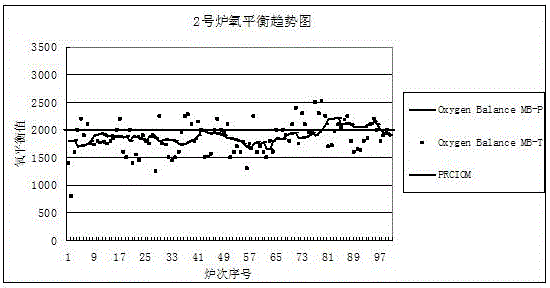
本發(fā)明涉及一種解決轉(zhuǎn)爐自動化煉鋼氧槍工作氧壓不穩(wěn)定的方法,特別是采用模擬量控制的方式解決轉(zhuǎn)爐自動化煉鋼吹煉工作氧壓不穩(wěn)定的問題,屬冶金自動化,屬于轉(zhuǎn)爐煉鋼自動化控制
技術(shù)領(lǐng)域:
。
背景技術(shù):
::轉(zhuǎn)爐煉鋼的目的是對兌入轉(zhuǎn)爐的鐵水和廢鋼等原料,通過氧槍連續(xù)吹氧的方式,不斷降低原料中的碳含量和提升溫度的過程。在轉(zhuǎn)爐出鋼前的冶煉終點,能否直接出鋼的判斷依據(jù),是鋼水碳含量和溫度能否滿足目標要求;因此,能準確判斷冶煉過程和終點鋼水碳含量是轉(zhuǎn)爐煉鋼的關(guān)鍵,冶煉終點命中率高的控制技術(shù)能減少補吹和倒?fàn)t取樣的次數(shù),可有效地縮短冶煉時間,提高轉(zhuǎn)爐產(chǎn)量,降低生產(chǎn)成本,是轉(zhuǎn)爐煉鋼的關(guān)鍵技術(shù)。例如:某廠轉(zhuǎn)爐氧槍供氧管道受場地空間限制,孔板流量計的布置不能滿足計量的準確性,總管氧壓的波動造成流量計量發(fā)生大的偏差,而且很不穩(wěn)定,供氧壓力受氧氣管網(wǎng)壓力波動影響,總管氧壓波動較大,波動范圍在1.3-2.5Mpa,每天均不同程度大范圍波動,給轉(zhuǎn)爐自動化煉鋼的順利進行造成極大影響?,F(xiàn)有的轉(zhuǎn)爐自動化煉鋼模型,大都采用達涅利自動化煉鋼模型,是按氧氣流量及累計氧氣消耗量及初始輸入物料參數(shù)、終點目標參數(shù)按照模型來進行自動計算,按計算結(jié)果對整個吹煉過程中加料量、吹氧量、加料時機、氧槍槍位變化時機、副槍動作時機、吹煉終點確定等過程進行自動控制,實現(xiàn)自動化煉鋼的目標;所以氧流量的計量穩(wěn)定及準確性是所有工作的基礎(chǔ)。不同轉(zhuǎn)爐,不同總管氧壓情況下,要達到相同的工作氧壓,需要的氧氣流量值均不相同,而當(dāng)設(shè)定同一流量值時,氧槍工作氧壓會發(fā)生大的波動,造成吹煉無法進行。因此,
背景技術(shù):
的轉(zhuǎn)爐自動化煉鋼模型難以適應(yīng)這樣的供氧條件,自動學(xué)習(xí)的結(jié)果常常偏離真實值,轉(zhuǎn)爐自動化煉鋼模型很難指導(dǎo)生產(chǎn)操作。技術(shù)實現(xiàn)要素:本發(fā)明的目的是提供一種解決轉(zhuǎn)爐自動化煉鋼氧槍工作氧壓不穩(wěn)定的方法,采用模擬計算量替代實際測量值參與自動化煉鋼模型控制,與自動化煉鋼系統(tǒng)實現(xiàn)無縫對接,改善自動化煉鋼效果,提高自動化煉鋼率;在供氧不穩(wěn)情況下轉(zhuǎn)爐自動化煉鋼率可實現(xiàn)100%,終點命中率可通過軟件原有的自學(xué)習(xí)功能不斷得到提高,解決
背景技術(shù):
存在的上述問題。本發(fā)明的技術(shù)方案是:一種解決轉(zhuǎn)爐自動化煉鋼氧槍工作氧壓不穩(wěn)定的方法,通過建立轉(zhuǎn)爐煉鋼工作氧壓與供氧流量關(guān)系的數(shù)學(xué)模型,根據(jù)實際工作氧壓計算供氧流量,并用該計算供氧流量替代儀表測量流量值,參與自動化煉鋼模型控制,實現(xiàn)自動化煉鋼過程的準確控制和穩(wěn)定操作。