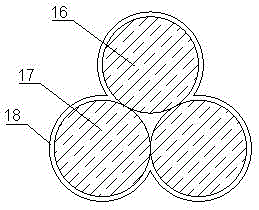
本發(fā)明涉及一種耐磨太陽能硅片線切割鋼線的制作方法及制備耐磨線切割鋼線用真空涂覆鍍膜設(shè)備。
背景技術(shù):
:中國光伏發(fā)電產(chǎn)業(yè)經(jīng)過近十幾年迅猛發(fā)展,太陽能硅片切割的耗材成本已降低到最低限度,其中切割用鋼線隨切片機(jī)臺的擴(kuò)產(chǎn)而大量消耗、年消耗鋼線材約十幾萬噸。在太陽能硅片線切割過程中,整個機(jī)理是利用碳化硅顆粒的堅硬特性和鋒利菱角將硅棒逐步截斷,因此切割中砂漿均勻地包覆在高速運(yùn)動中的鋼線表面,均勻平穩(wěn)的使碳化硅微粒作用于硅棒表面,同時及時帶走切割熱和破碎顆粒,保證硅片的表面質(zhì)量,鋼線是切割砂漿的一個載體同時也被高速運(yùn)動中的碳化硅間接磨損,線徑發(fā)生變化而影響線切品質(zhì)。隨著整個太陽能行業(yè)的發(fā)展,在太陽能硅片線切割中大量使用線切割鋼線,不利于環(huán)境控制,同時造成企業(yè)成本的增加,為了適應(yīng)未來市場需求及價格的競爭發(fā)展需要,整個行業(yè)都在為如何提高鋼線表面耐磨性、降低使用量、提高切割效率、降低切割綜合成本而又不改變現(xiàn)有切割設(shè)備和工藝,不停地尋找新的途徑。技術(shù)實(shí)現(xiàn)要素:本發(fā)明的目的是提供一種耐磨線切割鋼線的制作方法,以該方法制備的線切割鋼線,切割太陽能硅片時,能夠減小用量,同時增加出片量。本發(fā)明所述的耐磨線切割鋼線的制作方法是:a、把多根鋼線經(jīng)過加捻合股形成的捻合鋼線或者單根鋼線經(jīng)過漿料,使得漿料涂覆在捻合鋼線或者單根鋼線上;所述漿料由下述質(zhì)量份的組份組成:沸點(diǎn)大于100℃以上的溶劑20-80份,石墨烯9-80份,石墨烯合金5-31份,石墨烯或石墨烯合金微粒粒徑為0.1um-5um;b、把涂覆漿料的鋼線在真空下加熱烘干,去除溶劑;鋼線表面涂覆的石墨烯和石墨烯合金層的厚度為0.1um-5um;c、把去除溶劑后的鋼線采用磁控濺射方法進(jìn)行鍍銅;d、把鍍銅后的鋼線采用磁控濺射方法進(jìn)行鍍鎳。上述的耐磨線切割鋼線的制作方法,多根鋼線沿一定的螺旋角進(jìn)行加捻合股形成的捻合鋼線,螺旋角大于等于20度,小于等于75度。上述的耐磨線切割鋼線的制作方法,溶劑為二甲基乙酰胺,甲基呲咯烷酮或二者的混合液。上述的耐磨線切割鋼線的制作方法,石墨烯合金為鎳基石墨烯、銅基石墨烯、金剛石基石墨烯、鉬基石墨烯、碳化硅基石墨烯中任意一種或數(shù)種。上述的耐磨線切割鋼線的制作方法,鍍銅時,真空度小于2×10-1Pa,銅靶磁控濺射電流為15A。上述的耐磨線切割鋼線的制作方法,鍍鎳時,真空度4×10-3Pa以下,充入氬氣體作為濺射用氣體,使濺射工作氣壓在3x10-1Pa,鎳靶磁控濺射電流為20A。上述的耐磨線切割鋼線的制作方法,重復(fù)步驟a、b、c7-9次后,再進(jìn)行步驟d。本發(fā)明的有益效果:石墨烯目前是世上最薄也是最堅硬的納米材料,導(dǎo)熱系數(shù)是金剛石的3倍;單層石墨烯的比表面積是最好活性炭的1.75倍;具有超強(qiáng)的剛度和硬度,強(qiáng)度是鋼的100多倍。