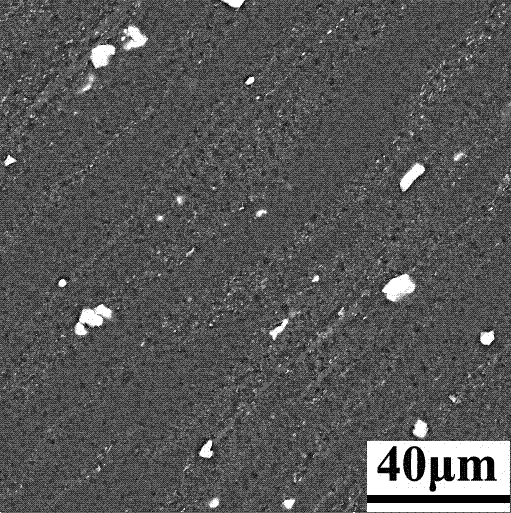
本發(fā)明屬于輕金屬材料
技術(shù)領(lǐng)域:
,涉及一種鎂合金,特別涉及一種Mg-Al-Sn-Sb鎂合金及其制備方法。
背景技術(shù):
:鎂合金作為質(zhì)輕減震的金屬結(jié)構(gòu)材料,具有比剛度高、抗震性好、比強(qiáng)度高、電磁屏蔽性能優(yōu)異、可回收性好等多種獨(dú)特的優(yōu)異性能,跟復(fù)合材料,涂層以及塑料材料相比,鎂可用于工程結(jié)構(gòu)材料,且鎂是綠色的工程材料,對(duì)環(huán)境友好。汽車所用燃料60%消耗于汽車自重,汽車質(zhì)量每降低100公斤,每百公里油耗可減少0.7升,因此,汽車輕量化成為汽車節(jié)能減排最主要的途徑,鎂合金在汽車、電子工業(yè)、航空航天等領(lǐng)域有廣闊的應(yīng)用前景。鎂在地殼和海水中的含量十分豐富,自本世紀(jì)初皮江法煉鎂技術(shù)在我國推廣應(yīng)用以來,原鎂產(chǎn)量迅速增長,但目前一半以上的原鎂仍主要用于鋁的合金元素、鋼鐵脫硫、金屬鈦還原等初級(jí)階段。用于鎂合金擠壓、板材、鑄件等深加工鎂合金產(chǎn)品的比例有待提高,因此,鎂合金的開發(fā)和應(yīng)用具有很大的發(fā)展?jié)摿ΑT趯?shí)際生產(chǎn)需求的推進(jìn)下,隨著汽車工業(yè)、通訊電子業(yè)等領(lǐng)域?qū)︽V合金需求的迅速增加,已開發(fā)出很多種類的鎂合金,如高強(qiáng)鎂合金、耐熱鎂合金和超輕鎂合金等。隨著科技的快速發(fā)展和生產(chǎn)測試技術(shù)的提高,現(xiàn)有的鎂合金材料在應(yīng)用方面面臨著各種新的挑戰(zhàn)。近些年,Mg-Al-Sn三元系由于具有較低的層錯(cuò)能而期望能成為一種性能優(yōu)良的新型鎂合金,因此成為鎂合金研究的熱點(diǎn)。同在2011年就有兩位學(xué)者進(jìn)行了這方面的研究,美國A.Luo對(duì)Mg-Al-Sn鑄態(tài)合金進(jìn)行了組織和機(jī)械性能研究(A.A.Luo,Fu,P.,Peng,L.,Kang,X.,Li,Z.andZhu,T.SolidificationMicrostructureandMechanicalPropertiesofCastMagnesium-Aluminum-TinAlloys[J].MetallurgicalandMaterialsTransactionsA,2011,43(1):360-368.),結(jié)果表明:室溫下,Mg-Al-Sn合金的屈服強(qiáng)度隨著合金(Al和Sn)含量的增加而增加,合金Mg-9Al-5Sn的屈服強(qiáng)度最高為127MPa;而極限抗拉強(qiáng)度隨合金含量的增加則變化不明顯,這與合金含量延展性的降低限度存在主要關(guān)系,其中,Mg-Al-Sn鑄態(tài)合金的室溫性能最好的是成分為Mg-5Al-1Sn的合金,抗拉強(qiáng)度為179MPa,而隨著合金含量的增加,Mg-9Al-5Sn合金的抗拉強(qiáng)度僅有149MPa。在同一年,吉林大學(xué)的劉俊嶺也對(duì)Mg-Al-Sn系鎂合金鑄態(tài)組織和力學(xué)性能進(jìn)行了研究(劉俊嶺.Al、Sn含量對(duì)Mg-Al-Sn系鎂合金鑄態(tài)組織和力學(xué)性能的影響[D],吉林大學(xué),2011年.),研究顯示:當(dāng)Al含量達(dá)到8wt%,Sn達(dá)到1~2wt%時(shí),合金具有極限抗拉強(qiáng)度280Mpa;當(dāng)Al達(dá)到6wt%,Sn達(dá)到2~3wt%時(shí),合金具有優(yōu)良的綜合力學(xué)性能,抗拉強(qiáng)度則為260Mpa。上述研究表明Mg-Al-Sn系鎂合金中合金元素的含量變化對(duì)合金應(yīng)變性能具有明顯的影響,然而隨著科技的快速發(fā)展,上述鎂合金的應(yīng)變性能已無法滿足目前更高的應(yīng)用需求。