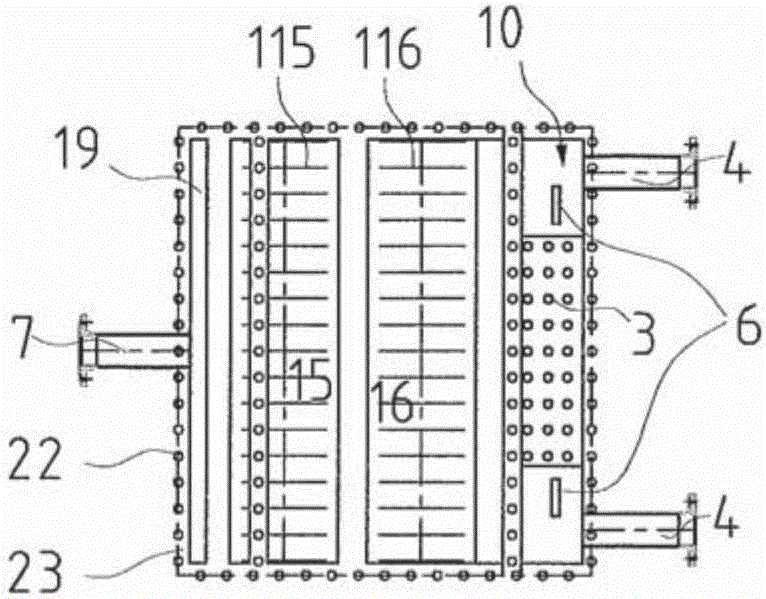
本發(fā)明涉及用于增強(qiáng)循環(huán)質(zhì)量反應(yīng)器(circulatingmassreactor)操作的方法,在該循環(huán)質(zhì)量反應(yīng)器中,由在該循環(huán)質(zhì)量反應(yīng)器中形成的煙道氣含有的熱的至少一部分傳遞到被設(shè)置為在該循環(huán)質(zhì)量反應(yīng)器中循環(huán)的流化材料,并且該循環(huán)質(zhì)量反應(yīng)器包含流化床室,在該流化床室的下部中提供用于將流化材料從煙道氣分離的含有流化材料的流化床,用于將流化材料從煙道氣分離的工具,以及回流管系統(tǒng),流化材料可以通過該回流管系統(tǒng)返回到流化床室,并且該回流管系統(tǒng)包括至少一條冷卻回流管,在該冷卻回流管中,依靠在回流管中適配的熱交換器將由經(jīng)過該冷卻回流管的流化材料含有的熱能中的一部分傳遞到在循環(huán)質(zhì)量反應(yīng)器中循環(huán)的傳熱液體。本發(fā)明也涉及用于執(zhí)行該方法的循環(huán)質(zhì)量反應(yīng)器。
背景技術(shù):在燃燒技術(shù)中固體微粒在煙道氣溫度上的穩(wěn)定化和平衡效果已經(jīng)在流化床反應(yīng)器中廣泛利用數(shù)十年。在也稱為流化床反應(yīng)器的帶有流化層的反應(yīng)器中,燃燒空氣從火爐的下部通過在燃燒室的底部上形成的砂床供應(yīng)。供應(yīng)到火爐的燃料在燃燒空氣的幫助下與以鼓泡(bubbling)方式作用的砂床混合,其中該燃料干燥并點(diǎn)燃。燃料與流化床的砂子、燃燒空氣和灰塵的繼續(xù)混合增強(qiáng)熱和氣體的混合和傳遞。此外,在流化床中的砂子材料結(jié)合熱,因此在燃燒過程期間將溫度平衡并且同時增強(qiáng)燃料的點(diǎn)火。帶有流化層的反應(yīng)器涉及流化床和循環(huán)流化床反應(yīng)器。另一方面,反應(yīng)器的概念覆蓋簡單反應(yīng)器和蒸汽鍋爐,在該簡單反應(yīng)器中到熱載體的實際傳熱不在該簡單反應(yīng)器自身中執(zhí)行,并且在該蒸汽鍋爐中生成的熱連同鍋爐一起傳遞到水或在鍋爐中循環(huán)的傳熱液體。然而在下文中,術(shù)語“鍋爐”不必需意圖將附近的每個主題限于僅涉及蒸汽鍋爐解決方案。尤其是在循環(huán)流化床反應(yīng)器中,目標(biāo)是在基本豎直的反應(yīng)室中在用于將流化材料流化的最小氣體流速和用于輸送的氣體流速之間調(diào)整氣體流速。通常,目標(biāo)是對于在流化狀態(tài)中的粉末形式的固體,即流化材料具有10-40%的體積分?jǐn)?shù)。流化材料的流化狀態(tài)的特征是在時間平均的兩側(cè)上由氣體在時間和位置上的瞬時速度的變化引起流化材料的瞬時速度在低于和高于零之間變化。結(jié)果,流化材料也在實際流化床上面輸送。在流化床上面一般使用比流化材料的氣流輸送的臨界速度更大的速度。在此情況下,流化材料與氣流一起從燃燒室排出。如果流化材料在燃燒室的氣流輸送區(qū)內(nèi)的體積分?jǐn)?shù)為小,在此情況下從燃燒室排出的流化材料的流動也為低,那么反應(yīng)器稱為鼓泡流化床反應(yīng)器。當(dāng)流化床的砂子主要保持在床自身中并且在剛好高于它的氣體空間中的時候,一般使用的術(shù)語是流化床鍋爐(FBB)。在循環(huán)流化床鍋爐(CFB),即循環(huán)質(zhì)量反應(yīng)器中,氣體速度以充當(dāng)熱載體微粒的砂屑的顯著部分與氣流一起從流化床向上清掃并且從反應(yīng)室排出的方式代替地確定大小。材料流依靠旋風(fēng)器或氣體返回設(shè)備返回到反應(yīng)室。涉及現(xiàn)有技術(shù)的問題每當(dāng)流化材料流化或在上升氣流中輸送時,豎直壓力梯度在氣流中以壓力在豎直方向上降低的方式形成。在氣流中壓力梯度的絕對值與流化材料的體積分?jǐn)?shù)成正比。另一方面,在水平方向上,壓力梯度基本為零。當(dāng)沒有水平速度維持壓力差在流動的所述狀態(tài)中的氣體中形成時,由在流化材料和氣體之間的摩擦效果引起從在反應(yīng)器室墻壁中的進(jìn)料孔供應(yīng)的氣體的水平速度分量迅速降低。初始水平氣流因此變得豎直。因為這點(diǎn),所以在流化床反應(yīng)器中,從墻壁供應(yīng)的燃燒空氣與低氧氣豎直主流低劣混合。同時,由于氣體溫度的控制需要作為整體的在反應(yīng)室中流化材料的顯著體積分?jǐn)?shù),因此良好水平混合的需求和良好溫度控制在所有的流化床反應(yīng)器中相互矛盾地不相容。所述不相容實際上是基于流化床技術(shù)的燃燒反應(yīng)器的不可避免的且基本的問題。低劣水平混合的問題尤其涉及作為在流化床中燃料熱降解的結(jié)果形成的氣體。其在燃料供應(yīng)工具附近作為極少與流化空氣混合的豎直低氧噴流從流化床排出。鼓泡流化床反應(yīng)器的功能缺點(diǎn)特別是尤其在含有大量可蒸發(fā)化合物的多塵的、濕潤的燃料的情況下,燃燒過多地移位到在流化床上面的區(qū)域,其中僅具有防止溫度升高的少量流化材料。結(jié)果,在燃燒室的上部中的溫度過多提高,并且在流化床中的溫度保持過低,這可以導(dǎo)致灰塵在燃燒室的上部中燃燒和/或燃燒室的熄滅。