jīng)時(shí)地增加,還有不少情況下銅微粒的一大半粒徑被轉(zhuǎn)變?yōu)檠趸~的氧化膜。另外,在200nm以下的銅微粒的情況下,顆粒表面的活性達(dá)到非常高的狀態(tài),即便是在氮?dú)獾确腔钚詺夥障禄蛘婵諚l件下進(jìn)行加熱燒制的方法,也會(huì)因氣氛中存在的微量的氧而使氧化進(jìn)行,有時(shí)會(huì)抑制銅微粒彼此的燒結(jié)。此外,關(guān)于燒制中的氧化膜的增大,在燒制的最終階段利用氫氣等進(jìn)行還原燒制的情況下,會(huì)增大還原時(shí)的體積收縮,有時(shí)會(huì)引起燒制密度的降低。另一方面,著眼于金屬微粒的技術(shù)的理由之一在于尺寸效應(yīng)引起的熔點(diǎn)降低。關(guān)于尺寸效應(yīng)引起的熔點(diǎn)降低,以金為例,單質(zhì)的熔點(diǎn)為1,064℃,但若粒徑為2nm左右,則熔點(diǎn)變?yōu)榧s300℃,熔點(diǎn)降低至電子材料等中可使用的溫度。但是,據(jù)報(bào)道,若粒徑超過20nm,則基本上確認(rèn)不到熔點(diǎn)降低。因此,若是粒徑為2nm左右的一位數(shù)納米級,則可以充分期待熔點(diǎn)降低。但是,在銅微粒的情況下,需要防止氧化的表面保護(hù)劑。根據(jù)銅微粒的比表面積的關(guān)系,表面保護(hù)劑的所需量為銅體積的幾倍以上,這會(huì)引起燒結(jié)時(shí)的大幅的體積收縮,難以得到高密度的燒結(jié)體。與此相對,已知下述方法:在燒結(jié)階段在還原氣氛下由金屬氧化物生成一位數(shù)納米級的顆粒,利用尺寸效應(yīng)引起的熔點(diǎn)降低,在300℃~400℃左右的溫度進(jìn)行燒結(jié)。另外,有文獻(xiàn)提出了下述方法:利用有機(jī)羧酸等熔劑去除與焊料的熔劑效果同樣地被覆微粒表面的氧化膜,使還原金屬表面露出并進(jìn)行燒結(jié)(例如參照日本特開2013-047365號公報(bào))。此外,在將銅微粒適用于可印刷電子的情況下,為了進(jìn)行漿料化而供給,制作粒徑分布顯示出單分散的顆粒,要求制成分散穩(wěn)定性良好的銅漿。作為制造粒徑統(tǒng)一的金屬微?;蚪饘傺趸镂⒘5姆椒ǎ岢隽艘恍┓桨?。例如,在對金屬微粒進(jìn)行液相合成的情況下,大多參照表示作為金屬核的溶質(zhì)的溶解度與時(shí)間的關(guān)系的LaMer模型。根據(jù)該模型,若溶解度低的金屬核的生成速度過快,則因凝聚機(jī)制而發(fā)生顆粒生長,因此形成結(jié)晶核的生長不充分的凝聚體顆粒,是不優(yōu)選的。作為其對策,考慮了對作為溶質(zhì)的金屬核的生成速度進(jìn)行控制的方法。例如,由儲(chǔ)存單元(reservoir)(固體或金屬螯合物)慢慢地釋放出顆粒生長所需要的物質(zhì),由此對溶液的過飽和度進(jìn)行控制,抑制顆粒生長中的新的核生成,從而將成核期和顆粒生長期分離,僅在極初期生成的核發(fā)生生長,由此能夠制作顯示出單分散的顆粒。作為在顆粒生長中供給溶質(zhì)的儲(chǔ)存單元的選擇方法,選擇溶解度或溶解速度足夠低的固體或絡(luò)合物。與上述相關(guān),已知將由甲酸銅衍生的絡(luò)合物熱分解而制造銅微粒的技術(shù)。甲酸銅的分解溫度為約220℃,通過形成絡(luò)合物結(jié)構(gòu),能夠降低分解溫度。例如,在日本特開2011-032558號公報(bào)中,提出了使用作為雙齒配體發(fā)揮功能的氨基醇的絡(luò)合物,在100℃進(jìn)行熱分解而制造金屬微粒的方法。在日本特開2008-013466號公報(bào)或日本特開2008-031104號公報(bào)中,提出了使用作為單齒配體發(fā)揮功能的脂肪族胺的絡(luò)合物,在120℃進(jìn)行熱分解而制造金屬微粒的方法。此外,還考慮了下述方法:在利用了表面活性劑的微反應(yīng)場對引入生長核的金屬核進(jìn)行限制,由此來控制粒徑。例如,有文獻(xiàn)提出了下述基于反膠團(tuán)法的金屬或金屬氧化物微粒的制造方法,其利用通過表面活性劑而穩(wěn)定地分散于有機(jī)溶劑中的納米尺寸的水滴作為反應(yīng)場(例如,參照日本特開平08-143916號公報(bào)、日本特開2009-082828號公報(bào)和日本專利第3900414號公報(bào))。現(xiàn)有技術(shù)文獻(xiàn)專利文獻(xiàn)專利文獻(xiàn)1:日本特開2011-032558號公報(bào)專利文獻(xiàn)2:日本特開2008-013466號公報(bào)專利文獻(xiàn)3:日本特開2008-031104號公報(bào)專利文獻(xiàn)4:日本特開2013-047365號公報(bào)專利文獻(xiàn)5:日本特開平08-143916號公報(bào)專利文獻(xiàn)6:日本特開2009-082828號公報(bào)專利文獻(xiàn)7:日本專利第3900414號公報(bào)技術(shù)實(shí)現(xiàn)要素:發(fā)明所要解決的課題但是,在日本特開2011-032558號公報(bào)所記載的技術(shù)中,由于絡(luò)合物的分解溫度過低,因而會(huì)因分解時(shí)的放熱而以速度逐漸增加的方式生成大量的金屬核,而且反應(yīng)溶液中含有的銅濃度比較高,為1.0~2.4mol/L,因此在凝聚機(jī)制中容易發(fā)生顆粒生長,生成粗大顆粒,從而產(chǎn)率容易降低。另外,在日本特開2008-013466號公報(bào)或日本特開2008-031104號公報(bào)所記載的技術(shù)中,構(gòu)成甲酸銅絡(luò)合物的脂肪族胺同時(shí)起到金屬微粒的分散保護(hù)劑的作用,因而難以發(fā)生顆粒生長,難以制造具有20nm至亞微米的粒徑的銅顆粒。此外,在日本特開2013-047365號公報(bào)所記載的技術(shù)中,使用溶解度低的氧化銅等固體銅化合物作為儲(chǔ)存單元,在有機(jī)羧酸中部分發(fā)生溶解,同時(shí)進(jìn)行還原,因此核的生成速度受到限制,與日本特開2011-032558號公報(bào)的溶解體系相比,在核的生長階段難以發(fā)生凝聚。但是,即便能夠控制凝聚,核生成的時(shí)間也長,而且被覆的羧酸的碳鏈短,難以獲得充分的顆粒間排斥,因此難以制造粒度分布統(tǒng)一的顆粒,而且容易形成表面受到氧化的銅顆粒。在日本特開平08-143916號公報(bào)、日本特開2009-082828號公報(bào)和日本專利第3900414號公報(bào)所記載的反膠團(tuán)法中,使用大量的表面活性劑使膠團(tuán)穩(wěn)定化,因此反應(yīng)中的膠團(tuán)被保持為一定尺寸,但另一方面反應(yīng)場的尺寸受到限制,因此難以制造20nm以上的顆粒。此外,反膠團(tuán)法難以提高銅化合物在反應(yīng)液中的濃度,不適合于制造大量的顆粒。鑒于上述情況,本發(fā)明的目的在于消除現(xiàn)有技術(shù)的問題,提供一種現(xiàn)有技術(shù)難以實(shí)現(xiàn)的兼具優(yōu)異的耐氧化性和燒結(jié)性的被覆銅顆粒;以及在低熱處理溫度、低氧環(huán)境下能夠獲得該被覆銅顆粒的制造方法。用于解決課題的手段本發(fā)明人為了解決上述課題而進(jìn)行了研究,結(jié)果發(fā)現(xiàn),通過適當(dāng)?shù)卦O(shè)定反應(yīng)液中包含的溶劑與作為絡(luò)合劑的氨基醇的SP值之差,能夠以在反應(yīng)初期為均勻體系、但在反應(yīng)中間階段形成兩層分離結(jié)構(gòu)的方式來構(gòu)成反應(yīng)體系,由此能夠高效地制造高品質(zhì)的被覆銅顆粒。本發(fā)明包括下述方式。(1)一種表面被覆有脂肪族羧酸的被覆銅顆粒的制造方法,該制造方法包括:得到包含甲酸銅、氨基醇、具有碳原子數(shù)為5以上的脂肪族基團(tuán)的脂肪族羧酸和溶劑的反應(yīng)液;和對反應(yīng)液中生成的絡(luò)合物進(jìn)行熱分解處理而生成金屬銅,其中,氨基醇與溶劑的SP值之差ΔSP值為4.2以上。(2)如(1)所述的被覆銅顆粒的制造方法,其中,氨基醇的SP值為11.0以上。(3)如(1)或(2)所述的被覆銅顆粒的制造方法,其中,熱分解處理的溫度為100℃~130℃。(4)如(1)~(3)中任一項(xiàng)所述的被覆銅顆粒的制造方法,其中,溶劑包含能夠與水形成共沸混合物的有機(jī)溶劑,該制造方法包括通過共沸去除熱分解處理生成的水的至少一部分。(5)如(1)~(4)中任一項(xiàng)所述的被覆銅顆粒的制造方法,其中,脂肪族羧酸的脂肪族基團(tuán)部分的碳原子數(shù)為5~17。(6)如(1)~(5)中任一項(xiàng)所述的被覆銅顆粒的制造方法,其中,反應(yīng)液中的銅離子濃度為1.0摩爾/升~2.5摩爾/升。(7)一種被覆銅顆粒,其通過(1)~(6)中任一項(xiàng)所述的被覆銅顆粒的制造方法得到,基于SEM觀察的平均一次粒徑DSEM為0.02μm~0.2μm,粒度分布的變動(dòng)系數(shù)(変動(dòng)係數(shù))(標(biāo)準(zhǔn)偏差SD/平均一次粒徑DSEM)的值為0.1~0.5。(8)一種被覆銅顆粒,其通過(1)~(6)中任一項(xiàng)所述的被覆銅顆粒的制造方法得到,由粉體X射線分析求出的結(jié)晶粒徑DXRD相對于基于SEM觀察的平均一次粒徑DSEM之比DXRD/DSEM為0.25~1.00。