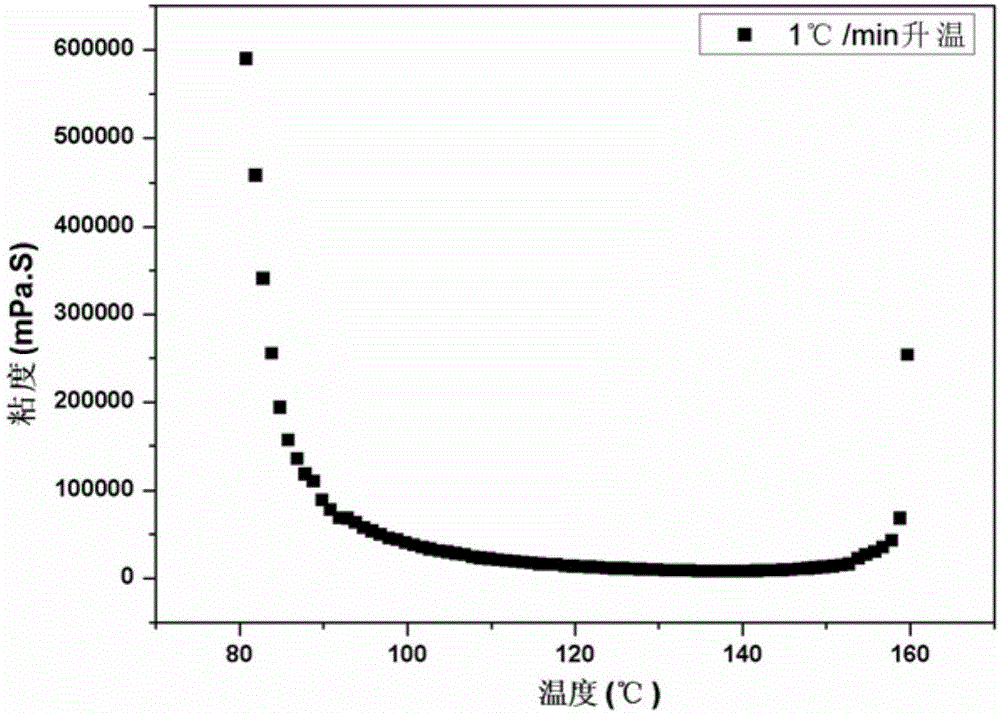
本發(fā)明涉及一種流動(dòng)可控的雙馬樹脂體系、制備方法及熱熔預(yù)浸料,屬于復(fù)合材料領(lǐng)域中原材料制備領(lǐng)域。
背景技術(shù):
:先進(jìn)樹脂基復(fù)合材料已發(fā)展成航空、航天、船舶、汽車等結(jié)構(gòu)部件的主要材料之一,而國內(nèi)外常用的先進(jìn)復(fù)合材料用樹脂基體主要有環(huán)氧樹脂、雙馬樹脂、氰酸脂樹脂和聚酰亞胺樹脂等,其中雙馬樹脂以其可比擬環(huán)氧樹脂的加工性和優(yōu)異的耐熱性成為先進(jìn)復(fù)合材料重點(diǎn)發(fā)展的樹脂基體之一。經(jīng)過幾十年的發(fā)展,國內(nèi)外研制出多種優(yōu)異的雙馬樹脂體系,其中瑞士Ciba-Geigy公司、美國Cytec公司及Hexcel公司,分別研制了XU292、5245C、5250-4等具有代表性的高性能雙馬樹脂體系。國內(nèi)625所、621所、西北工業(yè)大學(xué)等研制的QY8911系列樹脂、5405樹脂及X4502等樹脂體系,綜合性能優(yōu)異,已廣泛應(yīng)用于航空、航天領(lǐng)域。表1列舉了部分國內(nèi)外商品化雙馬樹脂體系的基本特性。表1國內(nèi)外幾種典型的雙馬樹脂體系牌號(hào)預(yù)浸料制備最高固化溫度加壓點(diǎn)XU292溶液法250℃140℃5250-4熱熔法232℃121℃/45minQY8911熱熔/溶液法200℃120℃/15minX4502熱熔/溶液法240℃120℃/30min雙馬樹脂一般制作成中間材料—預(yù)浸料使用,預(yù)浸料鋪覆成一定結(jié)構(gòu),經(jīng)過溫度和壓力控制完成固化,獲得具有力學(xué)性能和設(shè)計(jì)結(jié)構(gòu)的復(fù)合材料構(gòu)件。表1中這些典型的雙馬樹脂體系成型時(shí)均采用控制加壓點(diǎn)的成型方式,即在某個(gè)溫度臺(tái)階上保溫一定時(shí)間進(jìn)行加壓,加壓過早容易造成樹脂大量流失,加壓過晚會(huì)造成復(fù)合材料空隙率增加,因此加壓點(diǎn)的選擇對(duì)整個(gè)復(fù)合材料成型至關(guān)重要。不同的樹脂體系對(duì)應(yīng)加壓點(diǎn)均不相同,對(duì)于同一樹脂體系,不同的尺寸、厚度和結(jié)構(gòu)對(duì)應(yīng)加壓點(diǎn)的選擇也不相同,加壓點(diǎn)的選擇需要經(jīng)過大量的實(shí)驗(yàn)進(jìn)行確定。表1中這些典型的雙馬樹脂體系即便確定了加壓點(diǎn),加壓窗口一般也較窄,通常半小時(shí)左右,這給大型構(gòu)件成型帶來相當(dāng)大的風(fēng)險(xiǎn)。目前國內(nèi)外主流的環(huán)氧樹脂一般加壓點(diǎn)都相當(dāng)?shù)膶?,進(jìn)罐即可加壓,例如T800H/3900-2、IM7/M91等材料體系,這樣不但可以降低溫度控制加壓點(diǎn)的風(fēng)險(xiǎn),而且不同形狀和尺寸的產(chǎn)品可以同時(shí)進(jìn)罐,節(jié)省資源,提高效率。