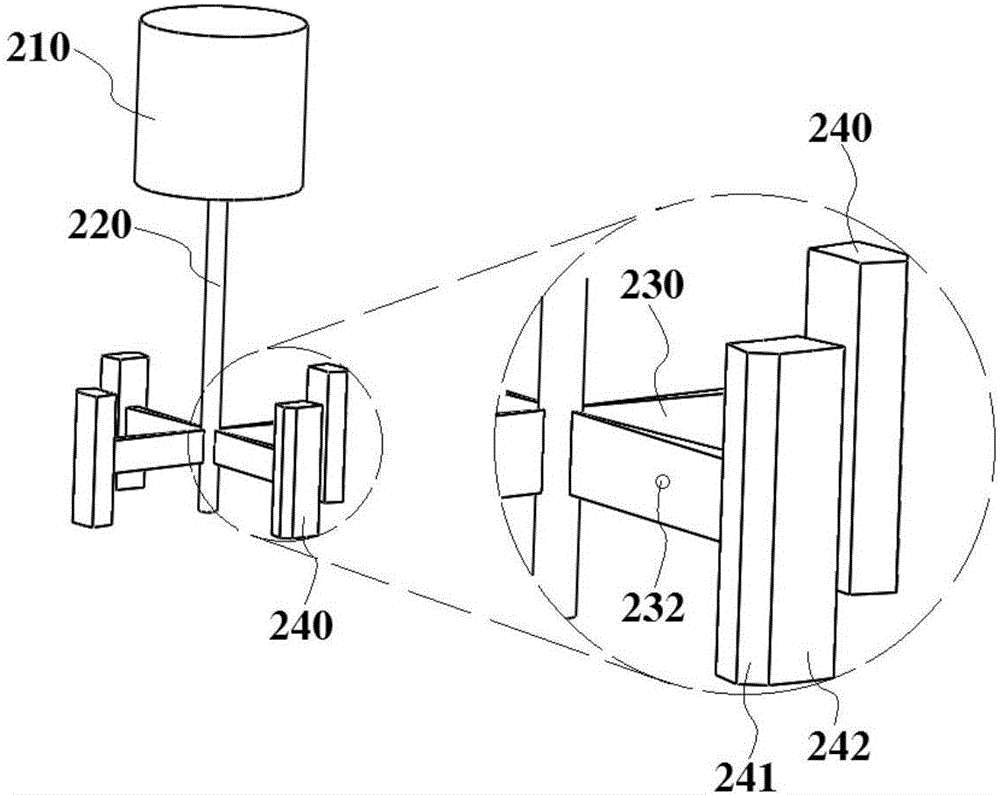
本發(fā)明涉及脫硫副產(chǎn)物的資源化應(yīng)用領(lǐng)域,更具體地說(shuō),涉及一種利用燒結(jié)煙氣脫硫副產(chǎn)物制備硫酸鈣晶須的方法。
背景技術(shù):
:隨著我國(guó)鋼鐵工業(yè)的持續(xù)迅猛發(fā)展,所產(chǎn)生的環(huán)境污染問(wèn)題十分突出,尤其“三廢”排放方面?zhèn)涫車(chē)?guó)家的高度關(guān)注,在最新修訂的“鋼鐵工業(yè)污染排放標(biāo)準(zhǔn)”中將SO2的排放控制作為重要內(nèi)容之一,強(qiáng)制性規(guī)定鋼鐵行業(yè)要限期實(shí)現(xiàn)減排量和煙氣達(dá)標(biāo)排放。在我國(guó)鋼鐵企業(yè),SO2排放量?jī)H次于電力工業(yè)和工業(yè)鍋爐的排放量,居第3位,而鋼鐵企業(yè)排放的SO2中50%-70%來(lái)自燒結(jié)工序,采用半干法脫硫技術(shù)進(jìn)行燒結(jié)煙氣脫硫,不僅投資低,且脫硫率較高,但是在半干法脫硫過(guò)程中產(chǎn)生了大量的脫硫副產(chǎn)物,目前,國(guó)內(nèi)外只有少部分脫硫副產(chǎn)物得到利用,絕大部分被拋棄,如果不加以合理利用,將會(huì)造成二次污染并占用大量土地。隨著我國(guó)環(huán)境保護(hù)意識(shí)的加強(qiáng),燒結(jié)礦煙氣脫硫副產(chǎn)物的綜合利用方面的研究逐漸受到人們的關(guān)注,并且燒結(jié)礦煙氣脫硫副產(chǎn)物的利用可以減少因堆放所消耗的資金、占用土地和環(huán)境污染,減少天然石膏的用量,進(jìn)而減少天然石膏的開(kāi)采量,保護(hù)生態(tài)環(huán)境。因此,許多高校和企業(yè)對(duì)燒結(jié)礦煙氣脫硫副產(chǎn)物綜合利用方面進(jìn)行了大量的研究,如利用燒結(jié)煙氣脫硫副產(chǎn)物制備硫酸、水泥緩凝劑、石膏建筑材料和硫酸鈣晶須等。其中,采用燒結(jié)煙氣脫硫副產(chǎn)物制備硫酸鈣晶須具有較高的附加值,硫酸鈣晶須是以單晶形式生長(zhǎng)出的一種短纖維,它具有均勻的橫截面,完整的外形及高度完善的內(nèi)部結(jié)構(gòu),與玻璃纖維相比,優(yōu)點(diǎn)在于它具有極高的強(qiáng)度,細(xì)微的尺寸,更易與樹(shù)脂、橡膠、塑料等有機(jī)高分子化合物結(jié)合,并且產(chǎn)品的外觀質(zhì)量?jī)?yōu)良。可廣泛用于汽車(chē)、航空航天、化工、冶金、國(guó)防、機(jī)械、電氣、船舶、石油和建材等諸多領(lǐng)域。以脫硫石膏為原料制備硫酸鈣晶須不僅可以減少脫硫石膏對(duì)環(huán)境的污染,還可以節(jié)約天然石膏資源,并且為脫硫石膏的高附加值利用開(kāi)辟了新途徑,但是現(xiàn)有的脫硫副產(chǎn)物制備硫酸鈣晶須的方法尚不完善,使得硫酸鈣晶須的質(zhì)量較差,嚴(yán)重限制了脫硫副產(chǎn)物的高效資源化應(yīng)用。經(jīng)專(zhuān)利檢索,東北大學(xué)的史培陽(yáng)也進(jìn)行了先關(guān)研究,并申請(qǐng)了相關(guān)專(zhuān)利,利用燒結(jié)礦煙氣脫硫副產(chǎn)物制備硫酸鈣晶須的方法(申請(qǐng)?zhí)枺?01010545829.1;申請(qǐng)日:2010.11.16)和利用煙氣脫硫石膏制備硫酸鈣晶須的方法(申請(qǐng)?zhí)枺?00810011193.5;申請(qǐng)日:2008.04.25),該方法為脫硫副產(chǎn)物的資源化應(yīng)用提供了一種途徑。此外,一種利用半干法脫硫灰和廢酸制備石膏晶須的工藝及裝置(申請(qǐng)?zhí)枺?01210405335.2,申請(qǐng)日:2012.10.22),實(shí)現(xiàn)了脫硫副產(chǎn)物的資源化應(yīng)用。但是,現(xiàn)有的方法生產(chǎn)得到的硫酸鈣晶須質(zhì)量較差,限制了脫硫副產(chǎn)物的高附加值應(yīng)用。技術(shù)實(shí)現(xiàn)要素:1.發(fā)明要解決的技術(shù)問(wèn)題本發(fā)明的目的在于克服現(xiàn)有技術(shù)中,在采用脫硫副產(chǎn)物制備晶須過(guò)程中制備方法尚不完善,致使制備得到的硫酸鈣晶須性能較差的問(wèn)題,提供一種利用燒結(jié)煙氣脫硫副產(chǎn)物制備硫酸鈣晶須的方法,大大提高了制備的硫酸鈣晶須的性能,實(shí)現(xiàn)了脫硫副產(chǎn)物的高附加值應(yīng)用。