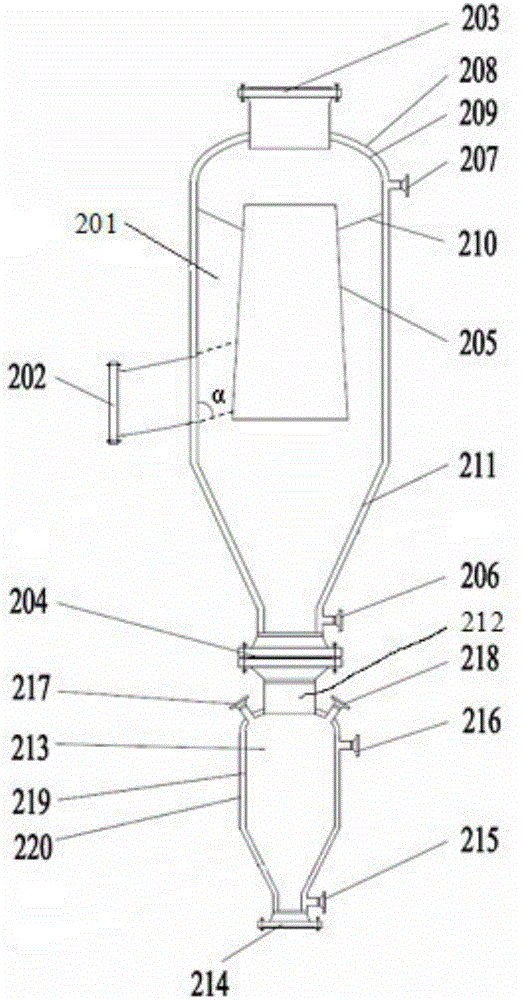
本發(fā)明屬于一種焦炭氣化的工藝及設(shè)備。
背景技術(shù):
:碎煤加壓氣化爐是一種固定床煤氣化爐,由于對(duì)原料煤要求低,即除強(qiáng)粘結(jié)性煤外,其余煤種都可以氣化,特別是低階煤和高灰熔點(diǎn)的劣質(zhì)煤以及氣化焦。該氣化爐被廣泛地應(yīng)用到煤制合成氨、甲醇、二甲醚、合成油和煤氣天然氣領(lǐng)域。但是目前工業(yè)運(yùn)行的碎煤加壓氣化工藝中使用的碎煤加壓氣化技術(shù)適合氣化有干餾、干燥層的煤,在氣化過程中干燥、干餾時(shí)候吸收熱量,氣化爐頂部溫度不至于超過氣化爐材料承受溫度以上,此外焦炭反應(yīng)活性差,像如Shell、GSP、航天爐、水煤漿等氣流床氣化技術(shù)和流化床氣化技術(shù)很難完全反應(yīng)(碳轉(zhuǎn)化率低),不適合焦炭氣化,面對(duì)目前冷清的焦炭產(chǎn)業(yè),開發(fā)焦炭氣化技術(shù)是迫在眉睫的問題。目前碎煤加壓氣化工藝在除塵、脫油工序中采用的為現(xiàn)代煤化工技術(shù)手冊(cè)第二版,第424至428頁(yè)中介紹的5中固定床氣化工藝流程,都采用水洗除塵、脫油工工藝,造成粗煤氣的顯示損失量,不利于熱量回收利用,還使得煤氣水循環(huán)量大、運(yùn)行成本高。專利:煤制清潔燃?xì)獾墓に嚰把b置,專利號(hào):201410767710.7公開的專利使用的旋風(fēng)除塵、脫油,但是旋風(fēng)除塵結(jié)構(gòu)未公開、粗煤氣出口溫度低時(shí)易發(fā)生焦油冷凝、造成排渣口堵塞、很難穩(wěn)定運(yùn)行。專利:雙切向環(huán)流式旋風(fēng)除塵器,專利號(hào):01243740.9公開的旋風(fēng)分離和上述專利中使用的旋風(fēng)除塵、脫油存在一樣的問題。隨著我國(guó)工業(yè)快速發(fā)展,化工裝置逐步向著高溫、高壓、大規(guī)?;陌l(fā)展,特別是煤氣化技術(shù)要求氣化壓力至少在40公斤以上,日投煤量達(dá)到千噸級(jí),再加上氣化的優(yōu)質(zhì)煤碳儲(chǔ)量越來越少,反而劣質(zhì)煤比例逐步增加,特別是灰熔點(diǎn)大于1500度以上的煤種的比例逐步增加,使得氣化煤氣或后續(xù)廢氣的溫度、壓力也相應(yīng)地提高,
專利名稱::一種高溫高壓廢熱鍋爐,申請(qǐng)?zhí)枺?01110462710.2的專利解決高壓、高溫問題,但是我們目前固定床氣化使用的熱回收工藝及設(shè)備:現(xiàn)代煤化工技術(shù)手冊(cè)第二版,第424至428頁(yè)介紹5中典型的固定床氣化工藝流程都是一級(jí)熱回收,產(chǎn)生一種等級(jí)的蒸汽,焦炭氣化煤氣粗口溫度高,使用原流程不僅造成資源浪費(fèi),同時(shí)還污染環(huán)境。
專利名稱::加壓煤氣用廢熱鍋爐,申請(qǐng)?zhí)枺?00510010273.5的專利主要用于解決粉煤氣化,提高了熱回收效率,但是仍然是一級(jí)熱回收,產(chǎn)生單一等級(jí)的蒸汽,未能充分對(duì)廢熱回收利用。技術(shù)實(shí)現(xiàn)要素:本發(fā)明的目的就是為了克服上述技術(shù)中的缺點(diǎn)和不足,提供一種無洗滌煤氣水產(chǎn)生,對(duì)煤氣廢熱能可分級(jí)回收利用,同時(shí)產(chǎn)生的不同等級(jí)蒸汽的焦炭氣化工藝及設(shè)備。