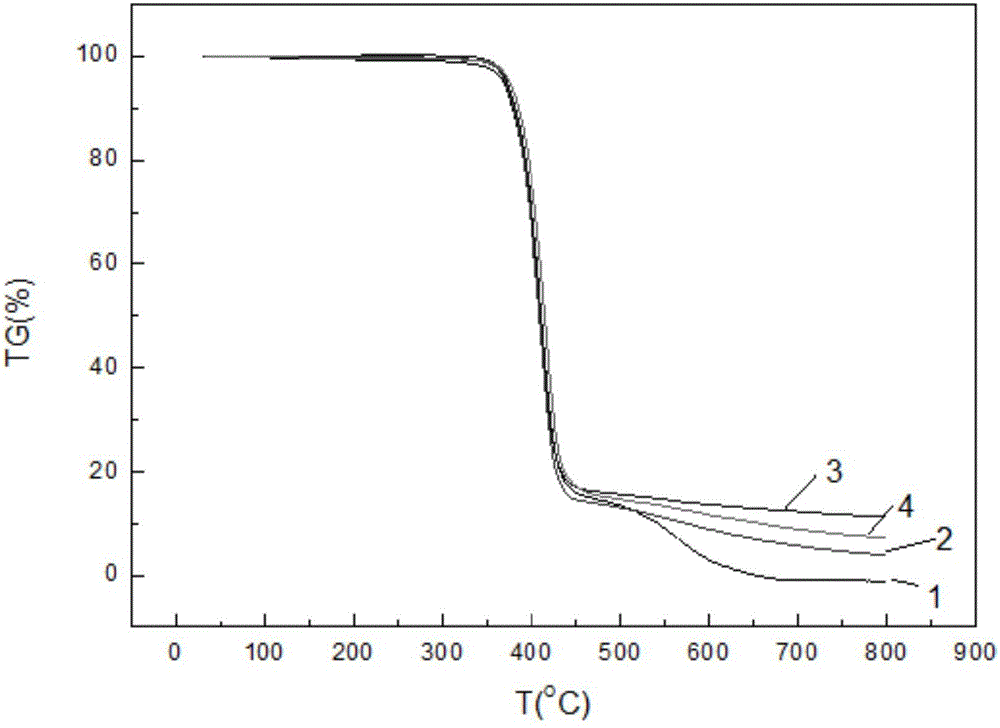
本發(fā)明涉及合成工藝,特別地,涉及一種合成聚對苯二甲酸乙二醇酯的方法。
背景技術(shù):
:聚對苯二甲酸乙二醇酯(PET),是對苯二甲酸(PTA)和乙二醇(EG)經(jīng)過酯化和縮聚反應(yīng)生成的產(chǎn)物,是我國聚酯產(chǎn)品生產(chǎn)中產(chǎn)量最大、品種最多的一類合成材料,應(yīng)用于纖維、薄膜、瓶用等多個領(lǐng)域。近年來,隨著歐美等國家和地區(qū),相繼提出“綠色纖維”的概念,環(huán)保綠色纖維紡織品成為了國際發(fā)展的潮流。這種對人體健康和環(huán)境沒有危害的原料織造的綠色纖維紡織品的潮流,使我國紡織品的出口受到了威脅。這是由于常用合成PET的催化劑是銻系催化劑、鍺系催化劑和鈦系催化劑。銻第催化催化劑主要包括三氧化二銻,醋酸銻和乙二醇銻,雖然銻系催化劑工藝比較成熟,具有催化活性適中,副反應(yīng)少,價格低廉等優(yōu)點(diǎn),但是Sb催化劑在被廣泛應(yīng)用的同時還存在一些明顯的缺點(diǎn):由于銻化合物本身具有一定的毒性,在自然界中又與劇毒的砷共存,因此,使用Sb催化劑的應(yīng)用受到了一定的局限。另外,由于Sb2O3或Sb(Ac)3催化合成的PET在紡絲時,殘留的Sb在熔體出噴絲孔時會夾帶PET一起升華,污染紡絲現(xiàn)場。環(huán)保方面,含Sb的EG殘渣必須要處理,Sb在織物染色工序中會被漫取出來造成對工藝水的污染,這些都會導(dǎo)致處理費(fèi)用的增加銻離子作為重金屬,對人體有慢性毒性和致癌性,在聚酯中含量大,不符合綠色紡織品的要求。鍺系催化劑中的鍺元素在自然界中資源稀少,使得鍺系催化劑價格昂貴,難以實現(xiàn)工業(yè)化使用。而鈦系催化劑,因其不含有重金屬,而且具有環(huán)保高效、對人體無害等優(yōu)點(diǎn),成為了可以替代銻和鍺的首選催化劑,成為了近年來的研究熱點(diǎn)。但是,鈦系催化劑本身穩(wěn)定性差、易水解,導(dǎo)致用其生產(chǎn)的PET產(chǎn)品熱穩(wěn)定性差、顏色發(fā)黃,而且還存在催化效率低等問題,一直沒有得到大規(guī)模使用。因此,亟待開發(fā)一種環(huán)境友好、催化效率高的生產(chǎn)PET的方法。技術(shù)實現(xiàn)要素:為了解決上述問題,本發(fā)明人進(jìn)行了銳意研究,發(fā)現(xiàn)在以對苯二甲酸和乙二醇為原料制備聚對苯二甲酸乙二醇酯的反應(yīng)中,使用包括鈦酸四丁酯、硅酸四乙酯和苯基膦酸的復(fù)合催化劑進(jìn)行催化,能夠得到分子量高、分子量分布窄、力學(xué)性能和熱穩(wěn)定性好的PET,而且該復(fù)合催化劑的催化活性為銻系催化劑活性的17倍以上,從而完成本發(fā)明。本發(fā)明提供了一種制備聚對苯二甲酸乙二醇酯的方法,該方法使用包括鈦酸四丁酯、硅酸四乙酯和苯基膦酸的復(fù)合催化劑進(jìn)行催化,優(yōu)選地,所述復(fù)合催化劑在酯化反應(yīng)前加入反應(yīng)體系。附圖說明圖1示出實驗例2中各樣品的DSC曲線圖;圖2示出實驗例3中各樣品的TG曲線;圖3示出實驗例3中各樣品的DTG曲線;圖4示出實驗例6中樣品的動力學(xué)曲線圖;圖5示出實驗例8中樣品的特性粘度曲線圖;圖6示出實驗例11中對比例2制得樣品的DSC曲線圖;圖7示出實驗例11中實施例3制得樣品的DSC曲線圖;圖8示出實驗例12中對比例2及實施例3酯化階段進(jìn)料制得樣品的TG曲線圖;圖9示出實驗例12中對比例2及實施例3酯化階段進(jìn)料制得樣品的DTG曲線圖;圖10示出實驗例12中對比例2及實施例3縮聚階段進(jìn)料制得樣品的TG曲線圖;圖11示出實驗例12中對比例2及實施例3縮聚階段進(jìn)料制得樣品的DTG曲線圖;圖12示出實驗例14中樣品用量與酯化時間關(guān)系圖;圖13示出實驗例15中樣品用量與縮聚時間關(guān)系圖;圖14示出實驗例17中樣品用量與PET色相關(guān)系圖;圖15示出實驗例18中樣品用量與PET熱性能關(guān)系圖;圖16示出實驗例19中不同催化劑用量制得PET的TG圖;圖17示出實驗例19中不同催化劑用量制得PET的DTG圖。具體實施方式下面通過對本發(fā)明進(jìn)行詳細(xì)說明,本發(fā)明的特點(diǎn)和優(yōu)點(diǎn)將隨著這些說明而變得更為清楚、明確。以下詳述本發(fā)明。根據(jù)本發(fā)明,提供了一種制備聚對苯二甲酸乙二醇酯的方法,其中,該方法使用復(fù)合催化劑進(jìn)行催化。在本發(fā)明中,制備聚對苯二甲酸乙二醇酯的原料為對苯二甲酸和乙二醇。在本發(fā)明中,所述復(fù)合催化劑包括鈦酸四丁酯、硅酸四乙酯和苯基膦酸。在本發(fā)明中,在所述復(fù)合催化劑中,鈦酸四丁酯、硅酸四乙酯與苯基膦酸的摩爾量之比為鈦酸四丁酯的摩爾量:硅酸四乙酯的摩爾量:苯基膦酸的摩爾量=(6~12):1:(1~3),優(yōu)選為(8~10):1:(1.5~2.5),如9:1:2,其中,鈦酸四丁酯的摩爾量以其中鈦元素的摩爾量計;硅酸四乙酯的摩爾量以其中硅元素的摩爾量計;苯基膦酸的摩爾量以其中磷元素的摩爾量計。本發(fā)明人發(fā)現(xiàn),以硅酸四乙酯的用量做為1摩爾當(dāng)量時,當(dāng)鈦酸四丁酯的摩爾量大于12摩爾當(dāng)量時,所合成的PET色相變差,顏色發(fā)黃,小于6摩爾當(dāng)量時,催化效率變低,反應(yīng)速率變慢。本發(fā)明人還發(fā)現(xiàn),以硅酸四乙酯的用量做為1摩爾當(dāng)量時,當(dāng)苯基膦酸的摩爾量大于3摩爾當(dāng)量時,苯基膦酸易與體系中金屬作用形成沉淀或凝膠,影響PET的質(zhì)量,小于1摩爾當(dāng)量時,復(fù)合催化劑易發(fā)生水解,穩(wěn)定性變差。在本發(fā)明一種優(yōu)選的實施方案中,所述復(fù)合催化劑還包括分散劑,優(yōu)選地,所述分散劑為乙二醇。