2.技術(shù)方案為達(dá)到上述目的,本發(fā)明提供的技術(shù)方案為:本發(fā)明的一種利用燒結(jié)煙氣脫硫副產(chǎn)物制備硫酸鈣晶須的方法,具體步驟如下:步驟一、去除雜質(zhì)將脫硫副產(chǎn)物去雜后加入硫酸進(jìn)行酸洗,將酸洗液進(jìn)行抽濾得到脫硫副產(chǎn)物顆粒,對(duì)脫硫副產(chǎn)物顆粒進(jìn)行水洗2-4次,并得到呈中性的脫硫副產(chǎn)物溶液;步驟二、低溫氧化將脫硫副產(chǎn)物溶液加入氧化裝置,向脫硫副產(chǎn)物溶液中吹入富氧空氣進(jìn)行吹氣氧化,吹氣氧化的過(guò)程中對(duì)脫硫副產(chǎn)物顆粒進(jìn)行間歇研磨,并控制脫硫副產(chǎn)物溶液的氧化溫度為50-90℃;步驟三、調(diào)配漿料將步驟二的脫硫副產(chǎn)物溶液進(jìn)行干燥得到脫硫副產(chǎn)物粉料,向脫硫副產(chǎn)物粉料中加入水,并控制固液比為1/6-1/10;攪拌使其充分乳化制得漿料;步驟四、水熱反應(yīng)將上述得到的漿料加入反應(yīng)釜中,在120-150℃的密閉條件下進(jìn)行下反應(yīng)60-180min,并得到反應(yīng)產(chǎn)物;步驟五、水洗干燥對(duì)反應(yīng)產(chǎn)物水洗1-3次,抽濾得到濾餅;再將濾餅置于干燥箱中干燥,干燥完成得到CaSO4晶須。優(yōu)選地,所述的步驟五中水洗的過(guò)程中,用于水洗的水溫為80-100℃。優(yōu)選地,所述的步驟四水熱反應(yīng)時(shí)的攪拌速度為15-25r/min。優(yōu)選地,步驟三中加入稀硫酸調(diào)節(jié)PH至3.5-5.3。優(yōu)選地,所述的步驟二中的富氧空氣中的氧氣體積比為40-60%。優(yōu)選地,氧化裝置包括氧化單元,該氧化單元包括氧化吹氣部件和研磨氧化腔體,其中氧化吹氣部件位于研磨氧化腔體的下部,氧化吹氣部件用于向研磨氧化腔體鼓入富氧空氣,所述的研磨氧化腔體由弧形研磨段和研磨間隙段組成;攪拌研磨單元,該攪拌研磨單元包括驅(qū)動(dòng)電機(jī)和攪拌研磨葉片,所述的驅(qū)動(dòng)電機(jī)上設(shè)置有攪拌研磨葉片,該攪拌研磨葉片的圓周上設(shè)置有葉片研磨圓?。簧鲜龅臄嚢柩心ト~片位于研磨氧化腔體內(nèi),且攪拌研磨葉片的葉片研磨圓弧與弧形研磨段相配合,在驅(qū)動(dòng)電機(jī)的驅(qū)動(dòng)下葉片研磨圓弧與弧形研磨段發(fā)生研磨運(yùn)動(dòng)。優(yōu)選地,所述的氧化單元還包括錐形收集倉(cāng),該錐形收集倉(cāng)為倒錐形,所述的氧化吹氣部件通過(guò)錐形收集倉(cāng)與研磨氧化腔體相連。優(yōu)選地,所述的攪拌研磨單元還包括電機(jī)驅(qū)動(dòng)軸和葉片連接桿,所述的驅(qū)動(dòng)電機(jī)通過(guò)電機(jī)驅(qū)動(dòng)軸與葉片連接桿相連,該葉片連接桿上設(shè)置有攪拌研磨葉片。優(yōu)選地,所述的具體步驟為:A、將脫硫副產(chǎn)物溶液加入氧化裝置之中,脫硫副產(chǎn)物在重力作用下下沉至底部的錐形收集倉(cāng)中;B、氧化吹氣部件將富氧空氣吹入氧化裝置,在富氧空氣的驅(qū)動(dòng)下,沉積在錐形收集倉(cāng)的脫硫副產(chǎn)物顆粒運(yùn)動(dòng)至氧化裝置頂部的研磨氧化腔體內(nèi),在攪拌研磨葉片旋轉(zhuǎn)攪拌的作用下,脫硫副產(chǎn)物顆粒運(yùn)動(dòng)至研磨氧化腔體的內(nèi)壁邊緣位置;C、在研磨氧化腔體的內(nèi)壁邊緣對(duì)脫硫副產(chǎn)物顆粒進(jìn)行間歇研磨,所述的間歇研磨為脫硫副產(chǎn)物顆粒運(yùn)動(dòng)至弧形研磨段時(shí),研磨氧化腔體的內(nèi)壁與攪拌研磨葉片的葉片研磨圓弧發(fā)生擠壓碰撞,將脫硫副產(chǎn)物顆粒表面的難溶物研磨去除,研磨后的脫硫副產(chǎn)物顆粒在研磨間隙段與葉片研磨圓弧分離,富氧空氣與脫硫副產(chǎn)物顆粒內(nèi)部反應(yīng),而后脫硫副產(chǎn)物顆粒再次運(yùn)動(dòng)至弧形研磨段時(shí)發(fā)生再次研磨、氧化。優(yōu)選地,所述的富氧空氣的溫度為60-150℃。3.