其中,耐熱就成為當(dāng)前鎂合金應(yīng)用的一個(gè)基本要求。耐熱鎂合金從最初的Mg-Al,發(fā)展到Mg-RE系,耐熱性能一定程度上得到較大提高,但稀土元素的成本高、資源日漸減少,迫使我們尋找更為合適的元素取代稀土元素。技術(shù)實(shí)現(xiàn)要素:有鑒于此,本發(fā)明所要解決的一個(gè)技術(shù)問題是提供一種Mg-Al-Sn-Sb鎂合金,提高鎂合金的變形性能。本發(fā)明所要解決的另一個(gè)技術(shù)問題是提供一種制備上述Mg-Al-Sn-Sb鎂合金的方法。為解決上述技術(shù)問題,本發(fā)明所采用的技術(shù)方案是:一種Mg-Al-Sn-Sb鎂合金,其質(zhì)量百分比組成為:Al:8.0-10.5%,Sn:2.0-5.5%,Sb:0-1.8%,其余為Mg和不可避免的雜質(zhì),不可避免的雜質(zhì)的總量小于0.05%。優(yōu)選地,所述Mg-Al-Sn-Sb鎂合金的質(zhì)量百分比組成為:Al:8.0-10.5%,Sn:2.0-5.5%,Sb:0.1-1.8%,其余為Mg和不可避免的雜質(zhì),不可避免的雜質(zhì)的總量小于0.05%。優(yōu)選地,所述Mg-Al-Sn-Sb鎂合金的質(zhì)量百分比組成為:Al:9.5-10.5%,Sn:4.5-5.0%,Sb:0.5-0.8%,其余為Mg和不可避免的雜質(zhì),不可避免的雜質(zhì)的總量小于0.05%。優(yōu)選地,所述Mg-Al-Sn-Sb鎂合金的質(zhì)量百分比組成為:Al:9.78%,Sn:4.81%,Sb:0.71%,其余為Mg和不可避免的雜質(zhì)。上述Mg-Al-Sn-Sb鎂合金的制備方法,包括如下步驟:步驟S1、合金熔煉:首先,按照所述Mg-Al-Sn-Sb鎂合金的質(zhì)量百分比組成,結(jié)合元素?zé)龘p率,計(jì)算合金元素配比,選擇稱取合金原料鎂錠、鋁錠、錫和銻;其次,將石墨坩堝放入真空感應(yīng)熔煉爐內(nèi),再將已裝入所述合金原料的不銹鋼坩堝放入所述石墨坩堝中,抽真空使所述真空感應(yīng)熔煉爐的真空度小于0.1Pa,通入惰性保護(hù)氣體,開始加熱至合金熔煉溫度,使合金原料充分熔化,得到合金熔液;最后,將裝有所述合金熔液的不銹鋼坩堝冷卻,擠壓,得到鑄錠車皮;步驟S2、均勻化處理:將所述鑄錠車皮去除頭部和底部兩端的鑄造缺陷,得到鑄錠樣品,然后進(jìn)行均勻化退火處理,以消除鑄態(tài)組織的成分偏析及枝晶偏析;步驟S3、熱擠壓:將所述均勻化處理后的鑄錠樣品和擠壓模具在300℃預(yù)熱,并在300℃溫度下保溫2小時(shí),然后在該溫度下進(jìn)行正向熱擠壓,得到鎂合金產(chǎn)品。優(yōu)選地,所述惰性保護(hù)氣體為氬氣。優(yōu)選地,所述合金熔煉溫度為690℃-750℃,保溫10分鐘。優(yōu)選地,所述冷卻是在裝有食鹽水的鐵桶中進(jìn)行冷卻。優(yōu)選地,所述均勻化退火處理是將所述鑄錠樣品以0.68℃/min的速度升溫至420℃,在420℃溫度下保溫12小時(shí)。優(yōu)選地,所述正向熱擠壓的擠壓比為25:1,擠壓速率為8~10.5mm/s。本發(fā)明與現(xiàn)有技術(shù)相比,其有益效果如下:1、本發(fā)明Mg-Al-Sn-Sb鎂合金中,Sb元素的加入使得合金的強(qiáng)化機(jī)制以及合金的性能得以改善,提高了鎂合金的強(qiáng)度;Sb元素與稀土元素和堿土元素相比,具有價(jià)格低、用量少、加入工藝簡單等優(yōu)點(diǎn),銻元素可以降低鎂合金的液相線,改善其流動(dòng)性,Sb元素在鎂中的溶解度極度低,Sb元素在Mg-Al系鎂合金中的存在方式主要是固溶于Mg17Al12相,Sb元素的強(qiáng)化作用主要是通過形成第二相顆粒Mg3Sb2高溫相來實(shí)現(xiàn)的,Mg3Sb2相與Mg17Al12相有著較為良好的界面共格關(guān)系,Mg3Sb2相可能是Mg17Al12相的形核襯底。