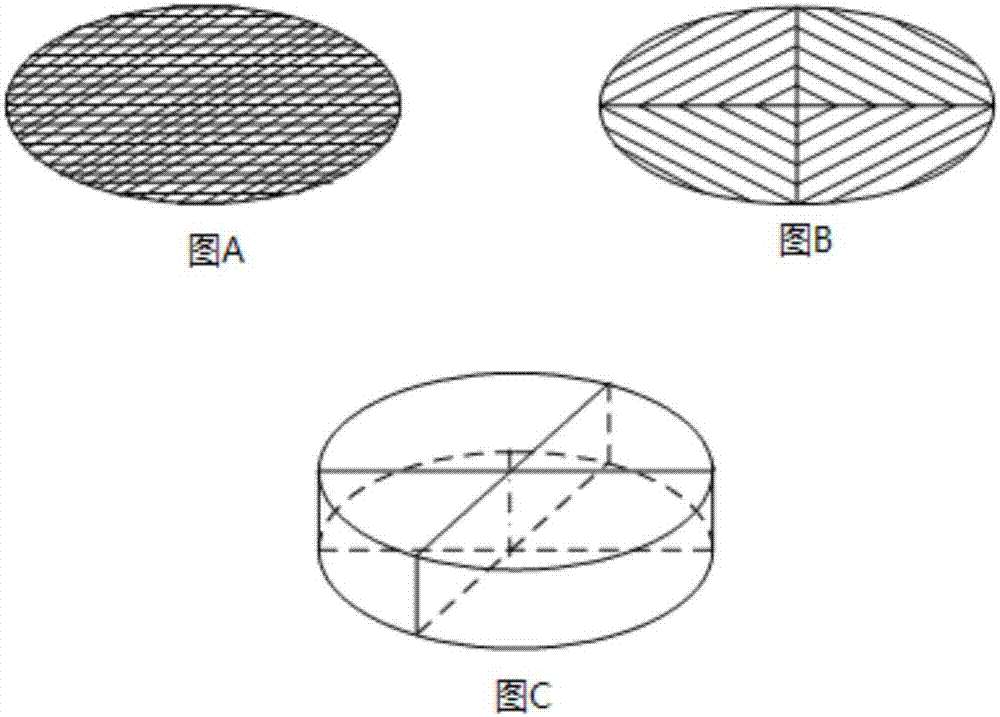
本發(fā)明涉及烴油加氫
技術領域:
,具體地,本發(fā)明涉及一種適用于液相加氫工藝的反應裝置和反應系統(tǒng),本發(fā)明還涉及采用所述反應系統(tǒng)的液相加氫反應方法。
背景技術:
:煉油加工技術主要包括催化裂化、加氫和延遲焦化等技術。其中,油品加氫技術是煉油技術最常用的技術之一。隨著原油的重劣質(zhì)趨勢加劇,同時世界各國對油品清潔程度要求越來越高,加氫裝置占的比重越來越大。目前,煉油加氫工藝主要為固定床加氫工藝、沸騰床加氫工藝和懸浮床加氫工藝。沸騰床加氫工藝和懸浮床加氫工藝主要用于處理渣油等重劣質(zhì)原料,固定床工藝技術應用則較為廣泛,包括汽油、柴油、蠟油和渣油的加氫精制;選擇性加氫脫烯烴、脫硫;加氫改質(zhì)或加氫裂化等。傳統(tǒng)的固定床加氫工藝為滴流床加氫工藝。傳統(tǒng)的滴流床加氫工藝為氣液固三相加氫工藝,反應系統(tǒng)中需要維持大量的循環(huán)氫;并且,在進行加氫反應時,氫氣需要從氣相進入液相,然后與反應物共同吸附在催化劑的表面,從而在催化劑活性中心的作用下進行反應,這一傳質(zhì)過程無疑會對加氫處理工藝的反應速率產(chǎn)生不利影響。針對滴流床加氫工藝存在的不足,研究人員開發(fā)了液相加氫工藝,但是早期的液相加氫工藝為了彌補烴油攜氫量的不足,需要將部分加氫產(chǎn)物循環(huán)和/或采用稀釋劑,以提高進料的氫氣攜帶量,滿足加氫反應的要求。隨著液相加氫工藝研究的深入,研究人員對烴油與氫氣的混合工藝進行改進,開發(fā)出了不采用加氫產(chǎn)物循環(huán),同時也不采用稀釋劑的液相加氫工藝。具體地,cn103666547b公開了一種烴油加氫處理方法,該方法包括在混合裝置中將氫氣注入烴油中,得到攜氫烴油,所述攜氫烴油進入固定床反應器中,在液相加氫處理條件下,與具有催化加氫作用的催化劑接觸,其中,通過平均孔徑為納米尺寸的通孔將氫氣一次或分次注入所述烴油中,注入的氫氣的總量為所述烴油的化學氫耗量的0.1-4倍,所述攜氫烴油與具有催化加氫作用的催化劑的接觸在不存在循環(huán)油的條件下進行。技術實現(xiàn)要素:盡管cn103666547b能在不存在循環(huán)油和稀釋劑的條件下,將烴油進行液相加氫處理,但是在實際操作過程中發(fā)現(xiàn),采用該方法將烴油進行加氫處理,仍然存在需要進一步提高加氫反應的效率的技術問題。本發(fā)明的發(fā)明人針對上述技術問題進行了深入研究,發(fā)現(xiàn)如果在反應器的催化劑床層之間設置分隔元件,將該分隔元件所處徑向截面分割成多個小區(qū)域,并使得從前一個催化劑床層輸出的物料通過這些小區(qū)域進入下一個催化劑床層進行反應,能有效地提高加氫反應的效率,獲得更好的加氫反應效果。基于上述發(fā)現(xiàn),完成了本發(fā)明。根據(jù)本發(fā)明的第一個方面,本發(fā)明提供了一種氣液反應裝置,該反應裝置包括反應器和至少一個混合器,所述反應器的內(nèi)部空間設置有n個用于裝填催化劑的催化反應區(qū),n為2以上的整數(shù),其中,第m個催化反應區(qū)與第m+1個催化反應區(qū)之間通過至少一個分隔構件相接,m為選自區(qū)間[1,n-1]的任意整數(shù),所述分隔構件用于將該分隔構件所處的催化反應區(qū)的徑向截面分割成多個分區(qū),并使得第m個催化反應區(qū)輸出的物料能通過所述多個分區(qū)進入第m+1個催化反應區(qū)中;所述混合器設置在所述反應器的內(nèi)部和/或外部,且以反應物料在反應器內(nèi)的流向為基準,所述混合器設置在第1個催化反應區(qū)的上游,用于將氣相反應原料與液相反應原料混合,使得氣相反應原料溶解和/或作為分散相分散在所述液相反應原料中,形成原料混合物,并將原料混合物送入反應器中;所述混合器含有第一通道和第二通道,所述第一通道具有用于將氣相反應原料引入該通道的入口,所述第二通道具有用于將液相反應原料引入該通道的入口以及將原料混合物引出該通道的出口,所述第一通道和所述第二通道之間通過一構件鄰接,所述構件的至少部分區(qū)域為有孔區(qū),所述第一通道內(nèi)的氣相反應原料通過所述有孔區(qū)中的孔而進入所述第二通道中,形成所述原料混合物。根據(jù)本發(fā)明的第二個方面,本發(fā)明提供了一種用于液相加氫的反應系統(tǒng),該反應系統(tǒng)包括反應單元以及汽提單元,所述反應單元包括本發(fā)明第一個方面所述的反應裝置,用于將烴油與氫氣在液相加氫處理條件下接觸,所述汽提單元與所述反應裝置的反應器的液相反應產(chǎn)物輸出端連通,用于將所述反應器輸出的液相反應產(chǎn)物進行汽提,以除去所述液相反應產(chǎn)物中的揮發(fā)性物質(zhì)。