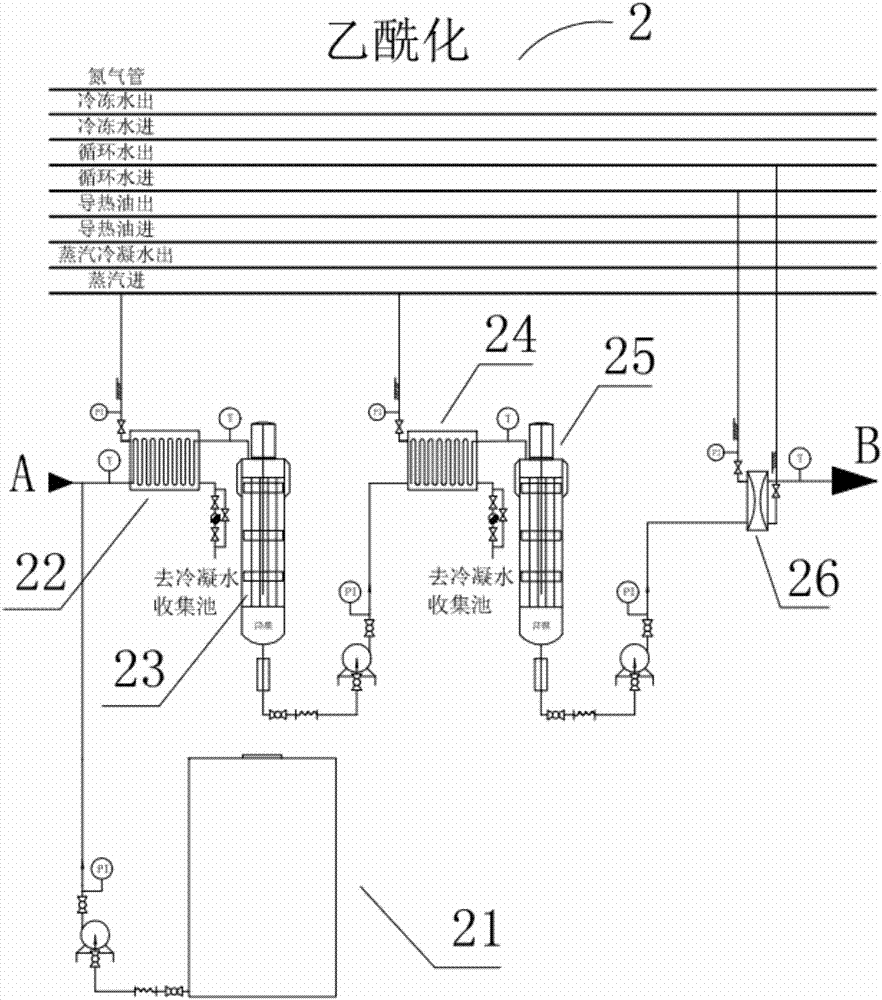
本發(fā)明涉及環(huán)保材料生產(chǎn)領(lǐng)域,更具體地說,它涉及一種生產(chǎn)環(huán)保增塑劑的反應裝置及方法。
背景技術(shù):
:環(huán)氧植物油類的新型環(huán)保增塑劑產(chǎn)品的合成方法主要包括酯化、乙?;碍h(huán)氧化等步驟,目前主要采用間歇式反應釜進行生產(chǎn),存在的主要問題是間歇式反應時間長,每步反應需要10到20個小時,導致副反應增多,影響產(chǎn)品質(zhì)量;且在反應釜中利用機械攪拌裝置時傳熱傳質(zhì)效率低,易超溫超壓,難以及時調(diào)節(jié);產(chǎn)品質(zhì)量不穩(wěn)定,批次之間存在差異等。以最后一步環(huán)氧化反應為例,采用無溶劑法硫酸催化,即按一定比例加入乙?;蟮闹虚g產(chǎn)物、甲酸和濃硫酸后,在不斷攪拌下雙氧水采用逐漸滴加的方式加入反應釜以防止反應過于劇烈。這種方法反應時間長,通常需要十幾個小時反應才能終止;容易生成副產(chǎn)物,影響產(chǎn)品的純度和收率;且生產(chǎn)過程不安全,若溫度控制不當容易發(fā)生沖料事故甚至發(fā)生爆炸。技術(shù)實現(xiàn)要素:本發(fā)明的目的在于克服現(xiàn)有技術(shù)的不足,提供一種有利于縮短反應時間、提高生產(chǎn)效率的生產(chǎn)環(huán)保增塑劑的反應裝置及方法。本發(fā)明可以通過采取以下技術(shù)方案予以實現(xiàn):一種生產(chǎn)環(huán)保增塑劑的反應裝置,包括依次連接的酯化反應單元、乙酰化反應單元、環(huán)氧化反應單元;所述酯化反應單元包括依次連接的酯化物料罐、酯化微通道反應器;所述乙?;磻獑卧ㄅc酯化微通道反應器連接的乙?;⑼ǖ婪磻鳎约斑B接在酯化微通道反應器和乙?;⑼ǖ婪磻髦g的乙?;锪瞎蓿凰霏h(huán)氧化反應單元包括與所述乙?;⑼ǖ婪磻鬟B接的環(huán)氧化微通道反應器,所述乙?;⑼ǖ婪磻髋c環(huán)氧化微通道反應器之間連接有環(huán)氧化物料罐。優(yōu)選地,所述酯化物料罐包括第一物料罐和第二物料罐,所述酯化微通道反應器包括用于一次酯化的相互串聯(lián)的第一微通道反應器和第二微通道反應器,以及用于二次酯化反應的第三微通道反應器;所述第一微通道反應器與第一物料罐的出料口連接;所述第二微通道反應器和第三微通道反應器之間串聯(lián)有第一刮膜式蒸發(fā)器,所述第二物料罐連接于所述第一刮膜式蒸發(fā)器與第三微通道反應器之間的連通管道的支路上;所述第三微通道反應器的出料口依次連接有第二刮膜式蒸發(fā)器、第一冷卻器,所述第一冷卻器設置有酯化反應物料的出料口。優(yōu)選地,所述乙?;⑼ǖ婪磻靼ㄏ嗷ゴ?lián)的第四微通道反應器、第五微通道反應器,所述乙?;锪瞎逓榈谌锪瞎蓿凰龅谒奈⑼ǖ婪磻髋c所述酯化反應單元的酯化反應物料的出料口相連通,且二者之間的連通管道的支路設置有第三物料罐;所述第四微通道反應器和第五微通道反應器之間串聯(lián)有第三刮膜式蒸發(fā)器,所述第五微通道反應器的出料口依次連接有第四刮膜式蒸發(fā)器、第二冷卻器,所述第二冷卻器設置有乙酰化反應物料的出料口。