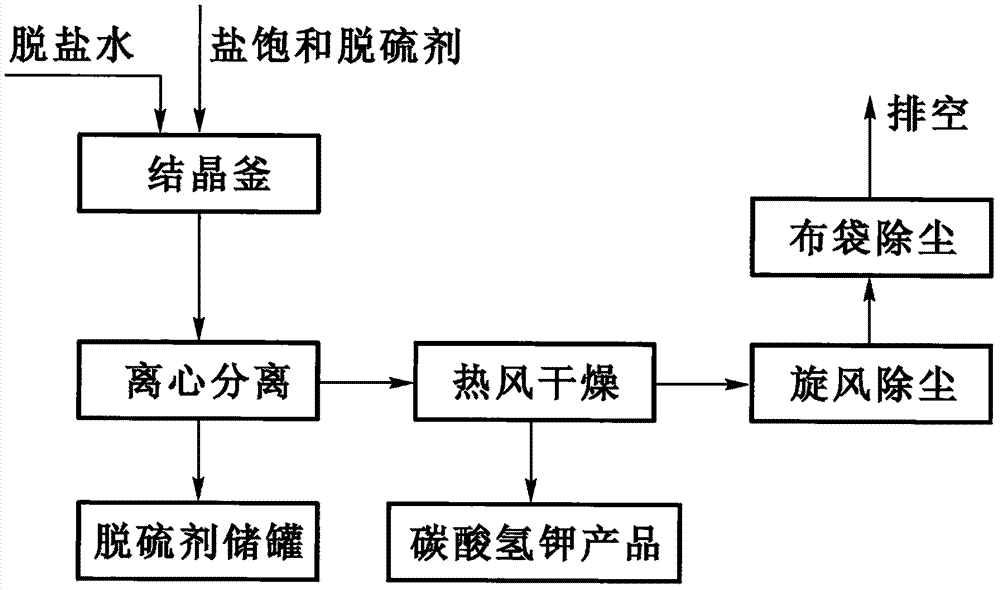
本發(fā)明涉及硫化氫處理工藝領(lǐng)域,尤其是一種濕法氧化硫化氫制硫磺循環(huán)經(jīng)濟(jì)工藝。
背景技術(shù):
:濕法氧化硫化氫制硫磺為由堿性吸收液吸收硫化氫制備硫磺,其中絡(luò)合鐵氧化還原法處理硫化氫并回收硫磺的工藝,采用了以絡(luò)合鐵為主要成分的液體脫硫劑,其主要用來(lái)脫除天然氣、油田伴生氣、水煤氣、煉焦?fàn)t氣中的劇毒、惡臭的硫化氫氣體,適宜于潛硫量低于10t/d、且酸氣中多共存大量二氧化碳的氣體處理。其工藝原理是:1)堿性水溶液與h2s反應(yīng)生成hs-h2s+co32-(oh-)→hs-+hco3-(h2o)(反應(yīng)式1)co2+co32-+h2o=2hco3-(反應(yīng)式2)2)液體脫硫劑中fe-l與hs-反應(yīng)生成過(guò)渡態(tài)hs-+2fe-l→2fe-(hs)-l(反應(yīng)式3)3)液體脫硫劑的再生及硫磺的生成2fe-(hs)-l+1/2o2(g)→2fe-l+oh-+2s(反應(yīng)式4)由以上工藝原理可見(jiàn):(1)由硫化氫氧化為硫單質(zhì)時(shí),不會(huì)消耗堿,但需要在堿性環(huán)境中(ph=9-10)進(jìn)行;(2)酸氣中共存的二氧化碳,幾乎被完全吸收,見(jiàn)表1。吸收二氧化碳需要消耗大量的堿,成本高昂,見(jiàn)表2,需要想辦法降低成本。表1ph值對(duì)h2s吸收轉(zhuǎn)化及co2吸收的影響ph值8.08.59.09.5剩余ω(h2s)7.7%3.3%0.77%0.00h2s吸收百分率92.3%96.7%99.23%100%剩余ω(co2)2.3%0.74%0.23%0.00co2吸收百分率97.7%99.26%99.77%100%表2噸硫磺藥劑成本與酸氣中二氧化碳含量的關(guān)系及相應(yīng)副鹽產(chǎn)量(3)副產(chǎn)的碳酸氫(鈉)鉀在脫硫劑中飽和后,會(huì)不斷析出,造成兩種危害,一是混入硫磺中降低硫磺品質(zhì)(鹽含量不低于30%),無(wú)法進(jìn)入市場(chǎng)銷售;二是在氣體噴嘴、管道、液泵處結(jié)垢,出現(xiàn)堵泵、積液等嚴(yán)重問(wèn)題,影響工藝平穩(wěn)運(yùn)行。所以一旦鹽飽和后,需要更換脫硫劑,大大增加了藥劑成本。目前很多工藝采用碳酸鈉作為脫硫劑ph調(diào)節(jié)劑,為了降低成本,有些工藝采用沉淀池結(jié)晶回收碳酸氫鈉,然后堿中和為碳酸鈉回用的辦法,雖然降低了藥劑成本,但由于碳酸氫鈉溶解度很小(17.0g,60℃),且隨溫度的降低溶解度變化不大(11.0g,20℃),見(jiàn)附圖3。