根據(jù)本發(fā)明的第三個方面,本發(fā)明提供了一種液相加氫處理方法,該方法在本發(fā)明第二個方面所述的反應系統(tǒng)中進行,包括以下步驟:(1)將烴油送入混合器的第二通道中,將氫氣送入混合器的第一通道中,并使得氫氣通過所述構件上的有孔區(qū)進入第二通道中,與烴油混合,得到含氫烴油;(2)將混合器輸出的含氫烴油以向上流動的方式送入反應器中,并依次通過反應器內(nèi)的n個催化反應區(qū),以與具有加氫催化作用的催化劑在液相加氫處理條件下接觸,得到加氫反應產(chǎn)物物流;(3)將所述加氫反應產(chǎn)物物流送入汽提單元中進行汽提,以除去加氫反應產(chǎn)物物流中的揮發(fā)性物質(zhì)。采用本發(fā)明的反應裝置將烴油進行液相加氫,不僅能實現(xiàn)在不采用循環(huán)油(即,循環(huán)的液相加氫產(chǎn)物)和稀釋劑的條件下,將烴油進行液相加氫,而且能有效地提高加氫反應的效率,獲得更好的加氫反應效果。附圖說明附圖是用來提供對本發(fā)明的進一步理解,并且構成說明書的一部分,與下面的具體實施方式一起用于解釋本發(fā)明,但并不構成對本發(fā)明的限制。圖1用于說明根據(jù)本發(fā)明的反應裝置采用的混合器中,用于鄰接第一通道和第二通道的構件的一種優(yōu)選實施方式,其中,圖a為該構件的立體示意圖,圖b為該構件的截面的示意圖;圖2用于說明根據(jù)本發(fā)明的反應裝置中采用的分隔元件的優(yōu)選實施方式,其中,圖a為采用篩網(wǎng)作為分隔元件,圖b為采用格柵作為分隔元件,圖c為采用肋板作為分隔元件;圖3用于說明根據(jù)本發(fā)明的反應裝置的一種優(yōu)選實施方式;圖4用于說明根據(jù)本發(fā)明的用于液相加氫工藝的反應系統(tǒng)的一種優(yōu)選實施方式。附圖標記說明301:混合器302:下封頭303:筒體304:混合器構件305:氣相反應原料入口306:液相反應原料入口307:壓力表308:反應器309:連接管道310:支撐篩板311:第一催化劑床層312:第二催化劑床層313:熱電偶314:分隔構件315:液相空間316:氣相空間317:液相導出管路318:液相減壓閥319:壓力表320:氣相壓力調(diào)節(jié)閥321:安全閥401:液相原料輸送管路402:進料泵403:換熱器404:混合器405:預加熱器406:反應器407:氣相輸出管路408:汽提塔409:廢氣輸出管路410:汽提塔塔底泵具體實施方式以下對本發(fā)明的具體實施方式進行詳細說明。應當理解的是,此處所描述的具體實施方式僅用于說明和解釋本發(fā)明,并不用于限制本發(fā)明。在本文中所披露的范圍的端點和任何值都不限于該精確的范圍或值,這些范圍或值應當理解為包含接近這些范圍或值的值。對于數(shù)值范圍來說,各個范圍的端點值之間、各個范圍的端點值和單獨的點值之間,以及單獨的點值之間可以彼此組合而得到一個或多個新的數(shù)值范圍,這些數(shù)值范圍應被視為在本文中具體公開。根據(jù)本發(fā)明的第一個方面,本發(fā)明提供了一種用于氣液反應的反應裝置,該反應裝置包括反應器和至少一個混合器。所述混合器用于將氣相反應原料與液相反應原料混合,使得氣相反應原料溶解和/或作為分散相分散在所述液相反應原料中,形成原料混合物,并將原料混合物送入反應器中。所述混合器含有第一通道和第二通道,所述第一通道具有用于將氣相反應原料引入該通道的入口,所述第二通道具有用于將液相反應原料引入該通道的入口以及將原料混合物引出該通道的出口,所述第一通道和所述第二通道之間通過一構件鄰接,所述構件的至少部分區(qū)域為有孔區(qū),所述第一通道內(nèi)的氣相反應原料通過所述有孔區(qū)中的孔而進入所述第二通道中。本發(fā)明中,術語“通道”是指用于容納原料的空間。所述構件中的有孔區(qū)中的孔為足以連通第一通道和第二通道的通孔,這樣能使得第一通道內(nèi)的氣相反應原料通過所述通孔而進入第二通道內(nèi),與第二通道內(nèi)的液相反應原料混合。從進一步提高混合效果的角度出發(fā),所述有孔區(qū)中的孔的平均孔徑優(yōu)選為不超過5μm。更優(yōu)選地,所述有孔區(qū)中的孔的平均孔徑為不超過3μm。進一步優(yōu)選地,所述有孔區(qū)中的孔的平均孔徑為不超過1μm。更進一步優(yōu)選地,所述有孔區(qū)中的孔的平均孔徑為1~800nm,這樣能更為有效地提高反應的效率,獲得明顯提高的反應效果。特別優(yōu)選地,所述有孔區(qū)中的孔的平均孔徑為50~500nm。所述平均孔徑采用電鏡法測定。可以在所述構件的部分區(qū)域設置有孔區(qū),也可以在所述構件的整個區(qū)域設置有孔區(qū)。從進一步提高混合效率的角度出發(fā),所述構件至少50%以上的區(qū)域為有孔區(qū),更優(yōu)選60%以上的區(qū)域為有孔區(qū),進一步優(yōu)選80%以上的區(qū)域為有孔區(qū),更進一步優(yōu)選90%以上的區(qū)域為有孔區(qū)。特別優(yōu)選所述構件的整個區(qū)域為有孔區(qū)。