本發(fā)明的目的就是旨在將高耐磨性,高強(qiáng)度,高耐腐蝕性的石墨烯及石墨烯合金材料和鋼線復(fù)合加工成滿足線鋸切割使用的線材,用以提高硬脆貴重材料的切割效率,降低成本。它是解決現(xiàn)階段常規(guī)鋼線存在的不耐磨缺陷的一種途徑。選用單線線徑大于8um的鋼線,以單根或3根,5根,7根,9根及大于9根的單線經(jīng)復(fù)合加捻制成螺旋多股捻合鋼線(也稱結(jié)構(gòu)鋼線),并且在這種捻合鋼線或者單根鋼線表面進(jìn)行涂覆耐磨石墨烯層和石墨烯合金層,這種合金層可以是一層或多層組成。這種新型耐磨鋼線可制成太陽能硅片多線切割機(jī)用鋼線,可用于切割寶石、玻璃、硬質(zhì)合金、陶瓷、稀土磁性材料、石材、石英晶體等硬脆性材料。本發(fā)明同時提供了一種能耗低、效率高的制備耐磨線切割鋼線用真空涂覆鍍膜設(shè)備。本發(fā)明所述制備耐磨線切割鋼線用真空涂覆鍍膜設(shè)備,包括真空腔體7,設(shè)置于真空腔體7內(nèi)的放卷機(jī)構(gòu)1、漿料涂覆系統(tǒng)2、鋼線真空烘干裝置3、磁控濺射鍍膜系統(tǒng)4、磁控濺射鍍膜系統(tǒng)5、收卷機(jī)構(gòu)6;放卷機(jī)構(gòu)1放出的鋼線,從漿料涂覆系統(tǒng)2中的漿料穿過,再經(jīng)鋼線真空烘干裝置3,再先后經(jīng)過磁控濺射鍍膜系統(tǒng)4和磁控濺射鍍膜系統(tǒng)5,最后經(jīng)收卷機(jī)構(gòu)6收卷。把放卷機(jī)構(gòu)1、漿料涂覆系統(tǒng)2、鋼線真空烘干裝置3、磁控濺射鍍膜系統(tǒng)4、磁控濺射鍍膜系統(tǒng)5、收卷機(jī)構(gòu)6等一起放置真空腔體中,而不是把各個裝置分別置于各自的真空腔體中,節(jié)約了能耗。同時采用放卷機(jī)構(gòu)、收卷機(jī)構(gòu),能夠聯(lián)系高效作業(yè),效率高。上述的制備耐磨線切割鋼線用真空涂覆鍍膜設(shè)備,它還包括上下兩個鋼線多槽導(dǎo)輪,鋼線多槽導(dǎo)輪上開有多個線槽;鋼線依次繞過兩個鋼線多槽導(dǎo)輪上的線槽;下部的鋼線多槽導(dǎo)輪位于裝在漿料涂覆系統(tǒng)2的漿料槽21中的漿料液面下;漿料槽21的上方是真空烘干裝置3,真空烘干裝置3的上方是磁控濺射鍍膜系統(tǒng)4;依次繞過兩個鋼線多槽導(dǎo)輪上的線槽的鋼線穿過真空烘干裝置3和磁控濺射鍍膜系統(tǒng)4。由于鋼線在上下兩個鋼線多槽導(dǎo)輪之間多次繞過,以簡單的方式實(shí)現(xiàn)了鋼線的重復(fù)多次涂覆、加熱烘干和磁控濺射鍍膜。上述的制備耐磨線切割鋼線用真空涂覆鍍膜設(shè)備,它還包括位于磁控濺射鍍膜系統(tǒng)5兩側(cè)的兩個鋼線多槽導(dǎo)輪,鋼線多槽導(dǎo)輪上開有多個線槽;鋼線依次繞過兩個鋼線多槽導(dǎo)輪上的線槽;依次繞過兩個鋼線多槽導(dǎo)輪上的線槽的鋼線穿過磁控濺射鍍膜系統(tǒng)5。由于鋼線在兩個鋼線多槽導(dǎo)輪之間多次繞過,以簡單的方式實(shí)現(xiàn)了鋼線的重復(fù)多次磁控濺射鍍膜。