本發(fā)明人發(fā)現(xiàn),硅酸四乙酯與鈦酸四丁酯互溶性差,當(dāng)單純使硅酸四乙酯、鈦酸四丁酯和苯基膦酸混合時,該組合物自然形成互不相溶的兩相,這不僅造成取用的不便,還會導(dǎo)致該復(fù)合催化劑在使用時的配比不確定,從而導(dǎo)致催化效率不穩(wěn)定。令人驚喜的是,本發(fā)明人發(fā)現(xiàn),作為聚合反應(yīng)原料的乙二醇對硅酸四乙酯、鈦酸四丁酯和苯基膦酸均具有良好的溶解性,以其作為溶劑制得的復(fù)合催化劑表現(xiàn)為單一的均相體系,而且,在使用該復(fù)合催化劑時,體系中的乙二醇不需要除去,直接充當(dāng)過量的原料即可,這樣處理還能夠促進(jìn)反應(yīng)的正向進(jìn)行,提高產(chǎn)率和收率。在本發(fā)明中,基于復(fù)合催化劑的總體積,其中,鈦元素的摩爾濃度為(0.1~1)mol/L,優(yōu)選為(0.2~0.8)mol/L,更優(yōu)選為(0.3~0.6)mol/L,如0.457mol/L。本發(fā)明人發(fā)現(xiàn),當(dāng)復(fù)合催化劑中鈦元素的摩爾濃度大于1mol/L時,當(dāng)復(fù)合催化劑中鈦元素的摩爾濃度小于0.1mol/L時,催化效率降低,反應(yīng)速度下降,,因此,本發(fā)明選擇基于復(fù)合催化劑的總體積,其中,鈦元素的摩爾濃度為(0.1~1)mol/L。在本發(fā)明中,所述復(fù)合催化劑通過以下方法制得:將硅酸四乙酯、苯基膦酸以及鈦酸四丁酯與分散劑混合。在本發(fā)明一種優(yōu)選的實施方式中,所述復(fù)合催化劑通過包括以下步驟的方法制得:步驟1-1、將硅酸四乙酯加入分散劑中,任選攪拌,得到硅酸四乙酯的分散體系;步驟1-2、將苯基膦酸加入到上述硅酸四乙酯的分散體系中,任選攪拌,然后加入到鈦酸四丁酯中。在本發(fā)明中,所述復(fù)合催化劑在酯化反應(yīng)前或酯化反應(yīng)階段加入反應(yīng)體系。本發(fā)明人發(fā)現(xiàn),復(fù)合催化劑加入的時機(jī)對PET產(chǎn)品的色相、分子量、分子量分布、熱性能以及力學(xué)性能具有較大影響,具體表現(xiàn)為與在縮聚反應(yīng)階段加入所述催化劑相比,在酯化反應(yīng)前或者酯化反應(yīng)階段加入所述復(fù)合催化劑得到的PET產(chǎn)品亮度高、顏色淺、分子量大、分子量分布窄、熱穩(wěn)定性高、力學(xué)性能強(qiáng)。(具體參見實驗例9~13)因此,本發(fā)明選擇在酯化反應(yīng)前或者在酯化反應(yīng)階段加入所述復(fù)合催化劑。本發(fā)明人經(jīng)過大量研究還發(fā)現(xiàn),復(fù)合催化劑的加入量對合成聚對苯二甲酸乙二醇酯中酯化反應(yīng)時間以及縮聚反應(yīng)時間產(chǎn)生了重要影響,具體表現(xiàn)為復(fù)合催化劑的使用量越大,酯化反應(yīng)的時間越短,而隨著復(fù)合催化劑使用量的增大,縮聚反應(yīng)時間先縮短后增長,在復(fù)合催化劑的用量為19μg/g(該用量基于對苯二甲酸的重量,以其中鈦元素的重量計)時,縮聚反應(yīng)的時間最短。(具體參見實驗例14~20)因此,本發(fā)明選擇復(fù)合催化劑的用量為(5~50)μg/g,優(yōu)選為(9~40)μg/g,更優(yōu)選為(15~30)μg/g,如9.5μg/g、19μg/g、28.5μg/g和38μg/g,特別優(yōu)選為19μg/g,其中,所述用量基于對苯二甲酸的重量,以其中鈦元素的重量計。在本發(fā)明一種優(yōu)選的實施方式中,所述方法包括以下步驟:步驟1、酯化反應(yīng):將對苯二甲酸、乙二醇和復(fù)合催化劑加入聚合釜中,混合,優(yōu)選地升溫,補(bǔ)加乙二醇和抗氧劑,優(yōu)選地,還補(bǔ)加熱穩(wěn)定劑,繼續(xù)混合;步驟2、縮聚反應(yīng):先使反應(yīng)釜內(nèi)處于低真空狀態(tài),一段時間后再進(jìn)入高真空狀態(tài),再使釜內(nèi)升溫,保持?jǐn)嚢柚练磻?yīng)結(jié)束。在本發(fā)明步驟1中,在初始投料時,對苯二甲酸、乙二醇以及復(fù)合催化劑的重量之比為苯二甲酸的重量:乙二醇的重量:復(fù)合催化劑的重量=(600~800):(265~365):(0.10~0.15),優(yōu)選為(650~750):(280~325):(0.11~0.13),如700:315:0.12。本發(fā)明對混合的方法不做特別限定,可以使用現(xiàn)有技術(shù)中任何一種液相混合的方式,如攪拌等。在本發(fā)明步驟1中,優(yōu)選地,將體系升溫至將體系升溫至(130~260)℃,優(yōu)選為(180~255)℃,如245℃或255℃。本發(fā)明人發(fā)現(xiàn),在上述溫度條件下,保證酯化速率穩(wěn)定并達(dá)到預(yù)設(shè)的酯化率。在本發(fā)明步驟1中,在上述溫度條件下保持1~3hr,優(yōu)選為1.5~2.5hr,如1.5hr。本發(fā)明人發(fā)現(xiàn),在上述溫度條件下保溫,保溫1~3小時使酯化反應(yīng)得以繼續(xù),有利于進(jìn)一步提高酯化率。本發(fā)明人發(fā)現(xiàn),在上述溫度條件下保溫30~40min.后,補(bǔ)加乙二醇,使其酯化率達(dá)到99%以上,同時加入抗氧劑,抑制在縮聚過程中的氧化降解,因此,向反應(yīng)體系中補(bǔ)加乙二醇和抗氧劑。優(yōu)選地,向體系中補(bǔ)加熱穩(wěn)定劑,基于對苯二甲酸的總重量,以熱穩(wěn)定劑的重量計,補(bǔ)加的熱穩(wěn)定劑的量為0.05%~0.2%,優(yōu)選為0.08~0.15%,如0.1%,在本發(fā)明中,所述熱穩(wěn)定劑為亞磷酸三苯酯。在本發(fā)明步驟1中,基于對苯二甲酸的總重量,以乙二醇的重量計,補(bǔ)加的乙二醇的量為0.5%~4%,優(yōu)選為1%~3%,如2%。在本發(fā)明步驟1中,基于對苯二甲酸的總重量,以抗氧劑的重量計,補(bǔ)加的抗氧劑的量為0.03%~0.1%,優(yōu)選為0.05~0.08%,如0.07%。在本發(fā)明中,抗氧劑優(yōu)選為抗氧劑1010,抗氧劑1212等。