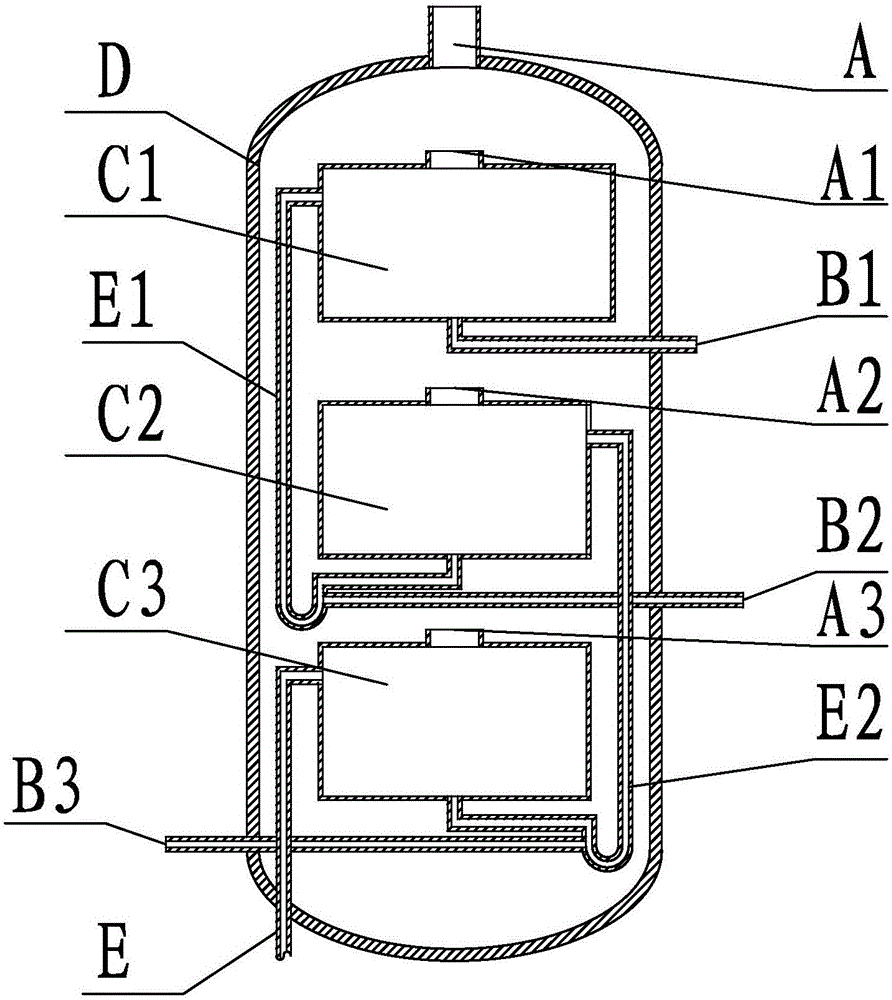
本發(fā)明涉及一種液相加氫反應(yīng)器及工藝方法,具體地說涉及一種加氫生成油循環(huán)的液相加氫反應(yīng)器,及使用該反應(yīng)器的液相加氫工藝方法。
背景技術(shù):
:在常規(guī)的固定床加氫工藝過程中,為了脫除原料中的硫、氮、氧、金屬等雜質(zhì)或減小原料油分子的大小,需要進行催化加氫反應(yīng)。為了控制催化劑床層的反應(yīng)溫度和避免催化劑積炭失活,通常采用較大的氫油體積比,在加氫反應(yīng)完成后必然有大量的氫氣富余。這些富余的氫氣通常經(jīng)循環(huán)氫壓縮機增壓后與新氫混合繼續(xù)作為反應(yīng)的氫氣進料。在這個工藝過程中,反應(yīng)器內(nèi)一般存在汽、液、固三相,氣相為氫氣以及汽化的原料油,液相為未汽化的原料油,固相為催化劑。由于氣相的量遠(yuǎn)遠(yuǎn)超過液相的量,在反應(yīng)器內(nèi),氣相是連續(xù)相,液相以滴流的形式通過催化劑床層,因此,被定義為滴流床反應(yīng)器,也可以定義為氣相循環(huán)滴流床加氫工藝。在三相滴流床反應(yīng)器內(nèi),氫氣需要從氣相傳遞到液相,然后在催化劑表面發(fā)生反應(yīng),這個過程需要大量氫氣來完成,一般氫油比(體積比)在50-5000:1,大量的過量氫氣需要進行循環(huán)使用,因此,該工藝循環(huán)氫壓縮機的投資占整個加氫裝置成本的比例較高,氫氣換熱系統(tǒng)能耗較大,如果能夠?qū)⒓託涮幚磉^程中的氫氣流量減小并省去氫氣循環(huán)系統(tǒng)和循環(huán)氫壓縮機,可以為企業(yè)節(jié)省投資,降低生產(chǎn)成本。一般含有簡單硫化物的原料在滴流床加氫反應(yīng)器中加氫脫硫的反應(yīng)速率除了與有機硫化物的濃度有關(guān)系外,還受催化劑的潤濕狀況、反應(yīng)器系統(tǒng)中的有機氮化物和H2S濃度等因素的影響。催化劑的潤濕因子是對在加氫反應(yīng)條件下催化劑表面被液體反應(yīng)物所浸潤程度的一種度量。催化劑的浸潤程度越高、催化劑的潤濕因子就越高,也就是說催化劑的有效利用率越高。在催化劑等因素確定的條件下,影響催化劑潤濕因子的主要因素是反應(yīng)器中液體的流速,以及氣體和液體流速的比(氫油比)。一般認(rèn)為,液體流速增加可增強催化劑潤濕效果,而常規(guī)加氫工藝多采用遠(yuǎn)遠(yuǎn)超過反應(yīng)所需的大氫油比,從而降低了催化劑的潤濕效果,對潤濕因子有不利的影響。有機氮化物是加氫催化劑的毒物,對加氫脫氮、加氫脫硫和加氫脫芳反應(yīng)有明顯的抑制作用。這種抑制作用主要是由于有些氮化物和大多數(shù)氮化物的中間反應(yīng)產(chǎn)物與催化劑的加氫反應(yīng)活性中心具有非常強的吸附能,從競爭吸附的角度抑制了其他加氫反應(yīng)的進行。而通過加氫產(chǎn)物循環(huán)將大大稀釋原料中的雜質(zhì)含量,有利于發(fā)揮催化劑的性能。