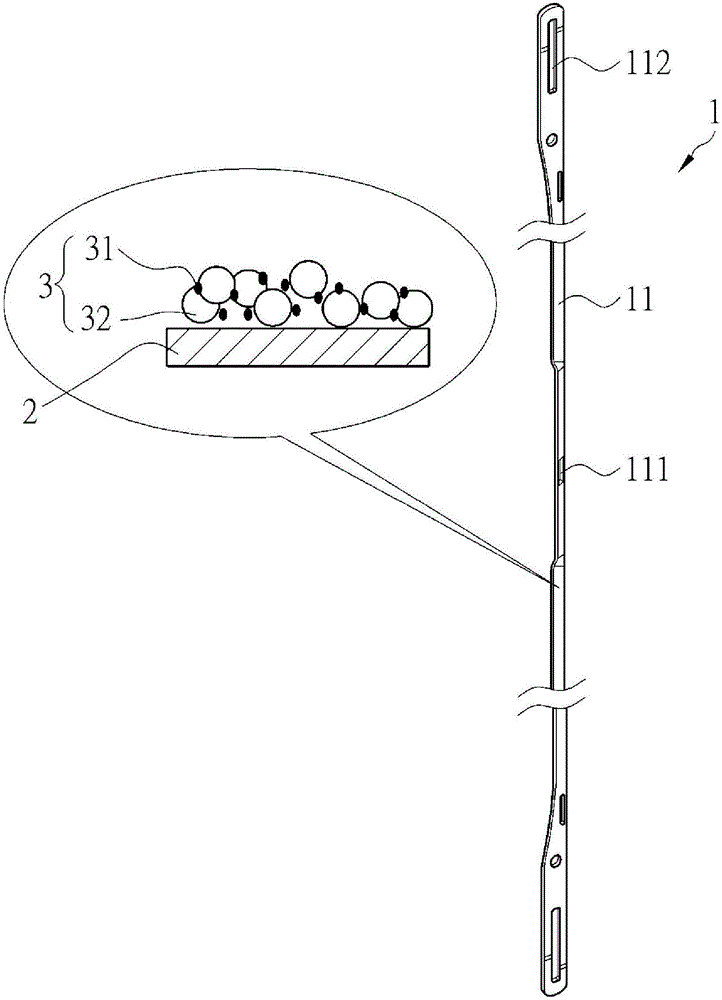
本發(fā)明涉及化工及紡織設(shè)備領(lǐng)域,尤其涉及一種耐磨特性及導(dǎo)熱性良好的涂覆復(fù)合電鍍層的織紗導(dǎo)向組件及其制作方法。
背景技術(shù):
:紡織纖維如棉、人造絲、聚酯、聚丙烯、聚酰胺、聚酰胺、羊毛,丙烯酸類、彈性纖維或其他彈性纖維等,都要將紡織纖維利用紡織機(jī)編織成為織布(織衣)。織紗導(dǎo)向組件為紡織機(jī)上的重要部件,如綜片(heald、heddle、harnesswire、guardwire,又稱為綜絲、綜線等)、筘片(heddlehook)、申克片(sinker,又稱為沉降片等)、鋼筘(reed、loomreed、dentreed)、停經(jīng)片(dropper)、紡針(knittingneedle)等。紡織機(jī)的車速高,一般在600~1000轉(zhuǎn)/min以上,織紗對(duì)織紗導(dǎo)向組件的摩擦和沖擊次數(shù)約為600~1000次/min,被引入織口的織紗隨著上、下層經(jīng)紗的交織,緯紗的彎曲程度增加,經(jīng)紗變形附加張應(yīng)力使得緯紗對(duì)織紗導(dǎo)向組件產(chǎn)生相對(duì)的作用力,加上織紗纖維特性和漿料等因素,加劇了織紗導(dǎo)向組件(如綜片的綜眼)的磨損,這種磨損屬于摩擦磨損、反復(fù)沖擊疲勞、應(yīng)力腐蝕等多種模式的復(fù)雜交互作用。例如,綜片是一個(gè)長(zhǎng)條型薄片結(jié)構(gòu),中間有綜眼,紡織纖維的經(jīng)紗在綜眼內(nèi)往復(fù)性地滑移,經(jīng)紗對(duì)綜眼形成切割狀的滑動(dòng)摩擦,在長(zhǎng)時(shí)間、高強(qiáng)度的摩擦作用下,綜眼附近因摩擦及熱累積而產(chǎn)生毛邊,一旦經(jīng)紗被割傷形成起毛起球嚴(yán)重,原本緊密的紗體結(jié)構(gòu)變得疏松無(wú)序,紗體單位截面內(nèi)纖維根數(shù)減少,導(dǎo)致經(jīng)紗條惡化,直至發(fā)生經(jīng)紗斷線。經(jīng)紗斷線導(dǎo)致紡織機(jī)頻繁停車更換綜片,嚴(yán)重影響紡織機(jī)工作效率,同時(shí)也造成布面瑕疵問題,降低成品等級(jí);類似的情況也發(fā)生在筘片、申克片、鋼筘、停經(jīng)片、或紡針上。尤其化纖、消光絲或倍捻紗等紡織纖維在織布時(shí),更要降低紡織機(jī)的轉(zhuǎn)速,以降低織紗導(dǎo)向組件(如綜片)磨損,這也直接造成產(chǎn)率低、成本高的問題,這是紡織業(yè)界急待解決的問題。常見的織紗導(dǎo)向組件(如綜片)是使用金屬薄片,如高碳鋼片或不銹鋼作為原料,經(jīng)過沖壓與拋光制成的。不銹鋼或金屬制的織紗導(dǎo)向組件(如綜片),具有較好的機(jī)械強(qiáng)度,對(duì)于棉線類的經(jīng)紗大約可承受約5000~10000公尺,但對(duì)于更強(qiáng)韌的聚酯線則降低至3000~5000公尺;為此,日本專利JP2001516814公開使用電鍍鎳、樹酯硬化層、氮化硬化或制成的全瓷表面;美國(guó)專利US7757516、US6230756公開使用真空電鍍(CVD、PVD等)涂覆二氧化硅(silica);中國(guó)專利CN102851825A公開在綜片本體表面利用雷射涂覆厚度為50~200μm的納米陶瓷涂層,納米陶瓷涂層是在陶瓷中加入或生成納米級(jí)顆粒、晶須、芯片纖維等;中國(guó)專利公開號(hào)CN200940182公開在綜片的綜眼周緣涂覆光滑的高強(qiáng)度耐磨材料(如搪瓷釉層、合金鍍層、聚四氟乙烯、聚全氟層),或綜眼由光滑的高強(qiáng)度耐磨材料制成;或如中國(guó)專利公開號(hào)CN201220317942.9公開在綜眼嵌入陶瓷圈;這些技術(shù)目的是降低經(jīng)紗的摩擦系數(shù),可在一定程度內(nèi)減少經(jīng)紗的摩擦損傷,但此類技術(shù)雖然可以延長(zhǎng)織紗導(dǎo)向組件的壽命,但對(duì)于數(shù)量龐大的織紗導(dǎo)向組件涂覆不易、價(jià)格昂貴,仍難以推廣使用。對(duì)于鋼筘或停經(jīng)片等織紗導(dǎo)向組件,類似的技術(shù)也被研究而公開,如德國(guó)斯巴力克(Spaleck)公司產(chǎn)品、中國(guó)專利公開號(hào)201210345825.8等使用電鍍硬鉻處理,如圖1,在不銹鋼停經(jīng)片91上先電鍍2~8μm的電鍍鎳耐磨層,再電鍍1~3μm的電鍍鉻層。