在鼓泡流化床反應(yīng)器中,如果燃料具有粗糙微粒尺寸并且僅含有少量的可蒸發(fā)化合物,在此情況下燃燒主要在流化床中發(fā)生,那么也面對伴隨溫度控制的問題。然后流化床溫度的過多升高變?yōu)閱栴}。對于前述原因,在基于鼓泡流化床的燃燒裝置中可以僅燃燒可以用其控制所述問題的燃料類型,這阻止或約束更經(jīng)濟(jì)燃料的使用。燃燒過程的低劣控制也提高鍋爐的監(jiān)控和維護(hù)成本并且在使用中導(dǎo)致昂貴的中斷。在公開US5257585中披露針對消除在源自鼓泡流化床反應(yīng)器的未燃燒氣體和氧氣之間混合的解決方案。在該方案中,在豎直燃燒室中心安排減小燃燒室的水平剖面的節(jié)流,于是可以認(rèn)為燃燒室分成兩個疊加區(qū)段。依靠節(jié)流,目標(biāo)是以在上區(qū)段中的混合改善的方式引導(dǎo)氣流。盡管在從反應(yīng)器排出的氣體中未燃燒化合物的濃度可以因此依靠本發(fā)明減小,然而其不解決在上面提到的鼓泡流化床反應(yīng)器的基本缺點(diǎn)。另一方面,在循環(huán)質(zhì)量反應(yīng)器中,目標(biāo)是通過在燃燒室的上部中故意提高流化材料的體積分?jǐn)?shù)來減小鼓泡流化床反應(yīng)器的所述問題,于是從燃燒室逃離的流化材料必須返回到流化床。那么分離和返回裝置必須添加到反應(yīng)器。當(dāng)靠近額定輸出操作時,只要流化材料的循環(huán)質(zhì)量流充足,那么鼓泡流化床反應(yīng)器的溫度控制問題可以避免。在循環(huán)質(zhì)量反應(yīng)器中,根據(jù)水平剖面計算的優(yōu)選氣體速度通常是5-6m/s。這意味著已經(jīng)隨著50%的部分負(fù)載,循環(huán)質(zhì)量流降到不顯著的水平,并且循環(huán)質(zhì)量反應(yīng)器開始帶有上面提到的問題相似于鼓泡流化床反應(yīng)器運(yùn)行。由于在循環(huán)質(zhì)量反應(yīng)器中同樣必須在燃燒室的上部中允許流化材料的顯著體積分?jǐn)?shù)從而平衡溫差,因此在循環(huán)質(zhì)量反應(yīng)器的燃燒室中氣體的低劣水平混合變?yōu)閱栴}。與在鼓泡流化床反應(yīng)器中相同,當(dāng)含有大量細(xì)粒和/或可蒸發(fā)化合物的燃料時,混合問題加強(qiáng)。在上面提到的兩種反應(yīng)器類型的另外特征是在它們中,溫度實際上僅由燃料的質(zhì)量和量確定,而不可能通過調(diào)整措施實質(zhì)上影響它們。通常具有生物量的在濕度上的特殊改變在鼓泡流化床鍋爐和循環(huán)質(zhì)量反應(yīng)器中都導(dǎo)致問題。它們的進(jìn)一步共同基本缺點(diǎn)是火爐的冷卻依靠傳熱表面發(fā)生,借此通常用于將循環(huán)水蒸發(fā)的燃燒室的冷卻壁表面導(dǎo)致不可控制的熱損失。這顯著提高所使用燃料的最低可容許有效熱值,限制在鍋爐中可使用的燃料的范圍,即燃料的靈活性。所述反應(yīng)器的另一共同基本缺點(diǎn)是在它們中,熱傳導(dǎo)表面尤其是過熱器與燃料灰分的腐蝕性化合物直接接觸。為減少過熱器的腐蝕,過熱蒸汽的溫度必須受限制,結(jié)果發(fā)電廠的供電減少。同樣在該方面中,生物量是尤其有問題的。由于當(dāng)前鍋爐類型,在芬蘭通常是泥煤的含硫附加燃料必須在燃燒生物量時使用,從而保護(hù)過熱器免于灰分腐蝕。當(dāng)燃燒材料分類為廢物時,所述缺點(diǎn)是特別有問題的。在CFB鍋爐的火爐的直接冷卻中包括的進(jìn)一步問題是必須在火爐的高度和流化材料的輸送之間做出低劣折衷,而且火爐的功率密度(MW/m3)保持為低,這使得火爐不必要地巨大且昂貴。作為折衷的結(jié)果,火爐呈現(xiàn)為高并且可以僅維持所需要的流化材料循環(huán)靠近額定輸出。CFB鍋爐的另一缺點(diǎn)是在火爐旁邊適配的外部分離器和回流管顯著增加空間需求和鍋爐的價格。為改善循環(huán)質(zhì)量反應(yīng)器的溫度控制,已做出將各種熱交換器與循環(huán)材料的回流管連接在一起的建議。另外,在循環(huán)材料的回流管中適配的解決方案必須基于已帶來在下文中列出的若干問題的流化技術(shù)。第一,在循環(huán)質(zhì)量反應(yīng)器中在循環(huán)材料的回流管中適配的熱交換器的基本問題是流化材料的不充足循環(huán)質(zhì)量流。該問題由在豎直燃燒室中由燃燒需要的延遲時間和由循環(huán)材料的輸送設(shè)定的需求之間不可避免的不相容引起。當(dāng)鍋爐必須在部分負(fù)載上使用,即以部分功率輸出使用時,所述問題變?yōu)樘貏e壓倒性的。第二,即使可以制作上面提到的在回流管中適配的熱交換器從而靠近額定輸出滿意操作,但它們?nèi)圆粸樵阱仩t中使用的燃料的最低可容許有效熱值消除在火爐中適配的熱交換表面的限制。在燃燒室中適配的冷卻表面不可避免地限制鍋爐的燃料靈活性,并且易受到污染、磨損和腐蝕。此外,從設(shè)備技術(shù)角度來看,這樣的流化床是昂貴且復(fù)雜的,并且其管道系統(tǒng)受到及其嚴(yán)重的腐蝕。循環(huán)材料流的調(diào)整也難于在其中以適當(dāng)?shù)姆绞竭M(jìn)行。此外,流化床冷卻器的內(nèi)部消耗為高,并且所需要的流化氣體在熱交換器中創(chuàng)造另外的熱需求。這進(jìn)一步加重已經(jīng)不充足的循環(huán)材料流的問題。由在回流管中適配的熱交換器中的流化氣體必須以基本上不妨礙微粒分離器操作的方式傳導(dǎo)離開熱交換器的事實提出另外的挑戰(zhàn)。