優(yōu)選地,所述環(huán)氧化微通道反應器包括依次連接的第六微通道反應器、第七微通道反應器、第八微通道反應器,所述環(huán)氧化物料罐包括相互并聯(lián)的第四物料罐和第五物料罐;所述乙?;磻獑卧c第六微通道反應器之間依次串聯(lián)有第一暫存罐、第一預熱器,所述第一暫存罐與乙?;磻锪系某隽峡谶B接;所述第四物料罐和第五物料罐均設置于所述第一預熱器與第六微通道反應器之間的連通管道的支路上;所述第八微通道反應器的出料口連接有第二暫存罐,所述第二暫存罐設置有環(huán)氧化反應物料的出料口。優(yōu)選地,所述第一物料罐、第一微通道反應器、第二微通道反應器、第三微通道反應器、第二物料罐均外接有循環(huán)導熱油;所述第四微通道反應器、第五微通道反應器均外接有蒸汽;所述第一冷卻器、第二冷卻器、第六微通道反應器、第七微通道反應器均外接有循環(huán)水;所述第八微通道反應器外接有循環(huán)冷凍水。優(yōu)選地,所述生產(chǎn)環(huán)保增塑劑的反應裝置還包括后處理單元;所述后處理單元包括依次連接的水洗堿洗單元、脫水脫酸單元、脫色脫臭單元。優(yōu)選地,所述水洗堿洗單元包括依次連接的外接有蒸汽的第二預熱器、第一分離機、第二分離機;所述第二預熱器和第一分離機之間分別連接有第一熱水罐、第一堿水罐;所述第一分離機和第二分離機之間分別連接有第二熱水罐、第二堿水罐;所述第二預熱器與所述第二暫存罐連接;所述脫水脫酸單元包括依次連接的第一干燥塔、第一脫酸塔、第二脫酸塔、第二干燥塔,所述第一干燥塔與第二分離機連接;所述依次連接的第二分離機、第一干燥塔、第一脫酸塔、第二脫酸塔、第二干燥塔的相鄰兩臺設備之間均設置有外接蒸汽的預熱器。優(yōu)選地,所述脫色脫臭單元包括活性炭吸附單元和分子蒸餾脫臭單元;所述活性炭吸附單元包括與過濾機連接的一個或者多個依次連接的外接有蒸汽且內(nèi)置有活性炭吸附劑的反應釜,所述反應釜與所述第二干燥塔連接;所述分子蒸餾脫臭單元包括依次連接的薄膜處理系統(tǒng)、分子蒸餾系統(tǒng);所述薄膜處理系統(tǒng)包括依次連接的第三暫存罐、第三預熱器、薄膜蒸發(fā)器、第一重組分接收罐;所述第三暫存罐與所述過濾機連接,所述第一重組分接收罐與所述薄膜蒸發(fā)器下部連通,所述薄膜蒸發(fā)器的上部與第一冷凝器的上部連通,所述第一冷凝器的下部連通有第一輕組分接收罐;所述分子蒸餾系統(tǒng)包括依次連接的再熱器、分子蒸餾器、第二重組分接收罐;所述再熱器與所述第一重組分接收罐連通,所述分子蒸餾器下部還分別連通有第二輕組分接收罐、第二冷凝器,所述第二冷凝器依次連通有冷阱、緩沖罐、高真空機組;所述第二冷凝器和冷阱的下部均與第二輕組分接收罐連通;所述第二輕組分接收罐和第二重組分接收罐的上部相互連通。一種用于生產(chǎn)新型環(huán)保增塑劑的方法,采用上述的生產(chǎn)環(huán)保增塑劑的反應裝置,包括以下步驟:(1)酯化反應:將酯化原料植物油酸、多元醇、酯化催化劑加入第一物料罐,加熱攪拌,混合預熱至130℃~170℃,使三種物料混合均勻;通過計量泵將混合物料打入第一微通道反應器進行反應,第一微通道反應器的溫度為160~180℃,停留時間為50~300s;隨后將反應物料打入第二微通道反應器進行反應,第二微通道反應器的溫度為180~200℃,停留時間為50~300s,完成一次酯化反應,反應產(chǎn)物經(jīng)過第一刮膜式蒸發(fā)器脫水;將二元酸與酯化催化劑加入第二物料罐,加熱攪拌,混合預熱至160~180℃,使兩種物料混合均勻,通過計量泵將混合物料與一次酯化反應脫水后的產(chǎn)物打入第三微通道反應器,第三微通道反應器的溫度為180~200℃,停留時間為80~200s,完成二次酯化反應,反應產(