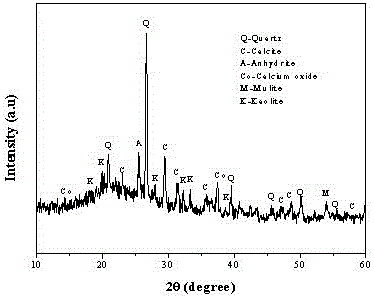
一種基于粉煤灰的CuO-CeO2/FAU脫硫劑的制備方法技術領域本發(fā)明涉及一種用于煙氣脫硫的粉煤灰制FAU沸石負載CuO-CeO2催化劑的制備方法,屬于粉煤灰資源化利用和環(huán)境功能材料制備領域。
背景技術:隨著中國經濟的快速增長以及能源消費的增多,中國已成為全世界最大的SO2排放國。根據國家統(tǒng)計數據,近兩年,中國SO2的排放總量已超過21Mt/a。其中,發(fā)電廠、鋼鐵廠以及冶煉廠是SO2的最大排放源,而由SO2造成的“酸雨”面積已約占國土總面積的40%,嚴重地影響了人們的身體健康和生存環(huán)境。為控制SO2的排放量,于2012年1月1日生效的《火電廠大氣污染物排放標準》的法規(guī)實際上已比歐盟的現行標準更加嚴格。因此,對于產生SO2污染源的企業(yè),治理煙氣中的SO2已成為當務之急。國內外也對煙氣脫硫技術進行了大量的研究,傳統(tǒng)的煙氣脫硫技術有石灰石-石膏法、檸檬吸收法、噴霧干燥法、活性炭脫硫法等。這些方法脫硫率比較高,但工藝復雜、運行費用高、防污不徹底、造成二次污染等不足。最近幾年,科技工作者研制出了新的脫硫技術包括硫化堿脫硫法、電子束脫硫技術、膜吸收法和微生物脫硫技術。但這些技術大多還處于試驗階段,有待進一步的工業(yè)應用驗證??傊?,各種各樣的的煙氣脫硫技術都取得了一定的經濟、社會和環(huán)保效益,但是也存在不足,因此尋求新的脫硫方法、開發(fā)新的吸附劑依舊是環(huán)保領域關注的焦點和急需解決的新課題。粉煤灰主要是由煤粉和空氣中的氧氣在高溫下發(fā)生燃燒反應而殘留的固體物,是燃煤熱電廠排出的環(huán)境污染物。由于我國對煤炭能源的過度依賴,粉煤灰年排放量急速增長,已成為中國最大的單一固體污染源。據預測,“十二五”末,我國粉煤灰年產生量將達到5.7億噸。為節(jié)約資源、保護環(huán)境、發(fā)展循環(huán)經濟、深入推進粉煤灰綜合利用健康發(fā)展,國家發(fā)改委等相關部門于2013年3月發(fā)布的《粉煤灰綜合利用管理辦法》規(guī)定,鼓勵粉煤灰高附加值的創(chuàng)新性研究等。粉煤灰的主要成分為SiO2和Al2O3,且二者總含量在70%以上,與沸石的化學組分極為相似。沸石主要由硅鋁酸鹽的礦石構成,其骨架的最基本結構由硅氧四面體及鋁氧四面體基本結構單元構成,相鄰兩個四面體通過氧原子連接,形成了在三維空間上無限延展的陰離子網狀結構。這種三維陰離子網狀結構使得沸石具有一些特殊的性質,三維空間結構的空穴和內部通道提高了分子的擴散速率,使得沸石成為一種有效的吸附劑。沸石結構中的Si原子被Al原子取代而呈負電性,因此沸石又具有較大的離子交換性能,使其在離子交換和分子篩方面的應用成為可能。因此,為發(fā)展粉煤灰的高附加值利用途徑,前人在粉煤灰制沸石合成方法及應用研究等方面開展了大量的研究。在粉煤灰沸石合成方面,目前常用的方法有:(1)水熱合成法,具體分為一步法、兩步法、微波輔助合成法和晶種法等。一步法操作簡單、生產成本低,但合成的沸石雜質較多、轉化率低;兩步法所合成的沸石純度高、總轉化率較大,但該法操作繁瑣、生產成本較高;微波輔助合成法反應時間短、生產成本低,但優(yōu)質沸石轉化率低。晶種法能有效縮短沸石生產周期。譚宏斌等在“將粉煤灰水熱合成高純沸石和粉煤灰沸石吸附劑的工藝”的發(fā)明中(CN101503202A)提供了將粉煤灰水熱合成高純沸石的工藝,其純度可達90%以上。呂海亮等公開發(fā)明的專利“一種粉煤灰沸石的多段合成方法”(CN101164884A)中報道了采用微波和常規(guī)油浴加熱相結合的多段合成技術合成出Na-Pc型沸石,其含量為37%,離子交換容量為186cmol/kg。MurayamaN.等(IntJMinerProcess,2002,64(1),1-17.)研究了水熱法制粉煤灰的沸石的反應機理,認為沸石水熱反應的步驟為:①粉煤灰中Si4+、Al3+的溶解;②硅酸鹽和鋁酸鹽凝結生成硅鋁凝膠;③硅鋁凝膠結晶生成沸石晶體。(2)堿熔融法,采用此法合成的沸石純度和轉化率都比較高,是比較理想的合成方法。朱校斌等在“一種制備納米粉煤灰沸石的方法”中報道了采用堿融法制備了納米粉煤灰沸石,所得沸石為NaX型,合成產率為60.56%,陽離子交換容量為394.0624mmol/100g(CN101993089A)。