那如何實(shí)現(xiàn)雙馬樹脂基復(fù)合材料成型時(shí)具有較為寬松的加壓窗口?這需要從雙馬樹脂體系的設(shè)計(jì)著手。復(fù)合材料成型時(shí)加壓時(shí)間的確定需要根據(jù)樹脂體系的流動(dòng)特性確定。工藝性能良好的雙馬樹脂體系應(yīng)在加壓時(shí)具有一定的樹脂流動(dòng)度,并應(yīng)具有較寬的加壓溫域范圍。所以突破樹脂體系的流動(dòng)可控技術(shù),即可實(shí)現(xiàn)雙馬樹脂復(fù)合材料寬松成型工藝條件的要求。雙馬樹脂的流動(dòng)可控技術(shù)主要是通過雙馬樹脂體系的配方設(shè)計(jì)實(shí)現(xiàn)的,但具有流動(dòng)可控的雙馬樹脂體系與一般雙馬樹脂體系相比粘度都較高,在雙馬樹脂體系合成制備時(shí)難度較大,對(duì)設(shè)備的要求較高,因此流動(dòng)可控雙馬樹脂的合成技術(shù)也是一個(gè)工程應(yīng)用的難點(diǎn)。技術(shù)實(shí)現(xiàn)要素:本發(fā)明的目的在于克服現(xiàn)有技術(shù)的上述不足,提供一種流動(dòng)可控的雙馬樹脂體系,該雙馬樹脂體系可制備成熱熔預(yù)浸料,其復(fù)合材料成型是流變特性可控的,可解決復(fù)合材料成型時(shí)由于采用加壓點(diǎn)控制風(fēng)險(xiǎn)所帶來的復(fù)合材料制件質(zhì)量穩(wěn)定性差和成型效率低的問題。本發(fā)明的另外一個(gè)目的在于提供一種流動(dòng)可控的雙馬樹脂體系的制備方法。本發(fā)明的又一個(gè)目的在于提供一種由上述雙馬樹脂體系制備得到的熱熔預(yù)浸料。本發(fā)明的上述目的主要是通過如下技術(shù)方案予以實(shí)現(xiàn)的:一種流動(dòng)可控的雙馬樹脂體系,包括如下質(zhì)量份數(shù)的組份:雙馬樹脂單體組分40~90份;工藝性調(diào)節(jié)組分10~60份;樹脂流變控制組分0~30份;所述工藝性調(diào)節(jié)組分為烯丙基苯酚、二烯丙基雙酚A、胺基苯乙炔、氰酸脂、環(huán)氧樹脂或苯并噁嗪樹脂中的一種或組合。在上述流動(dòng)可控的雙馬樹脂體系中,包括如下質(zhì)量份數(shù)的組份:雙馬樹脂單體組分50~70份;工藝性調(diào)節(jié)組分20~50份;樹脂流變控制組分5~20份。在上述流動(dòng)可控的雙馬樹脂體系中,所述雙馬樹脂單體組分為二苯甲烷二胺型雙馬單體、甲苯型雙馬單體、間苯型雙馬單體或二苯醚二胺型雙馬單體中的一種或組合。在上述流動(dòng)可控的雙馬樹脂體系中,所述雙馬樹脂單體組分為二苯甲烷二胺型雙馬單體與甲苯型雙馬單體的組合,二者的質(zhì)量比為1/2~2:1。在上述流動(dòng)可控的雙馬樹脂體系中,所述工藝性調(diào)節(jié)組分為烯丙基苯酚與二烯丙基雙酚A的組合,二者的質(zhì)量比為0.5~1:1;所述工藝性調(diào)節(jié)組分為胺基苯乙炔。在上述流動(dòng)可控的雙馬樹脂體系中,所述工藝性調(diào)節(jié)組分為環(huán)氧樹脂與苯并噁嗪樹脂的組合,二者的質(zhì)量比為0.2~1:1。