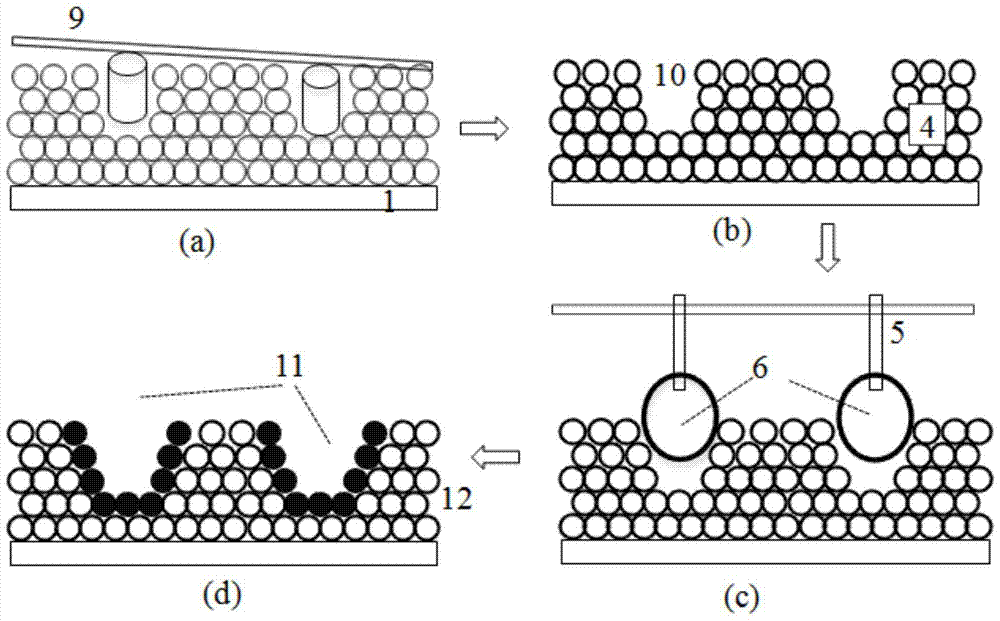
本發(fā)明屬于強(qiáng)化傳熱技術(shù)領(lǐng)域,特別涉及一種局部可控親疏水性的多孔傳熱表面制備方法。
背景技術(shù):沸騰相變傳熱作為一種高效傳熱手段,廣泛應(yīng)用于高效換熱器、快速冷卻以及能源存儲(chǔ)等領(lǐng)域。但鑒于沸騰過程存在膜沸騰或干壁現(xiàn)象,顯著降低傳熱效率,甚至導(dǎo)致設(shè)備燒毀的情況。在實(shí)際應(yīng)用過程中,沸騰傳熱必須控制在傳熱系數(shù)大和壁溫較低的核沸騰階段;或者為避免干壁、燒毀現(xiàn)象,提高對(duì)設(shè)備材料的要求、限制換熱器的應(yīng)用工況。因此,提高沸騰相變傳熱效率、保證換熱設(shè)備的安全高效運(yùn)行,其重中之重即為如何精確調(diào)控沸騰形態(tài),有效提高核沸騰形態(tài)下的相變傳熱性能。沸騰過程可分為自然對(duì)流傳熱、核沸騰、膜沸騰幾個(gè)階段。自然對(duì)流階段是沸騰氣泡產(chǎn)生之前較低熱通量狀態(tài);當(dāng)壁面過熱度增大到一定程度,在壁面核化中心處產(chǎn)生氣泡,初始?xì)馀菰谏仙^程中很快與周圍液體換熱冷卻消失,逐漸形成穩(wěn)定的核沸騰,核沸騰階段傳熱系數(shù)隨壁面過熱度的增大而明顯上升;當(dāng)過熱度達(dá)到臨界值,氣泡大量產(chǎn)生,在表面合并成熱導(dǎo)率低的汽膜,使傳熱分系數(shù)下降,轉(zhuǎn)變?yōu)槟罘序v。一旦壁面過熱度超過臨界值,沸騰進(jìn)入膜沸騰階段,傳熱表面出現(xiàn)干燒現(xiàn)象,換熱器即面臨燒毀的危險(xiǎn),同時(shí)其傳熱效率顯著降低;為此,實(shí)際應(yīng)用中核沸騰是沸騰相變傳熱的主要形態(tài)。而核化沸騰的兩大必要條件為過熱度和汽化核心,汽化核心密度正比于壁面熱流密度的平方,即加熱壁面汽化核心密度越大其傳熱效率越高;因此傳熱表面耦合多孔結(jié)構(gòu)能夠使其具有密度最大的汽化核心。一般情況下,多孔結(jié)構(gòu)傳熱表面的換熱性能是光滑表面的1.5‐3倍,致使近年來多孔結(jié)構(gòu)傳熱材料甚是火爆,也因此涌現(xiàn)出諸多制備多孔材料的方法和研究。事實(shí)上,多孔結(jié)構(gòu)相鄰多個(gè)汽化核心形成的氣泡之間具有相互作用,核化中心過密會(huì)引起氣泡之前的相互抑制或融合,惡化傳熱。另一方面,制備不同親疏水性表面或分割表面控制高效滴狀冷凝相變傳熱形態(tài);構(gòu)造微結(jié)構(gòu)促進(jìn)冷凝液滴Cassie態(tài)附著,加快液滴的脫落頻率,強(qiáng)化冷凝傳熱效率;設(shè)計(jì)外加電場(chǎng)抑制沸騰氣泡的產(chǎn)生,減小氣泡脫離半徑和脫離頻率,強(qiáng)化單相對(duì)流傳熱等等;已成為目前調(diào)控相變形態(tài),從根本上強(qiáng)化相變傳熱的前沿?zé)狳c(diǎn)課題。