上述的制備耐磨線切割鋼線用真空涂覆鍍膜設(shè)備,真空腔體7被隔板14成兩部分;放卷機(jī)構(gòu)1、鋼線真空烘干裝置3、磁控濺射鍍膜系統(tǒng)4位于隔板一側(cè)的真空腔體內(nèi);磁控濺射鍍膜系統(tǒng)5、收卷機(jī)構(gòu)6位于隔板另一側(cè)的真空腔體內(nèi)。上述的制備耐磨線切割鋼線用真空涂覆鍍膜設(shè)備,漿料涂覆系統(tǒng)2中的漿料槽21與真空腔體7合成一體。附圖說明圖1是七股捻合耐磨線切割鋼線的示意圖;,圖2是三股捻合耐磨線切割鋼線的示意圖;圖3是耐磨線切割鋼線的制作裝置示意圖;圖4是鋼線繞過鋼線多槽導(dǎo)輪9a、9b的示意圖。具體實(shí)施方式耐磨線切割鋼線的制作過程。一.多股結(jié)構(gòu)鋼線的制作工藝本發(fā)明采用的鋼線其線徑為8um至150um的高強(qiáng)度單線,經(jīng)多股加捻機(jī)按一定的捻度將多股鋼線合股成一種螺旋的切割用結(jié)構(gòu)鋼線,其中結(jié)構(gòu)鋼線由3根、5根、7根及大于9根的單線沿一定的螺旋角進(jìn)行加捻,其螺旋角可以從20度至75度之間選擇。當(dāng)然,本發(fā)明的耐磨線切割鋼線也可以是采用不加捻的單根鋼線。二.含固體石墨烯及石墨烯合金的多層鋼線表面涂覆工藝本發(fā)明采用的合金涂覆方式為石墨烯或石墨烯合金漿料以真空方式涂覆。將制備好的漿料涂覆于單根或多股復(fù)合鋼線表面,并進(jìn)行真空鍍膜將石墨烯或石墨烯合金等涂覆耐磨料固定在鋼線表面,并進(jìn)行多次重復(fù)涂覆和真空鍍膜,其層數(shù)可達(dá)到3至20層,使鋼線表面均勻涂覆多層含石墨烯或石墨烯合金的復(fù)合層,其涂層總厚度從0.1um至5um之間,從而得到了一種由石墨烯和石墨烯合金改性的單根或多股線結(jié)構(gòu)表面高耐磨層的切割線材。三.含固體石墨烯及石墨烯合金基料組成比主要利用真空鍍膜技術(shù)將石墨烯或石墨烯合金復(fù)合到切割鋼線表面為其提供一層或多層復(fù)合耐磨層,用于阻隔線切割過程中切割砂漿對切割鋼線的磨損。其中石墨烯合金采用銅基石墨烯、鎳基石墨烯、鉬基石墨烯、金剛石納米基石墨烯、碳化硅基石墨烯的一種或幾種,鋼線表面每一層石墨烯或石墨烯合金占用的表面積比例從10%-85%、涂覆漿料中固體石墨烯或石墨烯合金微粒使用比例從15%----85%、固體石墨烯或石墨烯合金微粒粒徑從0.1um----5um之間,其涂覆漿料載體選擇在真空環(huán)境下蒸發(fā)量小的溶劑,其中優(yōu)選用沸點(diǎn)大于100℃以上的溶劑:優(yōu)選二甲基乙酰胺(DMAC),甲基呲咯烷酮(NMP)或二者之間的溶劑混合液。下面通過配制石墨烯或石墨烯合金漿料具體闡述本發(fā)明的制作方法。實(shí)施例一1、漿料的組成(重量份):組成方案一方案二方案三方案四鎳基石墨烯5.5550銅基石墨烯25.5005石墨烯9105575DMAC溶劑600200NMP溶劑0852020注:漿料制作工藝相同,只配方組成不同2.結(jié)構(gòu)鋼線工藝將制備好的10um單根鋼線,使用7根鋼線復(fù)合加捻成多股復(fù)合螺旋結(jié)構(gòu)鋼線,螺旋角為60-65度之間,制成切割用結(jié)構(gòu)線材。