在上述流動(dòng)可控的雙馬樹脂體系中,所述樹脂流變控制組分為聚芳醚酮、聚醚砜、聚芳醚砜、熱塑性聚酰亞胺或聚醚酰亞胺中的一種或組合。在上述流動(dòng)可控的雙馬樹脂體系中,所述聚芳醚酮數(shù)均分子量為10000~500000,優(yōu)選數(shù)均分子量為250000~300000;所述聚醚砜數(shù)均分子量為10000~400000,優(yōu)選數(shù)均分子量為150000~250000;所述聚芳醚砜數(shù)均分子量為10000~500000,優(yōu)選數(shù)均分子量為250000~300000;所述熱塑性聚酰亞胺數(shù)均分子量為10000~300000,優(yōu)選數(shù)均分子量為60000~80000;所述聚醚酰亞胺數(shù)均分子量為10000~3000000,優(yōu)選數(shù)均分子量為100000~150000。一種流動(dòng)可控的雙馬樹脂體系的制備方法,包括如下步驟:步驟(一)、將樹脂流變控制組分加入到工藝性調(diào)節(jié)組分中,混合均勻,升溫到100-130℃,直到樹脂流變控制組分在工藝性調(diào)節(jié)組分中溶解完全;步驟(二)、將雙馬樹脂單體組分加入到步驟(一)得到的混合物中,進(jìn)行熔融共聚反應(yīng),至雙馬樹脂單體組分完全溶解,在100~130℃條件下進(jìn)行保溫反應(yīng),保溫反應(yīng)的反應(yīng)時(shí)間為0~4小時(shí),得到雙馬樹脂體系。在上述流動(dòng)可控的雙馬樹脂體系的制備方法中,所述步驟(二)中反應(yīng)時(shí)間為1~2小時(shí)。一種熱熔預(yù)浸料,由上述雙馬樹脂體系與纖維或織物復(fù)合制備得到。本發(fā)明與現(xiàn)有技術(shù)相比具有如下有益效果:(1)、本發(fā)明提供一種流動(dòng)可控的雙馬樹脂體系,包括雙馬樹脂單體組分、工藝性調(diào)節(jié)組分和樹脂流變控制組分,其中樹脂流變控制組分控制體系粘度,工藝性調(diào)節(jié)組分調(diào)節(jié)體系室溫操作工藝性,滿足室溫鋪覆性,本發(fā)明通過對(duì)雙馬樹脂單體組分、工藝性調(diào)節(jié)組分和樹脂流變控制組分中各組份以及配比的選擇,并通過進(jìn)一步優(yōu)化設(shè)計(jì),平衡工藝性調(diào)節(jié)組分和樹脂流變控制組分的用量,使得雙馬樹脂體系具有優(yōu)異的性能,可用于預(yù)浸料及復(fù)合材料的制備,降低了復(fù)合材料結(jié)構(gòu)件成型時(shí)錯(cuò)過加壓點(diǎn)的風(fēng)險(xiǎn),極大的提高了產(chǎn)品的成型質(zhì)量和成品率。(2)、本發(fā)明提供的流動(dòng)可控雙馬樹脂體系可以加熱熔融涂覆成樹脂膜,然后與纖維或織物復(fù)合制備熱熔預(yù)浸料,該預(yù)浸料室溫粘性好,復(fù)合材料成型時(shí)加壓窗口較寬,顯著降低了復(fù)合材料結(jié)構(gòu)件成型時(shí)錯(cuò)過加壓點(diǎn)的風(fēng)險(xiǎn),極大的提高了產(chǎn)品的成型質(zhì)量。