有益效果采用本發(fā)明提供的技術(shù)方案,與已有的公知技術(shù)相比,具有如下顯著效果:(1)本發(fā)明的一種利用燒結(jié)煙氣脫硫副產(chǎn)物制備硫酸鈣晶須的方法,通過(guò)對(duì)脫硫副產(chǎn)物的充分氧化改性,提高了脫硫副產(chǎn)物中硫酸鈣的純度,為后續(xù)生長(zhǎng)良好的晶須做好物質(zhì)基礎(chǔ),在調(diào)配漿料的過(guò)程中嚴(yán)格控制脫硫灰的漿料的固液比為1/6-1/10,而后選擇在120-150℃的密閉條件下進(jìn)行下反應(yīng)60-180min,使得制備的硫酸鈣晶須直徑小于1μm,長(zhǎng)徑比到達(dá)80,硫酸鈣晶須的強(qiáng)度的理論強(qiáng)度達(dá)到0.02E-0.05E,表明光潔度較高,大大提高了硫酸鈣晶須的性能,實(shí)現(xiàn)了脫硫副產(chǎn)物的高附加值應(yīng)用;(2)本發(fā)明的一種利用燒結(jié)煙氣脫硫副產(chǎn)物制備硫酸鈣晶須的方法,在水熱反應(yīng)結(jié)束后水洗的過(guò)程中,創(chuàng)造性的提出了采用水溫為80-100℃的水進(jìn)行水洗,從而提高了硫酸鈣晶須表面光潔度,減少了制備的硫酸鈣晶須的斷裂面,進(jìn)一步提高了硫酸鈣晶須制備的質(zhì)量,改善了晶須的性能;(3)本發(fā)明的一種利用燒結(jié)煙氣脫硫副產(chǎn)物制備硫酸鈣晶須的方法,在氧化的過(guò)程中進(jìn)行間歇研磨,將脫硫副產(chǎn)物顆粒表面的難溶物研磨去除,即將附著在脫硫副產(chǎn)物顆粒表面的硫酸鈣在機(jī)械力研磨的作用下被研磨去除,使得顆粒內(nèi)部的亞硫酸鈣暴露在顆粒表面,促進(jìn)了氧氣分子與亞硫酸鈣表面的接觸,從而加快并促進(jìn)了顆粒內(nèi)部的亞硫酸鈣的氧化,并大大提高了脫硫副產(chǎn)物中硫酸鈣的氧化率,使得SO32-的氧化率達(dá)到78.52%,使得脫硫副產(chǎn)物得到有效改性。附圖說(shuō)明圖1為本發(fā)明的氧化裝置的整體結(jié)構(gòu)示意圖;圖2為本發(fā)明的氧化裝置的攪拌研磨單元的示意圖;圖3為本發(fā)明的攪拌研磨單元的仰視示意圖;圖4為本發(fā)明的實(shí)施例5的結(jié)構(gòu)示意圖;圖5為本發(fā)明的實(shí)施例6的結(jié)構(gòu)示意圖;圖6為本發(fā)明的實(shí)施例7的結(jié)構(gòu)示意圖;圖7為本發(fā)明的一種利用燒結(jié)煙氣脫硫副產(chǎn)物制備硫酸鈣晶須的方法的流程圖;圖8為本發(fā)明的實(shí)施例1制備的硫酸鈣晶須的掃描電鏡圖片;圖9為本發(fā)明的對(duì)比例1制備的硫酸鈣晶須的掃描電鏡圖片;圖10為現(xiàn)有技術(shù)制備的硫酸鈣晶須的掃描電鏡圖片。示意圖中的標(biāo)號(hào)說(shuō)明:100、氧化單元;110、氧化吹氣部件;111、底吹氣孔;120、錐形收集倉(cāng);130、研磨氧化腔體;131、弧形研磨段;132、研磨間隙段;133、間隙段吹氣孔;140、水浴加熱箱;200、攪拌研磨單元;210、驅(qū)動(dòng)電機(jī);220、電機(jī)驅(qū)動(dòng)軸;221、驅(qū)動(dòng)軸頂吹氣孔;230、葉片連接桿;231、連接桿頂吹氣孔;232、連接桿水平氣孔;240、攪拌研磨葉片;241、葉片倒角;242、葉片研磨圓弧。具體實(shí)施方式下文對(duì)本發(fā)明的示例性實(shí)施例的詳細(xì)描述參考了附圖,該附圖形成描述的一部分,在該附圖中作為示例示出了本發(fā)明可實(shí)施的示例性實(shí)施例。盡管這些示例性實(shí)施例被充分詳細(xì)地描述以使得本領(lǐng)域技術(shù)人員能夠?qū)嵤┍景l(fā)明,但應(yīng)當(dāng)理解可實(shí)現(xiàn)其他實(shí)施例且可在不脫離本發(fā)明的精神和范圍的情況下對(duì)本發(fā)明作各種改變。下文對(duì)本發(fā)明的實(shí)施例的更詳細(xì)的描述并不用于限制所要求的本發(fā)明的范圍,而僅僅為了進(jìn)行舉例說(shuō)明且不限制對(duì)本發(fā)明的特點(diǎn)和特征的描述,以提出執(zhí)行本發(fā)明的最佳方式,并足以使得本領(lǐng)域技術(shù)人員能夠?qū)嵤┍景l(fā)明。因此,本發(fā)明的范圍僅由所附權(quán)利要求來(lái)限定。下文對(duì)本發(fā)明的詳細(xì)描述和示例實(shí)施例可結(jié)合附圖來(lái)更好地理解,其中本發(fā)明的元件和特征由附圖標(biāo)記標(biāo)識(shí)。