冷卻到室溫后一噸脫硫劑析出的碳酸氫鈉僅為60kg,析鹽再生后的脫硫劑一經(jīng)運(yùn)行又快速達(dá)到飽和狀態(tài),需要頻繁更換脫硫劑進(jìn)行脫鹽操作,工藝難度加大,這不僅需要很大的沉淀池(貧液槽),而且需要消耗大量的中和用堿以及泵送、制冷等需要大量的電能,成本依然高企。若將生成的碳酸氫鈉,通過(guò)焙燒法再生為碳酸鈉(反應(yīng)式5),可以基本平衡堿的消耗。由于回收工藝執(zhí)行的難度很大,所以實(shí)際很少采用焙燒法再生碳酸鈉,從而無(wú)法有效降低藥劑成本。當(dāng)前硫磺回收工藝多采用koh作為脫硫劑ph調(diào)節(jié)劑,由于碳酸氫鉀的溶解度(67.0,60℃)是碳酸氫鈉的3.94倍,可以延長(zhǎng)脫硫劑的鹽飽和周期接近4倍,見(jiàn)附圖3;加之碳酸氫鉀隨溫度的降低溶解度變化很大(35.0g,20℃),冷卻到室溫后一噸脫硫劑可析出的碳酸氫鉀為320kg,從這個(gè)角度看,可以延長(zhǎng)脫硫劑的鹽飽和周期5.3倍,可以有效抑制鹽的結(jié)晶問(wèn)題。由于很多脫硫工藝并未采用結(jié)晶脫鹽的辦法,硫磺中鹽含量始終無(wú)法得到有效解決,藥劑成本也一直居高不下,甚至高達(dá)7850元/噸硫磺。成本之高往往使很多企業(yè)即便建設(shè)了硫磺回收裝置,也不能正常開(kāi)工,而是采用直接通過(guò)火炬燃燒生成二氧化硫排放,帶來(lái)嚴(yán)重的大氣污染問(wèn)題。隨著環(huán)保法的實(shí)施,必須尋求經(jīng)濟(jì)可行的硫化氫治理辦法。技術(shù)實(shí)現(xiàn)要素:有鑒于此,本發(fā)明的目的是提供一種濕法氧化硫化氫制硫磺循環(huán)經(jīng)濟(jì)工藝,實(shí)現(xiàn)堿的自我平衡供給,提高硫磺品質(zhì),減少堵泵、堵氣體噴嘴的停工檢修,以及更換脫硫劑帶來(lái)的成本和環(huán)境問(wèn)題。為達(dá)上述目的,本發(fā)明采用的技術(shù)方案如下:一種濕法氧化硫化氫制硫磺循環(huán)經(jīng)濟(jì)工藝,包括以下步驟:a.在濕法氧化硫化氫制硫磺過(guò)程中,以碳酸鉀作為液體脫硫劑的ph調(diào)節(jié)劑,反應(yīng)后得到碳酸氫鉀和液體脫硫劑的混合物,所述碳酸氫鉀溶解于液體脫硫劑中;b.所述碳酸氫鉀和液體脫硫劑的混合物通過(guò)冷卻降溫得到碳酸氫鉀的結(jié)晶鹽和混合物1,所述混合物1包含液體脫硫劑和殘留的溶解于液體脫硫劑中的碳酸氫鉀;c.所述碳酸氫鉀的結(jié)晶鹽通過(guò)離心固液分離,得到固體碳酸氫鉀;d.所述固體碳酸氫鉀通過(guò)煅燒得到碳酸鉀。優(yōu)選地,步驟a所述液體脫硫劑ph值控制在9~10。優(yōu)選地,步驟a所述液體脫硫劑ph值控制在9.5。