chǎn)物經(jīng)過第二刮膜式蒸發(fā)器脫水,然后進入第一冷卻器進行冷卻降溫至110~120℃;(2)乙酰化反應:將乙?;噭┖鸵阴;呋瘎┘尤氲降谌锪瞎藁靹颍ㄟ^計量泵將該混合物與步驟(1)后的產(chǎn)物一起打入第四微通道反應器,第四微通道反應器的溫度為75~85℃,停留時間為50~150s,進行初步乙酰化反應,隨后經(jīng)過第三刮膜式蒸發(fā)器脫水;隨后進入第五微通道反應器,第五微通道反應器的溫度為85~95℃,停留時間為80~170s,完成乙?;磻环磻a(chǎn)物經(jīng)過第四刮膜式蒸發(fā)器脫水,然后進入第二冷卻器進行冷卻降溫至40~50℃;(3)環(huán)氧化反應:將步驟(2)的產(chǎn)物打入第一暫存罐,所述第四物料罐為甲酸或乙酸罐,第五物料罐為雙氧水和濃硫酸的混合罐,或雙氧水和磷酸的混合罐,將第一暫存罐、第四物料罐、第五物料罐的物料通過計量泵依次打入第六微通道反應器,第六微通道反應器的溫度為55~65℃,停留時間為100~250s;隨后進入第七微通道反應器,第七微通道反應器的溫度為65~75℃,停留時間為100~250s;然后進入第八微通道反應器進行淬滅,第八微通道反應器的溫度為25~35℃,反應結(jié)束;隨后進入第二暫存罐靜止分層,上層酸水去污水處理池,下層粗產(chǎn)品等待進入后處理單元;(4)水洗堿洗:將步驟(3)的下層粗產(chǎn)品測試酸值,若酸值合格,則抽入第一分離機中進行水洗;若酸值不合格,則在第一分離機中進行堿洗,然后再進入第二分離機中進行水洗;堿洗水洗溫度均設置為70℃;脫水脫酸:水洗后的粗產(chǎn)品進入第一干燥塔,溫度為100~120℃,進行抽真空除水分;隨后分別依次進入第一脫酸塔、第二脫酸塔,脫除粗產(chǎn)品中的酸性物質(zhì),第一脫酸塔溫度為110~120℃,第二脫酸塔的溫度為120~130℃;隨后進入第二干燥塔,溫度為130~150℃;脫色脫臭:隨后將粗產(chǎn)品進入活性炭吸附單元的反應釜中,粗產(chǎn)品反應釜內(nèi)部的活性炭和活性白土在80~90℃下混合攪拌1~2h,進行脫色,隨后進入過濾機進行固液分離;隨后將脫色的粗產(chǎn)品依次進入分子蒸餾脫臭單元的薄膜處理系統(tǒng)和分子蒸餾系統(tǒng)進行脫臭處理,最終得到新型環(huán)保增塑劑產(chǎn)品。與現(xiàn)有技術(shù)相比較,本發(fā)明的有益效果是:利用該微通道反應裝置和方法生產(chǎn)的環(huán)保增塑劑產(chǎn)品可以達到和間歇式反應釜中生產(chǎn)的增塑劑產(chǎn)品一樣的指標要求,但是每一步反應時間僅需幾分鐘,大大縮短了生產(chǎn)時間,提高了生產(chǎn)效率。附圖說明圖1是本發(fā)明的酯化反應單元的結(jié)構(gòu)示意圖;圖2是乙酰化反應單元的結(jié)構(gòu)示意圖;圖3是環(huán)氧化反應單元的結(jié)構(gòu)示意圖;圖4是水洗堿洗單元的結(jié)構(gòu)示意圖;圖5是脫水脫酸單元的結(jié)構(gòu)示意圖;圖6是活性炭吸附單元的結(jié)構(gòu)示意圖;圖7是薄膜處理系統(tǒng)的結(jié)構(gòu)示意圖;圖8是分子蒸餾系統(tǒng)的結(jié)構(gòu)示意圖。具體實施方式以下結(jié)合附圖對本發(fā)明的具體實施方式作詳細描述。如圖1-8所示,一種生產(chǎn)環(huán)保增塑劑的反應裝置,包括依次連接的酯化反應單元1、乙酰化反應單元2、環(huán)氧化反應單元3;所述酯化反應單元1、乙?;磻獑卧?