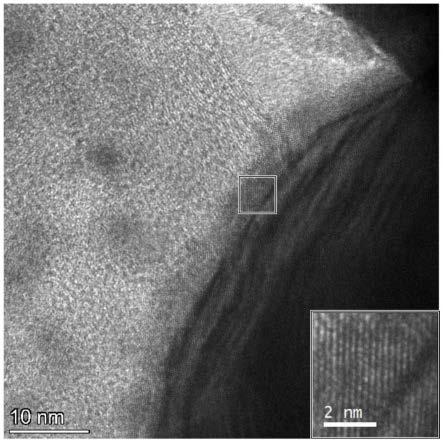
1.本發(fā)明涉及半導體封裝材料技術領域,尤其涉及一種高性能復合材料及其制備方法和應用。
背景技術:2.石墨烯有著超高的面內(nèi)導熱率、超高的電子遷移率、更寬的比表面積、優(yōu)異的力學性能、負的熱膨脹系數(shù)等一系列優(yōu)秀特性,將其優(yōu)化后應用于半導體領域的封裝材料中能顯著提高導熱、導電、機械性、可靠性等性能。
3.隨著半導體器件材料的發(fā)展,第一代半導體材料——硅的物理性能的應用已接近極限。而以氮化鎵(gan)和碳化硅(sic)為代表的第三代半導體材料,因其具有高頻率、高功率、高電壓、高工作溫度等更為優(yōu)越的性能而被發(fā)掘并應用。與第一、二代半導體相比,第三代半導體材料更適合應用于當前的5g通信、智能電網(wǎng)、高速軌道交通、新能源汽車、消費電子、航空航天等領域,但高的功率密度和高工作溫度使得熱管理成為封裝的關鍵所在。
4.目前傳統(tǒng)的封裝材料已經(jīng)難以滿足第三代半導體低溫封裝高溫服役的需求。為了發(fā)揮第三代半導體材料高溫工作的性能優(yōu)勢,同時確保器件系統(tǒng)高性能、高可靠性,研究人員必須研發(fā)能滿足第三代半導體高溫工作的高導熱固晶材料。
5.當前工業(yè)生產(chǎn)使用的封裝材料主要有微米銅和納米銅,微米銅在進行低溫封裝燒結(jié)時存在孔隙率大造成封裝結(jié)構(gòu)界面熱阻大、性能低的問題;而納米銅則存在易氧化難以控制燒結(jié)后的性能,以及材料成本高的難題。因此需進一步優(yōu)化固晶材料的低溫燒結(jié)性能,提升經(jīng)濟效益。
技術實現(xiàn)要素:6.本發(fā)明所要解決的技術問題是如何低成本提供一種滿足半導體封裝互連、散熱應用的高性能復合材料。
7.為了解決上述問題,本發(fā)明提出以下技術方案:
8.一種高性能復合材料的制備方法,包括以下步驟:
9.s1、對石墨烯材料進行表面處理,所述石墨烯材料包括石墨烯或其衍生物;
10.s2、將納米金屬顆粒加入ctab溶液中進行表面處理,再經(jīng)過超聲分散得到懸浮液;
11.s3、將s1處理得到的石墨烯材料加入所述懸浮液中,超聲分散,充分攪拌反應,將反應產(chǎn)物洗滌干燥后得到填充顆粒;
12.s4、對大粒徑金屬顆粒進行表面處理;
13.s5、將填充顆粒與s4處理得到的大粒徑金屬顆?;旌虾蠹尤胫鷦┻M行燒結(jié),得到高致密、高導熱的復合材料;
14.所述填充顆粒與大粒徑金屬顆粒的粒徑比為0.1-0.5。
15.作為優(yōu)選的,在其他方案中,所述步驟s1中的表面處理包括對石墨烯材料進行氧化處理或在氧化后的石墨烯材料表面修飾納米金屬顆粒。
16.所述的納米金屬顆粒為cu、ag、ni、ti、au、al、sn中的至少一種,粒徑為10-1000nm。
17.需要說明的是,在石墨烯材料表面修飾納米金屬顆粒的方法可以是熱還原法、電解等方法。此步驟可以使得石墨烯材料更好的分散開來,利于后續(xù)步驟s3的包覆。
18.優(yōu)選的,所述的大粒徑金屬顆粒為cu、ag、ni、ti、au、al、sn中的至少一種,粒徑為100nm-10μm。