(3)鹽熱合成法,該法耗水量大、后期處理麻煩,目前未得到廣泛應用。此外,粉煤灰沸石合成方法還包括堿熔融-痕量水法,堿熔融-蒸汽法,堿熔融-室溫久置法等。張雪峰等“堿融-微波法合成粉煤灰沸石的方法”的發(fā)明中(CN102107878A)公開了堿熔融-微波法合成粉煤灰沸石的方法,該法操作簡單、反應時間短且合成產率較高。趙亞娟等報道了“粉煤灰利用堿熔-蒸汽法制備沸石分子篩的方法”,該發(fā)明對堿融-蒸汽法制備出的粉煤灰沸石晶粒進行了XRD和SEM表征,其顆粒大小為1μm左右(CN101481118A)。ShigemotoN等(J.Mater.Sci.,1993,28(17),4781-4786.)以粉煤灰為原料通過堿融-水熱法合成了NaX型沸石,結晶度為62%。在應用方面,粉煤灰沸石因有高Al/Si比而具有較高的離子交換容量,如NaP1、4A、X、KM、F等類型的沸石的離子交換容量均大于5meq/g,此類沸石在處理含氮和磷、有機染料、重金屬等廢水中有著廣泛的應用前景。YamamotoH等(AdvancedMaterialsforEnergyConversion,2002,269-278.)在實驗研究發(fā)現Ca基粉煤灰沸石用于同步脫磷脫氮的效果優(yōu)于其他普通的方法。Zhang,M.L.等(Desalination,2011,271(1-3),111-121.)深入研究了粉煤灰沸石在不同的接觸時間、pH、氨溶液起始濃度、沸石劑量等條件對溶液中氨鹽去除效果的影響。該實驗結果表明沸石對氨鹽的最大吸附量為24.3mg/g,并且再生后的沸石與原沸石具有相同的吸附能力。該研究小組還進行了粉煤灰沸石去除溶液中總磷的吸附機理和最大吸附容量等研究(Sep.Sci.Technol.,2011,46(14),2260-2274.)。Wu,C.N.等采用水熱法制備的粉煤灰沸石用于去除溶液中的亞甲藍取得了良好的效果(ProgressinEnvironmentalScienceandEngineering,Pts1-4,610-613:1286-1289.)。另外,粉煤灰沸石在去除廢水中重金屬離子的應用也引起了許多研究者的興趣。在處理重金屬離子的成本方面,粉煤灰合成沸石是商品13X沸石的1/5(Eur.J.Chem.,2010,7(4),1200-1205.)。沸石具有大小均一的空穴通道和很大的比表面積,易于分子的吸附和擴散,傳統(tǒng)法合成的沸石可以用于篩分氣體、吸附分離、催化裂化,也可以作為干燥劑、催化劑載體、填料等使用。例如,BabajideO以南非F類粉煤灰為原料合成X型沸石并將其用于催化太陽花油和甲醇轉化為脂肪酸甲基酯,所得產物產率高達83.53%(CatalToday,2012,190(1),54-60.)。同時由于硅基氧化物特別是沸石和介孔有機硅因具有高比表面積、較大孔隙率、可多次循環(huán)利用、熱穩(wěn)定性以及化學穩(wěn)定性等特點而成為良好的SO2的吸附劑。在所有這些硅基材料中,沸石被作為SO2吸附劑而引起大量研究者的興趣。根據文獻檢索發(fā)現,有許多國外研究者做了關于沸石作為吸附劑模擬煙氣脫硫的實驗研究。Chriswell采用紫外可見分光光度計法,首次研究了具有交叉孔道的十元環(huán)商品硅酸鹽-1對混合氣(0.05%SO2,9.4%O2,10.3%CO2,其余為N2)中SO2的吸附容量隨反應溫度的升高而降低(AnalChem,1982,54,1911–1913.)。Querol等將粉煤灰中提取的硅溶液通過水熱處理獲得較高純度的4A-X沸石(3:2),此4A-X沸石在25℃下對氣體(0.3%SO2,其余為He)中SO2的吸附容量為297mg/g,為鈉菱沸石(99mg/g)的3倍,該研究小組認為這是由于相比于較小孔徑的鈉菱沸石(3.8?),X沸石具有較大的孔徑(7?),占較小比例的4A沸石孔徑(4?)也相對較高(JournalofChemicalTechnologyandBiotechnology,2002,77,292–298.)。然而,通過大量的文獻調研發(fā)現,以粉煤灰為原料合成沸石作為催化劑載體用于煙氣脫硫處理的應用鮮有人報道。并且通過調查研究可以發(fā)現,前人在以粉煤灰合成沸石方面,其主要缺點是其最終產品結晶度不高、比表面積較低,且產物中含有較多雜相,也使得SO2吸附容量不高。