微結(jié)構(gòu)制備疏水或超疏水表面,使得冷凝液滴在范德華力、毛細(xì)結(jié)構(gòu)的毛細(xì)吸引力以及與之對(duì)應(yīng)的慣性力、剪切力的共同作用下,更容易跳躍脫離,大大減小液滴的脫離直徑和液滴合并的可能性,有效抑制大面積的膜換熱形態(tài),降低表面液滴熱阻。而有超親水性的表面微結(jié)構(gòu)能夠在毛細(xì)吸引力作用下,促進(jìn)沸騰氣泡脫離后液相的及時(shí)補(bǔ)充,縮短了氣泡脫離周期,從而提高池沸騰臨界熱流密度;光滑表面的親疏水性對(duì)沸騰臨界熱通量的影響很小,而多孔親水性表面可將沸騰臨界熱通量提高至原來的1.5‐1.6倍,其多孔結(jié)構(gòu)空隙和毛細(xì)泵力是強(qiáng)化沸騰傳熱的根本。而疏水的多孔金屬反而大大降低了沸騰臨界熱流密度,形成了類似與膜沸騰的氣泡層。多孔金屬強(qiáng)化沸騰的主要優(yōu)勢(shì),在于表面密集的核化中心,以及微小孔隙能夠提供較大的毛細(xì)作用力使液體補(bǔ)充。控制成核中心,調(diào)控高熱流密度在傳熱表面的分布,一直是沸騰傳熱過程中的重點(diǎn)和難點(diǎn);如何巧妙設(shè)計(jì)多孔金屬結(jié)構(gòu),調(diào)控汽化核心在沸騰表面的分布,是利用多孔金屬強(qiáng)化沸騰相變的關(guān)鍵。本發(fā)明提出多孔結(jié)構(gòu)耦合親疏水性能調(diào)控沸騰傳熱性能,是從相變傳熱的物理機(jī)理出發(fā),從根本上強(qiáng)化傳熱性能的新技術(shù)、新方法。
技術(shù)實(shí)現(xiàn)要素:本發(fā)明的目的在于提出一種局部可控親疏水性的多孔傳熱表面制備方法,其特征在于,所述局部可控親疏水性的多孔傳熱表面制備方法,包括如下步驟:步驟1,首先利用顆粒燒結(jié)制備多孔金屬傳熱表面;步驟2,然后對(duì)整體骨架進(jìn)行親水性處理,針對(duì)局部毛細(xì)結(jié)構(gòu)進(jìn)行疏水表面處理;步驟3,經(jīng)過恒溫一定時(shí)間的化學(xué)鍵合,最終獲得具有可控“疏水點(diǎn)”以及“親水毛細(xì)結(jié)構(gòu)”的整體親水局部疏水的多孔金屬傳熱表面;所述步驟1利用顆粒燒結(jié)制備多孔金屬表面為采用金屬顆粒燒結(jié)制備多孔金屬結(jié)構(gòu)的平面、或者具有固定的汽化核心空穴的多孔金屬表面;具體步驟:(1.1)首先對(duì)不同直徑金屬顆粒進(jìn)行分類篩選并做預(yù)處理,保證顆粒的均勻性;(1.2)平鋪金屬顆粒于換熱金屬表面上,用刮板刮平確保金屬顆粒表面平整,然后進(jìn)入焙燒爐燒結(jié);(1.3)所述平整金屬顆粒表面是借鑒單層石墨烯取樣方法制備,利用黏貼薄膜粘附單層高熔點(diǎn)鹵鹽顆粒,壓覆于金屬顆粒層頂部獲得生胚,或者利用模具壓覆金屬顆粒表面獲得具有汽化核心空穴的生胚;將生胚在惰性氣體保護(hù)下燒結(jié),并在保持氣體保護(hù)狀態(tài)下冷卻;繼而將燒結(jié)表面浸泡溫水中脫溶,獲得具有固定汽化核心空穴的多孔金屬表面。