同時(shí)Sb元素是有效的表面活性元素,分布在固體和液體界面上,減小了表面張力,能有效抑制晶粒長大,對(duì)鎂合金的鑄造性能、顯微組織及力學(xué)性能等有著重要影響,同時(shí)熱擠壓過程中,Sb元素可以阻礙再結(jié)晶晶粒長大從而有效細(xì)化擠壓態(tài)組織。Sn元素在鎂合金中除了可以細(xì)化合金的晶粒以外,同時(shí)形成熱穩(wěn)定性好、顯微硬度和熔點(diǎn)高的顆粒相Mg2Sn,該顆粒相對(duì)基體有著顯著的彌散強(qiáng)化作用,提高合金的室溫和高溫力學(xué)性能,提高合金在耐高溫抗蠕變性能方面的特有優(yōu)勢。2、本發(fā)明采用真空感應(yīng)熔煉爐進(jìn)行合金制備,并以惰性氣體氬氣作為保護(hù)氣體,降低了鎂合金的揮發(fā),合金熔液在電磁力的作用下產(chǎn)生的有規(guī)律的劇烈運(yùn)動(dòng)可使合金熔液的溫度更加均勻以及使熔煉合金的成分更加均勻。相比其他電阻爐鎂合金熔煉所采用的手動(dòng)攪拌成分均勻化的方法,感應(yīng)爐熔煉的合金成分更加均勻;同時(shí)感應(yīng)爐熔煉的電磁力的作用可以加快合金的熔煉速度,同時(shí)在電磁力的作用下克服自身靜壓力,可把合金溶液深處的溶液中的氣體排出,從而減少氣體夾雜的鑄造缺陷,因此可以得到成分更加均勻,鑄造缺陷更少的高質(zhì)量鑄錠。此外,采用食鹽水冷卻以及300℃的低溫?cái)D壓工藝,也對(duì)本發(fā)明合金優(yōu)良性能具有積極的影響。3、本發(fā)明鎂合金在擠壓態(tài)和時(shí)效態(tài)條件下可獲得高的強(qiáng)度和耐熱性能,不含貴重金屬元素,具有良好的擠壓性能和成型性能,能滿足工業(yè)化放大生產(chǎn)要求。本發(fā)明合金的制備工藝簡單,易操作;所采用的設(shè)備如真空感應(yīng)熔煉爐、熱擠壓機(jī)等均為現(xiàn)代化通用設(shè)備,具有可復(fù)制性強(qiáng)的特點(diǎn)。附圖說明圖1:本發(fā)明擠壓態(tài)Mg-10.19Al-5.1Sn合金的微觀組織掃描照片(不含Sb);圖2:本發(fā)明擠壓態(tài)Mg-10.19Al-4.99Sn-0.18Sb合金的微觀組織掃描圖;圖3:本發(fā)明擠壓態(tài)Mg-9.75Al-5.02Sn-0.52Sb合金的微觀組織掃描圖;圖4:本發(fā)明擠壓態(tài)Mg-9.78Al-4.81Sn-0.71Sb合金的微觀組織掃描圖;圖5:本發(fā)明擠壓態(tài)Mg-9.62Al-4.86Sn-0.85Sb合金的微觀組織掃描圖;圖6:本發(fā)明擠壓態(tài)Mg-10.19Al-4.99Sn-0.18Sb合金在室溫、150℃和200℃條件下的工程應(yīng)力-應(yīng)變曲線。具體實(shí)施方式為了更好地理解本發(fā)明,下面結(jié)合實(shí)施例進(jìn)一步清楚闡述本發(fā)明的內(nèi)容,但本發(fā)明的保護(hù)內(nèi)容不僅僅局限于下面的實(shí)施例。在下文的描述中,給出了大量具體的細(xì)節(jié)以便提供對(duì)本發(fā)明更為徹底的理解。然而,對(duì)于本領(lǐng)域技術(shù)人員來說顯而易見的是,本發(fā)明可以無需一個(gè)或多個(gè)這些細(xì)節(jié)而得以實(shí)施。本發(fā)明提供了一種Mg-Al-Sn-Sb鎂合金,其質(zhì)量百分比組成為:Al:8.0-10.5%,Sn:2.0-5.5%,Sb:0-1.8%,其余為Mg和不可避免的雜質(zhì),不可避免的雜質(zhì)的總量小于0.05%。其中,所述Al的質(zhì)量百分比含量優(yōu)選為9.0~10.5%,更優(yōu)選為9.5-10.5%,最優(yōu)選為9.78%;所述Sn的質(zhì)量百分比含量優(yōu)選為4.0~5.0%,更優(yōu)選為4.5~5.0%,最優(yōu)選為4.81%;所述Sb的質(zhì)量百分比含量優(yōu)選為0.1~1.8%,更優(yōu)選為0.5~0.8%,最優(yōu)選為0.71%;所述不可避免的雜質(zhì)的質(zhì)量百分含量小于0.05%,所述雜質(zhì)為本領(lǐng)域技術(shù)人員熟知的不可避免的雜質(zhì),通常包括Fe,Ni,Si等雜質(zhì)元素。