加氫脫硫副產(chǎn)物H2S對加氫脫硫、脫氮、脫芳反應(yīng)也有明顯的抑制作用。少量H2S存在就會大大降低加氫脫硫速率,并且H2S在催化劑表面的吸附為單層吸附,一旦吸附中心被H2S占據(jù),反應(yīng)速率將不再隨H2S分壓提高而下降。因此,采用有效的手段消除H2S的影響是解決深度脫硫的關(guān)鍵問題。CN86108622公開了一種重整生成油的加氫精制工藝,氫油體積比為200:1-1000:1;CN93101935.4公開了一種劣質(zhì)原料油一段加氫裂化工藝方法,氫油體積比1300:1-1500:1;CN94102955.7公開了一種催化裂解汽油加氫精制方法,體積氫油比150:1-500:1。這些專利的特點是具有較高的氫油比,因此必須具有氫氣循環(huán)環(huán)節(jié)和循環(huán)氫壓縮機。US6213835、US6428686、CN200680018017.3等公開了一種預(yù)先溶解氫氣的加氫工藝,通過控制液體進料中的氫氣量控制反應(yīng)器中的液體量或氣壓。但其沒有完全解決將在加氫精制反應(yīng)過程中產(chǎn)生的H2S、NH3等有害雜質(zhì)脫除的問題,導(dǎo)致其不斷在反應(yīng)器內(nèi)累積,大大降低了反應(yīng)效率,也無法有效處理硫、氮含量較高的原料,上述文獻也沒有公開反應(yīng)器的具體結(jié)構(gòu)。鑒于上述現(xiàn)有的滴流床加氫工藝方法存在的問題,本發(fā)明人基于從事此類項目開發(fā)、研究、設(shè)計多年豐富的實務(wù)經(jīng)驗及專業(yè)知識,并配合學(xué)理的運用,積極加以研究創(chuàng)新,以期創(chuàng)設(shè)一種安全有效的液相加氫反應(yīng)器及液相加氫工藝方法,能夠解決現(xiàn)有的加氫技術(shù)存在的問題,使其更具有實用性。經(jīng)過不斷的研究、設(shè)計,并經(jīng)過反復(fù)試作樣品及改進后,終于創(chuàng)設(shè)出確具實用價值的本發(fā)明方法。技術(shù)實現(xiàn)要素:針對現(xiàn)有技術(shù)的不足,本發(fā)明提供一種成本低、效率高的加氫液相產(chǎn)物循環(huán)的液相加氫反應(yīng)器,采用適宜的結(jié)構(gòu)形式,有效地補充液相原料中的氫氣,同時脫除了進入催化劑床層的硫化氫和氨等雜質(zhì),避免了這些有害雜質(zhì)對催化反應(yīng)的不利影響;多個獨立的催化劑床層串聯(lián),增加了加氫處理工藝的靈活性,提高了原料適應(yīng)性和催化劑的有效活性,并延長了催化劑使用壽命。同時提供一種采用該反應(yīng)器的液相加氫工藝方法。本發(fā)明的目的及解決其技術(shù)問題是采用以下技術(shù)方案來實現(xiàn)的。