所述步驟2對(duì)整體骨架進(jìn)行親水性表面改性,及針對(duì)局部毛細(xì)結(jié)構(gòu)進(jìn)行疏水表面改性;包括:(2.1)首先對(duì)整體骨架的各表面進(jìn)行親水性的表面改性,所述進(jìn)行親水性的表面改性即按照步驟1進(jìn)行固定汽化空穴的多孔金屬表面處理或?qū)饘傥⒔Y(jié)構(gòu)進(jìn)行親水處理;(2.2)所述局部毛細(xì)結(jié)構(gòu)進(jìn)行疏水改性是利用毛細(xì)管注液器吸取疏水處理液,局部注入疏水處理液滴于具有固定汽化核心空穴或局部的汽化核心點(diǎn)的多孔金屬表面中;經(jīng)過恒定室溫一定時(shí)間的化學(xué)鍵合,以疏水處理液與金屬表面物完成縮合反應(yīng)為準(zhǔn),獲得具有親水毛細(xì)結(jié)構(gòu)和局部疏水點(diǎn)的多孔金屬表面;所述疏水處理液為具有疏水基團(tuán)可以與氧化金屬表面發(fā)生鍵合反應(yīng)的均可。所述多孔金屬表面處理或?qū)饘傥⒔Y(jié)構(gòu)進(jìn)行親水處理是將多孔金屬傳熱表面放在NaClO2:NaOH:Na3PO4·12H2O:H2O=3.75:5:10:81.25wt%的金屬氧化液中,在96℃浸泡30min,對(duì)多孔金屬表面處理或?qū)饘傥⒔Y(jié)構(gòu)進(jìn)行親水化處理。所述毛細(xì)管局部注入疏水處理液滴大小則根據(jù)毛細(xì)管直徑d和液體表面張力σ計(jì)算液體進(jìn)入毛細(xì)管的高度h,以及液滴體積和液滴直徑D決定,并估算疏水點(diǎn)直徑D`;或局部疏水點(diǎn)液滴的大小還能利用精密微步進(jìn)電機(jī)控制;由于多孔毛細(xì)結(jié)構(gòu)的親水性,因此D`>D;當(dāng)利用機(jī)加工方法制備固定汽化核心空穴時(shí),其尺度與沸騰氣泡相近,則同理反推微細(xì)針頭的直徑與液滴的直徑由下面二式計(jì)算:其中ρ為液體密度,mg為液體質(zhì)量;所述疏水處理液體是指能夠?qū)⒔饘俦砻媸杷揎?,在金屬氧化層表面形成疏水基團(tuán)的功能化液體。所述局部毛細(xì)結(jié)構(gòu)進(jìn)行疏水改性的毛細(xì)管注液器是加工具有靈活固定排布針管的定位微細(xì)管注液器,利用定位微細(xì)管注液器將疏水處理溶液準(zhǔn)確引入步驟1得到的具有固定汽化空穴的多孔金屬表面上,得到固定汽化核心空穴或局部的汽化核心點(diǎn),并進(jìn)行恒定、高溫脫水處理,獲得具有傳熱性和疏水性好的固定汽化核心空穴的多孔金屬表面。所述恒定、高溫脫水處理為60℃恒溫浸泡1h,然后80‐200℃脫水3h。所述步驟1‐(1.3)的焙燒爐燒結(jié)為600‐700℃燒結(jié)3h,然后氮?dú)獗Wo(hù)下自然冷卻;獲得多孔金屬傳熱表面。