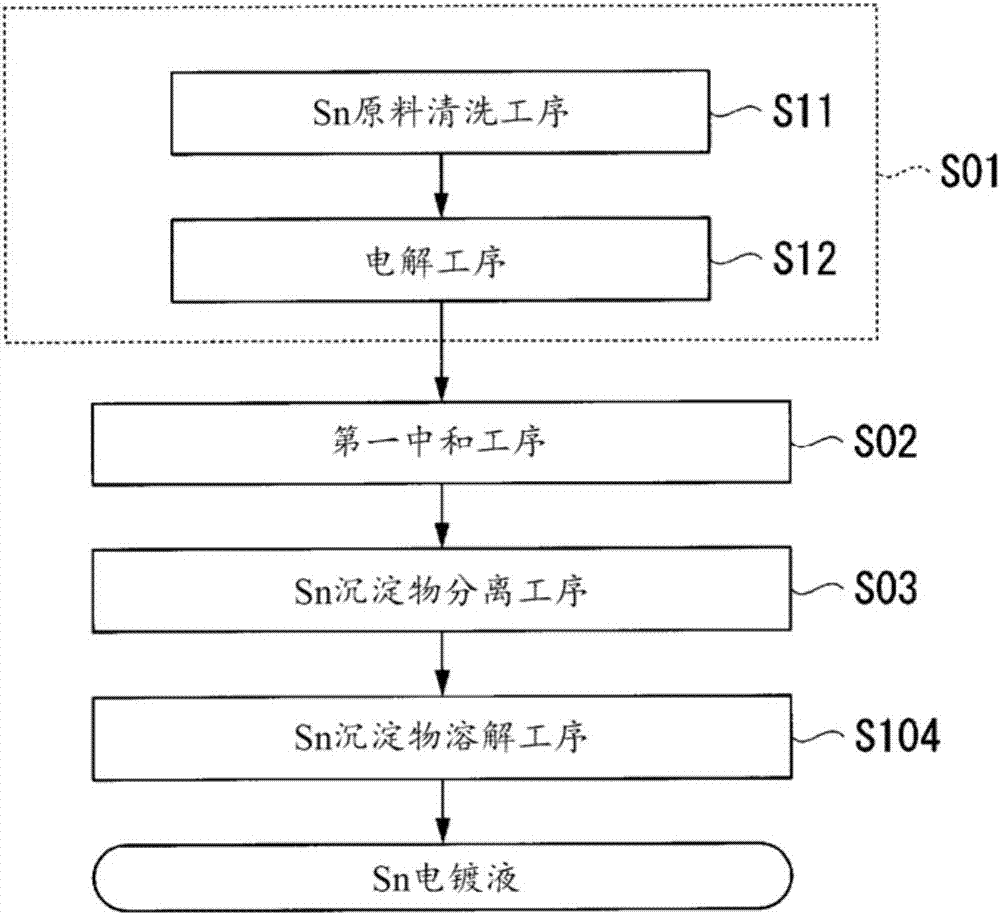
本發(fā)明涉及一種用作焊接或電鍍等的Sn原料的氧化亞錫的制造方法、氧化亞錫以及形成Sn電鍍時使用的Sn電鍍液的制造方法及Sn電鍍液的雜質去除方法。本申請主張基于2014年3月6日于日本申請的專利申請2014-044174號及2015年2月19日于日本申請的專利申請2015-030553號的優(yōu)先權,并將其內(nèi)容援用于此。
背景技術:Sn作為在金屬材料的表面形成電鍍膜的電鍍材料而被廣泛地使用。例如,作為引線框架或連接器等的電子部件材料,廣泛提供有,在由銅或銅合金形成的銅基材的表面實施有Sn電鍍或焊接鍍的附有鍍層的銅材料。另外,該附有鍍層的銅材料也可使用于上述半導體裝置。此外,在鋼板上形成有Sn電鍍的鍍錫鐵材料從以前開始就使用于各種用途。在此,進行Sn電鍍時,有因Sn電鍍液中的雜質伴隨Sn析出而導致電鍍膜的特性變化的憂慮。另外,Sn電鍍液中的雜質會極大的影響電鍍性。因此,要求減少了雜質的Sn電鍍液。此外,因為Sn電鍍液中的雜質會在使用中蓄積,而有電鍍性隨時間發(fā)生變化的憂慮。因此,要求從使用后的Sn電鍍液中有效地去除雜質。另外,在專利文獻1-3中提出有從化學鍍Sn電鍍液中去除作為雜質的Cu的方法。專利文獻1:日本特開2012-140649號公報(A)專利文獻2:日本特開2012-140650號公報(A)專利文獻3:日本特開2013-060638號公報(A)然而,在專利文獻1-3所記載的方法中,雖然公開有減少Cu的方法,但并沒有考慮其他元素,例如,Na、K、Pb、Fe、Ni、Zn、Al、Mg、Ca、Cr、Mn、Co、In、Cd等其他元素。
技術實現(xiàn)要素:本發(fā)明是鑒于上述情況而做成的,其目的在于提供一種能夠有效地去除Na、K、Pb、Fe、Ni、Cu、Zn、Al、Mg、Ca、Cr、Mn、Co、In、Cd等元素的氧化亞錫的制造方法、氧化亞錫、Sn電鍍液的制造方法及Sn電鍍液的雜質去除方法。為了解決上述問題,本發(fā)明的氧化亞錫的制造方法,其特征在于,具備:含Sn離子的酸液形成工序,使酸液含有Sn離子而獲得含Sn離子的酸液;第一中和工序,對所述含Sn離子的酸液,添加選自碳酸銨、碳酸氫銨和氨水中的任意一種以上的堿性溶液,使pH保持在3~6,由此獲得Sn沉淀物;Sn沉淀物分離工序,將所述Sn沉淀物從所述含Sn離子的酸液分離;Sn沉淀物分散工序,使分離的所述Sn沉淀物分散于溶劑液;及第二中和工序,對所述Sn沉淀物的分散液添加堿性溶液并進行加熱,由此從所述Sn沉淀物獲得SnO,在所述第一中和工序中,使Na、K、Pb、Fe、Ni、Cu、Zn、Al、Mg、Ca、Cr、Mn、Co、In、Cd殘留于所述含Sn離子的酸液中。