實(shí)施例1本發(fā)明的一種利用燒結(jié)煙氣脫硫副產(chǎn)物制備硫酸鈣晶須的方法,具體步驟如下:步驟一、去除雜質(zhì)采用100目的圓孔篩對(duì)脫硫副產(chǎn)物進(jìn)行水篩,并將大顆粒的雜質(zhì)去除,將脫硫副產(chǎn)物去雜后加入硫酸進(jìn)行酸洗,將酸洗液進(jìn)行真空抽濾得到脫硫副產(chǎn)物顆粒,對(duì)脫硫副產(chǎn)物顆粒進(jìn)行水洗2-4次,本實(shí)施例優(yōu)選3次,并得到呈中性的脫硫副產(chǎn)物溶液;其中所述的脫硫副產(chǎn)物為鐵礦燒結(jié)過(guò)程中燒結(jié)煙氣干法脫硫或者半干法脫硫的脫硫副產(chǎn)物,水洗過(guò)程中的水為去離子水。步驟二、低溫氧化將脫硫副產(chǎn)物溶液加入氧化裝置,向脫硫副產(chǎn)物溶液中吹入富氧空氣進(jìn)行吹氣氧化,吹氣氧化的過(guò)程中對(duì)脫硫副產(chǎn)物顆粒進(jìn)行間歇研磨,并控制脫硫副產(chǎn)物溶液的氧化溫度為90℃;更具體的說(shuō),吹氣氧化步驟如下:A、將脫硫副產(chǎn)物溶液加入氧化裝置之中,脫硫副產(chǎn)物在重力作用下下沉至底部的錐形收集倉(cāng)120中;B、氧化吹氣部件110將富氧空氣吹入氧化裝置,在富氧空氣的驅(qū)動(dòng)下,沉積在錐形收集倉(cāng)120的脫硫副產(chǎn)物顆粒運(yùn)動(dòng)至氧化裝置頂部的研磨氧化腔體130內(nèi),在攪拌研磨葉片240旋轉(zhuǎn)攪拌的作用下,脫硫副產(chǎn)物顆粒運(yùn)動(dòng)至研磨氧化腔體130的內(nèi)壁邊緣位置;C、在研磨氧化腔體130的內(nèi)壁邊緣對(duì)脫硫副產(chǎn)物顆粒進(jìn)行間歇研磨,間歇研磨為脫硫副產(chǎn)物顆粒運(yùn)動(dòng)至弧形研磨段131時(shí),研磨氧化腔體130的內(nèi)壁與攪拌研磨葉片240的葉片研磨圓弧242發(fā)生擠壓碰撞,脫硫副產(chǎn)物顆粒在弧形研磨段131的內(nèi)壁與葉片研磨圓弧242的擠壓、碰撞作用下,將脫硫副產(chǎn)物顆粒表面的難溶物研磨去除,研磨后的脫硫副產(chǎn)物顆粒在研磨間隙段132與葉片研磨圓弧242分離,富氧空氣將內(nèi)部的亞硫酸鈣氧化為硫酸鈣,而后脫硫副產(chǎn)物顆粒再次運(yùn)動(dòng)至弧形研磨段131時(shí)發(fā)生再次研磨、氧化。其中富氧空氣的溫度為150±5℃,150±5℃的氧化氣體為研磨氧化腔體130內(nèi)的脫硫副產(chǎn)物溶液進(jìn)行加熱,富氧空氣中的氧氣體積比為60%。表1脫硫副產(chǎn)物的氧化率樣品名稱(chēng)SO32-氧化率現(xiàn)有技術(shù)40.20%實(shí)施例178.52%在資源化利用脫硫副產(chǎn)物制備硫酸鈣晶須的過(guò)程中,不能直接利用亞硫酸鈣(CaSO3)制備硫酸鈣晶須,因此采用脫硫副產(chǎn)物進(jìn)行改性處理,其中所述的改性處理為對(duì)脫硫副產(chǎn)物進(jìn)行氧化處理,使得脫硫副產(chǎn)物中的亞硫酸鈣(CaSO3)轉(zhuǎn)化為硫酸鈣(CaSO4)。如表1所示,現(xiàn)有的氧化方法在氧化改性脫硫副產(chǎn)物時(shí),SO32-的氧化率僅為40.20%,致使SO32-的氧化率較低,并造成脫硫副產(chǎn)物的利用效率較差;而采用本實(shí)施例的氧化裝置,通過(guò)在氧化的過(guò)程中進(jìn)行間歇研磨,將脫硫副產(chǎn)物顆粒表面的難溶物研磨去除,即將附著在脫硫副產(chǎn)物顆粒表面的硫酸鈣在機(jī)械力研磨的作用下被研磨去除,使得顆粒內(nèi)部的亞硫酸鈣暴露在顆粒表面,促進(jìn)了氧氣分子與亞硫酸鈣表面的接觸,從而加快并促進(jìn)了顆粒內(nèi)部的亞硫酸鈣的氧化,并大大提高了脫硫副產(chǎn)物中硫酸鈣的氧化率,使得SO32-的氧化率達(dá)到78.52%,從而大大提高了脫硫副產(chǎn)物中硫酸鈣的純度,為后續(xù)生長(zhǎng)良好的晶須做好物質(zhì)基礎(chǔ)。步驟三、調(diào)配漿料將步驟二的脫硫副產(chǎn)物溶液進(jìn)行干燥得到脫硫副產(chǎn)物粉料,將脫硫副產(chǎn)物粉料與媒晶劑混合后向混合物中加入水,并控制固液比為1/8;加入稀硫酸調(diào)節(jié)PH為5.0,攪拌使其充分乳化制得漿料;步驟四、水熱反應(yīng)將上述得到的漿料加入反應(yīng)釜中,在140±5℃的密閉條件下進(jìn)行下反應(yīng)120min,并得到反應(yīng)產(chǎn)物;水熱反應(yīng)時(shí)的攪拌速度為15-25r/min,優(yōu)選20r/min。