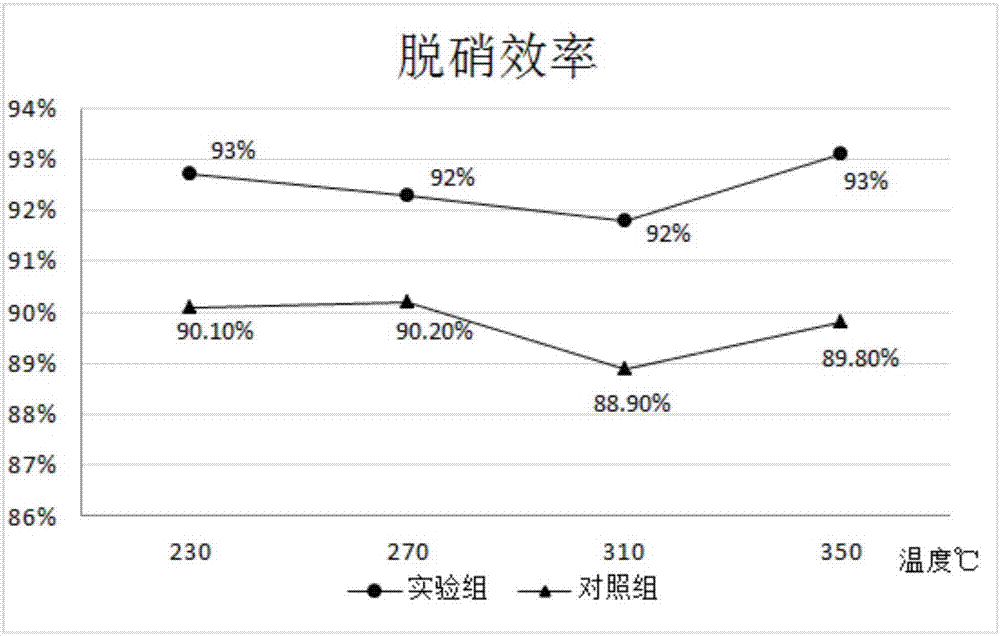
本發(fā)明涉及一種燃氣機組用低溫多孔scr脫硝催化劑的制備方法,屬于煙氣脫硝
技術領域:
。
背景技術:
:近年來,天然氣的需求量正以每年8%的速度增長。在未來的一段時間內(nèi),天然氣將作為我國調整能源結構最為重要的能源形式,因燃氣機組煙氣中的粉塵含量遠低于燃煤機組,對于scr蜂窩式催化劑壁厚有著更嚴格的要求,現(xiàn)階段燃煤電廠用scr蜂窩式脫硝催化劑單元內(nèi)壁厚度為0.8mm左右,而燃氣機組所用催化劑內(nèi)壁厚度為小于0.4mm。這就意味著燃氣機組用低溫多孔scr脫硝催化劑要有更大的孔徑和更高的機械強度,為了提高催化劑的孔徑和機械強度,就需要增加更多的造孔劑及機械加強劑,從而導致在催化劑制備的混煉階段,物料的粘稠度增加,出現(xiàn)過濾困難。另外,由于造孔劑和機械加強劑及其他物料的添加比例與燃煤機組用scr脫硝催化劑有所不同,在干燥階段和煅燒的降溫階段,所需的環(huán)境條件也不一樣,如果控制不當,會使催化劑開裂,從而使整批催化劑報廢或極大影響催化效果。技術實現(xiàn)要素:針對現(xiàn)有技術存在的上述缺陷,本發(fā)明提出了一種新的燃氣機組用低溫多孔scr脫硝催化劑的制備方法,改變混合方式以增加過濾的持續(xù)出料時間,避免催化劑開裂,提高催化劑成型率。本發(fā)明是采用以下的技術方案實現(xiàn)的:一種燃氣機組用低溫多孔scr脫硝催化劑的制備方法,包括以下步驟:(1)混煉:包括如下小步:a)干混:將100-150份鈦白粉、8-20份羧甲基纖維素和5-10份聚氧化乙烯加入混煉機混合,添加7-18份木漿和25-50份玻璃纖維,混合;b)濕混:添加50-80份去離子水、5-15份偏釩酸銨溶液、10-20份偏鎢酸銨溶液、30-55份氨水、10-20份乳酸、1-5份硝酸鈰溶液和0.1-1.5份硝酸鐠溶液,攪拌;c)抽濕:抽濕設備抽出混煉機內(nèi)水汽;(2)成型:包括如下小步:d)將物料用過濾板過濾,留下粒徑小于過濾板網(wǎng)孔的物料,將過濾完成的物料制作成需要的形狀;e)將上述形狀的物料放入擠出機,擠出成型;(3)干燥:包括如下小步:f)一次干燥:耗時8-11天,在此期間,干燥條件滿足:環(huán)境溫度從30℃上升到70℃,送風頻率從15hz上升到50hz,空氣濕度從80%下降到10%;g)二次干燥;耗時14小時,在此期間,干燥條件滿足:環(huán)境溫度從35℃上升到60℃。(4)煅燒:包括如下小步:h)升溫階段:耗時14-18小時,在此期間,升溫條件滿足:環(huán)境溫度從室溫上升到650℃;i)降溫階段:耗時7-9小時,在此期間,降溫條件滿足:環(huán)境溫度從650℃下降到室溫。進一步地,所述小步a)中,7-18份木漿和25-50份玻璃纖維的添加和混合的方式為:先添加7-18份木漿,攪拌,后添加25-50份玻璃纖維,攪拌。進一步地,所述小步a)中,添加木漿后攪拌時間不少于5分鐘,攪拌轉速為150-240轉/分鐘;添加玻璃纖維后攪拌時間不少于5分鐘,攪拌轉速為150-240轉/分鐘;所述小步b)中,濕混步驟的攪拌時間不少于20分鐘,攪拌轉速為150-240轉/分鐘;小步c)中抽濕時間不少于30分鐘。