這樣構成的本發(fā)明的氧化亞錫的制造方法中,由于具有對含Sn離子的酸液,添加選自碳酸銨、碳酸氫銨和氨水中的任意一種以上的堿性溶液,使pH保持在3~6,由此獲得Sn沉淀物的第一中和工序,因此,能夠減少所述沉淀物中的Na、K、Pb、Fe、Ni、Cu、Zn、Al、Mg、Ca、Cr、Mn、Co、In、Cd的含量。并且,由于具備:Sn沉淀物分離工序,將該Sn沉淀物從所述含Sn離子的酸液分離;沉淀物分散工序,使分離的Sn沉淀物分散于純水等溶劑液;及第二中和工序,對所述Sn沉淀物的分散液添加堿性溶液并進行加熱,由此從所述Sn沉淀物獲得SnO,因此,能夠獲得減少Na、K、Pb、Fe、Ni、Cu、Zn、Al、Mg、Ca、Cr、Mn、Co、In、Cd的含量的氧化亞錫。在此,本發(fā)明的氧化亞錫的制造方法中,優(yōu)選在所述沉淀物分散工序和所述第二中和工序之間具備對所述Sn沉淀物的分散液添加鹽酸或檸檬酸的酸添加工序。此時,通過在酸添加工序中添加鹽酸或檸檬酸,即使在所述Sn沉淀物中含有第一中和工序S02之前的酸成分,也能夠去除該酸成分,并能夠在之后的第二中和工序中有效地形成SnO(氧化亞錫)。本發(fā)明的氧化亞錫的特征在于,Na、K、Pb、Fe、Ni、Cu、Zn、Al、Mg、Ca、Cr、Mn、Co、In、Cd的含量分別以重量比計被設為1ppm以下。這樣構成的本發(fā)明的氧化亞錫中,Na、K、Pb、Fe、Ni、Cu、Zn、Al、Mg、Ca、Cr、Mn、Co、In、Cd的含量分別以重量比計降低至1ppm以下、因此可作為高質量的氧化亞錫而使用于各種用途中。另外,Na、K、Pb、Fe、Ni、Cu、Zn、Al、Mg、Ca、Cr、Mn、Co、In、Cd的合計含量,以重量比計,優(yōu)選為小于15ppm,進一步優(yōu)選小于7.5ppm。本發(fā)明的Sn電鍍液的制造方法為在進行Sn電鍍時使用的Sn電鍍液的制造方法,其特征在于,通過使由上述氧化亞錫的制造方法獲得的氧化亞錫溶解于酸液中而制造Sn電鍍液。這樣構成的本發(fā)明的Sn電鍍液的制造方法中,由于使用通過上述氧化亞錫的制造方法獲得的氧化亞錫,因此,Sn電鍍液中的Na、K、Pb、Fe、Ni、Cu、Zn、Al、Mg、Ca、Cr、Mn、Co、In、Cd的含量會減少,從而能夠提高電鍍性。并且,本發(fā)明的Sn電鍍液的制造方法為在進行Sn電鍍時使用的Sn電鍍液的制造方法,其特征在于,具備:含Sn離子的酸液形成工序,使酸液含有Sn離子而獲得含Sn離子的酸液;第一中和工序,對所述含Sn離子的酸液,添加選自碳酸銨、碳酸氫銨和氨水中的任意一種以上的堿性溶液,使pH保持在3~6,由此獲得Sn沉淀物;Sn沉淀物分離工序,將所述Sn沉淀物從所述含Sn離子的酸液分離;及Sn沉淀物溶解工序,將分離的所述Sn沉淀物溶解于酸液,在所述第一中和工序中,使Na、K、Pb、Fe、Ni、Cu、Zn、Al、Mg、Ca、Cr、Mn、Co、In、Cd殘留于所述含Sn離子的酸液中。