優(yōu)選地,所述液體脫硫劑主要由絡(luò)合鐵組成。優(yōu)選地,步驟a所述液體脫硫劑密度控制在1.02~1.05g/cm3。優(yōu)選地,所述混合物1用碳酸鉀調(diào)節(jié)ph值后送入脫硫劑儲(chǔ)罐,供下次濕法氧化硫化氫制硫磺使用。優(yōu)選地,所述濕法氧化硫化氫制硫磺為絡(luò)合鐵法、酞菁鈷磺酸鹽法或改良蒽醌二磺酸鈉法。本發(fā)明的濕法氧化硫化氫制硫磺循環(huán)經(jīng)濟(jì)工藝通過(guò)以碳酸鉀為脫硫劑的ph調(diào)節(jié)劑,并將副產(chǎn)物碳酸氫鉀通過(guò)冷卻結(jié)晶法過(guò)濾回收,回收的碳酸氫鉀通過(guò)煅燒再生成碳酸鉀的循環(huán)經(jīng)濟(jì)工藝,不僅可以實(shí)現(xiàn)堿的自我平衡供給,在保證處理效率的前提下使藥劑成本降低95%,綜合成本降低80%,單位硫磺處理成本降低至1000元/t以下;還能提高硫磺品質(zhì),使硫磺含量≥90%,并能夠減少由于脫硫劑析鹽導(dǎo)致的堵泵、堵氣體噴嘴停工檢修、脫硫劑更換帶來(lái)的環(huán)境問(wèn)題。本發(fā)明是一條循環(huán)經(jīng)濟(jì)的、綠色的、可持續(xù)的濕法氧化硫化氫處理工藝,有重要的應(yīng)用價(jià)值和現(xiàn)實(shí)意義。附圖說(shuō)明通過(guò)以下參照附圖對(duì)本發(fā)明實(shí)施例的描述,本發(fā)明的上述以及其它目的、特征和優(yōu)點(diǎn)將更為清楚,在附圖中:圖1示出硫磺回收裝置流程圖;圖2示出碳酸鉀回收及煅燒再生工藝;圖3示出鹽的溶解度曲線。具體實(shí)施方式以下基于實(shí)施例對(duì)本發(fā)明進(jìn)行描述,但是本發(fā)明并不僅僅限于這些實(shí)施例。文中碳酸氫鉀是指溶解后的碳酸氫鉀,碳酸氫鉀結(jié)晶鹽是碳酸氫鉀析出的結(jié)晶。本發(fā)明提供一種濕法氧化硫化氫制硫磺循環(huán)經(jīng)濟(jì)工藝,包括以下步驟:a.在濕法氧化硫化氫制硫磺過(guò)程中,以碳酸鉀作為液體脫硫劑的ph調(diào)節(jié)劑,反應(yīng)后得到碳酸氫鉀和液體脫硫劑的混合物,所述碳酸氫鉀溶解于液體脫硫劑中。濕法氧化硫化氫制硫磺為一種常用的硫化氫制硫磺工藝,液體脫硫劑與硫化氫的反應(yīng)原理為現(xiàn)有技術(shù),故不再解釋,碳酸鉀與硫化氫、二氧化碳的中和反應(yīng)原理如下:h2s+k2co3→khs+khco3(反應(yīng)式5)co2+k2co3+h2o=2khco3(反應(yīng)式6)碳酸鉀在作為液體脫硫劑的ph調(diào)節(jié)劑,與硫化氫、二氧化碳反應(yīng),將硫化氫中的硫轉(zhuǎn)變?yōu)閔s-