進一步地,所述小步c)中,最終得到的物料含水率為25%-30%。在混煉階段,本發(fā)明將傳統(tǒng)的混煉步驟優(yōu)化為:干混、濕混和抽濕,可以提高混合效率,在較短的時間內(nèi)實現(xiàn)原料的迅速混合,提高過濾時的持續(xù)出料時間。在混合的過程中,先加入鈦白粉、羧甲基纖維素、聚氧化乙烯等粉末狀的物質,將其充分混合之后,再加入木漿,通過攪拌將木漿與其他原料混勻之后,再加入玻璃纖維,通過攪拌將玻璃纖維與其他原料混勻。經(jīng)試驗證明,這種混合方式可以顯著提高過濾時的持續(xù)出料時間。進一步地,所述小步d)中,使用的過濾板為scr多孔催化劑濕胚擠出過濾板:包括等距排列的金屬條,還包括加強筋,加強筋與金屬條垂直,加強筋與金屬條固定在一起形成過濾板體。進一步地,所述小步d)中,過濾板相鄰金屬條的間距為0.4-0.6mm?,F(xiàn)階段scr催化劑生產(chǎn)廠家使用普通的鋼絲網(wǎng)進行物料過濾,該過濾網(wǎng)較易獲得,成本較低,但是損耗較大,在過濾過程中易出現(xiàn)破網(wǎng)的情況,難以立即發(fā)現(xiàn)。過濾網(wǎng)出現(xiàn)問題之后,物料中的大顆粒會混入物料當中,一旦有粒徑超過0.6mm的雜質顆粒進入催化劑物料中,會造成堵模具現(xiàn)象,無法滿足多孔催化劑的生產(chǎn)技術要求。該scr多孔催化劑濕胚擠出過濾板使用加強筋固定金屬條,強度高,使用壽命長,使用過程中不易變形,不易破損,一旦破損易于發(fā)現(xiàn)??梢员苊獬^0.6mm的雜質顆粒混入到過濾后的物料當中,從而避免擠出成型時堵模具的現(xiàn)象。進一步地,所述小步f)中,包括以下階段:第一階段:耗時3-4天,在此期間,干燥條件滿足:環(huán)境溫度從30℃上升到40℃,送風頻率從15hz上升到30hz,空氣濕度從80%下降到70%;第二階段:耗時3-4天,在此期間,干燥條件滿足:環(huán)境溫度從40℃上升到60℃,送風頻率從30hz上升到40hz,空氣濕度從70%下降到40%;第三階段:耗時2-3天,在此期間,干燥條件滿足:環(huán)境溫度從60℃上升到70℃,送風頻率從40hz上升到60hz,空氣濕度從40%下降到10%。各個階段的干燥時間、環(huán)境溫度、送風頻率和空氣濕度會影響到成料的效果,如果各參數(shù)配合不當,成料的質量會嚴重降低,甚至產(chǎn)生裂紋,導致一批物料報廢。進一步地,所述小步g)中,最終得到的物料含水率為5%—10%。。進一步地,所述小步h)中,包括以下階段:第一升溫階段:耗時7-9小時,在此期間,升溫條件滿足:環(huán)境溫度從室溫上升到400℃;第二升溫階段:耗時7-9小時,在此期間,升溫條件滿足:環(huán)境溫度從400℃上升到650℃。第一升溫階段是化學反應階段,這一階段,乳酸、木漿、聚氧化乙烯、羧甲基纖維素等有機物被燒掉,偏釩酸銨轉化為v2o5,偏鎢酸銨轉化為wo3。第二升溫階段催化劑會發(fā)生燒結作用,提高催化劑的機械強度。在降溫階段,關鍵要控制降溫的速度,防止溫度變化過于劇烈而導致催化劑開裂。進一步地,在實驗檢測條件下,制得的多孔scr脫硝催化劑在溫度230-350℃之間的脫硝效率達到91%以上。