通常情況下,活性氧化鋁因具備較高的比表面而成為常用的脫硫劑載體,然而活性氧化鋁在組織結構上易于團聚導致其孔結構較少,因此表現出較差的SO2去除效果(FuelProcessingTechnology,2013,114,81–100.)。針對現有技術的不足,本發(fā)明首次提出將粉煤灰合成物相單一、結晶度較高、形貌規(guī)則的、熱穩(wěn)定較好的FAU型沸石分子篩作為載體,負載CuO-CeO2用于去除煙氣中的SO2。這樣一方面可以提高粉煤灰的綜合利用價值,另外也為煙氣脫硫提供一種價廉易得、性能良好的脫硫劑,從而達到“以廢治廢”的效果,對促進粉煤灰的資源化利用以及環(huán)境保護具有重要的現實意義。在本發(fā)明中,我們報道了通過堿熔融-水熱法以粉煤灰為原料制備FAU型沸石分子篩,并以FAU沸石為載體負載CuO-CeO2形成脫硫劑材料(CuO-CeO2/FAU)。相比于其它粉煤灰合成方法,堿熔融-水熱法具有產物的轉化率高、產量大以及純度高的優(yōu)點,尤其在水熱反應前引入堿熔融活化處理過程,可以將煤灰中的石英、莫來石可以轉化為硅鋁酸鹽,有利于水熱反應的進行,堿熔融過程在FAU沸石合成中發(fā)揮了重要的作用。粉煤灰制FAU沸石尤其適合作為催化劑載體,這是由于粉煤制FAU沸石具有天然礦物八面沸石的骨架結構,其結構單元與LTA分子篩一樣,均是β籠,β籠像金剛石中的碳原子一樣排列,相鄰的β籠之間通過六方柱連接,從而形成一個超籠結構和三維孔道體系。超籠中含有4個按四面體取向的十二圓環(huán)孔口,其直徑7.4?×7.4?。其較大的空體積(約占50%)和三維十二元環(huán)孔道體系,使得它在催化方面有著極其重要的應用。同時,由于二氧化硫是一種比較活潑的氣體,科研人員研究發(fā)現許多金屬氧化物如氧化錳、氧化鋅、氧化鐵、氧化銅等氧化物對二氧化硫具有較強的吸附性,在常溫或低溫下,金屬氧化物對二氧化硫起吸附作用,高溫情況下,金屬氧化物與二氧化硫發(fā)生化學反應,生成金屬鹽,從而實現脫硫的目的。從吸附效果和經濟性來講,在眾多的金屬氧化物中,銅和鐵最有應用前景,常用于脫硫劑的制備。此外,享有“工業(yè)維生素”美稱的CeO2因具有+4和+3兩種價態(tài),能夠進行儲存和釋放氧的,即在富氧條件下+3價氧化成+4價,在催化反應中,又可以釋放參與氧化反應。同時,添加適量的CeO2可以避免沸石在高溫下燒造成比表面積的燒結,可以提高脫硫劑的反應活性和動力學反應特性。當煙氣通過CuO-CeO2/FAU脫硫劑時,SO2被吸附到脫硫劑表面的活性位,形成吸附態(tài)的SO2,吸附態(tài)的SO2與鄰近的氧化銅所攜帶的氧鍵合后形成SO3,吸附態(tài)的SO3與鄰近的銅配位形成硫酸銅鹽,脫硫劑表面的氧空位由氣氛中的氧或CeO2中氧釋放進行填充。吸附過SO2的脫硫劑可以在H2或CH4的氣氛中進行還原再生。
技術實現要素:發(fā)明目的:針對目前現有技術的不足之處,本發(fā)明采用堿熔融-水熱法,以粉煤灰為原料合成具有單一物相、結晶度較高、熱穩(wěn)定較好且比表面積較大的FAU型沸石分子篩,并首次將粉煤灰制FAU型沸石分子篩作為載體,負載CuO-CeO2金屬氧化物制備脫硫劑。所述的制備方法包括堿熔融-水熱法和浸漬法,首先在酸浸后的粉煤灰原料中添加NaOH助熔劑進行堿熔融反應,得到硅鋁酸鹽,然后,加入去離子水,攪拌一定時間后,得到硅鋁溶膠-凝膠體系,轉移至晶化反應釜,密封陳化一段時間后,再在一定溫度下進行晶化反應后,離心、洗滌、干燥得到粉煤灰制FAU型沸石分子篩。最后,將所得到的FAU沸石分子篩浸漬在含Cu(NO3)2和Ce(NO3)3的溶液中,振蕩過濾后,將浸漬后的樣品進行干燥和煅燒,得到CuO-CeO2/FAU脫硫劑。本發(fā)明的技術方案是:一種基于粉煤灰的CuO-CeO2/FAU脫硫劑的制備方法,包括以酸浸后的粉煤灰為原料,采用堿熔融-水熱法制備FAU型沸石分子篩,然后將粉煤灰制FAU沸石為載體,運用溶液浸漬法,使得沸石內孔表面負載上CuO-CeO2金屬氧化劑制備脫硫劑,此多孔性的脫硫劑可以將SO2吸附到內孔道,在400℃下,氧化銅與SO2反應生成硫酸銅,從而達到去除煙氣中SO2的目的,本發(fā)明的制備過程包括如下兩個步驟:1.1第一步是FAU型粉煤灰沸石的制備:取適量粉煤灰在100℃的條件下烘干24h,待冷卻后,按5:1~10:1(V/m)的比例加入4~6mol/L的鹽