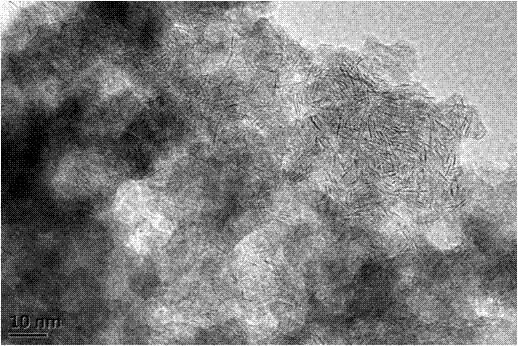
本發(fā)明涉及一種加氫處理催化劑,特別是一種加氫處理催化劑中間體、加氫處理催化劑及其制備方法。
背景技術:
:常規(guī)的加氫催化劑為氧化態(tài),而實際使用時真正起活性作用的物質為硫化態(tài),因此氧化態(tài)加氫催化劑在開工使用前需要預硫化。常用的預硫化方式為器內(nèi)預硫化和器外預硫化,其中器內(nèi)預硫化是將氧化態(tài)催化劑裝入加氫反應器內(nèi),在升溫過程中向反應器中通入氫氣和硫化劑,使其生成硫化氫,從而使加氫活性金屬由氧化物轉化為硫化物。器外預硫化是指催化劑在裝入反應器前與硫化劑結合,再裝入反應器中。開工時,需要通入h2,隨著溫度的升高,硫化劑分解生成硫化氫,從而使加氫活性金屬轉化為硫化物。cn1171430a中描述了一種典型的器內(nèi)預硫化方法,其中硫化劑選用二硫化碳或二甲基二硫醚等,硫化劑氣體與催化劑的體積比一般為300~600,硫化在常壓或高壓下進行,一般的升溫和恒溫程序為在200~240℃下硫化2~6小時,再在320~360℃硫化8~12小時。這不僅增加了生產(chǎn)成本,而且硫化過程容易對人和環(huán)境造成污染,因此國內(nèi)外的科研人員都積極器外預硫化。us4,650,563先將鎳或鈷的無機鹽和硫代鉬酸銨以及乙二胺混合,在一定條件下反應生成復合物,然后在含有硫化氫的氫氣中反應得到所需催化劑。us7,132,386報道了一種制備鈷鉬硫化型催化劑的方法,先將硫代鉬酸銨、氯化鈷和烷基溴化氨混合生成中間產(chǎn)物,再將其移入反應釜內(nèi),在300℃,500psi氫壓下反應生成mos2和co9s8。cn101491765a公開一種硫化型加氫催化劑的制備方法,通過浸漬法將硫化劑與第vib族金屬和第viii族金屬無機鹽負載在載體孔中,低溫處理使之分散在催化劑載體孔道表面,從而制備出負載型高活性的硫化型催化劑。綜上,加氫催化劑不管采取哪種方式進行硫化,其原理都是在氫氣存在下,將硫化劑中的硫轉化成硫化氫,然后由生成的硫化氫與催化劑中活性金屬反應,使其轉化為金屬的硫化物。由于硫化過程均會生成硫化氫,硫化氫再與活性金屬反應,此過程會產(chǎn)生大量的熱,從而造成硫化過程溫度迅速上升。為避免溫升過快,硫化過程均緩慢地升溫,但這會造成催化劑硫化時間過長,不利于縮短開工時間。再者,現(xiàn)有的器外預硫化與器內(nèi)預硫化均在氫氣作用下進行預硫化或活化,均會出現(xiàn)氧化態(tài)加氫催化劑的氫解反應,而且由于活性組分與載體結合力往往太強,使加氫催化劑不能被完全硫化,從而造成加氫催化劑中活性金屬組分的硫化不充分,活性金屬分散度不好,活性金屬組分不能充分發(fā)揮作用,造成金屬浪費。技術實現(xiàn)要素:針對現(xiàn)有技術的不足,本發(fā)明提供了一種加氫處理催化劑中間體、加氫處理催化劑及其制備方法。采用該催化劑中間體制備加氫處理催化劑時,在焙燒硫化時不需要經(jīng)過硫化氫的生成反應和硫化氫與活性金屬的硫化反應,不產(chǎn)生額外的熱量,很好地解決了器外預硫化催化劑的氣密和放熱問題,避免了催化劑硫化過程中溫升過快的問題;該催化劑為完全意義的硫化型催化劑,可以直接升溫加氫反應溫度,可大幅縮短開工時間;該加氫處理催化劑硫化充分,金屬分散度好,具有很好的加氫性能。本發(fā)明提供了一種加氫處理催化劑中間體,其包括加氫活性金屬組分和載體組分,還包括有機化合物,有機化合物為通式(?。┧镜幕衔?,通式(?。椋海á。