本發(fā)明還提供了一種Mg-Al-Sn-Sb鎂合金的制備方法,包括如下步驟:步驟S1、合金熔煉:首先,按照所述Mg-Al-Sn-Sb鎂合金的質(zhì)量百分比組成,結(jié)合元素?zé)龘p率,計(jì)算合金元素配比,選擇稱取合金原料鎂錠、鋁錠、錫和銻;其次,將石墨坩堝放入真空感應(yīng)熔煉爐內(nèi),再將已裝入所述合金原料的不銹鋼坩堝放入所述石墨坩堝中,抽真空使所述真空感應(yīng)熔煉爐的真空度小于0.1Pa,通入惰性保護(hù)氣體,開始加熱至合金熔煉溫度,使合金原料充分熔化,得到合金熔液;最后,將裝有所述合金熔液的不銹鋼坩堝冷卻,擠壓,得到鑄錠車皮;步驟S2、均勻化處理:將所述鑄錠車皮去除頭部和底部兩端的鑄造缺陷,得到鑄錠樣品,然后進(jìn)行均勻化退火處理,以消除鑄態(tài)組織的成分偏析及枝晶偏析;步驟S3、熱擠壓:將所述均勻化處理后的鑄錠樣品和擠壓模具在300℃預(yù)熱,并在300℃溫度下保溫2小時(shí),然后在該溫度下進(jìn)行正向熱擠壓,得到鎂合金產(chǎn)品。在上述方法中,所述鎂錠優(yōu)選為鎂單質(zhì),鋁錠優(yōu)選為鋁單質(zhì),錫優(yōu)選為錫單質(zhì),銻優(yōu)選為銻單質(zhì)。在上述方法中,步驟S1中的所述惰性保護(hù)氣體優(yōu)選為氬氣;所述合金熔煉溫度優(yōu)選為690℃-750℃,保溫10分鐘;所述冷卻優(yōu)選在裝有食鹽水的鐵桶中進(jìn)行冷卻。在上述方法中,步驟S2中的所述均勻化退火處理優(yōu)選將所述鑄錠樣品以0.68℃/min的速度升溫至420℃,在420℃溫度下保溫12小時(shí)。在上述方法中,步驟S3中的所述正向熱擠壓優(yōu)選為擠壓比為25:1,擠壓速率為8~10.5mm/s。實(shí)施例1一種Mg-Al-Sn-Sb鎂合金,其質(zhì)量百分比組成為:Al:10.19%;Sn:5.1%;Sb:0%;其余為Mg和不可避免的雜質(zhì),其不可避免的雜質(zhì)總量小于0.05%。本實(shí)施例Mg-Al-Sn-Sb鎂合金按下述制備方法獲得:步驟S1、合金熔煉:首先,按照所述Mg-Al-Sn-Sb鎂合金的質(zhì)量百分比組成,結(jié)合元素?zé)龘p率,計(jì)算合金元素配比,分別稱取合金原料鎂錠、鋁錠和錫;然后,將石墨坩堝放入真空感應(yīng)熔煉爐內(nèi),再將已裝入所述合金原料的不銹鋼坩堝放入所述石墨坩堝中,抽真空使所述真空感應(yīng)熔煉爐的真空度小于0.1Pa,通入惰性保護(hù)氣體氬氣,開始加熱至合金熔煉溫度,所述合金熔煉溫度為690℃,保溫10分鐘,使合金原料充分熔化,得到合金熔液;最后,將裝有所述合金熔液的不銹鋼坩堝放入裝有食鹽水的鐵桶里冷卻,擠壓,得到鑄錠車皮;步驟S2、均勻化處理:將所述鑄錠車皮去除頭部和底部兩端的鑄造缺陷,得到鑄錠樣品,然后進(jìn)行均勻化退火處理,以消除鑄態(tài)組織的成分偏析及枝晶偏析,所述均勻化退火處理是將所述鑄錠樣品以0.68℃/min的速度升溫至420℃,在420℃溫度下保溫12小時(shí);步驟S3、熱擠壓:將所述均勻化處理后的鑄錠樣品和擠壓模具在300℃預(yù)熱,并在300℃溫度下保溫2小時(shí),然后在該溫度下進(jìn)行正向熱擠壓,所述正向熱擠壓的擠壓比為25:1,擠壓速率為9.41mm/s,得到鎂合金產(chǎn)品。經(jīng)拉伸力學(xué)性能測試實(shí)驗(yàn)檢測,本實(shí)施例所得鎂合金在室溫條件下的抗拉強(qiáng)度和屈服強(qiáng)度分別可以達(dá)到339MPa和249MPa。實(shí)施例2一種Mg-Al-Sn-Sb鎂合金,其質(zhì)量百分比組成為:Al:10.19%;Sn:4.99%;Sb:0.18%;其余為Mg和不可避免的雜質(zhì),其不可避免的雜質(zhì)總量小于0.05%。