本發(fā)明的工藝,包括如下步驟:(1)以焦炭為原料,經(jīng)過碎煤加壓氣化生成壓力為1.0-8.0MPa、溫度為500-650℃的含油塵粗煤氣;(2)將含油塵粗煤氣進(jìn)入除塵旋風(fēng)分離裝置中的旋風(fēng)分離器進(jìn)行分離,煤氣中油塵受離心力和離開內(nèi)筒體時(shí)突然降速雙重作用的影響,使油塵及部分氣體從內(nèi)筒體和外筒體的間隙返回錐筒體進(jìn)行自旋分離,分離后的氣體與進(jìn)入旋風(fēng)分離器的含油塵粗煤氣混合并再次分離,得到每立方米粗煤氣中油塵的含量在1-80mg的粗煤氣和含油塵;(3)將步驟(2)得到的粗煤氣進(jìn)入一體式廢熱回收器,先后通過過熱器、熱回收器Ⅱ、熱回收器Ⅰ分級(jí)回收熱量后由回收廢熱后煤氣出口排出到冷卻器,回收熱量生成低壓飽和、中壓飽和,過熱的三個(gè)等級(jí)的蒸汽,產(chǎn)生的冷凝液送到攪拌、洗滌裝置;(4)冷卻器進(jìn)行冷卻,得到產(chǎn)品煤氣和輕油,輕油送到攪拌、洗滌裝置;(5)將含油塵送入攪拌、洗滌裝置進(jìn)行洗滌、攪拌形成焦油、水、渣的混合物,經(jīng)過超級(jí)離心機(jī)分離,得到含塵焦油輕組分以及水和渣重組份,水和渣重組份靜置分層處理,得到水和渣;含塵焦油輕組分通過孔徑在1-120um范圍的金屬燒結(jié)網(wǎng)過濾器進(jìn)行再次分離,使焦油中塵的含量降到0.85mg以下,過濾得到的焦油作為產(chǎn)品,塵富集在燒結(jié)金屬網(wǎng)過濾器底部間隙排出。如上所述以焦炭為原料進(jìn)行碎煤加壓氣化是指焦炭加入碎煤加壓氣化爐,依靠重力作用緩慢下降并從上到下經(jīng)過干燥、干餾、甲烷化、氣化和殘?zhí)既紵鱾€(gè)床層,氣化劑經(jīng)氣化劑入口進(jìn)入氣化爐進(jìn)行一系列反應(yīng),最終生成壓力為1.0-8.0MPa、溫度為500-650℃的含油塵粗煤氣。如上所述的碎煤加壓氣化使用的碎煤加壓氣化爐是指薩松盧爾吉技術(shù)有限公司在中國(guó)申請(qǐng)的專利號(hào)為200580041975.8的固定床煤氣化爐,或內(nèi)蒙古大唐國(guó)際克什克騰煤制天然氣有限責(zé)任公司申請(qǐng)的專利號(hào)為CN201320037548.4的一種碎煤加壓氣化裝置;賽鼎工程有限公司申請(qǐng)的專利號(hào)為CN201410763734.5的一種碎煤加壓氣化爐,在上述氣化爐的基礎(chǔ)上,通過延長(zhǎng)氣化爐的高度1-3米,博斯曼套筒采用水夾套結(jié)構(gòu)。如上所述進(jìn)入除塵旋風(fēng)分離裝置中旋風(fēng)分離器的含油塵粗煤氣速度為15-27m/s。如上所述的旋風(fēng)除塵器和灰罐均采用夾套雙層結(jié)構(gòu),維持旋風(fēng)除塵器外筒體內(nèi)壁和灰罐內(nèi)壁的壁溫在180-240℃之間,防止含油塵冷凝。如上所述的含油塵富集到旋風(fēng)分離器的外筒體底部,使用煤氣或惰性氣氛對(duì)灰罐進(jìn)行充壓至與旋風(fēng)分離器壓力一致,打開含油塵排放閥進(jìn)行排灰,排完灰后關(guān)閉含油塵排放閥,卸灰罐壓力到常壓后將含油塵排出灰罐進(jìn)行攪拌、洗滌。如上所述的除塵旋風(fēng)分離器裝置,它包括旋風(fēng)除塵器201和灰罐213,旋風(fēng)除塵器1包括外筒體211和內(nèi)筒體205,外筒體211的上部呈直筒,下部呈倒錐形,外筒體211由外筒體外壁208和外筒體內(nèi)壁209組成,并形成夾套結(jié)構(gòu),內(nèi)筒體205通過拉伸件210固定在外筒體內(nèi)壁209上,含油塵粗煤氣進(jìn)口202通過外筒體211與內(nèi)筒體205下部相通,粗煤氣出口203位于外筒體211頂端,外筒體外壁208上部有旋風(fēng)除塵器熱水出口207,下部有旋風(fēng)除塵器熱水進(jìn)口206,外筒體211的底端出口通過含油塵排放閥204與灰罐213頂端連接。