多根鋼線捻合屬于現(xiàn)有技術(shù)。3.真空涂覆鍍膜制作工藝(參見圖3)真空涂覆鍍膜使用的設(shè)備如圖3,主要包括放卷機(jī)構(gòu)1、漿料涂覆系統(tǒng)2、鋼線真空烘干裝置3,經(jīng)磁控濺射鍍膜系統(tǒng)4、磁控濺射鍍膜系統(tǒng)5、收卷機(jī)構(gòu)6、真空腔體7、真空抽氣系統(tǒng)8、13、鋼線多槽導(dǎo)輪9a、9b、9c、9d、磁控濺射鍍膜系統(tǒng)4的磁控濺射電源10,磁控濺射鍍膜系統(tǒng)4的磁控濺射電源11、導(dǎo)向輥12、隔板14等。真空腔體7被隔板14成兩部分。放卷機(jī)構(gòu)1、鋼線多槽導(dǎo)輪9a、9b、鋼線真空烘干裝置3、磁控濺射鍍膜系統(tǒng)4位于隔板一側(cè)的真空腔體內(nèi)。磁控濺射鍍膜系統(tǒng)5、收卷機(jī)構(gòu)6、鋼線多槽導(dǎo)輪9c、9d位于隔板另一側(cè)的真空腔體內(nèi)。真空抽氣系統(tǒng)8、13分別對隔板兩側(cè)的真空腔體內(nèi)抽真空。參見圖4,放卷機(jī)構(gòu)1放出單根鋼線或捻合鋼線1a后,經(jīng)過導(dǎo)向輥12的導(dǎo)向后繞入鋼線多槽導(dǎo)輪9a中的一個線槽中9a1,從線槽9a1繞出的鋼線向上穿過鋼線真空烘干裝置3,經(jīng)磁控濺射鍍膜系統(tǒng)4再繞入鋼線多槽導(dǎo)輪9b中的一個線槽中9b1,從線槽9b1繞出的鋼線向下經(jīng)磁控濺射鍍膜系統(tǒng)4、穿過鋼線真空烘干裝置3,再繞入鋼線多槽導(dǎo)輪9a中的另一個線槽9a2。從線槽9a2繞出的鋼線向上穿過鋼線真空烘干裝置3,經(jīng)磁控濺射鍍膜系統(tǒng)4再繞入鋼線多槽導(dǎo)輪9b中的一個線槽中9b2,從線槽9b2繞出的鋼線向下經(jīng)磁控濺射鍍膜系統(tǒng)4、穿過鋼線真空烘干裝置3,再繞入鋼線多槽導(dǎo)輪9a中的另一個線槽9a3。如此循環(huán),鋼線在鋼線多槽導(dǎo)輪9a、9b之間多次繞過。鋼線多槽導(dǎo)輪9a位于裝在漿料涂覆系統(tǒng)2的漿料槽21中的漿料液面下。鋼線在繞經(jīng)鋼線多槽導(dǎo)輪9a時,實(shí)現(xiàn)了漿料的涂覆。為了簡化結(jié)構(gòu),漿料槽21與真空腔體7合成一體。鋼線真空烘干裝置3主要包括加熱器31。加熱器31設(shè)置在漿料槽21與磁控濺射鍍膜系統(tǒng)4之間的真空腔體7外壁上。最后從鋼線多槽導(dǎo)輪9b上的一個線槽中繞出的鋼線穿過隔板14后,再繞經(jīng)位于磁控濺射鍍膜系統(tǒng)5兩端的鋼線多槽導(dǎo)輪9c、9d,鋼線多槽導(dǎo)輪9c、9d的結(jié)構(gòu)與鋼線繞過鋼線多槽導(dǎo)輪9c、9d的結(jié)構(gòu)與前述的鋼線多槽導(dǎo)輪9a、9b類同,繞過鋼線多槽導(dǎo)輪9c、9d的鋼線反復(fù)穿過磁控濺射鍍膜系統(tǒng)5進(jìn)行鍍膜。最后從鋼線多槽導(dǎo)輪9b上的一個線槽中繞出的鋼線進(jìn)入收卷機(jī)構(gòu)6進(jìn)行收卷。