本發(fā)明一種液相加氫反應(yīng)器,包括:廢氣總排出口(A)、獨立催化劑床層廢氣排出口(A1-An)、原料油輸入管線(B1)、氫氣補充管線(B2-Bn)、多個獨立催化劑床層(C1-Cn)、反應(yīng)器筒體(D)、產(chǎn)品輸出管線(E)、液相產(chǎn)物輸送管線(E1-E(n-1));其中,n為大于1的整數(shù);所述廢氣總排出口(A)設(shè)置于反應(yīng)器筒體(D)的頂端,所述的多個獨立催化劑床層(C1-Cn)之間是彼此串聯(lián)設(shè)置在反應(yīng)器筒體(D)內(nèi);獨立催化劑床層廢氣排出口(A1-An)設(shè)置于相應(yīng)的獨立催化劑床層(C1-Cn)的頂部;所述產(chǎn)品輸出管線(E)與最后一個獨立催化劑床層連通;所述的原料油輸入管線(B1)與第一獨立催化劑床層(C1)連通;氫氣補充管線(B2-Bn)與液相產(chǎn)物輸送管線(E1-E(n-1))連通;液相產(chǎn)物輸送管線(E1-E(n-1))的一端與獨立催化劑床層(C1-C(n-1))連通,另一端與獨立催化劑床層(C2-Cn)連通。本發(fā)明的目的及解決其技術(shù)問題還可采用以下技術(shù)措施進一步實現(xiàn)。前述的液相加氫反應(yīng)器,其中,所述的原料油輸入管線(B1)的一端與第一獨立催化劑床層(C1)的底部連通,另一端設(shè)于反應(yīng)器筒體(D)的外部;氫氣補充管線(B2-Bn)的一端與液相產(chǎn)物輸送管線(E1-E(n-1))連通,另一端設(shè)于反應(yīng)器筒體(D)的外部;其中,氫氣補充管線(B2)的一端與液相產(chǎn)物輸送管線(E1)連通,氫氣補充管線(Bn)的一端與液相產(chǎn)物輸送管線(E(n-1))連通。前述的液相加氫反應(yīng)器,其中,所述產(chǎn)品輸出管線(E)的上端設(shè)置于最后一個獨立催化劑床層上部的側(cè)面,下端設(shè)于反應(yīng)器筒體(D)的外部;所述液相產(chǎn)物輸送管線(E1-E(n-1))的上端設(shè)置于相應(yīng)的獨立催化劑床層(C1-C(n-1))上部的側(cè)面并與其連通,液相產(chǎn)物輸送管線(E1)下端與獨立催化劑床層(C2)底部連通,液相產(chǎn)物輸送管線(E(n-1))下端與獨立催化劑床層(Cn)底部連通。前述的液相加氫反應(yīng)器,其中,所述的多個獨立催化劑床層(C1-Cn)的上部分別設(shè)有氣液分離空間,廢氣總排出口(A)將多個獨立催化劑床層廢氣排出口(A1-An)排出的廢氣一并排出反應(yīng)器外,反應(yīng)生成的液相產(chǎn)物在氣-液分離空間的下部以溢流的方式流出,經(jīng)過液相產(chǎn)物輸送管線(E1-E(n-1))并與從相應(yīng)的氫氣補充管線進來的新氫混合后進入下一個獨立催化劑床層的底部。前述的液相加氫反應(yīng)器,其中,所述的多個獨立催化劑床層(C1-Cn)中裝填的催化劑類型相同或不同;獨立催化劑床層的個數(shù)為1-10個,優(yōu)選2-6個,最佳為3-4個。前述的液相加氫反應(yīng)器,其中,所述催化劑床層之間靠溢流控制液位。前述的液相加氫反應(yīng)器,其中,每個催化劑床層補充的新氫量按照氫油體積比為(1-100):1的比例補充,優(yōu)選(5-20):1。