(9)一種絲網(wǎng)印刷用的導(dǎo)電性組合物,其包含通過(1)~(6)中任一項(xiàng)所述的被覆銅顆粒的制造方法得到的被覆銅顆粒和介質(zhì)。(10)一種噴墨印刷用的導(dǎo)電性組合物,其包含通過(1)~(6)中任一項(xiàng)所述的被覆銅顆粒的制造方法得到的被覆銅顆粒和介質(zhì)。(11)一種電路形成物,其具備基材和配置于基材上的作為(9)或(10)所述的導(dǎo)電性組合物的熱處理物的配線圖案。發(fā)明的效果根據(jù)本發(fā)明,能夠提供一種現(xiàn)有技術(shù)難以實(shí)現(xiàn)的兼具優(yōu)異的耐氧化性和燒結(jié)性的被覆銅顆粒;以及在低熱處理溫度、低氧環(huán)境下能夠獲得該被覆銅顆粒的制造方法。附圖說明圖1A是在合成實(shí)施例1中制作的被覆銅顆粒后立即測定的XRD數(shù)據(jù)。圖1B是將實(shí)施例1中制作的被覆銅顆粒以粉體的狀態(tài)在大氣中、25℃下保存4個(gè)月后所測定的XRD數(shù)據(jù)。圖2A是實(shí)施例1中制作的被覆銅顆粒的Tof-SIMS分析的結(jié)果,示出了負(fù)離子模式(Negative)分析結(jié)果。圖2B是實(shí)施例1中制作的被覆銅顆粒的Tof-SIMS分析的結(jié)果,將負(fù)離子模式分析結(jié)果部分放大示出。圖3是實(shí)施例1中制作的被覆銅顆粒的TG-DTA分析數(shù)據(jù)。圖4是對實(shí)施例1的合成中的反應(yīng)溫度和氣體產(chǎn)生總量作圖而得到的數(shù)據(jù)。圖5是在實(shí)施例1的合成中餾出的餾分的FT-IR分析數(shù)據(jù)。圖6是參考例2中制作的被覆銅顆粒的XRD數(shù)據(jù)。圖7是實(shí)施例1中制作的被覆銅顆粒的SEM觀察圖像。圖8是實(shí)施例2中制作的被覆銅顆粒的SEM觀察圖像。圖9是實(shí)施例4中制作的被覆銅顆粒的SEM觀察圖像。圖10是比較例1中制作的被覆銅顆粒的SEM觀察圖像。圖11是比較例2中制作的被覆銅顆粒的SEM觀察圖像。圖12是比較例3中制作的被覆銅顆粒的SEM觀察圖像。圖13是比較例4中制作的被覆銅顆粒的SEM觀察圖像。圖14是比較例5中制作的被覆銅顆粒的SEM觀察圖像。圖15是實(shí)施例5中制作的被覆銅顆粒的SEM觀察圖像。圖16A是實(shí)施例6中制作的被覆銅顆粒的SEM觀察圖像。圖16B是實(shí)施例6中制作的被覆銅顆粒的放大SEM觀察圖像。圖17A是實(shí)施例7中制作的被覆銅顆粒的SEM觀察圖像。圖17B是實(shí)施例7中制作的被覆銅顆粒的放大SEM觀察圖像。圖18A是實(shí)施例8中制作的被覆銅顆粒的SEM觀察圖像。圖18B是實(shí)施例8中制作的被覆銅顆粒的放大SEM觀察圖像。圖19A是實(shí)施例9中制作的被覆銅顆粒的SEM觀察圖像。圖19B是實(shí)施例9中制作的被覆銅顆粒的放大SEM觀察圖像。圖20A是實(shí)施例1中制作的被覆銅顆粒的放大SEM觀察圖像。圖20B是實(shí)施例1中制作的被覆銅顆粒的粒度分布測定數(shù)據(jù)。圖21是比較例6中制作的被覆銅顆粒的XRD數(shù)據(jù)。圖22是比較例7中制作的被覆銅顆粒的XRD數(shù)據(jù)。圖23A是比較例6中制作的被覆銅顆粒的SEM觀察圖像。圖23B是將比較例6中制作的被覆銅顆粒漿料化并在氮?dú)鈿夥障掠?00℃燒制1小時(shí)而成的燒結(jié)膜的SEM觀察圖像。圖24A是實(shí)施例1中制作的被覆銅顆粒的SEM觀察圖像。圖24B是將使實(shí)施例1中制作的被覆銅顆粒漿料化而成的銅漿A在氮?dú)鈿夥障掠?50℃燒制1小時(shí)而成的燒結(jié)膜的SEM觀察圖像。圖25是銅漿A燒制膜的截面SEM圖像。圖26A是比較例7中制作的被覆銅顆粒的SEM觀察圖像。圖26B是將使比較例7中制作的被覆銅顆粒漿料化而成的銅漿B在氮?dú)鈿夥障掠?50℃燒制1小時(shí)而成的燒結(jié)膜的SEM觀察圖像。圖27是銅漿C燒制膜的截面SEM圖像。圖28A是示出試驗(yàn)例2的XPS最外表面組成分析數(shù)據(jù)中的碳原子的圖。圖28B是示出試驗(yàn)例2的XPS最外表面組成分析數(shù)據(jù)中的氧原子的圖。圖28C是示出試驗(yàn)例2的XPS最外表面組成分析數(shù)據(jù)中的銅原子的圖。圖29A是示出試驗(yàn)例3的XPS最外表面組成分析數(shù)據(jù)中的碳原子的圖。圖29B是示出試驗(yàn)例3的XPS最外表面組成分析數(shù)據(jù)中的氧原子的圖。圖29C是示出試驗(yàn)例3的XPS最外表面組成分析數(shù)據(jù)中的銅原子的圖。圖30A是示出試驗(yàn)例2的XPS深度剖析(XPS-DepthProfile)組成分析數(shù)據(jù)中的碳原子的分布的圖。圖30B是示出試驗(yàn)例2的XPS深度剖析組成分析數(shù)據(jù)中的氧原子的分布的圖。圖30C是示出試驗(yàn)例2的XPS深度剖析組成分析數(shù)據(jù)中的銅原子的分布的圖。圖31A是示出試驗(yàn)例3的XPS深度剖析組成分析數(shù)據(jù)中的碳原子的分布的圖。圖31B是示出試驗(yàn)例3的XPS深度剖析組成分析數(shù)據(jù)中的氧原子的分布的圖。圖31C是示出試驗(yàn)例3的XPS深度剖析組成分析數(shù)據(jù)中的銅原子的分布的圖。具體實(shí)施方式本說明書中,關(guān)于“工序”這一用語,不僅包括獨(dú)立的工序,即便在無法與其它工序明確區(qū)分的情況下,只要能夠達(dá)到該工序的所期望的目的則也包括在本術(shù)語中。另外,使用“~”所表示的數(shù)值范圍表示將“~”前后所記載的數(shù)值分別作為最小值和最大值包含在內(nèi)的范圍。此外,關(guān)于組合物中的各成分的含量,在組合物中存在多種與各成分對應(yīng)的物質(zhì)時(shí),只要不特別聲明,則是指在組合物中存在的該多種物質(zhì)的總量。<被覆銅顆粒的制造方法>本實(shí)施方式的被覆銅顆粒的制造方法為一種表面被覆有脂肪族羧酸的被覆銅顆粒的制造方法,該制造方法包括:得到包含甲酸銅、氨基醇、具有碳原子數(shù)為5以上的脂肪族基團(tuán)的脂肪族羧酸和溶劑的反應(yīng)液;和對反應(yīng)液中生成的絡(luò)合物進(jìn)行熱分解處理而生成金屬銅,其中,氨基醇與溶劑的SP值之差ΔSP值為4.2以上。將甲酸銅作為起始原料,在液相中使甲酸銅絡(luò)合物的熱分解還原反應(yīng)進(jìn)行,伴隨著反應(yīng)的進(jìn)行,由甲酸銅絡(luò)合物向反應(yīng)溶劑中放出與其不相溶的氨基醇,從而形成類似油包水乳液(Water-in-OilEmulsion)的新反應(yīng)場。在該反應(yīng)場中繼續(xù)產(chǎn)生銅的金屬核,同時(shí)核生長反應(yīng)進(jìn)行,從而認(rèn)為可生成耐氧化性和燒結(jié)性優(yōu)異、粒徑得到控制、粒度統(tǒng)一的還原銅顆粒。另外,甲酸銅絡(luò)合物的熱分解速度被適當(dāng)?shù)乜刂?,從而溶質(zhì)的供給得到控制。由此,金屬核的生長得到控制,認(rèn)為可生成粒度更統(tǒng)一的還原銅顆粒。此外,通過液相中存在脂肪族羧酸,從而利用物理吸附使脂肪族羧酸高密度地被覆所生成的還原銅顆粒。如此制造的被覆銅顆粒由基本上不存在氧化膜的還原銅顆粒構(gòu)成,其表面通過物理吸附而被覆有脂肪族羧酸,因此認(rèn)為耐氧化性與燒結(jié)性的平衡優(yōu)異。由此,在被覆銅顆粒的燒制工序中,作為被覆銅顆粒的有機(jī)保護(hù)劑的脂肪族羧酸在400℃以下的溫度被去除。因此,無需使用氫氣等還原氣氛,能夠在可通過氮?dú)庵脫Q等手段實(shí)現(xiàn)的低氧氣氛中進(jìn)行被覆銅顆粒彼此的燒結(jié)。因此,對于燒結(jié)需要還原性氣氛的現(xiàn)有銅顆粒來說,還能夠有效地用于難以適用的部位、例如氫脆或與氫的反應(yīng)所致的變質(zhì)成為問題的部位。另外,能夠利用氮?dú)庵脫Q回焊爐等現(xiàn)有設(shè)備進(jìn)行燒結(jié),因而在經(jīng)濟(jì)性的方面也優(yōu)異。本實(shí)施方式的被覆銅顆粒的制造方法中使用的反應(yīng)液包含甲酸銅、至少一種氨基醇、至少一種具有碳原子數(shù)為5以上的脂肪族基團(tuán)的脂肪族羧酸、和溶劑。反應(yīng)液可以根據(jù)需要進(jìn)一步包含其它添加劑。(甲酸銅)甲酸銅由二價(jià)銅離子和相對于1摩爾銅離子為2摩爾的甲酸根離子構(gòu)成。甲酸銅可以為酸酐,也可以為水合物。另外,甲酸銅可以使用市售品,也可以使用新制備的物質(zhì)。將甲酸銅熱分解而得到還原銅的微粒的方法例如公開于日本特公昭61-19682號公報(bào)等中。甲酸與通常的羧酸不同,具有還原性,因而在將甲酸銅熱分解時(shí)能夠還原二價(jià)銅離子。例如,已知無水甲酸銅在非活性氣體中進(jìn)行加熱時(shí)在210℃~250℃發(fā)生熱分解而生成金屬銅。對反應(yīng)液中的甲酸銅的含量沒有特別限制,可以根據(jù)目的等適當(dāng)選擇。