如上所述的內(nèi)筒體205是錐筒體結(jié)構(gòu),呈上部小,底部大錐筒形。如上所述的含油塵粗煤氣進(jìn)口202與外筒體內(nèi)壁209的夾角α為75-89度之間。如上所述的灰罐213包括排灰口214、灰罐夾套給水口215、灰罐夾套排水口216、平衡氣進(jìn)口217、平衡氣出口218,灰罐213的底端為排灰口214,灰罐213的頂端為油塵入口212,灰罐213的上部呈垂直形,下部呈倒錐形,并采用夾套雙層結(jié)構(gòu),灰罐213的頂部有平衡氣進(jìn)口217和平衡氣出口218,灰罐213的上部有灰罐夾套排水口216,灰罐213的下部有灰罐夾套給水口215。如上所述的灰罐213夾套雙層結(jié)構(gòu)由灰罐內(nèi)壁219和灰罐外壁220組成。本發(fā)明旋風(fēng)除塵器201以外筒體內(nèi)壁209的1m直徑為基準(zhǔn),其它結(jié)構(gòu)相對(duì)參數(shù)如表1。表1旋風(fēng)除塵器設(shè)計(jì)結(jié)構(gòu)參數(shù)序號(hào)結(jié)構(gòu)名稱結(jié)構(gòu)相對(duì)參數(shù)(單位m)1外筒體內(nèi)壁209直徑1.02含油塵粗煤氣進(jìn)口202位置(從外筒體直筒底部計(jì)量)0.25-0.503含油塵粗煤氣進(jìn)口202直徑0.2-0.254內(nèi)筒體205高度0.5-0.855外筒體211直筒高度1.5-1.66粗煤氣出口203直徑0.25-0.307外筒體211錐形高度2.2-2.58外筒體211的底端出口直徑0.30-0.359內(nèi)筒體205與外筒體內(nèi)壁209之間距離0.2-0.3如上所述的一體式廢熱回收器,它包括除了塵的粗煤氣進(jìn)口302、回收廢熱粗煤氣出口303、廢液排放口304和殼體301,其特征在于殼體301頂端有除了塵的粗煤氣進(jìn)口302,底端有廢液排放口304,下部有回收廢熱粗煤氣出口303,上部有過熱器307,中部從上到下有熱回收器Ⅱ306和熱回收器Ⅰ305。如上所述的過熱器307有中壓蒸汽入口312和過熱蒸汽出口313。如上所述的熱回收器Ⅱ306有熱回收器Ⅱ給水口310和中壓蒸汽出口311。如上所述的熱回收器Ⅰ305有熱回收器Ⅰ給水口308和低壓蒸汽出口309。本發(fā)明可以根據(jù)后續(xù)蒸汽品質(zhì)要求,設(shè)立不同的換熱面積,生產(chǎn)不同數(shù)量和等級(jí)的蒸汽。本發(fā)明的有益效果如下:1、干法脫出碎煤加壓氣化生產(chǎn)的粗煤氣中含油塵,避免大量洗滌煤氣水產(chǎn)生和處理。2、工藝流程短、能耗低、煤氣顯熱損失少,有利于廢熱分級(jí)回收。3、一體式廢熱回收器占地面積小、投資低,熱回收效率高。附圖說明圖1是本發(fā)明的工藝示意圖。圖2是本發(fā)明的除塵旋風(fēng)分離器裝置結(jié)構(gòu)示意圖。圖3是本發(fā)明的一體式廢熱回收器結(jié)構(gòu)示意圖。如圖所示,201-旋風(fēng)除塵器、202-含油塵粗煤氣進(jìn)口、203-粗煤氣出口、204-含油塵排放閥、205-內(nèi)筒體、206-旋風(fēng)除塵器熱水進(jìn)口、207-旋風(fēng)除塵器熱水出口、208-外筒體外壁、209-外筒體內(nèi)壁、210-拉伸件、211-外筒體、212-油塵入口、213-灰罐、214-排灰口、215-灰罐夾套給水口、216-灰罐夾套排水口、217-平衡煤氣進(jìn)口、218-平衡煤氣出口、219-灰罐內(nèi)壁、220-灰罐外壁、α-粗煤氣通道與旋風(fēng)除塵器外筒體內(nèi)壁夾角301