所述有孔區(qū)中的孔隙率可以根據(jù)該構件的具體類型進行選擇。在能使得構件具有滿足使用要求的強度的條件下,從進一步提高混合效率的角度出發(fā),所述有孔區(qū)中的孔隙率優(yōu)選為5~45%,更優(yōu)選為10~40%,進一步優(yōu)選為20~35%。所述孔隙率是指有孔區(qū)中的孔隙體積占有孔區(qū)的總體積的百分數(shù),采用氮氣吸附法方法測定。所述構件的具體形式?jīng)]有特別限定,只要所述構件能使得兩條通道相鄰接即可。在一種實施方式中,所述構件為隔板,可以在一個箱體中設置具有有孔區(qū)的隔板,將箱體的內(nèi)部空間分隔為兩個部分,分別作為第一通道和第二通道。在另一種實施方式中,如圖1所示,所述構件為管道,其中,管道的壁的至少部分區(qū)域為有孔區(qū)??梢詫⒐艿琅c一殼體配合使用,使得管道的外壁與殼體的內(nèi)壁之間留有空間,從而形成由所述管道的壁相鄰接的第一通道和第二通道。在該實施方式中,所述管道本體上的通道可以為1條,優(yōu)選為2條以上,如4~20條。在該實施方式中,所述管道的壁的至少部分區(qū)域為有孔區(qū),從而將第一通道和第二通道連通。在一種實施方式中,所述管道的壁上的有孔區(qū)中的孔的平均孔徑不滿足前文所述的孔徑尺寸,此時可以在所述管道的壁的內(nèi)表面和/或外表面上設置多孔膜,所述多孔膜中的孔的平均孔徑為滿足前文所述的孔徑尺寸。即,所述多孔膜上的孔的平均孔徑為不超過5μm,優(yōu)選為不超過3μm,更優(yōu)選為不超過1μm,進一步優(yōu)選為1~800nm,更進一步優(yōu)選為50~500nm。在另一種實施方式中,所述管道的壁上的有孔區(qū)中的孔的平均孔徑為前文所述的孔徑尺寸,此時可以在所述管道的壁的內(nèi)表面和/或外表面上設置所述多孔膜,也可以不設置多孔膜。在該實施方式中,所述管道(包括多孔膜)的材質(zhì)以不會與第一通道和第二通道中流通的物料發(fā)生化學相互作用、并且能在混合條件下仍然具有滿足要求的強度為準,例如可以為金屬、陶瓷或者聚合物。根據(jù)本發(fā)明的反應裝置,所述第一通道和第二通道各自設置有入口,以將氣相反應原料和液相反應原料分別引入第一通道和第二通道中。第二通道在容納所述液相反應原料的同時,還為混合提供空間,從而獲得原料混合物。所述第二通道還設置有出口,用于將原料混合物引出。所述第一通道可以設置出口,也可以不設置出口。對于第二通道,優(yōu)選將所述入口設置在第二通道的一端,將出口設置在與所述入口相對的另一端,這樣一方面能獲得更好的混合效果,另一方面還能提高混合器與反應器的裝配性。對于第一通道,可以將入口設置在第一通道的一端,優(yōu)選將入口設置在與所述構件相對的側(cè)壁上,這樣能使得進入第一通道的氣相反應原料更易于透過有孔區(qū)進入第二通道中進行混合。在進行操作時,通常使得第一通道內(nèi)的壓力高于用于第二通道內(nèi)的壓力,利用壓力差將第一通道內(nèi)的氣相反應原料壓入第二通道內(nèi)。從進一步提高所述構件的使用壽命的角度出發(fā),優(yōu)選在第一通道的入口處設置防沖擊擋板,以避免從第一通道的入口引入的物料對所述構件產(chǎn)生沖擊。所述防沖擊擋板設置在第一通道的入口處,使得由入口引入的物料撞擊所述沖擊擋板后,進入第一通道內(nèi)。所述防沖擊擋板的材質(zhì)可以為常見的不會與第一通道內(nèi)的物料發(fā)生化學相互作用的材料,例如金屬板、陶瓷板或者聚合物板。所述混合器還可以設置壓力檢測元件,從而對第一通道內(nèi)的壓力進行監(jiān)控,從而調(diào)控送入第一通道的氣相反應原料的量。根據(jù)本發(fā)明的反應裝置,反應器的內(nèi)部空間設置有n個用于裝填催化劑的催化反應區(qū),其中,n為2以上的整數(shù),可以為2~10的整數(shù),例如:2、3、4、5、6、7、8、9或者10。優(yōu)選地,n為2~8的整數(shù)。更優(yōu)選地,n為2~4的整數(shù)。根據(jù)本發(fā)明的反應裝置,第m個催化反應區(qū)與第m+1個催化反應區(qū)之間通過至少一個分隔構件相接,其中,m為選自區(qū)間[1,n-1]的任意整數(shù)。作為一個實例,在n為2~10的整數(shù)時,m為選自區(qū)間[1,9]的任意整數(shù),可以為1、2、3、4、5、6、7、8或9。即,反應器的內(nèi)部空間中,至少兩個相鄰的催化反應區(qū)之間通過至少一個分隔構件相接。可以在任意兩個相鄰的催化反應區(qū)之間設置所述分隔構件,也可以在每兩個相鄰的催化反應區(qū)之間設置所述分隔構件。所述分隔構件用于將該分隔構件所處的反應器的徑向截面空間分割成多個區(qū)域,同時所述分隔構件還能使得第m個催化反應區(qū)輸出的物料通過由該分隔構件分隔出的區(qū)域,進入第m+1個催化反應區(qū)中。所述分隔構件可以為常見的能實現(xiàn)上述作用的構件。