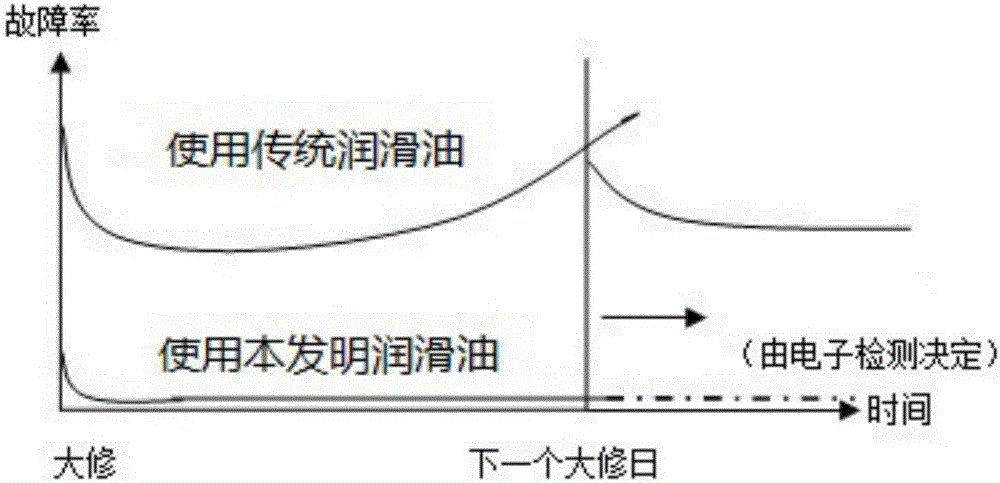
本發(fā)明涉及潤滑
技術(shù)領(lǐng)域:
,具體涉及一種功能性潤滑油。
背景技術(shù):
:潤滑,幾乎是伴隨著人類文明歷史的成長而發(fā)展的一個古老而又新穎的話題。自從達.芬奇在十五世紀給它下了定義以來,至今已有400多年的歷史了。然而,由于生產(chǎn)力低下,潤滑作為一門跨邊緣的基礎(chǔ)技術(shù)在很長一個歷史時期里未被人們認識和重視。只是在近代,特別是石油化學工業(yè)的發(fā)展,它才得到了飛速發(fā)展。但無論是古代的動、植物油或脂的應用,還是近代礦物油加各種添加劑的使用,都是依靠油在摩擦副的表現(xiàn)形成油膜強度來達到潤滑和減小摩擦的,本質(zhì)上還是滑動摩擦。我國各潤滑油研制和生產(chǎn)廠家,本著向國際標準靠攏的原則,近年來開展了各種潤滑油技術(shù)的開發(fā)和研制工作。但是仍然受制于國外技術(shù)的限制,這些油品大多存在著諸多問題,主要表現(xiàn)在:(1)易氧化:溫度是影響油品使用的最重要的因素之一,摩擦副之間既有設(shè)備旋轉(zhuǎn)及工作部件之間的摩擦熱能,又有壓力環(huán)境下產(chǎn)生的內(nèi)能。高溫可以加劇油品的氧化變質(zhì),試驗數(shù)據(jù)表明,溫度每升高10℃,氧化速度加劇一倍。同時還要考慮環(huán)境中水分、污染顆粒等的影響,以及潤滑油潤滑工作中的溫度高低交替等影響因素,潤滑油易氧化變質(zhì)。(2)極壓抗磨性不足:設(shè)備潤滑過程中對極壓抗磨性能要求嚴格,尤其如軸承部件之間等都存在著摩擦,特別是現(xiàn)在高壓、高轉(zhuǎn)速、高強度持續(xù)運轉(zhuǎn)的情況下,極壓抗磨性能不足的潤滑油,易造成磨損或設(shè)備損壞。(3)壽命短:一般產(chǎn)品的使用壽命短暫,長這一年短則數(shù)月,頻繁的更換、停機均是大量的浪費,也極大的降低了生產(chǎn)效率。另外,還有過高的祭壇傾向等問題,都嚴重制約著潤滑技術(shù)的發(fā)展。技術(shù)實現(xiàn)要素:本發(fā)明的目的在于:提供一種改變傳統(tǒng)的潤滑油形成油膜的潤滑方式,在潤滑過程中將滑動摩擦變?yōu)闈L動摩擦的功能性潤滑油及其制備方法。本發(fā)明是通過以下技術(shù)方案實現(xiàn)的:一種功能性潤滑油,由以下重量份的原料制備而成:0.1-2.0%的降凝劑,0.5-3.0%的含磷型抗磨劑;0.8-4.0%的極壓劑;0.01-1.5%的金屬防銹劑;0.01-1.5%的金屬減活劑;為0.1-3.0%的抗氧劑;300-500ppm的消泡劑;0.8-4.0%的減磨劑,余量為基礎(chǔ)油,其中減磨劑為二硫代磷酸鉬減磨劑。進一步的:基礎(chǔ)油為APIIII類加氫精制礦物基礎(chǔ)油。進一步的:降凝劑為烷基萘型降凝劑或聚甲基丙烯酸酯型降凝劑。進一步的:含磷型抗磨劑為亞磷酸二正丁酯或磷酸三甲酚酯。進一步的:極壓劑為硫化烯烴。進一步的:金屬防銹劑為油酸酰胺或油?;彼帷_M一步的:金屬減活劑為噻二唑及其衍生物。進一步的:抗氧劑為苯基-α-萘胺或二烷基二苯胺。進一步的:消泡劑為聚甲基丙烯酸酯型消泡劑。所述的功能性潤滑油的制備方法,在帶攪拌和加熱功能的調(diào)和釜中,加入基礎(chǔ)油,然后按重量份添加0.1-2.0%的降凝劑,0.5-3.0%的含磷型抗磨劑;0.8-4.0%的極壓劑;0.01-1.5%的金屬防銹劑;0.01-1.5%的金屬減活劑;0.1-3.0%的抗氧劑;300-500ppm的消泡劑;0.8-4.0%的減磨劑,在50-70℃下攪拌1-3h調(diào)和而成。與現(xiàn)有技術(shù)相比,本發(fā)明具有以下有益效果:在潤滑過程中,形成微共晶滾珠,吸附填補在摩擦副之間,將傳統(tǒng)的滑動摩擦變?yōu)闈L動摩擦,大大提升了潤滑效果。