這樣構成成的本發(fā)明的Sn電鍍液的制造方法中,由于具有對所述含Sn離子的酸液,添加選自碳酸銨、碳酸氫銨和氨水中的任意一種以上的堿性溶液,使pH保持在3~6,由此獲得Sn沉淀物的第一中和工序,因此,Sn沉淀物中的Na、K、Pb、Fe、Ni、Cu、Zn、Al、Mg、Ca、Cr、Mn、Co、In、Cd的含量會減少。而且,由于具備:Sn沉淀物分離工序,將所述Sn沉淀物從所述含Sn離子的酸液分離;及Sn沉淀物溶解工序,將分離的所述Sn沉淀物溶解于酸液,因此,能夠獲得Na、K、Pb、Fe、Ni、Cu、Zn、Al、Mg、Ca、Cr、Mn、Co、In、Cd的含量減少的Sn電鍍液。本發(fā)明的Sn電鍍液的雜質去除方法為從酸液中存在Sn離子的Sn電鍍液去除雜質元素的Sn電鍍液的雜質去除方法,其特征在于,具備:第一中和工序,對所述Sn電鍍液,添加選自碳酸銨、碳酸氫銨和氨水中的任意一種以上的堿性溶液,使pH保持在3~6,由此獲得Sn沉淀物;Sn沉淀物分離工序,將所述Sn沉淀物從所述Sn電鍍液分離;及Sn沉淀物溶解工序,將分離的所述Sn沉淀物溶解于酸液,在所述第一中和工序中,使Na、K、Pb、Fe、Ni、Cu、Zn、Al、Mg、Ca、Cr、Mn、Co、In、Cd殘留于所述Sn電鍍液中。這樣構成的本發(fā)明的Sn電鍍液的雜質去除方法中,由于具有對所述含Sn離子的酸液電鍍液,添加選自碳酸銨、碳酸氫銨和氨水中的任意一種以上的堿性溶液,使pH保持在3~6,由此獲得Sn沉淀物的第一中和工序,因此,能夠使因使用而蓄積有雜質的Sn電鍍液中的Na、K、Pb、Fe、Ni、Cu、Zn、Al、Mg、Ca、Cr、Mn、Co、In、Cd殘留于Sn電鍍液中的狀態(tài)下獲得Sn沉淀物。而且由于具備:Sn沉淀物分離工序,將該Sn沉淀物從Sn電鍍液分離;及Sn沉淀物溶解工序,將分離的所述Sn沉淀物溶解于酸液,因此,能夠獲得Na、K、Pb、Fe、Ni、Cu、Zn、Al、Mg、Ca、Cr、Mn、Co、In、Cd的含量減少的Sn電鍍液。如上所述,根據(jù)本發(fā)明,能夠提供一種能夠有效去除Na、K、Pb、Fe、Ni、Cu、Zn、Al、Mg、Ca、Cr、Mn、Co、In、Cd等元素的氧化亞錫的制造方法、氧化亞錫、Sn電鍍液的制造方法及Sn電鍍液的雜質去除方法。附圖說明圖1為表示本發(fā)明的第一實施方式的氧化亞錫的制造方法的流程圖。圖2為表示本發(fā)明的第二實施方式的Sn電鍍液的制造方法的流程圖。圖3為表示本發(fā)明的第三實施方式的Sn電鍍液的雜質去除方法的流程圖。