在一種優(yōu)選的實施方式中,所述分隔構件為篩網(wǎng)型分隔構件、格柵型分隔構件以及肋板型分隔構件中的一種或兩種以上的組合。所述篩網(wǎng)型分隔構件為多孔網(wǎng)狀,例如可以為圖2中的圖a示出的篩網(wǎng)。所述篩網(wǎng)中的網(wǎng)孔的直徑可以為篩網(wǎng)的常見尺寸。從進一步提高反應效率的角度出發(fā),所述篩網(wǎng)中的網(wǎng)孔的直徑優(yōu)選為10~250μm,更優(yōu)選為30~150μm,進一步優(yōu)選為50~100μm,更進一步優(yōu)選為60~80μm。所述格柵型分隔構件可以為圖2中的圖b示出的格柵。格柵中,柵條之間的間距可以為格柵的常見尺寸。從進一步提高反應效率的角度出發(fā),柵條之間的間距優(yōu)選為2~100mm,更優(yōu)選為10~40mm,進一步優(yōu)選為15~30mm。以肋板作為分隔構件時,可以通過將兩個以上的肋板交叉設置(如圖2中的圖c所示),從而將徑向截面分隔成多個區(qū)域。交叉設置的肋板的數(shù)量可以為2條以上,優(yōu)選為4~6條。所述分隔構件的尺寸隨催化反應區(qū)的徑向尺寸而定,以能使得第m個催化反應區(qū)的液體物料全部由該分隔構件進入第m+1個催化反應區(qū)為準。相鄰的兩個催化反應區(qū)之間設置的分隔構件的數(shù)量可以為1個,也可以為2個以上。在所述分隔構件為篩網(wǎng)型分隔構件或者格柵型分隔構件時,在相鄰的兩個催化反應區(qū)之間設置一個分隔構件即可有效地提高反應的效率,當然相鄰的兩個催化反應區(qū)之間也可以設置兩個以上分隔構件。在所述分隔構件為肋板型分隔構件時,可以在相鄰的兩個催化反應區(qū)之間設置一個分隔構件,從進一步提高加氫效率的角度出發(fā),優(yōu)選設置兩個以上分隔構件,該兩個以上分隔構件可以均為肋板型分隔構件,也可以為肋板型分隔構件與篩網(wǎng)型分隔構件和/或格柵型分隔構件的組合。在兩個以上分隔構件均為肋板型分隔構件時,相鄰的兩個肋板型分隔構件優(yōu)選為錯位設置,即相鄰的兩個肋板型分隔構件向水平面進行投影時,肋板的投影位置不重合,這樣能更為有效地提高反應的效率。優(yōu)選地,將肋板型分隔構件與篩網(wǎng)型分隔構件和/或格柵型分隔構件組合使用,從而獲得進一步提高的反應效率。在將肋板型分隔構件與篩網(wǎng)型分隔構件和/或格柵型分隔構件組合使用時,以物料的流向為基準,所述肋板型分隔構件可以位于所述篩網(wǎng)型分隔構件和格柵型分隔構件的上游,也可以設置在篩網(wǎng)型分隔構件和格柵型分隔構件的下游,還可以將肋板型分隔構件與篩網(wǎng)型分隔構件和格柵型分隔構件間隔設置。優(yōu)選地,將肋板型分隔構件設置在篩網(wǎng)型分隔構件和格柵型分隔構件的下游,或者將肋板型分隔構件與篩網(wǎng)型分隔構件和格柵型分隔構件間隔設置,且在該組分隔構件的最下游設置篩網(wǎng)型分隔構件或者格柵型分隔構件??梢圆捎贸R?guī)方法將所述分隔構件固定在反應器中。例如,可以將所述分隔構件的外周固定在反應器的內(nèi)壁上。固定方式?jīng)]有特別限定,具體可以列舉出焊接、螺栓固定和卡扣固定中的一種或兩種以上的組合。根據(jù)本發(fā)明的反應裝置,相鄰的催化反應區(qū)之間的間距可以為常規(guī)選擇,沒有特別限定。所述催化反應區(qū)用于填充催化劑,以使得進入催化反應區(qū)的物料與催化劑接觸進行反應。所述催化反應區(qū)中可以設置常見的各種構件用于填充催化劑,例如:可以在催化反應區(qū)中設置支撐板,用于承載袋裝催化劑;也可以在催化反應區(qū)中設置用于容納催化劑的容器,用于容納散裝催化劑。在催化反應區(qū)中可以設置溫度檢測元件和加熱元件,以對催化反應區(qū)中的溫度進行監(jiān)控和調(diào)節(jié)。所述溫度檢測元件和所述加熱元件可以為兩個獨立的元件,也可以將溫度檢測元件和加熱元件整合在一個元件中。具體地,可以在催化反應區(qū)中設置熱電偶,從而對催化反應區(qū)中的溫度進行監(jiān)控和調(diào)節(jié)。所述反應器的內(nèi)部空間還可以設置液相空間和氣相空間,以液相物料在反應器內(nèi)的流向為基準,所述液相空間位于第n個催化反應區(qū)的下游,且位于所述氣相空間的上游。所述液相空間用于接納來自于催化反應區(qū)的液相物料,所述氣相空間用于接納從液相空間逸出的氣相物料。在所述反應器的內(nèi)部空間具有液相空間和氣相空間時,所述反應裝置還可以具有壓力控制單元和液位監(jiān)測單元。所述壓力控制單元用于對氣相空間中的壓力進行調(diào)控。所述壓力控制單元可以包括壓力檢測元件和壓力調(diào)節(jié)元件。所述壓力檢測元件可以為常見的各種能檢測壓力變化的元件,如壓力表。所述壓力調(diào)節(jié)元件可以為各種能調(diào)節(jié)容器壓力的元件,如氣相壓力調(diào)節(jié)閥。根據(jù)壓力檢測元件檢測到的壓力值,壓力調(diào)節(jié)元件可以相應進行排氣或者補氣,從而對氣相空間中的壓力進行調(diào)控。