本實(shí)施例Mg-Al-Sn-Sb鎂合金按下述制備方法獲得:步驟S1、合金熔煉:首先,按照所述Mg-Al-Sn-Sb鎂合金的質(zhì)量百分比組成,結(jié)合元素?zé)龘p率,計(jì)算合金元素配比,分別稱取合金原料鎂錠、鋁錠、錫和銻;其次,將石墨坩堝放入真空感應(yīng)熔煉爐內(nèi),再將已裝入所述合金原料的不銹鋼坩堝放入所述石墨坩堝中,抽真空使所述真空感應(yīng)熔煉爐的真空度小于0.1Pa,通入惰性保護(hù)氣體氬氣,開始加熱至合金熔煉溫度,所述合金熔煉溫度為750℃,保溫10分鐘,使合金原料充分熔化,得到合金熔液;最后,將裝有所述合金熔液的不銹鋼坩堝放入裝有食鹽水的鐵桶里冷卻,擠壓,得到鑄錠車皮;步驟S2、均勻化處理:將所述鑄錠車皮去除頭部和底部兩端的鑄造缺陷,得到鑄錠樣品,然后進(jìn)行均勻化退火處理,以消除鑄態(tài)組織的成分偏析及枝晶偏析,所述均勻化退火處理是將所述鑄錠樣品以0.68℃/min的速度升溫至420℃,在420℃溫度下保溫12小時(shí);步驟S3、熱擠壓:將所述均勻化處理后的鑄錠樣品和擠壓模具在300℃預(yù)熱,并在300℃溫度下保溫2小時(shí),然后在該溫度下進(jìn)行正向熱擠壓,所述正向熱擠壓的擠壓比為25:1,擠壓速率為8.06mm/s,得到鎂合金產(chǎn)品。經(jīng)拉伸力學(xué)性能測試實(shí)驗(yàn)檢測,本實(shí)施例所得鎂合金在室溫條件下的抗拉強(qiáng)度和屈服強(qiáng)度分別可以達(dá)到353MPa和241MPa。實(shí)施例3一種Mg-Al-Sn-Sb鎂合金,其質(zhì)量百分比組成為:Al:9.75%;Sn:5.02%;Sb:0.52%;其余為Mg和不可避免的雜質(zhì),其不可避免的雜質(zhì)總量小于0.05%。本實(shí)施例Mg-Al-Sn-Sb鎂合金按下述制備方法獲得:步驟S1、合金熔煉:首先,按照所述Mg-Al-Sn-Sb鎂合金的質(zhì)量百分比組成,結(jié)合元素?zé)龘p率,計(jì)算合金元素配比,分別稱取合金原料鎂錠、鋁錠、錫和銻;其次,將石墨坩堝放入真空感應(yīng)熔煉爐內(nèi),再將已裝入所述合金原料的不銹鋼坩堝放入所述石墨坩堝中,抽真空使所述真空感應(yīng)熔煉爐的真空度小于0.1Pa,通入惰性保護(hù)氣體氬氣,開始加熱至合金熔煉溫度,所述合金熔煉溫度為720℃,保溫10分鐘,使合金原料充分熔化,得到合金熔液;最后,將裝有所述合金熔液的不銹鋼坩堝放入裝有食鹽水的鐵桶里冷卻,擠壓,得到鑄錠車皮;步驟S2、均勻化處理:將所述鑄錠車皮去除頭部和底部兩端的鑄造缺陷,得到鑄錠樣品,然后進(jìn)行均勻化退火處理,以消除鑄態(tài)組織的成分偏析及枝晶偏析,所述均勻化退火處理是將所述鑄錠樣品以0.68℃/min的速度升溫至420℃,在420℃溫度下保溫12小時(shí);步驟S3、熱擠壓:將所述均勻化處理后的鑄錠樣品和擠壓模具在300℃預(yù)熱,并在300℃溫度下保溫2小時(shí),然后在該溫度下進(jìn)行正向熱擠壓,所述正向熱擠壓的擠壓比為25:1,擠壓速率為10.00mm/s,得到鎂合金產(chǎn)品。經(jīng)拉伸力學(xué)性能測試實(shí)驗(yàn)檢測,本實(shí)施例所得鎂合金在室溫條件下的抗拉強(qiáng)度和屈服強(qiáng)度分別可以達(dá)到357MPa和230MPa。實(shí)施例4一種Mg-Al-Sn-Sb鎂合金,其質(zhì)量百分比組成為:Al:9.78%;Sn:4.81%;Sb:0.71%;其余為Mg和不可避免的雜質(zhì),其不可避免的雜質(zhì)總量小于0.05%。本實(shí)施例Mg-Al-Sn-Sb鎂合金的制備方法參閱實(shí)施例3,與實(shí)施例3所不同的是:步驟S3中擠壓速率為9.71mm/s。經(jīng)拉伸力學(xué)性能測試實(shí)驗(yàn)檢測,本實(shí)施例所得鎂合金在室溫條件下的抗拉強(qiáng)度和屈服強(qiáng)度分別可以達(dá)到378MPa和262MPa。