-殼體,302-除了塵的粗煤氣進(jìn)口,303-回收廢熱粗煤氣出口,304-廢液排放口,305-熱回收器Ⅰ,306-熱回收器Ⅱ,307-過熱器,308-熱回收器Ⅰ給水口,309-低壓蒸汽出口,310-熱回收器Ⅱ給水口,311-中壓蒸汽出口,312-中壓蒸汽入口,313-過熱蒸汽出口具體實(shí)施方式下面通過具體的實(shí)施例進(jìn)一步說明本發(fā)明,但是應(yīng)當(dāng)理解為這些實(shí)施例僅僅是用于更詳細(xì)、具體地說明之用,而不應(yīng)理解為用于以任何形式限制本發(fā)明。本部分對(duì)本發(fā)明中所使用到的材料以及試驗(yàn)方法進(jìn)行一般性的描述。雖然為實(shí)現(xiàn)本發(fā)明所使用的許多材料和操作方法是本領(lǐng)域公知的,但是本發(fā)明仍然在此作盡可能詳細(xì)描述。本領(lǐng)域技術(shù)人員清楚,在上下文中,如果未特別說明,本發(fā)明所用材料和操作方法是本領(lǐng)域公知的。以下結(jié)合附圖對(duì)本發(fā)明的具體實(shí)施方式做更為詳細(xì)的說明。實(shí)施例1碎煤加壓氣化爐是指在200580041975.8的固定床煤氣化爐的基礎(chǔ)上延長(zhǎng)2.9米,博斯曼套筒采用水夾套結(jié)構(gòu)。除塵旋風(fēng)分離器裝置,它包括旋風(fēng)除塵器201和灰罐213,旋風(fēng)除塵器1包括外筒體211和內(nèi)筒體205,外筒體211的上部呈直筒,下部呈倒錐形,外筒體211由外筒體外壁208和外筒體內(nèi)壁209組成,并形成夾套結(jié)構(gòu),內(nèi)筒體205通過拉伸件210固定在外筒體內(nèi)壁209上,含油塵粗煤氣進(jìn)口202通過外筒體211與內(nèi)筒體205下部相通,粗煤氣出口203位于外筒體211頂端,外筒體外壁208上部有旋風(fēng)除塵器熱水出口207,下部有旋風(fēng)除塵器熱水進(jìn)口206,外筒體211的底端出口通過含油塵排放閥204與灰罐213頂端連接。所述的內(nèi)筒體205是錐筒體結(jié)構(gòu),呈上部小,底部大錐筒形。所述的含油塵粗煤氣進(jìn)口202與外筒體內(nèi)壁209的夾角α為75度。所述的灰罐213包括排灰口214、灰罐夾套給水口215、灰罐夾套排水口216、平衡氣進(jìn)口217、平衡氣出口218,灰罐213的底端為排灰口214,灰罐213的頂端為油塵入口212,灰罐213的上部呈垂直形,下部呈倒錐形,并采用夾套雙層結(jié)構(gòu),灰罐213的頂部有平衡氣進(jìn)口217和平衡氣出口218,灰罐213的上部有灰罐夾套排水口216,灰罐213的下部有灰罐夾套給水口215。所述的灰罐213夾套雙層結(jié)構(gòu)由灰罐內(nèi)壁219和灰罐外壁220組成。所述外筒體內(nèi)壁209和灰罐內(nèi)壁219的壁溫在183℃。本發(fā)明旋風(fēng)除塵器201以外筒體內(nèi)壁209的1m直徑為基準(zhǔn),其它結(jié)構(gòu)相對(duì)參數(shù)如表2。表2旋風(fēng)除塵器設(shè)計(jì)結(jié)構(gòu)參數(shù)序號(hào)結(jié)構(gòu)名稱結(jié)構(gòu)相對(duì)參數(shù)(單位m)1外筒體內(nèi)壁209直徑1.02含油塵粗煤氣進(jìn)口202位置(從外筒體直筒底部計(jì)量)0.473含油塵粗煤氣進(jìn)口202直徑0.254內(nèi)筒體205高度0.795外筒體211直筒高度1.56粗煤氣出口203直徑0.257外筒體211錐形高度2.218外筒體211的底端出口直徑0.309內(nèi)筒體205與外筒體內(nèi)壁209之間距離0.22一體式廢熱回收器,它包括除了塵的粗煤氣進(jìn)口302、回收廢熱粗煤氣出口303、廢液排放口304和殼體301,其特征在于殼體301頂端有除了塵的粗煤氣進(jìn)口302,底端有廢液排放口304,下部有回收廢熱粗煤氣出口303,上部有過熱器307,中部從上到下有熱回收器Ⅱ306和熱回收器Ⅰ305。