在本發(fā)明步驟2中,在縮聚反應(yīng)過程中使反應(yīng)體系處于真空環(huán)境中。本發(fā)明人發(fā)現(xiàn),在縮聚開始階段應(yīng)使系統(tǒng)保持低真空狀態(tài),在增加反應(yīng)釜內(nèi)真空度的過程要緩慢的進(jìn)行,此時物料粘度較低,如果抽真空速度過快,容易將物料抽入真空系統(tǒng),導(dǎo)致管路堵塞。。在本發(fā)明步驟2中,所述的低真空狀態(tài)是指真空度在-30kPa~-80KPa,優(yōu)選為-50~-70kPa,如-60kPa。在反應(yīng)釜內(nèi)在低真空狀態(tài)下保持30~40min.后,再使反應(yīng)釜內(nèi)達(dá)到高真空狀態(tài)。本發(fā)明人發(fā)現(xiàn),低真空狀態(tài)保持一段時間可以防止真空系統(tǒng)堵料,避免聚合無法進(jìn)行。在本發(fā)明中,所述高真空狀態(tài)是指反應(yīng)釜內(nèi)絕對壓力在50~100Pa,優(yōu)選為50~70Pa,如50Pa。在本發(fā)明步驟2中,在高真空狀態(tài)下,使釜內(nèi)溫度升高到200℃~400℃,優(yōu)選為250℃~350℃,如280℃。本發(fā)明人發(fā)現(xiàn),在上述溫度條件下,既可以保證適宜的反應(yīng)速率,又能更好的抑制副反應(yīng)的發(fā)生,進(jìn)而保證產(chǎn)物的色相。在本發(fā)明步驟2中,攪拌的方式具體為先保持頻率在50Hz,至攪拌功率50W,再將頻率調(diào)至25Hz;待攪拌功率升至35KW,關(guān)閉攪拌,縮聚反應(yīng)結(jié)束,直到達(dá)到合適的聚合物粘度或者達(dá)到合適的聚合物分子量。任選地,還包括以下步驟:步驟3、切粒:用氮?dú)鈹D壓出料,鑄帶,再將得到PET樣條切粒得到的粒料;步驟4、烘干:將步驟3得到的粒料進(jìn)行烘干。本發(fā)明所具有的有益效果:(1)本發(fā)明中使用的復(fù)合催化劑包括鈦酸四丁酯、硅酸四乙酯和苯基膦酸,組成簡單;(2)本發(fā)明中所述制備聚對苯二甲酸乙二醇酯的反應(yīng),特定使用對苯二甲酸和乙二醇為原料;(3)在本發(fā)明提供的方法中,所用的復(fù)合催化劑的催化活性較高,具體地,催化活性約為三氧化二銻的17倍;(4)用該方法制得的聚對苯二甲酸乙二醇酯(PET)特性粘數(shù)高,而且分子量高、分子量分布窄的優(yōu)點(diǎn);(5)用該方法制得的PET玻璃化轉(zhuǎn)變溫度(Tg)、熔融溫度(Tm)冷結(jié)晶溫度(Tcc)與Sb2O3為催化劑樣品相差不大,但熱穩(wěn)定性提高;(6)用該方法制得PET的拉伸強(qiáng)力和斷裂伸長率提高。實施例以下通過具體實施例進(jìn)一步描述本發(fā)明。不過這些實施例僅僅是范例性的,并不對本發(fā)明的保護(hù)范圍構(gòu)成任何限制。實施例1復(fù)合催化劑的制備將2.23mL硅酸四乙酯加入乙二醇中,任選攪拌,得到硅酸四乙酯的二元醇溶液;將1.07mL苯基膦酸加入到上述硅酸四乙酯的二元醇溶液中,任選攪拌,然后加入20.47mL的鈦酸四丁酯中,得到復(fù)合催化劑。實施例2復(fù)合催化劑的制備將2.23mL硅酸四乙酯加入乙二醇中,任選攪拌,得到硅酸四乙酯的二元醇溶液;將1.61mL苯基膦酸加入到上述硅酸四乙酯的二元醇溶液中,任選攪拌,然后加入27.33mL的鈦酸四丁酯中,得到復(fù)合催化劑。實施例3復(fù)合催化劑的制備將2.23mL硅酸四乙酯加入乙二醇中,任選攪拌,得到硅酸四乙酯的二元醇溶液;將2.14mL苯基膦酸加入到上述硅酸四乙酯的二元醇溶液中,任選攪拌,然后加入30.75mL的鈦酸四丁酯中,得到復(fù)合催化劑。實施例4復(fù)合催化劑的制備將2.23mL硅酸四乙酯加入乙二醇中,任選攪拌,得到硅酸四乙酯的二元醇溶液;將2.68mL苯基膦酸加入到上述硅酸四乙酯的二元醇溶液中,任選攪拌,然后加入34.17mL的鈦酸四丁酯中,得到復(fù)合催化劑。實施例5復(fù)合催化劑的制備將2.23mL硅酸四乙酯加入乙二醇中,任選攪拌,得到硅酸四乙酯的二元醇溶液;將3.22mL苯基膦酸加入到上述硅酸四乙酯的二元醇溶液中,任選攪拌,然后加入41.00mL的鈦酸四丁酯中,得到復(fù)合催化劑。實施例6聚對苯二甲酸乙二醇酯的合成酯化反應(yīng)階段:向聚合釜中加入700gPTA、314gEG、0.0112g實施例3制備的復(fù)合催化劑(以其中的鈦元素的重量計),然后打開攪拌,從室溫加熱到釜內(nèi)溫230℃,控制釜內(nèi)壓力處于300-350KPa至出水量50mL,全開出水針閥,在常壓下補(bǔ)加13gEG、0.4g抗氧化劑1010和0.7g熱穩(wěn)定劑亞磷酸三苯酯。攪拌反應(yīng)40min,釜內(nèi)溫升到260℃,酯化反應(yīng)階段結(jié)束??s聚反應(yīng)階段:先處于低真空階段30-40min,此過程要緩慢的進(jìn)行,防止抽真空過快造成釜內(nèi)物料被吸出堵塞管道,待此階段結(jié)束后,再進(jìn)入高真空階段(反應(yīng)釜內(nèi)絕對壓力為50Pa),釜內(nèi)溫逐漸到280℃,先保持頻率在50Hz,至攪拌功率50W,再將頻率調(diào)至25Hz,待攪拌功率升至35KW。關(guān)閉攪拌,縮聚反應(yīng)結(jié)束。實施例7聚對苯二甲酸乙二醇酯的合成酯化反應(yīng)階段:向聚合釜中加入700gPTA、314gEG和0.0126g實施例3制備的復(fù)合催化劑(以其中的鈦元素的重量計),打開攪拌,從室溫加熱到釜內(nèi)溫230℃,控制釜內(nèi)壓力處于300-350KPa至出水量50mL,全開出水針閥,在常壓下補(bǔ)加13gEG、0.4g抗氧化劑1010和0.7g熱穩(wěn)定劑亞磷酸三苯酯。攪拌反應(yīng)40min,釜內(nèi)溫升到260℃,酯化反應(yīng)階段結(jié)束??s聚反應(yīng)階段:先處于低真空階段30-40min,此過程要緩慢的進(jìn)行,防止抽真空過快造成釜內(nèi)物料被吸出堵塞管道,待此階段結(jié)束后,再進(jìn)入高真空階段(反應(yīng)釜內(nèi)絕對壓力為50Pa),釜內(nèi)溫逐漸到280℃,先保持頻率在50Hz,至攪拌功率50W,再將頻率調(diào)至25Hz,待攪拌功率升至35KW。