所述定位微細(xì)管注液器由微細(xì)針頭固定在注射器活塞筒底部的排布定位板上,活塞及活塞推動(dòng)桿插入活塞筒,活塞筒底部與插入定位托內(nèi)槽構(gòu)成,與定位托底上定位配合,其定位托確保微細(xì)針頭在注射器上的位置分布與預(yù)設(shè)的汽化核心點(diǎn)或已有固定汽化核心空穴的分布保持一致;保證微細(xì)針頭與定位槽中多孔表面上的固定汽化核心空穴或預(yù)設(shè)汽化核心點(diǎn)的精準(zhǔn)定位,以便對(duì)局部進(jìn)行疏水表面改性。所述微細(xì)針頭尺寸為成核氣泡尺度,在10‐30微米范圍;其材質(zhì)為金屬、陶瓷或硬質(zhì)有機(jī)材料;其形狀為方形或圓形,其形狀尺寸與燒結(jié)模板保持一致;所述活塞筒、活塞以及活塞推動(dòng)桿的材料為陶瓷、金屬、玻璃或有機(jī)硬質(zhì)材料。所述金屬顆粒尺度為空心或?qū)嵭牡募{米級(jí)和微米級(jí)顆粒,其形狀為球形、柱形、方形或三角形。所述金屬顆粒為600nm‐40μm尺度的金屬Cu/CuO顆粒。本發(fā)明的有益效果是:本發(fā)明巧妙設(shè)計(jì)了局部改性裝置,基于流體動(dòng)力學(xué)與氣泡動(dòng)力學(xué)基本原理,從科學(xué)的角度巧妙設(shè)計(jì)傳熱表面,強(qiáng)化沸騰傳熱;對(duì)汽化核心進(jìn)行定位疏水改性,制備具有可控“疏水點(diǎn)”以及“親水毛細(xì)輸液結(jié)構(gòu)”的多孔沸騰表面;促使沸騰氣泡快速脫離,液體沿親水多孔金屬骨架定向流動(dòng),及時(shí)補(bǔ)充沸騰相變所需液體,最終實(shí)現(xiàn)降低換熱表面過熱度,提高沸騰傳熱臨界熱流密度的目標(biāo)。本發(fā)明不僅是強(qiáng)化沸騰傳熱技術(shù)上的突破,更將多孔結(jié)構(gòu)與局部親疏水引入沸騰過程,促進(jìn)沸騰傳熱領(lǐng)域知識(shí)體系的完善和發(fā)展;促進(jìn)換熱器領(lǐng)域的技術(shù)革新;具有深遠(yuǎn)的學(xué)術(shù)價(jià)值和社會(huì)效益。附圖說明圖1是多孔金屬表面的局部親疏水改性流程示意圖;其中(a)換熱表面排布金屬顆粒燒結(jié)多孔金屬表面(b)親水處理毛細(xì)結(jié)構(gòu)(c)局部疏水處理(d)獲得整體親水局部疏水的多孔傳熱表面。圖2是制備具有親水毛細(xì)結(jié)構(gòu)和固定疏水汽化核心的多孔金屬傳熱表面的流程示意圖;其中(a)壓覆模板燒結(jié)制備固定氣穴的多孔表面(b)親水處理多孔表面(c)定位微細(xì)管注液器進(jìn)行疏水定位改性(d)具有親水毛細(xì)結(jié)構(gòu)和疏水汽化核心空穴的多孔換熱表面。圖3是利用定位微細(xì)管注射器局部疏水改性示意圖。圖中標(biāo)號(hào):1—換熱金屬表面;2—金屬微納顆粒;3—刮板;4—親水多孔結(jié)構(gòu);5—定位微細(xì)管注液器;6—疏水處理溶液;7—局部疏水處理點(diǎn);8—同時(shí)具有親水和疏水的多孔傳熱表面;9—制備汽化核心空穴模板;10—汽化核心空穴;11—疏水空穴;12—具有親水多孔和疏水汽化核心空穴的多孔表面;13—試樣底座;14—定位孔;15—微細(xì)針頭;16—注液器;17—定位托;18—活塞筒;19—活塞;20—活塞推動(dòng)桿;21—凹槽具體實(shí)施方式本發(fā)明提出一種局部親疏水性的多孔傳熱表面制備方法;以下結(jié)合附圖對(duì)本發(fā)明進(jìn)行說明,但不以任何方式限制本發(fā)明。