所述的過熱器307有中壓蒸汽入口312和過熱蒸汽出口313。所述的熱回收器Ⅱ306有熱回收器Ⅱ給水口310和中壓蒸汽出口311。所述的熱回收器Ⅰ305有熱回收器Ⅰ給水口308和低壓蒸汽出口309。(1)以焦炭為原料,經(jīng)過碎煤加壓氣化生成壓力為6.5MPa、溫度為600℃的含油塵粗煤氣;(2)將含油塵粗煤氣以18m/s的速度進(jìn)入除塵旋風(fēng)分離裝置中的旋風(fēng)分離器201進(jìn)行分離,煤氣中油塵受離心力和離開內(nèi)筒體205時(shí)突然降速雙重作用的影響,使油塵及部分氣體從內(nèi)筒體205和外筒體211的間隙返回錐筒體進(jìn)行自旋分離,分離后的氣體與進(jìn)入旋風(fēng)分離器201的含油塵粗煤氣混合并再次分離,得到每立方米粗煤氣中油塵的含量在50mg的粗煤氣和含油塵;(3)將含油塵富集到旋風(fēng)分離器的外筒體底部,使用煤氣或惰性氣氛對(duì)灰罐進(jìn)行充壓至與旋風(fēng)分離器壓力一致,打開含油塵排放閥進(jìn)行排灰,排完灰后關(guān)閉含油塵排放閥,卸灰罐壓力到常壓后將含油塵排出灰罐送到攪拌、洗滌裝置;(4)將步驟(2)得到的粗煤氣進(jìn)入一體式廢熱回收器,先后通過過熱器、熱回收器Ⅱ、熱回收器Ⅰ分級(jí)回收熱量后由回收廢熱粗煤氣出口3排出到冷卻器,回收熱量過程生成1.5MPa,198.2℃的低壓飽和蒸汽,7.0MPa,285.7℃的中壓蒸汽和6.4MPa、540℃的過熱蒸汽三個(gè)等級(jí)的蒸汽,產(chǎn)生的冷凝液經(jīng)廢液排放口排出一體式廢熱回收器送到攪拌、洗滌裝置;。(5)冷卻器進(jìn)行冷卻,得到產(chǎn)品煤氣和輕油,輕油送到攪拌、洗滌裝置;(6)將含油塵送入攪拌、洗滌裝置進(jìn)行洗滌、攪拌形成焦油、水、渣的混合物,經(jīng)過超級(jí)離心機(jī)分離,得到含塵焦油輕組分以及水和渣重組份,水和渣重組份靜置分層處理,得到水和渣;含塵焦油輕組分通過孔徑在12um的金屬燒結(jié)網(wǎng)過濾器進(jìn)行再次分離,使焦油中塵的含量降到0.75mg,過濾得到的焦油作為產(chǎn)品,塵富集在燒結(jié)金屬網(wǎng)過濾器底部間隙排出。實(shí)施例2碎煤加壓氣化爐是指CN201410763734.5的一種碎煤加壓氣化爐的基礎(chǔ)上延長(zhǎng)1.1米,博斯曼套筒采用水夾套結(jié)構(gòu)。含油塵粗煤氣進(jìn)口202與外筒體內(nèi)壁209形成夾角α為76度。外筒體內(nèi)壁209和灰罐內(nèi)壁219的壁溫在273℃。本發(fā)明旋風(fēng)除塵器201以外筒體內(nèi)壁209的1m直徑為基準(zhǔn),其它結(jié)構(gòu)相對(duì)參數(shù)如表3。