以方案一的組份來說明漿料配制方案:將鎳基石墨烯5.5份、銅基石墨烯25.5份和9份石墨烯微粒,置于帶超聲循環(huán)的攪拌反應(yīng)罐中并加入60份DMAC溶劑,對此混合體進(jìn)行循環(huán)超聲和攪拌分散均勻成一定粘度的槳料.將此漿料放置到漿料供給系統(tǒng)2中,使?jié){料能均勻涂覆到鋼線表面。涂覆漿料后的鋼線進(jìn)入真空烘干區(qū)域去除溶劑,在多股鋼線表面形成石墨烯與石墨烯耐磨層。啟動真空抽氣系統(tǒng)13,工藝要求真空度小于2×10-1Pa,磁控濺射鍍膜系統(tǒng)4以銅靶為靶材,磁控濺射電流為15A條件下將銅沉積于3x10um多股鋼線1a表面。由于鋼線在鋼線多槽導(dǎo)輪9a、9b之間多次繞過,實(shí)現(xiàn)了鋼線重復(fù)多次涂覆、加熱烘干和鍍銅膜工藝。以確保獲得成分均勻的合金鍍膜層;其每層厚度控制在0.02um—0.05um之間,層數(shù)控制在7---9層之間。已鍍合金鍍膜層的鋼線再進(jìn)入磁控濺射系統(tǒng)5進(jìn)行鍍鎳層,加厚鍍膜提升耐磨特性。磁控濺射鍍膜系統(tǒng)5以鎳靶為靶材,要求真空抽氣系統(tǒng)8將真空度抽至4×10-3Pa以下,充入氬氣體作為濺射用氣體,使濺射工作氣壓在3x10-1Pa,磁控濺射電流20A條件下將鎳鍍于鋼線表面。最終鎳層厚度控制0.25um—0.5um之間。將實(shí)例一中不同組份的方案組成的漿料涂覆鋼線,按上述方法制備成7股結(jié)構(gòu)鋼線(耐磨線切割鋼線)。參見圖1,7股結(jié)構(gòu)鋼線16具有7根單根高強(qiáng)度鋼線17,其外表具有含石墨烯和石墨烯合金多層鍍膜耐磨層18。取線徑7x10um鋼線涂覆成耐磨層厚度5um時,可制得線徑為40um左右的切割鋼線,在不改變現(xiàn)有PV800切片機(jī)工藝下、鋼線每刀使用量減少45%--55%。每刀增加12%---13%的出片量。實(shí)施例二:1、漿料的組成(重量份):組成方案五方案六方案七金剛石基石墨烯2.51015銅基石墨烯25.500石墨烯101055DMAC溶劑628010NMP溶劑0010注:漿料制作工藝相同,只配方組成不同2.結(jié)構(gòu)鋼線工藝將制備好的10um單根鋼線,使用7根鋼線復(fù)合加捻成多股復(fù)合螺旋結(jié)構(gòu)鋼線,螺旋角為60---65度之間,制成切割用結(jié)構(gòu)線材。3.真空涂覆鍍膜制作工藝(參見圖3)采用的制備設(shè)備參見實(shí)施例一和圖3,不再贅述。以方案七的組份來說明漿料配制方案:將金剛石基石墨烯15份、銅基石墨烯0份和55份石墨烯微粒,置于帶超聲循環(huán)的攪拌反應(yīng)罐中并加入10份NMP溶劑、10份DMAC溶劑,對此混合體進(jìn)行循環(huán)超聲和攪拌分散均勻成一定粘度的槳料。將此漿料放置到漿料供給系統(tǒng)中,使?jié){料能均勻涂覆到鋼線表面。涂覆漿料后的鋼線進(jìn)入真空烘干區(qū)域去除NMP溶劑和DMAC溶劑,在多股鋼線表面形成石墨烯與石墨烯耐磨層。啟動真空抽氣系統(tǒng)13,工藝要求真空度小于2×10-1Pa,磁控濺射鍍膜系統(tǒng)4以銅靶為靶材,磁控濺射電流為15A條件下將銅沉積于3x10um多股鋼線1a表面。