雖然電鍍硬鉻表面硬度相對(duì)于電鍍鎳層較硬,若經(jīng)特別處理硬度可達(dá)1000HV,但其存在使用Cr6+的環(huán)保問題,并且因?yàn)殡婂冇层t鍍層應(yīng)力大,無(wú)法承受長(zhǎng)期的反復(fù)沖擊疲勞、應(yīng)力腐蝕,造成電鍍鉻層破裂或磨損,反而造成容易切割的痕道及毛邊。歐洲專利EP0485633、美國(guó)專利US5511587、中國(guó)專利公開號(hào)201220262380.2公開使用硫酸鎳電鍍?cè)?,將類鉆(DLC)、碳化硅(SiC)、氧化鋁(Al2O3)、氧化鋯(ZrO2)、氧化鉻(Cr2O3)等耐磨顆粒與電鍍鎳共沉積在異形鋼筘片或其他織紗導(dǎo)向組件上,例如厚度為5~20μm、1~10μm等,達(dá)到表面硬度1000-2000HV以上、表面摩擦系數(shù)0.14以下;又如歐洲專利EP0550752公開在碳化鈦或其他碳化物、氧化物、電鍍鉻上涂覆DLC,以達(dá)到高耐磨的目的,然而這種納米顆粒的合金化學(xué)復(fù)合層存在附著力不良、制作成本過高等問題,也難推廣使用。雖然近年來(lái),在塑料材料上的突破,使用塑料材料取代金屬的塑料綜片;塑料綜片相對(duì)金屬的綜片節(jié)省材料成本,但難解決耐磨問題,中國(guó)專利公開號(hào)CN201228305公開在塑料綜片的綜眼部分制成陶瓷綜眼,利用陶瓷光滑的高耐磨特性,減小與經(jīng)紗間的摩擦系數(shù)達(dá)到保護(hù)經(jīng)紗的目的;但不論嵌入陶瓷綜眼或利用塑料電鍍強(qiáng)化塑料綜片或塑料材料的織紗導(dǎo)向組件,從大量生產(chǎn)或成本方面考慮難以實(shí)施。塑料綜片或塑料材料的織紗導(dǎo)向組件在織造高強(qiáng)度的紡織纖維時(shí),仍存在壽命不長(zhǎng)、經(jīng)常停機(jī)更換、織布質(zhì)量不良、廢棄的塑料綜片難以回收造成環(huán)境的巨大破壞等問題。鉻金屬材料、鉻鈷鉬合金材料、鉻鈷合金材料、鉻鐵合金材料,普遍具有綜合機(jī)械性能佳、高硬度、耐磨耗性強(qiáng)、耐高溫、耐腐蝕等特性可使用于苛刻工業(yè)環(huán)境,中國(guó)專利CN103060617A公開高溫合金鍛造技術(shù),但這類材料又普遍存在韌性不佳、容易脆化的特性,如果直接用這類材料制成織紗導(dǎo)向組件則更為昂貴。若利用電漿輔助化學(xué)沉積法、氣相沉積法(CVD)、高能量微弧技術(shù)、高溫碳化、低溫碳化、物理氣相沉積(PVD)、美國(guó)專利US4925394的濺鍍法或氣相沉積法、EP1878943的擴(kuò)散鉻化法、臺(tái)灣專利公開號(hào)TW201101565的使用粉浴法、臺(tái)灣專利TWI297365等先前技術(shù),所公開可以利用碳化鉻粉末材料對(duì)工具以前述的方式(俗稱干式法)將鉻金屬、鉻鈷鉬合金、鉻鈷合金材、鉻鐵合金等合金材料涂覆在綜片上,雖較能克服韌性不佳容易脆化的特性,但也無(wú)法解決制造成本昂貴與難以大量生產(chǎn)的問題。金屬化陶瓷(metallicceramic)為非金屬元素滲雜有金屬元素共同形成的一種類陶瓷(Ceramic-like)結(jié)構(gòu)的共構(gòu)物,使其兼具有金屬特性與陶瓷特性,例如,有些共構(gòu)物具有一般陶瓷的硬度與很好的耐腐蝕性、或兼具有金屬光澤性與導(dǎo)電性、或兼具有陶瓷的色澤等;臺(tái)灣專利TWI441954、TWI441961、TWI533526及中國(guó)專利CN103726091等使用電鍍方法(俗稱濕式法)在基材上形成碳化鉻的金屬化陶瓷層,這種金屬化陶瓷層具有疏水性及良好的導(dǎo)電性,若要增加硬度則要使用高溫烘烤或用火焰燒灼;由于織紗導(dǎo)向組件輕又薄,不能使用高溫烘烤或用火焰燒灼以增加電鍍層硬度,否則會(huì)造成薄片的織紗導(dǎo)向組件喪失機(jī)械性能或翹曲,而且上述產(chǎn)品表面平整度不良及摩擦系數(shù)較大,對(duì)于細(xì)又軟的織紗仍會(huì)有刮紗現(xiàn)象,不能用于織紗導(dǎo)向組件。綜上,上述技術(shù)在解決高硬度、高疏水性、抗沾黏、高導(dǎo)電性等方面均有一定缺陷,運(yùn)用這些技術(shù)無(wú)法獲得具有高硬度、且具有耐磨性、更具有低摩擦力、熱傳導(dǎo)系數(shù)高避免熱累積的電鍍金屬化陶瓷層而應(yīng)用在織紗導(dǎo)向組件,因此,有必要研發(fā)更新的技術(shù)、提出有效的具體的改善方案。