┢渲?,x,y相同或不同,選自堿金屬離子、nh4+或h;z為-nr1r2、-sr3或r4;r1與r2相同或不同,選自h、含1至20個碳原子的烷基、苯環(huán)、五元芳雜環(huán)或六元芳雜環(huán);r3選自堿金屬離子、nh4+或h;r4選自h、含1至20個碳原子的烷基、苯環(huán)、五元芳雜環(huán)或六元芳雜環(huán)。堿金屬離子優(yōu)選為k+、na+。在有機化合物中,含1至20個碳原子的烷基可以為有取代或無取代的烷基,取代基為羥基、羧基、醛基、羰基中的一種或幾種。在有機化合物中,苯環(huán)、五元芳雜環(huán)、六元芳雜環(huán)可以為有取代或無取代的苯環(huán)、五元芳雜環(huán)、六元芳雜環(huán),取代基選自氟、氯、溴、硝基、含1至3個碳原子的直鏈或支鏈的烷氧基中的一種或多種;芳雜環(huán)為吡啶、嘧啶、噻吩、呋喃或吡咯。在通式(?。┲?,s為硫原子,n為氮原子。在有機化合物中,當z為-nr1r2時,所述有機化合物可以為有2-取代胺基的4,6-二巰基均三嗪鹽,如可以為2-苯胺-4,6-二巰基均三嗪鹽、2-仲胺-4,6-二巰基均三嗪鹽、2-二正丁胺基-4,6-二巰基均三嗪鹽,2-乙醇胺-4,6-二巰基均三嗪鹽、2-十八胺-4,6-二巰基均三嗪鹽。當z為-sr3時,所述有機化合物可以為2,4,6-三巰基均三嗪或2,4,6-三巰基均三嗪鹽,如2,4,6-三巰基均三嗪單鈉鹽、2,4,6-三巰基均三嗪單鈉鹽、2,4,6-三巰基均三嗪單銨鹽、2,4,6-三巰基均三嗪二銨鹽、2,4,6-三巰基均三嗪三銨鹽。當z為r4時,r4為h時,所述有機化合物可以為2,4-二巰基均三嗪鹽,如2,4-二巰基均三嗪單鈉鹽,2,4-二巰基均三嗪二鈉鹽、2,4-二巰基均三嗪單銨鹽,2,4-二巰基均三嗪二銨鹽;當r4為含1至20個碳原子的有取代或無取代、直鏈或支鏈的烷基時,所述有機化合物,例如可以為2-正丙醇-4,6-二巰基均三嗪鹽。所述有機化合物可以選自以下化合物,但不限于以下化合物:2,4,6-三巰基均三嗪鹽、2,4-二巰基均三嗪鹽、2-苯胺-4,6-二巰基均三嗪鹽、2-仲胺-4,6-二巰基均三嗪鹽、2-二正丁胺基-4,6-二巰基均三嗪鹽、2-乙胺基-4,6-二巰基均三嗪鹽、2-乙醇胺-4,6-二巰基均三嗪鹽、2-十八胺-4,6-二巰基均三嗪鹽、2-正丙醇-4,6-二巰基均三嗪鹽中的一種或幾種。2,4,6-三巰基均三嗪鹽可以為單鈉或單銨鹽,也可以為二鈉或二銨鹽,也可以為三鈉或三銨鹽,而具有4,6-二巰基均三嗪結構的鹽類化合物,可以為單鈉或單銨鹽,也可以為二鈉或二銨鹽。所述有機化合物和加氫活性金屬以絡合物的形式存在于載體組分中。所述有機化合物在催化劑中間體中的含量以硫元素計為加氫活性金屬理論需硫量的85%~120%,優(yōu)選為90%~110%。本發(fā)明的加氫活性金屬可以采用本領域常規(guī)使用的加氫活性金屬,加氫活性金屬可以選用第vib族金屬和第viii族金屬中的一種或多種,以催化劑中間體的干基重量為基準,加氫活性金屬以金屬氧化物計的重量含量為4%~60%。加氫活性金屬優(yōu)選含有第vib族金屬和第viii族金屬,其中第viii族金屬/(第vib族金屬+第viii族金屬)以金屬元素計的重量比為0.1~0.35。第vib金屬一般選自w、mo中的一種或幾種,第viii族金屬一般選自ni、co中的一種或幾種。本發(fā)明的加氫處理催化劑可以使用本領域常規(guī)使用的載體組分,載體組分可以為耐熔多孔物質的前驅物,選自氧化鋁、氧化硅、氧化鈦、氧化鎂、氧化鋯、無定形硅鋁中的一種或多種前驅物。