19.優(yōu)選的,所述步驟s3中,石墨烯材料的加入量為0.01-1w.t%。
20.優(yōu)選的,所述步驟s3中,在常溫下,攪拌0.5-1.5h。
21.可以理解的,本發(fā)明中,對于原始石墨烯材料,進行氧化處理或氧化后在表面修飾納米金屬顆粒,得到的石墨烯產(chǎn)物的水溶液是天然帶負電荷的;另將納米金屬顆粒加入ctab溶液中進行表面改性可以使其帶正電荷。因此,將兩種溶液攪拌混合使其正負電荷相吸進行包覆、包覆產(chǎn)物即得到抗氧化能力強,導熱性能突出的填充顆粒。本發(fā)明所用包覆方法為常溫物理吸覆,操作簡單,雜質(zhì)少,無有害物質(zhì)生成。結(jié)合后由tem可見晶格結(jié)合緊密相互交融,且超聲、離心均無法使其脫落,可見其結(jié)合并非僅僅依靠范德華力的物理吸附,即在常溫下便有相應的化學鍵形成??梢?,本發(fā)明利用氧化石墨烯包覆納米金屬顆粒在防止小顆粒金屬氧化的同時,也能很好利用石墨烯的超高面內(nèi)熱導性能進行傳熱,獲得高性能的填充材料。從實驗結(jié)果也可知填充后的封裝材料致密性和導熱性能提升明顯,實際效果突出。
22.例如,步驟s1的表面處理為氧等離子體處理,用氧等離子體處理過的石墨烯(包括石墨烯、石墨烯衍生物),在保證其晶格完整的同時提高其潤濕性。在其他方案中,還可以對氧化后的石墨烯、氧化還原石墨烯、及相應的石墨烯衍生物表面進行負載納米金屬顆粒,使得石墨烯材料更好的分散,負載的納米金屬顆粒與石墨烯材料之間通過化學鍵鍵合,傳熱可靠。處理后的石墨烯在步驟s3中能夠與納米金屬顆粒能實現(xiàn)更好的包覆,提升納米金屬顆粒的抗氧化能力和導熱能力。在步驟s5中與大粒徑金屬顆粒一起燒結(jié)時,能大大降低大粒徑金屬顆粒之間的孔隙率,提升燒結(jié)的致密性、減少界面熱阻,在低溫低壓條件下便可獲得性能優(yōu)異的封裝材料。
23.優(yōu)選的,所述步驟s5中,所述填充顆粒的加入量為10-50w.t%。如填充顆粒的加入量過少會造成填充不致密,孔隙率高;而加入量過高會使得各界面熱阻增加影響導熱性能。
24.優(yōu)選的,所述步驟s5中,采用燒結(jié)溫度為200-800℃;燒結(jié)時間為20-120min;燒結(jié)壓力為0-50mpa。
25.更為優(yōu)選的,所述步驟s5中,燒結(jié)溫度為250℃;燒結(jié)時間為30min;燒結(jié)壓力為5mpa,燒結(jié)得到的封裝材料燒結(jié)致密,熱機電性能優(yōu)異。
26.優(yōu)選的,所述步驟s5中,所述助劑包括粘合劑、分散劑、稀釋劑。
27.需要說明的是,所述填充顆粒與大粒徑金屬顆粒的粒徑比為0.1-0.5。填充顆粒為小粒徑的金屬顆粒,可對大粒徑的金屬顆粒之間的間隙進行填充,進而提升材料致密度,過小會造成填充顆粒消耗過多,界面熱阻大,經(jīng)濟效益低。過大無法發(fā)揮填充效果。。
28.本發(fā)明還提供一種高性能復合材料,由所述的高性能復合材料的制備方法制得。
29.本發(fā)明提供的所述的高性能復合材料在制成半導體封裝材料、互連線路、熱界面材料中的應用。