尤其為上面的原因,一般必需放棄工藝技術(shù)上敏感的在循環(huán)質(zhì)量反應(yīng)器的回流管中適配的流化床熱交換器。在公開US4672918中披露用于在循環(huán)質(zhì)量反應(yīng)器中改善溫度控制的設(shè)想。所述反應(yīng)器基于同樣已知的換熱式冷卻的(recuperativecooled)燃燒室。在該公開中,循環(huán)質(zhì)量分入兩個平行回流管,其中一個包含傳熱表面。即使在最優(yōu),所述解決方案仍僅可以對循環(huán)質(zhì)量反應(yīng)器的溫度控制提供部分改善。然而,其不消除或減小在上面描述的循環(huán)質(zhì)量反應(yīng)器的其他基本缺點(diǎn)。根據(jù)該公開,在冷卻回流管中的循環(huán)質(zhì)量流由在回流管的上部中適配的機(jī)械裝置調(diào)整。這導(dǎo)致眾多問題。第一,機(jī)械致動器受到強(qiáng)烈磨損和污染。第二,自由下落的循環(huán)質(zhì)量的速度變?yōu)楦?,這導(dǎo)致傳熱表面的迅速磨損。此外,為可能在回流管中配合根據(jù)溫度控制顯著的傳熱表面的量,冷卻回流管的剖面應(yīng)是巨大的。經(jīng)過回流管到旋風(fēng)器的氣流然后提高到有問題的比例,并且與氣體一起運(yùn)載的灰塵化合物導(dǎo)致傳熱表面尤其是過熱器的污染。在冷卻器的剖面上充分均勻劃分循環(huán)質(zhì)量在實踐中是不可能的。即使在其最優(yōu)的情況下,因為在較低輸出的情況下在冷卻回流管中沒有足夠的循環(huán)材料,所以根據(jù)本發(fā)明的冷卻裝置僅在用高于50%的部分負(fù)載操作時運(yùn)作。然而,在公開US4672918中披露的解決方案的甚至更大的缺點(diǎn)是傳熱表面在反應(yīng)器的熔爐中適配。它們不可避免地降低燃料的靈活性,尤其是在部分負(fù)載的情況下。例如從圖1呈現(xiàn),火爐的墻壁實施為冷卻板結(jié)構(gòu),表明反應(yīng)器的冷卻意圖主要通過火爐的墻壁結(jié)構(gòu)來發(fā)生。所述解決方案不以任何方式解決在上面提到的燃燒控制的基本和關(guān)鍵問題。此外,根據(jù)該公開的反應(yīng)器導(dǎo)致需要大量維護(hù)的昂貴構(gòu)造。在專利申請F(tuán)I20031540和WO2009022060中披露的是基本上軸對稱的循環(huán)質(zhì)量反應(yīng)器,在下文中稱為CTC反應(yīng)器(恒溫燃燒),其中兩個或更多的平行流化材料回流管適配換熱式中間循環(huán)冷卻器,熱從該回流管返回的流化材料傳遞到液體、蒸汽或氣體。在中間循環(huán)冷卻器中,在熱交換器中循環(huán)材料在壓縮狀態(tài)中,并且依靠中間循環(huán)冷卻器,反應(yīng)器的冷卻隨著在反應(yīng)器中將溫度值設(shè)定在挑選點(diǎn)來調(diào)整。接收熱的流動的初始溫度依靠氣體中間循環(huán)冷卻器來調(diào)整。在CTC反應(yīng)器中,循環(huán)材料的燃燒和輸送在相同的豎直燃燒室中發(fā)生,并且因此以便限制反應(yīng)器的高度,必須在根據(jù)燃燒的充足延遲時間和由循環(huán)材料的輸送需要的氣體速度之間做出低劣折衷。為了即使在合理的部分負(fù)載范圍內(nèi)仍獲得充足的固體流,在燃燒室之后CTC反應(yīng)器的中心中適配的立管中燃料微粒的延遲時間必須限于不足以燃燒的水平。因此,CTC反應(yīng)器的滿意操作的前提是可以使得燃燒在旋風(fēng)器之前幾乎完全發(fā)生。因為在那里流化材料的體積分?jǐn)?shù)近似于零,所以燃燒進(jìn)入旋風(fēng)器室的移位導(dǎo)致在氣體溫度上的有害提高。傳遞到旋風(fēng)器的源自補(bǔ)充燃燒的熱能也不可用于在反應(yīng)器的燃燒室中維持溫度。這導(dǎo)致燃料靈活性的限制;尤其是導(dǎo)致強(qiáng)烈補(bǔ)充燃燒的潮濕材料的自發(fā)燃燒不可以在CTC反應(yīng)器中執(zhí)行,即使材料的熱值允許該自發(fā)燃燒。在旋風(fēng)器中的補(bǔ)充燃燒也提高反應(yīng)器的結(jié)構(gòu)的維護(hù)成本并且縮短其壽命。由于作為在整個噴嘴基座上均勻配料的燃料和含氧氣體熱分解的結(jié)果在燃料供應(yīng)工具附近產(chǎn)生的含煤和含烴氣體在立管之前低劣混合,因此該問題由CTC反應(yīng)器的軸對稱結(jié)構(gòu)惡化。盡管在CTC反應(yīng)器中可以靠近額定輸出調(diào)整傳熱并且過熱器的污染和腐蝕問題已解決,但CTC反應(yīng)器的上面提到的缺點(diǎn)是火爐必須設(shè)計為燃燒過程和絕熱冷卻的不相容需求的折衷。因為進(jìn)入旋風(fēng)器的氣體的巨大體積分?jǐn)?shù)導(dǎo)致結(jié)構(gòu)的侵蝕并且提高固體的滲透度,所以流化材料的單步分離也可以認(rèn)為是CTC反應(yīng)器的缺點(diǎn)。CTC反應(yīng)器結(jié)構(gòu)的問題也在于難以在冷卻形式中實施的立管,尤其是在小型反應(yīng)器中,并且該立管在冷卻時尤其是在燃燒腐蝕的、含灰塵的物質(zhì)時提高反應(yīng)器的維修和維護(hù)成本。在化石燃料的價格提高之后,對于發(fā)電廠使用可用的低質(zhì)量燃料是成本高效的,但由于上面原因因此這是不可能的。