關(guān)于反應(yīng)液中的甲酸銅的含量,例如從制造效率的方面出發(fā),優(yōu)選為1.0~2.5摩爾/升、更優(yōu)選為1.5~2.5摩爾/升、特別優(yōu)選為2.0~2.5摩爾/升。(氨基醇)氨基醇是具有至少1個(gè)氨基的醇化合物,只要是能夠與甲酸銅形成絡(luò)合物的化合物就沒有特別限制。通過使反應(yīng)液中存在氨基醇,從而由甲酸銅生成絡(luò)合物,能夠可溶于溶劑中。氨基醇優(yōu)選為單氨基一元醇化合物,更優(yōu)選為氨基無取代的單氨基一元醇化合物。并且,氨基醇還優(yōu)選為單齒配位性的單氨基一元醇化合物。對氨基醇的沸點(diǎn)沒有特別限制,優(yōu)選高于熱分解處理的反應(yīng)溫度。具體地說,氨基醇的沸點(diǎn)優(yōu)選為120℃以上、更優(yōu)選為130℃以上。對沸點(diǎn)的上限值沒有特別限制,例如為400℃以下、優(yōu)選為300℃以下。進(jìn)而,從極性的方面出發(fā),氨基醇的SP值優(yōu)選為11.0以上、更優(yōu)選為12.0以上、進(jìn)一步優(yōu)選為13.0以上。對氨基醇的SP值的上限值沒有特別限制,例如為18.0以下、優(yōu)選為17.0以下。本說明書中的SP值基于Hildebrand的定義。根據(jù)該定義,SP值是指25℃下每1mL試樣的分子間結(jié)合能E1的平方根。SP值的計(jì)算方法采用了“公益社團(tuán)法人石油學(xué)會(huì)主頁”中記載的方法(http://sekiyu-gakkai.or.jp/jp/dictionary/petdicsolvent.html#solubility2)。具體地說,如下進(jìn)行計(jì)算。分子間結(jié)合能E1是由蒸發(fā)潛熱減去氣體能量而得到的值。蒸發(fā)潛熱Hb以試樣的沸點(diǎn)Tb的形式由下式給出。Hb=21×(273+Tb)通過下式,由該Hb值求出25℃的摩爾蒸發(fā)潛熱H25。H25=Hb×[1+0.175×(Tb-25)/100]通過下式,由摩爾蒸發(fā)潛熱H25求出分子間結(jié)合能E。E=H25-596通過下式,由分子間結(jié)合能E求出每1mL試樣的分子間結(jié)合能E1。E1=E×D/Mw此處,D為試樣的密度,Mw為試樣的分子量,根據(jù)下式由E1求出SP值。SP=(E1)1/2需要說明的是,關(guān)于包含OH基的溶劑,對每一個(gè)OH基,需要+1的校正。[例如,參照三菱石油技術(shù)資料、No.42,p3,p11(1989)]作為氨基醇,具體可例示出2-氨基乙醇(沸點(diǎn):170℃、SP值:14.54)、3-氨基-1-丙醇(沸點(diǎn):187℃、SP值:13.45)、5-氨基-1-戊醇(沸點(diǎn):245℃、SP值:12.78)、DL-1-氨基-2-丙醇(沸點(diǎn):160℃、SP值:12.74)、N-甲基二乙醇胺(沸點(diǎn):247℃、SP值:13.26)等,優(yōu)選選自由這些組成的組中的至少一種。氨基醇可以單獨(dú)使用1種,也可以將2種以上組合使用。對反應(yīng)液中的氨基醇的含量沒有特別限制,可以根據(jù)目的等適當(dāng)選擇。氨基醇的含量例如相對于反應(yīng)液中的銅離子優(yōu)選為1.5~4.0倍摩爾的范圍、更優(yōu)選為1.5~3.0倍摩爾的范圍。若氨基醇的含量相對于銅離子為1.5倍摩爾以上,則可以充分得到甲酸銅的溶解性,能夠縮短反應(yīng)所需要的時(shí)間。另外,若為4.0倍摩爾以下,則能夠抑制所生成的被覆銅顆粒的污染。(脂肪族羧酸)脂肪族羧酸只要是脂肪族基團(tuán)的碳原子數(shù)為5以上的長鏈脂肪族羧酸就沒有特別限制。脂肪族基團(tuán)可以為直鏈狀和支鏈狀中的任一種,并且可以為飽和脂肪族基團(tuán)和不飽和脂肪族基團(tuán)中的任一種。脂肪族基團(tuán)的碳原子數(shù)為5以上,優(yōu)選為5以上17以下、更優(yōu)選為7以上17以下。若脂肪族基團(tuán)的碳原子數(shù)為5以上,則具有作為粒度分布的指標(biāo)的變動(dòng)系數(shù)(変動(dòng)率)減小的傾向。這例如可以通過碳鏈的長度與影響締合力的范德華力的大小相關(guān)性高來進(jìn)行說明。即,認(rèn)為:碳鏈長的羧酸的締合力強(qiáng),有助于作為微反應(yīng)場的類似油包水乳液的相穩(wěn)定,從而能夠高效地制造粒徑統(tǒng)一的銅顆粒。另外,脂肪族羧酸的沸點(diǎn)優(yōu)選高于熱分解處理的溫度。具體地說,脂肪族羧酸的沸點(diǎn)優(yōu)選為120℃以上、更優(yōu)選為130℃以上。對沸點(diǎn)的上限值沒有特別限制,例如為400℃以下。若沸點(diǎn)為400℃以下,則具有被覆銅顆粒的燒結(jié)性進(jìn)一步提高的傾向。作為脂肪族羧酸,具體可例示出油酸、亞油酸、硬脂酸、十七烷酸、月桂酸、辛酸等,優(yōu)選為選自由這些組成的組中的至少一種。脂肪族羧酸可以單獨(dú)使用1種,也可以將2種以上組合使用。對反應(yīng)液中的脂肪族羧酸的含量沒有特別限制,可以根據(jù)目的等適當(dāng)選擇。脂肪族羧酸的含量例如相對于反應(yīng)液中的銅離子優(yōu)選為2.5~25摩爾%的范圍、更優(yōu)選為5.0~15摩爾%的范圍。若脂肪族羧酸的含量相對于銅離子為25摩爾%以下,則具有能夠抑制反應(yīng)體系的粘度升高的傾向。另外,若脂肪族羧酸的含量相對于銅離子為2.5摩爾%以上,則具有可得到充分的反應(yīng)速度、生產(chǎn)率提高的傾向,具有作為粒度分布的指標(biāo)的變動(dòng)系數(shù)減小的傾向。(溶劑)關(guān)于構(gòu)成反應(yīng)液的溶劑,只要按照不過度抑制由甲酸引起的還原反應(yīng)、與氨基醇的SP值之差ΔSP值為4.2以上的方式進(jìn)行選擇,就沒有特別限制,可以從通常使用的有機(jī)溶劑中適當(dāng)選擇。若氨基醇的SP值與溶劑的SP值之差ΔSP值為4.2以上,則得到所形成的被覆銅顆粒的粒度分布的范圍窄、粒徑統(tǒng)一的被覆銅顆粒。ΔSP值為4.2以上,從反應(yīng)場的形成性和被覆銅顆粒的品質(zhì)的方面出發(fā),優(yōu)選為4.5以上、更優(yōu)選為5.0以上。對ΔSP值的上限沒有特別限制,例如ΔSP值為11.0以下、優(yōu)選為10.0以下。溶劑的SP值按照ΔSP值為4.2以上的方式進(jìn)行選擇,溶劑的SP值優(yōu)選小于氨基醇的SP值。溶劑的SP值優(yōu)選為11.0以下、更優(yōu)選為10.0以下。對溶劑的SP值的下限沒有特別限制,例如溶劑的SP值優(yōu)選為7.0以上。另外,溶劑的沸點(diǎn)優(yōu)選高于熱分解處理的溫度。具體地說,溶劑的沸點(diǎn)優(yōu)選為120℃以上、更優(yōu)選為130℃以上。對沸點(diǎn)的上限值沒有特別限制,例如沸點(diǎn)為400℃以下、優(yōu)選為300℃以下。此外,溶劑還優(yōu)選為能夠與水形成共沸混合物的有機(jī)溶劑。若能夠與水形成共沸混合物,則能夠容易地從反應(yīng)體系中去除通過熱分解處理在反應(yīng)液中生成的水。作為溶劑,具體可例示出乙基環(huán)己烷(沸點(diǎn):132℃、SP值:8.18)、C9系環(huán)己烷[丸善石油制造、商品名:スワクリーン#150](沸點(diǎn):149℃、SP值:7.99)、正辛烷(沸點(diǎn):125℃、SP值:7.54)等,優(yōu)選為選自由這些組成的組中的至少一種。溶劑可以單獨(dú)使用1種,也可以將2種以上組合使用。溶劑為2種以上的組合的情況下,優(yōu)選包含與氨基醇不相溶的主溶劑和能夠與氨基醇相溶的輔助溶劑。主溶劑的具體例如上所述。輔助溶劑的沸點(diǎn)的優(yōu)選方式與主溶劑相同。輔助溶劑的SP值優(yōu)選大于主溶劑,更優(yōu)選大為與氨基醇相溶的程度。作為輔助溶劑的具體例,可以舉出EO系二醇醚、PO系二醇醚、二烷基二醇醚等二醇醚。更具體地說,可以舉出甲基二乙二醇、異丙基乙二醇、丁基乙二醇等EO系二醇醚;甲基亞丙基二乙二醇、甲基亞丙基三乙二醇、丙基丙二醇、丁基丙二醇等PO系二醇醚、二甲基二乙二醇等二烷基二醇醚等,優(yōu)選為選自由這些組成的組中的至少一種。需要說明的是,這些輔助溶劑均可以由日本乳化劑(株)等獲得。溶劑為2種以上的組合的情況下,溶劑的SP值以考慮到溶劑中包含的各溶劑的SP值和摩爾容積的平均SP值的形式來計(jì)算。具體地說,在溶劑由溶劑1和溶劑2這兩種構(gòu)成的情況下,平均SP值由下式算出。δ3=[V1×δ1+V2×δ2]/(V1+V2)δ3:混合溶劑的平均SP值、δ1:溶劑1的SP值、V1:溶劑1的摩爾容積、δ2:溶劑2的SP值、V2:溶劑2的摩爾容積反應(yīng)液中包含的溶劑量優(yōu)選按照銅離子的濃度為1.0~2.5摩爾/升的方式來選擇,更優(yōu)選按照銅離子的濃度為1.5~2.5摩爾/升的方式來選擇。若反應(yīng)液中的銅離子濃度為1.0摩爾/升以上,則生產(chǎn)率進(jìn)一步提高,若銅離子濃度為2.5摩爾/升以下,則反應(yīng)液的粘度升高得到抑制,可獲得良好的攪拌性。(絡(luò)合物)由包含甲酸銅、氨基醇、長鏈脂肪族羧酸和溶劑的反應(yīng)液生成來自甲酸銅的絡(luò)合物。對絡(luò)合物的結(jié)構(gòu)沒有特別限定,可以僅由1種構(gòu)成,也可以包含2種以上。另外,絡(luò)合物伴隨著熱分解處理的進(jìn)行,其構(gòu)成可以發(fā)生變化。