30.具體地,在步驟s5中,將填充顆粒、s4處理得到的大粒徑金屬顆粒,在燒結(jié)溫度為
200-800℃,燒結(jié)壓力為0-50mpa的條件下,制成高性能復合材料。
31.具體地,在步驟s5中,將填充顆粒、s4處理得到的大粒徑金屬顆粒與粘合劑、分散劑、稀釋劑等助劑混合制成漿料/墨水,在燒結(jié)溫度為100-300℃,燒結(jié)壓力為0-10mpa的條件下,制成互連線路。
32.具體地,在步驟s5中,將填充顆粒、s4處理得到的大粒徑金屬顆粒與粘合劑、分散劑、稀釋劑等助劑混合制成膏體,在燒結(jié)溫度為150-300℃,燒結(jié)壓力為0-20mpa的條件下,制成熱界面材料。
33.與現(xiàn)有技術相比,本發(fā)明所能達到的技術效果包括:
34.本發(fā)明的高性能復合材料是采用石墨烯材料包覆納米金屬顆粒制成填充顆粒,再將填充顆粒與大粒徑的金屬顆?;旌蠠Y(jié)成制得。本發(fā)明提供的方法在常溫下就能實現(xiàn)石墨烯/納米金屬顆粒的有效包覆,結(jié)合緊密;同時,在低溫低壓下就能燒結(jié)得到高性能的封裝材料。經(jīng)石墨烯包覆后的納米金屬顆粒具有一定的抗氧化能力,并且在與大粒徑的金屬顆粒混合燒結(jié)時,能夠提高燒結(jié)體致密性,降低熱膨脹系數(shù),同時本發(fā)明利用石墨烯材料的超高面內(nèi)熱導性能進行高效傳熱,在低溫低壓條件下便可獲得高性能、高導熱的復合材料。
35.本發(fā)明提供的高性能復合材料可在低溫燒結(jié)、封裝互連等領域具有實際的經(jīng)濟效益及突出的性能優(yōu)勢。在“全銅化”背景下的第三代半導體封裝領域有著廣泛的應用前景。
附圖說明
36.為了更清楚地說明本發(fā)明實施例技術方案,下面將對實施例描述中所需要使用的附圖作簡單地介紹,顯而易見地,下面描述中的附圖是本發(fā)明的一些實施例,對于本領域普通技術人員來講,在不付出創(chuàng)造性勞動的前提下,還可以根據(jù)這些附圖獲得其他的附圖。
37.圖1是本發(fā)明實施例提供的步驟s4中,填充顆粒與大粒徑金屬顆粒進行空隙填充的原理圖。
38.圖2是本發(fā)明實施例1、2和對比例1制得的復合材料的密度標準方差直方圖。
39.圖3是本發(fā)明實施例1、2和對比例1制得的復合材料的熱導率標準方差直方圖。
40.圖4是本發(fā)明實施例1步驟s1得到的石墨烯sem效果圖,可見石墨烯存在團聚及重疊。
41.圖5是本發(fā)明實施例2步驟s1得到的石墨烯sem效果圖,可見石墨烯已充分分散。
42.圖6是本發(fā)明實施例2的填充顆粒tem效果圖。
具體實施方式
43.下面將結(jié)合本發(fā)明實施例中的附圖,對實施例中的技術方案進行清楚、完整地描述。顯然,以下將描述的實施例僅僅是本發(fā)明一部分實施例,而不是全部的實施例?;诒景l(fā)明中的實施例,本領域普通技術人員在沒有作出創(chuàng)造性勞動前提下所獲得的所有其他實施例,都屬于本發(fā)明保護的范圍。
44.實施例1
45.本實施例提供一種高性能復合材料及其制備方法,包括以下步驟:
46.s1、對石墨烯進行氧等離子體表面處理,得到氧化石墨烯(表面搭載含氧官能團的石墨烯(ptg),見圖4,其中,ptg代表具有含氧官能團的氧等離子體處理石墨烯);
47.s2、對納米銅顆粒用抗壞血酸進行表面的去氧化處理,再將其加入ctab溶液中進行表面改性,再經(jīng)過超聲分散得到懸浮液;
48.s3、將s1得到的ptg加入所述懸浮液中,超聲分散,充分攪拌反應,將反應產(chǎn)物用無水乙醇洗滌,真空干燥,得到填充顆粒;
49.s4、對大粒徑的銅顆粒用抗壞血酸進行表面的去氧化處理;
50.s5、將填充顆粒與s4處理得到的大粒徑銅顆?;旌虾蠹尤胫鷦┻M行燒結(jié),由于填充顆粒與大粒徑銅顆粒之間的粒徑差別大,填充顆粒可填充在大粒徑的銅顆粒之間的縫隙,填充原理見圖2,因此能夠得到高致密、高導熱的封裝材料。
51.本實施例步驟s3中,氧化石墨烯的加入量為0.6w.t%。
52.本實施例步驟s3中,在常溫下,超聲分散時間為20min;磁力攪拌1h,攪拌轉(zhuǎn)速為350rpm。
53.本實施例步驟s2的納米銅顆粒粒徑為300nm。
54.本實施例步驟s5中,填充顆粒與大粒徑銅顆粒的粒徑比為0.3。
55.本實施例步驟s5中,所述填充顆粒的加入量為30w.t%。
56.本實施例步驟s5中,采用真空熱壓法燒結(jié):燒結(jié)氣氛為氬氫混合氣;燒結(jié)溫度為250℃;燒結(jié)時間為30min;燒結(jié)壓力為5mpa。
57.實施例2
58.本實施例提供一種高性能復合材料及其制備方法,包括以下步驟:
59.s1、對石墨烯進行氧等離子體表面處理,得到氧化石墨烯(表面搭載含氧官能團的石墨烯(ptg)),再通過熱還原法在ptg上負載納米銅顆粒,見圖5;其中,ptg代表具有含氧官能團的氧等離子體處理石墨烯;
60.s2、對納米銅顆粒用抗壞血酸進行表面的去氧化處理,再將其加入ctab溶液中進行表面改性,再經(jīng)過超聲分散得到懸浮液;
61.s3、將s1得到的ptg加入所述懸浮液中,超聲分散,充分攪拌反應,將反應產(chǎn)物用無水乙醇洗滌,真空干燥,得到填充顆粒;其反應原理見圖1。本步驟所得到的填充顆粒的tem效果圖見圖6,可見顆粒的晶格結(jié)合緊密,無明顯分層。
62.s4、對大粒徑的銅顆粒用抗壞血酸進行表面的去氧化處理;
63.s5、將填充顆粒與s4處理得到的大粒徑銅顆粒混合后加入助劑進行燒結(jié),由于填充顆粒與大粒徑銅顆粒之間的粒徑差別大,填充顆??商畛湓诖罅降你~顆粒之間的縫隙,填充原理見圖2,因此能夠得到高致密、高導熱的封裝材料。
64.具體地,本發(fā)明實施例1及實施例2的步驟s1中的氧等離子體表面處理方式為:
65.將25mg的石墨烯放入等離子體腔室內(nèi),然后抽至真空,接著將o2氣體引入腔室,氣體流速保存為100sccm,同時將等離子機的射頻功率調(diào)至110w,對石墨烯進行氧等離子處理30min,得到表面搭載含氧官能團的石墨烯。
66.本實施例步驟s3中,石墨烯的加入量為0.6w.t%。
67.本實施例步驟s3中,在常溫下,超聲分散時間為20min;磁力攪拌1h,攪拌轉(zhuǎn)速為350rpm。
68.本實施例步驟s2的納米銅顆粒粒徑為300nm。
69.本實施例步驟s5中,填充顆粒與大粒徑銅顆粒的粒徑比為0.3。