包括以下幾個步驟:①計算供氧流量模型的確定基于在供氧管路固定、氧槍參數(shù)已確定的情況下,氧槍的流量與噴頭參數(shù)及出口氧壓相關(guān)的原理,按照流體力學(xué)及氣體方程可推導(dǎo)出通過氧槍噴孔的氣體流量公式如下:F0:氧氣流量,m3/minP工作:工作氧壓,MpaT環(huán):氧氣環(huán)境溫度,℃Cd:氧槍噴孔流量系數(shù),通常取0.96-0.99N:氧槍噴孔個數(shù)A喉:氧槍噴孔喉口面積,mm2通過上述公式計算結(jié)果,確定計算供氧流量與工作氧壓的關(guān)系;驗證:通過物料平衡計算,與上述計算供氧流量的模擬計算值相比,驗證后基本符合實際,因此,用此計算供氧流量替代流量計測量值,參與自動化冶煉過程控制,能夠準確反應(yīng)實際氧氣消耗與入爐料條件及終點目標之間的關(guān)系;②模型實現(xiàn)采用氧槍工作氧壓及氧氣工作環(huán)境溫度按理想氣體方程及噴頭設(shè)計流量壓力特性計算供氧流量,用計算供氧流量替代孔板流量計流量,參與轉(zhuǎn)爐吹煉過程的流量控制,并把計算供氧流量應(yīng)用到已有的轉(zhuǎn)爐自動化煉鋼模型上,同時保留孔板流量計流量做為參考,不參與控制。把計算供氧流量應(yīng)用到已有的轉(zhuǎn)爐自動化煉鋼模型上,通過修改已有轉(zhuǎn)爐自動化煉鋼模型的程序?qū)崿F(xiàn)。依據(jù)氧壓與氧流量的關(guān)系,經(jīng)過嵌入程序進行計算,實時產(chǎn)生工作氧壓與供氧流量的對應(yīng)值,并將計算供氧流量顯示的操作界面上,與副槍自動化煉鋼氧流量控制模型無縫對接,為自動化煉鋼順利進行提供了保障。在轉(zhuǎn)爐自動化煉鋼模型中設(shè)定目標流量,通過自動化煉鋼程序來實時自動調(diào)整流量,實現(xiàn)對流量的控制,進而穩(wěn)定了供氧壓力,避開了總管氧壓大范圍波動對流量表測量值精確度的干擾;副槍系統(tǒng),通過在每爐吹煉前中期采用靜態(tài)模型進行過程控制,利用副槍TSC探頭在不終斷吹煉的情況下直接插入鋼水中進行定C、定溫并取樣分析,利用TSC測量結(jié)果和設(shè)定終點目標差值在后續(xù)的吹煉過程中采用動態(tài)控制模式,重新計算后續(xù)吹煉用氧量及輔料用量,自動控制吹煉終點,實現(xiàn)轉(zhuǎn)爐吹煉終點碳、溫度的自動命中。本發(fā)明采用吹煉過程氧氣模擬計算供氧流量直接替代儀表測量值,參與轉(zhuǎn)爐吹煉過程自動化控制,實時根據(jù)氧槍工作氧壓計算吹煉過程供氧流量,實現(xiàn)了穩(wěn)定吹煉過程供氧壓力的目的。本發(fā)明的主要創(chuàng)新特點有:(1)不需要增加儀表及穩(wěn)壓閥組或改造氧氣管道,而是通過模擬計算供氧流量替代測量值實現(xiàn)自動控制氧流量及工作氧壓,因此無需投入,不占空間;(2)計算時間響應(yīng)快速,可忽略不計;(3)計算供氧流量與實際流量值偏差小,能夠保證自動化煉鋼模型的正確運算;(4)能與現(xiàn)有的達涅利自動化煉鋼模型無縫對接,實現(xiàn)自動化煉鋼。本發(fā)明的實用性在于:(1)適用于國內(nèi)煉鋼轉(zhuǎn)爐供氧管路設(shè)計缺陷或供氧系統(tǒng)壓力波動大,同時配備轉(zhuǎn)爐副槍自動化煉鋼系統(tǒng)的所有煉鋼廠,采用本方法可快速解決問題,免去巨額改造投資及時間;(2)無額外設(shè)備維護費用,全部功能通過現(xiàn)有裝備實現(xiàn);(3)本方法軟件程序簡單,可自主開發(fā)和優(yōu)化。本發(fā)明適用于現(xiàn)有煉鋼廠煉鋼系統(tǒng)供氧氣條件不穩(wěn)定、自動化煉鋼不能正常進行且無改造空間或無資金改造的情況下使用。本發(fā)明積極效果:轉(zhuǎn)爐自動化煉鋼需要對吹煉過程氧氣流量及工作氧壓進行準確控制,并對數(shù)據(jù)進行收集、分析,以不斷通過軟件自學(xué)習(xí)功能自動調(diào)整模型參數(shù)適應(yīng)吹煉過程,達到準確控制轉(zhuǎn)爐煉鋼鋼水終點成份、溫度的目的。