即,在熱分解處理的初期主要存在的絡(luò)合物與在熱分解處理的后期主要存在的絡(luò)合物相互可以為不同的構(gòu)成。作為在反應(yīng)液中生成的絡(luò)合物,優(yōu)選包含銅離子和作為配體的甲酸根離子及氨基醇。通過包含氨基醇作為配體,從而絡(luò)合物的熱分解溫度降低。作為在反應(yīng)液中生成的絡(luò)合物,具體可以舉出:1個(gè)銅離子與2分子甲酸根離子和2分子氨基醇配位的絡(luò)合物;1個(gè)銅離子與1分子甲酸根離子和1分子脂肪族羧酸及2分子氨基醇配位的絡(luò)合物;等。在反應(yīng)液中生成的絡(luò)合物通過熱分解處理而生成金屬銅。熱分解處理的溫度根據(jù)絡(luò)合物的結(jié)構(gòu)等適當(dāng)選擇即可。一般來說,甲酸銅的熱分解溫度為約220℃,但甲酸銅與氨基醇一同形成絡(luò)合物,從而例如如日本特開2008-013466號公報(bào)等中所記載的那樣,認(rèn)為其熱分解溫度為110~120℃左右。因此,熱分解處理的溫度優(yōu)選為100~130℃、更優(yōu)選為110~130℃。若熱分解處理的溫度為130℃以下,則能夠抑制由脂肪族羧酸與氨基醇的脫水反應(yīng)所引起的酰胺的生成,具有所得到的被覆銅顆粒的清洗性提高的傾向。通過絡(luò)合物的熱分解而生成金屬銅,反應(yīng)液中存在的脂肪族羧酸吸附于所生成的金屬銅的表面,從而可以得到表面被覆有脂肪族羧酸的被覆銅顆粒。脂肪族羧酸在金屬銅表面的吸附優(yōu)選為物理吸附。由此,被覆銅顆粒的燒結(jié)性進(jìn)一步提高。通過在絡(luò)合物的熱分解中抑制氧化銅的生成,從而脂肪族羧酸的物理吸附得到促進(jìn)。在熱分解處理中,優(yōu)選將伴隨著絡(luò)合物的熱分解反應(yīng)而生成的水的至少一部分去除。通過在熱分解處理中進(jìn)行水的去除,從而能夠更有效地抑制氧化銅的生成。對水的去除方法沒有特別限制,可以從通常使用的水分去除方法中適當(dāng)選擇。例如,優(yōu)選使用能夠與水形成共沸混合物的有機(jī)溶劑作為溶劑,通過共沸去除生成的水。熱分解處理的時(shí)間根據(jù)熱分解處理的溫度等適當(dāng)選擇即可。例如可以為30~180分鐘。另外,熱分解處理的氣氛優(yōu)選為氮?dú)鈿夥盏确腔钚詺夥?。在被覆銅顆粒的制造方法中,作為控制所生成的被覆銅顆粒的粒度分布的因素,例如可以舉出脂肪族羧酸的種類和添加量、甲酸銅絡(luò)合物的濃度和混合溶劑的比例(主溶劑/輔助溶劑)等。關(guān)于控制被覆銅顆粒的尺寸的因素,可以通過適當(dāng)?shù)乇3挚刂平饘俸水a(chǎn)生數(shù)的升溫速度、即向反應(yīng)體系的投入熱量、和與微反應(yīng)場的大小有關(guān)的攪拌速度來統(tǒng)一。關(guān)于被覆銅顆粒的制造方法,制備包含甲酸銅、氨基醇、脂肪族羧酸和溶劑的反應(yīng)液,在所期望的溫度下進(jìn)行熱分解處理,通過上述容易的操作能夠高效地制造粒徑統(tǒng)一、耐氧化性和燒結(jié)性優(yōu)異的被覆銅顆粒。在被覆銅顆粒的制造方法中,得到粒度分布窄的被覆銅顆粒。關(guān)于這點(diǎn),例如可以如下考慮。即,通過使作為絡(luò)合劑的氨基醇(用于使甲酸銅可溶于反應(yīng)溶劑中)與溶劑的SP值之差ΔSP值為4.2以上,以甲酸銅氨基醇絡(luò)合物或甲酸的1分子被脂肪族羧酸取代的甲酸銅氨基醇絡(luò)合物的狀態(tài)發(fā)生溶解,但絡(luò)合物被熱分解、作為絡(luò)合劑的氨基醇發(fā)生游離時(shí),游離的氨基醇無法與溶劑互溶,開始形成2相。游離的氨基醇由于與甲酸銅、甲酸銅氨基醇絡(luò)合物的親和性高,因而作為甲酸銅的新絡(luò)合劑或溶劑發(fā)揮作用,形成極性高的內(nèi)核(液滴),采取極性低的溶劑包圍外側(cè)的類似油包水乳液的2相結(jié)構(gòu),推測其作為微反應(yīng)場發(fā)揮功能。此外,反應(yīng)體系中的水和在脂肪族羧酸的取代中脫離的甲酸也存在于該微反應(yīng)場。在微反應(yīng)場中,金屬核、其生長顆粒和作為金屬核產(chǎn)生源的甲酸銅氨基醇絡(luò)合物、甲酸的1分子被脂肪族羧酸取代的甲酸銅氨基醇絡(luò)合物、水以及甲酸被隔離,反應(yīng)進(jìn)行。隨著脂肪族羧酸作為金屬銅生長顆粒的被覆材料被固定而減少,在反應(yīng)初期甲酸銅絡(luò)合物的熱分解機(jī)制按照后述的反應(yīng)式1~3進(jìn)行,但逐漸按照反應(yīng)式4的機(jī)制進(jìn)行,產(chǎn)生氣體成分發(fā)生變化。在微反應(yīng)場,由于反應(yīng)式5所示的水引起的甲酸銅氨基醇絡(luò)合物的水解而生成CuO,但經(jīng)過反應(yīng)式6或反應(yīng)式7而再次被還原,因此能夠制造不含氧化亞銅或氧化銅的還原銅顆粒。另外,由于微反應(yīng)場中包含的銅原子數(shù)受到限定,因而銅顆粒的粒徑被控制為一定。并且,在微反應(yīng)場生成表面未形成氧化銅的銅顆粒,因此存在于微反應(yīng)場的脂肪族羧酸容易發(fā)生物理吸附,可認(rèn)為能夠高效地獲得粒徑統(tǒng)一、耐氧化性和燒結(jié)性優(yōu)異的被覆銅顆粒。關(guān)于被覆銅顆粒的制造方法,在熱分解處理后可以進(jìn)一步具有所得到的被覆銅顆粒的清洗工序、分離工序、干燥工序等。作為被覆銅顆粒的清洗工序,例如可以舉出利用有機(jī)溶劑的清洗工序。作為清洗工序中使用的有機(jī)溶劑,可以舉出甲醇等醇溶劑、丙酮等酮溶劑等。它們可以單獨(dú)使用1種,也可以將2種以上組合使用。<被覆銅顆粒>本實(shí)施方式的被覆銅顆粒利用上述被覆銅顆粒的制造方法進(jìn)行制造,基于SEM觀察的平均一次粒徑DSEM為0.02~0.2μm,粒度分布的變動(dòng)系數(shù)(標(biāo)準(zhǔn)偏差SD/平均一次粒徑DSEM)的值為0.1~0.5。通過利用上述被覆銅顆粒的制造方法進(jìn)行制造,形成粒度分布的變動(dòng)系數(shù)小、粒徑統(tǒng)一的狀態(tài)。通過被覆銅顆粒的粒度分布的變動(dòng)系數(shù)小,從而可獲得能夠容易地制作分散性優(yōu)異、高濃度的分散物的效果。另外,本實(shí)施方式的被覆銅顆粒通過上述被覆銅顆粒的制造方法獲得,由粉體X射線分析求出的結(jié)晶粒徑DXRD相對于基于SEM觀察的平均一次粒徑DSEM之比DXRD/DSEM為0.25~1.00。通過利用上述被覆銅顆粒的制造方法進(jìn)行制造,能夠減小結(jié)晶粒徑與平均一次粒徑之差。由此,耐氧化性優(yōu)異,其結(jié)果可得到燒結(jié)性進(jìn)一步提高的效果。本實(shí)施方式的被覆銅顆粒通過上述被覆銅顆粒的制造方法獲得,從而銅顆粒的表面被覆有脂肪族羧酸。被覆銅顆粒的脂肪族羧酸是局部存在于銅顆粒的表面并抑制氧化或凝聚的被覆材料,在燒結(jié)時(shí)從顆粒表面被去除,進(jìn)而在燒結(jié)溫度以下發(fā)生分解或揮發(fā),因此可抑制殘存于通過燒結(jié)而形成的銅覆膜中。認(rèn)為這是由于例如脂肪族羧酸物理吸附于銅顆粒的表面。另外,構(gòu)成被覆銅顆粒的銅顆粒由于粒徑統(tǒng)一,因而分散性優(yōu)異。此外,構(gòu)成銅顆粒的微晶直徑與SEM觀察直徑之差小,因而被覆銅顆粒不通過多個(gè)銅顆粒的凝聚而構(gòu)成顆粒,在凝聚顆粒邊界部存在被覆材料、雜質(zhì)、氧化層等導(dǎo)致的燒結(jié)抑制得到抑制。<導(dǎo)電性組合物>本實(shí)施方式的導(dǎo)電性組合物包含通過上述被覆銅顆粒的制造方法得到的被覆銅顆粒中的至少一種和介質(zhì)。導(dǎo)電性組合物能夠適合用于配線圖案形成,能夠在低溫下容易地形成導(dǎo)電性優(yōu)異的配線圖案。即,本實(shí)施方式包括上述被覆銅顆粒的作為導(dǎo)電性組合物的使用。導(dǎo)電性組合物中包含的介質(zhì)的構(gòu)成可以根據(jù)導(dǎo)電性組合物的目的等適當(dāng)選擇。例如,在導(dǎo)電性組合物為絲網(wǎng)印刷用的情況下,作為介質(zhì),可以舉出烴溶劑、高級醇溶劑、溶纖劑、乙酸溶纖劑溶劑等。另外,絲網(wǎng)印刷用的導(dǎo)電性組合物的固體成分濃度例如可以為40~95質(zhì)量%。此處,導(dǎo)電性組合物的固體成分是指不揮發(fā)性成分的總量。另外,例如在導(dǎo)電性組合物為噴墨印刷用的情況下,作為介質(zhì),可以舉出烴溶劑、高級醇溶劑、溶纖劑、乙酸溶纖劑溶劑等。噴墨印刷用的導(dǎo)電性組合物的固體成分濃度例如可以為40~90質(zhì)量%。除了被覆銅顆粒和介質(zhì)以外,導(dǎo)電性組合物可以根據(jù)需要進(jìn)一步包含其它添加劑。作為其它添加劑,例如可以舉出硅烷偶聯(lián)劑、鈦酸酯偶聯(lián)劑等偶聯(lián)劑、聚酯系分散劑、聚丙烯酸系分散劑等分散劑等。<電路形成物>本實(shí)施方式的電路形成物具備基材、和配置于基材上的作為上述導(dǎo)電性組合物的熱處理物的配線圖案。通過由上述導(dǎo)電性組合物形成配線圖案,從而配線圖案的導(dǎo)電性優(yōu)異。并且,由于能夠在低溫下形成配線圖案,因而基材的選擇范圍的自由度大。作為基材的材質(zhì),例如可以舉出聚酰亞胺膜、玻璃、陶瓷、金屬等。