本發(fā)明基于此,利用電鍍技術(shù)發(fā)展出具有高硬度、且具有耐磨性、良好的耐腐蝕性、更具有低摩擦力、熱傳導(dǎo)系數(shù)高避免熱累積的金屬化陶瓷電鍍層,將金屬化陶瓷涂覆在織紗導(dǎo)向組件上,增加織紗導(dǎo)向組件的壽命、改善紡織業(yè)界現(xiàn)有的生產(chǎn)瓶頸、以提高質(zhì)量與產(chǎn)能。技術(shù)實(shí)現(xiàn)要素:有鑒于現(xiàn)有技術(shù)問題,本發(fā)明主要目的為提供一種涂覆復(fù)合金屬碳化物陶瓷電鍍層的織紗導(dǎo)向組件,組件基材可使用鐵質(zhì)基材制成的織紗導(dǎo)向組件、不銹鋼基材制成的織紗導(dǎo)向組件、鎳基材制成的織紗導(dǎo)向組件、塑料基材制成的織紗導(dǎo)向組件,或由其他金屬或金屬合金制成的織紗導(dǎo)向組件;其中,若該組件基材為不導(dǎo)電材質(zhì)如塑料、陶瓷、玻璃,則在該組件基材表面以電鍍或無(wú)電鍍涂覆一導(dǎo)電層,如涂覆一層鐵、銅、鉻、鎳、銀、金或其合金(例如使用無(wú)電電鍍鎳),均不受限。復(fù)合金屬碳化物陶瓷電鍍層系經(jīng)由電鍍形成非晶相碳化鉻結(jié)構(gòu)附著在該組件基材表面;該復(fù)合金屬碳化物陶瓷電鍍層為濕式電化學(xué)的電鍍方法,在組件基材上電鍍涂覆一層金屬化陶瓷(metallicceramic),為達(dá)到耐磨、耐腐蝕、良好導(dǎo)熱性及低摩擦系數(shù)的目的,該復(fù)合金屬碳化物陶瓷電鍍層為以碳化鉻基(ChromiumCarbidebase,CrCbase)為成份的金屬化陶瓷,系經(jīng)由電鍍形成一非晶相碳化鉻結(jié)構(gòu)(amorphoustypemicrostructureofCrC)附著在該組件基材表面的全部位置或一部分位置;該復(fù)合金屬碳化物陶瓷電鍍層成份為包含鉻元素(Cr)、碳元素(C)、氧元素(O)、由鉻-碳所形成的碳化鉻基的金屬化陶瓷。對(duì)于不限制的所形成的非晶相碳化鉻結(jié)構(gòu),為六碳化二十三鉻(Cr23C6)或三碳化七鉻(Cr7C3)之一或其組合;其中,該復(fù)合金屬碳化物陶瓷電鍍層碳元素的含量范圍為18~35At%。復(fù)合金屬碳化物陶瓷電鍍層中碳元素的含量是以原子數(shù)比例At%(atomicpercent),依據(jù)下列方程式所計(jì)算,其中,NC為單位體積中復(fù)合金屬碳化物陶瓷電鍍層中碳元素原子數(shù),Ntot為單位體積中復(fù)合金屬碳化物陶瓷電鍍層的總原子數(shù)。在耐磨耗與低摩擦系數(shù)特性上,該復(fù)合金屬碳化物陶瓷電鍍層的鉻-碳沉積的碳化鉻的非晶相碳化鉻結(jié)構(gòu)具有高硬度特點(diǎn),該涂覆復(fù)合金屬碳化物陶瓷電鍍層的織紗導(dǎo)向組件摩擦系數(shù)為0.45以下,摩擦系數(shù)系依據(jù)ASTMD3702-94以300牛頓荷重試驗(yàn);其表面硬度為750Hv以上、900Hv以下;其熱傳導(dǎo)系數(shù)為185W/(m·K)以上,熱傳導(dǎo)系數(shù)系在溫度300K依據(jù)ASTMC177試驗(yàn)。在厚度上,較佳的該復(fù)合金屬碳化物陶瓷電鍍層的厚度范圍在0.5μm至3.5μm之間;在以電鍍技術(shù)上,可調(diào)整使用操作條件可獲得比0.5μm更薄的鍍層,但在織紗導(dǎo)向組件的實(shí)用的耐久性上,以超過0.5μm為較適當(dāng);又以電鍍技術(shù)上,可調(diào)整使用操作條件可獲得比3.5μm更厚的鍍層,但在鍍層內(nèi)應(yīng)力產(chǎn)生的缺陷較少的考慮下,在織紗導(dǎo)向組件的實(shí)用與經(jīng)濟(jì)成本與附著力考慮上,以不超過3.5μm為較適當(dāng)。同樣的,經(jīng)長(zhǎng)期研究,在硬度上,較佳的該復(fù)合金屬碳化物陶瓷電鍍層的硬度范圍在750Hv至900Hv之間,經(jīng)實(shí)際測(cè)試,本發(fā)明的技術(shù)應(yīng)用于產(chǎn)品時(shí),與塑料綜片相比提高壽命40倍以上;當(dāng)超過900Hv的復(fù)合金屬碳化物陶瓷電鍍層涂覆在需要彎曲彈性的織紗導(dǎo)向組件上,因高硬度的電鍍層內(nèi)部應(yīng)力(stress)較大,將容易產(chǎn)生附著不良或脆裂;而低于750Hv則耐磨性不夠優(yōu)異,若與高磷含量的電鍍鎳的織紗導(dǎo)向組件相比壽命僅提高3~5倍。本發(fā)明另一主要目的在于提供一種以電化學(xué)制成復(fù)合金屬碳化物陶瓷電鍍層的織紗導(dǎo)向組件的方法,解決現(xiàn)有技術(shù)中織紗導(dǎo)向組件不耐磨耗或制程昂貴而無(wú)法大量生產(chǎn)等問題。