關(guān)閉攪拌,縮聚反應(yīng)結(jié)束。實施例8聚對苯二甲酸乙二醇酯的合成酯化反應(yīng)階段:向聚合釜中加入700gPTA、314gEG、0.0133g實施例3制備的復(fù)合催化劑(以其中的鈦元素的重量計),打開攪拌,從室溫加熱到釜內(nèi)溫230℃,控制釜內(nèi)壓力處于300-350KPa至出水量50mL,全開出水針閥,在常壓下補(bǔ)加13gEG、0.4g抗氧化劑1010和0.7g熱穩(wěn)定劑亞磷酸三苯酯。攪拌反應(yīng)40min,釜內(nèi)溫升到260℃,酯化反應(yīng)階段結(jié)束??s聚反應(yīng)階段:先處于低真空階段30-40min,此過程要緩慢的進(jìn)行,防止抽真空過快造成釜內(nèi)物料被吸出堵塞管道,待此階段結(jié)束后,再進(jìn)入高真空階段,釜內(nèi)溫逐漸到280℃,先保持頻率在50Hz,至攪拌功率50W,再將頻率調(diào)至25Hz,待攪拌功率升至35KW。關(guān)閉攪拌,縮聚反應(yīng)結(jié)束。實施例9聚對苯二甲酸乙二醇酯的合成酯化反應(yīng)階段:向聚合釜中加入700gPTA、314gEG、0.014g實施例3制備的復(fù)合催化劑(以其中的鈦元素的重量計),從室溫加熱到釜內(nèi)溫230℃,控制釜內(nèi)壓力處于300-350KPa至出水量50mL,全開出水針閥,在常壓下補(bǔ)加13gEG、0.4g抗氧化劑1010和0.7g熱穩(wěn)定劑亞磷酸三苯酯。攪拌反應(yīng)40min,釜內(nèi)溫升到260℃,酯化反應(yīng)階段結(jié)束??s聚反應(yīng)階段:先處于低真空階段30-40min,此過程要緩慢的進(jìn)行,防止抽真空過快造成釜內(nèi)物料被吸出堵塞管道,待此階段結(jié)束后,再進(jìn)入高真空階段(反應(yīng)釜內(nèi)絕對壓力為50Pa),釜內(nèi)溫逐漸到280℃,先保持頻率在50Hz,至攪拌功率50W,再將頻率調(diào)至25Hz,待攪拌功率升至35KW。關(guān)閉攪拌,縮聚反應(yīng)結(jié)束。實施例10聚對苯二甲酸乙二醇酯的合成酯化反應(yīng)階段:向聚合釜中加入700gPTA、314gEG、0.0154g實施例3制備的復(fù)合催化劑(以其中的鈦元素的重量計),打開攪拌,從室溫加熱到釜內(nèi)溫230℃,控制釜內(nèi)壓力處于300-350KPa至出水量50mL,全開出水針閥,在常壓下補(bǔ)加13gEG、0.4g抗氧化劑1010和0.7g熱穩(wěn)定劑亞磷酸三苯酯。攪拌反應(yīng)40min,釜內(nèi)溫升到260℃,酯化反應(yīng)階段結(jié)束??s聚反應(yīng)階段:先處于低真空階段30-40min,此過程要緩慢的進(jìn)行,防止抽真空過快造成釜內(nèi)物料被吸出堵塞管道,待此階段結(jié)束后,再進(jìn)入高真空階段(反應(yīng)釜內(nèi)絕對壓力為50Pa),釜內(nèi)溫逐漸到280℃,先保持頻率在50Hz,至攪拌功率50W,再將頻率調(diào)至25Hz,待攪拌功率升至35KW。關(guān)閉攪拌,縮聚反應(yīng)結(jié)束。對比例對比例1重復(fù)實施例3的合成過程,區(qū)別在于,用乙二醇鈦替代鈦酸四丁酯,且不添加苯基膦酸,制得二元復(fù)合催化劑。對比例2重復(fù)實施例3的合成過程,區(qū)別在于,用乙二醇鈦替代鈦酸四丁酯,制得復(fù)合催化劑。對比例3重復(fù)實施例8的合成過程,區(qū)別在于,催化劑采用三氧化二銻(Sb2O3),且用量為334μg/g,其中,基于1g對苯二甲酸,Sb元素的用量為334μg。對比例4重復(fù)實施例8的合成過程,區(qū)別在于,催化劑采用乙二醇鈦。對比例5重復(fù)實施例8的合成過程,區(qū)別在于,催化劑采用對比例1制備的二元復(fù)合催化劑。對比例6重復(fù)實施例8的合成過程,區(qū)別在于,催化劑采用對比例2制備的復(fù)合催化劑。對比例7重復(fù)實施例8的合成過程,區(qū)別在于,在縮聚反應(yīng)階段加入實施例3制備的復(fù)合催化劑。實驗例實驗例1色度測試色相是PET產(chǎn)品的一項重要指標(biāo),通常用L值,b值表示。當(dāng)L值越大,產(chǎn)品的亮度越大,產(chǎn)品就會越白,反之越黑;產(chǎn)品的b值越大,產(chǎn)品的顏色越黃,反之越藍(lán)。通常鈦系催化劑合成PET的L值大,說明PET產(chǎn)品亮度好,b值高,表明產(chǎn)品偏黃,這是因為鈦系催化劑由于催化活性高,在催化酯化、縮聚主反應(yīng)的同時也催化很多副反應(yīng),同時體系內(nèi)鏈交換反應(yīng)加劇,導(dǎo)致產(chǎn)物色相變黃。本發(fā)明采用北京康光光學(xué)儀器有限公司生產(chǎn)的SC-100全自動色差計,分別對實施例8和對比例3~6合成的聚對苯二甲酸乙二醇酯進(jìn)行測試,得樣品的色度b值和L值。其中,測試溫度為室溫,測試次數(shù)為5次,結(jié)果取平均值,測試結(jié)果如表1所示。表1實施例8和對比例3~6合成的樣品的b值和L值樣品催化劑用量(μg/g)b值L值實施例8196.8342.69對比例33344.2233.67對比例4199.3741.77對比例5198.3242.07對比例6197.5141.65注:樣品均為大有光PET。由表1可以看出:(1)在實施例8和對比例4~對比例6中,實施例8得到的樣品的b值最小,L值最大,說明,利用本發(fā)明所述的復(fù)合催化劑得到的PET發(fā)黃程度偏低;(2)實施例8得到的樣品的b值高于對比例3得到的樣品的b值,那是因為鈦系催化劑本身特點(diǎn)所致,其得到的產(chǎn)品會稍微發(fā)黃,但是對于實施例8而言,其發(fā)黃程度已經(jīng)得到了明顯改善,并且可以滿足使用要求,因此,本發(fā)明所述復(fù)合催化劑優(yōu)于毒性的三氧化二銻。