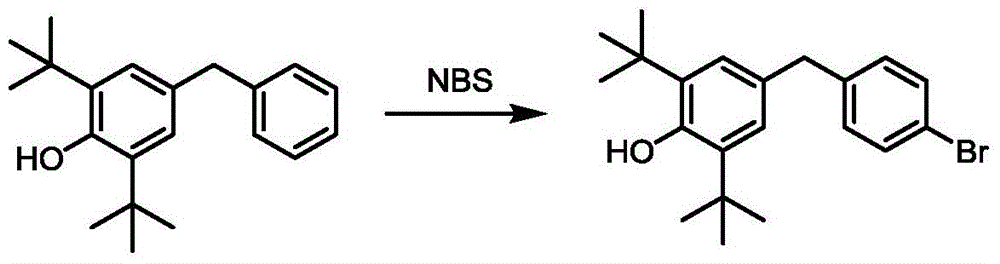
本發(fā)明涉及潤滑油領(lǐng)域,具體地,涉及一種含有特定添加劑的潤滑油組合物及其制備方法。
背景技術(shù):
:目前已知能夠有效起到抗氧化作用的潤滑油添加劑主要包括酚類和胺類化合物。酚類化合物含有一個或多個受阻酚官能團(tuán),胺類化合物則含有一個或多個氮原子,這些特殊的官能團(tuán)能夠捕捉氧化過程生成的自由基化合物,從而阻止氧化過程的繼續(xù)發(fā)生。由于當(dāng)前機(jī)械設(shè)備的工作條件趨于強(qiáng)烈,往往會加速氧化速率,縮短潤滑油的使用壽命,因此對抗氧劑的效率和經(jīng)濟(jì)性提出了更高的要求。美國專利US4824601A報道了二苯基胺和二異丁烯在酸活化的堿土金屬催化劑(earthcatalyst)作用下形成的烷基化胺混合物,它在潤滑油和其它功能流體中抗氧化能力表現(xiàn)優(yōu)異。美國專利US2005230664A1報道了一種以下通式的抗氧劑9,10-二氫化吖啶的合成方法,它是使用烷基化二苯基胺與醛或酮在酸性催化劑作用下縮合制備。專利CN1191340C采用受阻叔丁基酚類、醛、二硫化碳和二烷基胺發(fā)生縮合制備化合物,該化合物具有較強(qiáng)的捕捉自由基和分解過氧化物的能力,能給油品氧化安定性提供更有效的保護(hù),還可起到抗磨作用。專利US4225450報道了一種由受阻叔丁基酚類與烷基二硫代氨基甲酸 鹽反應(yīng)制備的多硫化物酚類抗氧劑,具有較好的抗氧化作用和抗磨作用。技術(shù)實(shí)現(xiàn)要素:本發(fā)明的目的是為了滿足對潤滑油組合物的抗氧化能力的高要求,提供一種潤滑油組合物及其制備方法。本發(fā)明的發(fā)明人在研究中發(fā)現(xiàn),潤滑油組合物含有式(I)所示結(jié)構(gòu)的化合物:能夠使?jié)櫥徒M合物具有優(yōu)良的抗氧化性能。因此,為了實(shí)現(xiàn)上述目的,一方面,本發(fā)明提供了一種潤滑油組合物,以潤滑油組合物的重量為基準(zhǔn),所述潤滑油組合物含有以下組分:90-99.99重量%的潤滑油基礎(chǔ)油、0.01-10重量%的抗氧多效添加劑,所述抗氧多效添加劑為式(I)所示結(jié)構(gòu)的化合物:優(yōu)選地,以潤滑油組合物的重量為基準(zhǔn),所述潤滑油組合物含有以下組分:96-99.9重量%的潤滑油基礎(chǔ)油、0.1-4重量%的抗氧多效添加劑。另一方面,本發(fā)明提供了一種潤滑油組合物的制備方法,所述方法包括:將含有潤滑油基礎(chǔ)油和抗氧多效添加劑的原料混合均勻得到潤滑油組合物,其中,以潤滑油組合物的重量為基準(zhǔn),潤滑油基礎(chǔ)油的用量為90-99.99重量%,抗氧多效添加劑的用量為0.01-10重量%,所述抗氧多效添加劑為式(I) 所示結(jié)構(gòu)的化合物:優(yōu)選地,以潤滑油組合物的重量為基準(zhǔn),潤滑油基礎(chǔ)油的用量為96-99.9重量%,抗氧多效添加劑的用量為0.1-4重量%。本發(fā)明的潤滑油組合物具有優(yōu)異的抗氧化性能,可抑制高溫氧化沉積物的生成。本發(fā)明的其它特征和優(yōu)點(diǎn)將在隨后的具體實(shí)施方式部分予以詳細(xì)說明。附圖說明圖1是制備抗氧多效添加劑的步驟(a)的反應(yīng)方程式。