步驟五、水洗干燥對(duì)反應(yīng)產(chǎn)物水洗1-3次,優(yōu)選2次,水洗的過(guò)程中,用于水洗的水溫為90℃,抽濾得到濾餅,得到濾餅后采用無(wú)水乙醇對(duì)濾餅清洗,從而將脂溶性的雜質(zhì)去除;再將濾餅置于干燥箱中干燥,其中干燥箱的干燥溫度為90℃,干燥完成得到CaSO4晶須,制備得到的晶須如圖8所示。圖10為采用現(xiàn)有技術(shù)制備的硫酸鈣晶須的掃描電鏡圖片,由圖10可看出采用現(xiàn)有技術(shù)制備得到的硫酸鈣晶須粒徑粗大,硫酸鈣晶須表面附著較多顆粒,使得硫酸鈣晶須表面光潔程度較差,大大降低了硫酸鈣晶須的強(qiáng)度,使得制備得到的硫酸鈣晶須容易發(fā)生斷裂。圖8相對(duì)于圖10可以看出,采用本實(shí)施例的制備得到的硫酸鈣晶須直徑小于1μm,長(zhǎng)徑比到達(dá)80,硫酸鈣晶須的強(qiáng)度的理論強(qiáng)度達(dá)到0.02E-0.05E,表明光潔度較高,提高了硫酸鈣晶須的制備質(zhì)量,符合工業(yè)應(yīng)用要求,實(shí)現(xiàn)了脫硫副產(chǎn)物的高附加值應(yīng)用。對(duì)比例1本對(duì)比例的基本內(nèi)容同實(shí)施例1,不同之處在于:步驟五中水洗的過(guò)程中,用于水洗的水溫為室溫,即為20℃,抽濾得到濾餅,得到濾餅后采用無(wú)水乙醇對(duì)濾餅清洗,從而將脂溶性的雜質(zhì)去除;再將濾餅置于干燥箱中干燥,其中干燥箱的干燥溫度為90℃,干燥完成得到CaSO4晶須,制備得到的晶須如圖9所示。對(duì)比例1用于水洗的水溫為室溫制備得到的硫酸鈣晶須,由圖9與圖8對(duì)比看出,圖9表面具有少量的裂紋,硫酸鈣晶須表面附著少量顆粒,致使硫酸鈣晶須表面光潔程度有所降低,影響了硫酸鈣晶須的性能。但是,圖9相對(duì)于圖10仍然具有較高的質(zhì)量。對(duì)于該問(wèn)題,發(fā)明人在研究的過(guò)程中也非常詫異,但是產(chǎn)生該問(wèn)題的機(jī)理尚不清晰,為此申請(qǐng)人開(kāi)展多次研討會(huì),分析討論產(chǎn)生該問(wèn)題的反應(yīng)機(jī)理,并認(rèn)為產(chǎn)生該問(wèn)題的機(jī)理可能是由于水洗的水溫較低,使得制備得到的硫酸鈣晶須在水洗的過(guò)程中容易發(fā)生斷裂,使得在晶須表面出現(xiàn)裂紋,并使得較小的顆粒附著于晶須表面,致使使硫酸鈣晶須表面光潔程度有所降低。實(shí)施例2本實(shí)施例的氧化裝置包括氧化單元100和攪拌研磨單元200,其中氧化單元100包括氧化吹氣部件110、錐形收集倉(cāng)120和研磨氧化腔體130,其中氧化吹氣部件110位于研磨氧化腔體130的下部,氧化吹氣部件110用于向研磨氧化腔體130鼓入富氧空氣,氧化吹氣部件110內(nèi)安放有4-8層陶瓷球,優(yōu)選5層,陶瓷球促進(jìn)了富氧空氣的均勻分布;研磨氧化腔體130由弧形研磨段131和研磨間隙段132組成;上述的錐形收集倉(cāng)120為倒錐形,氧化吹氣部件110通過(guò)錐形收集倉(cāng)120與研磨氧化腔體130相連。氧化吹氣部件110上設(shè)置有底吹氣孔111,底吹氣孔111用于向研磨氧化腔體130內(nèi)吹入富氧空氣。將脫硫副產(chǎn)物溶液加入氧化裝置后,脫硫副產(chǎn)物在重力作用下下沉至底部,由于錐形收集倉(cāng)120為倒錐形,在重力作用下脫硫副產(chǎn)物顆?;易詣?dòng)的聚集在錐形收集倉(cāng)120中,氧化吹氣部件110將富氧空氣吹入氧化裝置,在富氧空氣的驅(qū)動(dòng)下,沉積在錐形收集倉(cāng)120的脫硫副產(chǎn)物顆粒運(yùn)動(dòng)至氧化裝置頂部的研磨氧化腔體130內(nèi),在攪拌研磨葉片240旋轉(zhuǎn)攪拌的作用下,脫硫副產(chǎn)物顆粒運(yùn)動(dòng)至研磨氧化腔體130的內(nèi)壁邊緣位置并發(fā)生氧化反應(yīng),部分脫硫副產(chǎn)物顆粒氧化后在重力作用下又再次聚集在下部的錐形收集倉(cāng)120中,下部的氧化吹氣部件110再次將脫硫副產(chǎn)物顆粒吹起,從而促進(jìn)了脫硫副產(chǎn)物顆粒的充分氧化。