氧化鋁的前驅物為擬薄水鋁石、薄水鋁石中的一種或幾種,氧化硅的前驅物為硅膠、硅溶膠、水溶性硅油等中的一種或幾種,氧化鈦的前驅物為硫酸鈦、氫氧化鈦中的一種或幾種,氧化鋯的前驅物為氧氯化鋯、硫酸鋯、硝酸鋯等中的一種或幾種。本發(fā)明還提供了上述加氫處理催化劑中間體的制備方法,包括如下步驟:(l)將載體組分加水打漿,得到漿液;(2)將含加氫活性金屬組分的溶液和有機化合物溶液分別或同時加入到所述漿液中,攪拌均勻;(3)將步驟(2)所得的物料進行過濾、洗滌、干燥,得到催化劑中間體。在步驟(1)中,所述載體組分和水的重量比為(1:5)~(1:50)。在步驟(2)中,所述含加氫活性金屬組分的溶液的濃度為10wt%~60wt%。所述有機化合物溶液先將有機化合物溶于溶劑中,然后再浸漬到載體上。所述有機化合物溶液中的溶劑為丙酮、乙醇、水、甲醇、甲乙酮中的一種或幾種,所述有機化合物溶液的濃度為5wt%~60wt%。在步驟(3)中,所述干燥的溫度為20~150℃,時間為0.5~48h,優(yōu)選為70~120℃,時間為1~24h。本發(fā)明還提供了一種加氫處理催化劑,采用上述的加氫處理催化劑中間體,經(jīng)成型、干燥和焙燒后,得到所述的加氫處理催化劑。所述加氫處理催化劑的比表面積為150~450m2/g,孔容為0.2~1.0ml/g,平均孔直徑為3~15nm,優(yōu)選為比表面積為180~350m2/g,孔容為0.3~0.8ml/g,平均孔直徑為4~12nm。在步驟(1)中,本發(fā)明的加氫處理催化劑可以使用本領域常規(guī)使用的載體組分,載體組分可以為耐熔多孔物質的前驅物,優(yōu)選為氧化鋁、氧化硅、氧化鈦、氧化鎂、氧化鋯、無定形硅鋁中的一種或多種前驅物。氧化鋁的前驅物為擬薄水鋁石、薄水鋁石中的一種或幾種,氧化硅的前驅物為硅膠、硅溶膠、水溶性硅油等中的一種或幾種,氧化鈦的前驅物為硫酸鈦、氫氧化鈦中的一種或幾種,氧化鋯的前驅物為氧氯化鋯、硫酸鋯、硝酸鋯等中的一種或幾種。在步驟(2)中,本發(fā)明的加氫活性金屬可以采用本領域常規(guī)使用的加氫活性金屬,加氫活性金屬可以選用第vib族金屬和第viii族金屬中的一種或多種,以催化劑中間體的干基重量為基準,加氫活性金屬以金屬氧化物計的重量含量為4%~60%。加氫活性金屬優(yōu)選含有第vib族金屬和第viii族金屬,其中第viii族金屬/(第vib族金屬+第viii族金屬)以金屬元素計的重量比為0.1~0.35。第vib金屬一般選自w、mo中的一種或幾種,第viii族金屬一般選自ni、co中的一種或幾種。所述焙燒為兩步焙燒,第一步焙燒的溫度為150~300℃,時間為1~10h,優(yōu)選為180~280℃,時間為3~8h,第二步焙燒的溫度為450~600℃,焙燒時間為2~10小時,優(yōu)選為480~550℃,時間為3~8h。本發(fā)明還提供了一種上述的加氫處理催化劑的制備方法,在所述加氫處理催化劑中間體中加入成型助劑和/或擴孔劑,然后進行混捏,成型,干燥,在惰性氣體的保護下進行焙燒,得到所述的加氫處理催化劑。所述成型助劑為本領域常規(guī)使用的成型助劑,可以為助擠劑、粘合劑中的一種或幾種;所述擴孔劑為本領域常規(guī)使用的擴孔劑,可以為炭黑、磷酸銨、碳酸銨、聚乙二醇、聚乙烯醇、聚丙烯酰胺、聚苯乙烯中的一種或幾種。所述粘合劑和助擠劑均為本領域常規(guī)使用的粘合劑和助擠劑。所述粘合劑一般可以采用小孔氧化鋁,助擠劑可以是淀粉、甲基纖維素、田菁粉、甲酸、酒石酸、檸檬酸中的一種或幾種;也可以是復合助擠劑檸檬酸-田菁粉等。