包含下列步驟:S1:提供一織紗導(dǎo)向組件,該織紗導(dǎo)向組件的基材為一組件基材,該組件基材表面至少有一導(dǎo)電層;若該組件基材為導(dǎo)電材質(zhì)則具有該導(dǎo)電層,若該組件基材為不導(dǎo)電(如塑料)則于該組件基材表面以無(wú)電鍍或電鍍一層導(dǎo)電層或涂覆一層導(dǎo)電層;在實(shí)際應(yīng)用時(shí),該組件基材即為待電鍍的織紗導(dǎo)向組件或其一部份;S2:配置碳化鉻陶瓷電鍍液,該碳化鉻陶瓷電鍍液系包含:三價(jià)鉻主鹽、螯合劑、pH調(diào)節(jié)劑及帄整劑所形成的水溶液;先將三價(jià)鉻主鹽溶于液體中,再加入螯合劑、pH調(diào)節(jié)劑及帄整劑,并可進(jìn)一步再加入共沉積劑;三價(jià)鉻主鹽系提供三價(jià)鉻(Cr3+)離子與螯合劑產(chǎn)生螯合作用,pH調(diào)節(jié)劑作用在于穩(wěn)定該碳化鉻陶瓷電鍍液的電化學(xué)特性、當(dāng)產(chǎn)生電化學(xué)反應(yīng)時(shí)可維持電離子電鍍的效率,帄整劑作用在于使復(fù)合金屬碳化物陶瓷電鍍層堆積時(shí)降低鍍層應(yīng)力與產(chǎn)生電鍍層細(xì)致平滑;其中,三價(jià)鉻主鹽可選用硫酸系三價(jià)鉻主鹽、氯酸系三價(jià)鉻主鹽其一或其組合;其中,該硫酸系三價(jià)鉻主鹽系包含三價(jià)鉻(Cr3+)與硫酸根(SO42-)形成的化合物,如硫酸鉻(Cr2(SO4)3)、硫酸鉻銨(NH4Cr(SO4)2·12H2O)、硫酸鉻鉀(CrK(SO4)2·12H2O);該氯酸系三價(jià)鉻主鹽為三價(jià)鉻(Cr3+)與氯離子(Cl-)、過氯酸離子(ClO4-)兩者之一或其組合形成的化合物,如氯化鉻(CrCl3·6H2O)、過氯酸鉻(Cr(ClO4)3);該螯合劑包含甲酸、甲酸鹽、乙酸、乙酸鹽類其一或其組合,如甲酸(HCOOH)、甲酸銨(HCOONH4)、甲酸鈉(HCOONa)、乙酸(CH3COOH)、乙酸銨(CH3COONH4)、乙酸鈉(CH3COONa)、乙酸鉀(CH3COOK)之一或其組合;該pH調(diào)節(jié)劑包含硼酸鹽與銨鹽之組合,其中硼酸鹽選自于硼酸、四硼酸鈉(Na2B4O7.10H2O)、過硼酸鈉(NaBO3.NH2O)其一或其組合;其中銨鹽選自于硝酸銨(NH4NO3)、硫酸銨((NH4)2SO4)、氯化銨(NH4Cl)、硫酸氫銨(NH4HSO4)其一或其組合;該帄整劑包含胺或酰胺,其中胺或酰胺選自于乙二胺(C2H4(NH2)2)、二甲胺((CH3)2NH)、丙胺(C3H9N)、乙酰胺(CH3CONH2)、丙烯酰胺(CH2=CHCONH2)、苯甲酰胺(C6H5CONH2)其一或其組合。為能電鍍出具有需求功能的電鍍層,三價(jià)鉻主鹽、螯合劑及pH調(diào)節(jié)劑應(yīng)有適當(dāng)?shù)呐浞奖壤?,較佳的,該碳化鉻陶瓷電鍍液中該三價(jià)鉻主鹽之三價(jià)鉻(Cr3+)摩爾濃度為1.5~5.0M、與該螯合劑之碳元素摩爾濃度為0.8~1.2:1、與該pH調(diào)節(jié)劑之硼與銨合計(jì)摩爾濃度為1.7~4.5比1;S3:以電鍍方式,將該組件基材置為陰極,并浸入于碳化鉻陶瓷電鍍液中;在一定電鍍溫度條件與一定電流密度條件下進(jìn)行電鍍,電鍍時(shí),同時(shí)攪拌該碳化鉻陶瓷電鍍液;經(jīng)預(yù)定時(shí)間后,在該組件基材的導(dǎo)電層表面上形成該復(fù)合金屬碳化物陶瓷電鍍層;該電流密度條件范圍為5A/dm2至30A/dm2之間;其中,該電鍍溫度條件為操作設(shè)定溫度為23℃以下,較佳者電鍍溫度條件為所設(shè)定溫度之±3℃以內(nèi)。S4:將電鍍后的織紗導(dǎo)向組件置入一氣氛烘箱中,該氣氛烘箱中系為真空、填充干燥空氣或填充氮?dú)馄湟唬^佳者,以填充富含氮?dú)獾臍怏w,以利水氣排出。氣氛烘箱以一定脫水溫度條件進(jìn)行烘烤,該脫水溫度條件為165℃(含)以下,于該組件基材上形成復(fù)合金屬碳化物陶瓷電鍍層;所形成的復(fù)合金屬碳化物陶瓷電鍍層為非晶相碳化鉻結(jié)構(gòu)附著在該組件基材表面的全部或一部分,該非晶相碳化鉻結(jié)構(gòu)至少包括六碳化二十三金屬(M23C6)或三碳化七金屬(M7C3)之一或其組合,其中金屬M(fèi)為鉻;該復(fù)合金屬碳化物陶瓷電鍍層之碳元素含量范圍18~35At%、熱傳導(dǎo)系數(shù)為185W/(m·K)以上。