由于鋼線在鋼線多槽導(dǎo)輪9a、9b之間多次繞過,實(shí)現(xiàn)了鋼線重復(fù)多次涂覆、加熱烘干和鍍銅膜工藝,以確保獲得成分均勻的合金鍍膜層;其每層厚度控制在0.02um—0.05um之間,層數(shù)控制在7---9層之間。已鍍合金鍍膜層的鋼線再進(jìn)入磁控濺射系統(tǒng)5進(jìn)行鍍鎳層,加厚鍍膜提升耐磨特性。磁控濺射鍍膜系統(tǒng)5以鎳靶為靶材,要求真空抽氣系統(tǒng)8將真空度抽至4×10-3Pa以下,充入氬氣體作為濺射用氣體,使濺射工作氣壓在3x10-1Pa,鎳靶磁控濺射電流20A條件下將鎳鍍于鋼線表面,最終鎳層厚度控制在0.25um—0.5um之間。將實(shí)例二中不同組份的方案組成的漿料涂覆鋼線,按上述方法制備成7股結(jié)構(gòu)鋼線(耐磨線切割鋼線)。取線徑7x10um鋼線涂覆成耐磨層厚度5um時,可制得線徑為40um左右的太陽能硅片線切割用耐磨結(jié)構(gòu)鋼線,在不改變現(xiàn)有PV800切片機(jī)工藝下、鋼線每刀使用量減少70%--75%。每刀增加12%---13%的出片量。實(shí)施例三:1.漿料的組成(重量份)鉬基石墨烯4.5份銅基石墨烯25.5份石墨烯10份DMAC溶劑60份2.結(jié)構(gòu)鋼線工藝將制備好的10um單根鋼線,使用3根復(fù)合加捻成多股復(fù)合螺旋結(jié)構(gòu)鋼線,螺旋角為30-35度之間,制成切割用結(jié)構(gòu)線材。3.真空涂覆鍍膜制作工藝(參見圖3)采用的制備設(shè)備參見實(shí)施例一和圖3,不再贅述。將鉬基石墨烯4.5份、銅基石墨烯25.5份和10份石墨烯微粒,置于帶超聲循環(huán)的攪拌反應(yīng)罐中并加入60份DMAC溶劑,對此混合體進(jìn)行循環(huán)超聲和攪拌分散均勻成一定粘度的槳料。將此漿料放置到漿料供給系統(tǒng)中,使?jié){料能均勻涂覆到鋼線表面。涂覆漿料后的鋼線進(jìn)入真空烘干區(qū)域去除DMAC溶劑,在多股鋼線表面形成石墨烯與石墨烯耐磨層。啟動真空抽氣系統(tǒng)13,工藝要求真空度小于2×10-1Pa,磁控濺射鍍膜系統(tǒng)4以銅靶為靶材,磁控濺射電流為15A條件下將銅沉積于3x10um多股鋼線表面。由于鋼線在鋼線多槽導(dǎo)輪9a、9b之間多次繞過,實(shí)現(xiàn)了鋼線重復(fù)多次涂覆、加熱烘干和鍍銅膜工藝,以確保獲得成分均勻的合金鍍膜層;其每層厚度控制在0.02um—0.05um之間,層數(shù)控制在7---9層之間。已鍍合金鍍膜層的鋼線再進(jìn)入磁控濺射系統(tǒng)5進(jìn)行鍍鎳層,加厚鍍膜提升耐磨特性。磁控濺射鍍膜系統(tǒng)5以鎳靶為靶材,要求真空抽氣系統(tǒng)8將真空度抽至4×10-3Pa以下,充入氬氣體作為濺射用氣體,使濺射工作氣壓在3x10-1Pa,鎳靶磁控濺射電流20A條件下將鎳鍍于鋼線表面,最終鎳層厚度控制在0.25um—0.5um之間。按上述方法制備成3股結(jié)構(gòu)鋼線。參見圖2,3股結(jié)構(gòu)鋼線16具有3根單根高強(qiáng)度鋼線17,其外表具有含石墨烯和石墨烯合金多層鍍膜耐磨層18。