當(dāng)各種因素造成總管供氧壓力波動時,造成吹煉氧氣流量檢測的準確性受到較大的影響,從而影響到自動化煉鋼過程吹氧工作氧壓的巨大波動,被迫使自動化煉鋼不能進行而改用手動控制,自動化煉鋼模型無法應(yīng)用,大大影響轉(zhuǎn)爐煉鋼的命中率。本專利申請是不進行任何投資的情況下,采用模擬量參與自動化煉鋼的流量控制,使自動化煉鋼模型脫離總管氧壓波動對其的干擾,實現(xiàn)100%自動化煉鋼,模型不斷得到優(yōu)化完善,煉鋼終點命中率得到有效提高。附圖說明圖1為本發(fā)明實施例計算供氧流量與工作氧壓關(guān)系圖;圖2為本發(fā)明實施例修改達涅利自動化煉鋼模型程序說明示意圖;圖3為本發(fā)明實施例1號爐使用本發(fā)明后氧平衡值情況(100爐數(shù)據(jù));圖4為本發(fā)明實施例2號爐使用本發(fā)明后氧平衡值情況(100爐數(shù)據(jù))。具體實施方式以下結(jié)合附圖,通過實施例對本發(fā)明做進一步說明。一種解決轉(zhuǎn)爐自動化煉鋼氧槍工作氧壓不穩(wěn)定的方法,通過建立轉(zhuǎn)爐煉鋼工作氧壓與供氧流量關(guān)系的數(shù)學(xué)模型,根據(jù)實際工作氧壓計算供氧流量,并用該計算供氧流量替代儀表測量流量值,參與自動化煉鋼模型控制,實現(xiàn)自動化煉鋼過程的準確控制和穩(wěn)定操作。包括以下步驟:①計算供氧流量模型的確定基于在供氧管路固定、氧槍參數(shù)已確定的情況下,氧槍的流量與噴頭參數(shù)及出口氧壓相關(guān)的原理,按照流體力學(xué)及氣體方程可推導(dǎo)出通過氧槍噴孔的氣體流量公式如下:F0:氧氣流量,m3/minP工作:工作氧壓,MpaT環(huán):氧氣環(huán)境溫度,℃Cd:氧槍噴孔流量系數(shù),通常取0.96-0.99N:氧槍噴孔個數(shù)A喉:氧槍噴孔喉口面積,mm2通過上述公式計算結(jié)果,確定計算供氧流量與工作氧壓的關(guān)系;②模型實現(xiàn)采用氧槍工作氧壓及氧氣工作環(huán)境溫度按理想氣體方程及噴頭設(shè)計流量壓力特性計算供氧流量,用計算供氧流量替代孔板流量計流量,參與轉(zhuǎn)爐吹煉過程的流量控制,并把計算供氧流量應(yīng)用到已有的轉(zhuǎn)爐自動化煉鋼模型上,同時保留孔板流量計流量作為參考,不參與控制。把計算供氧流量應(yīng)用到已有的轉(zhuǎn)爐自動化煉鋼模型上,通過修改已有轉(zhuǎn)爐自動化煉鋼模型的程序?qū)崿F(xiàn)。依據(jù)氧壓與氧流量的關(guān)系,經(jīng)過嵌入程序進行計算,實時產(chǎn)生工作氧壓與供氧流量的對應(yīng)值,并將計算供氧流量顯示的操作界面上,與副槍自動化煉鋼氧流量控制模型無縫對接,為自動化煉鋼順利進行提供了保障。在轉(zhuǎn)爐自動化煉鋼模型中設(shè)定目標流量,通過自動化煉鋼程序來實時自動調(diào)整流量,實現(xiàn)對流量的控制,進而穩(wěn)定了供氧壓力,避開了總管氧壓大范圍波動對流量表測量值精確度的干擾;副槍系統(tǒng),通過在每爐吹煉前中期采用靜態(tài)模型進行過程控制,利用副槍TSC探頭在不終斷吹煉的情況下直接插入鋼水中進行定C、定溫并取樣分析,利用TSC測量結(jié)果和設(shè)定終點目標差值在后續(xù)的吹煉過程中采用動態(tài)控制模式,重新計算后續(xù)吹煉用氧量及輔料用量,自動控制吹煉終點,實現(xiàn)轉(zhuǎn)爐吹煉終點碳、溫度的自動命中。在實施例中,參照附圖1,確定計算供氧流量與工作氧壓的關(guān)系圖。實施例的計算模型驗證,參照表1、表2。