酸,在室溫下溶解1~2h,濾去上層輕質部分,將下層沉淀物質反復洗滌過濾,至中性,得到酸浸后粉煤灰原料,然后取適量酸浸處理的粉煤灰,按質量比1.25:1~1:1.25(灰/NaOH)的比例加入NaOH,研磨后置于鎳坩堝中,在500~600℃下焙燒60~90min,將所得到的堿熔融物研磨后置于250mL錐形瓶中,按1:7~1:11的比例加入去離子水,在室溫下磁力攪拌(250r/min)2~3.5h得到硅鋁凝膠,然后將硅鋁凝膠轉移至反應釜中,室溫下密封陳化6~75h后,然后將反應釜置于烘箱中,調節(jié)溫度在90~100℃,晶化反應3~24h后,離心、洗滌至產物pH值約為8~9,收集固相成分,在100℃下干燥后,研磨成粉末狀,得FAU型沸石分子篩;1.2第二步是FAU型沸石分子篩內孔表面負載CuO-CeO2金屬氧化劑:取適量的上述粉煤灰制FAU型沸石分子篩1.000~1.500g置于50mL錐形瓶中,加入0.1~1mol/L的Cu(NO3)2溶液20mL,再于錐形瓶后中添加0.01~0.05mol/L的Ce(NO3)3溶液2~5mL,在室溫下振蕩2~3h,轉速為200~250r/min,離心,將過濾后得到的沸石于烘箱中,干燥24h后取出樣品置于剛玉坩堝中,程序升溫至300~400℃,在該條件下煅燒3~5h,得到CuO-CeO2/FAU脫硫劑;作為對現有技術的進一步發(fā)展,所說的沸石分子篩的合成原料為粉煤灰固體廢棄物以及酸、堿,沒有其他的添加劑或導向劑;所說的粉煤制FAU型沸石分子篩具有物相單一、形狀規(guī)則、分散性好、比表面積大、多孔結構、結晶度高和熱穩(wěn)定性高的特點;所說的CuO-CeO2/FAU脫硫劑中的CuO在FAU沸石載體上以單分子層分散形式存在;所說的CuO-CeO2/FAU脫硫劑能夠對SO2進行物理和化學吸附;所說的脫硫劑原料來源豐富、易制備、成本低,具有極強的市場應用前景。相對于現有技術的有益效果。近年來,以粉煤灰為原料合成沸石吸引了大批研究者的興趣。2013年HumsJosepfErich等人公開了發(fā)明專利(WO2013144865A1)“SynthesisofzeoliteXwithhierarchicalmorphologyfromflyash”,該發(fā)明提供了具有多級形貌的X型沸石的合成方法。它采用了下述步驟:將粉煤灰原料與NaOH混合在高溫下反應獲得堿熔融熟料,按質量比1~5:1加入去離子水得到漿料,此后進行固液分離,對分離后的液體在80~100℃進行晶化反應,得到X型粉煤灰沸石,所合成的沸石的最大BET比表面積為282.41m2/g。2010年張志劍等公開了“功能化粉煤灰沸石復合顆粒的制備方法”(CN102091593A),該方法首先將粉煤灰、堿金屬和水按質量比100:4.8:200混合后,在60℃下攪拌反應5h,然后加入鋁酸鈉調節(jié)初步水熱處理的硅鋁摩爾比為1.5:1,反應20h后,繼續(xù)按粉煤灰:氧化鈣為100:1的比例添加氧化鈣,反應2h后,將反應產物進行過濾、洗滌和干燥,最后得到粉煤灰納米沸石復合顆粒,該沸石復合顆粒比表面積為38.4~70.2m2/g,可用于氮磷回收與脫除。2013年楊魁等公布了“循環(huán)流化床及底灰合成沸石的方法”(CN103204518A),該方法將脫炭處理后的粉煤灰底灰與經球磨機磨細后的底灰進行混合,按固液比為5:1(重量比)加入3.2mol/L的堿液,在95℃的常壓體系下進行攪拌反應,最后洗滌產物至pH為9,收集固相成分,干燥后續(xù)得到A型沸石產物,其外比表面積為0.974±0.023m2/g。2013年王建成等在“超臨界水熱合成粉煤灰沸石的方法”(CN103408032A)公開了利用超臨界水熱合成法制備了粉煤灰沸石,并將其用于脫除煤氣中的汞,最佳脫除率為95%以上。但是這些文獻報道的以粉煤灰為原料制備沸石分子篩,在合成方法上條件較苛刻、合成周期較長、需要引入添加劑等缺點,并且所合成的產物比表面積不高。并且,在粉煤灰沸石的利用方面并沒有涉及到脫硫劑的制備。因此,運用粉煤灰為原料制備高比面積和高熱穩(wěn)定性的沸石分子篩,將其作為載體用于脫硫劑的制備,能夠為粉煤灰沸石提供新的利用途徑。本發(fā)明首先是以堿熔融-水熱法制備FAU型粉煤灰沸石:用電子天平準備稱取25.000g烘干后的粉煤灰,按10:1(V/m)的比例加入6mol/L的鹽酸,在室溫下溶解2h,濾去上層輕質部分,將下層沉淀物質反復洗滌過濾,至中性,干燥后得到酸浸后粉煤灰原料。