所述液位監(jiān)測單元用于對液相空間中的液位高度進行監(jiān)控。所述液位監(jiān)測單元可以采用常規(guī)方法對液相空間中的液位高度進行監(jiān)測,例如:可以在反應器上設置監(jiān)測孔,從而對液相空間中的液位高度進行監(jiān)測;還可以設置液位傳感器,從而對液相空間中的液位高度進行監(jiān)測。根據(jù)本發(fā)明的反應裝置,反應器上設置有用于引入反應原料的入口,用于將反應產(chǎn)物引出的出口。所述出口的數(shù)量可以根據(jù)引出的反應產(chǎn)物的類型進行選擇,可以包括用于引出液相物料的液相物流出口和/或用于引出氣相物料的氣相物流出口。根據(jù)本發(fā)明的反應裝置,從進一步提高反應器的操作安全性的角度出發(fā),優(yōu)選在反應器的頂部設置安全閥。所述安全閥可以為常見的各種安全閥,可以為彈簧式安全閥和/或杠桿式安全閥。根據(jù)本發(fā)明的反應裝置,所述混合器可以設置在反應器的內(nèi)部,也可以設置在反應器的外部。優(yōu)選地,所述混合器設置在反應器外部,這樣既能減小反應器的占地面積,又便于維修??梢圆捎贸R?guī)方法將所述混合器與所述反應器連接在一起,從而使得混合器輸出的原料混合物能進入所述反應器的催化反應區(qū)中,與催化劑接觸反應。所述混合器與所述反應器之間的連接為密封連接,從而避免物料泄露??梢酝ㄟ^在混合器的原料混合物出口(即,第二通道的出口)處與所述反應器的反應物料入口設置法蘭盤,通過螺栓將混合器上的混合原料出口與反應器上的反應原料入口連通。根據(jù)具體情況,還可以設置連接管道,以連接混合器上的原料混合物出口以及所述反應器上的反應原料入口。在連接處可以采用各種密封材料,如橡膠密封墊。從進一步提高反應效果的角度出發(fā),所述混合器上的原料混合物出口的內(nèi)徑、反應器上的反應原料入口的內(nèi)徑、以及可選的連接管道的內(nèi)徑之間的比例優(yōu)選為1:0.6~1.5:0.6~1.5,更優(yōu)選為1:0.8~1.2:0.8~1.2。圖3示出了根據(jù)本發(fā)明的反應裝置的一種優(yōu)選實施方式。以下結(jié)合圖3對該優(yōu)選實施方式進行詳細說明。如圖3所示,混合器301設置在反應器308的外部,且設置在反應器308的底部?;旌掀?01為具有下封頭302的筒體303,筒體內(nèi)填充多個管道壁為多孔的管道作為混合器構件304,所述管道的外壁與所述筒體的內(nèi)壁之間留有空間,將管道本體上的通道作為第二通道,將管道與筒體內(nèi)壁之間的空間作為第一通道。在殼體的下封頭302上設置氣相反應原料入口305,用于為第一通道提供物料,在筒體303的側(cè)壁上設置液相反應原料入口306,用于為第二通道提供原料。在氣相反應原料入口305入口處優(yōu)選設置防沖擊板(圖3中未示出)以避免進入第一通道的氣相反應原料直接撞擊管道的外壁,使得管道的外壁被沖蝕。在筒體303上可以設置壓力表307,以對第一通道內(nèi)的壓力進行監(jiān)控?;旌掀?01的上端與連接管道309密封連接,用于接納混合器301的第二通道輸出的原料混合物,并將原料混合物送入反應器308中。在反應器308的入口處設置支撐篩板310,由連接管309進入的原料混合物能均勻地進入反應器的催化反應區(qū)(即,具有催化劑的區(qū)域)。反應器308中設置有至少兩個催化劑床層(圖3僅示例性地示出兩個催化劑床層,分別為第一催化劑床層311和第二催化劑床層312)。催化劑床層中可以設置熱電偶(圖3中為在第二催化劑床層312中設置熱電偶313),從而對第一催化劑床層311和第二催化劑床層312的溫度進行調(diào)控。在第一催化劑床層311和第二催化劑床層312之間設置分隔構件314,從而將分隔構件314所處徑向截面分隔成多個小區(qū)域,使得第一催化劑床層311流出的物流通過所述多個小區(qū)域進入第二催化劑床層312中。在第二催化劑床層312的上游設置液相空間315,用于接納從第二催化劑床層312流出的液相物料。在液相空間315的上游設置氣相空間316,用于接納從液相空間315中逸出的氣相物料。在反應器308的外部(通常為頂部)設置用于引出液相空間315中的液相物料的液相導出管路317。在液相導出管路317上可以設置液相減壓閥318。在液相空間315相對應的反應器壁上可以設置觀察窗口(圖3中未示出),以對液相空間315內(nèi)的液位高度進行觀察。在反應器308的外部(通常為頂部)設置用于對氣相空間316中的壓力進行監(jiān)控的壓力表319,同時還設置氣相壓力調(diào)節(jié)閥320,從而根據(jù)壓力表319的顯示值,確定是否開啟氣相壓力調(diào)節(jié)閥320以及開啟的程度。為確保反應器安全運行,同時還設置安全閥321。以下結(jié)合圖3,對本發(fā)明的反應裝置的操作方法進行詳細說明。