實(shí)施例5一種Mg-Al-Sn-Sb鎂合金,其質(zhì)量百分比組成為:Al:9.62%;Sn:4.86%;Sb:0.85%;其余為Mg和不可避免的雜質(zhì),其不可避免的雜質(zhì)總量小于0.05%。本實(shí)施例Mg-Al-Sn-Sb鎂合金的制備方法參閱實(shí)施例3,與實(shí)施例3所不同的是:步驟S3中擠壓速率為10.52mm/s。經(jīng)拉伸力學(xué)性能測試實(shí)驗(yàn)檢測,本實(shí)施例所得鎂合金在室溫條件下的抗拉強(qiáng)度和屈服強(qiáng)度分別可以達(dá)到355MPa和239MPa。實(shí)施例6一種Mg-Al-Sn-Sb鎂合金,其質(zhì)量百分比組成為:Al:9.05%;Sn:3.10%;Sb:0.00%;其余為Mg和不可避免的雜質(zhì),其不可避免的雜質(zhì)總量小于0.05%。本實(shí)施例Mg-Al-Sn-Sb鎂合金的制備方法參閱實(shí)施例3,與實(shí)施例3所不同的是:步驟S3中擠壓速率為9.37mm/s。經(jīng)拉伸力學(xué)性能測試實(shí)驗(yàn)檢測,本實(shí)施例所得鎂合金在室溫條件下的抗拉強(qiáng)度和屈服強(qiáng)度分別可以達(dá)到348MPa和243MPa。實(shí)施例7一種Mg-Al-Sn-Sb鎂合金,其質(zhì)量百分比組成為:Al:8.92%;Sn:4.95%;Sb:1.78%;其余為Mg和不可避免的雜質(zhì),其不可避免的雜質(zhì)總量小于0.05%。本實(shí)施例Mg-Al-Sn-Sb鎂合金的制備方法參閱實(shí)施例3,與實(shí)施例3所不同的是:步驟S3中擠壓速率為9.76mm/s。經(jīng)拉伸力學(xué)性能測試實(shí)驗(yàn)檢測,本實(shí)施例所得鎂合金在室溫條件下的抗拉強(qiáng)度和屈服強(qiáng)度分別可以達(dá)到322MPa和218Mpa。實(shí)施例8一種Mg-Al-Sn-Sb鎂合金,其質(zhì)量百分比組成為:Al:9.12%;Sn:2.05%;Sb:0.72%;其余為Mg和不可避免的雜質(zhì),其不可避免的雜質(zhì)總量小于0.05%。本實(shí)施例Mg-Al-Sn-Sb鎂合金的制備方法參閱實(shí)施例3,與實(shí)施例3所不同的是:步驟S3中擠壓速率為10.31mm/s。經(jīng)拉伸力學(xué)性能測試實(shí)驗(yàn)檢測,本實(shí)施例所得鎂合金在室溫條件下的抗拉強(qiáng)度和屈服強(qiáng)度分別可以達(dá)到343MPa和240MPa。實(shí)施例9一種Mg-Al-Sn-Sb鎂合金,其質(zhì)量百分比組成為:Al:8.03%;Sn:3.98%;Sb:1.55%;其余為Mg和不可避免的雜質(zhì),其不可避免的雜質(zhì)總量小于0.05%。本實(shí)施例Mg-Al-Sn-Sb鎂合金的制備方法參閱實(shí)施例3,與實(shí)施例3所不同的是:步驟S3中擠壓速率為10.02mm/s。經(jīng)拉伸力學(xué)性能測試實(shí)驗(yàn)檢測,本實(shí)施例所得鎂合金在室溫條件下的抗拉強(qiáng)度和屈服強(qiáng)度分別可以達(dá)到341MPa和225MPa。對(duì)比例1一種Mg-Al-Sn-Sb鎂合金,其質(zhì)量百分比組成與實(shí)施例1相同,所不同的是:該實(shí)施例Mg-Al-Sn-Sb鎂合金按下述制備方法獲得:步驟S1、鎂合金的熔煉及鑄造:設(shè)定坩堝溫度為720℃~730℃,開始加熱;當(dāng)坩堝內(nèi)的溫度達(dá)到300℃~320℃時(shí)加入鎂錠;并通入體積比例為10:1的CO2和SF6的保護(hù)氣;鎂錠完全熔化后,依次加入經(jīng)過預(yù)熱的鋁錠和錫,5分鐘后加攪拌器,攪拌鎂合金溶液8~10分鐘;掏出鎂合金溶液的表面浮渣,并將鎂合金溶液澆鑄到鐵模具中得到鎂合金的鑄錠;步驟S2、均勻化處理:將鑄錠在馬弗爐中以300℃的溫度保溫18小時(shí),然后升溫到400℃保溫10小時(shí),最后在70℃溫水中進(jìn)行淬火;步驟S3、擠壓:將均勻化處理后的鑄錠,車削成直徑為80mm的圓錠,在390℃的環(huán)境中預(yù)熱1小時(shí),在擠壓溫度為400℃,擠壓比為25:1,擠壓速度為16mm/s~20mm/s的條件下制備出鎂合金棒材。