然后準確稱取5.000g酸浸處理的粉煤灰,按質量比1:1.25(灰/NaOH)的比例加入NaOH,研磨后置于鎳坩堝中,在600℃下焙燒90min,將所得到的堿熔融物研磨后置于250mL錐形瓶中,按1:11的比例加入去離子水,在室溫下磁力攪拌(250r/min)3.5h得到硅鋁凝膠,然后將硅鋁凝膠轉移至反應釜中,室溫下密封陳化53h后,置于烘箱中在100℃下晶化24h后,離心、洗滌至pH值為8~9。100℃下干燥12h后,研磨成粉末狀,得FAU型沸石分子篩。其次,是FAU沸石內孔表面負載有CuO和CeO2脫硫劑的制備:取適量的上述粉煤灰制FAU型沸石分子篩1.500g置于50mL錐形瓶中,加入0.5mol/L的Cu(NO3)2溶液20mL,再于錐形瓶后中添加0.05mol/L的Ce(NO3)3溶液2mL,在室溫下振蕩3h,轉速為250r/min。離心,將分離后得到的沸石于烘箱中,干燥12h后取出樣品置于剛玉坩堝中,程序升溫至300~400℃,在該條件下煅燒5h,得到CuO-CeO2/FAU脫硫劑。綜上所述,基于粉煤灰合成的CuO-CeO2/FAU脫硫劑,是對粉煤灰進行酸浸預處理后,通過堿熔融反應對粉煤灰中的石英和莫來石等成分進行活化得到硅鋁酸鹽熟料,然后對添加去離子水后的硅鋁凝膠在室溫下陳化一段時間后,置于水熱環(huán)境下經歷硅酸鹽和鋁酸鹽的再聚合、沸石成核、生長以及二次成核等過程得到沸石晶體,再通過浸漬法在沸石內孔表面負載上CuO和CeO2得到CuO-CeO2/FAU脫硫劑,最后將CuO-CeO2/FAU脫硫劑置于固定流化床中部,300~400℃下,通過CuO與SO2反應生成硫酸銅,實現煙氣脫硫的目的。其一:基于粉煤灰合成的CuO-CeO2/FAU脫硫劑,合成原料為粉煤灰。粉煤灰為熱電廠產生的固體廢棄物,其來源廣且儲量大,不僅可以節(jié)約化工原料,而且由于廢物利用,將拓寬粉煤灰的綜合利用途徑,具有巨大的經濟效益和環(huán)保效益;合成過程中沒有導向劑或模板劑等有機物的參與,環(huán)保性好;該合成方法具有設備簡單、易于操作等優(yōu)點。其二:基于粉煤灰合成的CuO-CeO2/FAU脫硫劑,尤其是對粉煤灰酸浸處理以去除堿土金屬以及有機揮發(fā)物等雜質后,進行堿熔融反應獲得均勻片狀的硅鋁酸鹽,有易于后續(xù)的晶化反應,獲得結晶性能更好的沸石晶體。其三:基于粉煤灰合成的CuO-CeO2/FAU脫硫劑,其載體為粉煤灰制FAU型分子篩,其物相單一、為規(guī)則的正八面體形貌、結晶度較高(88.78%)、比表面積較大(343.64m2/g)、熱穩(wěn)定性較好,具有多孔性,其介孔體積占71.05%,其骨架結構由硅氧四面體和鋁氧四面體構成,具有雙六元環(huán)結構。其四:基于粉煤灰合成的CuO-CeO2/FAU脫硫劑,其所采用的載體粉煤灰制FAU沸石的化學組成在合成前后發(fā)生了很大的變化,本發(fā)明中所采用的粉煤灰質量組成(SiO2:49.11%,Al2O3:24.90%,CaO:11.66%,Fe2O3:4.84%,TiO2:1.52%,MgO:1.50%)、酸浸后粉煤灰質量組成(SiO2:55.90%,Al2O3:33.81%,CaO:0.51%,Fe2O3:3.54%,TiO2:1.46%,MgO:0.50%)和粉煤灰制FAU沸石質量組成(SiO2:44.38%,Al2O3:31.15%,CaO:0.46%,Fe2O3:3.56%,TiO2:1.46%,MgO:0.44%)。如上述成分表示,再根據美國實驗材料協(xié)會,本發(fā)明所采用的粉煤灰原料屬于低鈣F類粉煤灰;酸浸后的粉煤灰在Ca2+和Mg2+等金屬離子均明顯下降,SiO2和Al2O3在原料中的組成相對含量提高;粉煤灰制FAU沸石產品的SiO2/Al2O3的摩爾比為2~2.5:1,在組成上為X型分子篩。其五:基于粉煤灰合成的CuO-CeO2/FAU脫硫劑,是在粉煤灰制FAU型沸石上負載CuO和CeO2金屬氧化劑,通過控制Cu(NO3)2的濃度,實現CuO活性組分在沸石顆粒表面的單分子層分散,沸石中含有CeO2可以防止脫硫劑在高溫下造成比表面積的燒結,并且添加適量的CeO2可以提高脫硫劑的反應活性和動力學反應特性。