圖1為多孔金屬表面的局部親疏水改性流程示意圖。其制備過程主要由四部操作組成:其中(a)換熱表面排布金屬顆粒燒結(jié)多孔金屬表面(b)親水處理毛細(xì)結(jié)構(gòu)(c)局部疏水處理(d)獲得整體親水局部疏水的多孔傳熱表面。首先在換熱金屬表面1排布金屬顆粒2,其厚度為100‐200微米,并用刮板3刮平金屬顆粒,以確保金屬顆粒2在金屬表面1上不存在堆積而產(chǎn)生的空穴;然后將排布有金屬顆粒2的金屬表面1固定于試樣底座13中完成。壓制固定后送入真空燒結(jié)爐,氮?dú)獗Wo(hù)情況下,600‐700℃燒結(jié)3h;燒結(jié)完畢,氮?dú)獗Wo(hù)下冷卻至室溫,取出試樣獲得多孔金屬傳熱表面4,然后,將多孔金屬傳熱表面4放在NaClO2:NaOH:Na3PO4·12H2O:H2O=3.75:5:10:81.25wt%的金屬氧化液中,在96℃浸泡30min,對(duì)多孔金屬結(jié)構(gòu)進(jìn)行親水化處理;利用試樣底座13和定位托17定位微細(xì)管注液器5,推動(dòng)活塞推動(dòng)桿20使活塞19擠壓疏水處理液體‐全氟辛基硅烷6,將其局部注入多孔金屬表面的固定汽化核心空穴或局部的汽化核心點(diǎn)中;經(jīng)過室溫下30min放置,,使得疏水處理液與金屬表面物發(fā)生縮合反應(yīng),金屬表面修飾上疏水基團(tuán),獲得具有親水毛細(xì)結(jié)構(gòu)和局部疏水點(diǎn)7的多孔金屬傳熱表面8(如圖1(d)所示)。圖2為制備具有親水毛細(xì)結(jié)構(gòu)和固定疏水汽化核心的多孔金屬傳熱表面的流程示意圖,其中(a)壓覆模板燒結(jié)制備固定氣穴的多孔表面(b)親水處理多孔表面(c)定位微細(xì)管注液器進(jìn)行疏水定位改性(d)具有親水毛細(xì)結(jié)構(gòu)和疏水汽化核心空穴的多孔換熱表面。利用機(jī)械加工等方法設(shè)計(jì)空穴模板9壓覆金屬顆粒2表層,獲得具有固定汽化核心空穴10的多孔金屬表面,對(duì)其整體進(jìn)行親水性處理,并對(duì)固定汽化核心空穴10利用定位微細(xì)管注液器5對(duì)空穴進(jìn)行局部疏水處理,此為強(qiáng)化沸騰的重點(diǎn)。(a)壓覆模板燒結(jié)制備固定汽化核心空穴的多孔表面過程中,利用激光刻蝕技術(shù)加工具有微柱結(jié)構(gòu)的空穴模板9,該模板中微柱結(jié)構(gòu)的尺寸與沸騰氣泡的尺度相當(dāng),可為球形、柱形、方形、三角形等,其分布可根據(jù)需要設(shè)計(jì)為均勻分布、非均勻分布等。燒結(jié)、脫模以后獲得具有固定汽化核心空穴10的多孔金屬傳熱表面。采用對(duì)空金屬進(jìn)行親水性處理的方法,使得金屬顆粒之間的空隙具有親水性,此為(b)親水化表面處理。