本實(shí)施例的攪拌研磨單元200包括電機(jī)驅(qū)動(dòng)軸220、葉片連接桿230、驅(qū)動(dòng)電機(jī)210和攪拌研磨葉片240,所述的驅(qū)動(dòng)電機(jī)210上設(shè)置有攪拌研磨葉片240,具體的說(shuō)明是:驅(qū)動(dòng)電機(jī)210通過(guò)電機(jī)驅(qū)動(dòng)軸220與葉片連接桿230相連,葉片連接桿230位于電機(jī)驅(qū)動(dòng)軸220下部,該葉片連接桿230上設(shè)置有攪拌研磨葉片240,攪拌研磨葉片240能以電機(jī)驅(qū)動(dòng)軸220為轉(zhuǎn)動(dòng)軸心轉(zhuǎn)動(dòng),該攪拌研磨葉片240的圓周上設(shè)置有葉片研磨圓弧242;上述的攪拌研磨葉片240位于研磨氧化腔體130內(nèi),且攪拌研磨葉片240的葉片研磨圓弧242與弧形研磨段131相配合,在驅(qū)動(dòng)電機(jī)210的驅(qū)動(dòng)下葉片研磨圓弧242與弧形研磨段131發(fā)生研磨運(yùn)動(dòng)。研磨氧化過(guò)程中,脫硫副產(chǎn)物顆粒氧化的過(guò)程中顆粒表面的亞硫酸鈣先與氧氣反應(yīng)生成硫酸鈣,由于硫酸鈣微溶于水溶液,亞硫酸鈣氧化生成硫酸鈣后附著于顆粒表面,阻止了氧氣分子向脫硫副產(chǎn)物顆粒內(nèi)部的擴(kuò)散傳質(zhì),從而阻礙了顆粒內(nèi)部的亞硫酸鈣的充分氧化;脫硫副產(chǎn)物顆粒運(yùn)動(dòng)至弧形研磨段131時(shí),研磨氧化腔體130的內(nèi)壁與攪拌研磨葉片240的葉片研磨圓弧242發(fā)生擠壓碰撞,脫硫副產(chǎn)物顆粒在弧形研磨段131的內(nèi)壁與葉片研磨圓弧242的擠壓、碰撞作用下,將脫硫副產(chǎn)物顆粒表面的難溶物研磨去除,即將附著在脫硫副產(chǎn)物顆粒表面的硫酸鈣在機(jī)械力研磨的作用下被研磨去除,使得顆粒內(nèi)部的亞硫酸鈣暴露在顆粒表面,促進(jìn)了氧氣分子與亞硫酸鈣表面的接觸,從而加快并促進(jìn)了顆粒內(nèi)部的亞硫酸鈣的氧化。脫硫副產(chǎn)物始終處于研磨的過(guò)程中,則由于研磨的過(guò)程中攪拌研磨葉片240與研磨氧化腔體130內(nèi)壁之間的間隙較小,研磨過(guò)程中富氧空氣的氣泡難以進(jìn)入攪拌研磨葉片240與研磨氧化腔體130內(nèi)壁之間的間隙之中,使得在研磨過(guò)程中,脫硫副產(chǎn)物顆粒難以與氧結(jié)合發(fā)生氧化反應(yīng)。研磨后的脫硫副產(chǎn)物顆粒在研磨間隙段132與葉片研磨圓弧242分離,富氧空氣將內(nèi)部的亞硫酸鈣氧化為硫酸鈣,而后脫硫副產(chǎn)物顆粒再次運(yùn)動(dòng)至弧形研磨段131時(shí)發(fā)生再次研磨、氧化。發(fā)明人創(chuàng)新的提出的間歇研磨大大提高了氧化過(guò)程的氧化效率,即將附著于氧化物表面的硫酸鈣研磨去除后,脫硫副產(chǎn)物顆粒盡快與攪拌研磨葉片240分離,從而促進(jìn)了脫硫副產(chǎn)物顆粒與氧氣的接觸,加快了氧化效率。本實(shí)施例的弧形研磨段131與攪拌研磨葉片240轉(zhuǎn)動(dòng)軸心的距離等于弧形研磨段131與攪拌研磨葉片240轉(zhuǎn)動(dòng)軸心的距離,該轉(zhuǎn)動(dòng)軸心即為電機(jī)驅(qū)動(dòng)軸220的軸心,且弧形研磨段131的圓弧半徑與葉片研磨圓弧242的圓弧半徑相同,所述的研磨間隙段132與攪拌研磨葉片240轉(zhuǎn)動(dòng)軸心的距離大于弧形研磨段131與攪拌研磨葉片240轉(zhuǎn)動(dòng)軸心的距離。本實(shí)施中研磨氧化腔體130的橫截面為橢圓形,所述的橢圓形的短軸頂點(diǎn)處為弧形研磨段131,在橢圓形的短軸頂點(diǎn)處攪拌研磨葉片240與研磨氧化腔體130相接處,葉片研磨圓弧242與弧形研磨段131發(fā)生相對(duì)運(yùn)動(dòng),并對(duì)脫硫副產(chǎn)物顆粒產(chǎn)生擠壓力,將脫硫副產(chǎn)物顆粒擠壓破碎,葉片研磨圓弧242離開(kāi)橢圓形的短軸頂點(diǎn)處即進(jìn)入研磨間隙段132,此時(shí)脫硫副產(chǎn)物顆粒與葉片研磨圓弧242分離,并發(fā)生氧化反應(yīng)。實(shí)施例3本實(shí)施例的基本內(nèi)容同實(shí)施例2,不同之處在于:攪拌研磨葉片240上設(shè)置有葉片倒角241,在研磨氧化的過(guò)程中,在攪拌研磨葉片240驅(qū)動(dòng)下,脫硫副產(chǎn)物顆粒運(yùn)動(dòng)至弧形研磨段131與葉片倒角241之間的間隙,后續(xù)的運(yùn)動(dòng)過(guò)程中,脫硫副產(chǎn)物顆粒繼續(xù)運(yùn)動(dòng)至弧形研磨段131與葉片研磨圓弧242之間,而后脫硫副產(chǎn)物顆粒進(jìn)行機(jī)械研磨,葉片倒角241促進(jìn)了脫硫副產(chǎn)物顆粒進(jìn)行機(jī)械研磨。