將液相反應原料從液相反應原料入口306引入混合器301內(nèi)的第二通道中,將氣相反應原料從氣相反應原料入口305引入混合器301內(nèi)的第一通道中。通過壓力表307對第一通道內(nèi)的壓力進行監(jiān)控,從而調(diào)節(jié)送入第一通道內(nèi)的氣相反應原料在第一通道與第二通道之間形成壓力差,使得第一通道內(nèi)的氣體通過管道的壁上的孔而進入第二通道中,與第二通道中的液相反應原料混合,形成原料混合物。原料混合物離開混合器301,通過連接管道309,進入反應器308中。在反應器308中,原料混合物通過底部支撐篩板310進入第一催化劑床層311中,與催化劑在液相反應條件下接觸反應。從第一催化劑床層311流出的物流通過分隔構件314進入第二催化劑床層312中繼續(xù)與催化劑在液相反應條件下接觸反應。在反應過程中,通過熱電偶313對第一催化劑床層311和第二催化劑床層312中的溫度進行調(diào)節(jié),以使其滿足反應要求。由第二催化劑床層312流出的物流進入液相空間315中,從液相空間315逸出的氣相物流進入氣相空間316中。通過設置在反應器壁上的觀察窗口對液相空間315中的液位高度進行監(jiān)控,使其滿足反應器的操作要求。通過液相導出管路317將液相空間315中的液相反應物引出。在反應過程中,由壓力表319對氣相空間316中的壓力進行監(jiān)控,通過氣相壓力調(diào)節(jié)閥320,根據(jù)壓力表319的檢測壓力,確定是否需要將氣相空間的氣相物流引出以及引出量。根據(jù)本發(fā)明的反應裝置特別適用于實施氣液反應。本領域技術人員可以理解的是本發(fā)明的反應裝置也可以實施液液反應。根據(jù)本發(fā)明的第二個方面,本發(fā)明提供了一種用于液相加氫的反應系統(tǒng),該反應系統(tǒng)包括反應單元以及汽提單元,所述反應單元包括本發(fā)明第一個方面所述的反應裝置,用于將烴油與氫氣在液相加氫處理條件下接觸,所述汽提單元與所述反應裝置的反應器的液相反應產(chǎn)物輸出端連通,用于將所述反應器輸出的液相反應產(chǎn)物進行汽提,以除去所述液相反應產(chǎn)物中的揮發(fā)性物質(zhì)。所述反應裝置在本發(fā)明第一個方面中已經(jīng)進行了詳細的說明,此處不再詳述。所述汽提單元可以采用常規(guī)的各種汽提裝置對反應單元輸出的液相反應產(chǎn)物進行汽提。具體地,所述汽提單元可以包括汽提塔以及相應的管路,以將液相反應產(chǎn)物引入汽提塔,進行汽提,并將汽提產(chǎn)生的氣相物流輸出,將經(jīng)汽提的液相反應產(chǎn)物送出反應裝置,進入后續(xù)的操作單元中。圖4示出了根據(jù)本發(fā)明的反應系統(tǒng)的一種優(yōu)選實施方式。以下結(jié)合圖4對該優(yōu)選實施方式進行詳細說明。如圖4所示,加氫原料油由液相原料輸送管路401通過進料泵402,進入換熱器403中,與液相加氫反應產(chǎn)物進行換熱后,進入混合器404的第二通道中。氫氣通過預加熱器405加熱后,進入混合器404的第一通道中。在混合器404中將加氫原料油與氫氣混合得到加氫反應原料。將加氫反應原料以向上流的方式送入加氫反應器406中,在液相加氫處理條件下與具有加氫催化作用的催化劑接觸反應,得到加氫反應產(chǎn)物。反應過程中,將加氫反應器406輸出的氣相物流通過氣相輸出管路407輸出。將加氫反應產(chǎn)物送入汽提塔408中進行汽提,汽提出的氣相物流通過廢氣輸出管路409輸出,經(jīng)汽提的加氫反應產(chǎn)物中的至少部分通過汽提塔塔底泵410進入換熱器403中與加氫原料油換熱后輸出,剩余部分可以直接輸出。根據(jù)本發(fā)明的反應系統(tǒng)特別適用于將烴油在液相加氫處理條件下進行加氫處理,能夠在較低的氫氣用量下,獲得更高的加氫處理效果。由此,根據(jù)本發(fā)明的第三個方面,本發(fā)明提供了一種液相加氫處理方法,該方法在本發(fā)明第二個方面所述的反應系統(tǒng)中進行,包括以下步驟:(1)將烴油送入混合器的第二通道中,將氫氣送入混合器的第一通道中,并使得氫氣通過所述構件上的有孔區(qū)進入第二通道中,與烴油混合,得到含氫烴油;(2)將混合器輸出的含氫烴油以向上流動的方式送入反應器中,并依次通過反應器內(nèi)的n個催化反應區(qū),以與具有加氫催化作用的催化劑在液相加氫處理條件下接觸,得到加氫反應產(chǎn)物物流;(3)將所述加氫反應產(chǎn)物物流送入汽提單元中進行汽提,以除去加氫反應產(chǎn)物物流中的揮發(fā)性物質(zhì)。步驟(1)中,烴油與氫氣可以在常規(guī)條件下進行混合。從進一步提高混合效果以及加氫反應效果的角度出發(fā),優(yōu)選烴油和氫氣在加氫處理溫度下進行混合。根據(jù)本發(fā)明的加氫處理方法,即使在較低的氫氣用量下,也能獲得提高的加氫反應效果。氫氣的具體用量可以根據(jù)烴油的種類以及加氫反應的類型進行選擇。