圖2是制備抗氧多效添加劑的步驟(b)的反應(yīng)方程式。圖3是制備抗氧多效添加劑的步驟(c)的反應(yīng)方程式。圖4是制備例制備的抗氧多效添加劑的氫譜譜圖。圖5是制備例制備的抗氧多效添加劑的碳譜譜圖。圖6是制備例制備的抗氧多效添加劑的質(zhì)譜譜圖。具體實(shí)施方式以下對本發(fā)明的具體實(shí)施方式進(jìn)行詳細(xì)說明。應(yīng)當(dāng)理解的是,此處所描述的具體實(shí)施方式僅用于說明和解釋本發(fā)明,并不用于限制本發(fā)明。一方面,本發(fā)明提供了一種潤滑油組合物,以潤滑油組合物的重量為基準(zhǔn),潤滑油組合物含有以下組分:90-99.99重量%的潤滑油基礎(chǔ)油、0.01-10重量%的抗氧多效添加劑,所述抗氧多效添加劑為式(I)所示結(jié)構(gòu)的化合物:本發(fā)明中,以潤滑油組合物的重量為基準(zhǔn),潤滑油基礎(chǔ)油的含量優(yōu)選為95-99.98重量%,更優(yōu)選為96-99.9重量%;抗氧多效添加劑的含量優(yōu)選為0.02-5重量%,更優(yōu)選為0.1-4重量%。本發(fā)明旨在通過潤滑油組合物中含有式(I)所示結(jié)構(gòu)的化合物而實(shí)現(xiàn)發(fā)明目的,即使?jié)櫥徒M合物具有優(yōu)良的抗氧化等性能。因此,對于潤滑油組合物中各常規(guī)組分的選擇,均沒有特定的限制。本發(fā)明中,潤滑油基礎(chǔ)油可以為本領(lǐng)域常規(guī)使用的潤滑油基礎(chǔ)油,例如可以為礦物潤滑油和/或合成潤滑油。礦物潤滑油在粘度上可以從輕餾分礦物油到重餾分礦物油,包括液體石蠟油和加氫精制的、溶劑處理過的鏈烷、環(huán)烷和混合鏈烷-環(huán)烷型礦物潤滑油,通常分為I、II、III類基礎(chǔ)油,常見的商品牌號包括I類150SN、600SN,II類100N、150N、350N等。合成潤滑油可以包括聚合烴油、烷基苯及其衍生物,聚合烴油具體的例子包括但不限于聚丁烯、聚丙烯、丙烯-異丁烯共聚物、氯化的聚丁烯、聚(1-己烯)、聚(1-辛烯)、聚(1-癸烯),常見的商品牌號包括PAO4、PAO6、PAO8、PAO10等,烷基苯及其衍生物具體的例子包括但不限于十二烷基苯、十四烷基苯、二壬基苯、二(2-乙基己基)苯,烷基苯的衍生物包括烷基化的二苯醚和烷基化的二苯硫及其衍生物、類似物和同系物等。合成潤滑油的另一適合類型可以為酯類油,包括二羧酸(如苯二甲酸、琥珀酸、烷基琥珀酸和烯基琥珀酸、馬來酸、壬二酸、辛二酸、癸二酸、反丁烯二酸、己二酸、亞油酸二聚物、丙二酸,烷基丙二酸、烯基丙二酸)與 各種醇(如丁醇、己醇、十二烷基醇、2-乙基己基醇、乙二醇、丙二醇)發(fā)生縮合反應(yīng)生成的酯或復(fù)合酯。這些酯的具體例子包括但不限于己二酸二丁酯、癸二酸二(2-乙基己基)酯、反丁烯二酸酸二正己酯、癸二酸二辛酯、壬二酸二異辛酯、壬二酸二異癸酯、鄰苯二甲酸二辛酯、鄰苯二甲酸二癸酯、癸二酸二(廿烷基)酯、亞油酸二聚物的2-乙基己基二酯等。合成潤滑油的另一適合類型可以為費(fèi)托法合成烴油以及對這種合成烴油通過加氫異構(gòu)、加氫裂化、脫蠟等工藝處理得到的潤滑油基礎(chǔ)油。本發(fā)明中,潤滑油基礎(chǔ)油優(yōu)選粘度指數(shù)大于80、飽和烴含量大于90重量%、硫含量小于0.03重量%的潤滑油基礎(chǔ)油。本發(fā)明的潤滑油組合物還可以含有防銹劑和/或抗泡劑。