實驗例2差示掃描量熱(DSC)測試本實驗例所用樣品為實施例8和對比例3~6制得。采用日本SeikoInstrumentsInc.的SeikoDSC-6200型差示掃描量熱儀對上述樣品進(jìn)行測試,其中,氮?dú)饬魉贋?0mL/min狀態(tài)下,溫度范圍為30℃-300℃,升溫速率為10℃/min,試樣重量6-10mg,測試結(jié)果如圖1所示,其中,曲線1表示對比例3制得樣品的DSC曲線;曲線2表示對比例4制得樣品的DSC曲線;曲線3表示對比例5制得樣品的DSC曲線;曲線4表示對比例6制得樣品的DSC曲線;曲線5表示實施例8制得樣品的DSC曲線;由圖1可得表2所示數(shù)據(jù):表2PET樣品的轉(zhuǎn)變溫度和結(jié)晶度樣品Tg(℃)Tcc(℃)Tm(℃)Xcc(%)對比例373.6132.3249.830.1對比例473.9137.2252.328.7對比例573.5141.2252.126.3對比例673.7140.2254.227.1實施例873.0141.0252.926.6由表2可以看出,實施例8得到的樣品的玻璃化轉(zhuǎn)變溫度與對比例3得到的樣品的玻璃化轉(zhuǎn)變溫度相差無幾,幾乎一致,但是,實施例8得到的樣品的熔融溫度和冷結(jié)晶溫度均有所升高。由表2還可以看出,本發(fā)明提供的復(fù)合催化劑的使用量(催化劑的用量以Ti:PTA質(zhì)量比計)少,所合成的PET分子量分布窄,PET分子量與用三氧化二銻合成的PET相近,甚至?xí)摺1景l(fā)明提供的復(fù)合催化劑合成的PET樣品的玻璃化轉(zhuǎn)變溫度(Tg)、熔融溫度(Tm)、冷結(jié)晶溫度(Tcc)與三氧化二銻催化合成的PET樣品的玻璃化轉(zhuǎn)變溫度(Tg)、熔融溫度(Tm)、冷結(jié)晶溫度(Tcc)相差不大,表明兩種催化劑合成的產(chǎn)物組成、結(jié)構(gòu)極其相近。實驗例3熱失重(TG)測試本實驗例所用樣品為實施例8、對比例3、4和6制得。操作方法或儀器:采用北京光學(xué)儀器廠生產(chǎn)的WCT-2D微機(jī)差熱天平測試,在氮?dú)獾谋Wo(hù)下進(jìn)行測試樣品聚酯的熱穩(wěn)定性。溫度范圍0-800℃,升溫速率為10℃/min,氮?dú)饬魉?00ml/min,試樣重量為6.0-8.0mg。測試結(jié)果如圖2和圖3所示,其中,圖2示出樣品的TG測試曲線;圖3示出樣品的DTG曲線。在圖2中,曲線1表示對比例3制得樣品的TG曲線;曲線2表示對比例4制得樣品的TG曲線;曲線3表示對比例6制得樣品的TG曲線;曲線4表示實施例8制得樣品的TG曲線;在圖3中,曲線1表示對比例3樣品的DTG曲線;曲線2表示對比例4制得樣品的DTG曲線;曲線3表示對比例6制得樣品的DTG曲線;曲線4表示實施例8制得樣品的DTG曲線。將各樣品的失重率對應(yīng)溫度列表如下表3表3失重率對應(yīng)溫度(℃)由圖2和圖3以及表3可知,本發(fā)明提供的復(fù)合催化劑合成的PET樣品熱穩(wěn)定性比三氧化二銻催化合成的PET樣品的熱穩(wěn)定性有所提高。聚合物的無氧熱降解一般分為兩個歷程,其一為消除反應(yīng),即消除一些低分子揮發(fā)性物質(zhì),如H2、H2O、HCl等,而聚合物的大分子主鏈基本不變;另一為大分子主鏈發(fā)生斷裂裂解。PET的熱降解主要是鏈端熱降解和鏈間熱降解,其中鏈間熱降解是與之機(jī)相連的β位碳原子上的氫原子先斷裂,導(dǎo)致相對分子量下降,生成碳基和乙烯基;二鏈端熱降解則導(dǎo)致乙醛的生成,造成樣品質(zhì)量的下降。由分子量分析可知,本發(fā)明提供的復(fù)合催化劑的活性高,效率高,催化合成的PET分子量比三氧化二銻催化合成的PET分子量大,所以PET的起始分解溫度有所升高,相較于三氧化二銻催化合成的PET熱穩(wěn)定性略有提高,PET的鏈端的熱降解反應(yīng)得到了有效的抑制,從而使失重溫度升高。實驗例4力學(xué)性能測試本實驗例所用樣品為實施例8、對比例3~5制得。采用INSTRON5966萬能電子材料試驗機(jī),分別對實施例8和對比例3~5進(jìn)行測試,測試結(jié)果如表3所示,其中,試樣標(biāo)距為25mm,拉伸速率為10mm/min,測試標(biāo)準(zhǔn)根據(jù)GB/T1040-92。表4力學(xué)性能測試結(jié)果由表4可以看出,由實施例8得到的樣品兼具高的拉伸強(qiáng)度和高的斷裂伸長率,其中,與對比例3(以Sb2O3為催化劑)相比,實施例8得到的樣品的拉伸強(qiáng)度提高20.4%,斷裂伸長率提高61.8%。其中,在表4中,實施例8制得產(chǎn)品的拉伸強(qiáng)度增大百分比和斷裂伸長率增大百分比均是以對比例3得到的樣品的試驗值為基礎(chǔ)。實驗例5凝膠滲透色譜(GPC)本實驗例所用樣品為實施例8、對比例3和5制得。采用Water公司的GPC515-2410System凝膠色譜儀分別對實施例8和對比例3~5合成的聚對苯二甲酸乙二醇酯進(jìn)行測試,表征樣品的分子量及分子量分布,其中,以間甲酚為溶劑,試樣濃度3-4mg/ml,流速1.0ml/min,標(biāo)準(zhǔn)樣品為聚苯乙烯(PS),檢測器溫度為100℃。其中,檢測結(jié)果如表5所示。表5實施例8、對比例3和對比例5合成的樣品的分子量及分子量分布樣品Mw(×104)Mw/Mn實施例84.361.82對比例33.851.94對比例53.261.86由表5可知,實施例8制得的樣品的分子量均大于對比例3和對比例5得到的樣品的分子量,且實施例8制得的樣品的分子量分布較低,說明,利用本發(fā)明所述復(fù)合催化劑可以得到高分子量和低分子量分布的PET產(chǎn)物。實驗例6反應(yīng)速率常數(shù)分析該實驗例所用樣品為對比例3及實施例8制得??s聚動力學(xué)的取樣:聚酯PET聚合進(jìn)入縮聚階段,一開始先處于低真空階段30-40min,此過程要緩慢的進(jìn)行,防止抽真空過快造成釜內(nèi)物料被吸出堵塞管道,待此階段結(jié)束后,再進(jìn)入高真空階段,釜內(nèi)溫逐漸到280℃,先保持頻率在50Hz,至攪拌功率50W,再將頻率調(diào)至25Hz,待攪拌功率升至35KW。