本發(fā)明的有益效果是:1.混煉步驟包括干混、濕混、和抽濕三步,干混時先加木漿后加玻璃纖維,先干混后濕混,以實現(xiàn)各成分的快速均勻混合,降低混煉時間,提高混煉后的持續(xù)出料時間。2.成型時,使用scr多孔催化劑濕胚擠出過濾板進行過濾,該濾板的強度更高,不易破損,可以避免過濾時堵模具,過濾效果更好。3.干燥時,通過干燥時間、送風頻率、空氣濕度等參數(shù)的配合,可縮短干燥時間,避免催化劑開裂。4.煅燒時,通過升溫階段的溫度控制實現(xiàn)部分原料的化學轉化,并可利用燒結作用提高催化劑的強度;降溫時控制降溫時間和溫度變化趨勢,避免催化劑開裂。5.添加鈰、鐠元素,使多孔scr脫硝催化劑在溫度為230-350℃之間具有較高的脫硝效率。6.添加木漿,使催化劑的孔容、孔徑顯著提升,可提高催化劑的脫硝效率。7.由于燃氣機組排出廢氣溫度通常在350-420℃,本專利所研究的低溫多孔scr脫硝催化劑最低反應溫度只需230℃,余熱可以被重新利用,降低運營成本。附圖說明圖1.低溫催化劑氨逃逸率隨溫度變化趨勢圖。圖2.低溫催化劑脫硝效率隨溫度變化對比圖。具體實施方式為了使本發(fā)明目的、技術方案更加清楚明白,下面結合附圖對本發(fā)明作進一步詳細說明。實施例一:將100kg鈦白粉、8kg羧甲基纖維素和5kg聚氧化乙烯加入混煉機充分混合,添加7kg木漿,攪拌5分鐘,攪拌轉速200轉/分鐘;添加25kg玻璃纖維,攪拌5分鐘,攪拌轉速200轉/分鐘。添加50kg去離子水、5kg偏釩酸銨溶液、10kg偏鎢酸銨溶液、30kg氨水、10kg乳酸、1kg硝酸鈰溶液和0.1kg硝酸鐠溶液,攪拌25分鐘。抽濕設備抽濕35分鐘,最終得到的物料含水率為26.2%。將物料用scr多孔催化劑濕胚擠出過濾板過濾,留下粒徑小于過濾板網(wǎng)孔的物料,將過濾完成的物料制作成長方體;將長方體物料放入擠出機,擠出成型。將成型之后的物料用濕端自動化設備碼放至一次干燥窯車,由叉車將一次干燥窯車轉運至一次干燥間,進入耗時10天的一次干燥,在此期間,環(huán)境溫度從30℃上升到70℃,送風頻率從15hz上升到50hz,空氣濕度從80%下降到10%;一次干燥結束之后,由叉車將一次干燥窯車轉運至濕端自動化設備,該設備會將一次干燥窯車上的物料碼放至二次干燥窯車,碼放完成后由叉車將二次干燥窯車轉運至二次干燥間,進入耗時14小時的二次干燥,在此期間,環(huán)境溫度從35℃上升到60℃。將干燥后的物料放入催化劑煅燒爐,進入16小時的升溫階段,在此期間,環(huán)境溫度從室溫上升到650℃;進入8小時的降溫階段,在此期間,環(huán)境溫度從650℃下降到室溫。另外,本實施例對比了干燥時間對最后加工效果的影響,在其他條件不變的情況下,如果干燥時間變?yōu)?天,催化劑頂面、左側面和右側面會產(chǎn)生平均長度為20cm,寬0.2-1mm的縱裂紋(料長0.6-1.3m)。如圖1所示,由本實施例獲得的催化劑在230-350℃的溫度范圍內(nèi),具有較低的氨逃逸。針對本實施例,做了5組對照試驗,比較了不同混合方式下的過濾持續(xù)出料時間。