技術(shù)實現(xiàn)要素:本發(fā)明的目標(biāo)是提供解決方案,現(xiàn)有技術(shù)的上面提到的缺陷可以依靠該解決方案減少或完全避免,這些缺陷中最顯著的是燃料的不充足的靈活性和過熱器的腐蝕。本發(fā)明的進(jìn)一步目標(biāo)是減少循環(huán)質(zhì)量反應(yīng)器的尺寸和制造成本。用于實現(xiàn)該目標(biāo)的根據(jù)本發(fā)明的方法的特征在權(quán)利要求1的特征部分中披露。用于實施根據(jù)本發(fā)明的方法的循環(huán)質(zhì)量反應(yīng)器進(jìn)而由在權(quán)利要求10的特征部分中披露的內(nèi)容來特征化。此外,本發(fā)明的優(yōu)選實施例在從屬權(quán)利要求中披露。在上面描述的CFB反應(yīng)器和CTC反應(yīng)器的問題基本上由它們針對在相同的基本豎直的燃燒室中執(zhí)行循環(huán)質(zhì)量的燃燒、冷卻和輸送的事實引起,這不可避免地導(dǎo)致與在上面描述的缺點(diǎn)的低劣折衷。本發(fā)明實質(zhì)上消除在上面描述的已知燃燒裝置和方法的缺點(diǎn)。即,為避免在上面描述的缺陷,燃燒過程、充當(dāng)流化材料的熱載體微粒的熱載體微粒的輸送,以及火爐的冷卻現(xiàn)在已安排為相互獨(dú)立的分離功能。為實現(xiàn)這點(diǎn),其中燃料的氧化基本完全發(fā)生的反應(yīng)器火爐以在分離燃燒室中實現(xiàn)高效混合與充足延遲時間的方式分成兩個分離燃燒室,下燃燒室和上燃燒室。下燃燒室的主要功能是點(diǎn)火與混合,并且上燃燒室的主要功能是燃燒的完成。連接燃燒室的立管的目的僅是將燃燒室的絕熱冷卻需要的流化材料流從下燃燒室提升到上燃燒室。燃燒室的冷卻依靠在燃燒室外面冷卻的流化材料絕熱地發(fā)生,借此沒有污染、磨損和腐蝕的熱傳導(dǎo)表面需要放置在燃燒室中,并且燃燒室的溫度可以通過調(diào)節(jié)冷卻流化材料的流動來控制。在構(gòu)造意義上,本發(fā)明特征在于一方面上下燃燒室,并且另一方面,用于分離流化材料的分離裝置和該流化材料的回流管用下燃燒室最低,在其頂部上并且相互平行的是立管與由分離設(shè)備和回流管構(gòu)成的實體,并且最頂部是上燃燒室的方式在層中相疊安置。這樣根據(jù)制造技術(shù)實現(xiàn)有利且特別緊湊的構(gòu)造。在燃燒空間中的燃燒氣體和最終的煙道氣的充分冷卻依靠熱載體微粒基本絕熱地發(fā)生。因此燃燒室至少不在任何實質(zhì)范圍上提供傳熱表面,但燃燒室以及在它們之間的流動管通過薄噴補(bǔ)(thingunning)受保護(hù)免于磨損和對最優(yōu)選的燃料靈活性有害的冷卻。在系統(tǒng)外面的傳熱基本上從流化材料發(fā)生進(jìn)入在循環(huán)質(zhì)量的回流管中適配的熱交換器中流動的介質(zhì),該流化材料從煙道氣分離,所述介質(zhì)通常是水和/或水蒸汽。熱也可以傳遞進(jìn)入氣體或粉末。由于在根據(jù)本發(fā)明的安排中,沒有關(guān)于燃燒或熱交換的技術(shù)需求需要在立管(riserconduit)上做出,因此現(xiàn)在可以僅關(guān)于熱載體微粒的輸送需求來確定大小。在立管中的氣體流速可以用由絕熱冷卻的需求確定的流化材料流動也可以用低部分負(fù)載維持的方式來自由確定大小。用本發(fā)明實現(xiàn)的優(yōu)點(diǎn)依靠根據(jù)本發(fā)明的安排實現(xiàn)燃料的最大靈活性,并且冷卻反應(yīng)器需要的傳熱表面受保護(hù)免于污染、磨損和腐蝕。應(yīng)用本發(fā)明的設(shè)想的循環(huán)質(zhì)量反應(yīng)器也在結(jié)構(gòu)上非常簡單并且特別緊湊,并因此對制造也是經(jīng)濟(jì)的。由根據(jù)本發(fā)明的解決方案提供的優(yōu)點(diǎn)中的更多從本發(fā)明的以下優(yōu)選實施例呈現(xiàn)。附圖說明下面參考附圖更詳細(xì)地描述本發(fā)明,在附圖中:圖1示出從側(cè)面所見的根據(jù)本發(fā)明的循環(huán)質(zhì)量反應(yīng)器的剖面圖,圖2沿直線A-A示出圖1的循環(huán)質(zhì)量反應(yīng)器作為縱剖面圖,圖3沿直線B-B示出圖1的循環(huán)質(zhì)量反應(yīng)器作為從上方觀察的橫向剖面圖,以及圖4沿圖2的直線C-C示出圖1的循環(huán)質(zhì)量反應(yīng)器作為從上方觀察的橫向剖面圖。參考號的列表用于在循環(huán)質(zhì)量反應(yīng)器中燃燒燃料的根據(jù)本發(fā)明的方法可以依靠根據(jù)在圖1-4中示出的實施例的裝置來實施,圖1-4的參考號在下文中列出:循環(huán)質(zhì)量反應(yīng)器1流化空氣室2用于流化空氣的配料噴嘴3副空氣供應(yīng)工具4副空氣室5副空氣室的空氣配料噴嘴6燃料供應(yīng)工具7流化床室8在下燃燒室中包含的上燃燒空間和混合室9立管10上燃燒室,即后燃燒室11分離器入口12分離器空氣偏導(dǎo)器13回流管系統(tǒng)的上部14蒸發(fā)回流管15過熱回流管16蒸發(fā)回流管的致動器17過熱回流管的致動器18未冷卻回流管19分離器的渦流室20中心管道21承載結(jié)構(gòu)22絕熱器23流化材料80第一燃燒室89流化床108立管10饋送開孔110過熱器熱交換器115蒸發(fā)器熱交換器116分離器120通過流化床的主空氣流138主空氣流153副空氣流156通過立管的流動160在上燃燒室11中的計劃主要流動路徑166在分離室中的煙道氣和流化材料懸浮的漩渦170離開分離器的煙道氣171通過分離器室的流化材料的優(yōu)選路徑180煙道氣和流化材料懸浮的路徑189上燃燒室和空隙的邊界201下燃燒室和空隙的邊界202空隙區(qū)203流化材料溢流經(jīng)過冷卻的回流管280具體實施方式圖1示出循環(huán)質(zhì)量反應(yīng)器1,其根據(jù)現(xiàn)有技術(shù)包含用于將其中安排的空氣流化的流化空氣室2和配料噴嘴3,通過它們,主空氣通過在流化床室8底部安排的流化床吹入該流化床室8。