對基材的厚度沒有特別限制,可以根據(jù)目的等適當(dāng)選擇?;牡暮穸壤缈梢詾?.01mm~5mm。關(guān)于配線圖案的形成,例如可以通過在基材上以所期望的圖案賦予導(dǎo)電性組合物,并對所賦予的導(dǎo)電性組合物進(jìn)行熱處理來進(jìn)行。通過使用導(dǎo)電性組合物,能夠在低溫下高效地形成具有所期望的圖案且導(dǎo)電性優(yōu)異的配線圖案。電路形成物例如通過下述制造方法來制造,該制造方法包括:準(zhǔn)備基材的工序;在基材上賦予導(dǎo)電性組合物的工序;和對導(dǎo)電性組合物進(jìn)行熱處理的工序。即,本實(shí)施方式還包括使用上述導(dǎo)電性組合物的電路形成物的制造方法。對導(dǎo)電性組合物的賦予方法沒有特別限制,例如可以通過噴墨印刷法、絲網(wǎng)印刷法、柔版印刷法、點(diǎn)膠法等進(jìn)行。導(dǎo)電性組合物的賦予量可以根據(jù)目的等適當(dāng)選擇,例如,可以使熱處理后的厚度為1~100μm。導(dǎo)電性組合物的熱處理的溫度例如可以為200~600℃、優(yōu)選為250~450℃。熱處理的時(shí)間例如可以為1~120分鐘、優(yōu)選為5~60分鐘。熱處理的氣氛優(yōu)選為低氧氣氛。作為低氧氣氛,可以舉出氮?dú)鈿夥铡鍤鈿夥盏?。并且氧濃度?yōu)選為1,000ppm以下。實(shí)施例下面,通過實(shí)施例來具體說明本發(fā)明,但本發(fā)明不被這些實(shí)施例所限定。下面示出實(shí)施例中使用的試驗(yàn)方法的詳細(xì)情況。<平均一次粒徑和變動(dòng)系數(shù)的計(jì)算>測定裝置:日本電子制造FE-EPMAJXA-8510F平均一次粒徑:樣品20點(diǎn)的平均值變動(dòng)系數(shù):由樣品20點(diǎn)的標(biāo)準(zhǔn)偏差/平均值所計(jì)算的值<SEM觀察圖像>測定裝置:日本電子制造FE-EPMAJXA-8510F測定條件:加速電壓6KV或15KV觀察倍率×10,000~×75,000<粉體X射線衍射(XRD)的測定>測定器:島津制造XRD-6100測定條件:靶材Cu管電壓40KV、管電流30.0mA<Tof-SIMS(飛行時(shí)間型2次離子質(zhì)譜儀)的測定>測定器;ULVAC-PHI制造PHITRIFTIV型測定條件:1次離子種類Au、加速電壓30KV<TG-DTA測定>有機(jī)殘留物和金屬含量的測定測定裝置:Rigaku制造TG8120升溫速度:10℃/min測定溫度范圍:25℃~600℃測定氣氛:氮100ml/min<粒度分布測定>激光衍射散射式粒度分布測定測定裝置:堀場制作所制造LA-960測定溶劑:KYOWANOLM分散劑:聚丙烯酸系分散劑分散方法:超聲波5分鐘<電阻值測定>體積固有電阻值的測定測定裝置:共和理研制造K-705RS測定方法:四端子測定法測定點(diǎn)數(shù):n=5的平均值導(dǎo)電膜厚:由SEM截面觀察決定<基于XPS的最外表面組成分析和深度剖析分析>測定裝置:JEOL制造JPS-9010MX高速蝕刻離子槍:XP-HSIG3深度剖析分析條件離子束直徑:Ar離子加速電壓:500V(電流:8.6mA)以SiO蝕刻速度計(jì)相當(dāng)于20~25nm/min(數(shù)據(jù)_0至數(shù)據(jù)_6為從下至上)數(shù)據(jù)_0:無蝕刻數(shù)據(jù)_1:實(shí)行蝕刻時(shí)間-0.9秒(累計(jì):0.9秒)數(shù)據(jù)_2:實(shí)行蝕刻時(shí)間-3.0秒(累計(jì):3.9秒)數(shù)據(jù)_3:實(shí)行蝕刻時(shí)間-3.0秒(累計(jì):6.9秒)數(shù)據(jù)_4:實(shí)行蝕刻時(shí)間-3.0秒(累計(jì):9.9秒)數(shù)據(jù)_5:實(shí)行蝕刻時(shí)間-3.0秒(累計(jì):12.9秒)數(shù)據(jù)_6:實(shí)行蝕刻時(shí)間-3.0秒(累計(jì):15.9秒)(參考例1)下面示出本實(shí)施例中使用的甲酸銅、甲酸銅無水物的制造例,關(guān)于甲酸銅的制造方法,已經(jīng)公知多種方法,但也可以使用通過其它方法制造的甲酸銅。[堿式碳酸銅的前處理]若為塊,則容易未反應(yīng)而殘存,因此進(jìn)行了28目左右的篩分處理。[合成過程]向5升4口燒瓶中加入甲酸0.96kg、離子交換水1.44kg,一邊攪拌均勻一邊一點(diǎn)一點(diǎn)地加入堿式碳酸銅。注意二氧化碳的產(chǎn)生而加入全部量。投入結(jié)束后,將溫度升高至60℃,繼續(xù)反應(yīng)0.5小時(shí)。確認(rèn)到基本上沒有二氧化碳的餾出(將冷凝水導(dǎo)入水捕集器,進(jìn)行確認(rèn)),在該時(shí)刻,甲酸銅和堿式碳酸銅部分未溶解而殘留。追加離子交換水1.60Kg,在60℃繼續(xù)反應(yīng)1.0小時(shí)。確認(rèn)反應(yīng)液變?yōu)樯钏{(lán)色透明液后,終止反應(yīng),用蒸發(fā)器減壓濃縮,蒸餾除去1.5升水。該時(shí)刻結(jié)晶已經(jīng)析出,形成漿料狀。冷卻至室溫并對反應(yīng)物進(jìn)行過濾,用1升丙酮進(jìn)行清洗。所得到的結(jié)晶顯示出藍(lán)綠色。接下來,如下進(jìn)行干燥脫水。關(guān)于干燥溫度,在真空0.5KPa(最終)下于80℃以下(粉體的溫度)實(shí)施。通過干燥脫水形成淺藍(lán)色結(jié)晶。甲酸銅的熱分解溫度:214.9℃(氮?dú)庵?、大氣中為200℃左右[品質(zhì)確認(rèn)]通過TG-DTA測定確認(rèn)了含有Cu%與理論值近似。甲酸銅無水物的式量:153.84含有Cu%=41.3%、失重%=58.5%左右(實(shí)施例1)將具備攪拌機(jī)、溫度計(jì)、回流冷凝管、75mL迪安-斯達(dá)克(Dean-Stark)管、氮?dú)鈱?dǎo)入管的3000mL玻璃制四口燒瓶設(shè)置于油浴中。向其中添加甲酸銅無水物484g(3.1摩爾)、月桂酸(關(guān)東化學(xué)社制造)68.1g(0.11當(dāng)量/甲酸銅無水物)、作為反應(yīng)溶劑的三丙二醇單甲醚(東京化成社制造)150g(0.23當(dāng)量/甲酸銅無水物)和スワクリーン150(Godo社制造)562g(1.42當(dāng)量/甲酸銅無水物),一邊以200rpm進(jìn)行攪拌一邊混合。在氮?dú)鈿夥障乱?00rpm加熱攪拌至液溫達(dá)到50℃。向其中緩慢滴加3-氨基-1-丙醇(東京化成社制造)712g(3.00當(dāng)量/甲酸銅無水物)。滴加結(jié)束后,以340rpm加熱攪拌至液溫達(dá)到120℃左右。適時(shí)去除由Dean-Stark管所捕集的水層,使其不回流至反應(yīng)體系內(nèi)。隨著液溫升高,反應(yīng)溶液開始由深藍(lán)色變?yōu)椴韬稚a(chǎn)生了二氧化碳的起泡。將二氧化碳的起泡結(jié)束作為反應(yīng)終點(diǎn),停止油浴溫度調(diào)節(jié),冷卻至室溫。冷卻至室溫后,添加甲醇(關(guān)東化學(xué)社制造)550g進(jìn)行混合。將該混合溶液靜置30分鐘以上,傾潷上清,得到沉淀物。向該沉淀物中添加甲醇(關(guān)東化學(xué)社制造)550g、丙酮(關(guān)東化學(xué)社制造)300g進(jìn)行混合。將該混合溶液靜置30分鐘以上,傾潷上清,得到沉淀物,再重復(fù)一次該操作。利用甲醇(關(guān)東化學(xué)社制造)550g對該沉淀物進(jìn)行共洗,同時(shí)移至500mL茄型燒瓶中。靜置30分鐘以上,傾潷上清,將所得到的沉淀物設(shè)置于旋轉(zhuǎn)式蒸發(fā)器中,在40℃、1kPa以下進(jìn)行真空干燥。真空干燥結(jié)束后,冷卻至室溫,一邊進(jìn)行氮?dú)庵脫Q一邊減壓釋放,得到194g的茶褐色的被覆銅顆粒。將所得到的被覆銅顆粒的SEM觀察圖像示于圖7。并且,將放大SEM觀察圖像示于圖20A,將粒度分布示于圖20B。(實(shí)施例2)除了將3-氨基-1-丙醇變?yōu)镈L-1-氨基-2-丙醇以外,與實(shí)施例1同樣地合成被覆銅顆粒。將所得到的被覆銅顆粒的SEM觀察圖像示于圖8。(實(shí)施例3)除了將3-氨基-1-丙醇變?yōu)?-氨基-1-戊醇、將反應(yīng)溶劑變?yōu)檎镣橐酝?,與實(shí)施例1同樣地合成被覆銅顆粒。(實(shí)施例4)除了將3-氨基-1-丙醇變?yōu)镈L-1-氨基-2-丙醇、將反應(yīng)溶劑變?yōu)檎镣橐酝猓c實(shí)施例1同樣地合成被覆銅顆粒。將所得到的被覆銅顆粒的SEM觀察圖像示于圖9。(比較例1)除了將3-氨基-1-丙醇變?yōu)?-己胺以外,與實(shí)施例1同樣地合成被覆銅顆粒。將所得到的被覆銅顆粒的SEM觀察圖像示于圖10。(比較例2)除了將3-氨基-1-丙醇變?yōu)?-二乙基氨基乙醇以外,與實(shí)施例1同樣地合成被覆銅顆粒。將所得到的被覆銅顆粒的SEM觀察圖像示于圖11。(比較例3)除了將3-氨基-1-丙醇變?yōu)?-二甲胺基乙醇以外,與實(shí)施例1同樣地合成被覆銅顆粒。將所得到的被覆銅顆粒的SEM觀察圖像示于圖12。(比較例4)除了將3-氨基-1-丙醇變?yōu)?-氨基-1-戊醇以外,與實(shí)施例1同樣地合成被覆銅顆粒。