具體實施方式以下,對本發(fā)明的實施方式的氧化亞錫、氧化亞錫的制造方法、Sn電鍍液的制造方法及Sn電鍍液的雜質去除方法進行說明。<第一實施方式>首先,對本發(fā)明的第一實施方式的氧化亞錫的制造方法及氧化亞錫進行說明。本實施方式的氧化亞錫能夠使用于焊接材料或金屬Sn的原料、Sn電鍍液的Sn供給材料等各種用途。本實施方式的氧化亞錫,Na、K、Pb、Fe、Ni、Cu、Zn、Al、Mg、Ca、Cr、Mn、Co、In、Cd的含量分別以重量比計被設為1ppm以下。如上所述,本實施方式的氧化亞錫(以氧化亞錫為主體的組合物)是減少了上述特定雜質元素的物質。以下,對如上述那樣規(guī)定本實施方式的氧化亞錫中的雜質元素含量的理由進行說明。(Pb:1ppm以下)Pb為與Sn的特性相似,難以從Sn分離的元素。因此,將氧化亞錫作為Sn電鍍液的Sn供給材料使用時,在Sn電鍍液中Pb會作為雜質元素而蓄積,從而對電鍍性造成影響。因此,在本實施方式中,將氧化亞錫中的Pb的含量規(guī)定為以重量比計為1ppm以下。(Na、K:分別為1ppm以下)Na、K等元素,有時在Sn原料的精制時混入,將氧化亞錫作為Sn電鍍液的Sn供給材料使用時,在Sn電鍍液中會作為雜質元素蓄積,有可能對電鍍性造成影響。因此,在本實施方式中,將氧化亞錫中的Na、K的含量規(guī)定為以重量比計為1ppm以下。(Fe、Ni、Cu、Zn:分別為1ppm以下)Fe、Ni、Cu、Zn這些元素,會從被電鍍物、鍍底層等混入Sn電鍍液內(nèi),在Sn電鍍液中會作為雜質蓄積,有可能對電鍍性造成影響。因此,在本實施方式中,將氧化亞錫中的Fe、Ni、Cu、Zn的含量規(guī)定為以重量比計為1ppm以下。(Al、Mg、Ca、Cr、Mn、Co、In、Cd:分別為1ppm以下)Al、Mg、Ca、Cr、Mn、Co、In、Cd等元素,有可能會從Sn原料中混入,將氧化亞錫作為Sn電鍍液的Sn供給材料使用時,在Sn電鍍液中作為雜質蓄積,有可能對電鍍性造成影響。因此,在本實施方式中,將氧化亞錫中的Al、Mg、Ca、Cr、Mn、Co、In、Cd的含量規(guī)定為以重量比計為1ppm以下。另外,為了可靠地抑制對Sn電鍍液的影響,優(yōu)選將上述Na、K、Pb、Fe、Ni、Cu、Zn、Al、Mg、Ca、Cr、Mn、Co、In、Cd的合計含量,以重量比計設為小于15ppm,更優(yōu)選小于7.5ppm。接著,參考圖1的流程圖,對本實施方式的氧化亞錫的制造方法進行說明。(含Sn離子的酸液形成工序S01)首先,使酸液含有Sn離子,形成含Sn離子的酸液。在本實施方式中,準備高純度的金屬Sn(純度99.99質量%以上),并使用酸性洗滌劑清洗該金屬Sn(Sn原料清洗工序S11)。此時,清洗至去除金屬Sn表面的油分和氧化物,使金屬Sn的表面出現(xiàn)金屬光澤為止。