副空氣通過副空氣室5、通過空氣配料噴嘴6供應(yīng)到在流化床108上面的燃燒區(qū)9。燃料供應(yīng)從流化床室8的末端通過合適的燃料供應(yīng)工具7發(fā)生?;诨剂虾涂稍偕剂霞捌浠旌衔锏娜魏我阎牧峡梢杂米魅剂?。循環(huán)質(zhì)量反應(yīng)器可以用于將被設(shè)置為在傳熱液體循環(huán)(未示出)中流動的傳熱液體加熱、蒸發(fā)以及過熱,該熱傳導(dǎo)液體循環(huán)被設(shè)置為將該傳熱液體循環(huán)通過,以便將燃燒空氣預(yù)熱并且一般用于燃燒反應(yīng)器的其他已知用途。從燃燒室11排出的煙道氣和流化材料的流動最終引導(dǎo)到分離器,其中流化材料從煙道氣分離。流化材料返回到流化床室8并且煙道氣通過工具21從反應(yīng)器移除。圖1尤其進(jìn)一步示出承載結(jié)構(gòu)22和絕熱配件23。在下文中更詳細(xì)討論本發(fā)明的中心特征,具體依靠作為循環(huán)質(zhì)量反應(yīng)器的問題在上面描述并且本發(fā)明以解決該問題作為目標(biāo)的問題來討論。除了輸送流化材料的問題之外,燃燒反應(yīng)器的共同挑戰(zhàn)和同時有待解決的問題涉及根據(jù)加熱和流動技術(shù)在下文中呈現(xiàn)的良好燃燒控制的前提:1)基于變化的燃料質(zhì)量和燃燒反應(yīng)器輸出即部分負(fù)載,調(diào)整燃燒室或多個燃燒室的冷卻的可能性,2)關(guān)于流化反應(yīng)器,維持在同樣帶有部分負(fù)載的燃燒室中穩(wěn)定溫度需要的熱載體微粒的體積分?jǐn)?shù)的可能性,以及3)在燃燒室中燃料和氧氣的高效混合以及用于微粒燃燒的充足延遲時間。根據(jù)點(diǎn)1)的需求,燃燒室的冷卻不可以基于從氣體和熱載體微粒到在燃燒室中適配的冷卻表面的直接輻射的和對流的熱交換,而不降低反應(yīng)器的燃料靈活性。根據(jù)本發(fā)明的燃燒方法的中心特征具體涉及該問題。本發(fā)明首先特征在于涉及燃燒的空間,即帶有流化床室8和在其上面的燃燒區(qū)9的下燃燒室89、立管10、燃燒室11,并且同樣優(yōu)選的用于流化材料與分離室分離的分離裝置120基本未冷卻,即在它們中的流動絕熱地發(fā)生。因此同樣為特征的是在這些空間中的溫度控制基于流化材料,即基于由熱載體微粒引起的冷卻。另一方面,熱載體微粒的冷卻不發(fā)生,直到在流化材料返回管15、16中,其中循環(huán)水或其他合適傳熱劑的蒸發(fā)和/或過熱依靠熱交換器115、116來執(zhí)行。在所述反應(yīng)器部件中,因此直接接觸不可以在懸浮物和傳熱表面直接發(fā)生,該直接接觸引起約100kW/m2的熱損失,降低反應(yīng)器的燃料靈活性。在上面點(diǎn)2)和3)中設(shè)定的需求也基本上相互不相容。在點(diǎn)2)中需要的高氣體速度不可避免地與在點(diǎn)3)中需要的充足延遲時間不相容。本發(fā)明也對該問題提供解決方案。更具體地,熱載體微粒的燃燒過程和輸送變?yōu)橄嗷オ?dú)立的分離程序。燃料在流化床室8中并且在該流化床室8上面的燃燒空間9中點(diǎn)火,燃燒空氣、氣化燃料和焦煤微粒高效混合。流化床室8和燃燒空間9一起形成下燃燒室89。流化床室的明確向上導(dǎo)引的氣流在該流化床上面燃燒空間9中基本上在朝向立管10的水平方向上轉(zhuǎn)彎。氣體和熱載體微粒引導(dǎo)進(jìn)入立管10。下燃燒室89的主要功能是將燃料點(diǎn)火并且提供氧氣、氣化燃料和焦煤微粒的良好混合。與例如在公開US4672918和WO2009022060中披露的安排比較,根據(jù)下燃燒室89的安排的優(yōu)點(diǎn)是現(xiàn)在即使在流化床中燃料微粒的最短可能延遲時間也被最大化。燃燒在上燃燒室11中完成。因此,立管10現(xiàn)在可以僅按照熱載體微粒的輸送需要來確定大小。由于可以關(guān)于立管因此實際上忽視主要是延遲時間的燃燒技術(shù)需求,所以在管中的氣體速度可以純粹基于充足熱載體流也可以在部分輸出的情況下輸送來確定,借此煙道氣的流動并因此流速也關(guān)于在額定輸出情況下的氣流必然降低。在立管10之后燃燒室11中燃燒過程的完成用其充足的大小來確保。本發(fā)明的總體構(gòu)造設(shè)想從圖1最優(yōu)呈現(xiàn)。關(guān)于反應(yīng)器的總體結(jié)構(gòu),根據(jù)本發(fā)明的反應(yīng)器特征在于立管10,并且另一方面連接下和上燃燒室89、11的由分離器設(shè)備120和回流管系統(tǒng)15、16、19形成的實體基本豎直位于燃燒室之間,并且因此同時相互平行。