前述的液相加氫反應(yīng)器,其中,所述原料油輸入管線(B1)是從第一獨立催化劑床層(C1)的底部同時輸入新鮮原料、循環(huán)液體加氫產(chǎn)物、新氫三者的混合物,所述循環(huán)液體加氫產(chǎn)物與所述新鮮原料的體積比為(0.1-30):1,優(yōu)選(0.5-15):1,最佳為(1-5):1。前述的液相加氫反應(yīng)器,其中,催化劑床層的反應(yīng)條件為:反應(yīng)溫度150-450℃,反應(yīng)壓力1-20MPa,液時空速0.2-15h-1。前述的液相加氫反應(yīng)器,其中,利用該反應(yīng)器進行液相加氫反應(yīng)的工藝方法為:(1)將新鮮原料、循環(huán)液體加氫產(chǎn)物、新氫在管線中進行混合,使氫氣溶解在液體原料油中,形成一種新鮮原料、循環(huán)液體加氫產(chǎn)物、新氫的液相混合物,在加氫工藝條件下,該液相混合物從原料油輸入管線(B1)進入反應(yīng)器筒體(D),在第一獨立催化劑床層(C1)進行催化加氫反應(yīng),反應(yīng)產(chǎn)物在第一獨立催化劑床層(C1)上部的氣-液分離空間進行分離,廢氣從第一獨立催化劑床層廢氣排出口(A1)排出,進一步經(jīng)過廢氣總排出口(A)排出反應(yīng)器外;液相產(chǎn)物經(jīng)第一獨立催化劑床層生成的液相產(chǎn)物輸送管線(E1)到達第二獨立催化劑床層的底部,并與從第二獨立催化劑床層氫氣補充管線(B2)進來的新氫混合后從底部進入第二獨立催化劑床層;(2)第一獨立催化劑床層的液相產(chǎn)物和新氫在第二獨立催化劑床層進行催化反應(yīng)后,經(jīng)第二獨立催化劑床層上部的氣-液分離空間進行分離,廢氣從第二獨立催化劑床層廢氣排出口(A2)排出,進一步經(jīng)過廢氣總排出口(A)排出反應(yīng)器外;液相產(chǎn)物經(jīng)第二獨立催化劑床層生成的液相產(chǎn)物輸送管線(E2)到達第三獨立催化劑床層的底部,并與從第三獨立催化劑床層氫氣補充管線(B3)進來的新氫混合后從底部進入第三獨立催化劑床層;(3)按照步驟(2)的工藝方法進行多個獨立催化劑床層的液相加氫反應(yīng)工藝,直到最后一個獨立催化劑床層,在最后一個獨立催化劑床層中,氣-液分離后的液相產(chǎn)物經(jīng)產(chǎn)品輸出管線(E)輸出反應(yīng)器外,得到最終產(chǎn)物,該最終產(chǎn)物一部分作為最終產(chǎn)品進入下游產(chǎn)品分離系統(tǒng),另一部分作為新一輪的催化加氫反應(yīng)原料,也就是原料油輸入管線(B1)中的循環(huán)液體加氫產(chǎn)物。本發(fā)明液相加氫反應(yīng)器及液相加氫工藝方法中,所述的每個獨立的催化劑床層的上部均設(shè)有氣-液分離空間,收集反應(yīng)產(chǎn)生的廢氣,然后通過管道排出反應(yīng)器;反應(yīng)生成的液相產(chǎn)物在氣-液分離空間的下部以溢流的方式流出,進入下一個催化劑床層的底部。