(c)設(shè)計(jì)與空穴模板9具有相同尺寸的微細(xì)針頭15分布的定位微細(xì)管注液器5,并在定位托17的協(xié)助下定準(zhǔn)定位固定汽化核心空穴10,利用定位微細(xì)管注液器5中活塞推動(dòng)桿20與活塞19的擠壓,將疏水處理溶液6注入固定汽化核心空穴10中;經(jīng)過室溫下30min放置,使得疏水處理液與金屬表面物發(fā)生縮合反應(yīng),金屬表面修飾上疏水基團(tuán),,獲得具有親水毛細(xì)結(jié)構(gòu)和“疏水空穴”11的多孔金屬傳熱表面(如圖2中(d)所示)。圖3是利用定位微細(xì)管注射器9局部疏水改性示意圖;該流程中定位微細(xì)管注射器5是本發(fā)明的關(guān)鍵部件。其主要由微細(xì)針頭15、注液器16和定位托17組成。其中微細(xì)針頭15材質(zhì)可為金屬、陶瓷、玻璃、有機(jī)等硬質(zhì)材料,尺度為10‐30微米。注液器16由活塞筒18、活塞19以及推動(dòng)桿20組成,其負(fù)責(zé)存儲(chǔ)疏水溶液?;钊?8、活塞19以及推動(dòng)桿20為了簡(jiǎn)便,設(shè)計(jì)與試樣形狀保持一致。當(dāng)將定位托17與試樣底座13利用螺栓通過定位孔14固定后,定位托17的突出部分與試樣底座13頂部的定位槽21吻合,用于精確定位固定汽化核心空穴10的位置。定位托17與試樣底座13利用螺栓通過定位孔14固定并壓緊。定位托17與試樣底座13其材料可以為玻璃、金屬或有機(jī)等硬質(zhì)材料。裝配后微細(xì)針頭15即準(zhǔn)確對(duì)準(zhǔn)固定汽化核心空穴10,并利用活塞19與推動(dòng)桿20共同作用將疏水溶液注入固定汽化核心空穴10中,即可對(duì)固定汽化核心空穴10進(jìn)行疏水化改性。其中疏水處理溶液6為充分混合,具有流動(dòng)性,可與金屬表面進(jìn)行化學(xué)鍵合形成疏水表面的混合溶液。所述疏水處理液為具有疏水基團(tuán)可以與氧化金屬表面發(fā)生鍵合反應(yīng)的均可。實(shí)施例1燒結(jié)多孔金屬表面:選用紫銅金屬為換熱金屬基面材料30mm×40mm,首先對(duì)其進(jìn)行超聲表面清洗處理;選用傳熱性能好的600nm‐1μm尺度的金屬Cu/CuO微米顆粒;利用塑料刮板將金屬顆粒平鋪于基體表面,其厚度為120微米。將換熱金屬基面固定于定位槽內(nèi);在氮?dú)獗Wo(hù)下,600‐700℃燒結(jié)3h,然后氮?dú)獗Wo(hù)下自然冷卻;獲得多孔金屬傳熱表面。多孔金屬傳熱表面親水性處理:先將多孔金屬傳熱表面(多孔金屬結(jié)構(gòu))用丙酮超聲清洗20min,再用酒精、異丙醇、去離子水依次清洗,利用2.0M鹽酸去除氧化膜,去離子水清洗,氮?dú)庵懈稍?;然后浸泡?6℃的按質(zhì)量百分比=3.75:5:10:100的亞氯酸鈉NaClO2,氫氧化鈉NaOH,十二水磷酸鈉Na3PO4·12H2O和去離子水的混合堿液中,形成300nm厚度的氧化亞銅薄膜,然后氧化成1μm厚的氧化銅氧化層。