在優(yōu)選安排中,以下燃燒室9、在燃燒室9上面的回流管系統(tǒng)14、15、16、19,在回流管系統(tǒng)上面的漩渦室20以及燃燒室11以所述順序從底部開始形成四層基本疊加構(gòu)造的方式,分離器裝置120的分離器或漩渦室20和在開放下表面或底部上在其整個下側(cè)上方連接到其的回流管系統(tǒng)14、15、16、19平行于基本豎直的立管10適配。當(dāng)下燃燒室89和上燃燒室11以它們一起足以完成燃燒的方式設(shè)計并確定大小時,已使得連接到燃燒室末端的立管比上下燃燒室窄得多,借此可能利用在下和上燃燒室之間變得可用的空間,以便將基本水平的延伸分離器裝置和回流管系統(tǒng)15、16、19定位。這在圖1中進(jìn)一步圖解,其中假想邊界在原理上具有參考號201和202。反應(yīng)器因此分成三個區(qū)域,于是保持在原理上在下燃燒室89和空隙之間的邊界201與原理上在上燃燒室11和空隙之間的對應(yīng)邊界202之間,在燃燒室203之間的空隙區(qū)現(xiàn)在可以如在上面描述用于將立管10和分離器裝置120以及回流管系統(tǒng)15、16、19定位。此外,依靠利用煙道氣和流化材料的雙路流動的燃燒室的優(yōu)選構(gòu)造,進(jìn)一步可能增強(qiáng)混合并且減少作為整體的循環(huán)質(zhì)量反應(yīng)器需要的空間,如依靠計劃懸浮流動路徑161圖解。甚至更緊湊的結(jié)構(gòu)在水平安排用于分離器裝置120時獲得,其中基于離心力在分離器室中形成的湍流圍繞基本水平延伸的軸前進(jìn)。這樣實現(xiàn)特別緊湊的構(gòu)造,同時為煙道氣使得充分長的延遲時間可能,并且另一方面確保充分高的煙道氣流速度,從而在所有運(yùn)行狀況下保證流化材料的高效且不中斷的輸送。本發(fā)明的詳情和優(yōu)選實施例在前面描述根據(jù)本發(fā)明的構(gòu)造的中心操作設(shè)想及其主要特征。在下文中,根據(jù)本發(fā)明的燃燒反應(yīng)器的個別裝置更詳細(xì)討論,并且同時披露本發(fā)明的不同實施例的更多特征以及它們引起的優(yōu)點(diǎn)。根據(jù)前面內(nèi)容,根據(jù)本發(fā)明的燃燒方法的優(yōu)選實施例因此基本上包含以下主要階段:1.燃料進(jìn)入流化床室8的供應(yīng),以及該燃料在流化床室8及其流化床108中的氣化。2.在第一燃燒室89中尤其是在部分負(fù)載的情況下,氣化燃料的部分甚至完全的氧化,該第一燃燒室89包含流化床室8并且優(yōu)選包含在其上面的混合與燃燒空間9。3.依靠在立管10中煙道氣流,燃燒氣體和熱載體微粒氣動輸送到上燃燒室11。4.尤其在至少燃燒室11中部分負(fù)載的情況下燃燒的完成。5.在分離室13、14中氣體和熱載體微粒的分離。6.已分離熱載體微粒通過回流管15、16、19返回到流化床室8。7.在熱載體微粒中結(jié)合的熱在用于此目的的位于回流管中的熱交換器115、116中傳遞到循環(huán)水。流化床8的主要功能是在立管10的方向上來自回流管15、16、19的粉末狀熱載體材料80的水平輸送,以及通過供應(yīng)裝置7來到的固體燃料加工成氣體和微小結(jié)焦微粒。裝置技術(shù)方面,已知流化床室8是絕熱室,更優(yōu)選基本上是矩形棱柱的形狀。流化空氣通過在流化床室的下部中適配的流化空氣噴嘴3導(dǎo)引。在圖1-4中示出的實施例中,燃料供應(yīng)裝置7相對于立管10優(yōu)選適配到下燃燒室89的相對末端,借此將在流化床108中燃料微粒的最短可能延遲時間最大化。通過未冷卻回流管19返回到流化床的熱載體流最優(yōu)選引導(dǎo)到緊鄰燃料供應(yīng)裝置7的附近,在此處由燃料的干燥和熱降解引起熱能的消耗最高。該安排的進(jìn)一步優(yōu)點(diǎn)是作為熱降解的結(jié)果在供應(yīng)裝置7附近產(chǎn)生的氣體的主要部分和燃料的細(xì)粒部分從流化床室8迅速輸送到在其上面的燃燒空間9。在燃燒空間9中,流動已經(jīng)轉(zhuǎn)入基本水平的流動。在燃燒室89中它們的延遲時間因此最大化,并且與連同燃燒空間一起提供的副空氣6的混合盡可能的高效。在混合空間9中提供的副空氣噴嘴6可以在混合空間的內(nèi)表面上以許多方式適配。圖3舉例示出在混合空間底部流化床8的相對側(cè)面上副空氣噴嘴6的安排。在流化床室8中,氣體的豎直流化速度以為燃料微粒獲得充足延遲時間的方式來設(shè)定。燃料的完全氣化需要的流化空氣流通常是整個空氣流的20-30%。流化床室8的水平面的剖面表面以基于其計算的氣體的流化速度是0.5-1.5m/s的方式來確定大小。在根據(jù)本發(fā)明的循環(huán)質(zhì)量反應(yīng)器型燃燒裝置中,下燃燒室89因此由流化床室8并且由優(yōu)選剛好在其上面適配的混合與燃燒空間9構(gòu)成。在燃燒空間中,流化材料的體積分?jǐn)?shù)基本上小于在流化床中的體積分?jǐn)?shù),最優(yōu)選1-5%。應(yīng)注意流化材料的體積分?jǐn)?shù)在立管10中優(yōu)選小于1%,并且在上燃燒室11中小于3%。燃燒空間9是絕熱的、基本水平的腔室,其在豎直平面上的剖面中優(yōu)選基本矩形,該腔室的高度以源自流化床室8的豎直氣流和源自副空氣噴嘴的空氣在燃燒空間9中朝向立管10的下端提供顯著水平的速度分量的方式確定大小?;旌鲜?的中心任務(wù)實際上是確保從流化床室8上升的燃料尤其是氣化燃料和副空氣在立管10之前的高效混合。盡管本申請分離討論流化床室8和燃燒或混合室9,但問題是如在圖1中示出,優(yōu)選具有均勻空間,即具有基于在其中安排的特殊功能或多個功能在功能上劃分成區(qū)域的下燃燒室89。