,自身生成碳酸氫鉀,由于碳酸氫鉀的溶解度(67.0g,60℃),碳酸氫鈉溶解度(17.0g,60℃),碳酸氫鉀溶解度是碳酸氫鈉的3.94倍,因此,液體脫硫劑中可溶解更多的碳酸氫鉀,延長(zhǎng)液體脫硫劑的鹽飽和周期接近4倍,選用碳酸鉀作為脫硫劑的ph調(diào)節(jié)劑,不選用碳酸鈉或氫氧化鉀,不僅有利于控制液體脫硫劑的ph值和酸緩沖容量,還能延長(zhǎng)液體脫硫劑中碳酸氫鉀的飽和析鹽周期,即液體脫硫劑中溶解碳酸氫鉀達(dá)到飽和狀態(tài)的時(shí)間,選擇碳酸鉀做液體脫硫劑的ph調(diào)節(jié)劑可以延長(zhǎng)液體脫硫劑飽和析鹽周期5.3倍(與碳酸鈉比),有效抑制液體脫硫劑中ph調(diào)節(jié)劑過(guò)早結(jié)晶。上述過(guò)程中還包含了液體脫硫劑氧化硫化氫得到并分離出硫磺的過(guò)程,屬于現(xiàn)有技術(shù)。b.所述碳酸氫鉀和液體脫硫劑的混合物通過(guò)冷卻降溫得到碳酸氫鉀的結(jié)晶鹽和混合物1,所述混合物1包含液體脫硫劑和殘留的溶解于液體脫硫劑中的碳酸氫鉀,此時(shí)液體脫硫劑中溶解的碳酸氫鉀為飽和狀態(tài)。冷卻降溫的手段可以是自然冷卻降溫,也可采用降溫設(shè)備,降溫方式可采用梯度降溫、急速降溫等。原理如圖3所示,碳酸氫鉀隨溫度的降低溶解度變化很大,碳酸氫鉀溶解度在20℃時(shí)為35.0g,因此通過(guò)冷卻降溫的辦法,將含碳酸氫鉀的脫硫劑從60℃降溫至20℃,碳酸氫鉀將以鹽結(jié)晶的形式析出,同時(shí),碳酸氫鉀會(huì)殘留部分溶解于液體脫硫劑中。冷卻到室溫后一噸液體脫硫劑可析出的碳酸氫鉀為320kg。c.所述碳酸氫鉀的結(jié)晶鹽通過(guò)離心固液分離,得到固體碳酸氫鉀,如圖2所示。d.所述固體碳酸氫鉀通過(guò)煅燒得到碳酸鉀。采用200℃熱空氣煅燒分解生產(chǎn),見(jiàn)反應(yīng)式7。將回收的固體碳酸氫鉀煅燒制碳酸鉀,制備的碳酸鉀可以基本補(bǔ)充步驟a中碳酸鉀的消耗,無(wú)須再外購(gòu)碳酸鉀,吸收二氧化碳消耗的大量碳酸鉀將完全得到再生,同時(shí),在煅燒過(guò)程中吸收的二氧化碳又釋放出來(lái),可直排入大氣,不會(huì)帶來(lái)環(huán)境污染問(wèn)題。進(jìn)一步地,步驟a所述液體脫硫劑ph值控制在9~10。ph值低于9時(shí),h2s吸收效率不高,ph值高于10時(shí),液體脫硫劑中主要成分生成沉淀概率增大,并且hs-轉(zhuǎn)化為s2-,將無(wú)法與液體脫硫劑反應(yīng),脫硫體系被改變。優(yōu)選地,步驟a所述液體脫硫劑ph值控制在9.5,當(dāng)ph值為9.5時(shí),h2s可100%被吸收,吸收效率最佳。