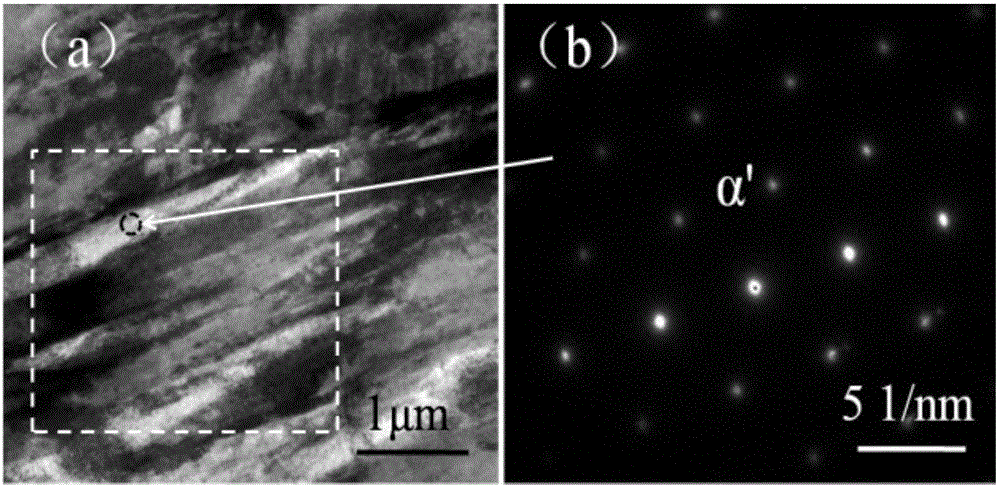
本發(fā)明屬于第三代高強(qiáng)汽車用鋼板卷的生產(chǎn)
技術(shù)領(lǐng)域:
,特別是提供了一種具有優(yōu)良塑性的超高強(qiáng)度中錳汽車鋼板及制備方法。是基于多種強(qiáng)化機(jī)制,將成分與組織控制相結(jié)合的設(shè)計(jì)理念來開發(fā)的新鋼種,著重通過不同的軋制工藝控制和成分設(shè)計(jì)獲得超細(xì)晶粒和亞微米級析出相,并且采用適宜的臨界區(qū)退火處理獲得鐵素體和奧氏體等多相組織,通過析出強(qiáng)化、形變誘導(dǎo)相變強(qiáng)化和孿晶強(qiáng)化手段獲得的新型具有優(yōu)良塑性的超高強(qiáng)度汽車鋼板的制備工藝。
背景技術(shù):
:隨著汽車工業(yè)的飛速發(fā)展,人們在享受交通便利的同時(shí),也遭受著汽車帶來的大氣污染和資源浪費(fèi)。汽車鋼輕量化、高強(qiáng)化是汽車安全、長壽、低成本和節(jié)能減排的必然趨勢。第一代汽車鋼(AHSS,IF,BH,DP,TRIP和馬氏體鋼等)平均15-20GPa·%的強(qiáng)塑積不能滿足日益增長的汽車安全碰撞系數(shù)和沖壓零部件優(yōu)良成型性的需求,第二代汽車鋼(TWIP,奧氏體不銹鋼等)具有優(yōu)良的機(jī)械性能強(qiáng)塑積可達(dá)60GPa·%,但由于材料成本或工藝成本過高難以大規(guī)模生產(chǎn)。在此基礎(chǔ)上美國的Krupitzer和Heimbuch提出第三代汽車鋼的概念,即該鋼不但具有良好的強(qiáng)度和塑性(強(qiáng)塑積可達(dá)到30GPa·%),而且其合金含量遠(yuǎn)遠(yuǎn)低于第二代汽車鋼,實(shí)現(xiàn)了輕量化、低成本、高安全的多重要求。錳含量為5%~12%的中錳鋼以其低廉的成本、相對小的密度和優(yōu)良的力學(xué)性能受到了各國科學(xué)家的廣泛關(guān)注,并被認(rèn)為是最有前景的第三代先進(jìn)汽車用鋼之一?,F(xiàn)有中錳鋼的研究大多采用不同的技術(shù)手段進(jìn)行組織控制獲得含有穩(wěn)定殘余奧氏體的復(fù)相組織,通過變形過程中殘奧的TRIP效應(yīng)提升汽車鋼板的強(qiáng)度和成型性。目前針對中錳體系的汽車用鋼國內(nèi)學(xué)者已經(jīng)進(jìn)行了深入的研究,比如中國專利文獻(xiàn)中申請?zhí)枮?01310507894.9的專利公開了0.1-0.4%C+3-8%Mn成分體系的中錳鋼經(jīng)熱連軋→冷軋→連續(xù)退火可以得到抗拉強(qiáng)度980MPa和1180MPa兩種級別的鋼板;申請?zhí)?01210429409.6的專利公開了0.05-0.45%C+2.5-8%Mn的中錳鋼經(jīng)熱軋→退火或者熱軋→冷軋→兩段式退火可得到強(qiáng)度在0.6-1.2GPa,延伸率范圍45-20%的鋼板;200910091129.7和201110005359.4的專利公開了0.01-0.50%C+3.50-9%Mn的中錳鋼經(jīng)經(jīng)熱軋→罩式退火→冷軋→罩式退火或連續(xù)退火可以得到強(qiáng)度0.7-1.3GPa,延伸率55-30%的鋼板;201210261920.X的專利公開了0.11-0.30%C+0.1-2.0%Si+5-10%Mn的中錳鋼經(jīng)熱軋→卷取→罩式爐退火→冷軋→連續(xù)退火工藝可以得到抗拉強(qiáng)度1000MPa級別、強(qiáng)塑積30GPa%的鋼板。