表3旋風(fēng)除塵器設(shè)計(jì)結(jié)構(gòu)參數(shù)序號(hào)結(jié)構(gòu)名稱結(jié)構(gòu)相對(duì)參數(shù)(單位m)1外筒體內(nèi)壁209直徑1.02含油塵粗煤氣進(jìn)口202位置(從外筒體直筒底部計(jì)量)0.253含油塵粗煤氣進(jìn)口202直徑0.214內(nèi)筒體205高度0.515外筒體211直筒高度1.516粗煤氣出口203直徑0.267外筒體211錐形高度2.218外筒體211的底端出口直徑0.319內(nèi)筒體205與外筒體內(nèi)壁209之間距離0.22(1)以焦炭為原料,經(jīng)過碎煤加壓氣化生成壓力為7.8MPa、溫度為640℃的含油塵粗煤氣;(2)將含油塵粗煤氣以26m/s的速度進(jìn)入除塵旋風(fēng)分離裝置中的旋風(fēng)分離器201進(jìn)行分離,煤氣中油塵受離心力和離開內(nèi)筒體205時(shí)突然降速雙重作用的影響,使油塵及部分氣體從內(nèi)筒體205和外筒體211的間隙返回錐筒體進(jìn)行自旋分離,分離后的氣體與進(jìn)入旋風(fēng)分離器201的含油塵粗煤氣混合并再次分離,得到每立方米粗煤氣中油塵的含量在75mg的粗煤氣和含油塵;(3)將含油塵富集到旋風(fēng)分離器的外筒體底部,使用煤氣或惰性氣氛對(duì)灰罐進(jìn)行充壓至與旋風(fēng)分離器壓力一致,打開含油塵排放閥進(jìn)行排灰,排完灰后關(guān)閉含油塵排放閥,卸灰罐壓力到常壓后將含油塵排出灰罐送到攪拌、洗滌裝置;(4)將步驟(2)得到的粗煤氣進(jìn)入一體式廢熱回收器,先后通過過熱器、熱回收器Ⅱ、熱回收器Ⅰ分級(jí)回收熱量后由回收廢熱粗煤氣出口3排出到冷卻器,回收熱量過程生成生成0.6MPa,158.7℃的低壓飽和蒸汽,6.0MPa,275.4℃的中壓蒸汽和7.8MPa、340℃的過熱蒸汽三個(gè)等級(jí)的蒸汽,產(chǎn)生的冷凝液經(jīng)廢液排放口排出一體式廢熱回收器送到攪拌、洗滌裝置。(5)冷卻器進(jìn)行冷卻,得到產(chǎn)品煤氣和輕油,輕油送到攪拌、洗滌裝置;(6)將含油塵送入攪拌、洗滌裝置進(jìn)行洗滌、攪拌形成焦油、水、渣的混合物,經(jīng)過超級(jí)離心機(jī)分離,得到含塵焦油輕組分以及水和渣重組份,水和渣重組份靜置分層處理,得到水和渣;含塵焦油輕組分通過孔徑在25um的金屬燒結(jié)網(wǎng)過濾器進(jìn)行再次分離,使焦油中塵的含量降到0.32mg,過濾得到的焦油作為產(chǎn)品,塵富集在燒結(jié)金屬網(wǎng)過濾器底部間隙排出。實(shí)施例3碎煤加壓氣化爐是指在CN201410763734.5的一種碎煤加壓氣化爐的碎煤加壓氣化爐,的高度延長(zhǎng)2.5米,博斯曼套筒采用水夾套結(jié)構(gòu)。含油塵粗煤氣進(jìn)口202與外筒體內(nèi)壁209形成夾角α為82度。外筒體內(nèi)壁209和灰罐內(nèi)壁219的壁溫在225℃。本發(fā)明旋風(fēng)除塵器201以外筒體內(nèi)壁209的1m直徑為基準(zhǔn),其它結(jié)構(gòu)相對(duì)參數(shù)如表4。表4旋風(fēng)除塵器設(shè)計(jì)結(jié)構(gòu)參數(shù)(1)以焦炭為原料,經(jīng)過碎煤加壓氣化生成壓力為1.1MPa、溫度為515℃的含油塵粗煤氣;(2)將含油塵粗煤氣以26m/s的速度進(jìn)入除塵旋風(fēng)分離裝置中的旋風(fēng)分離器201進(jìn)行分離,煤氣中油塵受離心力和離開內(nèi)筒體205時(shí)突然降速雙重作用的影響,使油塵及部分氣體從內(nèi)筒體205和外筒體211的間隙返回錐筒體進(jìn)行自旋分離,分離后的氣體與進(jìn)入旋風(fēng)分離器201的含油塵粗煤氣混合并再次分離,得到每立方米粗煤氣中油塵的含量在32mg的粗煤氣和含油塵;(3)將含油塵富集到旋風(fēng)分離器的外筒體底部,使用煤氣或惰性氣氛對(duì)灰罐進(jìn)行充壓至與旋風(fēng)分離器壓力一致,打開含油塵排放閥進(jìn)行排灰,排完灰后關(guān)閉含油塵排放閥,卸灰罐壓力到常壓后將含油塵排出灰罐送到攪拌、洗滌裝置;(4)將步驟(2)得到的粗煤氣進(jìn)入一體式廢熱回收器,先后通過過熱器、熱回收器Ⅱ、熱回收器Ⅰ分級(jí)回收熱量后由回收廢熱粗煤氣出口3排出到冷卻器,回收熱量過程生成生成1.2MPa,187.8℃的低壓飽和蒸汽,2.1MPa,212.2℃的中壓蒸汽和3.2MPa、380℃的過熱蒸汽三個(gè)等級(jí)的蒸汽,產(chǎn)生的冷凝液經(jīng)廢液排放口排出一體式廢熱回收器送到攪拌、洗滌裝置。