實(shí)施例4本實(shí)施例的基本內(nèi)容同實(shí)施例2,不同之處在于:電機(jī)驅(qū)動(dòng)軸220底部設(shè)置有驅(qū)動(dòng)軸頂吹氣孔221(如圖3所示),研磨氧化的過(guò)程中驅(qū)動(dòng)軸頂吹氣孔221同樣可以將富氧空氣吹入研磨氧化腔體130,且驅(qū)動(dòng)軸頂吹氣孔221與底吹氣孔111的幾何中心位于同一條軸線(xiàn)上,驅(qū)動(dòng)軸頂吹氣孔221和底吹氣孔111的共同作用下,脫硫副產(chǎn)物顆粒及液體不斷的由研磨氧化腔體130的中心運(yùn)動(dòng)至研磨氧化腔體130的弧形研磨段131,促使著脫硫副產(chǎn)物顆粒在弧形研磨段131發(fā)生機(jī)械研磨,從而加速了脫硫副產(chǎn)物顆粒的氧化效果。值得進(jìn)一步說(shuō)明的是,葉片連接桿230的底部設(shè)置有連接桿頂吹氣孔231,該連接桿頂吹氣孔231吹氣方向向下,即氣流由上至下進(jìn)入脫硫副產(chǎn)物溶液(如圖2所示);另外,葉片連接桿230的側(cè)面上設(shè)置有連接桿水平氣孔232,該連接桿水平氣孔232的出氣方向平行于水平面,連接桿水平氣孔232噴入的富氧空氣,不僅促進(jìn)了脫硫副產(chǎn)物顆粒與氧氣分子的混合,而且促使著脫硫副產(chǎn)物顆粒隨水流運(yùn)動(dòng)至研磨氧化腔體130的邊緣位置,加速了脫硫副產(chǎn)物顆粒的研磨、氧化過(guò)程。實(shí)施例5如圖4所示,本實(shí)施例的基本內(nèi)容同實(shí)施例2,不同之處在于:本實(shí)施例研磨氧化腔體130由2個(gè)弧形研磨段131和2個(gè)研磨間隙段132組成,其中研磨間隙段132為矩形槽狀。實(shí)施例6如圖5所示,本實(shí)施例的基本內(nèi)容同實(shí)施例2,不同之處在于:本實(shí)施例研磨氧化腔體130由4個(gè)弧形研磨段131和4個(gè)研磨間隙段132組成,其中研磨間隙段132為矩形槽狀,且研磨間隙段132內(nèi)上設(shè)置有間隙段吹氣孔133,該間隙段吹氣孔133向研磨氧化腔體130同時(shí)吹入富氧空氣,間隙段吹氣孔133的吹氣流量小于底吹氣孔111的吹氣流量;防止脫硫副產(chǎn)物顆粒在研磨間隙段132停留時(shí)間過(guò)長(zhǎng),從而促進(jìn)脫硫顆粒氧化和研磨。實(shí)施例7如圖6所示,本實(shí)施例的基本內(nèi)容同實(shí)施例2,不同之處在于:本實(shí)施例的研磨氧化腔體130外部設(shè)置有水浴加熱箱140,該水浴加熱箱140用于為研磨氧化腔體130進(jìn)行水浴加熱。實(shí)施例8本實(shí)施例的一種利用燒結(jié)煙氣脫硫副產(chǎn)物制備硫酸鈣晶須的方法,具體步驟如下:步驟一、去除雜質(zhì)將脫硫副產(chǎn)物去雜后加入硫酸進(jìn)行酸洗,將酸洗液進(jìn)行真空抽濾得到脫硫副產(chǎn)物顆粒,對(duì)脫硫副產(chǎn)物顆粒進(jìn)行4次水洗,并得到呈中性的脫硫副產(chǎn)物溶液;步驟二、低溫氧化將脫硫副產(chǎn)物溶液加入氧化裝置,向脫硫副產(chǎn)物溶液中吹入富氧空氣進(jìn)行吹氣氧化,吹氣氧化的過(guò)程中對(duì)脫硫副產(chǎn)物顆粒進(jìn)行間歇研磨,并控制脫硫副產(chǎn)物溶液的氧化溫度為80℃;其中富氧空氣的溫度為80±5℃,并輔助水浴加熱,水浴加熱箱140為研磨氧化腔體130內(nèi)的脫硫副產(chǎn)物溶液進(jìn)行加熱,富氧空氣中的氧氣體積比為40%,吹氣氧化的時(shí)間為3h。步驟三、調(diào)配漿料將步驟二的脫硫副產(chǎn)物溶液進(jìn)行干燥得到脫硫副產(chǎn)物粉料,將脫硫副產(chǎn)物粉料與媒晶劑混合后向混合物中加入水,并控制固液比為1/6;加入稀硫酸調(diào)節(jié)PH為3.5,攪拌使其充分乳化制得漿料;其中脫硫副產(chǎn)物中還加入有媒晶劑,每50g脫硫副產(chǎn)物中媒晶劑的加入量為0.5g,所述的媒晶劑為氯化鎂。步驟四、水熱反應(yīng)將上述得到的漿料加入反應(yīng)釜中,在120±5℃的密閉條件下進(jìn)行下反應(yīng)60min,并得到反應(yīng)產(chǎn)物;水熱反應(yīng)時(shí)的攪拌速度為15-25r/min,優(yōu)選20r/min。