由上可見,雖然中錳TRIP鋼通過不超過9%Mn含量的成分,可以獲得良好的塑性,且強(qiáng)塑積達(dá)到了30GPa·%以上,但是其屈服強(qiáng)度一般<700MPa,且抗拉強(qiáng)度一般在1000Pa之內(nèi),不超過1300MPa以下,嚴(yán)重阻礙了汽車進(jìn)一步輕量化的進(jìn)程。因此在更高強(qiáng)度級別的汽車用鋼板技術(shù)還是個(gè)空白。技術(shù)實(shí)現(xiàn)要素:本發(fā)明的目的在于提供一種具有優(yōu)良塑性的超高強(qiáng)度中錳汽車鋼板及制備方法,解決了上述問題。本發(fā)明采用成分與組織控制相結(jié)合的設(shè)計(jì)理念,在進(jìn)一步優(yōu)化和窄化中錳鋼碳和錳成分含量基礎(chǔ)上,添加微合金強(qiáng)化元素V,通過顯著的析出強(qiáng)化效果提高屈服和抗拉強(qiáng)度(圖1);并且通過熱-機(jī)械處理和臨界退火處理獲得超細(xì)晶粒、雙相組織,并使C和Mn元素在殘留奧氏體相中富集到一定程度,導(dǎo)致殘余奧氏體有足夠的穩(wěn)定性以保證鋼板在變形過程中奧氏體相會發(fā)生TRIP(相變誘導(dǎo)塑性)或TWIP(孿生誘導(dǎo)塑性)效應(yīng)(圖2-3),從而最終獲得超高強(qiáng)度且塑性優(yōu)良的汽車鋼板。本發(fā)明設(shè)計(jì)了兩種工藝得到不同拉伸性能結(jié)合的鋼板,一是溫軋鋼板經(jīng)過罩式退火5h以上后,得到超高強(qiáng)度1500MPa級別鋼板,其屈服強(qiáng)度≥1000MPa,抗拉強(qiáng)度≥1500MPa,延伸率為15%-22%,強(qiáng)塑積為20-40GPa·%;二是冷軋鋼板經(jīng)700-800℃連續(xù)退火5-10min后,得到強(qiáng)度級別1200MPa以上的超高強(qiáng)度高塑性鋼板,其屈服強(qiáng)度為750-1100MPa,抗拉強(qiáng)度為1200-1600MPa,延伸率為20-50%,強(qiáng)塑積達(dá)到20-70GPa·%。本發(fā)明的創(chuàng)新之處在于將多種強(qiáng)化手段(細(xì)晶強(qiáng)化、沉淀強(qiáng)化、形變誘導(dǎo)相變強(qiáng)化和孿晶強(qiáng)化)與雙相鋼的生產(chǎn)工藝相結(jié)合,著重通過改變不同的軋制和退火工藝在顯著提高汽車鋼板強(qiáng)度的同時(shí),保證了良好的成型性。本發(fā)明的鋼板化學(xué)成分設(shè)計(jì)鋼板的化學(xué)成分借鑒羅海文教授等開發(fā)的雙相、孿生誘導(dǎo)塑性、超高強(qiáng)度汽車鋼板(申請公開號為201410669029.9)的化學(xué)成分基礎(chǔ)上進(jìn)行優(yōu)化,添加合金元素V,各個(gè)元素的比例為:0.3-0.5wt%C,8-12wt%Mn,1.8-3.5wt%Al,0.25-0.7wt%V,P≤0.008wt%,S≤0.08wt%,余量為Fe及不可避免的不純物。其中V元素的添加一方面可以細(xì)化晶粒,另一方面通過形成納米尺度的析出物起到沉淀強(qiáng)化的作用,之前的應(yīng)用V的微合金化多用于BCC類型組織的鋼中進(jìn)行沉淀強(qiáng)化,而多相組織鋼的屈服通常都是在較軟相中開始的,因此只進(jìn)行某一相的選擇性強(qiáng)化可能并不會顯著提高鋼的屈服強(qiáng)度;而本發(fā)明中V的添加可導(dǎo)致FCC和BCC類型兩種不同結(jié)構(gòu)的組織中都可以進(jìn)行納米尺度的析出沉淀強(qiáng)化,從而使得基體的屈服強(qiáng)度大幅度提高。