(3)、本發(fā)明寬泛的加壓窗口使得不同的雙馬樹脂體系、同一樹脂體系,不同尺寸、不同厚度和結(jié)構(gòu)的產(chǎn)品可同時(shí)進(jìn)罐,降低了復(fù)合材料成型時(shí)的巨大成本,顯著提高了復(fù)合材料成型效率。(4)、本發(fā)明根據(jù)實(shí)際需要通過樹脂流變控制組分的質(zhì)量占比和分子量控制雙馬樹脂的流變特性,通過工藝性調(diào)節(jié)組分調(diào)整雙馬樹脂的室溫粘性,滿足熱熔預(yù)浸料的工藝需求,該雙馬樹脂體系可用于航空航天及民用產(chǎn)業(yè)的超大尺寸和結(jié)構(gòu)復(fù)雜的復(fù)合材料結(jié)構(gòu)件的制備,具有重要的商業(yè)價(jià)值。附圖說明圖1為本發(fā)明實(shí)施例1制備得到的流動(dòng)可控雙馬樹脂的粘度-溫度曲線;圖2為本發(fā)明實(shí)施例2制備得到的流動(dòng)可控雙馬樹脂的粘度-溫度曲線;圖3為本發(fā)明實(shí)施例3制備得到的流動(dòng)可控雙馬樹脂的粘度-溫度曲線;圖4為本發(fā)明實(shí)施例4制備得到的流動(dòng)可控雙馬樹脂的粘度-溫度曲線。具體實(shí)施方式下面結(jié)合具體實(shí)施例對(duì)本發(fā)明作進(jìn)一步詳細(xì)的描述:本發(fā)明所提供的流動(dòng)可控雙馬樹脂,是由下述原料通過熔融共聚方法制備得到的:雙馬樹脂單體組分、工藝性調(diào)節(jié)組分和樹脂流變控制組分。其中雙馬樹脂單體組分、工藝性調(diào)節(jié)組分和樹脂流變控制組分的質(zhì)量份數(shù)分別為40~90份,10~60份,0~30份,優(yōu)選為50~70份,20~50份,5~20份。本發(fā)明中雙馬樹脂單體組分為二苯甲烷二胺型雙馬單體、甲苯型雙馬單體、間苯型雙馬單體或二苯醚二胺型雙馬單體中的一種或組合。當(dāng)為組合時(shí),優(yōu)選二苯甲烷二胺型雙馬單體與甲苯型雙馬單體的組合,二者的質(zhì)量比為1/2~2:1。工藝性調(diào)節(jié)組分為烯丙基苯酚、二烯丙基雙酚A、胺基苯乙炔、氰酸脂、環(huán)氧樹脂或苯并噁嗪樹脂中的一種或組合,工藝性調(diào)節(jié)組分優(yōu)選為胺基苯乙炔。當(dāng)為組合時(shí),優(yōu)選烯丙基苯酚與二烯丙基雙酚A的組合,二者的質(zhì)量比為0.5~1:1。或者優(yōu)選為環(huán)氧樹脂與苯并噁嗪樹脂的組合,二者的質(zhì)量比為0.2~1:1。樹脂流變控制組分為聚芳醚酮、聚醚砜、聚芳醚砜、熱塑性聚酰亞胺或聚醚酰亞胺中的一種或組合。其中聚芳醚酮數(shù)均分子量為10000~500000,優(yōu)選數(shù)均分子量為250000~300000;聚醚砜數(shù)均分子量為10000~400000,優(yōu)選數(shù)均分子量為150000~250000;聚芳醚砜數(shù)均分子量為10000~500000,優(yōu)選數(shù)均分子量為250000~300000;熱塑性聚酰亞胺數(shù)均分子量為10000~300000,優(yōu)選數(shù)均分子量為60000~80000;聚醚酰亞胺數(shù)均分子量為10000~3000000,優(yōu)選數(shù)均分子量為100000~150000。