成型可以根據(jù)最終催化劑的形狀確定,如擠條等。所述干燥的溫度為70~140℃,時間為1~24h。所述焙燒為兩步焙燒,第一步焙燒的溫度為150~300℃,時間為1~10h,優(yōu)選為180~280℃,時間為3~8h,第二步焙燒的溫度為450~600℃,焙燒時間為2~10小時,優(yōu)選為480~550℃,時間為3~8h。本發(fā)明還提供了一種加氫處理催化劑的開工方法,其包括如下步驟:(1)將硫化型催化劑裝入反應器中;(2)通入氫氣置換反應器中及反應器前后管線中的空氣,逐步升溫至反應壓力和反應溫度,進原料油開始進行加氫反應。本發(fā)明與現(xiàn)有的技術相比具有如下優(yōu)點:(1)本發(fā)明的加氫處理催化劑中間體中,加氫活性金屬組分和有機化合物是以絡合物的狀態(tài)存在,這種存在方式非常穩(wěn)定,便于貯存和運輸。只需焙燒成型后的加氫處理催化劑中間體,有機化合物中的硫便可直接與均三嗪環(huán)斷鍵,在載體表面原位形成金屬硫化物,便可完成催化劑的硫化過程,制得完全硫化型加氫處理催化劑。本發(fā)明開辟了一種全新的硫化方法,硫化過程不需要再經(jīng)過硫化氫的生成反應和硫化氫與活性金屬的硫化反應,從根本上避免產(chǎn)生大量熱,徹底地解決了催化劑床層溫度迅速上升的問題。(2)本發(fā)明的加氫處理催化劑,在焙燒過程中,有機化合物中的硫原子便直接與均三嗪環(huán)斷鍵,在載體表面原位形成金屬硫化物,這種原位硫化使加氫活性金屬組分硫化充分,而且斷裂后的雜環(huán)以氣體的形式溢出,從而促使載體組分形成新的空隙和孔道,使活性金屬硫化物充分暴露,在加氫反應時,可產(chǎn)生更多的活性位,形成更多的邊角棱位,有利于反應物的吸附,避免硫化過程的金屬聚集,進而提高了活性金屬的利用效率,因此提高了催化劑的加氫性能。本發(fā)明的催化劑為完全意義的硫化型催化劑,裝入加氫處理反應器,可直接升溫至反應溫度,便可開工生產(chǎn),大幅度地縮短開工時間。(3)本發(fā)明的加氫處理催化劑的制備方法,活性金屬和有機化合物加入攪拌的漿液中,使活性金屬與有機化合物絡合,并與載體組分均勻分散,這樣有利于活性金屬均勻分布在載體表面,尤其是在后續(xù)的焙燒過程中,形成新的空隙和孔道,可產(chǎn)生更多的活性位,使加氫活性金屬組分硫化充分,因此提高了催化劑的加氫性能。(4)本發(fā)明的加氫處理催化劑,生產(chǎn)工藝簡單,催化劑制備成本低,可大規(guī)模地用于加氫處理裝置。附圖說明圖1為實施例1的加氫處理催化劑a的掃描電鏡(tem)圖;圖2為對比例2的加氫處理催化劑h的掃描電鏡(tem)圖;圖3為對比例1和2的催化劑在反應器中開工硫化過程中的硫化氫生成曲線圖和實施例1的催化劑焙燒過程中硫化氫生成曲線圖。具體實施方式下面通過實施例進一步描述本發(fā)明的技術特點,但這些實施例不能限制本發(fā)明,涉及的wt%為質量分數(shù)。實施例1加氫處理催化劑a的制備稱取鉬酸銨40.6g,硝酸鎳21.7g,氨水50ml,與去離子水混合均勻至100ml,得到溶液i。取2,4,6-三巰基均三嗪三銨鹽41g溶于50ml水中得到溶液ii。稱取大孔擬薄水鋁石(干基為73wt%)84g和硅膠(含二氧化硅30wt%)24ml放入1l水中,強力攪拌20min后,將溶液i和ii并流滴入,之后再攪拌30min后洗滌,抽濾。抽濾所得濾餅在80℃下低溫熱處理3小時。