更進(jìn)一步,碳化鉻陶瓷電鍍液可添加入一共沉積劑,該共沉積劑可選用下列群組之一、所形成的復(fù)合金屬碳化物陶瓷電鍍層分別如下:(1)該共沉積劑包含第一群組金屬鹽,第一群組金屬鹽可為硝酸鈷(Co(NO3)2·6H2O)、硫酸鈷(CoSO4·7H2O)、氯化鈷(CoCl2)或氯酸鈷(Co(ClO3)2)之一或其組合;該三價(jià)鉻主鹽之三價(jià)鉻(Cr3+)摩爾濃度與該第一群組金屬鹽之鈷(Co2+)摩爾濃度為15~30比1;該復(fù)合金屬碳化物陶瓷電鍍層系為非晶相碳化鉻鈷結(jié)構(gòu)附著在該組件基材表面之全部或一部分,該非晶相碳化鉻結(jié)構(gòu)至少包括鈷元素與六碳化二十三金屬(M23C6)或三碳化七金屬(M7C3)之一或其組合,其中金屬M(fèi)為鉻鈷(Co,Cr)。當(dāng)加入第一群組金屬鹽(鈷鹽)為共沉積劑,該復(fù)合金屬碳化物陶瓷電鍍層之成份進(jìn)一步包含非晶相碳化鉻鈷結(jié)構(gòu);其中,非晶相碳化鉻鈷結(jié)構(gòu)至少包括鈷元素與六碳化二十三鉻鈷((Co,Cr)23C6)或三碳化七鉻鈷((Co,Cr)7C3)之一或其組合;該復(fù)合金屬碳化物陶瓷電鍍層碳元素之含量范圍為12~20%、鉻元素之含量至少35At%以上、鈷元素之含量范圍為鉻元素之含量之0.65~0.76倍;該涂覆復(fù)合金屬碳化物陶瓷電鍍層之織紗導(dǎo)向組件動(dòng)摩擦系數(shù)為0.45以下;其中,該復(fù)合金屬碳化物陶瓷電鍍層,其表面硬度為800Hv以上。(2))該共沉積劑包含第二群組金屬鹽,該第二群組金屬鹽可為鐵鹽,選自于硫酸亞鐵(FeSO4)、硫酸亞鐵銨((NH4)2Fe(SO4)2.6H2O)或氯化亞鐵(FeCl2)之一或其組合;該三價(jià)鉻主鹽之三價(jià)鉻(Cr3+)摩爾濃度與該第二群組金屬鹽之亞鐵(Fe2+)或鐵(Fe3+)摩爾濃度為10~20比1;該復(fù)合金屬碳化物陶瓷電鍍層系為非晶相碳化鉻鐵結(jié)構(gòu)附著在該組件基材表面之全部或一部分,該非晶相碳化鉻結(jié)構(gòu)至少包括鐵元素及六碳化二十三金屬(M23C6)或三碳化七金屬(M7C3)之一或其組合,其中金屬M(fèi)為鉻鐵(Fe,Cr)。當(dāng)加入第二群組金屬鹽(鐵鹽)為共沉積劑,其中,該復(fù)合金屬碳化物陶瓷電鍍層之成份進(jìn)一步包含非晶相碳化鉻鐵結(jié)構(gòu);其中,非晶相碳化鉻鐵結(jié)構(gòu)至少包括鐵元素與六碳化二十三鉻鐵((Fe,Cr)23C6)或三碳化七鉻鐵((Fe,Cr)7C3)之一或其組合;該復(fù)合金屬碳化物陶瓷電鍍層碳元素之含量范圍為12~18%、鉻元素之含量至少35At%以上、鐵元素之含量范圍為鉻元素之含量之0.3~0.5倍;該涂覆復(fù)合金屬碳化物陶瓷電鍍層之織紗導(dǎo)向組件動(dòng)摩擦系數(shù)為0.45以下;其中,該復(fù)合金屬碳化物陶瓷電鍍層,其表面硬度為830Hv以上。在此特別說(shuō)明,前述的三價(jià)鉻主鹽、螯合劑、pH調(diào)節(jié)劑、帄整劑與共沉積劑所列舉的各化學(xué)藥品并非限制性,對(duì)于同屬三價(jià)鉻鹽、甲酸鹽、乙酸鹽、硼酸鹽、銨鹽、胺或酰胺、金屬鹽之其他化學(xué)藥品,經(jīng)適當(dāng)組合調(diào)整后若可達(dá)相同功能,都在本發(fā)明的范圍之內(nèi)。如上所述,依本發(fā)明的一種涂覆復(fù)合金屬碳化物陶瓷電鍍層之織紗導(dǎo)向組件,其可具有一或多個(gè)下述優(yōu)點(diǎn):(1)本發(fā)明的涂覆復(fù)合金屬碳化物陶瓷電鍍層的織紗導(dǎo)向組件,該織紗導(dǎo)向組件可應(yīng)用于各種天然纖維或合成纖維,或軟質(zhì)纖維或硬質(zhì)纖維,如棉、人造絲、聚酯、聚丙烯、聚酰胺6、聚酰胺66、滌綸(如Ekslive)、羊毛、丙烯酸纖維、彈性纖維等。(2)涂覆復(fù)合金屬碳化物陶瓷電鍍層的織紗導(dǎo)向組件可在任何鐵系基材、不銹鋼基材、鎳系基材、塑料基材先涂覆上鐵系或鎳系之中介層的織紗導(dǎo)向組件表面,形成高含碳量的復(fù)合金屬碳化物陶瓷電鍍層,通過碳化物陶瓷化的非晶向結(jié)構(gòu)(陶瓷特性)與高的含碳量,可提高該電鍍層的硬度、導(dǎo)熱性與耐蝕性,達(dá)到耐腐蝕與耐磨的紡織組件的需求。(3)本發(fā)明的涂覆復(fù)合金屬碳化物陶瓷電鍍層的織紗導(dǎo)向組件,因復(fù)合金屬碳化物陶瓷電鍍層亦具有金屬的特性,具有良好的導(dǎo)熱性與低的摩擦系數(shù),可將織紗導(dǎo)向組件快速均熱、避免熱累積(熱量可以快速沿軸向方向或徑向方向傳導(dǎo)出去),且藉由碳化物陶瓷化非晶向結(jié)構(gòu)的高硬度特性,使織紗導(dǎo)向組件可以增長(zhǎng)使用壽命。