經(jīng)拉伸力學(xué)性能測試實(shí)驗(yàn)檢測,本實(shí)施例鎂合金的抗拉強(qiáng)度為285MPa,屈服強(qiáng)度為204MPa。與本發(fā)明實(shí)施例1所得合金相比,力學(xué)性能有顯著的下降,說明本發(fā)明制備方法制備鎂合金更有利于提高其力學(xué)性能。對(duì)比例2一種Mg-Al-Sn-Sb鎂合金,其質(zhì)量百分比組成為:Al:9.78%;Sn:5.92%;Sb:0.71%;其余為Mg和不可避免的雜質(zhì),其不可避免的雜質(zhì)總量小于0.05%。本實(shí)施例Mg-Al-Sn-Sb鎂合金的制備方法同實(shí)施例4。經(jīng)拉伸力學(xué)性能測試實(shí)驗(yàn)檢測,本實(shí)施例所得鎂合金在室溫條件下的抗拉強(qiáng)度和屈服強(qiáng)度分別可以達(dá)到304MPa和213MPa。與本發(fā)明實(shí)施例4相比,當(dāng)合金中Sn的質(zhì)量百分比含量提高至5.92%,其力學(xué)性能并沒有提高,反而有明顯的下降,也說明在本發(fā)明所限定的合金組成范圍內(nèi),合金組配的協(xié)同性更好,更有利于合金力學(xué)性能的發(fā)揮。本發(fā)明上述實(shí)施例1~9及對(duì)比例1~2所得合金的拉伸力學(xué)性能測試均是在室溫25℃下,采用新三思CMT-5105微機(jī)控制電子萬能試驗(yàn)機(jī),拉伸試樣標(biāo)準(zhǔn)件按照國標(biāo)GB/T228-2002制備,拉伸試樣標(biāo)距為50mm,標(biāo)距內(nèi)直徑為5mm,試驗(yàn)采用勻速單向位移拉伸,拉伸速率為3mm/s。此外,本發(fā)明還抽取實(shí)施例1、2、4和5所得合金樣品,分別在150℃和200℃下進(jìn)行拉伸力學(xué)性能測試實(shí)驗(yàn),試驗(yàn)方法同上。拉伸性能數(shù)據(jù)見表1所示。表1擠壓態(tài)合金的抗拉強(qiáng)度和屈服強(qiáng)度結(jié)果鎂合金抗拉強(qiáng)度/屈服強(qiáng)度/Mpa,室溫25℃抗拉強(qiáng)度/屈服強(qiáng)度/Mpa,150℃抗拉強(qiáng)度/屈服強(qiáng)度/Mpa,200℃實(shí)施例1Mg-10.19Al-5.1Sn339/249321/238236/201實(shí)施例2Mg-10.19Al-4.99Sn-0.18Sb353/241285/237186/169實(shí)施例4Mg-9.78Al-4.81Sn-0.71Sb378/262265/228175/158實(shí)施例5Mg-9.62Al-4.86Sn-0.85Sb355/250253/215168/152由表1可見,實(shí)施例1、2、4和5所得鎂合金的抗拉強(qiáng)度隨Sb含量的增加呈現(xiàn)先增加后降低的趨勢。特別是Mg-9.78Al-4.81Sn-0.71Sb合金在擠壓態(tài)的抗拉強(qiáng)度為378MPa,屈服強(qiáng)度為262MPa,較Mg-10.19Al-5.1Sn合金的抗拉強(qiáng)度提高明顯;并且其經(jīng)過100℃/24小時(shí)+180℃/10小時(shí)的時(shí)效處理后抗拉強(qiáng)度可增加至389MPa,屈服強(qiáng)度可增加至293MPa。鎂合金材料在使用過程中要承受高溫,這就對(duì)鎂合金的耐熱性能提出了很高的要求?,F(xiàn)在耐熱鎂合金的應(yīng)用對(duì)象主要是轎車的發(fā)動(dòng)機(jī)和傳動(dòng)機(jī)構(gòu)零部件,如變速箱殼體、排氣管等,要求鎂合金材料工作溫度≥120℃,應(yīng)力為35-70Mpa的應(yīng)用條件(閆蘊(yùn)琪,張廷杰等,耐熱鎂合金的研究現(xiàn)狀與發(fā)展方向[J].