由于其自限制性,氧化層厚度不受氧化時(shí)間長度影響,氧化銅表面接觸角在10‐30°,具有較強(qiáng)親水性。局部疏水改性:設(shè)計(jì)定位微細(xì)管注液器,其整個(gè)形狀和試樣一致,大小為30mm×40mm,設(shè)計(jì)定位2排、每排4條當(dāng)量直徑為20微米的微細(xì)棉線,伸出定位托的長度約為25μm;利用微細(xì)棉線浸潤氟硅烷乙醇溶液(1%體積比),然后在定位托和定位槽的精準(zhǔn)定位下,對(duì)多孔金屬傳熱表面(多孔金屬結(jié)構(gòu))進(jìn)行局部疏水液的注入;60℃恒溫浸泡1h,然后120℃脫水3h,使得氟硅烷與氧化銅進(jìn)行鍵合。至此獲得同時(shí)具有多孔親疏結(jié)構(gòu)和局部疏水點(diǎn)的多孔金屬銅沸騰表面,多孔親水結(jié)構(gòu)加速液相在多孔結(jié)構(gòu)內(nèi)部的流動(dòng)與傳輸,疏水點(diǎn)提高了沸騰氣泡的脫離頻率,強(qiáng)化了傳熱表面的沸騰傳熱性能。實(shí)施例2燒結(jié)多孔金屬表面:選用紫銅金屬為換熱金屬基面材料30mm×40mm,首先對(duì)其進(jìn)行超聲表面清洗處理;選用傳熱性能好的10‐35μm尺度的金屬Cu/CuO微米顆粒;利用塑料刮板將金屬顆粒平鋪于基體表面,其厚度為100‐200微米。將換熱金屬基面固定于定位槽內(nèi);在氮?dú)獗Wo(hù)下,600‐700℃燒結(jié)3h,然后氮?dú)獗Wo(hù)下自然冷卻;獲得多孔金屬傳熱表面。多孔金屬傳熱表面親水性處理:先將多孔金屬傳熱表面(多孔金屬結(jié)構(gòu))用丙酮超聲清洗20min,再用酒精、異丙醇、去離子水依次清洗,利用2.0M鹽酸去除氧化膜,去離子水清洗,氮?dú)庵懈稍?;然后浸泡?6℃的按質(zhì)量百分比=3.75:5:10:81.25的亞氯酸鈉NaClO2,NaOH,Na3PO4·12H2O和去離子水的混合堿液中,形成300nm厚度的氧化亞銅薄膜,然后氧化成1μm厚的氧化銅氧化層。由于其自限制性,氧化層厚度不受氧化時(shí)間長度影響,氧化銅表面接觸角在10‐30°,具有較強(qiáng)親水性。局部疏水改性:設(shè)計(jì)定位微細(xì)管注液器,其整個(gè)形狀和試樣一致,大小為30mm×40mm,設(shè)計(jì)定位2排、每排4條當(dāng)量直徑為20微米的微細(xì)棉線,伸出定位托的長度約為25μm;利用微細(xì)棉線浸潤氟硅烷乙醇溶液(1%體積比),然后在定位托和定位槽的精準(zhǔn)定位下,對(duì)多孔金屬傳熱表面(多孔金屬結(jié)構(gòu))進(jìn)行局部疏水液的注入;60℃恒溫浸泡1h,然后180℃脫水2.5h,使得氟硅烷與氧化銅進(jìn)行鍵合。至此獲得同時(shí)具有多孔親疏結(jié)構(gòu)和局部疏水點(diǎn)的多孔金屬銅沸騰表面,多孔親水結(jié)構(gòu)加速液相在多孔結(jié)構(gòu)內(nèi)部的流動(dòng)與傳輸,疏水點(diǎn)提高了沸騰氣泡的脫離頻率,強(qiáng)化了傳熱表面的沸騰傳熱性能。