(4)本發(fā)明的涂覆復(fù)合金屬碳化物陶瓷電鍍層的織紗導(dǎo)向組件,在復(fù)合金屬碳化物陶瓷電鍍層電鍍時(shí),可添加鈷鹽或鐵鹽,使復(fù)合金屬碳化物陶瓷電鍍層的成份上可含有碳化鉻鈷(Cr-Co)之陶瓷化、碳化鉻鐵合金(Cr-Fe)之陶瓷化,可提高復(fù)合金屬碳化物陶瓷電鍍層的表面硬度,增加涂覆復(fù)合金屬碳化物陶瓷電鍍層之織紗導(dǎo)向組件的使用壽命。(5)本發(fā)明的涂覆復(fù)合金屬碳化物陶瓷電鍍層的織紗導(dǎo)向組件,系采用三價(jià)鉻電鍍,其電鍍液及廢水為三價(jià)鉻不含六價(jià)鉻,三價(jià)鉻毒性遠(yuǎn)低于六價(jià)鉻,可減少環(huán)境的負(fù)擔(dān),為潔凈的產(chǎn)品并符合RoHS、REACH要求。附圖說(shuō)明為了更清楚地說(shuō)明本發(fā)明具體實(shí)施方式或現(xiàn)有技術(shù)中的技術(shù)方案,下面將對(duì)具體實(shí)施方式或現(xiàn)有技術(shù)描述中所需要使用的附圖作簡(jiǎn)單地介紹,顯而易見地,下面描述中的附圖是本發(fā)明的一些實(shí)施方式,對(duì)于本領(lǐng)域普通技術(shù)人員來(lái)講,在不付出創(chuàng)造性勞動(dòng)的前提下,還可以根據(jù)這些附圖獲得其他的附圖。圖1為現(xiàn)有技術(shù)中織紗導(dǎo)向組件結(jié)構(gòu)的示意圖;圖2為本發(fā)明的涂覆復(fù)合金屬碳化物陶瓷電鍍層的織紗導(dǎo)向組件第一組實(shí)施例的示意圖;圖3為本發(fā)明的涂覆復(fù)合金屬碳化物陶瓷電鍍層的織紗導(dǎo)向組件第二組實(shí)施例的示意圖;圖4為本發(fā)明的涂覆復(fù)合金屬碳化物陶瓷電鍍層的織紗導(dǎo)向組件第三組實(shí)施例的示意圖;圖5為本發(fā)明的涂覆復(fù)合金屬碳化物陶瓷電鍍層的織紗導(dǎo)向組件第四組實(shí)施例的示意圖;圖6為本發(fā)明的涂覆復(fù)合金屬碳化物陶瓷電鍍層之織紗導(dǎo)向組件第五組實(shí)施例的示意圖;圖7為本發(fā)明的涂覆復(fù)合金屬碳化物陶瓷電鍍層的織紗導(dǎo)向組件第六組實(shí)施例的示意圖;圖8為本發(fā)明的涂覆復(fù)合金屬碳化物陶瓷電鍍層的制造方法步驟流程圖;圖9為本發(fā)明的復(fù)合金屬碳化物陶瓷電鍍層的織紗導(dǎo)向組件第一組實(shí)施例I的XPS分析照片;圖10為本發(fā)明的涂覆復(fù)合金屬碳化物陶瓷電鍍層的織紗導(dǎo)向組件第四組實(shí)施例I之SEM表面形貌照片;圖11為本發(fā)明的涂覆復(fù)合金屬碳化物陶瓷電鍍層的織紗導(dǎo)向組件第六組實(shí)施例II之SEM表面形貌照片。附圖標(biāo)記:1:織紗導(dǎo)向組件,11:綜片,111:綜眼,112:綜片鉤,12:筘片,13:申克片,14:鋼筘,15:停經(jīng)片,16:紡針,2:組件基材,3:復(fù)合金屬碳化物陶瓷電鍍層,31:碳元素,32:鉻元素,33:鈷元素,34:鐵元素,91:不銹鋼停經(jīng)片,92:電鍍鎳耐磨層,93:電鍍鉻層。具體實(shí)施方式下面將結(jié)合附圖和具體實(shí)施方式對(duì)本發(fā)明的技術(shù)方案進(jìn)行清楚、完整地描述,但是本領(lǐng)域技術(shù)人員將會(huì)理解,下列所描述的實(shí)施例是本發(fā)明一部分實(shí)施例,而不是全部的實(shí)施例,僅用于說(shuō)明本發(fā)明,而不應(yīng)視為限制本發(fā)明的范圍?;诒景l(fā)明中的實(shí)施例,本領(lǐng)域普通技術(shù)人員在沒有做出創(chuàng)造性勞動(dòng)前提下所獲得的所有其他實(shí)施例,都屬于本發(fā)明保護(hù)的范圍。實(shí)施例中未注明具體條件者,按照常規(guī)條件或制造商建議的條件進(jìn)行。所用試劑或儀器未注明生產(chǎn)廠商者,均為可以通過市售購(gòu)買獲得的常規(guī)產(chǎn)品。