其六:基于粉煤灰合成的CuO-CeO2/FAU脫硫劑,其載體上單分子層分散的活性組分CuO含量為8.88%,利用載體的多孔性,將SO2吸附到脫硫劑孔隙內,在400℃下,活性組分CuO與SO2反應生成CuSO4,從而成功捕獲煙氣中SO2。所說的煙氣成分為2.03vol%SO2、9.94vol%CO2、10.34vol%O2、其余為N2。在300~400℃脫硫反應的方程式如下:其七:基于粉煤灰合成的CuO-CeO2/FAU脫硫劑,可以在H2或CH4的氣體氛圍下進行還原,然后在O2氛圍下氧化再生,從而增加脫硫劑的使用周期。附圖說明圖1是本發(fā)明所采用堿熔融-水熱法合成沸石分子篩的工藝流程示意圖。圖2是本發(fā)明所采用的粉煤灰原料X-射線衍射圖。圖3是本發(fā)明所采用的粉煤灰掃描電子顯微鏡圖。圖4是本發(fā)明所采用的粉煤灰堿熔融熟料的掃描電子顯微鏡圖。圖5是本發(fā)明所采用粉煤灰制FAU沸石分子篩的X-射線衍射圖。圖6是本發(fā)明所采用的粉煤灰制FAU沸石分子篩的掃描電子顯微鏡圖。圖7是本發(fā)明所采用的粉煤灰制FAU沸石分子篩的傅里葉-紅外光譜圖。圖8是本發(fā)明所采用的粉煤制FAU沸石分子篩的DSC-TGA曲線,插圖是800℃煅燒下FAU沸石X-射線衍射圖。圖9是本發(fā)明所采用的粉煤制FAU沸石分子篩吸附等溫曲線圖。圖10是本發(fā)明所采用的粉煤制FAU沸石分子篩孔徑分布圖。圖11是本發(fā)明所采用的CuO-CeO2/FAU脫硫劑的制備及脫硫反應示意圖。圖12是本發(fā)明所采用的不同CuO負載量下CuO-CeO2/FAU的X-射線衍射圖。圖13是本發(fā)明所采用的不同負載量下CuO-CeO2/FAU的掃描電子顯微鏡圖。根據附圖進一步解釋具體實施方式。圖1是本發(fā)明所采用的CuO-CeO2/FAU脫硫劑載體粉煤灰制FAU沸石分子篩的合成示意圖。其具體制備步驟如下:(1)粉煤灰原粉在100℃的條件下干燥24h以除去其中的水分等雜質;(2)將干燥后的粉煤灰進行研磨,加入6mol/L的鹽酸溶解2h,以除去其中的有機質和可溶性Ca2+、Mg2+和Fe(II、III)等金屬離子;(3)稱取5.000g算經預處理后的粉煤灰和NaOH按質量比1:1.25的充分混合,置于鎳坩堝中,在600℃溫度煅燒90min。(4)將上述制得的熟料按1:11(m/V)加入去離子水,在室溫下強烈攪拌3.5h直至固體溶解,得到一定比例的硅鋁溶膠。將所得的硅鋁溶膠置于具有Teflon襯里的不銹鋼反應釜,密封后在室溫下陳化53h后,然后在100℃下水熱反應24h,反應結束后,將所得樣品離心進行固液分離,并用去離子水反復洗滌,直到產物的pH值在8~9左右。收集固相成分,在100℃下干燥后,研磨成粉末狀,得FAU沸石分子篩。圖2是本發(fā)明所采用的粉煤灰原料X-射線衍射圖。粉煤灰的主要晶相為石英(SiO2)、方解石(CaCO3)、氧化鈣(CaO)和硬石膏(CaSO4),次要晶相是莫來石(3Al2O3·2SiO2)和高嶺石(Al2Si2O5(OH)4)以及硅線石(Al2SiO5),此外還有少量的金剛石(C)。圖3是本發(fā)明所采用的粉煤灰掃描電子顯微鏡圖。(A)表示粉煤灰原料在1.00k放大倍數下,顆粒為實心球體,此外還有少量碎屑,以不規(guī)則顆粒為主,(B)和(C)分別表示在2.70k和8.00k的放大倍數下,粉煤灰的結構特征為片狀,(D)表示在27.0k放大倍數下,可以看出顆粒表面密實粗糙。根據不同放大倍數的顯微圖片可知,此粉煤灰顆粒大多表現為不規(guī)則的密實顆粒。圖4是本發(fā)明所采用的粉煤灰堿熔融熟料的掃描電子顯微鏡圖。粉煤灰堿熔融熟料呈片狀且成分均一,說明堿熔融的效果非常好,這將有助于后續(xù)的水熱合成反應。圖5是本發(fā)明所采用粉煤灰制FAU沸石分子篩的X-射線衍射圖。根據PDF卡片索引,為FAU沸石,英文名Faujasite,syn,PDF卡片號為12-0228,分子式為Na2Al2Si3.3O10.67·H2O。由圖可以看出,衍射峰強度較高,本底有細小漫散峰,通過Jade軟件計算,其結晶度為88.78%。粉煤灰制FAU型沸石的孔道由12個硅氧四面體或鋁氧四面體圍成,形成一個平行于<111>方向的三維十二元環(huán)孔道體系,其孔徑在0.75nm左右,與<111>方向相垂直的面網是晶體的主要晶面。其孔道結構均是β籠,相鄰的β籠通過雙六元環(huán)(D6R)連接。圖6是本發(fā)明所采用的粉煤灰制FAU沸石分子篩的掃描電子顯微鏡圖。