本發(fā)明液相加氫反應(yīng)器及工藝方法中,所述的每個催化劑床層進料都設(shè)有新氫補充口,以保證原料液體混合物進行氫氣飽和;同時,過量的氫氣可將反應(yīng)生成的硫化氫、氨等雜質(zhì)氣提出來,進入氣-液分離空間,然后通過管道排出反應(yīng)器。本發(fā)明液相加氫反應(yīng)器及工藝方法中,所述的液相混合物料通過催化劑床層的反應(yīng)條件可以根據(jù)原料油的性質(zhì)、產(chǎn)品質(zhì)量要求由本領(lǐng)域技術(shù)人員具體確定,一般為:反應(yīng)溫度為150-450℃,反應(yīng)壓力為1-20MPa,液時空速為0.2-15h-1。本發(fā)明液相加氫反應(yīng)器及工藝方法中,所使用的催化劑可以根據(jù)反應(yīng)的需要,使用適宜的加氫催化劑,實現(xiàn)不同的加氫目的。本發(fā)明的溫度控制、壓力控制系統(tǒng)操作均與常規(guī)加氫工藝方法中使用的控制方法相同。本發(fā)明一種液相加氫反應(yīng)器及液相加氫工藝方法與現(xiàn)有技術(shù)相比具有下列優(yōu)點及有益效果。1、本發(fā)明省去了氫氣循環(huán)系統(tǒng)和循環(huán)氫壓縮機,降低成本,可廣泛應(yīng)用于各種油品加氫處理過程。2、本發(fā)明設(shè)有多個獨立的催化劑床層,每個催化劑床層進料都設(shè)有新氫補充口,以保證液體原料充分溶解氫氣;所使用的氫氣量略多于液體原料的溶解氫量,從而保證液體原料充分溶氫。3、本發(fā)明的每個催化劑床層都設(shè)有反應(yīng)生成廢氣的排放口,以減少或避免反應(yīng)生成的H2S、NH3等有害雜質(zhì)對加氫反應(yīng)的影響。4、本發(fā)明的新鮮原料與循環(huán)液體加氫產(chǎn)物及補入的新氫,依次通過第一獨立催化劑床層、第二、三等多個獨立催化劑床層,保證較高的雜質(zhì)脫除率,確保出口產(chǎn)品質(zhì)量。5、在每個獨立的催化劑床層中,可針對原料油中所含雜質(zhì)的種類(如:硫化物、氮化物、芳烴化合物、重金屬、瀝青質(zhì)等)和含量的不同,分別填裝不同類型的催化劑,更加有效的脫除雜質(zhì),提高催化劑利用效率和催化劑使用壽命。6、本發(fā)明不需要設(shè)置復(fù)雜的內(nèi)部構(gòu)件,操作簡單、易控制,靈活、適用性強。7,在本發(fā)明中,催化劑床層之間是靠溢流控制液位,節(jié)省了液位控制所需的儀表和設(shè)備,簡化了設(shè)備,降低了設(shè)備投資和成本。8,與其他多段液相加氫每段都需要設(shè)置壓力控制系統(tǒng)的反應(yīng)器相比,本發(fā)明將廢氣從一個出口排出裝置,可以只設(shè)一個壓力控制系統(tǒng),節(jié)省投資和操作費用。上述說明僅是本發(fā)明技術(shù)方案的概述,為了能夠更清楚了解本發(fā)明的技術(shù)手段,而可依照說明書的內(nèi)容予以實施,并且為了讓本發(fā)明的上述和其他目的、特征和優(yōu)點能夠更明顯易懂,以下特舉較佳實施例,并配合附圖,詳細(xì)說明如下。