、環(huán)氧化反應單元3均包括有相連接的物料罐和微通道反應器。微通道反應器,也稱微尺度或微結(jié)構(gòu)反應器,其特征尺寸在幾十到幾百微米,遠小于傳統(tǒng)反應器的特征尺寸,但對分子水平的反應而言,該尺度依然非常大,因此不會改變化學反應機理和本征動力學特性。微通道反應器是通過改變流體的傳熱、傳質(zhì)及流動特性強化化工過程的,具有溫度和反應時間控制精準、結(jié)構(gòu)安全、無放大效應和產(chǎn)品質(zhì)量穩(wěn)定等優(yōu)點。本實施例中,微通道反應器均為增強混合型通道結(jié)構(gòu),其結(jié)構(gòu)可以為心型結(jié)構(gòu)、球型結(jié)構(gòu)、球型帶擋板結(jié)構(gòu)或水滴狀結(jié)構(gòu),通道管徑為0.25~5mm。酯化反應單元1包括依次連接的第一物料罐11、用于一次酯化反應的第一微通道反應器12和第二微通道反應器13、第一刮膜式蒸發(fā)器14、用于二次酯化反應的第三微通道反應器15、第二刮膜式蒸發(fā)器16、第一冷卻器17;第一刮膜式蒸發(fā)器14與第三微通道反應器15之間連接有第二物料罐18。第一物料罐11、第一微通道反應器12、第二微通道反應器13、第三微通道反應器15、第二物料罐18均外接有循環(huán)導熱油。在第一物料罐11、第二物料罐18中均設置有攪拌裝置,在第一物料罐11與第一微通道反應器12之間設置有計量泵、壓力表及溫度計,用于輸送物料,監(jiān)測物料的壓力和溫度;第二微通道反應器13的物料進口和出口處均設置有溫度計,用于監(jiān)測物料的溫度。在第一刮膜式蒸發(fā)器14與第三微通道反應器15、第二物料罐18與第三微通道反應器15之間均設置有計量泵、壓力表,用于輸送物料,監(jiān)測物料的壓力;兩股物料混合后,靠近第三微通道反應器15設置有溫度計,用于監(jiān)測混合物料的溫度。第一冷卻器17通過循環(huán)水進行冷卻降溫。其中,一次酯化反應可以為酯交換反應或酯化反應,二次酯化反應可以為酯化反應或酯交換反應,在一次酯化反應中設置相互連接的第一微通道反應器12和第二微通道反應器13,可以根據(jù)需要進行不同階段的溫度的設置,提高反應程度。酯交換和酯化反應為可逆反應,并且在酯交換反應的過程中可能會伴隨產(chǎn)生酯化反應,產(chǎn)生水分,影響反應的進程,因此需要設立第一刮膜式蒸發(fā)器14,去除酯化反應產(chǎn)生的水分,避免影響后面的第三微通道反應器15的酯化反應,同時在第三微通道反應器15之后設立第二刮膜式蒸發(fā)器16,去除產(chǎn)生的水分,避免對后續(xù)乙?;磻斐捎绊懀瑫r在乙?;磻倪^程中,由于去除掉了水分,能夠促進進一步的酯化反應。乙?;磻獑卧?包括依次連接的第四微通道反應器22、第三刮膜式蒸發(fā)器23、第五微通道反應器24、第四刮膜式蒸發(fā)器25、第二冷卻器26;第四微通道反應器22與第一冷卻器17連接,第一冷卻器17和第四微通道反應器22之間連接有第三物料罐21。第四微通道反應器22、第五微通道反應器24均外接有蒸汽,第二冷卻器26外接有循環(huán)水。乙酰化反應會產(chǎn)生水分,影響反應進程,因此需要脫水。經(jīng)第一冷卻器17冷卻至一定溫度的兩次酯化后的物料與來自于第三物料罐21中的物料混合后進入第四微通道反應器22中進行初步乙酰化反應,然后經(jīng)第三刮膜式蒸發(fā)器23脫水后經(jīng)過計量泵再進入第五微通道反應器24進行進一步的乙?;磻?,反應結(jié)束后物料經(jīng)第四刮膜式蒸發(fā)器25脫水后進入第二冷卻器26。