在此過程中,每間隔一定時間,在氮?dú)獗Wo(hù)作用下用鋼棒從加料口取樣。聚酯的縮聚反應(yīng)是二級可逆平衡反應(yīng)縮聚反應(yīng)可按G.Rafler方程計算:積分整理得:公式中:COH為羥乙酯基濃度;k為反應(yīng)速度常數(shù);為t時刻聚合物的平均相對分子質(zhì)量;為起始反應(yīng)物的平均相對分子質(zhì)量。在縮聚反應(yīng)中定時取樣,測其特性黏度[η],按公式(3)計算可得其平均相對分子質(zhì)量。其中K=2.1×10-4,α=0.82依據(jù)上述方法,以平均相對分子質(zhì)量對縮聚反應(yīng)時間作圖可得縮聚反應(yīng)的動力學(xué)曲線,對數(shù)據(jù)進(jìn)行線性回歸處理可得各反應(yīng)的速率常數(shù)。結(jié)果如圖4及表6所示,在圖4中,曲線1表示實施例8制得樣品的速率常數(shù)曲線;曲線2表示對比例3制得樣品的速率常數(shù)曲線。表6催化劑對切片顏色及縮聚反應(yīng)速率的影響由圖4及表6可知,實施例8制得的復(fù)合催化劑的反應(yīng)的速率常數(shù)為91.00k/[g.(mol.min)-1],對比例3制得的催化劑的反應(yīng)的速率常數(shù)為81.51k/[g.(mol.min)-1],由此可見,本發(fā)明催化劑在添加量僅為對比例的1/17的情況下,縮聚反應(yīng)速率仍然高于對比例。實驗例7催化活性分析本實驗例所用樣品為實施例8、對比例3、4和6制得。實驗操作方法和儀器同實驗例6,催化劑活性是通過催化劑添加量計算得到,結(jié)果如表7所示,表7不同催化劑的用量以及合成所需時間表在表7中,以對比例3催化劑的活性為標(biāo)準(zhǔn),即,將對比例3催化劑的催化活性值記為1倍,其它催化劑的催化活性值與該值進(jìn)行比較,得出其它催化劑的催化活性倍數(shù)。由表7可知,因為對苯二甲酸PTA和乙二醇EG的酯化反應(yīng)為自催化反應(yīng),用本發(fā)明提供的復(fù)合催化劑合成PET時,酯化時間縮短,所以說明本發(fā)明提供的復(fù)合催化劑對酯化反應(yīng)有一定的催化作用,原因是本發(fā)明提供的復(fù)合催化劑中含有的鈦金屬元素能與對苯二甲酸PTA和對苯二甲酸乙二醇酯(BHET)進(jìn)行配位絡(luò)合反應(yīng),鈦金屬元素增加了其羰基碳的正電性,有利于乙二醇EG的羥基進(jìn)行親核攻擊,加快酯化反應(yīng)速率。本發(fā)明提供的復(fù)合催化劑用量(催化劑的用量以Ti:PTA質(zhì)量比計)為19ug.g-1時,縮聚時間為160min,Sb2O3催化劑的用量為334ug.g-1,縮聚時間為160min。由此可見,本發(fā)明提供的復(fù)合催化劑用量為19ug.g-1的催化活性相當(dāng)于Sb2O3用量為334ug.g-1的催化活性,由此,能夠推算出,本發(fā)明提供的復(fù)合催化劑的催化活性是Sb2O3催化活性的17倍。乙二醇鈦的催化活性高于17倍,由于乙二醇鈦催化活性過高,導(dǎo)致PET產(chǎn)品的b值過高,顏色過黃。實驗例8不同聚合時間對PET產(chǎn)品特性粘度的影響本實驗例所用樣品為實施例3和對比例3制得。操作方法:將四氯乙烷和苯酚按質(zhì)量比1:1混合均勻,相對密度為1.2850g/ml(20℃)的混合溶劑。利用烏氏粘度計測試試樣的特性粘度。其中,特性黏數(shù)與平均相對分子量存在以下關(guān)系,毛細(xì)管直徑為0.8mm,恒溫水浴溫度為25±0.1℃,計算公式為:其中:[η]為特性粘度,t0為純?nèi)軇┑牧鞒鰰r間,ηr=t/t0為相對粘度,ηsp=(ηr-1)為增比粘度,c為溶液中聚合物濃度。結(jié)果如圖5及表8所示,在圖5中,曲線1表示實施例8制得樣品的特性粘度曲線;曲線2表示對比例6制得樣品的特性粘度曲線。表8不同聚合時間制得產(chǎn)品的特性粘數(shù)[η]由圖5及表8可知,在相同的聚合時間內(nèi),達(dá)到相同的攪拌功率,用本發(fā)明提供的復(fù)合催化劑催化合成的PET特性粘數(shù)高,是因為本發(fā)明提供的復(fù)合催化劑的活性高,催化效率高,合成的PET分子量高且分子量分布窄。實驗例9復(fù)合催化劑加入時機(jī)對反應(yīng)時間以及PET產(chǎn)品色相的影響本實驗例所用樣品由對比例2及實施例3制得,結(jié)果如下表9所示:表9復(fù)配催化劑加入時機(jī)對合成PET反應(yīng)時間及色相的影響由表9可知,在合成PET過程中,在縮聚階段加入催化劑比酯化階段添加催化劑時酯化和縮聚速率明顯變慢,聚合時間顯著增長,合成的PET的色相較差。不受任何理論束縛,本發(fā)明人認(rèn)為,本發(fā)明提供的復(fù)合催化劑對酯化和縮聚均有催化作用,酯化階段加入提高了酯化速率,使酯化時間縮短;同時由于酯化階段加入,經(jīng)歷攪拌時間長,比在縮聚前加入催化劑的分散性好,且本發(fā)明提供的復(fù)合催化劑和對苯二甲酸雙羥乙酯形成了穩(wěn)定的絡(luò)合物,復(fù)合催化劑穩(wěn)定性高,水解失活率低,因此縮聚反應(yīng)速率也高,反應(yīng)時間縮短。相反,在縮聚階段加入,由于反應(yīng)釜內(nèi)的高溫環(huán)境,復(fù)合催化劑穩(wěn)定性差,使本發(fā)明提供的復(fù)合催化劑發(fā)生水解,降低了該復(fù)合催化劑的活性,降低了復(fù)合催化劑的效率,且由于攪拌時間短,復(fù)合催化劑分散性較差,導(dǎo)致縮聚反應(yīng)時間顯著增長。另外,本發(fā)明提供的復(fù)合催化劑由于催化活性高,在催化酯化、縮聚主反應(yīng)的同時也催化很多副反應(yīng),同時體系內(nèi)鏈交換反應(yīng)加劇,導(dǎo)致產(chǎn)物色相變黃。實驗例10復(fù)合催化劑加入時機(jī)對合成PET分子量及分子量分布的影響本實驗例所用樣品由對比例2及實施例3制得,用凝膠滲透色譜(GPC)測試PET聚合物的分子量及其分子量分布,測試結(jié)果見表10。表10復(fù)配催化劑加入時機(jī)對合成PET分子量及分子量分布的影響由表10可知,對于對比例2制得的催化劑,加入時機(jī)對合成的PET的分子量和分子量分布影響不大。