附圖說明圖1為本發(fā)明液相加氫反應(yīng)器的二段獨立催化劑床層結(jié)構(gòu)示意圖。圖2為本發(fā)明液相加氫反應(yīng)器的三段獨立催化劑床層結(jié)構(gòu)示意圖。圖3為本發(fā)明液相加氫反應(yīng)器的四段獨立催化劑床層結(jié)構(gòu)示意圖。【主要元件符號說明】A:廢氣總排出口A1:第一獨立催化劑床層產(chǎn)生的廢氣排出口。A2:第二獨立催化劑床層產(chǎn)生的廢氣排出口。A3:第三獨立催化劑床層產(chǎn)生的廢氣排出口。A4:第四獨立催化劑床層產(chǎn)生的廢氣排出口。B1:原料油輸入管線。B2:第二獨立催化劑床層氫氣補充管線。B3:第三獨立催化劑床層氫氣補充管線。B4:第四獨立催化劑床層氫氣補充管線。C1:第一獨立催化劑床層。C2:第二獨立催化劑床層。C3:第三獨立催化劑床層。C4:第四獨立催化劑床層。D:反應(yīng)器筒體。E1:第一獨立催化劑床層生成的液相產(chǎn)物輸送管線。E2:第二獨立催化劑床層生成的液相產(chǎn)物輸送管線。E3:第三獨立催化劑床層生成的液相產(chǎn)物輸送管線。E:產(chǎn)品輸出管線。具體實施方式為更進一步說明本發(fā)明的液相加氫反應(yīng)器和液相加氫工藝方法,以下結(jié)合附圖及較佳實施例,對依據(jù)本發(fā)明提出的一種液相加氫反應(yīng)器及液相加氫工藝方法,其具體實施方式、結(jié)構(gòu)、特征及其效果,詳細(xì)說明如下。請參閱圖1。本發(fā)明描述如下:新鮮原料油經(jīng)加壓和循環(huán)油(循環(huán)液體加氫產(chǎn)物)、新氫混合后,從第一獨立催化劑床層C1底部通過原料油輸入管線B1進入第一獨立催化劑床層C1進行加氫反應(yīng);反應(yīng)生成產(chǎn)物進入第一獨立催化劑床層C1上部的氣-液分離空間進行氣-液分離;氣-液分離產(chǎn)生的廢氣從頂部的第一催化劑床層廢氣排出口A1排到反應(yīng)器中,經(jīng)廢氣總排出口A排出反應(yīng)器筒體D;氣-液分離產(chǎn)生的液相產(chǎn)物以溢流的形式從第一催化劑床層生成的液相產(chǎn)物輸送管E1流出,在進入第二獨立催化劑床層C2之前,通過第二催化劑床層氫氣補充管線B2補充新氫,然后從第二獨立催化劑床層C2的底部進入第二獨立催化劑床層C2,進行加氫催化反應(yīng)。第二獨立催化劑床層C2反應(yīng)產(chǎn)物的分離過程及流程與第一獨立催化劑床層C1相同。以圖3為例,最后的催化劑床層為第四獨立催化劑床層C4,其進料為來自第三獨立催化劑床層C3生成的液相產(chǎn)物和從第四獨立催化劑床層氫氣補充管線B4補進的新氫,進料從第四獨立催化劑床層C4的下部進入,反應(yīng)后經(jīng)氣-液分離,生成的氣體從第四獨立催化劑床層C4的上部排出,最終生成的液相產(chǎn)物,從反應(yīng)器的產(chǎn)品輸出管線E輸出。