步驟五、水洗干燥對(duì)反應(yīng)產(chǎn)物水洗1-3次,優(yōu)選2次,水洗的過(guò)程中,用于水洗的水溫為80℃,抽濾得到濾餅,得到濾餅后采用無(wú)水乙醇對(duì)濾餅清洗,從而將硅油等有機(jī)雜質(zhì)去除;再將濾餅置于干燥箱中干燥,其中干燥箱的干燥溫度為80℃,干燥完成得到CaSO4晶須,此時(shí)得到的CaSO4晶須以二水硫酸鈣為主,若需制備半水硫酸鈣,則需在500-600℃焙燒4-6h。實(shí)施例9本實(shí)施例的一種利用燒結(jié)煙氣脫硫副產(chǎn)物制備硫酸鈣晶須的方法,具體步驟如下:步驟一、去除雜質(zhì)將脫硫副產(chǎn)物去雜后加入硫酸進(jìn)行酸洗,將酸洗液進(jìn)行真空抽濾得到脫硫副產(chǎn)物顆粒,對(duì)脫硫副產(chǎn)物顆粒進(jìn)行水洗2次,并得到呈中性的脫硫副產(chǎn)物溶液;步驟二、低溫氧化將脫硫副產(chǎn)物溶液加入氧化裝置,向脫硫副產(chǎn)物溶液中吹入富氧空氣進(jìn)行吹氣氧化,吹氣氧化的過(guò)程中對(duì)脫硫副產(chǎn)物顆粒進(jìn)行間歇研磨,并控制脫硫副產(chǎn)物溶液的氧化溫度為50℃;其中富氧空氣的溫度為60±5℃,60±5℃的氧化氣體為研磨氧化腔體130內(nèi)的脫硫副產(chǎn)物溶液進(jìn)行加熱,并輔助水浴加熱,水浴加熱箱140為研磨氧化腔體130內(nèi)的脫硫副產(chǎn)物溶液進(jìn)行加熱,富氧空氣中的氧氣體積比為50%,吹氣氧化時(shí)間為3h。步驟三、調(diào)配漿料將步驟二的脫硫副產(chǎn)物溶液進(jìn)行干燥得到脫硫副產(chǎn)物粉料,將脫硫副產(chǎn)物粉料與媒晶劑混合后向混合物中加入水,并控制固液比為1/10;加入稀硫酸調(diào)節(jié)PH為5.3,攪拌使其充分乳化制得漿料;其中脫硫副產(chǎn)物中還加入有媒晶劑,每50g脫硫副產(chǎn)物中媒晶劑的加入量為0.2g,所述的媒晶劑由氯化鎂和硫酸鉀組成,其中各組分的質(zhì)量百分比為:氯化鎂:60%,硫酸鉀:40%。步驟四、水熱反應(yīng)將上述得到的漿料加入反應(yīng)釜中,在150±5℃的密閉條件下進(jìn)行下反應(yīng)180min,并得到反應(yīng)產(chǎn)物;水熱反應(yīng)時(shí)的攪拌速度為15-25r/min,優(yōu)選20r/min。步驟五、水洗干燥對(duì)反應(yīng)產(chǎn)物水洗1-3次,優(yōu)選2次,水洗的過(guò)程中,用于水洗的水溫為95℃,抽濾得到濾餅,得到濾餅后采用無(wú)水乙醇對(duì)濾餅清洗,從而將硅油等有機(jī)雜質(zhì)去除;再將濾餅置于干燥箱中干燥,其中干燥箱的干燥溫度為60℃,干燥完成得到CaSO4晶須。在上文中結(jié)合具體的示例性實(shí)施例詳細(xì)描述了本發(fā)明。但是,應(yīng)當(dāng)理解,可在不脫離由所附權(quán)利要求限定的本發(fā)明的范圍的情況下進(jìn)行各種修改和變型。詳細(xì)的描述和附圖應(yīng)僅被認(rèn)為是說(shuō)明性的,而不是限制性的,如果存在任何這樣的修改和變型,那么它們都將落入在此描述的本發(fā)明的范圍內(nèi)。此外,
背景技術(shù):
旨在為了說(shuō)明本技術(shù)的研發(fā)現(xiàn)狀和意義,并不旨在限制本發(fā)明或本申請(qǐng)和本發(fā)明的應(yīng)用領(lǐng)域。值得進(jìn)一步說(shuō)明的是,媒晶劑也可以為硫酸鎂、氯化鎂、硫酸鉀、氯化鉀其中的一種或者兩種以上的組合。更具體地,盡管在此已經(jīng)描述了本發(fā)明的示例性實(shí)施例,但是本發(fā)明并不局限于這些實(shí)施例,而是包括本領(lǐng)域技術(shù)人員根據(jù)前面的詳細(xì)描述可認(rèn)識(shí)到的經(jīng)過(guò)修改、省略、(例如各個(gè)實(shí)施例之間的)組合、適應(yīng)性改變和/或替換的任何和全部實(shí)施例。權(quán)利要求中的限定可根據(jù)權(quán)利要求中使用的語(yǔ)言而進(jìn)行廣泛的解釋?zhuān)也幌抻谠谇笆鲈敿?xì)描述中或在實(shí)施該申請(qǐng)期間描述的示例,這些示例應(yīng)被認(rèn)為是非排他性的。例如,在本發(fā)明中,術(shù)語(yǔ)“優(yōu)選地”不是排他性的,這里它的意思是“優(yōu)選地,但是并不限于”。在任何方法或過(guò)程權(quán)利要求中列舉的任何步驟可以以任何順序執(zhí)行并且不限于權(quán)利要求中提出的順序。因此,本發(fā)明的范圍應(yīng)當(dāng)僅由所附權(quán)利要求及其合法等同物來(lái)確定,而不是由上文給出的說(shuō)明和示例來(lái)確定。當(dāng)前第1頁(yè)1 2 3