本發(fā)明雙馬樹脂體系粘度較大,在工程化生產(chǎn)中,制備這種高粘度的樹脂需要反應(yīng)釜具有非常好的控溫能力和快速均質(zhì)能力,這是因?yàn)榕可a(chǎn)時(shí),產(chǎn)量較大,整個(gè)反應(yīng)過程產(chǎn)生的反應(yīng)熱大量積累,由于樹脂粘度太大,反應(yīng)熱不易擴(kuò)散,所以釜中不同部位的物料溫度很不均勻,這會(huì)導(dǎo)致制備的樹脂質(zhì)量不均一。一般的反應(yīng)釜僅在釜壁處設(shè)置有傳感器,無法監(jiān)測(cè)物料內(nèi)部的溫度。根據(jù)高粘度雙馬樹脂不易散熱的特點(diǎn),在攪拌器中預(yù)置溫度傳感器,監(jiān)測(cè)物料內(nèi)部的溫度,以便于物料溫度控制。此外提高設(shè)備的高速均質(zhì)能力,加速熱量的均勻擴(kuò)散,即反應(yīng)釜具備較好的控溫能力和快速均質(zhì)能力。本發(fā)明所述的雙馬樹脂體系整個(gè)制備過程包括下述步驟:步驟(一)、將樹脂流變控制組分加入到工藝性調(diào)節(jié)組分中,混合均勻,升溫到100-130℃,直到樹脂流變控制組分在工藝性調(diào)節(jié)組分中溶解完全;步驟(二)、將雙馬樹脂單體組分加入到步驟(一)得到的混合物中,進(jìn)行熔融共聚反應(yīng),至雙馬樹脂單體組分完全溶解,在100~130℃條件下進(jìn)行保溫反應(yīng),保溫反應(yīng)的反應(yīng)時(shí)間為0~4小時(shí),優(yōu)選1~2小時(shí),得到流動(dòng)可控的雙馬樹脂體系。本發(fā)明制備方法通過對(duì)制備工藝條件的優(yōu)化設(shè)計(jì)顯著提升了制備得到的雙馬樹脂體系的性能和質(zhì)量。實(shí)施例1制備流動(dòng)可控雙馬樹脂,選取二苯甲烷二胺型雙馬樹脂單體50份,烯丙基苯酚+二烯丙基雙酚A(質(zhì)量比為1:1)37.5份,數(shù)均分子量為170000的聚醚砜12.5份。將37.5份的烯丙基苯酚+二烯丙基雙酚A與12.5份的聚醚砜在具有精確控溫和快速均質(zhì)能力的反應(yīng)釜中室溫混合均勻,然后邊升溫邊攪拌,溫度升至120℃時(shí)保溫,直至聚醚砜溶解完全。然后加入50份二苯甲烷二胺型雙馬樹脂單體,進(jìn)行熔融共聚反應(yīng),反應(yīng)溫度升至130℃,保溫1h,得到本發(fā)明所述的流動(dòng)可控雙馬樹脂。該樹脂室溫橙紅色粘稠固體。通過旋轉(zhuǎn)粘度計(jì)表征該流動(dòng)可控雙馬樹脂的流變特性,見圖1,升溫速率為1℃/min,流動(dòng)可控雙馬樹脂最低粘度為3Pa·S,如圖1所示為本發(fā)明實(shí)施例1制備得到的流動(dòng)可控雙馬樹脂的粘度-溫度曲線。將本發(fā)明制備的流動(dòng)可控雙馬樹脂制備熱熔樹脂膠膜,然后與T800碳纖維復(fù)合,制備出熱熔預(yù)浸料。將該熱熔預(yù)浸料剪裁鋪貼成240mmx440mmx2mm的板材進(jìn)行固化,根據(jù)粘度曲線選擇在25℃、80℃和150℃加壓。成型后的板材進(jìn)行金相分析和板材出膠量的統(tǒng)計(jì),見表2,在三個(gè)不同溫度點(diǎn)進(jìn)行加壓制備的三塊板材孔隙率為0,成型質(zhì)量良好;三個(gè)加壓點(diǎn)下板材料的出膠量變化不大,主要取決于選擇的吸膠材料的吸膠能力。