一般地,相對于100體積烴油,氫氣的用量可以為0.1~30000體積,優(yōu)選為1~10000體積,更優(yōu)選為1.5~1000體積,進一步優(yōu)選為2~500體積,更進一步優(yōu)選為2.2~300體積,特別優(yōu)選為2.5~150體積。步驟(2)中,具有加氫催化作用的催化劑可以根據(jù)處理的烴油的種類以及加氫反應的類型進行選擇,沒有特別限定。步驟(2)中,含氫烴油與具有加氫催化作用的催化劑在液相加氫處理條件下接觸反應。所述液相加氫處理條件是指在加氫反應過程中,液相烴油作為連續(xù)相,氫氣作為分散相溶解分散在烴油中。步驟(2)中,含氫烴油與具有加氫催化作用的催化劑在足以使得加氫反應進行的條件下進行。可以根據(jù)烴油的具體種類以及進行的加氫反應的類型進行選擇。一般地,溫度可以為130~400℃,壓力可以為0.3~20mpa,優(yōu)選為1~10mpa,所述壓力為表壓。步驟(2)中,含氫烴油即使以較高的空速進入反應器與催化劑接觸反應,也能獲得較好的反應效果。一般地,含氫烴油的體積空速可以為0.5~50h-1,優(yōu)選為0.8~20h-1,更優(yōu)選為1~10h-1。步驟(3)中,汽提可以在常規(guī)條件下進行,沒有特別限定。汽提出的氣相物流可以直接送入后續(xù)燃燒系統(tǒng)中進行處理。經(jīng)汽提的加氫反應產(chǎn)物物流可以直接送入后續(xù)的操作單元中進行處理。根據(jù)本發(fā)明的液相加氫處理方法,無需將液相加氫產(chǎn)物物流循環(huán)送入反應器中;并且混合器和反應器的進料也無需稀釋油。根據(jù)本發(fā)明的液相加氫處理方法可以對多種烴油進行加氫處理。所述烴油可以為重質(zhì)油和/或輕質(zhì)油,其具體實例可以包括但不限于汽油、重整生成油、噴氣燃料、柴油、常壓渣油、減壓渣油、催化裂化循環(huán)油和煤焦油中的一種或兩種以上。根據(jù)本發(fā)明的液相加氫處理方法可以進行多種類型的加氫反應,特別優(yōu)選為加氫精制,例如可以為加氫脫烯烴、加氫脫硫、加氫脫氮、加氫脫氧和加氫脫金屬中的一種或多種。以下結(jié)合實施例詳細說明本發(fā)明,但并不因此限制本發(fā)明的范圍。以下實施例和對比例中,采用掃描電鏡來測定平均孔徑,采用壓汞法方法測定孔徑分布,采用氮氣吸附法測定孔隙率。以下實施例和對比例中,壓力均為表壓。實施例1~6用于說明本發(fā)明。實施例1本實施例在圖4示出的反應系統(tǒng)中進行,其中,采用圖3示出的反應裝置?;旌掀髦械臉嫾楣鼙跒槎嗫椎墓艿?商購自北京中天元環(huán)境工程有限責任公司,管道橫截面如圖1所示,管道上均勻分布有19個液體通道,每個液體通道的內(nèi)徑為3.3mm,管壁上的孔的平均孔徑為50nm,孔徑處于50~55nm范圍內(nèi)的孔的占總孔的比例為98%,孔隙率為20%),該管道與一殼體配合使用,管道的外壁與殼體的內(nèi)壁形成的空間為原料通道,管道本體上的通道為混合通道?;旌掀魃系脑匣旌衔锍隹诘膬?nèi)徑、反應器上的反應原料入口的內(nèi)徑、以及連接管道的內(nèi)徑之間的比例為1:0.9:0.9。反應器中,裝填兩個催化劑床層,在兩個催化劑床層之間設置一個多孔篩網(wǎng),該多孔篩網(wǎng)的外徑與催化劑床層相同,由位于上游的催化劑床層流出的物流通過該多孔篩網(wǎng)進入位于下游的催化劑床層中。其中,多孔篩網(wǎng)中的網(wǎng)孔的直徑為75μm,兩個催化劑床層之間的距離為800mm。反應器中裝填的催化劑為購自中石化催化劑分公司的型號為hdo-18的催化劑。將催化重整生成油在換熱器中與反應器流出的加氫反應產(chǎn)物物流進行換熱,將原料油加熱至140℃后,送入混合器的第二通道中,第二通道內(nèi)的壓力為1.5mpa。將氫氣預熱至140℃后,送入混合器的第一通道中,并使得第一通道內(nèi)的氫氣進入第二通道中,與催化重整生成油混合,得到加氫反應原料物流。其中,氫氣與催化重整生成油的體積比為2.5:1。加氫反應原料物流進入反應器中,與催化劑在液相加氫處理條件下接觸反應。其中,反應條件為:溫度為140℃,壓力為1.5mpa,加氫反應原料物流的體積空速為6h-1。加氫反應得到的產(chǎn)物物流從加氫反應器的頂部輸出,進入汽提塔中進行汽提,得到的經(jīng)汽提的產(chǎn)物物流在換熱器中與作為原料的催化重整生成油進行換熱后,直接輸出,其性質(zhì)參數(shù)在表1中列出。對比例1采用與實施例1相同的方法進行加氫反應,不同的是,在催化劑床層之間不設置多孔篩網(wǎng)。得到的經(jīng)汽提的產(chǎn)物物流的性質(zhì)參數(shù)在表1中列出。實施例2采用與實施例1相同的方法進行加氫反應,不同的是,在催化劑床層之間設置的不是多孔篩網(wǎng),而是肋板型分隔構件,其中,肋板的數(shù)量為兩個,兩個肋板十字交叉設置,將肋板所處徑向截面分隔成面積均等的四塊。得到的經(jīng)汽提的產(chǎn)物物流的性質(zhì)參數(shù)在表1中列出。