本發(fā)明涂覆復(fù)合金屬碳化物陶瓷電鍍層的織紗導(dǎo)向組件為使用電化學(xué)電鍍的方法制成,說(shuō)明如下:參閱圖2,為本發(fā)明涂覆復(fù)合金屬碳化物陶瓷電鍍層的織紗導(dǎo)向組件之示意圖;圖中,織紗導(dǎo)向組件1系如綜片11,綜片11通常為不銹鋼、合金鋼或中高碳鋼薄片所制成,即組件基材2為不銹鋼、合金鋼或中高碳鋼,綜片11的兩端為綜片鉤112,綜片鉤112系鉤掛于紡織機(jī)上,織紗則穿過綜眼111,紡織時(shí)綜片11會(huì)上下移動(dòng)讓經(jīng)紗通過,緯紗則快速通過綜眼111,對(duì)綜眼111產(chǎn)生快速摩擦。綜片11的全部或至少綜眼111系利用本發(fā)明涂覆復(fù)合金屬碳化物陶瓷電鍍層的織紗導(dǎo)向組件所制成,系在組件基材2先涂覆一層導(dǎo)電層,再于導(dǎo)電層表面以電鍍覆蓋一層復(fù)合金屬碳化物陶瓷電鍍層3,復(fù)合金屬碳化物陶瓷電鍍層3成分分析系由碳元素31與鉻元素32形成非晶相的Cr-C結(jié)構(gòu)。參閱圖8,本發(fā)明涂覆復(fù)合金屬碳化物陶瓷電鍍層的織紗導(dǎo)向組件制作方法的示意圖,主要利用電化學(xué)反應(yīng)的特點(diǎn),將組件基材2置為陰極,組件基材2為包含有導(dǎo)電層,若該組件基材2為金屬則具有導(dǎo)電層,若該組件基材2為非金屬則于該組件基材2表面以無(wú)電鍍或涂覆一導(dǎo)電層,在實(shí)際應(yīng)用時(shí),該組件基材2即為待電鍍的工件;在組件基材2的導(dǎo)電層表面,使碳化鉻陶瓷電鍍液中的碳離子在電場(chǎng)的電化學(xué)反應(yīng)與鉻離子在陰極表面上發(fā)生鉻-碳之還原成核反應(yīng),而因組件基材2與碳化鉻陶瓷電鍍液之間存在的微小間隙內(nèi),碳化鉻陶瓷電鍍液濃度差會(huì)產(chǎn)生鉻-碳的擴(kuò)散作用,使鉻-碳會(huì)自然地生長(zhǎng),而形成復(fù)合金屬碳化物陶瓷電鍍層3。本發(fā)明以下實(shí)施例使用的組件基材2可使用具有導(dǎo)電性的金屬材料組件基材2、導(dǎo)電陶瓷組件基材2,或涂覆有導(dǎo)電層的非金屬組件基材2等,在后續(xù)的實(shí)施例為利于了解,系使用鐵質(zhì)組件基材2(包含高碳鋼材料、不銹鋼材料制成的織紗導(dǎo)向組件的組件基材2),此為實(shí)施例實(shí)行的方式之一,但不受限。本發(fā)明形成復(fù)合金屬碳化物陶瓷電鍍層3的碳化鉻陶瓷電鍍液系包含:三價(jià)鉻主鹽、螯合劑、pH調(diào)節(jié)劑及帄整劑所形成之水溶液;三價(jià)鉻主鹽的來(lái)源可為硫酸系三價(jià)鉻主鹽或氯酸系三價(jià)鉻主鹽之水溶性鹽;硫酸系三價(jià)鉻主鹽如硫酸鉻(Cr2(SO4)3)、硫酸鉻銨(NH4Cr(SO4)2·12H2O)、硫酸鉻鉀(CrK(SO4)2·12H2O)等之一或其組合,氯酸系三價(jià)鉻鹽如氯化鉻(CrCl3·6H2O)、過氯酸鉻(Cr(ClO4)3)等之一或其組合;不為所限。為進(jìn)行碳化鉻陶瓷電鍍液的螯合作用,本發(fā)明之螯合劑可選用甲酸(HCOOH)、乙酸(CH3COOH)或其鹽類,如甲酸(HCOOH)、甲酸銨(HCOONH4)、甲酸鈉(HCOONa)、乙酸(CH3COOH)、乙酸銨(CH3COONH4)、乙酸鈉(CH3COONa)、乙酸鉀(CH3COOK)之一或其組合,當(dāng)提高螯合劑的相對(duì)濃度時(shí),可增加復(fù)合金屬碳化物陶瓷電鍍層3的含碳量。碳化鉻陶瓷電鍍液之pH調(diào)節(jié)劑系作為調(diào)整電鍍液的用途,通??墒褂媒怆x度較低的鹽類,使其兼具有緩沖劑(bufferagent)的功能,常用的添加劑為無(wú)機(jī)酸的鹽類、銨鹽類、硼酸或其鹽類等,如硼酸鹽系選自于硼酸(H3BO3)、四硼酸鈉(Na2B4O7.10H2O)、過硼酸鈉(NaBO3.NH2O)其一或其組合;其中銨鹽系選自于硝酸銨(NH4NO3)、硫酸銨((NH4)2SO4)、氯化銨(NH4Cl)、硫酸氫銨(NH4HSO4)其一或其組合,當(dāng)提高pH調(diào)節(jié)劑的相對(duì)濃度時(shí),可提高復(fù)合金屬碳化物陶瓷電鍍層3的耐蝕性。為增加復(fù)合金屬碳化物陶瓷電鍍層3的平整性與平滑性,可加入帄整劑,該帄整劑可選用胺或酰胺,其中胺或酰胺可選自于乙二胺(C2H4(NH2)2)、二甲胺((CH3)2NH)、丙胺(C3H9N)、乙酰胺(CH3CONH2)、丙烯酰胺(CH2=CHCONH2)、苯甲酰胺(C6H5CONH2)其一或其組合。對(duì)于不限制性的配方組成與操作條件,本發(fā)明的碳化鉻陶瓷電鍍液的配方實(shí)施例如表1。表1、碳化鉻陶瓷電鍍液組成表以上濃度以M(mole/L)表示系以每升碳化鉻陶瓷電鍍液中該純物質(zhì)之摩爾數(shù)計(jì)算,其不含不純物之質(zhì)量;以下皆同。