(5)冷卻器進(jìn)行冷卻,得到產(chǎn)品煤氣和輕油,輕油送到攪拌、洗滌裝置;(6)將含油塵送入攪拌、洗滌裝置進(jìn)行洗滌、攪拌形成焦油、水、渣的混合物,經(jīng)過超級(jí)離心機(jī)分離,得到含塵焦油輕組分以及水和渣重組份,水和渣重組份靜置分層處理,得到水和渣;含塵焦油輕組分通過孔徑在56um的金屬燒結(jié)網(wǎng)過濾器進(jìn)行再次分離,使焦油中塵的含量降到0.65mg,過濾得到的焦油作為產(chǎn)品,塵富集在燒結(jié)金屬網(wǎng)過濾器底部間隙排出。實(shí)施例4碎煤加壓氣化爐是指在中國(guó)專利號(hào):201410763734.5的碎煤加壓氣化爐的高度延長(zhǎng)1.5米,博斯曼套筒采用水夾套結(jié)構(gòu)。含油塵粗煤氣進(jìn)口202與外筒體內(nèi)壁209形成夾角α為86度。外筒體內(nèi)壁209和灰罐內(nèi)壁219的壁溫在273℃。本發(fā)明旋風(fēng)除塵器201以外筒體內(nèi)壁209的1m直徑為基準(zhǔn),其它結(jié)構(gòu)相對(duì)參數(shù)如表5。表5旋風(fēng)除塵器設(shè)計(jì)結(jié)構(gòu)參數(shù)序號(hào)結(jié)構(gòu)名稱結(jié)構(gòu)相對(duì)參數(shù)(單位m)1外筒體內(nèi)壁209直徑1.02含油塵粗煤氣進(jìn)口202位置(從外筒體直筒底部計(jì)量)0.473含油塵粗煤氣進(jìn)口202直徑0.254內(nèi)筒體205高度0.685外筒體211直筒高度1.536粗煤氣出口203直徑0.287外筒體211錐形高度2.458外筒體211的底端出口直徑0.349內(nèi)筒體205與外筒體內(nèi)壁209之間距離0.24(1)以焦炭為原料,經(jīng)過碎煤加壓氣化生成壓力為3.0MPa、溫度為580℃的含油塵粗煤氣;(2)將含油塵粗煤氣以19m/s的速度進(jìn)入除塵旋風(fēng)分離裝置中的旋風(fēng)分離器201進(jìn)行分離,煤氣中油塵受離心力和離開內(nèi)筒體205時(shí)突然降速雙重作用的影響,使油塵及部分氣體從內(nèi)筒體205和外筒體211的間隙返回錐筒體進(jìn)行自旋分離,分離后的氣體與進(jìn)入旋風(fēng)分離器201的含油塵粗煤氣混合并再次分離,得到每立方米粗煤氣中油塵的含量在21mg的粗煤氣和含油塵;(3)將含油塵富集到旋風(fēng)分離器的外筒體底部,使用煤氣或惰性氣氛對(duì)灰罐進(jìn)行充壓至與旋風(fēng)分離器壓力一致,打開含油塵排放閥進(jìn)行排灰,排完灰后關(guān)閉含油塵排放閥,卸灰罐壓力到常壓后將含油塵排出灰罐送到攪拌、洗滌裝置;(4)將步驟(2)得到的粗煤氣進(jìn)入一體式廢熱回收器,先后通過過熱器、熱回收器Ⅱ、熱回收器Ⅰ分級(jí)回收熱量后由回收廢熱粗煤氣出口3排出到冷卻器,回收熱量過程生成生成0.8MPa,170.4℃的低壓飽和蒸汽,4.0MPa,250.3℃的中壓蒸汽和4.0MPa、400℃的過熱蒸汽三個(gè)等級(jí)的蒸汽,產(chǎn)生的冷凝液經(jīng)廢液排放口排出一體式廢熱回收器送到攪拌、洗滌裝置。