表1:轉(zhuǎn)爐裝入物料情況表鐵水裝入量廢鋼裝入量鐵水比%廢鋼比%成鋼量比%噸鋼返礦加入比%135100.930.0680.9240.020表2:氧平衡計算表由以上物料平衡計算,與(1)項中流量模擬計算值相比,基本符合實際,驗證:通過物料平衡計算,與上述計算供氧流量的模擬計算值相比,驗證后基本符合實際,因此,用此計算供氧流量替代流量計測量值,參與自動化冶煉過程控制,能夠準確反應(yīng)實際氧氣消耗與入爐料條件及終點目標之間的關(guān)系;實施例中模型實現(xiàn):現(xiàn)經(jīng)過分析,采用氧槍工作氧壓及氧氣工作環(huán)境溫度按理想氣體方程及噴頭設(shè)計流量壓力特性計算氧槍流量,用此流量替代孔板流量計流量參與轉(zhuǎn)爐吹煉過程的流量控制,并把此參數(shù)應(yīng)用到達涅利自動化煉鋼模型L1及L2,同時保留原孔板流量計流量做為參考(不參與控制),具體修改要求如下:流量計算程序修改程序說明,參照附圖2.附圖2中:F計算:氧氣流量,m3/min;P:氧槍工作氧壓,Mpa;T1、T2:供氧管路支路末端截止閥狀態(tài)(1:表示閥關(guān)限位觸發(fā);0:表示閥關(guān)限位未觸發(fā));P1、P2:1號、2號氧槍工作氧壓,Mpa;T環(huán):氧氣工作環(huán)境溫度,℃。應(yīng)用范圍:本實施例對3座轉(zhuǎn)爐進行改造,3座轉(zhuǎn)爐L1東、西氧槍氧流量調(diào)節(jié)閥控制;3座轉(zhuǎn)爐副槍L1單爐實際氧耗累積量計量;3座轉(zhuǎn)爐副槍自動化煉鋼L2模型單爐氧耗累積量計量、氧流量計量;其它需更改的點(現(xiàn)場確定)。在沒有任何資金投入的情況下,成功解決了氧壓波動及氧量計量波動對轉(zhuǎn)爐自動化煉鋼供氧模型影響的問題,統(tǒng)一了3座轉(zhuǎn)爐供氧模型參數(shù),使轉(zhuǎn)爐供氧模型全面實現(xiàn)自動化。主要效果如下:(1)總氧耗的穩(wěn)定性根據(jù)投入應(yīng)用后300爐數(shù)據(jù)分析,單爐氧耗量波動在5900-6400m3/t(與鐵水成份、溫度、廢鋼量、是否留渣、返礦加入量等因素的影響具有較強的對應(yīng)性),噸鋼氧耗波動在49-52m3/t,與理論計算相符,也與實際轉(zhuǎn)爐冶煉工藝經(jīng)驗值相符。(2)、總管氧壓對工作氧壓及氧流量的影響使用該發(fā)明后三座轉(zhuǎn)爐過程控制參數(shù)如下,在總管氧壓波動時,氧流量及工作氧壓基本不受影響,轉(zhuǎn)爐自動化煉鋼模型實現(xiàn)了參數(shù)統(tǒng)一,100%支持自動化煉鋼,具體見表3。表3:典型供氧參數(shù)實際情況表120t轉(zhuǎn)爐1號爐煉鋼生產(chǎn),鐵水140t,廢鋼5t,吹煉過程總管氧壓波動在1.3~2.5MPa,調(diào)節(jié)閥后氧壓波動在1.3~1.5MPa,氧槍吹煉流量設(shè)定在400M3/min,吹煉工作氧壓穩(wěn)定在0.6MPa左右,氧平衡值設(shè)定為2000,模型單爐實際氧平衡值穩(wěn)定在2250±200,波動范圍1990~2500。1號爐使用本發(fā)明后氧平衡值情況(100爐數(shù)據(jù))參照附圖3。120t轉(zhuǎn)爐2號爐煉鋼生產(chǎn),鐵水140t,廢鋼5t,吹煉過程總管氧壓波動在1.3~2.5MPa,調(diào)節(jié)閥后氧壓波動在1.3~1.5MPa,氧槍吹煉流量設(shè)定在400M3/min,吹煉工作氧壓穩(wěn)定在0.6MPa左右,氧平衡值設(shè)定為2000,模型實際單爐氧平衡值穩(wěn)定在1850±200。2號爐使用本發(fā)明后氧平衡值情況(100爐數(shù)據(jù))參照附圖4。當(dāng)前第1頁1 2 3