將所得到的被覆銅顆粒的SEM觀察圖像示于圖13。(比較例5)除了將反應(yīng)溶劑變?yōu)檎链家酝猓c實(shí)施例1同樣地合成被覆銅顆粒。將所得到的被覆銅顆粒的SEM觀察圖像示于圖14。下面記載變化了長鏈脂肪族羧酸的種類和添加量的實(shí)施例。(實(shí)施例5)將月桂酸變?yōu)橛退?8.16g,溶劑不使用輔助溶劑,將スワクリーン#150變?yōu)?12g,除此以外與實(shí)施例1同樣地合成被覆銅顆粒。將所得到的被覆銅顆粒的SEM觀察圖像示于圖15。(實(shí)施例6)除了將月桂酸48g變?yōu)?6g以外,與實(shí)施例1同樣地合成被覆銅顆粒。將所得到的被覆銅顆粒的SEM觀察圖像示于圖16A和圖16B。(實(shí)施例7)除了將月桂酸48g變?yōu)?44g以外,與實(shí)施例1同樣地合成被覆銅顆粒。將所得到的被覆銅顆粒的SEM觀察圖像示于圖17A和圖17B。(實(shí)施例8)除了將作為反應(yīng)溶劑的スワクリーン#150變?yōu)?50g,將甲基亞丙基三乙二醇變?yōu)?62g以外,與實(shí)施例1同樣地合成被覆銅顆粒。將所得到的被覆銅顆粒的SEM觀察圖像示于圖18A和圖18B。(實(shí)施例9)除了將月桂酸變?yōu)樾了嵋酝?,與實(shí)施例1同樣地合成被覆銅顆粒。將所得到的被覆銅顆粒的SEM觀察圖像示于圖19A和圖19B。(比較例6)根據(jù)日本特開2013-047365號公報(bào)的實(shí)施例1中記載的方法,合成了被覆銅顆粒。具體地說,如下使用乙酸作為被覆材料,合成了被覆銅顆粒。將作為銅化合物的氧化亞銅(I)(古河化學(xué)社制造;粒徑:2~4μ)14.3g(0.1摩爾)、作為被覆材料的乙酸3.0g(50mmol)、作為還原劑的肼一水合物(和光純藥工業(yè)制造)5.0g(0.1摩爾)、作為溶劑的異丙醇100ml進(jìn)行混合,加入至300ml的4口燒瓶中。對燒瓶安裝冷凝器、溫度計(jì)、氮?dú)鈱?dǎo)入管和攪拌裝置。一邊以200ml/min通入氮?dú)猓贿呥M(jìn)行攪拌,升溫至70℃,繼續(xù)加熱、攪拌1小時(shí),使氧化亞銅(I)還原,得到被覆銅顆粒分散液。利用桐山濾紙No.5B對被覆銅顆粒分散液進(jìn)行減壓過濾,濾出粉體。將濾出的粉體用甲醇(關(guān)東化學(xué)工業(yè)制造)清洗3次,在40℃、1kPa以下的條件下進(jìn)行減壓干燥,冷卻至室溫后,進(jìn)行氮?dú)庵脫Q并取出,得到12g的茶褐色粉體。測定了粉體的XRD(示于圖21),結(jié)果檢測出若干被認(rèn)為是來自原料的氧化亞銅(I)。將所得到的被覆銅顆粒的SEM觀察圖像示于圖23A。(比較例7)對比較例6進(jìn)行規(guī)模擴(kuò)大,使反應(yīng)時(shí)間為2倍,合成了被覆銅顆粒。將作為銅化合物的氧化亞銅(I)(古河化學(xué)社制造)71.5g(0.5摩爾)、作為被覆材料的乙酸15.0g(250mmol)、作為還原劑的肼一水合物(和光純藥工業(yè)制造]25.0g(0.5摩爾)、作為溶劑的異丙醇500ml進(jìn)行混合,加入至1,000ml的4口燒瓶中。對燒瓶安裝冷凝器、溫度計(jì)、氮?dú)鈱?dǎo)入管和攪拌裝置。一邊以200ml/min通入氮?dú)?,一邊進(jìn)行攪拌,升溫至70℃,繼續(xù)加熱、攪拌2小時(shí),使氧化亞銅(I)還原,得到被覆銅顆粒分散液。利用桐山濾紙No.5B對被覆銅顆粒分散液進(jìn)行減壓過濾,濾出粉體。將濾出的粉體用甲醇(關(guān)東化學(xué)工業(yè)制造)清洗3次,在40℃、1kPa以下的條件下進(jìn)行減壓干燥,冷卻至室溫后,進(jìn)行氮?dú)庵脫Q并取出,得到62g的茶褐色粉體。測定了粉體的XRD(示于圖22),結(jié)果原料氧化亞銅(I)定量地轉(zhuǎn)化為還原銅。將所得到的被覆銅顆粒的SEM觀察圖像示于圖26A。<評價(jià)>為了利用實(shí)施例1中制造的被覆銅顆粒明確被覆有脂肪族羧酸的被覆銅顆粒的組成,實(shí)施了粉體X射線分析、SEM觀察、Tof-SIMS表面分析和TG-DTA測定。為了調(diào)查實(shí)施例1中制造的被覆銅顆粒的核的結(jié)構(gòu)和粒徑,實(shí)施了粉體X射線分析。根據(jù)粉體X射線分析的結(jié)果(圖1A),檢測出來自還原銅的峰(2θ=43.3°附近),未檢測出氧化銅(2θ=35.5°和38.7°)、氧化亞銅(2θ=37.0°附近)。由該結(jié)果可知,本實(shí)施方式的被覆銅顆粒沒有氧化物層,以還原銅作為核而形成。由粉體X射線的衍射角度和半峰寬根據(jù)Scherrer公式計(jì)算出結(jié)晶粒徑。Scherrer公式由式(1)表示。D=Kλ/(βcosθ)···(1)此處,D為結(jié)晶粒徑,K為Scherrer常數(shù)(假定為球體,作為K=1代入),λ為測定X射線的波長(CuKα:),β由式(2)表示。β=b-B···(2)此處,b為峰的半峰寬,B為裝置的校正系數(shù)(B=0.114)。根據(jù)計(jì)算結(jié)果,被覆銅顆粒的微晶直徑DXRD為48.9nm。由SEM觀察結(jié)果計(jì)算出的平均一次粒徑DSEM為85.8nm,因而若計(jì)算DXRD/DSEM則為0.57,可知微晶直徑相對于平均一次粒徑比較大。為了調(diào)查被覆銅顆粒的表面組成,實(shí)施了Tof-SIMS表面分析。根據(jù)Tof-SIMS表面分析的結(jié)果,基本上定量地檢測出游離的月桂酸(示于圖2A),還檢測出一部分微量的、與63Cu和65Cu的氫氧化物結(jié)合的月桂酸(示于圖2B)。由于未檢測出與63Cu和65Cu結(jié)合的月桂酸,因而可知存在于被覆銅顆粒表面的是大體通過物理吸附所被覆的月桂酸。為了調(diào)查被覆銅顆粒中被覆表面的有機(jī)成分量,實(shí)施了TG-DTA分析(圖3)。由TG-DTA分析結(jié)果可知,熱失重為1.09質(zhì)量%,在月桂酸的沸點(diǎn)附近基本上全部脫離。該結(jié)果還暗示了月桂酸以物理方式吸附,推測被覆銅顆粒能夠表現(xiàn)出低溫?zé)Y(jié)性。通過下述方法計(jì)算出被覆銅顆粒的表面的脂肪族羧酸的被覆密度。根據(jù)Tof-SIMS的分析結(jié)果,若熱失重成分的總量假定為月桂酸,則被覆銅顆粒中包含的月桂酸的根數(shù)由式(3)表示。[月桂酸根數(shù)]=Macid/(MW/NA)···(3)此處,Macid為熱失重測定質(zhì)量值(g),MW為月桂酸分子量(g/mol),NA為阿伏伽德羅常數(shù)(6.02×1023根/mol)。由SEM觀測計(jì)算出的一次粒徑基本上全部來自還原銅,若其形狀假定為球體,則1g銅顆粒中的顆粒數(shù)由式(4)表示。[1g中的顆粒數(shù)]=MCu/[(4πr3/3)×d×10-21]···(4)此處,MCu為由熱失重測定值求出的質(zhì)量計(jì)算值(g),r為由SEM觀測計(jì)算出的一次粒徑的半徑(nm),d為密度(以銅的密度代入;d=8.94)。1g銅顆粒中的顆粒表面積利用式(4)、由式(5)表示。[1g中的銅顆粒表面積(nm2)]=[1g中的顆粒數(shù)]×4πr2···(5)利用月桂酸的銅顆粒的被覆密度(根/nm2)利用(3)式和(5)式、由式(6)表示。[被覆密度]=[月桂酸根數(shù)]/[1g中的銅顆粒表面積]···(6)由計(jì)算結(jié)果可知,被覆銅顆粒中的月桂酸的被覆密度為4.23根/nm2。根據(jù)《化學(xué)與教育(化學(xué)と教育)40卷2號(1992年)求出硬脂酸分子的截面積-實(shí)驗(yàn)值和計(jì)算值-(ステアリン酸分子の斷面積を求める-実験値と計(jì)算値-)》,由硬脂酸分子的范德華半徑計(jì)算出最小面積,由該計(jì)算值換算的飽和被覆面積理論值為約5.00根/nm2。由該理論值推測,本實(shí)施方式的被覆銅顆粒以比較高的密度在顆粒表面局部存在月桂酸。關(guān)于該濃密的被覆效果,雖然月桂酸被覆是比化學(xué)吸附弱的物理吸附,但認(rèn)為可作為耐氧化性優(yōu)異的理由。接著,關(guān)于本發(fā)明的反應(yīng)機(jī)制,以實(shí)施例1為例,通過反應(yīng)中排出的氣體和蒸發(fā)餾出物的成分分析來進(jìn)行推測。<氣體成分分析>方法:氣相色譜法測定器:GLSCIENCESGL320檢測器:導(dǎo)熱系數(shù)檢測器(TCD)柱:不銹鋼柱柱填充劑(氫):分子篩5A柱填充劑(二氧化碳):活性炭載氣(氫):N220mL/min載氣(二氧化碳):He50mL/min測定溫度:43~50℃電流值:70~120mA<蒸發(fā)餾出成分分析>方法:紅外分光法測定器:PerkinElmerSpectrumOne[表1]采集編號采集時(shí)刻(分)排出量(L/分鐘)H2(%)CO(%)CO2(%)備注(1)170.22<0.1<0.10.5其它為N2(2)191.030.5<0.152.3其它為N2(3)262.450.5<0.188.5其它為N2(4)282.2812.0<0.181.0(5)312.0945.1<0.150.0(6)441.4552.9<0.145.9(7)680.8836.5<0.157.9(8)760.8334.4<0.160.1(9)990.4233.2<0.164.6(10)1190.2729.3<0.162.6在反應(yīng)初期中,排出氣體成分為二氧化碳,由于反應(yīng)溫度為120℃左右(圖4),因而認(rèn)為經(jīng)過下述反應(yīng)式1以反應(yīng)式2的反應(yīng)機(jī)制進(jìn)行。