接著,將清洗的金屬Sn在酸液中電解,形成含Sn離子的酸液(電解工序S12)。此時,作為酸液無特別限定,可以使用甲磺酸、鹽酸、硝酸、硫酸、硼氟酸、苯酚磺酸、烷醇磺酸(アルカノールスルホン酸)、烷基磺酸等或這些的混合酸。并且,Sn的濃度,優(yōu)選設為例如50g/L以上且150g/L以下的范圍內(nèi),在本實施方式中,設為100~110g/L。(第一中和工序S02)接著,對含Sn離子的酸液,添加選自碳酸銨、碳酸氫銨和氨水中的任意一種以上的堿性溶液,使pH保持在3~6,由此獲得作為不溶性成分的Sn沉淀物(氫氧化錫等)。此時,Sn作為Sn沉淀物(氫氧化錫等)被回收的同時,Na、K、Fe、Ni、Cu、Zn、Al、Mg、Ca、Cr、Mn、Co、In、Cd等元素作為可溶性成分殘留于含Sn離子的溶液中。其中,“殘留于含Sn離子的溶液中”是指,在形成含Sn離子的酸液工序S01中形成的酸液中含有的Na、K、Fe、Ni、Cu、Zn、Al、Mg、Ca、Cr、Mn、Co、In、Cd的總元素質量設為100%時,99.0%以上殘留于第一中和工序S02結束后的可溶性成分(含Sn離子的酸液)中。另外,在本實施方式中,將添加碳酸氫銨水溶液至pH為3.5~4的范圍。(Sn沉淀物分離工序S03)接著,將Sn沉淀物(氫氧化錫等)從含Sn離子的酸液分離。(Sn沉淀物分散工序S04)接著,用純水對分離的Sn沉淀物(氫氧化錫等)反復進行2~3次分散和過濾,以進行Sn沉淀物(氫氧化錫等)的清洗。由此,去除附著于Sn沉淀物(氫氧化錫等)表面的雜質。然后,將清洗后的Sn沉淀物(氫氧化錫等)分散于純水中。(酸添加工序S05)接著,根據(jù)需要,對分散有Sn沉淀物(氫氧化錫等)的分散液添加鹽酸或檸檬酸。通過此酸添加工序S05,分離Sn沉淀物(氫氧化錫等)中的酸成分。(第二中和工序S06)接著,對分散有Sn沉淀物(氫氧化錫等)的分散液添加堿性溶液并進行加熱,由此從Sn沉淀物(氫氧化錫等)獲得SnO(氧化亞錫)。在該第二中和工序S06中,通過使Sn沉淀物(氫氧化錫等)脫水,形成SnO(氧化亞錫)。在本實施方式中,將碳酸氫銨水溶液作為堿性溶液添加至pH為6以上的同時,加熱至100℃以上。(清洗、干燥工序S07)接著,用純水對所獲得的SnO(氧化亞錫)反復進行2~3次分散和過濾,以進行SnO(氧化亞錫)的清洗。由此,去除附著于SnO(氧化亞錫)的表面的雜質。然后,將清洗后的SnO(氧化亞錫)過濾、干燥。通過以上的工序,制造本實施方式的氧化亞錫。根據(jù)如上所構成的本實施方式的氧化亞錫,Na、K、Pb、Fe、Ni、Cu、Zn、Al、Mg、Ca、Cr、Mn、Co、In、Cd的含量分別以重量比計為1ppm以下,因此即使在制造過程中混入這些元素的情況下,也可充分地減少氧化亞錫中的雜質元素,可利用于各種用途。