防銹劑可以選自咪唑類和/或烯基丁二酸酯類,優(yōu)選為4,5-二氫咪唑、烯基咪唑啉丁二酸鹽和烯基丁二酸酯中的至少一種,例如可以選用錦州康泰潤滑油添加劑有限公司生產(chǎn)的T746、T703、T747??古輨┛梢赃x用聚硅氧烷型抗泡劑,例如可以為硅油和/或聚二甲基硅氧烷。對于防銹劑、抗泡劑的含量無特殊要求,可以為本領(lǐng)域常規(guī)的含量,此為本領(lǐng)域技術(shù)人員所公知,在此不再贅述。本發(fā)明中,式(I)所示結(jié)構(gòu)的化合物的制備方法優(yōu)選包括:(a)將2,6-二叔丁基苯酚、甲醛和苯進(jìn)行縮合反應(yīng),生成式(II)所示的中間體M,(b)將步驟(a)得到的中間體M與溴化試劑接觸進(jìn)行溴代反應(yīng),生成式(III)所示的溴代產(chǎn)物,(c)使步驟(b)得到的溴代產(chǎn)物與式(IV)所示的化合物接觸進(jìn)行偶聯(lián)反應(yīng),生成式(I)所示的抗氧劑,本發(fā)明步驟(a)中,縮合反應(yīng)的條件優(yōu)選包括:在惰性氣氛下,在第一溶劑中,在第一催化劑的存在下,將2,6-二叔丁基苯酚、甲醛和苯在-20-0℃下反應(yīng)0.5-1.5h后升至15-30℃,然后加熱至70-80℃反應(yīng)1-3h。本發(fā)明中,惰性氣氛可以為本領(lǐng)域常規(guī)的惰性氣氛,例如可以由氮?dú)?、氬氣等氣體提供。本領(lǐng)域技術(shù)人員應(yīng)該理解的是,為了使反應(yīng)穩(wěn)定進(jìn)行,在-20-0℃下反應(yīng)0.5-1.5h后升至15-30℃,應(yīng)該緩慢升溫至15-30℃,例如,可以將在-20-0℃下反應(yīng)0.5-1.5h后的體系置于15-30℃的環(huán)境溫度下,使反應(yīng)體系自身緩慢升溫至15-30℃。本發(fā)明中,第一溶劑優(yōu)選選自甲醇、乙醇、N,N-二甲基甲酰胺和乙腈中的至少一種,更優(yōu)選為甲醇和/或乙腈,更進(jìn)一步優(yōu)選為甲醇。本發(fā)明中,第一催化劑可以為無機(jī)酸或有機(jī)酸,優(yōu)選選自醋酸、對甲基苯甲酸和苯磺酸中的至少一種,更優(yōu)選為醋酸。本發(fā)明中,2,6-二叔丁基苯酚、甲醛和苯的用量基本上為等摩爾量,但甲醛和苯可以適當(dāng)過量。2,6-二叔丁基苯酚、甲醛和苯的摩爾比優(yōu)選為0.9-1.5:0.9-10:0.9-10。本發(fā)明步驟(a)中,第一催化劑的用量可以為催化量,以2,6-二叔丁基苯酚的摩爾數(shù)為基準(zhǔn),第一催化劑的用量優(yōu)選為5-100摩爾%,更優(yōu)選為10-30摩爾%。本領(lǐng)域技術(shù)人員應(yīng)該理解的是,本發(fā)明步驟(a)中,為了得到較純凈的中間體M,還需要對反應(yīng)后的體系進(jìn)行后處理,后處理的方式可以包括減壓除去溶劑,然后經(jīng)溶劑稀釋、洗滌、干燥、減壓再除去溶劑,例如,將反應(yīng)后的體系在0.01-0.05MPa、40-60℃下除去溶劑,然后倒入1-10倍體積的乙酸乙酯(或二氯甲烷)中,分別用蒸餾水和飽和食鹽水洗滌,然后在15-30℃下加入無水氯化鈣或者無水硫酸鈉等干燥劑,保持10-60min。過濾除去干燥劑后,在0.01-0.05MPa、40-60℃下除去溶劑,以得到中間體M。