即,首先通過1分子月桂酸發(fā)生與甲酸銅氨基醇絡(luò)合物的1分子甲酸的平衡交換反應(yīng)。(反應(yīng)式1)(HCOO-)(HCOO-)Cu2+·(H2NC3H6OH)2+C11H23COOH→(C11H23COO-)(HCOO-)Cu2+·(H2NC3H6OH)2+HCOOH通常認(rèn)為,在210~250℃附近顯示出熱分解性的甲酸銅通過形成基于月桂酸和3-氨基-1-丙醇的絡(luò)合物,從而熱分解溫度降低。在100~130℃附近通過絡(luò)合物的熱分解反應(yīng)而釋放出二氧化碳,同時(shí)二價(jià)銅離子的還原反應(yīng)進(jìn)行(反應(yīng)式2)。認(rèn)為月桂酸以物理方式吸附于絡(luò)合物的分解后生成的還原銅。(反應(yīng)式2)(C11H23COO-)(HCOO-)Cu2+·(H2NC3H6OH)2→Cu:C11H23COOH+2H2NC3H6OH+CO2認(rèn)為吸附于該還原銅的月桂酸取得了可逆平衡(反應(yīng)式3),在還原銅附近通過甲酸銅烷醇胺絡(luò)合物和反應(yīng)式1而再次發(fā)生月桂酸平衡交換反應(yīng),連續(xù)地產(chǎn)生還原金屬核。(反應(yīng)式3)Cu:C11H23COOH↑↓Cu+C11H23COOH在反應(yīng)后半部分,排出氣體成分為氫氣和二氧化碳,根據(jù)其成分比認(rèn)為下述反應(yīng)機(jī)制進(jìn)行。(反應(yīng)式4)。(HCOO-)(HCOO-)Cu2+·(H2NC3H6OH)2→Cu+2H2NC3H6OH+H2+2CO2和與甲酸銅形成絡(luò)合物的平衡交換反應(yīng)相比,隨著作為還原銅的顆粒生長機(jī)制的被覆材料的月桂酸被消耗,認(rèn)為不僅是反應(yīng)式1進(jìn)行,反應(yīng)式4也同時(shí)進(jìn)行。反應(yīng)中餾出的蒸發(fā)餾分為水分子(圖5)。在日本特開2011-032558號公報(bào)中公開了下述內(nèi)容:通過殘留的水分子,甲酸銅氨基醇絡(luò)合物受到水解,生成氧化銅。若適用于本發(fā)明,則通過下述反應(yīng)生成氧化銅。(反應(yīng)式5)(HCOO-)(HCOO-)Cu2+·(H2NC3H6OH)2+H2O→CuO+2H2NC3H6OH+2HCOOH反應(yīng)體系中存在水分子的情況下,認(rèn)為反應(yīng)式5的機(jī)制進(jìn)行,生成氧化銅,但在實(shí)施例1中得到的被覆銅顆粒中未確認(rèn)到銅氧化物的存在(圖1A)。由這些結(jié)果推測,與主反應(yīng)不同,存在將氧化銅還原的反應(yīng)機(jī)制。作為氧化銅的還原反應(yīng)機(jī)制,可考慮例如反應(yīng)式6這樣的基于甲酸的還原反應(yīng)。(反應(yīng)式6)。2CuO+2HCOOH→Cu2O+HCOOH+H2O+CO2→2Cu+2H2O+2CO2另外,還考慮如反應(yīng)式7這樣通過氧化銅和甲酸而再生出甲酸銅,還原反應(yīng)進(jìn)行。(反應(yīng)式7)CuO+2HCOOH→(HCOO-)(HCOO-)Cu2++H2O再生的甲酸銅經(jīng)過反應(yīng)式1并根據(jù)反應(yīng)式2進(jìn)行還原反應(yīng)。通過這些副反應(yīng),認(rèn)為生成水分子,作為蒸發(fā)餾分而排出。該副反應(yīng)是只要反應(yīng)體系中存在甲酸就可發(fā)生的反應(yīng),因此推測,即便生成氧化銅,通過反應(yīng)式6和反應(yīng)式7的還原反應(yīng)機(jī)制也能夠合成沒有氧化膜的被覆銅顆粒。為了驗(yàn)證該還原反應(yīng)機(jī)制是否在本實(shí)施方式的制造方法中發(fā)生,有意地向反應(yīng)體系中加入氧化銅而實(shí)施反應(yīng),進(jìn)行了確認(rèn)。其結(jié)果在參考例2中進(jìn)行說明。(參考例2)將具備攪拌機(jī)、溫度計(jì)、回流冷凝管、氮?dú)鈱?dǎo)入管的100mL玻璃制四口燒瓶設(shè)置于油浴。向其中添加甲酸銅無水物12.0g(0.08摩爾)、氧化銅(關(guān)東化學(xué)社制造)2.0g(0.32當(dāng)量/甲酸銅無水物)、月桂酸(關(guān)東化學(xué)社制造試、試劑1級)2.0g(0.12當(dāng)量/甲酸銅無水物)、三丙二醇單甲醚(東京化成社制造)4.4g(0.27當(dāng)量/甲酸銅無水物)、スワクリーン150(Godo社制造)16.6g(1.67當(dāng)量/甲酸銅無水物),一邊以200rpm進(jìn)行攪拌一邊進(jìn)行混合。在氮?dú)鈿夥障乱?00rpm加熱攪拌至液溫達(dá)到50℃。向其中緩慢滴加3-氨基-1-丙醇(東京化成社制造)21.0g(3.50當(dāng)量/甲酸銅無水物)。滴加結(jié)束后,以340rpm加熱攪拌至液溫達(dá)到120℃左右。隨著液溫升高,反應(yīng)溶液開始由深藍(lán)色變?yōu)椴韬稚a(chǎn)生二氧化碳的起泡。將二氧化碳的起泡結(jié)束作為反應(yīng)終點(diǎn),停止油浴溫度調(diào)節(jié),冷卻至室溫。冷卻至室溫后,添加甲醇(關(guān)東化學(xué)社制造)20.0g進(jìn)行混合。將該混合溶液靜置30分鐘以上,傾潷上清,得到沉淀物。向該沉淀物中添加甲醇(關(guān)東化學(xué)社制造)20.0g、丙酮(關(guān)東化學(xué)社制造)10.0g進(jìn)行混合。將該混合溶液靜置30分鐘以上,傾潷上清,得到沉淀物,再重復(fù)一次該操作。利用甲醇(關(guān)東化學(xué)社制造)20.0g對該沉淀物進(jìn)行共洗,同時(shí)移至100mL茄型燒瓶中。靜置30分鐘以上,傾潷上清,將所得到的沉淀物設(shè)置于旋轉(zhuǎn)式蒸發(fā)器中,在40℃、1kPa以下進(jìn)行真空干燥。真空干燥結(jié)束后,冷卻至室溫,一邊進(jìn)行氮?dú)庵脫Q一邊減壓釋放,得到6.5g的茶褐色銅粉末。對參考例2中得到的被覆銅顆粒實(shí)施了粉體X射線分析(圖6)??芍砑拥难趸~基本上被還原,轉(zhuǎn)化為還原銅。由該結(jié)果暗示,即便反應(yīng)體系中生成氧化銅,也可通過基于甲酸的還原反應(yīng)而轉(zhuǎn)化為還原銅。根據(jù)日本特開2011-032558號公報(bào)中記載的反應(yīng)機(jī)制例,與本實(shí)施方式同樣地形成包含脂肪族羧酸的甲酸銅氨基醇絡(luò)合物。(反應(yīng)式8)。(R1COO-)(HCOO-)Cu2+:[(C2H5)2NC2H4OH]2→Cu:[(C2H5)2NC2H4OH]2+R1COOH+CO2另外,在日本特開2011-032558號公報(bào)中記載了下述內(nèi)容:由于限定為雙齒配位性的氨基醇,因而這樣的甲酸銅絡(luò)合物的熱分解溫度低;在脂肪族羧酸與甲酸銅氨基醇絡(luò)合物的交換反應(yīng)中脫離的甲酸被排出到體系外。此外,由于為低溫下的反應(yīng)條件,因此認(rèn)為基于反應(yīng)體系中存在的甲酸的還原反應(yīng)不進(jìn)行。另外,根據(jù)日本特開2008-013466號公報(bào)中記載的反應(yīng)機(jī)制例,存在于反應(yīng)體系中的甲酸全部通過絡(luò)合物的熱分解反應(yīng)而被分解為氫和二氧化碳。(反應(yīng)式9)(HCOO-)(HCOO-)Cu2+·(NH2R2)2→Cu+2NH2R2+H2+2CO2與此相對,在本實(shí)施方式的反應(yīng)機(jī)制中,通過甲酸銅絡(luò)合物的熱分解反應(yīng)而生成還原銅,并且根據(jù)反應(yīng)式6和反應(yīng)式7,還同時(shí)兼具將副產(chǎn)物氧化銅還原的反應(yīng)機(jī)制,因此是所合成的被覆銅顆粒難以被氧化的制造方法。本實(shí)施方式的制造方法不需要對作為金屬銅氧化的原因所舉出水或氧進(jìn)行嚴(yán)密的制造管理,是適合于更簡便的合成的制造方法。接著,對于實(shí)施例1~4和比較例1~5中得到的被覆銅顆粒,實(shí)施了原料的SP值計(jì)算、TG-DTA測定、粉體X射線分析(XRD)和SEM觀察。測定方法如下。結(jié)果示于表2。[表2]如表2的結(jié)果所示,可知:構(gòu)成甲酸銅氨基醇絡(luò)合物的氨基醇的SP值與反應(yīng)溶劑、或者主溶劑與輔助溶劑的混合溶劑的SP值之差即ΔSP值大、為4.2以上的情況下,能夠制造個(gè)別的被覆銅顆粒,但在4.2以下的情況下,無法形成個(gè)別的被覆銅顆粒,而形成凝聚體的形態(tài),作為被覆銅顆粒的制造方法不合適。另外,關(guān)于在一次顆粒中所占的晶粒的大小的比例,若將其定義為結(jié)晶度,則為0.25以上,在大多情況下為0.50左右,表明由1個(gè)大的微晶構(gòu)成了被覆銅顆粒。對于實(shí)施例5~8和比較例6~7中得到的被覆銅顆粒,實(shí)施了粉體X射線分析和SEM觀察。將結(jié)果示于表3。