而對于實施例3制得的復(fù)合催化劑加入時機(jī)對合成的PET的分子量影響較大但對分子量分布影響不明顯,縮聚前加入催化劑合成的PET的分子量明顯比酯化前加入催化劑合成PET的分子量低。不受任何理論束縛,本發(fā)明人認(rèn)為:在縮聚階段加入,由于反應(yīng)釜內(nèi)的高溫環(huán)境,催化劑穩(wěn)定性差,使鈦系催化劑發(fā)生水解,且鈦酸丁酯最容易受到水的攻擊。而乙二醇鈦由于水解熱力學(xué)推動勢相對較小,并且由于乙二醇溶劑的粘度較高,反應(yīng)比較緩慢,所以鈦酸四丁酯水解程度高,降低了對比例2催化劑的活性,在相同的聚合時間內(nèi)所達(dá)到的分子量變低。實驗例11復(fù)合催化劑加入時機(jī)對合成PET熱性能的影響本實驗例所用樣品為對比例2和實施例3制得,進(jìn)行DSC測試,結(jié)果如圖6~圖7和表11所示,在圖6中,曲線4表示對比例2制得催化劑在酯化前加入;曲線4’表示對比例2制得催化劑在縮聚前加入;在圖7中,曲線5表示實施例3制得催化劑在酯化前加入;曲線5’表示實施例3制得催化劑在縮聚前加入;表11復(fù)配催化劑加入時機(jī)對合成PET熱性能的影響催化劑加入時機(jī)Tg(℃)Tcc(℃)Tm(℃)Xcc(%)對比例2酯化階段73.7140.2254.234.0對比例2縮聚階段72.7135.8251.630.1實施例3酯化階段73.0141.0252.926.6實施例3縮聚階段72.3136.2252.329.8由圖6、圖7和表11可知,酯化前加入催化劑合成的PET比縮聚前加入催化劑合成的PET冷結(jié)晶溫度(Tcc)均有升高,玻璃化轉(zhuǎn)變溫度(Tg)、熔融溫度(Tm)基本一致。其可能的原因是:縮聚階段加入催化劑,由于攪拌時間比酯化階段加入催化劑時間短,催化劑的分散性較差,導(dǎo)致大分子鏈的運(yùn)動能力下降,不利于大分子鏈段向晶格擴(kuò)散,因此晶粒的生長速度較慢,所以冷結(jié)晶溫度(Tcc)均有升高。實驗例12復(fù)合催化劑加入時機(jī)對合成PET熱穩(wěn)定性的影響本實驗例所用樣品由實施例3制得。熱失重(TG)測試反映了聚合物的熱穩(wěn)定性,測試結(jié)果見圖8~圖11,不同失重率對應(yīng)的溫度見表12,在圖8中,曲線4表示對比例2制得催化劑在酯化前加入;曲線4’表示對比例2制得催化劑在縮聚前加入;在圖9中,曲線4表示對比例2制得催化劑在酯化前加入;曲線4’表示對比例2制得催化劑在縮聚前加入;在圖10中,曲線5表示實施例3制得催化劑在酯化前加入;曲線5’表示實施例3制得催化劑在縮聚前加入;在圖11中,曲線5表示實施例3制得催化劑在酯化前加入;曲線5’表示實施例3制得催化劑在縮聚前加入。表12復(fù)配催化劑加入時機(jī)對合成PET熱穩(wěn)定性的影響由圖8~圖11及表12可知,對于對比例2的樣品在縮聚前加入催化劑合成的PET比酯化前加入催化劑合成的PET的熱穩(wěn)定性有所提高。而對于實施例3的樣品在縮聚前加入催化劑合成的PET比酯化前加入催化劑合成的PET的熱穩(wěn)定性有所降低。不受任何理論束縛,本發(fā)明人認(rèn)為:對于對比例2的樣品,在縮聚前加入催化劑合成的PET分子量比酯化前合成的分子量大,分子量分布窄,所以聚酯的起始分解溫度都有所升高,從而使失重溫度略有提高。對于實施例3的樣品,在縮聚前加入催化劑合成的PET分子量比酯化前合成的分子量小,所以聚酯的起始分解溫度都有所降低,從而使失重溫度略有降低。實驗例13復(fù)配催化劑加入時機(jī)對合成PET力學(xué)性能的影響本實驗例所用樣品為對比例2及實施例3制得,結(jié)果如表13所示:表13復(fù)合催化劑加入時機(jī)對合成PET力學(xué)性能的影響由表13可知,對于對比例2的樣品,加入時機(jī)對合成的PET的力學(xué)性能的影響不大;而對于實施例3的樣品,加入時機(jī)對合成的PET的較大,縮聚前加入催化劑合成PET切片比酯化前加入催化劑合成PET切片的拉伸強(qiáng)度和斷裂伸長率均有降低。不受任何理論的束縛,本發(fā)明人認(rèn)為:在縮聚階段加入,由于反應(yīng)釜內(nèi)的高溫環(huán)境,催化劑穩(wěn)定性差,使鈦系催化劑發(fā)生水解,降低了鈦系催化劑的活性,在相同的聚合時間內(nèi)所達(dá)到的分子量變低,導(dǎo)致PET切片的力學(xué)性能變差。根據(jù)上述分析可知,復(fù)配催化劑的加入時機(jī)最好在酯化階段前加入。實驗例14復(fù)合催化劑用量對酯化時間的影響本實驗例所用樣品為實施例3制得,分別以9.5ug.g-1,19ug.g-1,28.5ug.g-1,38ug.g-1的量合成PET,研究該催化劑不同用量對酯化時間的影響,結(jié)果如圖12所示。由圖12可知,對苯二甲酸PTA和乙二醇EG的酯化反應(yīng)為自催化反應(yīng),實施例3制得樣品對酯化反應(yīng)有一定的催化作用,隨著實施例3制得樣品用量的增加,酯化時間逐漸的縮短,在達(dá)到要求的酯化率下,最多縮短酯化時間40min。不受任何理論束縛,本發(fā)明人認(rèn)為:該復(fù)配催化劑中含有的鈦金屬元素能與對苯二甲酸PTA和對苯二甲酸乙二醇酯(BHET)進(jìn)行配位絡(luò)合反應(yīng),金屬元素增加了其羰基碳的正電性,有利于乙二醇EG的羥基進(jìn)行親核攻擊,加快酯化反應(yīng)速率;在催化劑用量(催化劑的用量以Ti:PTA質(zhì)量比計)為38ug.g-1時催化效果最明顯。實驗例15復(fù)合催化劑用量對縮聚時間的影響本實驗例所用樣品為實施例3制得,分別以9.5ug.g-1,19ug.g-1,28.5ug.g-1,38ug.g-1的量合成PET,研究該催化劑不同用量對縮聚時間的影響,結(jié)果如圖13所示。