該鋼板還可以包括以下Ni:0.1-3.0wt%、Cr:0.2-3.0wt%、Mo:0.1-0.8wt%、Si:0.3-2.3wt%、Cu:0.5-2.0wt%、B:0.0005-0.005wt%、Nb:0.02-0.10wt%、[N]:0.002-0.25wt%、Ti:0.05-0.25wt%、RE稀土:0.002-0.005wt%或Ca:0.005-0.03wt%中的一種或多種混合。通過合理的化學(xué)成分和工藝設(shè)計(jì)實(shí)現(xiàn)析出強(qiáng)化、形變誘導(dǎo)相變強(qiáng)化、孿晶強(qiáng)化等多種強(qiáng)化機(jī)制的綜合應(yīng)用,進(jìn)而獲得超高強(qiáng)度。通過熱軋→酸洗→溫軋→罩式退火工藝可以獲得抗拉強(qiáng)度超過1500MPa、強(qiáng)塑積20-40GPa%的鋼板;或者熱軋→熱軋退火→酸洗→冷軋→連續(xù)退火工藝可以獲得抗拉強(qiáng)度超過1200MPa、強(qiáng)塑積35-65GPa·%的冷軋鋼板。本發(fā)明的超高強(qiáng)汽車板的制備工藝步驟1按照上述化學(xué)成分百分比分別稱取原料,通過轉(zhuǎn)爐、電爐或感應(yīng)爐冶煉獲得鋼液;步驟2將步驟1所獲得的鋼液,通過連鑄生產(chǎn)得到鑄坯或模鑄生產(chǎn)得到鑄錠;步驟3熱軋。將鑄坯或鑄錠經(jīng)1100-1250℃加熱,經(jīng)粗軋機(jī)進(jìn)行3-10道次軋制,熱軋到30-50mm厚度規(guī)格,在溫度為1000-1100℃進(jìn)入熱連軋機(jī)組進(jìn)行5-7道次軋制到3-10mm,軋后在550-700℃卷取。步驟4本步驟分為兩個(gè)工藝路線,溫軋→罩式退火或者冷軋→連續(xù)退火。溫軋:首先將步驟3制得的熱軋板卷進(jìn)行酸洗處理,然后將酸洗過后的熱軋板卷在250℃-700℃之間某一溫度保溫5-10min,在冷軋機(jī)帶溫軋制到1.5-2mm后,卷取,然后空冷至室溫。當(dāng)加熱溫度較高時(shí)(500-700℃),需要注意鋼板離開加熱爐后溫降明顯,其具體加熱溫度的選擇要保證鋼卷在出爐后,經(jīng)過溫降,仍能保證至軋機(jī)時(shí)的第一道次軋制溫度≥450℃,在高加熱溫度時(shí)的保溫時(shí)間要短于低加熱溫度,避免在加熱時(shí)鋼板氧化。經(jīng)過3-8道次軋制到1.5-2mm后,溫軋壓下率在30-70%之間,卷取,然后空冷至室溫。冷軋:首先將步驟3制得的熱軋板卷在650-700℃罩式退火5-10h,空冷至室溫,然后對熱軋板進(jìn)行酸洗處理,將酸洗過后的熱軋板卷進(jìn)行5-25道次冷軋,至1.5-2.0mm,冷軋壓下率在50-65%之間。步驟5將溫軋后的板卷在600-650℃罩式退火5-50h,然后空冷至室溫,得到屈服強(qiáng)度:1000-1200MPa,抗拉強(qiáng)度:1500-1800MPa,延伸率為15%-22%,強(qiáng)塑積為20-40GPa·%的10Mn超高強(qiáng)汽車鋼板;冷軋鋼板在700-800℃連續(xù)退火5-10min后得到屈服強(qiáng)度為750-1100MPa,抗拉強(qiáng)度為1100-1600MPa,延伸率為35-65%,強(qiáng)塑積達(dá)到35-65GPa·%的具有優(yōu)良塑性的超高強(qiáng)汽車鋼板;溫軋板罩式退火或者冷軋板連續(xù)退火后,優(yōu)秀的力學(xué)性能歸因于熱-機(jī)械處理獲得的超細(xì)晶雙相組織和V的添加帶來的沉淀強(qiáng)化效應(yīng),其適當(dāng)?shù)膴W氏體穩(wěn)定性可以在變形過程中發(fā)生TRIP或TWIP效應(yīng),同時(shí)提高汽車鋼板的強(qiáng)度和塑性,而溫軋工藝獲得的強(qiáng)度更高,是由于溫軋時(shí)的再結(jié)晶可得到更為細(xì)小的鐵素體和奧氏體晶粒,在退火后還很穩(wěn)定,有助于屈服強(qiáng)度的進(jìn)一步提高。