本發(fā)明步驟(a)中,2,6-二叔丁基苯酚、甲醛和苯進(jìn)行縮合反應(yīng)的反應(yīng)方程式如圖1所示,圖1中,第一溶劑采用的是甲醇,第一催化劑采用的是醋酸,僅為舉例說明的目的,不對本發(fā)明的范圍構(gòu)成限制。本發(fā)明步驟(b)中,溴代反應(yīng)的條件優(yōu)選包括:在惰性氣氛下,在第二溶劑中,在第二催化劑的存在下,在避光條件下,將步驟(a)得到的中間體M與溴化試劑在15-30℃下反應(yīng)1-2h,然后用淬滅劑淬滅?!岸栊詺夥铡比缜八?,在此不再贅述。本領(lǐng)域技術(shù)人員應(yīng)該理解的是,為了反應(yīng)更穩(wěn)定地進(jìn)行,優(yōu)選向中間體M中緩慢加入溴代試劑。本發(fā)明中,第二溶劑優(yōu)選選自四氫呋喃、二氯甲烷、氯仿和乙醚中的至少一種,更優(yōu)選為四氫呋喃。本發(fā)明中,第二催化劑優(yōu)選選自硝酸銨、過氧化苯甲酰(BPO)和偶氮二異丁腈(AIBN)中的至少一種。本發(fā)明中,溴化試劑優(yōu)選為N-溴代琥珀酰亞胺(NBS)和/或Br2,更優(yōu)選為NBS。本發(fā)明步驟(b)中,用淬滅劑進(jìn)行淬滅,淬滅劑可以為本領(lǐng)域常用的淬滅劑,例如可以為飽和食鹽水。本發(fā)明步驟(b)中,中間體M與溴化試劑的用量基本上為等摩爾量,但溴化試劑一般可以適當(dāng)過量,達(dá)到反應(yīng)底物的1.1-3倍當(dāng)量。中間體M與溴化試劑摩爾比優(yōu)選為0.9-1.2:0.9-3.0。本發(fā)明步驟(b)中,第二催化劑的用量可以為催化量,以中間體M的摩爾數(shù)為基準(zhǔn),第二催化劑的用量優(yōu)選為10-100摩爾%,更優(yōu)選為40-60摩爾%。本發(fā)明方法步驟(b)中,中間體M與溴化試劑接觸進(jìn)行溴代反應(yīng)的反應(yīng)方程式如圖2所示,圖2中,溴化試劑采用的是NBS,僅為舉例說明的目的,不對本發(fā)明的范圍構(gòu)成限制。本發(fā)明步驟(b)中,除了生成式(III)所示的溴代產(chǎn)物外,還有微量鄰位的溴代產(chǎn)物生成,沒有間位的溴代產(chǎn)物生成,但鄰位的溴代產(chǎn)物的量很微少,對后續(xù)反應(yīng)沒有實(shí)質(zhì)影響,可以忽略不計。本領(lǐng)域技術(shù)人員應(yīng)該理解的是,本發(fā)明步驟(b)中,為了得到較純凈的溴代產(chǎn)物,還需要對淬滅后的體系進(jìn)行后處理,后處理的方式可以包括水洗、干燥、減壓除去溶劑,例如,將淬滅后的體系用蒸餾水洗滌,然后在15-30℃下加入無水氯化鈣或者無水硫酸鈉等干燥劑,保持10-60min。過濾除去干燥劑后,在0.01-0.05MPa、40-60℃下除去溶劑,以得到溴代產(chǎn)物。本發(fā)明步驟(c)中,偶聯(lián)反應(yīng)的條件優(yōu)選包括:在惰性氣氛下,在第三溶劑中,在第三催化劑的存在下,將步驟(b)得到的溴代產(chǎn)物與式(IV)所示的化合物在80-100℃下反應(yīng)4-8h?!岸栊詺夥铡比缜八?,在此不再贅述。本發(fā)明中,為了使反應(yīng)穩(wěn)定進(jìn)行,優(yōu)選逐漸升溫至80-100℃,然后在80-100℃下反應(yīng)4-8h。