并且,將該氧化亞錫作為Sn電鍍液的Sn供給材料而使用的情況下,也能夠抑制Sn電鍍液的電鍍性降低,能夠有效地形成高品質的電鍍膜。并且,通過將本實施方式的氧化亞錫溶解于甲磺酸或硫酸水溶液等酸液中,從而能夠制造Sn電鍍液。該Sn電鍍液,由于Na、K、Pb、Fe、Ni、Cu、Zn、Al、Mg、Ca、Cr、Mn、Co、In、Cd的含量極少,因此電鍍性得到提高,能夠有效地形成高品質的電鍍膜。根據(jù)本實施方式的氧化亞錫的制造方法,由于其具備對含Sn離子的酸液添加堿性溶液(在本實施方式中為碳酸氫銨),使pH保持在3~6,由此獲得Sn沉淀物(氫氧化錫等)的第一中和工序S02,因此,能夠減少Sn沉淀物(氫氧化錫等)中的Na、K、Pb、Fe、Ni、Cu、Zn、Al、Mg、Ca、Cr、Mn、Co、In、Cd的含量。而且,由于具備:Sn沉淀物分離工序S03,將該Sn沉淀物(氫氧化錫等)從含Sn離子的酸液分離;Sn沉淀物分散工序S04,將分離的Sn沉淀物(氫氧化錫等)分散于純水等溶劑液;第二中和工序S06,對Sn沉淀物(氫氧化錫等)的分散液添加堿性溶液并進行加熱,由此從Sn沉淀物(氫氧化錫等)獲得SnO(氧化亞錫),因此能夠有效地獲得Na、K、Pb、Fe、Ni、Cu、Zn、Al、Mg、Ca、Cr、Mn、Co、In、Cd的含量減少的氧化亞錫。并且,在本實施方式中,在Sn沉淀物分散工序S04與第二中和工序S06之間,具備對Sn沉淀物(氫氧化錫等)的分散液添加鹽酸或檸檬酸的酸添加工序S05,因此即使在Sn沉淀物(氫氧化錫等)中含有第一中和工序S02之前的酸成分,也能夠去除該酸成分,在之后的第二中和工序S06中能夠有效地形成SnO(氧化亞錫)。具體而言,無需嚴格控制第二中和工序S06中的pH值、加熱溫度,便能夠有效地形成SnO(氧化亞錫)。<第二實施方式>接著,用圖2的流程圖對本發(fā)明的第二實施方式的Sn電鍍液的制造方法進行說明。其中,對于與第一實施方式相同的構成標記相同的符號,并省略詳細說明。(含Sn離子的酸液形成工序S01)首先,與第一實施方式相同地使酸液含有Sn離子,形成含Sn離子的酸液。該含Sn離子的酸液形成工序S01中,通過實施Sn原料清洗工序S11及電解工序S12,形成含Sn離子的酸液。(第一中和工序S02)接著,對含Sn離子的酸液,添加選自碳酸銨、碳酸氫銨和氨水中的任意一種以上的堿性溶液,使pH保持在3~6,由此獲得Sn沉淀物(氫氧化錫等)。此時,將Sn作為Sn沉淀物(氫氧化錫等)回收的同時,Na、K、Fe、Ni、Cu、Zn、Al、Mg、Ca、Cr、Mn、Co、In、Cd等元素會殘留于含Sn離子的酸液中。(Sn沉淀物分離工序S03)接著,將Sn沉淀物(氫氧化錫等)從含Sn離子的酸液分離。