說明該流動(dòng)可控雙馬樹脂加壓窗口很寬泛,出膠量可控,工藝性良好。表2復(fù)合材料成型質(zhì)量及出膠量加壓點(diǎn)25℃80℃150℃孔隙率/%000出膠量/g7.85.64.3實(shí)施例2制備流動(dòng)可控雙馬樹脂,選取二苯甲烷二胺型雙馬樹脂單體+甲苯型雙馬單體(二者質(zhì)量比為1:1)55份,胺基苯乙炔35份,數(shù)均分子量為270000的聚芳醚砜10份。將35份的胺基苯乙炔與10份的聚芳醚砜在具有精確控溫和快速均質(zhì)能力的反應(yīng)釜中室溫混合均勻,然后邊升溫邊攪拌,溫度升110℃時(shí)保溫,直至聚芳醚砜溶解完全.然后加入55份二苯甲烷二胺型雙馬樹脂單體+甲苯型雙馬單體,進(jìn)行熔融共聚反應(yīng),反應(yīng)溫度升至115℃,保溫1h,得到本發(fā)明所述的流動(dòng)可控雙馬樹脂。該樹脂室溫紅色粘稠固體。通過旋轉(zhuǎn)粘度計(jì)表征該流動(dòng)可控雙馬樹脂的流變特性,見圖2,升溫速率為1℃/min。該流動(dòng)可控雙馬樹脂最低粘度為9Pa·S,如圖2所示為本發(fā)明實(shí)施例2制備得到的流動(dòng)可控雙馬樹脂的粘度-溫度曲線。將本發(fā)明制備的流動(dòng)可控雙馬樹脂制備熱熔樹脂膠膜,然后與T700碳纖維復(fù)合,制備出熱熔預(yù)浸料。將該熱熔預(yù)浸料剪裁鋪貼成240mmx440mmx2mm的板材進(jìn)行固化,根據(jù)粘度曲線選擇在25℃、80℃和140℃加壓。成型后的板材進(jìn)行金相分析和板材出膠量的統(tǒng)計(jì),見表3,在三個(gè)不同溫度點(diǎn)進(jìn)行加壓制備的三塊板材孔隙率為0,成型質(zhì)量良好;三個(gè)加壓點(diǎn)下板材料的出膠量變化不大,主要取決于選擇的吸膠材料的吸膠能力。說明該流動(dòng)可控雙馬樹脂加壓窗口很寬泛,出膠量可控,工藝性良好。表3復(fù)合材料成型質(zhì)量及出膠量加壓點(diǎn)25℃80℃140℃孔隙率/%000出膠量/g4.23.62.8實(shí)施例3制備流動(dòng)可控雙馬樹脂,選取二苯甲烷二胺型雙馬樹脂單體+甲苯型雙馬單體(二者質(zhì)量比為1:1)55份,氰酸脂35份,數(shù)均分子量為130000的聚酰亞胺樹脂10份。將35份的氰酸脂與10份的聚酰亞胺樹脂在具有精確控溫和快速均質(zhì)能力的反應(yīng)釜中室溫混合均勻,然后邊升溫邊攪拌,溫度升至130℃時(shí)保溫,直至聚酰亞胺樹脂溶解完全。然后加入55份二苯甲烷二胺型雙馬樹脂單體+甲苯型雙馬單體,進(jìn)行熔融共聚反應(yīng),反應(yīng)溫度升至120℃,保溫1h,得到本發(fā)明所述的流動(dòng)可控雙馬樹脂。該樹脂室溫紅色粘稠固體。通過旋轉(zhuǎn)粘度計(jì)表征該流動(dòng)可控雙馬樹脂的流變特性,見圖3,升溫速率為1℃/min,該流動(dòng)可控雙馬樹脂最低粘度為4Pa·S,如圖3所示為本發(fā)明實(shí)施例3制備得到的流動(dòng)可控雙馬樹脂的粘度-溫度曲線。