本發(fā)明生產(chǎn)的汽車鋼板的屈服強(qiáng)度可以達(dá)到了千兆帕級,且抗拉強(qiáng)度已經(jīng)明顯超越了現(xiàn)有汽車用馬氏體鋼,并且延伸率明顯高于馬氏體鋼。這為汽車鋼的進(jìn)一步輕量化提供了生產(chǎn)依據(jù)。附圖說明圖1為本發(fā)明生產(chǎn)的溫軋板中含V析出相均勻彌散的分布在奧氏體和鐵素體晶粒內(nèi)的透射電鏡照片。圖2為本發(fā)明生產(chǎn)的溫軋板斷口附近的相變馬氏體組織(a)及其衍射斑點(diǎn)(b)的透射電鏡照片。圖3為本發(fā)明生產(chǎn)的溫軋板斷口附近的形變孿晶組織(a)和其衍射斑點(diǎn)(b)的透射電鏡照片。具體實(shí)施方式實(shí)施例下面就實(shí)施例對本發(fā)明的技術(shù)方案做進(jìn)一步說明。表1發(fā)明鋼化學(xué)成分成分C%Mn%Al%P%S%V%Nb%A0.479.971.85<0.005<0.0050.7-B0.3811.693.14<0.005<0.0050.720.1C0.308.962.5<0.005<0.0050.3-D0.358.212.56<0.005<0.0050.310.031冶煉澆鑄:實(shí)施例采用表1所示化學(xué)成分百分比稱取原料,通過感應(yīng)爐冶煉澆注成錠后,熱鍛成50mm厚的板坯;2粗軋:將熱鍛后的板坯在1150℃固溶2.5個(gè)小時(shí),開軋溫度1000℃,4-7道次軋完,終軋溫度800℃(4mm厚),軋后在550-700℃卷??;3溫軋或冷軋:將A,B鋼熱軋板卷酸洗后在250℃,400℃,600℃,750℃,800℃進(jìn)行不同壓下量(50%,63%)的溫軋?zhí)幚?;將C鋼的熱軋板卷在650℃軟化退火10h,D鋼熱軋板卷700℃軟化退火5h,然后酸洗后都進(jìn)行冷軋,壓下量分別為50%,63%。4退火:將經(jīng)過不同溫軋工藝軋制的A鋼和B鋼在600-650℃之間不同的退火溫度進(jìn)行罩式退火5h,C鋼和D鋼在700-800℃之間進(jìn)行5-10min的連續(xù)退火,空冷后加工成標(biāo)準(zhǔn)樣品進(jìn)行拉伸實(shí)驗(yàn)。表2中試驗(yàn)號中字母對應(yīng)的是表1中的各個(gè)成分。四個(gè)成分不同退火和軋制試驗(yàn)方案所獲得的機(jī)械性能也列入表2,力學(xué)性能指標(biāo)均是取自2-3個(gè)拉伸試樣的平均值。表2A,B,C和D鋼板經(jīng)過不同軋制工藝和亞臨界退火后的力學(xué)性能(表中試驗(yàn)號字母對應(yīng)表1中的成分)由表2看出,其中A1、A4、A5、A8、A9、A10、A11、A12、A14、B2、B4、B5、B6溫軋板經(jīng)過罩式退火后的屈服強(qiáng)度均超過1GPa,抗拉強(qiáng)度在1500MPa以上,其強(qiáng)度性能接近現(xiàn)有的熱成型鋼,而同時(shí)都有良好的塑性,其強(qiáng)塑積在30GPa·%附近;C2、C3、C4、C5、D2、D3、D4和D5的冷軋板經(jīng)過短時(shí)間連續(xù)退火后的強(qiáng)度在1200-1600MPa之間,并且有非常出眾的延展性,強(qiáng)塑積最高可以達(dá)到65GPa·%。上述兩個(gè)工藝所得到的鋼板的力學(xué)性能要領(lǐng)先于現(xiàn)有報(bào)道的產(chǎn)品性能。當(dāng)前第1頁1 2 3