圖(A)產物在放大1.00k時,可以觀察到合成產物大小均勻,轉化率較高;(B)和(C)分別表示在放大2.50k和5.00k時,可以觀察到產物為規(guī)則的正八面體;(D)表示在產物放大22.0k時,可以測得沸石晶粒的邊長約為3.85μm。由圖可以看出,實驗中所合成的粉煤灰FAU-CFA轉化率較高、產物結晶性好、物相較純。圖7是本發(fā)明所采用的粉煤灰制FAU沸石分子篩的傅里葉-紅外光譜圖,測定區(qū)域為400~1300cm-1。硅鋁沸石分子篩由于骨架振動而引發(fā)的譜帶大部分出現在中紅外區(qū),通常具有如下特點:(1)在1000cm-1附近有很強的吸收;(2)在450cm-1有較強的吸收;(3)在450~1000cm-1與200~400cm-1兩種區(qū)間范圍內,沸石的骨架構型不同,其吸收譜帶也表現為較大的差異。一般來說,雙環(huán)結構的振動峰在500~650cm-1區(qū)間出現。FAU型沸石在562cm-1處有較強的吸收,則認為雙六元環(huán)的特征振動吸收峰。FAU型沸石在1005cm-1和986cm-1處吸收峰最強,其次,較強的吸收峰均出現在460cm-1處,為內部四面體的彎曲振動。圖8是本發(fā)明所采用的粉煤制FAU沸石分子篩的DSC-TGA曲線。FAU沸石在80℃處有一個小吸熱谷,這是沸石脫去表面吸附水的過程(100℃以下)。而空穴內部的水需要的較高的溫度才能釋放出來,并且由圖可以看出,盡管FAU-CFA沸石的孔徑較大,至少需要加熱到400℃,所有的自由水和鈉離子結合水才能全部脫去,FAU沸石的質量損失6.88%;并且由圖可以看出,FAU沸石在700℃附近有一小吸熱峰,并且沒有出現質量的損失,說明這是一個晶格轉變特征峰,伴隨著FAU沸石的骨架結構的坍塌,在更高的溫度下重結晶生成新的物相,由上文中的煅燒實驗可知,在800℃下FAU-CFA已轉變成霞石晶相。插圖是800℃煅燒下FAU沸石X-射線衍射圖。FAU型沸石在700℃溫度范圍內,可以保持骨架結構的穩(wěn)定,在400~800℃內,沸石所對應的TG曲線仍舊比較平滑,質量沒有發(fā)生變,說明FAU-CFA熱穩(wěn)定性較好,能夠滿足工業(yè)上分子篩700℃以下的在催化和吸附等領域的應用要求。圖9是本發(fā)明所采用的粉煤制FAU沸石分子篩吸附等溫曲線圖。參照IUPAC(InternationalUnionofPureandAppliedChemistry)吸附等溫線的四種類型,兩種沸石的吸附等溫線同時結合了I和IV型吸附等溫線的特性,多數沸石和類沸石分子篩的吸附平衡等溫線為I型,說明所合成的沸石具有多級孔結構特征。由于氮氣與沸石孔壁的強相互作用,吸附開始于很低的相對壓力下,在較低的相對壓力下(<0.3)微孔填充沒有觀察到毛細管凝聚現象,難以與單分子層吸附相區(qū)分。在相對壓力為0.4時,在兩種沸石的吸附和脫附等溫線出現分離,表現為一個遲滯環(huán)(hysteresisloop),說明吸附劑中存在大量的介孔和大孔,吸附質在吸附劑在介孔材料吸附等溫線中經常出現。并且,根據IUPAC遲滯環(huán)的分類,實驗中所合成的FAU沸石為H4型,H4型多歸因于狹縫孔道,根據出現H4遲滯環(huán)的材料的孔的性質,可以判斷FAU-CFA孔的形狀和尺寸較均勻。根據吸附等溫線,采用BET方程計算得到實驗中所合成的粉煤灰制FAU沸石的比表面積為343.64m2/g,室驗中所合成的粉煤灰沸石比表面積較大,明顯優(yōu)于天然材料,因此粉煤灰沸石有望成為一種可替代的催化劑載體、吸附劑等。圖10是本發(fā)明所采用的粉煤制FAU沸石分子篩孔徑分布圖。粉煤灰制FAU沸石分子篩孔徑主要集中在50nm以下,說明沸石屬于介孔材料(2~50nm)。從孔徑分布圖可以看出FAU型粉煤灰沸石呈現三個明顯的峰值,分別為3.91nm,10.24nm和27.07nm,50nm以下的空體積占71.05%,說明所采用的粉煤灰制FAU沸石的孔大部分為介孔。圖11是本發(fā)明所采用的CuO-CeO2/FAU脫硫劑的制備及脫硫再生示意圖。稱取適量上述粉煤灰制FAU型沸石分子篩于錐形瓶中,加入一定量的Cu(NO3)2和Ce(NO3)3溶液,在室溫下振蕩、離心,收集沉淀物干燥后,取出樣品于剛玉坩堝中,程序升溫至400℃,升溫速率為10℃/min,在該溫度下煅燒一段時間后,得到CuO-CeO2/FAU脫硫劑,然后稱取0.500~1.000gCuO-CeO2/FAU脫硫劑置于管式反應爐中部,通入混氣后進行脫硫,最后將進行脫硫反應后的CuO-CeO2/FAU脫硫劑在H2或CH4的氣體氛圍種進行還原,再在O2氛圍下進行氧化再生。