稀有金屬材料與工程,2004,33(6):561-565.)。表1還顯示了本發(fā)明實(shí)施例1、2、4和5所得鎂合金,分別進(jìn)行150℃和200℃的高溫拉伸試驗(yàn)所得的性能數(shù)據(jù),結(jié)果發(fā)現(xiàn):150℃拉伸,實(shí)施例1、2、4和5所得鎂合金的抗拉強(qiáng)度較室溫25℃拉伸分別降低了18Mpa、68Mpa、108Mpa和102Mpa,200℃拉伸,實(shí)施例1、2、4和5所得鎂合金的抗拉強(qiáng)度較室溫拉伸分別降低了103Mpa、167Mpa、198Mpa和187Mpa。以報(bào)道的ZMT614-0.5Y和ZMT614-0.1Y合金為例,兩者在室溫下的抗拉強(qiáng)度分別為368MPa和360MPa,在150℃拉伸時(shí)抗拉強(qiáng)度分別降低了129MPa和146MPa;而在200℃拉伸,兩者的抗拉強(qiáng)度分別降低了189Mpa和207MPa(胡光山.Y和Nd對(duì)Mg-Zn-Mn-Sn系變形鎂合金組織和性能的影響[D],重慶大學(xué),2015.)。與上述鎂合金的高溫拉伸性能相比,本發(fā)明合金在150℃和200℃下的抗拉強(qiáng)度下降趨勢明顯較慢。參閱圖6,本發(fā)明實(shí)施例2所得Mg-10.19Al-4.99Sn-0.18Sb合金分別在室溫25℃、150℃和200℃下的應(yīng)力-應(yīng)變曲線,結(jié)果顯示:隨著溫度的升高,抗拉強(qiáng)度下降;150℃和200℃的拉伸強(qiáng)度下降的速率隨著拉伸溫度的升高而變慢;在150℃拉伸,應(yīng)力值達(dá)到峰值很快出現(xiàn)下降,而拉伸溫度為200℃時(shí),應(yīng)力值達(dá)到峰值后出現(xiàn)小幅度下降,未出現(xiàn)明顯的穩(wěn)態(tài)階段。綜合上述分析可知,本發(fā)明鎂合金添加Sb元素后室溫下的抗拉強(qiáng)度和屈服強(qiáng)度得到明顯提高;而且本發(fā)明鎂合金在高溫150℃和200℃下的抗拉強(qiáng)度較現(xiàn)有鎂合金的下降趨勢減緩,高溫條件下的力學(xué)性能得以提高。因此,本發(fā)明Mg-Al-Sn-Sb鎂合金具有更加優(yōu)良的高溫形變性能。參閱圖1-5,本發(fā)明擠壓態(tài)合金的微觀組織掃描圖顯示,經(jīng)過擠壓變形之后,合金發(fā)生了不同程度的動(dòng)態(tài)再結(jié)晶,出現(xiàn)少量粗大晶粒和細(xì)小動(dòng)態(tài)再結(jié)晶晶粒的混晶組織,同時(shí)合金中未溶的第二相破碎成顆粒狀,沿著擠壓方向分布。添加Sb元素后,組織更加均勻,晶粒得到明顯細(xì)化,最終使Mg-Al-Sn-Sb鎂合金的力學(xué)性能得到明顯的增加。通過上述實(shí)施例可知:本發(fā)明的Mg-Al-Sn-Sb鎂合金具有高強(qiáng)耐熱性能,形變性能優(yōu)異,這充分挖掘了鎂合金材料的使用潛力,拓展了高強(qiáng)耐熱性能鎂合金成分范圍,擴(kuò)大了其應(yīng)用范圍。而且,本發(fā)明制備工藝所用設(shè)備為常規(guī)通用設(shè)備,工藝簡單,可復(fù)制性強(qiáng),易于操作。雖然以上描述了本發(fā)明的具體實(shí)施方式,但是熟悉本
技術(shù)領(lǐng)域:
的技術(shù)人員應(yīng)當(dāng)理解,我們所描述的具體的實(shí)施例只是說明性的,而不是用于對(duì)本發(fā)明的范圍的限定,熟悉本領(lǐng)域的技術(shù)人員在依照本發(fā)明的精神所作的等效的修飾以及變化,都應(yīng)當(dāng)涵蓋在本發(fā)明的權(quán)利要求所保護(hù)的范圍內(nèi)。當(dāng)前第1頁1 2 3