ph值控制可以通過(guò)ph測(cè)定控制儀控制,也可以通過(guò)人工添加碳酸鉀控制。更進(jìn)一步地,液體脫硫劑主要由絡(luò)合鐵組成。絡(luò)合鐵能夠與hs-結(jié)合生成絡(luò)合物。為了防止碳酸氫鉀在液體脫硫劑中過(guò)飽和,步驟a所述液體脫硫劑密度控制在1.02~1.05g/cm3,液體脫硫劑中溶解的碳酸氫鉀可以是飽和狀態(tài),也可以是接近飽和的狀態(tài),以飽和狀態(tài)最佳。通過(guò)監(jiān)測(cè)步驟a中液體脫硫劑的密度,可以推測(cè)溶解的碳酸氫鉀的含量,以便及時(shí)將接近飽和的液體脫硫劑送入再生系統(tǒng)。監(jiān)測(cè)液體脫硫劑的密度可以通過(guò)密度監(jiān)控設(shè)備監(jiān)控。液體脫硫劑脫除碳酸氫鉀結(jié)晶鹽后可回收使用,進(jìn)一步地,在20℃下,步驟c之后的混合物1中溶解的碳酸氫鉀為飽和狀態(tài),將混合物1用碳酸鉀調(diào)節(jié)ph值(9~10)后送入脫硫劑儲(chǔ)罐,在下一循環(huán)的濕法氧化硫化氫制硫磺過(guò)程中,溫度將升至60℃,混合物1再次變?yōu)椴伙柡蜖顟B(tài),能夠重新溶解碳酸氫鉀?;旌衔?中的液體脫硫劑在循環(huán)期間總量保持不變,至少能夠循環(huán)使用三個(gè)月,因此無(wú)需經(jīng)常更換脫硫劑,大大降低了硫磺回收單元的脫硫劑成本,更顯著降低了排放脫硫劑導(dǎo)致的環(huán)境污染。循環(huán)過(guò)程中,碳酸鉀變?yōu)樘妓釟溻浐蠼?jīng)轉(zhuǎn)換再次變?yōu)樘妓徕浭褂?。另外為提高硫磺品質(zhì),工藝中可增加熔硫釜,降低雜質(zhì)含量。更進(jìn)一步地,濕法氧化硫化氫制硫磺工藝可以是絡(luò)合鐵法、酞菁鈷磺酸鹽法、改良蒽醌二磺酸鈉法等制硫磺工藝。碳酸鉀本來(lái)是脫硫劑ph調(diào)節(jié)劑的一個(gè)選項(xiàng),多次在專利和文獻(xiàn)中提及,但實(shí)際應(yīng)用很少。原因可能是由于碳酸鉀(5800元/t)價(jià)格比碳酸鈉(2200元/t)貴2.64倍,并且普遍忽視脫硫劑析鹽帶來(lái)的問(wèn)題。后來(lái)選用koh,就是注意到了脫硫劑析鹽的問(wèn)題,但對(duì)析出的鹽——碳酸氫鉀卻沒(méi)有解決辦法。唯有選用碳酸鉀,才能實(shí)現(xiàn)堿的閉路循環(huán),基本平衡堿的消耗,同時(shí)可以大大延長(zhǎng)脫硫劑的使用壽命、延長(zhǎng)脫硫單元的正常運(yùn)行周期,從而大大降低處理成本。下面以一單元化內(nèi)外筒絡(luò)合鐵、硫化氫處理工藝為基礎(chǔ)列舉本發(fā)明的實(shí)施例和對(duì)比例,一單元化內(nèi)外筒絡(luò)合鐵、硫化氫處理工藝如圖1所示。