附圖說明圖1是本發(fā)明的潤滑油與普通潤滑油對機器故障率的影響監(jiān)測結(jié)果曲線圖;圖2是本發(fā)明的潤滑油對機器磨損顆粒的影響監(jiān)測結(jié)果曲線圖。具體實施方式為了使本發(fā)明的目的、技術(shù)方案及優(yōu)點更加清楚明白,以下結(jié)合實施例,對本發(fā)明進行進一步詳細說明。應當理解,此處所描述的具體實施例僅僅用以解釋本發(fā)明,并不用于限定本發(fā)明。一種功能性潤滑油,由以下重量份的原料制備而成:0.1-2.0%的降凝劑,0.5-3.0%的含磷型抗磨劑;0.8-4.0%的極壓劑;0.01-1.5%的金屬防銹劑;0.01-1.5%的金屬減活劑;為0.1-3.0%的抗氧劑;300-500ppm的消泡劑;0.8-4.0%的減磨劑,余量為基礎(chǔ)油,其中減磨劑為二硫代磷酸鉬減磨劑。其中:基礎(chǔ)油為APIIII類加氫精制礦物基礎(chǔ)油;降凝劑為烷基萘型降凝劑或聚甲基丙烯酸酯型降凝劑;含磷型抗磨劑為亞磷酸二正丁酯或磷酸三甲酚酯;極壓劑為硫化烯烴;金屬防銹劑為油酸酰胺或油?;彼幔唤饘贉p活劑為噻二唑及其衍生物;抗氧劑為苯基-α-萘胺或二烷基二苯胺;消泡劑為聚甲基丙烯酸酯型消泡劑。實施例一:本發(fā)明的潤滑油的制備過程如下:首先調(diào)配基礎(chǔ)油成分,在帶攪拌和加熱功能的調(diào)和釜中,加入APIIII類加氫精制礦物基礎(chǔ)油,然后按照以下組分及重量份配比添加各種添加劑,在50-70℃下攪拌1-3h調(diào)和而成。降凝劑烷基萘型降凝劑0.8%含磷型抗磨劑磷酸三甲酚酯1.0%極壓劑硫化烯烴2.0%金屬防銹劑油?;彼?.1%金屬減活劑噻二唑及其衍生物0.05%抗氧劑苯基-α-萘胺0.5%消泡劑聚甲基丙烯酸酯型消泡劑350ppm減磨劑二硫代磷酸鉬減摩劑1.8%通過上述方法制備的潤滑油,在添加進機械設(shè)備之后,基礎(chǔ)油作為載體及冷卻劑,攜帶二硫代磷酸鉬減摩劑抵達接觸邊界,在摩擦瞬間產(chǎn)生局部高溫及金屬晶破碎時產(chǎn)生的超聲波能量的激化下,二硫代磷酸鉬減摩劑與新磨損下的金屬微屑結(jié)合生成極性的及熔點極高的共晶復合物,共晶復合物作為微型的吸附性滾珠堆填在金屬凹凸不平處,增大了微觀接觸面積,變滑動摩擦為滾動摩擦,從而大大降低了摩擦力,減少了磨損。同時產(chǎn)生的微共晶滾球在烷基萘型降凝劑;磷酸三甲酚酯;硫化烯烴;油?;彼幔秽缍蚣捌溲苌?;苯基-α-萘胺;聚甲基丙烯酸酯型消泡劑的輔助下,具備了抗酸、抗堿、防銹、承受高壓及高溫的能力。在相關(guān)的檢測試驗中,我們可以清楚的看到本發(fā)明的潤滑油對于減小摩擦起到的作用。如圖2所示,是在將機器中的普通潤滑油,替換為本發(fā)明潤滑油后,磨損顆粒的監(jiān)測情況。有曲線圖可知,在使用本發(fā)明的潤滑油后,磨損顆粒的粒徑逐漸變小,可見機器的磨損越來越小,潤滑效果越來越好。在與傳統(tǒng)潤滑油(即未添加二硫代磷酸鉬減摩劑的潤滑油)的對比測試中,我們可以看到:如圖1所示,是本發(fā)明的潤滑油對機器故障率的影響,從圖中的監(jiān)測結(jié)果可以看到,機器大修的時間大大的往后推遲了,可見本發(fā)明的潤滑油的潤滑效果極佳,大大減少了機器的磨損,而提高了機器的使用壽命。以上述依據(jù)本發(fā)明的理想實施例為啟示,通過上述的說明內(nèi)容,相關(guān)工作人員完全可以在不偏離本項發(fā)明技術(shù)思想的范圍內(nèi),進行多樣的變更以及修改。本項發(fā)明的技術(shù)性范圍并不局限于說明書上的內(nèi)容,必須要根據(jù)權(quán)利要求范圍來確定其技術(shù)性范圍。當前第1頁1 2 3