在第一冷卻器17與第四微通道反應器22之間設置有兩個溫度計,靠近第一冷卻器17的溫度計用于監(jiān)測酯化反應后經(jīng)第一冷卻器17冷卻的物料溫度,靠近第四微通道反應器22的溫度計用于監(jiān)測兩股物料混合后的溫度。若兩股物料混合后溫度低于乙?;磻铚囟龋瑒t關(guān)小第一冷卻器17中循環(huán)水的流量,提高酯化反應后的物料溫度,進而提高兩股物料混合后的溫度。這樣設計的好處在于依靠酯化反應后物料本身的溫度對混合后的兩股物料溫度進行調(diào)節(jié),不需要外加換熱器,從而達到降低能耗的目的。在第三物料罐21與第四微通道反應器22、第三刮膜式蒸發(fā)器23與第五微通道反應器24、第四刮膜式蒸發(fā)器25與第二冷卻器26之間均設置有計量泵和壓力表,用于輸送物料并監(jiān)測物料壓力。在第四微通道反應器22、第五微通道反應器24和第二冷卻器26的物料出口處均設置有溫度計,用于監(jiān)測物料的溫度。環(huán)氧化反應單元3包括依次連接的第一暫存罐31、第一預熱器32、第六微通道反應器33、第七微通道反應器34、第八微通道反應器35、第二暫存罐36;第一預熱器32和第六微通道反應器33之間連接有并聯(lián)的第四物料罐37和第五物料罐38;第二冷卻器26和第一暫存罐31連接。由于環(huán)氧化反應屬于強放熱反應,第六微通道反應器33、第七微通道反應器34均采用外接循環(huán)水進行控溫。第八微通道反應器35外接有循環(huán)冷凍水,采用冷凍水使物料溫度急速下降至30℃左右,進行淬滅,停止反應。第一預熱器32外接有蒸汽。乙?;磻Y(jié)束后的物料經(jīng)第二冷卻器26冷卻后進入第一暫存罐31,經(jīng)第一預熱器32稍微預熱后與來自第四物料罐37、第五物料罐38的兩股物料一起進入第六微通道反應器33和第七微通道反應器34進行環(huán)氧化反應,然后進入第八微通道反應器35淬滅,環(huán)氧化反應結(jié)束后物料進入第二暫存罐36中靜置分層,上層酸水去污水處理池,下層粗產(chǎn)品等待后處理。第一暫存罐31與第六微通道反應器33、第四物料罐37與第六微通道反應器33、第五物料罐38與第六微通道反應器33之間均設置有計量泵和壓力表,用于輸送物料并監(jiān)測物料壓力。在第一預熱器32、第六微通道反應器33、第七微通道反應器34和第八微通道反應器35物料出口處均設置有溫度計,用于監(jiān)測物料的溫度。以上的刮膜式蒸發(fā)器均為降膜式蒸發(fā)器。一種生產(chǎn)環(huán)保增塑劑的反應裝置,它還包括后處理單元;所述后處理單元包括依次連接的水洗堿洗單元4、脫水脫酸單元5、脫色脫臭單元。水洗堿洗單元4包括依次連接的外接有蒸汽的第二預熱器41、第一分離機44、第二分離機47;所述第二預熱器41和第一分離機44之間分別連接有第一熱水罐42、第一堿水罐43;第一分離機44和第二分離機47之間分別連接有第二熱水罐45、第二堿水罐46;第二預熱器41與第二暫存罐36連接。在第二暫存罐36和第二預熱器41之間設置有計量泵和壓力表,用于輸送物料并監(jiān)測物料壓力。脫水脫酸單元5包括依次連接的第一干燥塔51、第一脫酸塔52、第二脫酸塔53、第二干燥塔54,第一干燥塔51與第二分離機47連接;依次連接的第二分離機47、第一干燥塔51、第一脫酸塔52、第二脫酸塔53、第二干燥塔54的相鄰兩臺設備之間均設置有外接蒸汽的預熱器。