本發(fā)明中,第三溶劑優(yōu)選選自二氯甲烷、氯仿、甲苯和四氫呋喃中的至少一種,更優(yōu)選為二氯甲烷。本發(fā)明中,第三催化劑優(yōu)選包括鈀鹽、配體和堿。鈀鹽優(yōu)選選自醋酸鈀和/或鈀-二亞芐基丙酮絡(luò)合物[Pd2(dba)3];配體優(yōu)選選自三叔丁基磷、聯(lián)萘酚(BINAP)和雙(二苯基膦基)二茂鐵(dppf)中的至少一種;堿優(yōu)選選自叔丁醇鈉、叔丁醇鉀、碳酸銫和碳酸鈉中的至少一種。本發(fā)明步驟(c)中,步驟(b)得到的溴代產(chǎn)物與式(IV)所示的化合物的用量基本上為等摩爾量,但式(IV)所示的化合物可以適當(dāng)過量。步驟(b)得到的溴代產(chǎn)物與式(IV)所示的化合物的摩爾比優(yōu)選為0.9-1.5:0.9-2.5。本發(fā)明步驟(c)中,催化劑的用量可以為催化量,以溴代產(chǎn)物的摩爾數(shù)為基準(zhǔn),鈀鹽的用量優(yōu)選為5-50摩爾%,更優(yōu)選為5-20摩爾%,更進(jìn)一步優(yōu)選為5-10摩爾%;配體的用量優(yōu)選為5-50摩爾%,更優(yōu)選為10-30摩爾%;堿的用量優(yōu)選為5-50摩爾%,更優(yōu)選為10-30摩爾%。本發(fā)明步驟(c)中,步驟(b)得到的溴代產(chǎn)物與式(IV)所示的化合物接觸進(jìn)行偶聯(lián)反應(yīng)的反應(yīng)方程式如圖3所示,圖3中,鈀鹽采用的是醋酸鈀,僅為舉例說明的目的,不對本發(fā)明的范圍構(gòu)成限制。本領(lǐng)域技術(shù)人員應(yīng)該理解的是,為了得到較純凈的最終產(chǎn)物,即式(I)所示的抗氧劑,本發(fā)明方法優(yōu)選還包括對反應(yīng)后的體系進(jìn)行后處理,后處理的方式可以包括過濾、溶劑稀釋、水洗、干燥、減壓除去溶劑,例如,將反應(yīng)后的體系過濾后的濾液倒入1-10倍體積的乙酸乙酯(或二氯甲烷)中,然后用蒸餾水洗滌,然后在15-30℃下加入無水氯化鈣或者無水硫酸鈉等干燥劑,保持10-60min。過濾除去干燥劑后,在0.01-0.05MPa、40-60℃下除去溶劑,以得到式(I)所示的抗氧劑。本發(fā)明中制備式(I)所示結(jié)構(gòu)的化合物的方法的各步驟優(yōu)選在攪拌下進(jìn)行,對于攪拌速度無特殊要求,可以為本領(lǐng)域常規(guī)的攪拌速度,例如,攪 拌速度可以為100-800rpm。本發(fā)明制備式(I)所示結(jié)構(gòu)的化合物的方法中,對于第一溶劑、第二溶劑和第三溶劑的量無特殊要求,可以為本領(lǐng)域常規(guī)的溶劑用量,此為本領(lǐng)域技術(shù)人員所公知,在此不再贅述。如上所述,本發(fā)明旨在通過潤滑油組合物中含有式(I)所示結(jié)構(gòu)的化合物而實(shí)現(xiàn)發(fā)明目的,即使?jié)櫥徒M合物具有優(yōu)良的抗氧化等性能。因此,對于潤滑油組合物的制備方法無特殊要求,可以采用本領(lǐng)域常規(guī)使用的方法,例如,第二方面,本發(fā)明還提供了一種潤滑油組合物的制備方法,該方法包括:將含有潤滑油基礎(chǔ)油和抗氧多效添加劑的原料混合均勻得到潤滑油組合物,其中,以潤滑油組合物的重量為基準(zhǔn),潤滑油基礎(chǔ)油的用量為90-99.99重量%,抗氧多效添加劑的用量為0.01-10重量%,所述抗氧多效添加劑為式(I)所示結(jié)構(gòu)的化合物:本發(fā)明方法中,優(yōu)選地,以潤滑油組合物的重量為基準(zhǔn),潤滑油基礎(chǔ)油的用量為95-99.98重量%,更優(yōu)選為96-99.9重量%;抗氧多效添加劑的用量為0.02-5重量%,更優(yōu)選為0.1-4重量%。