為清晰,本申請討論流化床108位于其中的流化床室8與燃燒或混合室9,在該燃燒或混合室9中副空氣的供應(yīng)并且該副空氣與燃燒氣體的混合發(fā)生,以便在燃燒室中將氣體混合物均化,并且增強(qiáng)主要在上燃燒室11中發(fā)生的燃燒過程。在混合室9中,氣體流動的主要方向因此是水平的,并且取決于副空氣的分配,當(dāng)在立管10的方向上從燃料供應(yīng)裝置7前進(jìn)時,氣體的水平速度在混合室9中增加。速度從實際上零速度最優(yōu)選增加到5-10米每秒的值。對于完全負(fù)載,速度可以甚至更大例如高達(dá)20m/s,并且對于對應(yīng)較低的部分負(fù)載,速度甚至低至約3m/s。在混合室9中,水平壓力基本恒定,這意味著由噴嘴6產(chǎn)生的自由噴流的滲透性足以引起副空氣和從流化床室上升的氣化燃料的混合。下燃燒室89的體積最優(yōu)選以基于燃料的高效熱值計算的在下燃燒室中的比容(體積/輸出)最優(yōu)選為4.0-0.4m3/MW的方式確定大小。立管10的唯一功能是在整個輸出范圍上輸送充足熱載體流到燃燒室11,并且因此立管可以僅基于流技術(shù)確定大小。結(jié)構(gòu)上,該類型的流管10是具有矩形或其他合適形狀的剖面的基本上豎直的、絕熱的管,其以在所需要最小輸出的情況下在立管中的氣體速度大于熱載體微粒的氣動輸送臨界速度的方式形成大小。通過在反應(yīng)器中調(diào)整熱載體微粒的量設(shè)定在立管中熱載體微粒的流動速率,以便對燃燒過程的溫度控制足夠。在立管10中輸送熱載體微粒需要在最低部分輸出所需要的氣體速度大于熱載體微粒自由下落的速度(終點(diǎn)速度)。在實踐中,所述終點(diǎn)速度約為2-3m/s,因此如果燃燒裝置以計劃方式操作,例如用20%的部分輸出操作,那么立管的水平剖面流面積應(yīng)確定大小,因此氣體速度安排到10-15m/s的額定輸出。立管10在實踐中優(yōu)選確定大小,使得其水平剖面的平均自由表面對下燃燒室89的上部9的豎直剖面的平均自由表面的比率小于0.5,并且最優(yōu)選0.3-0.15。立管的高度或長度根據(jù)構(gòu)造和布局的剩余部分由以下這些值確定。關(guān)于立管的額定輸出,由高氣體速度引起的所需要的熱載體流用低壓損失實現(xiàn),由于該低壓損失因此鍋爐的內(nèi)部消耗最小化。上燃燒室11的功能首先是將在立管11之后的燃燒過程帶到結(jié)束。因此其體積必須以從上管10輸送到燃燒室的到此為止未燃燒的氣體和焦炭微粒具有在所有負(fù)載狀況下和變化的燃料質(zhì)量的情況下變得完全氧化的時間的方式來確定大小。完全氧化因此涉及一般在燃燒反應(yīng)器和蒸汽鍋爐中達(dá)到的燃料微粒氧化的額定水平。一旦燃燒已完全結(jié)束,那么由在反應(yīng)空間中供應(yīng)的材料流、溫度和壓力確定的熱力學(xué)平衡已達(dá)到,但在實踐中該平衡可以在技術(shù)反應(yīng)器中僅漸進(jìn)近似。小比例(小于1%)的基本可氧化的量的燃料材料總是保持未燃燒。在技術(shù)意義上,可以因此認(rèn)為燃燒在從反應(yīng)器排出的氣體的全部化合物的濃度與遵守平衡的濃度對應(yīng)時完成,該平衡帶有所需要準(zhǔn)確度,在大多數(shù)情況下是約1-2%的充足準(zhǔn)確度。為確保完全氧化,上燃燒室的體積以在上燃燒室中的煙道氣的平均延遲時間(燃燒室的體積/氣體的體積流量)在額定輸出最優(yōu)選為1.0-3.0秒的方式來確定大小。在燃燒室設(shè)計中應(yīng)同時確保充足熱載體流在所需要的最小輸出輸送通過燃燒室,一直輸送到分離器裝置120。如果燃燒氣體和傳熱微粒通過在燃燒室11的上部中適配的出口來移除,那么在立管之后面對在所需要的燃燒延遲時間和熱載體流之間的在上面提到的基本不相容。為避免該不相容,在根據(jù)本發(fā)明的燃燒裝置中,氣體和熱載體微粒通過在燃燒室11的下部中適配的工具12排放。優(yōu)選以流動在從燃燒室排出之前能夠在相對于供應(yīng)方向基本相反的方向上轉(zhuǎn)彎的方式制作上燃燒室。煙道氣和熱載體微粒從上管10的流動首先基本豎直向上導(dǎo)引,此后流動的豎直方向在燃燒室的上部中朝向分離器裝置120最終豎直向下轉(zhuǎn)彎。來自立管10的豎直流基本相似于在燃燒室11中的自由噴流表現(xiàn),結(jié)果在燃燒室11中的氣體壓力基本恒定。依靠所述燃燒室11,實現(xiàn)煙道氣和流化材料的高效混合的安排,因此氧化是高效的,并且熱載體微粒的體積分?jǐn)?shù)和流動速率保持對于在整個燃燒室中氣體的溫度控制足夠。此外,在燃燒室11中的延遲時間變得足夠長,以便在煙道氣和流化材料引導(dǎo)到分離器裝置120之前完成燃燒。燃燒室11優(yōu)選以燃燒可以在分離器裝置工具12之前基本上在燃燒室11中完成的方式,以在額定負(fù)載的情況下由在反應(yīng)器中所燒掉燃料的燃燒生成的熱能中的多于30%不釋放直到在上燃燒室11中的方式來確定大小。關(guān)于部分負(fù)載,百分比是明顯較小的。甚至可能燃料然后在到達(dá)上燃燒室11之前完全氧化。根據(jù)本發(fā)明的安排的另一基本方面是煙道氣和流化材料的流動的絕熱性質(zhì)。即,燃燒室89、上燃燒室11和將它們連接的立管10的冷卻依靠在它們中循環(huán)的流化材料主要絕熱地發(fā)生,該流化材料在回流管15、16中冷卻。