(Sn沉淀物溶解工序S104)接著,用純水對分離的Sn沉淀物(氫氧化錫等)反復進行2~3次分散和過濾,以進行Sn沉淀物(氫氧化錫等)的清洗。由此,去除附著于Sn沉淀物(氫氧化錫等)的表面的雜質。然后,將清洗后的Sn沉淀物(氫氧化錫等)溶解于作為Sn電鍍液而使用的酸液中。由此,能夠形成Sn電鍍液。根據(jù)本實施方式的Sn電鍍液的制造方法,由于具有第一中和工序S02,即對含Sn離子的酸液添加選自碳酸銨、碳酸氫銨和氨水中的任意一種以上的堿性溶液,使pH保持在3~6,由此獲得Sn沉淀物,因此會減少Sn沉淀物中的Na、K、Pb、Fe、Ni、Cu、Zn、Al、Mg、Ca、Cr、Mn、Co、In、Cd的含量。而且,由于具備:Sn沉淀物分離工序S03,將Sn沉淀物從含Sn離子的酸液分離;Sn沉淀物溶解工序S104,將分離的所述Sn沉淀物溶解于酸液,因此能夠獲得Na、K、Pb、Fe、Ni、Cu、Zn、Al、Mg、Ca、Cr、Mn、Co、In、Cd的含量減少的Sn電鍍液。<第三實施方式>接著,用圖3的流程圖對本發(fā)明的第三實施方式的Sn電鍍液的雜質去除方法進行說明。其中,對于與第一、第二實施方式相同的構成標記相同的符號,并省略詳細說明。使用過的Sn電鍍中蓄積有Sn中含有的雜質元素、從被電鍍物、鍍底層混入的雜質元素,會使電鍍性劣化。因此,本實施方式的Sn電鍍液的雜質去除方法是從使用過的Sn電鍍液有效地去除雜質元素的方法。(第一中和工序S02)首先,對使用過的Sn電鍍液,添加選自碳酸銨、碳酸氫銨和氨水中的任意一種以上的堿性溶液,使pH保持在3~6,由此獲得Sn沉淀物(氫氧化錫等)。此時,Sn作為Sn沉淀物(氫氧化錫等)被回收的同時,Na、K、Fe、Ni、Cu、Zn、Al、Mg、Ca、Cr、Mn、Co、In、Cd等元素殘留于Sn電鍍液中。(Sn沉淀物分離工序S03)接著,將Sn沉淀物(氫氧化錫等)從含Sn離子的酸液分離。(Sn沉淀物溶解工序S104)接著,用純水對分離的Sn沉淀物(氫氧化錫等)反復進行2~3次分散和過濾,以進行Sn沉淀物(氫氧化錫等)的清洗。由此,去除附著于Sn沉淀物(氫氧化錫等)的表面的雜質。然后,將清洗后的Sn沉淀物(氫氧化錫等)溶解于作為Sn電鍍液而使用的酸液中。由此,能夠形成Sn電鍍液。根據(jù)本實施方式的Sn電鍍液的雜質去除方法,由于其具有第一中和工序S02,即對含Sn離子的酸液添加選自碳酸銨、碳酸氫銨和氨水中的任意一種以上的堿性溶液,使pH保持在3~6,由此獲得Sn沉淀物,因此能夠在使因使用而蓄積有雜質元素的Sn電鍍液中的Na、K、Pb、Fe、Ni、Cu、Zn、Al、Mg、Ca、Cr、Mn、Co、In、Cd殘留于Sn電鍍液中的狀態(tài)下,獲得Sn沉淀物。