70.本實施例步驟s4中,大粒徑銅顆粒的粒徑為1μm。
71.本實施例步驟s5中,所述填充顆粒的加入量為30w.t%。
72.本實施例步驟s5中,采用真空熱壓法燒結(jié):燒結(jié)氣氛為氬氫混合氣;燒結(jié)溫度為250℃;燒結(jié)時間為30min;燒結(jié)壓力為5mpa,燒結(jié)得到的封裝材料燒結(jié)致密,機電性能優(yōu)異。
73.本發(fā)明實施例1、實施例2的步驟s5中,加入的助劑具體為,加入松油醇與正丁醇進行混合,二者質(zhì)量比為7:3;將其與填充顆粒、大粒徑銅顆粒一起放入混料機混料2min,得到銅膏;再對混合好的銅膏進行真空熱壓燒結(jié),得到復合材料。
74.需要說明的是,助劑的選擇以及用量可由本領域技術人員根據(jù)實際需求進行選擇,本發(fā)明對此不做限制。
75.對比例1采用粒徑為1μm的微米銅作為復合材料。
76.實施例3:本實施例與實施例2的不同之處在于,步驟s3中,石墨烯的加入量為0.9w.t%。
77.實施例4:本實施例與實施例2的不同之處在于,步驟s3中,石墨烯的加入量為0.3w.t%。
78.實施例5:本實施例與實施例2的不同之處在于,步驟s5中,所述填充顆粒與大粒徑銅顆粒的粒徑比為0.2。
79.實施例6:本實施例與實施例2的不同之處在于,步驟s5中,所述填充顆粒與大粒徑銅顆粒的粒徑比為0.4。
80.實施例7:本實施例與實施例2的不同之處在于,步驟s5的填充顆粒的加入量為10w.t%。
81.實施例8:本實施例與實施例2的不同之處在于,步驟s5的填充顆粒的加入量為50w.t%。
82.性能驗證實驗
83.將實施例1、2與對比例1得到的復合材料作為封裝材料并用于半導體封裝互連的熱界面材料進行相同結(jié)構(gòu)的封裝,封裝時,采用真空熱壓法燒結(jié):燒結(jié)氣氛為氬氫混合氣;燒結(jié)溫度為250℃;燒結(jié)時間為30min;燒結(jié)壓力為5mpa,得到封裝結(jié)構(gòu)。為便于測量,本驗證實驗僅對復合材料測量密度以及熱導率,結(jié)果見圖3-4。
84.由圖可知,本發(fā)明實施例制得的高性能復合材料,經(jīng)石墨烯包覆后的納米金屬顆粒具有一定的抗氧化能力,并且在混合燒結(jié)時能對大粒徑的金屬顆粒之間的空隙進行填充,同時本發(fā)明利用石墨烯的超高面內(nèi)熱導性能進行高效傳熱,在低溫低壓條件下便可獲得高性能、高導熱的封裝結(jié)構(gòu)。而且,通過實驗可知,直接進行石墨烯包覆作為填充材料的性能雖然提升效果優(yōu)異,但進一步配合負載金屬粒子后再包覆的填充材料其性能效果更加突出。
85.在上述實施例中,對各個實施例的描述都各有側(cè)重,某個實施例中沒有詳細描述的部分,可以參見其他實施例的相關描述。
86.以上所述,為本發(fā)明的具體實施方式,但本發(fā)明的保護范圍并不局限于此,任何熟悉本技術領域的技術人員在本發(fā)明揭露的技術范圍內(nèi),可輕易想到各種等效的修改或替換,這些修改或替換都應涵蓋在本發(fā)明的保護范圍之內(nèi)。因此,本發(fā)明的保護范圍應以權(quán)利要求的保護范圍為準。