對照組的其他參數(shù)與本實施例相同,只調整了物料混合的方式,結果見下表:表1持續(xù)出料時間實驗編號12345平均值實驗組(先加木漿,后加玻璃纖維)83s80s76s81s80s80s對照1組(先加玻璃纖維,后加木漿)23s25s22s22s23s23s對照2組(固體與溶液同時混合)9s12s8s10s12s10.2s可見,固體和液體同時混合時的平均持續(xù)出料時間只有10.2s,先干混后濕混且先加玻璃纖維后加木漿的平均持續(xù)出料時間為23s,但先干混后濕混且先加木漿后加玻璃纖維的平均持續(xù)出料時間為80s??梢?,先干混后濕混的持續(xù)出料時間明顯長于固體與溶液同時混合的出料時間,即使是先干混后濕混,木漿與玻璃纖維的添加順序也對持續(xù)出料時間有極大影響。實施例二:將125kg鈦白粉、16kg羧甲基纖維素和8kg聚氧化乙烯加入混煉機充分混合,添加12kg木漿,攪拌8分鐘,攪拌轉速200轉/分鐘;添加35kg玻璃纖維,攪拌8分鐘,攪拌轉速200轉/分鐘;添加65kg去離子水、10kg偏釩酸銨溶液、15kg偏鎢酸銨溶液、45kg氨水、15kg乳酸、2.5kg硝酸鈰溶液和1kg硝酸鐠溶液,攪拌25分鐘;抽濕設備抽濕38分鐘,最終得到的物料含水率為28.2%。將物料用scr多孔催化劑濕胚擠出過濾板過濾,留下粒徑小于過濾板網(wǎng)孔的物料,將過濾完成的物料制作成長方體;將長方體物料放入擠出機,擠出成型。將成型之后的物料用濕端自動化設備碼放至一次干燥窯車,由叉車將一次干燥窯車轉運至一次干燥間,進入耗時4天的一次干燥第一階段,在此期間,環(huán)境溫度從30℃上升到40℃,送風頻率從15hz上升到30hz,空氣濕度從80%下降到70%;進入耗時3天的一次干燥第二階段,在此期間,環(huán)境溫度從40℃上升到60℃,送風頻率從30hz上升到40hz,空氣濕度從70%下降到40%;進入耗時2天的一次干燥第三階段,在此期間,環(huán)境溫度從60℃上升到70℃,送風頻率從40hz上升到60hz,空氣濕度從40%下降到10%。一次干燥結束之后,由叉車將一次干燥窯車轉運至濕端自動化設備,該設備會將一次干燥窯車上的物料碼放至二次干燥窯車,碼放完成后由叉車將二次干燥窯車轉運至二次干燥間,進入耗時14小時的二次干燥,在此期間,環(huán)境溫度從35℃上升到60℃。將干燥后的物料放入催化劑煅燒爐,進入8小時的第一升溫階段,在此期間,環(huán)境溫度從室溫上升到400℃;接著,進入8小時的第二升溫階段,在此期間,環(huán)境溫度從400℃上升到650℃;之后,進入8小時的降溫階段,在此期間,環(huán)境溫度從650℃下降到室溫。針對本實施例,做了5組對照試驗,實驗組添加木漿,對照組不添加木漿,其他條件不變,得到孔容、孔徑測試結果,見下表:表2孔容、孔徑對比表可見,添加木漿之后,催化劑的孔容、孔徑出現(xiàn)顯著提升,而孔容、孔徑是催化效果的重要參數(shù),可見本發(fā)明添加木漿后,可以起到顯著提高催化效果的作用。取230℃、270℃、310℃和350℃時5組實驗組的脫硝效率平均值和5組對照組的脫硝效率平均值進行對比,結果如圖2所示??梢?,按照本發(fā)明的方法制備的scr脫硝催化劑,脫硝效率在各溫度點都顯著高于對照組。本發(fā)明可廣泛運用于燃氣機組用低溫多孔scr脫硝催化劑的制備場合。當前第1頁12