如前所述,本發(fā)明方法中,原料還可以含有防銹劑和/或抗泡劑。本發(fā)明方法中,對于混合的方式無特殊要求,例如可以將除潤滑油基礎(chǔ)油的各原料組分分別加入到潤滑油基礎(chǔ)油中,也可以將除潤滑油基礎(chǔ)油的各組分混合制成濃縮物再加入到潤滑油基礎(chǔ)油中。本發(fā)明方法中,混合的條件優(yōu)選包括:溫度為40-90℃,時間為1-6h。潤滑油基礎(chǔ)油、抗氧多效添加劑、防銹劑、抗泡劑如前所述,在此不再 贅述。實(shí)施例以下的實(shí)施例將對本發(fā)明作進(jìn)一步的說明,但并不因此限制本發(fā)明。在以下實(shí)施例和對比例中:產(chǎn)物的理化分析方法:通過電感耦合等離子體離子發(fā)射光譜法測定元素含量。結(jié)構(gòu)表征方法:核磁共振法(1H氫譜,13C碳譜),高分辨質(zhì)譜。制備例在帶有電磁攪拌子(攪拌速度為200rpm)的500ml燒瓶中充入氮?dú)獗Wo(hù),加入150ml的甲醇和0.01mol的醋酸,在冰水浴中充分冷卻后,然后分別加入0.1mol的2,6-二叔丁基苯酚,0.2mol的甲醛和0.3mol的苯。反應(yīng)1小時后移去冰水浴,升至25℃后加熱至75℃持續(xù)回流2小時后停止反應(yīng),將反應(yīng)后的體系在0.03MPa、50℃下蒸出溶劑,然后加入250ml乙酸乙酯,并轉(zhuǎn)入分液漏斗中,分別用100ml蒸餾水(兩次)和50ml飽和食鹽水洗滌,并加入10g無水氯化鈣在25℃下干燥20min,過濾后的濾液在40℃、0.03MPa下蒸除溶劑,得到中間體產(chǎn)物M1。在帶有電磁攪拌子(攪拌速度為200rpm)的500ml燒瓶中充入氮?dú)獗Wo(hù),加入150ml的干燥四氫呋喃,然后溶入中間體產(chǎn)物M1,并加入0.05mol的硝酸銨,在避光條件下慢慢加入0.1mol溴代試劑NBS。在25℃下攪拌反應(yīng)1.5h,然后用飽和食鹽水淬滅,然后用100ml蒸餾水(兩次)洗滌,并加入10g無水硫酸鈉在25℃下干燥20min。過濾后的濾液在40℃、0.03MPa下蒸除溶劑,得到溴代產(chǎn)物。在帶有電磁攪拌子(攪拌速度為200rpm)的500ml燒瓶中充入氮?dú)獗? 護(hù),加入150ml的二氯甲烷作為溶劑,分別加入上述溴代產(chǎn)物和0.12mol的苯三唑化合物,隨后加入0.02mol的三叔丁基磷,0.02mol的叔丁醇鈉和0.005mol的Pd(OAc)2。逐漸升溫至90℃,持續(xù)攪拌6h。然后將反應(yīng)后的體系過濾后的濾液加入250ml乙酸乙酯,并轉(zhuǎn)入分液漏斗中,用100ml蒸餾水(兩次)洗滌,并加入10g無水硫酸鈉在25℃下干燥20min。過濾后的濾液在40℃、0.03MPa下蒸除溶劑,得到最終產(chǎn)物S1。S1的理化分析數(shù)據(jù)如下:氮含量,11.2%。將S1進(jìn)行結(jié)構(gòu)表征,分別得到氫譜、碳譜和高分辨率質(zhì)譜譜圖,分別見圖4、圖5和圖6。