每兩個塔之間均設置有計量泵和壓力表,用于輸送物料并監(jiān)測物料壓力。四個塔的不同之處在于,第一干燥塔51僅設置有真空裝置,用于脫除經(jīng)分離機水洗后的粗產(chǎn)品中的大部分水分;第一脫酸塔52和第二脫酸塔53中增加了通蒸汽裝置,通過氣提作用脫除粗產(chǎn)品中殘留的酸性物質(zhì),以達到進一步降低酸值的目的;第二干燥塔54中不僅有真空裝置和通蒸汽裝置,而且增加了通氮氣裝置,用于脫除粗產(chǎn)品中殘留的水分,以及一些無法在第一脫酸塔52和第二脫酸塔53中脫除的低分子物質(zhì)。脫色脫臭單元包括活性炭吸附單元6和分子蒸餾脫臭單元。活性炭吸附單元6包括與過濾機62連接的一個或者多個依次連接的外接有蒸汽且內(nèi)置有活性炭吸附劑的反應釜,所述反應釜與第二干燥塔54連接。在本實施例中,反應釜設有兩個。兩個反應釜(61,63)結(jié)構(gòu)相同,其內(nèi)部均設置有蒸汽加熱裝置、機械攪拌裝置、真空裝置和通氮氣裝置。經(jīng)脫水、脫酸后的粗產(chǎn)品在反應釜中與活性炭和活性白土在80~90℃時混合攪拌1~2h,通過二者的吸附作用脫除粗產(chǎn)品中的有色基團,以達到脫色的目的,然后經(jīng)過濾機62進行固液分離,得到的粗產(chǎn)品進入最后一步后處理分子蒸餾脫臭單元。分子蒸餾脫臭單元包括依次連接的薄膜處理系統(tǒng)7、分子蒸餾系統(tǒng)8。薄膜處理系統(tǒng)7包括依次連接的第三暫存罐71、第三預熱器72、薄膜蒸發(fā)器73、第一重組分接收罐74;第三暫存罐71與過濾機62連接,第一重組分接收罐74與薄膜蒸發(fā)器73下部連通,薄膜蒸發(fā)器73的上部與第一冷凝器75的上部連通,第一冷凝器75的下部連通有第一輕組分接收罐76。第一輕組分接收罐76、第一重組分接收罐74和緩沖罐依次連通,并通過與緩沖罐相連的普通真空機調(diào)節(jié)氣壓;第一輕組分接收罐76底部設有電動流量控制閥;第一冷凝器75的上端與下端分別與循環(huán)水進管和循環(huán)水出管連通。薄膜處理系統(tǒng)7與第三暫存罐71之間的流量控制系統(tǒng)設置在第三預熱器72與第三暫存罐71間的油管上,其包括閥組、電動流量控制閥、流量控制器和轉(zhuǎn)子流量計,電動流量控制閥和第三暫存罐71之間設有閥組,電動流量控制閥和第三預熱器72之間設置轉(zhuǎn)子流量計,轉(zhuǎn)子流量計和電動流量控制閥之間連接有流量控制器,轉(zhuǎn)子流量計的兩端分別串聯(lián)閥門后又與一閥門并聯(lián)。薄膜處理系統(tǒng)上的預熱溫控系統(tǒng)是在溫控器的控制下,將來自導熱油進管的導熱油經(jīng)過四通閥分別被泵入到第三預熱器72和薄膜蒸發(fā)器73,導熱油的流量經(jīng)閥門調(diào)節(jié),從第三預熱器72和薄膜蒸發(fā)器73排出的導熱油再經(jīng)四通閥進入到導熱油出管。分子蒸餾系統(tǒng)8包括依次連接的再熱器81、分子蒸餾器82、第二重組分接收罐83;再熱器81與第一重組分接收罐74連通,分子蒸餾器82下部還分別連通有第二輕組分接收罐84、第二冷凝器85,第二冷凝器85依次連通有冷阱86、緩沖罐、高真空機組;第二冷凝器85和冷阱86的下部均與第二輕組分接收罐84連通;第二輕組分接收罐84和第二重組分接收罐83的上部相互連通。