原來(lái)脫硫過(guò)程分兩步進(jìn)行,一個(gè)硫化氫吸收塔,一個(gè)脫硫劑再生塔,內(nèi)外筒結(jié)構(gòu)是吸收和再生在同一個(gè)釜內(nèi)完成,硫化氫吸收在內(nèi)筒,硫磺在外筒生成,并在內(nèi)外筒間循環(huán),典型工藝就是lo-cat工藝。實(shí)施例1選用一單元化內(nèi)外筒循環(huán)吸收氧化絡(luò)合鐵硫化氫處理工藝,以k2co3作為ph值調(diào)節(jié)劑(ph=9.5),酸氣組成為硫化氫72%、二氧化碳28%,酸氣流速61.3kg/h,處理溫度60℃,硫磺產(chǎn)量1.0t/d,硫磺回收率99%,k2co3消耗1266kg/t(硫磺),處理鹽飽和脫硫劑貧液(混合物1)5.8t,回收碳酸氫鉀1784kg/t(硫磺),煅燒得碳酸鉀1202kg/t(硫磺),回收率95.0%。回收再生的碳酸鉀可以基本平衡堿的消耗。處理成本約900元/t(硫磺)。對(duì)比例1選用一單元化內(nèi)外筒循環(huán)吸收氧化絡(luò)合鐵硫化氫處理工藝,以碳酸鈉為ph調(diào)節(jié)劑(ph=9.5),酸氣組成為硫化氫72%、二氧化碳28%,酸氣流速61.3kg/h,處理溫度60℃,硫磺產(chǎn)量1.0t/d,硫磺回收率94%,碳酸鈉消耗987kg/t(硫磺),處理鹽飽和脫硫液貧液(液體脫硫劑和殘留的溶解于液體脫硫劑的碳酸氫鈉)7.3t/t(硫磺),回收煅燒再生碳酸鈉400kg,回收率91.5%。綜合處理成本2800元/t(硫磺)。對(duì)比例2選用一單元化內(nèi)外筒循環(huán)吸收氧化絡(luò)合鐵硫化氫處理工藝,以koh作為ph調(diào)節(jié)劑(ph=9.5),酸氣組成為硫化氫72%、二氧化碳28%,酸氣流速61.3kg/h,處理溫度60℃,硫磺產(chǎn)量1.0t/d,硫磺回收率99%,koh消耗522kg/t(硫磺),處理鹽飽和脫硫液貧液(液體脫硫劑和殘留的溶解于液體脫硫劑的碳酸氫鉀)2.9t,回收碳酸氫鉀890kg/t(硫磺),回收率95.5%。副產(chǎn)的碳酸氫鉀含有少量硫磺和脫硫劑,無(wú)法外銷。處理成本約3500元/t(硫磺)。本領(lǐng)域的技術(shù)人員容易理解的是,在不沖突的前提下,上述各優(yōu)選方案可以自由地組合、疊加。以上所述僅為本發(fā)明的優(yōu)選實(shí)施例,并不用于限制本發(fā)明,對(duì)于本領(lǐng)域技術(shù)人員而言,本發(fā)明可以有各種改動(dòng)和變化。凡在本發(fā)明的精神和原理之內(nèi)所作的任何修改、等同替換、改進(jìn)等,均應(yīng)包含在本發(fā)明的保護(hù)范圍之內(nèi)。當(dāng)前第1頁(yè)12