[表3]若反應(yīng)時(shí)的升溫速度一定,則還原反應(yīng)的速度相同,金屬核的產(chǎn)生量也相同,因此可知,根據(jù)控制類似油包水的微反應(yīng)場的尺寸、穩(wěn)定性的因素的不同,粒徑和粒度分布存在差異。若是使微反應(yīng)場穩(wěn)定化的方向,則具有粒徑和變動(dòng)系數(shù)小的傾向,脂肪族羧酸的碳鏈越長則該傾向越大(實(shí)施例1、實(shí)施例5和實(shí)施例9的比較)。另外,脂肪族羧酸相對于銅原子的摩爾數(shù)變多時(shí),也具有穩(wěn)定化的傾向,但在反應(yīng)粘度升高的情況下,即使變動(dòng)系數(shù)小,粒徑也變大(實(shí)施例1、實(shí)施例6和7的比較)。還確認(rèn)到:即便改變反應(yīng)溶劑中的主溶劑與輔助溶劑的比例,使平均SP值從8.21變化為8.90,只要確保與氨基醇的ΔSP,則所得到的被覆銅顆粒的特性也不會(huì)產(chǎn)生大的差異(實(shí)施例1和實(shí)施例8的比較)。與此相對,根據(jù)在本實(shí)施方式的被覆銅顆粒和被覆材料為脂肪族羧酸這點(diǎn)上類似的日本特開2013-047365號公報(bào)的實(shí)施例,在比較例6和7中嘗試了制造被覆銅顆粒。這些方法是使銅原子的供給源為作為難溶性固體的儲(chǔ)存單元而制造被覆銅顆粒的方法。作為原料氧化亞銅(I),使用了粒徑小為2~4μm的物質(zhì),但在規(guī)定時(shí)間內(nèi)未反應(yīng)物殘留。通過使反應(yīng)時(shí)間加倍,從而定量地轉(zhuǎn)化為還原銅,但平均粒徑變大。另外,粒度分布也大,變動(dòng)系數(shù)為0.38和0.29。(試驗(yàn)例1)耐氧化性的評價(jià)確認(rèn)了在實(shí)施例1的條件下剛制造后的粉體X射線分析結(jié)果,并且在25℃儲(chǔ)藏4個(gè)月后同樣地進(jìn)行測定,確認(rèn)了有無氧化的進(jìn)行(圖1A和圖1B)。4個(gè)月后也未檢測出氧化成分,確認(rèn)到利用本實(shí)施方式的制造方法所制作的被覆銅顆粒具有優(yōu)異的耐氧化性。(試驗(yàn)例2)基于被覆銅顆粒漿料的燒制覆膜的特性將在實(shí)施例1的條件下制造的被覆銅顆粒用溶劑分散,制作銅漿組合物,在氮?dú)鈿夥障略?00℃和350℃進(jìn)行1小時(shí)燒制,制作銅覆膜(銅漿燒結(jié)層),測定了該覆膜的電阻。以形成下述組成的方式利用研缽將被覆銅顆粒和溶劑分散混煉,進(jìn)行漿料化,調(diào)配出金屬含量為33體積%的銅漿組合物。銅漿組合物A實(shí)施例1的被覆銅顆粒10質(zhì)量份KYOWANOLM(NHNeochem制造)2質(zhì)量份在內(nèi)側(cè)層積有12μm銅箔的40μm厚聚酰亞胺膜上,以濕厚度約10μm涂布該銅漿,在氮?dú)鈿夥障逻M(jìn)行干燥和燒制,制作出評價(jià)用試樣。通過基于SEM的截面觀察,對燒制后的銅的平均膜厚進(jìn)行計(jì)測。銅漿燒結(jié)層的膜厚為2.4μm。將所制作的被覆銅顆粒和燒制銅覆膜的SEM觀察圖像示于圖24A和圖24B,將測定中使用的評價(jià)用試樣的SEM截面觀察圖像示于圖25,將測定結(jié)果示于表4。在圖25中,在40μm厚聚酰亞胺膜層20的一個(gè)面上具有12μm厚銅箔層30的聚酰亞胺膜的與銅箔層30相反側(cè)的面上形成了作為銅漿組合物的燒制物的銅漿燒結(jié)層10。(試驗(yàn)例3)使用比較例7中制造的被覆銅顆粒,與試驗(yàn)例2同樣地制作銅漿組合物B,在氮?dú)鈿夥障掠?50℃進(jìn)行1小時(shí),制作出銅覆膜,測定了該覆膜的電阻。銅漿組合物B比較例7的被覆銅顆粒10質(zhì)量份KYOWANOLM(NHNeochem制造)2質(zhì)量份將所制作的被覆銅顆粒和燒制銅覆膜的SEM觀察圖像示于圖26A和圖26B,將電阻的測定結(jié)果示于表4。(試驗(yàn)例4)基于被覆銅顆粒與銅粉的混合漿料的燒制覆膜的特性添加實(shí)施例1中制造的被覆銅顆粒作為市售的銅粉的燒結(jié)劑,制作出銅漿組合物,在氮?dú)鈿夥障掠?00℃和350℃進(jìn)行1小時(shí)燒制,制作出銅覆膜,測定了該覆膜的電阻。按照形成下述組成的方式,利用三輥磨機(jī)對各材料進(jìn)行分散混煉,調(diào)配出金屬含量為60體積%的銅漿組合物。銅漿組合物C在內(nèi)側(cè)層積有12μm銅箔的40μm厚聚酰亞胺膜上,以濕厚度約10μm涂布該銅漿,在氮?dú)鈿夥障逻M(jìn)行干燥和燒制,制作出評價(jià)用試樣。通過基于SEM的截面觀察,對燒制后的銅的平均膜厚進(jìn)行計(jì)測。銅漿燒結(jié)層的膜厚為4.2μm。將測定中使用的評價(jià)用試樣的SEM截面觀察圖像示于圖27,將測定結(jié)果示于表4。在圖27中,在40μm厚聚酰亞胺膜層20的一個(gè)面上具有12μm厚銅箔層30的聚酰亞胺膜的與銅箔層30相反側(cè)的面上形成了作為銅漿組合物的燒制物的銅漿燒結(jié)層10。[表4]利用在非還原氣氛下能夠燒制的被覆銅顆粒制作銅漿組合物,對該燒結(jié)銅覆膜的電學(xué)特性及其表面組成結(jié)構(gòu)進(jìn)行評價(jià),從而確認(rèn)了工業(yè)上的技術(shù)有用性。使利用了實(shí)施例1中制造的被覆銅顆粒的銅漿組合物A為試驗(yàn)例2,使與市售的銅粉混合的銅漿組合物C為試驗(yàn)例4,作為比較,使利用了根據(jù)日本特開2013-047365號公報(bào)的實(shí)施例1所制作的比較例7中制作的被覆銅顆粒的銅漿組合物B為試驗(yàn)例3,分別對電學(xué)特性和XPS中的表面組成結(jié)構(gòu)進(jìn)行了評價(jià)。其結(jié)果,利用實(shí)施例1的被覆銅顆粒制備的銅漿組合物A和C顯示出4~6μΩ·cm的高導(dǎo)電性能。另外確認(rèn)到,未處理的聚酰亞胺面顯示出高密合性,在通常的彎曲測試中不發(fā)生剝離。銅漿組合物B是被相同的脂肪族羧酸所被覆的被覆銅顆粒,但顯示出22μΩ·cm這樣的比銅塊的體積固有電阻值高一位以上的值。通過XPS對利用銅漿組合物A和B所制作的燒結(jié)銅覆膜的表面組成結(jié)構(gòu)進(jìn)行組成分析,考察了電學(xué)特性的差異發(fā)生的機(jī)理。圖28和圖29的窄掃描(NarrowScan)中得到的數(shù)據(jù)顯示出銅漿組合物A和B的燒結(jié)銅覆膜的最外表面的組成信息。銅漿組合物B的燒結(jié)銅覆膜的最外表面與銅漿組合物A的燒結(jié)銅覆膜的最外表面相比,可知還原銅的比例高,氧化銅成分和有機(jī)物成分的比例少。利用銅漿組合物A制成的燒結(jié)銅覆膜的最外表面被推測是月桂酸的脂肪族羧酸所被覆,從而有機(jī)物成分增多。但是,雖然有氧化物成分,但還原銅以相當(dāng)?shù)牧柯冻?,可判斷不?huì)損害接觸電阻。接著,利用氬離子進(jìn)行蝕刻,通過XPS的深度剖析分析明確了從最外表面起幾nm的區(qū)域的表面組成。結(jié)果可知,銅漿組合物A和B均是從最外表面起深于1~2nm的區(qū)域由還原銅構(gòu)成。但是,銅漿組合物B與A相比,在深于幾nm的區(qū)域中碳成分也未減少,因而可預(yù)測燒結(jié)密度低。另外,在SEM觀察的結(jié)果中,燒結(jié)密度也存在明顯的差異,認(rèn)為這會(huì)成為電學(xué)特性的差異而顯現(xiàn)。因此可知,對于表現(xiàn)出被覆銅顆粒的低溫?zé)Y(jié)性的結(jié)構(gòu)來說,重要的并不是在低溫下去除被覆銅顆粒的被覆材料,而是以銅顆粒彼此的接觸、縮頸(necking)和銅原子的相互擴(kuò)散不被抑制的方式適度地被去除。在由本發(fā)明的被覆銅顆粒得到的燒結(jié)銅覆膜中,存在于顆粒間的被覆材料的脂肪族羧酸被有效地去除,同時(shí)可實(shí)現(xiàn)顆粒的接觸、縮頸以及銅原子的相互擴(kuò)散,可以達(dá)到接近銅塊的電阻值的特性。另外還可知,其結(jié)果,燒結(jié)銅覆膜的最外表面被被覆材料的脂肪族羧酸所覆蓋,可以期待作為對于氧的阻隔層。本發(fā)明的被覆銅顆粒的制造方法通過獨(dú)自的微反應(yīng)場來控制粒徑,能夠制造顆粒表面被脂肪族羧酸的高密度被覆層所覆蓋的耐氧化性優(yōu)異的被覆銅顆粒。并且,所得到的被覆銅顆?;旧嫌蛇€原銅構(gòu)成,認(rèn)為作為被覆材料的脂肪族羧酸以物理吸附的方式結(jié)合。因此,在被覆材料的沸點(diǎn)附近發(fā)生脫離,表現(xiàn)出燒結(jié)能力,因此能夠得到例如在常壓、300℃以下的比較低的溫度下具有接近銅塊的體積固有電阻值的銅燒結(jié)覆膜。此外,可以將被覆銅顆粒用溶劑等進(jìn)行漿料化,利用絲網(wǎng)印刷等手段形成配線圖案,所形成的配線圖案的燒制氣氛也是只要為低氧狀態(tài)即可,可以構(gòu)成能夠使用通常的氮?dú)庵脫Q爐等的通用性高的生產(chǎn)工藝。以參照的方式將日本國專利申請20104-112794號(申請日:2014年5月30日)的全部公開內(nèi)容引入本說明書中。本說明書中記載的全部文獻(xiàn)、專利申請以及技術(shù)標(biāo)準(zhǔn)與具體且分別記載了以參照的方式引入各個(gè)文獻(xiàn)、專利申請以及技術(shù)標(biāo)準(zhǔn)時(shí)相同程度地以參照的方式被引入本說明書中。當(dāng)前第1頁1 2 3