從上述制備例的理化分析數(shù)據(jù)、圖4、圖5和圖6可以看出,S1具有式(I)所示的結(jié)構(gòu)。實(shí)施例1本實(shí)施例用于說明本發(fā)明的潤滑油組合物及其制備方法。將0.1重量份的S1加入到99.9重量份的600SN潤滑油基礎(chǔ)油(粘度指數(shù)為87,飽和烴含量為92重量%,硫含量為0.02重量%)中,在60℃下攪拌3h,混合均勻得到潤滑油組合物A1。實(shí)施例2本實(shí)施例用于說明本發(fā)明的潤滑油組合物及其制備方法。將2.5重量份的S1加入到42重量份的PAO10和55.5重量份的PAO4的混合潤滑油基礎(chǔ)油中,在40℃下攪拌6h,混合均勻得到潤滑油組合物A2。實(shí)施例3本實(shí)施例用于說明本發(fā)明的潤滑油組合物及其制備方法。將2.5重量份的S1加入到46重量份的Yubase4和51.5重量份的Yubase6的混合潤滑油基礎(chǔ)油中,在40℃下攪拌6h,混合均勻得到潤滑油組合物A3。實(shí)施例4本實(shí)施例用于說明本發(fā)明的潤滑油組合物及其制備方法。將4重量份的S1加入到96重量份的300SN潤滑油基礎(chǔ)油(粘度指數(shù)為91,飽和烴含量為92重量%,硫含量為0.01重量%)中,在90℃下攪拌1h,混合均勻得到潤滑油組合物A4。對比例1按照實(shí)施例2的方法制備潤滑油組合物,不同的是,將S1替換為等重量份的二丁基二硫代氨基甲酸鋅,得到潤滑油組合物D1。對比例2按照實(shí)施例3的方法制備潤滑油組合物,不同的是,將S1替換為等重量份的二丁基二硫代氨基甲酸鋅,得到潤滑油組合物D2。測試?yán)龑櫥徒M合物A1-A4、D1-D2分別進(jìn)行如下測試:采用TA5000-DSC2910差熱分析儀進(jìn)行起始氧化溫度的測定;采用高壓差熱掃描量法(PDSC)進(jìn)行氧化誘導(dǎo)期的測定;表1A1A2A3A4D1D2起始氧化溫度,℃201231227252218214氧化誘導(dǎo)期,min18.252.745.264.535.834.5本領(lǐng)域技術(shù)人員應(yīng)該理解的是,起始氧化溫度越高,潤滑油的熱穩(wěn)定性越好;氧化誘導(dǎo)期越長,潤滑油的抗氧化性能越好。將A2與D1進(jìn)行比較,將A3與D2進(jìn)行比較,可以看出,本發(fā)明的潤滑油組合物具有更好的熱穩(wěn)定性、抗氧化性。本發(fā)明的潤滑油組合物具有優(yōu)異的抗氧化性能,可抑制高溫氧化沉積物的生成。以上結(jié)合附圖詳細(xì)描述了本發(fā)明的優(yōu)選實(shí)施方式,但是,本發(fā)明并不限于上述實(shí)施方式中的具體細(xì)節(jié),在本發(fā)明的技術(shù)構(gòu)思范圍內(nèi),可以對本發(fā)明的技術(shù)方案進(jìn)行多種簡單變型,這些簡單變型均屬于本發(fā)明的保護(hù)范圍。另外需要說明的是,在上述具體實(shí)施方式中所描述的各個具體技術(shù)特征,在不矛盾的情況下,可以通過任何合適的方式進(jìn)行組合,為了避免不必要的重復(fù),本發(fā)明對各種可能的組合方式不再另行說明。此外,本發(fā)明的各種不同的實(shí)施方式之間也可以進(jìn)行任意組合,只要其不違背本發(fā)明的思想,其同樣應(yīng)當(dāng)視為本發(fā)明所公開的內(nèi)容。當(dāng)前第1頁1 2 3