而且,由于具備:Sn沉淀物分離工序S03,將該Sn沉淀物從Sn電鍍液分離;Sn沉淀物溶解工序S104,將分離的Sn沉淀物溶解于酸液,由此能夠獲得Na、K、Pb、Fe、Ni、Cu、Zn、Al、Mg、Ca、Cr、Mn、Co、In、Cd的含量減少的Sn電鍍液。以上對本發(fā)明的實施方式進行了說明,但本發(fā)明并不限定于此,在不脫離其發(fā)明的技術思想范圍內(nèi)可以適當加以變更。例如,在本實施方式中,含Sn離子的酸液形成工序S01中,說明了電解金屬Sn的含Sn離子的酸液,但并不限定于此,也可以使用通過其他方法獲得的含Sn離子的酸液。并且,本發(fā)明的第一實施方式中,說明了在Sn沉淀分散工序S04和第二中和工序S06之間,具備添加鹽酸或檸檬酸的酸添加工序S05的方法,但并不限定于此,在最初就使用了鹽酸或檸檬酸的情況下,可以省略酸添加工序S05。實施例以下,對為了確認本發(fā)明的有效性而進行的確認實驗的結果進行說明。本發(fā)明例1~4中,作為第一中和工序,在鹽酸錫水溶液中添加碳酸氫銨中和至表1所示的pH。將得到的濾餅清洗而獲得Sn沉淀物,然后將該Sn沉淀物在純水中再分散。接著,作為第二中和工序,在Sn沉淀物的分散液中添加碳酸氫銨中和至pH為8的同時進行加熱,將得到的濾餅清洗并進行干燥,由此獲得氧化亞錫。本發(fā)明例5中,作為第一中和工序,在鹽酸錫水溶液中添加碳酸銨中和至表1所示的pH。將得到的濾餅清洗獲得Sn沉淀物,然后將該Sn沉淀物在純水中再分散。接著,作為第二中和工序,在Sn沉淀物的分散液中添加碳酸銨中和的同時進行加熱直至pH為8,將得到的濾餅清洗并干燥,由此獲得氧化亞錫。比較例中,作為中和工序,在Sn沉淀物的分散液中添加碳酸銨中和的同時進行加熱直至pH為8,將得到的濾餅清洗并進行干燥,由此獲得氧化亞錫。即,在比較例中,通過一次中和工序獲得了氧化亞錫。對如上述所獲得的氧化亞錫,使用ICP-MS,測定了作為雜質元素的Na、K、Pb、Fe、Ni、Cu、Zn、Al、Mg、Ca、Cr、Mn、Co、In、Cd的濃度(重量比)。將結果示于表1。[表1]在比較例中,各雜質元素的濃度較高。尤其,Na以重量比計高達1000ppm。相對于此,在本發(fā)明例中,雜質元素的濃度均較低。由以上實驗結果可確認到,根據(jù)本發(fā)明例,能夠有效的去除Na、K、Pb、Fe、Ni、Cu、Zn、Al、Mg、Ca、Cr、Mn、Co、In、Cd這些元素,能夠獲得減少這些雜質元素的高品質的氧化亞錫。產(chǎn)業(yè)上的可利用性通過獲得雜質元素的含量較少的氧化亞錫,能夠在Sn電鍍領域、其他利用Sn的技術領域中,獲得更高的效果。符號說明S01-含Sn離子的酸液形成工序,S02-第一中和工序,S03-Sn沉淀物分離工序,S04-Sn沉淀物分散工序,S06-第二中和工序。