圖12是本發(fā)明所采用的不同CuO負載量下CuO-CeO2/FAU的X-射線衍射圖。0M表示煅燒400℃下粉煤灰制FAU型沸石分子篩;0.1M、0.5M和1M分別為浸漬制備過程中Cu(NO3)2溶液的濃度為0.1mol/L、0.5mol/L和1mol/L的脫硫劑。由圖可知,0.1M試樣除了FAU沸石載體外,幾乎不存在其他的衍射峰,因此可以認為此時試樣中CuO大部分以單層或亞單層形式分布在FAU-CFA內外表面上;0.5M脫硫劑試樣除了原有的載體FAU-CFA衍射峰,同時在35.46°和38.78°處有明顯的CuO衍射峰,這是由于載體中的CuO達到了其單層分布容量,發(fā)生了明顯的團聚,導致了CuO晶體的出現;1M試樣載體FAU-CFA的衍射峰消失,只有CuO特征衍射峰,這有可能此試樣沸石載體的孔道和骨架結構在煅燒過程中發(fā)生塌陷的原因。CuO的團聚現象會造成其脫硫劑的活性降低,同時過量負載也會造成活性組分的浪費,因此,浸漬液濃度為0.1mol/L最為適宜。通過紫外分光光度法,計算得到此時脫硫劑CuO的含量為8.5~9.0%。圖13是本發(fā)明所采用的不同負載量下CuO-CeO2/FAU的掃描電子顯微鏡圖。由圖可知,0M和0.1M脫硫劑的形貌沒發(fā)生太大變化,基本為正八面體形貌;而0.5M試樣正八面載體的表面結構發(fā)生了較大的變化,轉變成了類似尖晶石的表面結構,1M脫硫劑試樣的載體形貌也基本消失,表面粗糙疏松多孔,沒有固定形態(tài),這與XRD檢測結果一致,同時在試樣中還發(fā)現有團聚的條狀CuO晶體。因此,從SEM形貌來看,0.1M脫硫劑試樣比較好,與圖12的XRD表征結果一致。具體實施方式1:一種基于粉煤灰的CuO-CeO2/FAU脫硫劑的制備方法,包括以酸浸后的粉煤灰為原料,采用堿熔融-水熱法制備FAU型沸石分子篩,然后將粉煤灰制FAU沸石為載體,運用溶液浸漬法,使得沸石內孔表面負載上CuO-CeO2金屬氧化劑制備脫硫劑,此多孔性的脫硫劑可以將SO2吸附到內孔道,在400℃下,氧化銅與SO2反應生成硫酸銅,從而達到去除煙氣中SO2的目的,本發(fā)明的制備過程包括如下兩個步驟:1.1第一步是FAU型粉煤灰沸石的制備:取適量粉煤灰在100℃的條件下烘干24h,待冷卻后,按5:1~10:1(V/m)的比例加入4~6mol/L的鹽酸,在室溫下溶解1~2h,濾去上層輕質部分,將下層沉淀物質反復洗滌過濾,至中性,得到酸浸后粉煤灰原料。然后取適量酸浸處理的粉煤灰,按質量比1.25:1~1:1.25(灰/NaOH)的比例加入NaOH,研磨后置于鎳坩堝中,在500~600℃下焙燒60~90min,將所得到的堿熔融物研磨后置于250mL錐形瓶中,按1:7~1:11的比例加入去離子水,在室溫下磁力攪拌(250r/min)2~3.5h得到硅鋁凝膠,然后將硅鋁凝膠轉移至反應釜中,室溫下密封陳化6~75h后,然后將反應釜置于烘箱中,調節(jié)溫度在90~100℃,晶化反應3~24h后,離心、洗滌至產物pH值約為8~9,收集固相成分,在100℃下干燥后,研磨成粉末狀,得FAU型沸石分子篩;1.2第二步是FAU型粉煤灰沸石內孔表面負載CuO-CeO2金屬氧化劑:取適量的上述粉煤灰制FAU型沸石分子篩1.000~1.500g置于50mL錐形瓶中,加入0.1~1mol/L的Cu(NO3)2溶液20mL,再于錐形瓶后中添加0.01~0.05mol/L的Ce(NO3)3溶液2~5mL,在室溫下振蕩2~3h,轉速為200~250r/min。離心,將分離后得到的沸石于烘箱中,干燥24h后取出樣品置于剛玉坩堝中,程序升溫至300~400℃,在該條件下煅燒3~5h,得到CuO-CeO2/FAU脫硫劑。具體實施方式2:準確稱取0.500~1.000gCuO-CeO2/FAU脫硫劑置于管式反應爐中部,通入混氣(2.03vol%SO2、9.94vol%CO2、10.34vol%O2、余N2),體積流量為1.4~2L/min,采用德國EcomJ2KN煙氣分析儀檢測尾氣中SO2的含量。反應溫度為400℃下,反應時間為200~300min,測得脫硫率為85%以上。