實施例3采用與實施例1相同的方法進行加氫反應,不同的是,在催化劑床層之間設置的分隔構件為多孔篩網(wǎng)(同實施例1)和肋板型分隔構件(同實施例2),其中,以反應物料的流向為基準,肋板型分隔構件位于多孔篩網(wǎng)的上游。得到的經(jīng)氣體的產(chǎn)物物流的性質(zhì)參數(shù)在表1中列出。實施例4采用與實施例1相同的方法進行加氫反應,不同的是,混合器中的構件為管壁為多孔的管道的壁上的孔的平均孔徑為5μm,孔隙率為35%,孔徑處于5~5.5μm范圍內(nèi)的孔占總孔的比例為95%(商購自北京中天元環(huán)境工程有限責任公司)。得到的經(jīng)汽提的產(chǎn)物物流的性質(zhì)參數(shù)在表1中列出。對比例2采用與實施例4相同的方法進行加氫反應,不同的是,在催化劑床層之間不設置多孔篩網(wǎng)。得到的經(jīng)汽提的產(chǎn)物物流的性質(zhì)參數(shù)在表1中列出。表1實施例5本實施例在圖4示出的反應系統(tǒng)中進行,其中,采用圖3示出反應裝置。混合器中的構件為管壁為多孔膜管(商購自北京中天元環(huán)境工程有限責任公司,管道基體上的通孔的平均孔徑為100μm,多孔膜上的通孔的平均孔徑為500nm,孔徑處于500~550nm范圍內(nèi)的孔的占總孔的比例為95%,孔隙率為25%),該管道與一殼體配合使用,管道的外壁與殼體的內(nèi)壁形成的空間為原料通道,管道本體上均勻分布的19條通道為混合通道。混合器上的原料混合物出口的內(nèi)徑、反應器上的反應原料入口的內(nèi)徑、以及連接管道的內(nèi)徑之間的比例為1:1:1。反應器中,裝填兩個催化劑床層,在兩個催化劑床層之間設置一個格柵,該格柵的外徑與催化劑床層相同,由位于上游的催化劑床層流出的物流通過該格柵進入位于下游的催化劑床層中。其中,格柵中柵條之間的間距為20mm,格柵的高度為50mm,兩個催化劑床層之間的距離為800mm。反應器中裝填的催化劑為購自中石化催化劑分公司的型號為rs-2000的催化劑。將焦化柴油在換熱器中與反應器流出的加氫反應產(chǎn)物物流進行換熱,將原料油加熱至350℃后,送入混合器的第二通道中,第二通道內(nèi)的壓力為8.0mpa。將氫氣預熱至350℃后,送入混合器的第一通道中,并使得第一通道內(nèi)的氫氣進入第二通道中,與焦化柴油混合,得到加氫反應原料物流。氫氣與焦化柴油的體積比為120:1。加氫反應原料物流進入加氫反應器中,與催化劑接觸反應。其中,反應條件為:溫度為350℃,壓力為8.0mpa,加氫反應原料物流的體積空速為1.5h-1。加氫反應得到的產(chǎn)物物流從加氫反應器的頂部輸出,進入汽提塔中進行汽提,得到的經(jīng)汽提的產(chǎn)物物流直接輸出,其性質(zhì)參數(shù)在表2中列出。對比例3采用與實施例5相同的方法進行加氫反應,不同的是,在催化劑床層之間不設置格柵。得到的經(jīng)汽提的產(chǎn)物物流的性質(zhì)參數(shù)在表2中列出。實施例6采用與實施例5相同的方法進行加氫反應,不同的是,混合器中的構件為管壁為多孔的管道的壁上的孔的平均孔徑為5μm,孔隙率為35%,孔徑處于5~5.5μm范圍內(nèi)的孔占總孔的比例為95%(商購自北京中天元環(huán)境工程有限責任公司)。得到的經(jīng)汽提的產(chǎn)物物流的性質(zhì)參數(shù)在表2中列出。對比例4采用與實施例6相同的方法進行加氫反應,不同的是,在催化劑床層之間不設置格柵。得到的經(jīng)汽提的產(chǎn)物物流的性質(zhì)參數(shù)在表2中列出。表2烴油性質(zhì)原料油實施例5對比例3實施例6對比例4密度(kg/m3)845.3828.6835.5832.3840.1總硫的質(zhì)量含量(ppm)247574198124297總氮的質(zhì)量含量(ppm)1830458640512732餾程(℃)初餾點21020220820220950%28727527728028595%355350354352355脫硫率(%)/97929588脫氮率(%)/75657260實施例1~6的結(jié)果證實,通過在反應器的催化反應區(qū)之間設置分隔構件,能有效地提高加氫反應的效率,獲得更好的加氫反應效果。以上詳細描述了本發(fā)明的優(yōu)選實施方式,但是,本發(fā)明并不限于上述實施方式中的具體細節(jié),在本發(fā)明的技術構思范圍內(nèi),可以對本發(fā)明的技術方案進行多種簡單變型,這些簡單變型均屬于本發(fā)明的保護范圍。另外需要說明的是,在上述具體實施方式中所描述的各個具體技術特征,在不矛盾的情況下,可以通過任何合適的方式進行組合,為了避免不必要的重復,本發(fā)明對各種可能的組合方式不再另行說明。此外,本發(fā)明的各種不同的實施方式之間也可以進行任意組合,只要其不違背本發(fā)明的思想,其同樣應當視為本發(fā)明所公開的內(nèi)容。當前第1頁12