(5)冷卻器進(jìn)行冷卻,得到產(chǎn)品煤氣和輕油,輕油送到攪拌、洗滌裝置;(6)將含油塵送入攪拌、洗滌裝置進(jìn)行洗滌、攪拌形成焦油、水、渣的混合物,經(jīng)過超級(jí)離心機(jī)分離,得到含塵焦油輕組分以及水和渣重組份,水和渣重組份靜置分層處理,得到水和渣;含塵焦油輕組分通過孔徑在82um的金屬燒結(jié)網(wǎng)過濾器進(jìn)行再次分離,使焦油中塵的含量降到0.65mg,過濾得到的焦油作為產(chǎn)品,塵富集在燒結(jié)金屬網(wǎng)過濾器底部間隙排出。實(shí)施例5碎煤加壓氣化爐是指中國(guó)專利:201320037548.4的碎煤加壓氣化裝置的高度延長(zhǎng)2.1米,博斯曼套筒采用水夾套結(jié)構(gòu)。含油塵粗煤氣進(jìn)口202與外筒體內(nèi)壁209形成夾角α為81度。外筒體內(nèi)壁209和灰罐內(nèi)壁219的壁溫在218℃。本發(fā)明旋風(fēng)除塵器201以外筒體內(nèi)壁209的1m直徑為基準(zhǔn),其它結(jié)構(gòu)相對(duì)參數(shù)如表6。表6旋風(fēng)除塵器設(shè)計(jì)結(jié)構(gòu)參數(shù)序號(hào)結(jié)構(gòu)名稱結(jié)構(gòu)相對(duì)參數(shù)(單位m)1外筒體內(nèi)壁209直徑1.02含油塵粗煤氣進(jìn)口202位置(從外筒體直筒底部計(jì)量)0.323含油塵粗煤氣進(jìn)口202直徑0.244內(nèi)筒體205高度0.625外筒體211直筒高度1.526粗煤氣出口203直徑0.277外筒體211錐形高度2.48外筒體211的底端出口直徑0.339內(nèi)筒體205與外筒體內(nèi)壁209之間距離0.27(1)以焦炭為原料,經(jīng)過碎煤加壓氣化生成壓力為4.3MPa、溫度為540℃的含油塵粗煤氣;(2)將含油塵粗煤氣以23m/s的速度進(jìn)入除塵旋風(fēng)分離裝置中的旋風(fēng)分離器201進(jìn)行分離,煤氣中油塵受離心力和離開內(nèi)筒體205時(shí)突然降速雙重作用的影響,使油塵及部分氣體從內(nèi)筒體205和外筒體211的間隙返回錐筒體進(jìn)行自旋分離,分離后的氣體與進(jìn)入旋風(fēng)分離器201的含油塵粗煤氣混合并再次分離,得到每立方米粗煤氣中油塵的含量在4mg的粗煤氣和含油塵;(3)將含油塵富集到旋風(fēng)分離器的外筒體底部,使用煤氣或惰性氣氛對(duì)灰罐進(jìn)行充壓至與旋風(fēng)分離器壓力一致,打開含油塵排放閥進(jìn)行排灰,排完灰后關(guān)閉含油塵排放閥,卸灰罐壓力到常壓后將含油塵排出灰罐送到攪拌、洗滌裝置;(4)將步驟(2)得到的粗煤氣進(jìn)入一體式廢熱回收器,先后通過過熱器、熱回收器Ⅱ、熱回收器Ⅰ分級(jí)回收熱量后由回收廢熱粗煤氣出口3排出到冷卻器,回收熱量過程生成生成1.1MPa,180.2℃的低壓飽和蒸汽,5.0MPa,263.8度的飽和中壓蒸汽,5.0MPa、440℃的過熱蒸汽。產(chǎn)生的冷凝液經(jīng)廢液排放口排出一體式廢熱回收器送到攪拌、洗滌裝置(5)冷卻器進(jìn)行冷卻,得到產(chǎn)品煤氣和輕油,輕油送到攪拌、洗滌裝置;(6)將含油塵送入攪拌、洗滌裝置進(jìn)行洗滌、攪拌形成焦油、水、渣的混合物,經(jīng)過超級(jí)離心機(jī)分離,得到含塵焦油輕組分以及水和渣重組份,水和渣重組份靜置分層處理,得到水和渣;含塵焦油輕組分通過孔徑在105um的金屬燒結(jié)網(wǎng)過濾器進(jìn)行再次分離,使焦油中塵的含量降到0.79mg,過濾得到的焦油作為產(chǎn)品,塵富集在燒結(jié)金屬網(wǎng)過濾器底部間隙排出。當(dāng)前第1頁(yè)1 2 3