再熱器81下端與第一重組分接收罐74相連通的油管上設有流量控制系統(tǒng),再熱器81的上端與分子蒸餾器82上部連通,第二冷凝器85與冷阱86液性連通,冷阱86、緩沖罐和高真空機組依次連通;第二輕組分接收罐84上部和第二重組分接收罐83上部連通,第二輕組分接收罐84上部和底部均設置有電動流量控制閥;分子蒸餾器82的下部與循環(huán)水進管和循環(huán)水出管連通;第二冷凝器85的上端與下端分別與循環(huán)水進管和循環(huán)水出管連通;冷阱86的頂部與冷凍水進管和冷凍水出管連通。再熱器81與第一重組分接收罐74之間的流量控制系統(tǒng)以及分子蒸餾系統(tǒng)8上的預熱溫控系統(tǒng)的作用方式與如前所述的薄膜處理系統(tǒng)7中相似。在本實施例中,分子蒸餾系統(tǒng)8設置有相互連接的兩組。先利用薄膜蒸發(fā)技術(shù)對經(jīng)活性炭吸附脫色后的粗產(chǎn)品進行脫氣脫水,然后利用兩級分子蒸餾脫除脂肪酸和低分子醇,最終獲得脫色脫味的、品質(zhì)較高的新型環(huán)保增塑劑產(chǎn)品a。一種用于生產(chǎn)新型環(huán)保增塑劑的方法,采用上述的生產(chǎn)環(huán)保增塑劑的反應裝置,包括酯化反應、乙?;磻?、環(huán)氧化反應。在酯化反應中,植物油可以為大豆油、亞麻油、棕櫚油、蓖麻油的一種或多種;多元醇可以為1,4-丁二醇、甘油、季戊四醇、三羥甲基丙烷的一種或多種;酯交換催化劑可以為氫氧化鈉、氫氧化鉀、氫氧化鈣、氧化鈣的一種或多種,酯化催化劑可以為鈦酸四丁酯、磷酸、磷酸鈉的一種或多種;二元酸可以為己二酸、鄰苯二甲酸酐、順丁烯二酸酐、對苯二甲酸的一種或多種。在乙?;磻?,乙酰化試劑可以為乙酰氯、冰醋酸、乙酸酐;催化劑為濃硫酸、對甲苯磺酸、酸性例子交換樹脂的一種或幾種。在環(huán)氧化反應中,催化劑可以為硫酸、磷酸。以下按照如上所述的微通道反應裝置及方法制備二元酸雙一乙酰環(huán)氧植物油酯環(huán)保增塑劑:(1)酯化反應:將750g大豆油、150g甘油、0.25g氫氧化鈉催化劑加入第一物料罐,加熱攪拌,混合預熱至170℃,使三種物料混合均勻;通過計量泵將混合物料打入第一微通道反應器進行反應,第一微通道反應器的溫度為170℃,停留時間為150s;隨后將反應物料打入第二微通道反應器進行反應,第二微通道反應器的溫度為200℃,停留時間為150s,完成一次酯化反應,所述一次酯化反應其實為酯交換反應,形成大豆油單酯,反應產(chǎn)物經(jīng)過第一刮膜式蒸發(fā)器脫水;將12.5g己二酸與0.6g磷酸催化劑加入第二物料罐,加熱攪拌,混合預熱至180℃,使兩種物料混合均勻,通過計量泵將混合物料與一次酯化反應脫水后的產(chǎn)物打入第三微通道反應器,第三微通道反應器的溫度為200℃,停留時間為150s,完成二次酯化反應,所述二次酯化反應其實為酯化反應,形成二元酸雙植物油酯,反應產(chǎn)物經(jīng)過第二刮膜式蒸發(fā)器脫水,然后進入第一冷卻器進行冷卻降溫至120℃;(2)乙?;磻簩?22g乙酰化試劑冰醋酸和1.2g乙?;呋瘎妆交撬峒尤氲降谌锪瞎藁靹?,通過計量泵將該混合物與步驟(1)后的產(chǎn)物一起打入第四微通道反應器,第四微通道反應器的溫度為80℃,停留時間為100s,進行初步乙?;磻?,隨后經(jīng)過第三刮膜式蒸發(fā)器脫水;隨后進入第五微通道反應器,第五微通道反應器的溫度為90℃,停留時間為100s,完成乙?;磻?;反應產(chǎn)物經(jīng)過第四刮膜式蒸發(fā)器脫水,然后進