將濾餅粉碎后加入田菁粉3g混合均勻,然后將小孔氧化鋁42g與檸檬酸3g,硝酸(濃度為30wt%)10ml,去離子水120ml打漿作為粘結劑,碾壓20min后,在擠條機上擠成1.2mm三葉草條,80℃干燥4小時,在氮氣爐中程序升溫焙燒,焙燒條件為:以3℃/min升溫至200℃,恒溫2小時,再以相同速率升溫至500℃,恒溫3小時,即得加氫處理催化劑a,主要物理性質見表1。實施例2加氫處理催化劑b的制備取氧化鉬33.5g,堿式碳酸鎳9.2g,磷酸2ml,去離子水60ml,混合均勻后煮沸1h,得到溶液i。稱取2,4-二巰基均三嗪二銨鹽58g溶于100ml丙酮溶液中,得溶液ii。稱取大孔擬薄水鋁石(干基為73wt%)72g、氧氯化鋯12g和水溶性硅油20g,然后放入1l水中,強力攪拌20min后,將溶液i滴入漿液中攪拌10min,然后再將溶液ii滴入漿液,滴入過程中強力攪拌,之后再攪拌30min后洗滌,抽濾。抽濾所得濾餅在80℃下低溫熱處理3小時。將濾餅粉碎后加入田菁粉3g混合均勻,然后將小孔氧化鋁56g與檸檬酸3g,硝酸(濃度為30wt%)10ml,去離子水120ml打漿作為粘結劑,碾壓20min后,在擠條機上擠成1.2mm三葉草條,80℃干燥4小時,在氮氣爐中程序升溫焙燒,焙燒條件為:以3℃/min升溫至220℃,恒溫2小時,再以相同速率升溫至500℃,恒溫3小時,即得加氫處理催化劑b,主要物理性質見表1。實施例3加氫處理催化劑c的制備稱取鉬酸銨40.6g,硝酸鎳21.7g,氨水50ml,與去離子水混合均勻至100ml,得到溶液i。取2,4,6-三巰基均三嗪單銨鹽102g溶于50ml水中得到溶液ii,其它步驟與實施例1相同,即得加氫處理催化劑c,主要物理性質見表1。實施例4加氫處理催化劑d的制備本實施例的原料和方法與實施例1基本相同,不同點在于:本實施例采用2-苯胺-4,6-二巰基均三嗪鹽74g替換實施例1中的2,4,6-三巰基均三嗪三銨鹽,焙燒條件為:以3℃/min升溫至250℃,恒溫2小時,再以相同速率升溫至550℃,恒溫3小時,即得加氫處理催化劑d。主要物理性質見表1。實施例5硫化型加氫處理催化劑e的制備本實施例的原料和方法與實施例2基本相同,不同點在于:本實施例采用2-乙胺基-4,6-二巰基均三嗪二銨鹽60g替換實施例2中的2,4-二巰基均三嗪二銨鹽。得到加氫處理催化劑e,主要物理性質見表1。實施例6加氫處理催化劑f的制備本實施例的原料和方法與實施例2基本相同,不同點在于:采用2-十八胺-4,6-二巰基均三嗪鹽120g替換實施例2中的2,4-二巰基均三嗪二銨鹽。得到加氫處理催化劑f,主要物理性質見表1。對比例1氧化型加氫處理催化劑g的制備取氧化鉬33.5g,堿式碳酸鎳9.2g,磷酸2ml,去離子水60ml,混合均勻后煮沸1h,加水至100ml得溶液i。稱取大孔擬薄水鋁石(干基為73wt%)84g和硅膠(含二氧化硅30wt%)24ml放入1l水中,強力攪拌20min后,將溶液i滴入,之后再攪拌30min后洗滌,抽濾。抽濾所得濾餅在120℃下低溫熱處理3小時。將濾餅粉碎后加入田菁粉3g、聚苯乙烯及聚乙二醇2000各5g混合均勻,然后將小孔氧化鋁42g、檸檬酸3g、硝酸(濃度為30wt%)10ml和去離子水120ml打漿作為粘結劑,碾壓20min后,在擠條機上擠成1.2mm三葉草條,120℃干燥4小時,在馬弗爐中升溫至500℃,恒溫3小時,即得氧化型加氫處理催化劑g,主要物理性質見表1。對比例2加氫處理催化劑h的制備取對比例1所得的焙燒樣,用巰基乙酸64g浸漬,室溫下干燥12小時即得加氫處理催化劑h,主要物理性質見表1。