取線徑3x10um鋼線涂覆成耐磨層厚度5um時,可制得線徑為22um太陽能硅片線切割用耐磨結(jié)構(gòu)鋼線,在不改變現(xiàn)有PV800切片機(jī)工藝下、鋼線每刀使用量減少50%-55%,每刀增加20%-22%的出片量。實(shí)施例四:1.漿料組份(重量份)碳化硅基石墨烯6.5份銅基石墨烯23.5份石墨烯10份NMP溶劑60份2.真空涂覆鍍膜制作工藝(參見圖3)采用的制備設(shè)備參見實(shí)施例一和圖3,不再贅述。將碳化硅基石墨烯6.5份、銅基石墨烯23.5份和10份石墨烯微粒,置于帶超聲循環(huán)的攪拌反應(yīng)罐中并加入60份NMP溶劑,對此混合體進(jìn)行循環(huán)超聲和攪拌分散均勻成一定粘度的槳料。將此漿料放置到漿料供給系統(tǒng)中,使?jié){料能均勻涂覆到不加捻的單根70um鋼線表面。涂覆漿料后的鋼線進(jìn)入真空烘干區(qū)域去除NMP溶劑,在單根70um的鋼線表面形成石墨烯與石墨烯耐磨層。啟動真空抽氣系統(tǒng)13,工藝要求真空度小于2×10-1Pa,磁控濺射鍍膜系統(tǒng)4以銅靶為靶材,磁控濺射電流為15A條件下將銅沉積于單根鋼線表面。由于鋼線在鋼線多槽導(dǎo)輪9a、9b之間多次繞過,實(shí)現(xiàn)了鋼線重復(fù)多次涂覆、加熱烘干和鍍銅膜工藝,以確保獲得成分均勻的合金鍍膜層;其每層厚度控制在0.02um—0.05um之間,層數(shù)控制在7---9層之間。已鍍合金鍍膜層的鋼線再進(jìn)入磁控濺射系統(tǒng)5進(jìn)行鍍鎳層,加厚鍍膜提升耐磨特性。磁控濺射鍍膜系統(tǒng)5以鎳靶為靶材,要求真空抽氣系統(tǒng)8將真空度抽至4×10-3Pa以下,充入氬氣體作為濺射用氣體,使濺射工作氣壓在3x10-1Pa,鎳靶磁控濺射電流20A條件下將鎳鍍于鋼線表面,最終鎳層厚度控制在0.25um—0.5um之間。按上述方法制備成單根結(jié)構(gòu)鋼線(耐磨線切割鋼線)。將實(shí)例四、含石墨烯和石墨烯合金的單根鋼線制成線徑可控的太陽能硅片線切割用耐磨結(jié)構(gòu)鋼線,取線徑70um鋼線涂覆成耐磨層厚度2um---3umm時,可制得線徑為75um---80um單根太陽能硅片線切割用耐磨鋼線,在不改變現(xiàn)有PV800切片機(jī)工藝下、鋼線每刀使用量減少70%--75%。本發(fā)明的鋼線表面用含石墨烯或石墨烯合金微粒真空鍍膜的多層結(jié)構(gòu)的太陽能硅片切割用單根或多股鋼線來取代常規(guī)用標(biāo)準(zhǔn)鋼線,耐磨性好,顯著提高了使用壽命,減少使用量,提高了出片率。以上所述的具體實(shí)施例,對本發(fā)明的目的、技術(shù)方案和有益效果進(jìn)行了進(jìn)一步詳細(xì)說明,所應(yīng)理解的是,以上所述僅為本發(fā)明的具體實(shí)施例而已,并不用于限制本發(fā)明,凡在本發(fā)明的精神和原則之內(nèi),所做的任何修改、等同替換、改進(jìn)等,均應(yīng)包含在本發(fā)明的保護(hù)范圍之內(nèi)。當(dāng)前第1頁1 2 3