主要通過墻壁在系統(tǒng)外面?zhèn)鬟f的熱的量是非常小的,通常約1kW/m2,而在帶有熱交換器的常規(guī)燃燒室解決方案中其約為100kW/m2。在它們之前的燃燒室和管以通過傳導(dǎo)和輻射傳遞到所述反應(yīng)器部件的墻壁的凈熱流尤其小于例如將從反應(yīng)器排出的煙道氣或流化床的溫度維持在期望的設(shè)定值所需要的熱輸出的50%,優(yōu)選小于30%,并且最優(yōu)選小于10%的方式確定大小并且隔離。分離器裝置120的功能就其本身來說是將熱載體微粒從煙道氣分離從而導(dǎo)引已分離微粒進(jìn)入回流管15、16、19,并且將煙道氣從燃燒裝置排出例如以便熱回收和凈化。微粒分離器120優(yōu)選由基本水平延伸的分離器室120構(gòu)成,氣體出口21在該分離器室120的一端或兩端適配。分離器裝置的優(yōu)選矩形進(jìn)口12在燃燒室11的下部中,優(yōu)選以在燃燒室中的向下引導(dǎo)的流動能夠繼續(xù)直接進(jìn)入分離器室20的方式適配。該安排的優(yōu)點(diǎn)是有待分離的流化材料的速度在工具12中大于氣體的速度。此外優(yōu)選以在腔室20以基本相切的方式引導(dǎo)流動通過進(jìn)口的方式安排該流動。這增強(qiáng)湍流的形成,并且另一方面促進(jìn)流化材料流向前直接引導(dǎo)通過腔室20的開放底部進(jìn)入回流管系統(tǒng)的上部14。將漩渦室20與回流管系統(tǒng)的上部14連接的開孔的自由表面對漩渦室的最大水平剖面的比率即使在其最小點(diǎn)也優(yōu)選大于0.7。管的剖面優(yōu)選基本均勻。在分離器進(jìn)口下面可以另外是合適的空氣偏導(dǎo)器13,依靠該空氣偏導(dǎo)器13,在漩渦室20中形成的基本水平的湍流可以受影響。根據(jù)本發(fā)明的該實施例,微粒分離器另外地特征在于其與立管10一起在上燃燒室11和下回流管15、16、19之間適配,如在上面參考圖1披露。最優(yōu)選在5-15m/s的速度來自在漩渦室20的邊緣上相切適配的進(jìn)口12的氣體和熱載體微粒的向下引導(dǎo)的流動在引導(dǎo)到出口21時在水平漩渦室20中形成強(qiáng)烈的、基本水平的湍流。由于在漩渦室中渦流的效應(yīng),因此在分離器室的下部中形成分離的慢流誘導(dǎo)湍流,其中流動速度為低并且回流管系統(tǒng)的上部14因此充當(dāng)高效沉積室。由于直接到回流管系統(tǒng)的上部的慣性力和重力的效應(yīng),因此來自進(jìn)口12的熱載體微粒的主要部分(高于99%)實際上繼續(xù)其移動,如由示出路線的箭頭180圖解。僅微粒的小部分在渦流170生成的情況下輸送進(jìn)入漩渦室20。由于在漩渦室20的墻壁表面上的離心加速度的效應(yīng),因此這些微粒在那里濃縮,并且由重力和源自漩渦室20底部的離心加速度的效應(yīng)從那里輸送,該漩渦室20底部在其下側(cè)上向回流管系統(tǒng)的上部14完全開放。已描述分離器安排的優(yōu)點(diǎn)尤其是有待分離的微粒的速度在進(jìn)口12比氣體的速度更高(高4-7m/s),以及漩渦室14的上部14的完全開放剖面表面,這些共同引起已由流動建模測試來驗證的熱載體微粒的高效分離。在回流管系統(tǒng)的上部14中,在回流管15、16中的流動可以由致動器17、18根據(jù)在熱交換器中需要的熱的量以調(diào)節(jié)方式來控制。在回流管15中,包含將在壓縮狀態(tài)中的熱載體材料的流動蒸發(fā)的傳熱表面的熱交換器115依靠致動器17以氣體的溫度在分離器的中心管21之后保持在其設(shè)定值的方式來導(dǎo)引,該致動器17在回流管的下部中適配。相似地,在回流管16中,包含將在壓縮狀態(tài)中的熱載體材料的流動過熱的傳熱表面的熱交換器116依靠致動器18以過熱蒸汽的溫度保持在其設(shè)定值的方式來導(dǎo)引,該致動器18在過熱回流管的下部中適配。未冷卻回流管19優(yōu)選充當(dāng)溢流管,借此不有意導(dǎo)引進(jìn)入回流管15、16的熱載體微粒的部分作為自調(diào)節(jié)流導(dǎo)引通過未冷卻回流管19直接進(jìn)入流化床室8。主動控制也可以關(guān)于未冷卻回流管19使用。凈化煙道氣171通過中心管21從分離器120排出。根據(jù)本發(fā)明的反應(yīng)器的承載結(jié)構(gòu)22最優(yōu)選實施為氣密的水和/或蒸汽冷卻的板件。根據(jù)本發(fā)明的反應(yīng)器的絕熱體23的目的是進(jìn)而保護(hù)承載結(jié)構(gòu)免于磨損和腐蝕,并且限制傳導(dǎo)到它們的熱流相對于燃燒室的冷卻需求為低。絕熱體可以用常規(guī)材料例如陶瓷材料最優(yōu)選實施。盡管本發(fā)明參考在圖1-4中示出的單個實施例在上面描述,然而本發(fā)明明顯不限于該描述和這些附圖,但各種修改在附加權(quán)利要求的保護(hù)范圍內(nèi)是可想象的,并且關(guān)于不同實施例披露的特征可能在本發(fā)明的基本設(shè)想內(nèi)與其他實施例一起使用,和/或存在的特征可以組合成不同實體,只要期望的和技術(shù)上的可能性為此存在。任何發(fā)明實施例可以因此在本發(fā)明設(shè)想內(nèi)執(zhí)行。盡管本申請主要披露本發(fā)明對循環(huán)質(zhì)量反應(yīng)器的應(yīng)用,但明顯其也可以關(guān)于常規(guī)流化床反應(yīng)器同樣在其他蒸汽鍋爐類型中使用。