測試例1本發(fā)明加氫處理催化劑的活性評價取實施例1-6的加氫處理催化劑進行活性穩(wěn)定性評價,評價在200ml固定床加氫處理裝置上進行,載氣為氫氣。原料油為常三線油,硫含量6524.1μg/g,氮含量為50.6μg/g。在裝置氣密后,引入氫氣并直接以30℃/h升溫至150℃,通入原料油,恒溫3h,繼續(xù)升溫至反應溫度350℃,恒溫8h后取樣分析。工藝條件為:壓力3.4mpa,空速2.0,溫度350℃,氫油體積比500。評價結果列于表2。測試例2加氫處理催化劑的活性評價取對比例2的催化劑進行活性穩(wěn)定性評價,評價在200ml固定床加氫處理裝置上進行。接通氫氣,保持壓力為3.5mpa,以20℃/h的升溫速度升至150℃,開始進原料油,恒溫3h,再以20℃/h升溫至反應溫度320℃,恒溫8小時后完成硫化。再升溫至350℃恒溫8小時后取樣分析。原料油及工藝條件與測試例1相同。評價結果見表2。測試例3氧化型加氫處理催化劑的活性評價取對比例1的催化劑進行活性穩(wěn)定性評價,評價在200ml固定床加氫處理裝置上進行。催化劑硫化過程中硫化油為航煤和二硫化碳的混合物,其密度為0.798g/cm3,硫含量為20000μg/g,氮含量為1.0μg/g,餾程為161~276℃。將氧化型催化劑裝入加氫反應器中,接通氫氣,保持壓力為3.5mpa,以20℃/h的升溫速度升至150℃,開始進硫化油,恒溫3小時,再以20℃/h的升溫速度升至230℃,恒溫8小時,再升溫至320℃恒溫8小時后完成硫化。然后換進原料油,升溫至350℃,再恒溫8小時后取樣分析。原料油及工藝條件與測試例1相同。評價結果見表2。表1催化劑的物化性質催化劑編號總金屬含量(以金屬氧化物計),wt%s,wt%比表面積,m2/g孔容,ml/g平均孔直徑,nm催化劑a2812.42370.457.6催化劑b2812.32350.447.5催化劑c2812.42230.447.9催化劑d2812.42260.437.6催化劑e2812.32270.427.4催化劑f2812.22200.437.8催化劑g28-1730.327.4催化劑h2811.91730.327.4注:催化劑的孔結構為轉化成氧化態(tài)后分析所得。表2催化劑的評價結果催化劑編號s,μg/gn,μg/g開工時間,h催化劑a18.10.423催化劑b21.50.623催化劑c26.70.523催化劑d27.90.423催化劑e25.40.723催化劑f28.10.523催化劑g78.62.944催化劑h72.41.536由表1、表2可以看出,在催化劑組成和工藝條件相同的情況下,實施例的催化劑的加氫活性明顯高于對比例。催化劑的制備工藝簡單,經(jīng)濟性好。催化劑為完全意義的硫化型催化劑,裝入加氫反應裝置可直接升至加氫反應溫度,大幅縮短開工時間。測試例1和2在換進原料油升溫至350℃,進行加氫8小時,取樣分析后,結束活性評價。取活性評價后的催化劑a和h,隔絕空氣進行tem表征,任意選取tem照片20張,統(tǒng)計照片中的二硫化鉬相的條紋層數(shù)和長度,其結果列于表3。表3mos2片晶的平均層數(shù)和長度催化劑平均層數(shù)平均長度/nma4.44.12h3.85.78由表3和圖1、2可知,催化劑a和h硫化后均生成ⅱ類活性相。與催化劑h相比,催化劑a的活性相的平均層數(shù)多,這說明催化劑在相同表面上能夠提供的活性位多,而平均長度小說明金屬在載體的分散度高,因此本發(fā)明方法能夠提高金屬在載體上的分散度,并產(chǎn)生較多的活性位,進而催化劑具有很好加氫性能。當前第1頁12