入第二冷卻器進行冷卻降溫至50℃;(3)環(huán)氧化反應:將步驟(2)的產(chǎn)物打入第一暫存罐,所述第四物料罐為甲酸罐,第五物料罐為雙氧水和磷酸的混合罐,將第一暫存罐、第四物料罐、第五物料罐的物料通過計量泵依次打入第六微通道反應器,其中,甲酸16g,磷酸0.6g,雙氧水150g,第六微通道反應器的溫度為60℃,停留時間為150s;隨后進入第七微通道反應器,第七微通道反應器的溫度為70℃,停留時間為150s;然后進入第八微通道反應器進行淬滅,第八微通道反應器的溫度為30℃,反應結(jié)束;隨后進入第二暫存罐靜止分層,上層酸水去污水處理池,下層粗產(chǎn)品等待進入后處理單元;(4)水洗堿洗:將步驟(3)的下層粗產(chǎn)品測試酸值,若酸值合格,則抽入第一分離機中進行水洗;若酸值不合格,則在第一分離機中進行堿洗,然后再進入第二分離機中進行水洗;堿洗水洗溫度均設置為70℃;脫水脫酸:水洗后的粗產(chǎn)品進入第一干燥塔,溫度為110℃,進行抽真空除水分;隨后分別依次進入第一脫酸塔、第二脫酸塔,脫除粗產(chǎn)品中的酸性物質(zhì),第一脫酸塔溫度為120℃,第二脫酸塔的溫度為130℃;隨后進入第二干燥塔,溫度為140℃;脫色脫臭:隨后將粗產(chǎn)品進入活性炭吸附單元的反應釜中,粗產(chǎn)品與反應釜內(nèi)部的活性炭和活性白土在85℃下混合攪拌1.5h,進行脫色,隨后進入過濾機進行固液分離;隨后將脫色的粗產(chǎn)品依次進入分子蒸餾脫臭單元的薄膜處理系統(tǒng)和分子蒸餾系統(tǒng)進行脫臭處理,最終得到新型環(huán)保增塑劑產(chǎn)品。將二元酸雙一乙酰環(huán)氧植物油酯環(huán)保增塑劑同時按照中國專利cn105085442的間歇式反應釜的方法進行制備,反應時間為24h,將粗產(chǎn)物經(jīng)過本發(fā)明的后處理單元進行處理,分別對以下節(jié)點進行測試:中間產(chǎn)品1:一次酯化反應后產(chǎn)物;中間產(chǎn)品2:二次酯化反應后產(chǎn)物;中間產(chǎn)品3:乙?;磻螽a(chǎn)物。在微通道反應裝置和間歇式反應釜中得到的中間產(chǎn)品1、中間產(chǎn)品2和中間產(chǎn)品3指標對比如表1:表1同時對在微通道反應裝置和間歇式反應釜中得到產(chǎn)物分別進行后處理后得到的產(chǎn)品指標對比如表2:表2檢測項目指標微通道反應裝置間歇式反應釜外觀淺黃色透明液體淺黃色透明液體淺黃色透明液體色度(pt-co)≤150130125酸值(以koh計)/(mg/g)≤32.252.12碘值/%≤31.981.87環(huán)氧值/%≥3.53.653.72密度(20℃)/(g/cm3)0.9900~1.05001.03001.0350閃點/℃≥250260265水份(重量)/%≤0.20.090.07采用微通道反應裝置得到的新型環(huán)保增塑劑產(chǎn)品可以達到和在間歇式反應釜中一樣的指標要求,但其每一步的反應時間僅需幾分鐘,而在間歇式反應釜需要4~10h,因此采用微通道反應裝置的反應時間遠小于利用間歇式反應釜,從而極大地提高了生產(chǎn)效率。在實際生產(chǎn)時,可以根據(jù)需要對所用原料的配比、溫度、時間進行調(diào)節(jié)。以上結(jié)合較佳實施例對本發(fā)明進行了描述,但本發(fā)明并不局限于以上揭示的實施例,而應當涵蓋各種根據(jù)本發(fā)明的本質(zhì)進行的修改、等效組合。當前第1頁12