將本發(fā)明制備的流動(dòng)可控雙馬樹脂制備熱熔樹脂膠膜,然后與T700碳纖維復(fù)合,制備出熱熔預(yù)浸料。將該熱熔預(yù)浸料剪裁鋪貼成240mmx440mmx2mm的板材進(jìn)行固化,根據(jù)粘度曲線選擇在25℃、80℃和110℃加壓。成型后的板材進(jìn)行金相分析和板材出膠量的統(tǒng)計(jì),見表4,在三個(gè)不同溫度點(diǎn)進(jìn)行加壓制備的三塊板材孔隙率為0,成型質(zhì)量良好;三個(gè)加壓點(diǎn)下板材料的出膠量變化不大,主要取決于選擇的吸膠材料的吸膠能力。說明該流動(dòng)可控雙馬樹脂加壓窗口很寬泛,出膠量可控,工藝性良好。表4復(fù)合材料成型質(zhì)量及出膠量加壓點(diǎn)25℃80℃110℃孔隙率/%000出膠量/g3.53.12.8實(shí)施例4制備流動(dòng)可控雙馬樹脂,選取二苯甲烷二胺型雙馬樹脂單體60份,單官能度苯并噁嗪樹脂25份,環(huán)氧樹脂5份,數(shù)均分子量為250000的聚芳醚酮樹脂10份。將25份的苯并噁嗪樹脂和5份的環(huán)氧樹脂與10份的聚芳醚酮樹脂在具有精確控溫和快速均質(zhì)能力的反應(yīng)釜中室溫混合均勻,然后邊升溫邊攪拌,溫度升至120℃時(shí)保溫,直至聚芳醚酮樹脂溶解完全.然后加入60份二苯甲烷二胺型雙馬樹脂單體,進(jìn)行熔融共聚反應(yīng),反應(yīng)溫度升至120℃,保溫1h,得到本發(fā)明所述的流動(dòng)可控雙馬樹脂。該樹脂室溫紅色粘稠固體。通過旋轉(zhuǎn)粘度計(jì)表征該流動(dòng)可控雙馬樹脂的流變特性,見圖4,升溫速率為1℃/min,該流動(dòng)可控雙馬樹脂最低粘度為6Pa·S。如圖4所示為本發(fā)明實(shí)施例4制備得到的流動(dòng)可控雙馬樹脂的粘度-溫度曲線。將本發(fā)明制備的流動(dòng)可控雙馬樹脂制備熱熔樹脂膠膜,然后與T700碳纖維復(fù)合,制備出熱熔預(yù)浸料。將該熱熔預(yù)浸料剪裁鋪貼成240mmx440mmx2mm的板材進(jìn)行固化,根據(jù)粘度曲線選擇在25℃、80℃和130℃加壓。成型后的板材進(jìn)行金相分析和板材出膠量的統(tǒng)計(jì),見表5,在三個(gè)不同溫度點(diǎn)進(jìn)行加壓制備的三塊板材孔隙率為0,成型質(zhì)量良好;三個(gè)加壓點(diǎn)下板材料的出膠量變化不大,主要取決于選擇的吸膠材料的吸膠能力。說明該流動(dòng)可控雙馬樹脂加壓窗口很寬泛,出膠量可控,工藝性良好。表5復(fù)合材料成型質(zhì)量及出膠量加壓點(diǎn)25℃80℃130℃孔隙率/%000出膠量/g5.54.63.1以上所述,僅為本發(fā)明最佳的具體實(shí)施方式,但本發(fā)明的保護(hù)范圍并不局限于此,任何熟悉本
技術(shù)領(lǐng)域:
的技術(shù)人員在本發(fā)明揭露的技術(shù)范圍內(nèi),可輕易想到的變化或替換,都應(yīng)涵蓋在本發(fā)明的保護(hù)范圍之內(nèi)。本發(fā)明說明書中未作詳細(xì)描述的內(nèi)容屬于本領(lǐng)域?qū)I(yè)技術(shù)人員的公知技術(shù)。當(dāng)前第1頁1 2 3