最終的液相產(chǎn)物(也就是從產(chǎn)品輸出管線E輸出的產(chǎn)物)一部分作為循環(huán)油(也即循環(huán)液體加氫產(chǎn)物)與新鮮原料油、氫氣混合,作為新一輪的催化加氫反應(yīng)原料,另一部分作為最終的加氫產(chǎn)品進入下游產(chǎn)品分離系統(tǒng)。所述的循環(huán)液體加氫產(chǎn)物與新鮮原料的體積比為(0.1-30):1,優(yōu)選(0.5-15):1,最佳為(1-5):1。本發(fā)明中,反應(yīng)器筒體D內(nèi)的每個獨立的催化劑床層的進料為串聯(lián)操作方式。因此,可按照處理的原料油的性質(zhì)和對加氫產(chǎn)品質(zhì)量的要求,設(shè)計獨立催化劑床層的數(shù)量和催化劑類型,以保證加氫反應(yīng)器最終產(chǎn)品的質(zhì)量滿足生產(chǎn)的要求。因此,多個獨立催化劑床層中裝填的催化劑類型可以相同,也可以不同。獨立催化劑床層的數(shù)量也可以根據(jù)具體情況設(shè)定,一般為2-10個,優(yōu)選2-6個,最佳為4個。每個催化劑床層補充的新氫量按照氫油體積比為1:1-100:1的比例補充,優(yōu)選5:1-20:1。催化劑床層的反應(yīng)條件為反應(yīng)溫度為150-450℃,反應(yīng)壓力為1-20MPa,液時體積空速為0.2-15h-1。下面結(jié)合實施例進一步闡述本發(fā)明的技術(shù)方案。實施例1-4本發(fā)明提出的一種液相加氫反應(yīng)器及液相加氫工藝方法,所用原料油性質(zhì)見表1,催化劑選用現(xiàn)有工業(yè)用的FH-UDS加氫催化劑,加氫工藝條件見表2,生成油品性質(zhì)見表3(裝置運轉(zhuǎn)300小時采樣分析取得的數(shù)據(jù))。表1原料油性質(zhì)項目原料油1原料油2密度(20℃)/(g/cm3)0.87230.8654餾程/℃132-365168-370硫含量/(μg/g)820111758氮含量/(μg/g)6521002實際膠質(zhì)/(mg/100ml)274780稠環(huán)芳烴/m%17.214.4總芳烴/m%32.828.8十六烷值42.547.4表2加氫工藝條件表3液相加氫生成油品性質(zhì)由表3數(shù)據(jù)可以看出,對兩種原料油進行加氫精制后,產(chǎn)品的硫含量都小于10μg/g。可以滿足未來成品油標(biāo)準(zhǔn)對柴油硫含量的要求。以上所述,僅是本發(fā)明的較佳實施例而已,并非對本發(fā)明作任何形式上的限制,雖然本發(fā)明已以較佳實施例揭露如上,然而并非用以限定本發(fā)明,任何熟悉本專業(yè)的技術(shù)人員,在不脫離本發(fā)明技術(shù)方案范圍內(nèi),當(dāng)可利用上述揭示的技術(shù)內(nèi)容作出些許更動或修飾為等同變化的等效實施例,但凡是未脫離本發(fā)明技術(shù)方案的內(nèi)容,依據(jù)本發(fā)明的技術(shù)實質(zhì)對以上實施例所作的任何簡單修改、等同變化與修飾,均仍屬于本發(fā)明技術(shù)方案的范圍內(nèi)。當(dāng)前第1頁1 2 3