由圖13所示,開始隨著實施例3樣品的用量(催化劑的用量以Ti:PTA質(zhì)量比計)的增加,縮聚反應(yīng)速率加快,聚合時間縮短,其后隨著實施例3樣品用量增加,縮聚反應(yīng)速率變慢,聚合時間逐漸延長,不受任何理論束縛,本發(fā)明人認(rèn)為:主要原因是本發(fā)明提供的復(fù)合催化劑催化活性高,在催化縮聚主反應(yīng)的同時也催化很多副反應(yīng),復(fù)合催化劑的用量過多使得副反應(yīng)速度加快,同時體系內(nèi)鏈交換反應(yīng)加劇,導(dǎo)致縮聚時間延長,同時鈦含量的增加會影響PET的熱穩(wěn)定性和色度。復(fù)合催化劑用量為19ug.g-1時,縮聚時間為170min,而前述Sb2O3催化劑的用量為334ug.g-1時,縮聚時間為160min。由此可見,實施例3樣品用量為19ug.g-1的催化活性相當(dāng)于Sb2O3用量為334ug.g-1的催化活性,該復(fù)合催化劑的催化活性大約是Sb2O3催化活性的17倍。實驗例16復(fù)合催化劑用量對合成PET特性黏數(shù)[η]的影響本實驗例所用樣品為實施例3制得,分別以9.5ug.g-1,19ug.g-1,28.5ug.g-1,38ug.g-1的量合成PET,研究該催化劑不同用量對PET特性黏數(shù)[η]的影響,結(jié)果如表14所示。表14不同催化劑用量對合成PET特性黏數(shù)[η]的影響由表14可知,開始合成出的PET的[η]隨著該催化劑的用量(催化劑的用量以Ti:PTA質(zhì)量比計)增加,變大,其后隨著該催化劑的用量增大,變小。不受任何理論束縛,本發(fā)明人認(rèn)為:本發(fā)明提供的復(fù)合催化劑催化活性高,在催化縮聚主反應(yīng)的同時也催化很多副反應(yīng),催化劑的用量過多使得副反應(yīng)速度加快,同時體系內(nèi)鏈交換反應(yīng)加劇,導(dǎo)致在相同時間內(nèi)合成出的PET的[η]先隨量的增加變大后隨催化劑的用量增加合成PET的[η]變小。由此可見,實施例3樣品的最佳用量為19ug.g-1。實驗例17復(fù)合催化劑用量對合成PET色相的影響本實驗例所用樣品為實施例3制得,分別以9.5ug.g-1,19ug.g-1,28.5ug.g-1,38ug.g-1的量合成PET,研究該催化劑不同用量對PET色相的影響,結(jié)果如圖14和表15所示,在圖14中,箭頭指示出該曲線對應(yīng)的縱坐標(biāo)。表15催化劑用量對PET色相的影響注:樣品均為大有光PET。由圖14和表15可知,PET產(chǎn)品b值隨著實施例3樣品用量的增加先減小達(dá)到一個最小值,然后再增加,不受任何理論束縛,本發(fā)明人認(rèn)為:這是因為隨著催化劑的用量的增加,其他的副反應(yīng)的反應(yīng)速率也增加,導(dǎo)致b值升高;L值隨著催化劑用量的增加而逐漸減?。痪C合考慮L值和b值,實施例3樣品的最佳用量為19ug.g-1。實驗例18復(fù)合催化劑用量對合成PET熱性能的影響本實驗例所用樣品為實施例3制得,分別以9.5ug.g-1,19ug.g-1,28.5ug.g-1,38ug.g-1的量合成PET,研究該催化劑不同用量對PET熱性能的影響,結(jié)果如圖15和表16所示。表16催化劑用量對PET熱性能的影響由圖15和表16可知,不同用量實施例3制得樣品的制備出的PET相比,玻璃化轉(zhuǎn)變溫度(Tg),熔融溫度(Tm)、冷結(jié)晶溫度(Tcc)基本一致。說明實施例3制得樣品的用量對制備出的PET的熱性能基本沒有影響。實驗例19復(fù)合催化劑用量對合成PET熱穩(wěn)定性的影響本實驗例所用樣品為實施例3制得,分別以9.5ug.g-1,19ug.g-1,28.5ug.g-1,38ug.g-1的量合成PET,研究該催化劑不同用量對PET熱穩(wěn)定性的影響,結(jié)果如圖16、圖17和表17所示,其中,圖16示出不同催化劑用量制得PET的TG曲線;圖17示出不同催化劑用量制得PET的DTG曲線。表17催化劑用量對PET熱穩(wěn)定性的影響由圖16、圖17和表17可知,實施例3制得樣品,在所研究的催化劑添加量范圍內(nèi),以不同用量合成出的PET樣品,在不同失重率對應(yīng)的溫度基本沒有變化,說明合成出的PET的熱穩(wěn)定性基本無差別。實驗例20復(fù)合催化劑用量對合成PET力學(xué)性能的影響本實驗例所用樣品為實施例3制得,分別以9.5ug.g-1,19ug.g-1,28.5ug.g-1,38ug.g-1的量合成PET,研究該催化劑不同用量對力學(xué)性能的影響,將合成出的PET制成啞鈴型樣條,進(jìn)行力學(xué)性能測試,研究該催化劑不同用量對合成PET力學(xué)性能的影響,力學(xué)性能測試結(jié)果見表18。表18PET啞鈴型樣條力學(xué)性能測試結(jié)果由表18可知,用實施例3制得樣品合成的PET的拉伸強(qiáng)度隨著催化劑用量的增加,先變大后變?。粩嗔焉扉L率隨著催化劑用量的增加,先變大后變小。在催化劑用量為19ug.g-1時,制得的PET樣條的拉伸強(qiáng)度最好,斷裂伸長率最高,這表明該催化劑的最佳用量是19ug.g-1。不受任何理論束縛,本發(fā)明人認(rèn)為:力學(xué)性能與分子結(jié)構(gòu)、分子量和超分子結(jié)構(gòu)有關(guān),本發(fā)明提供的復(fù)合催化劑催化活性高,在催化縮聚主反應(yīng)的同時也催化很多副反應(yīng),復(fù)合催化劑的用量過多使得副反應(yīng)速度加快,同時反應(yīng)體系內(nèi)鏈交換反應(yīng)加劇,導(dǎo)致在相同時間內(nèi)合成出的PET的分子量先隨量的增加變大后隨復(fù)合催化劑的用量增加合成PET的分子量變小,所以導(dǎo)致PET樣品的拉伸強(qiáng)度隨著催化劑用量的增加,先變大后變小;斷裂伸長率隨著催化劑用量的增加,先變大后變小。以上結(jié)合具體實施方式和范例性實例對本發(fā)明進(jìn)行了詳細(xì)說明,不過這些說明并不能理解為對本發(fā)明的限制。本領(lǐng)域技術(shù)人員理解,在不偏離本發(fā)明精神和范圍的情況下,可以對本發(fā)明技術(shù)方案及其實施方式進(jìn)行多種等價替換、修飾或改進(jìn),這些均落入本發(fā)明的范圍內(nèi)。本發(fā)明的保護(hù)范圍以所附權(quán)利要求為準(zhǔn)。當(dāng)前第1頁1 2 3