請(qǐng)參見圖2,圖2為本發(fā)明的第一組實(shí)施例的示意圖,首先提供組件基材2,此組件基材2之綜片材料可使用鐵質(zhì)基材制成、不銹鋼基材制成、銅基材制成、鎳基材制成,或由其上述金屬合金制成,通常采用沖制成型,但塑料材質(zhì)則通常使用射出成型制成。對(duì)于不同應(yīng)用,可先在前述的組件基材2上,再以先電鍍鍍上一層中介層(圖上未繪示),該中介層可為鐵、銅、鎳、鎳磷、貴金屬或其合金等,鍍上中介層的組件基材2僅為表面改質(zhì),仍統(tǒng)稱為組件基材2;在此不特別予以區(qū)分。根據(jù)不同制成的組件基材2(或含中介層),配制電鍍制程之脫脂溶液、酸洗溶液、碳化鉻陶瓷電鍍液;脫脂溶液的目的為去除組件基材2表面上的油脂,可采用有機(jī)溶劑、中性脫脂劑、堿性脫脂劑或酸性脫脂劑;酸洗溶液的目的為去除組件基材2表面上的氧化物并使組件基材2的表面活化,可采用稀硫酸、稀鹽酸、稀硝酸、稀磷酸或其混合之酸液;碳化鉻陶瓷電鍍液則另說(shuō)明如后;在此說(shuō)明,對(duì)于不同的組件基材2表面狀況,脫脂與酸洗并非必要的處理程序。接著,以電鍍的方法在組件基材2表面的全部或一部份上形成復(fù)合金屬碳化物陶瓷電鍍層3,以制成織紗導(dǎo)向組件1。由于系采用前述的碳化鉻陶瓷電鍍液,在適當(dāng)操作條件下,可形成碳化鉻基之復(fù)合金屬碳化物陶瓷電鍍層3;在電鍍之前,對(duì)于不電鍍復(fù)合金屬碳化物陶瓷電鍍層3的部份,則可使用防鍍漆、防鍍蓋、防鍍?nèi)裙ぞ?,將不電鍍?fù)合金屬碳化物陶瓷電鍍層3的部份先行遮蔽。在后續(xù)的實(shí)施例中,經(jīng)分析后,所形成的復(fù)合金屬碳化物陶瓷電鍍層3系經(jīng)由電鍍形成非晶相碳化鉻結(jié)構(gòu),附著在組件基材2表面,復(fù)合金屬碳化物陶瓷電鍍層3成份系由主要包含鉻元素32、碳元素31、氧元素等所組成,即復(fù)合金屬碳化物陶瓷電鍍層3的由鉻元素32、碳元素31形成非晶相碳化鉻結(jié)構(gòu),至少包括六碳化二十三鉻(Cr23C6)或三碳化七鉻(Cr7C3)之一或其組合。復(fù)合金屬碳化物陶瓷電鍍層3為非晶相碳化鉻結(jié)構(gòu)附著,為了達(dá)到鍍層硬度高、附著力好、耐磨性能好等特性要求,復(fù)合金屬碳化物陶瓷電鍍層3之碳元素31含量為18~35At%為較佳,碳元素31含量低則復(fù)合金屬碳化物陶瓷電鍍層3硬度較低,碳元素31含量高則復(fù)合金屬碳化物陶瓷電鍍層3硬度相對(duì)較高。在此說(shuō)明,現(xiàn)有技術(shù)中,如臺(tái)灣專利TWI441954、TWI441961、TWI533526及中國(guó)專利CN103726091雖亦使用三價(jià)鉻主鹽、螯合劑、pH調(diào)節(jié)劑、共沉積劑等構(gòu)成電鍍液,其主要的目的在于制造出高導(dǎo)電性、高耐蝕性或高疏水性的電鍍層,應(yīng)用這些專利所公開的技術(shù)無(wú)法制造出高表面硬度高、光滑、動(dòng)摩擦系數(shù)很小、熱傳導(dǎo)系數(shù)高的電鍍層,而因本發(fā)明的制造方法的組成成份、濃度或操作條件范圍等與前述現(xiàn)有技術(shù)不相同,也無(wú)法由這些現(xiàn)有的方法可以簡(jiǎn)單輕易地調(diào)整而導(dǎo)出本發(fā)明制造方法的技術(shù)。又因本發(fā)明制造方法與現(xiàn)有的方法在產(chǎn)品的應(yīng)用目的、電鍍層的結(jié)構(gòu)特性不相同,由于電鍍液的組成及操作條件不同,因此決定了本發(fā)明制造方法所產(chǎn)生的電鍍層的結(jié)構(gòu)特性與不同性能。本發(fā)明制造方法除了電鍍液配方組成不同與增加了帄整劑與共沉積劑(組件不同)使電化學(xué)反應(yīng)不同(反應(yīng)功能不同)而產(chǎn)生不同的效果外,更也因脫水烘干的技術(shù)使電鍍層穩(wěn)定而平滑降低摩擦系數(shù)。再者,通過帄整劑的選用,對(duì)于碳元素的生成略為抑制,相較于前述公開的專利技術(shù)中電鍍層含有二碳化三鉻(Cr3C2),通過二碳化三鉻(Cr3C2)提高了電鍍層的含碳量;但本發(fā)明目的之一對(duì)于導(dǎo)向組件不適于偏高的較高的含碳量,雖然較高的含碳量其硬度也較高,但較高的含碳量(電鍍層應(yīng)力較高)在導(dǎo)向組件反復(fù)彈性作動(dòng)時(shí),電鍍層容易破裂,因此本發(fā)明系在復(fù)合金屬碳化物陶瓷電鍍層3的非晶相碳化鉻結(jié)構(gòu)中降低二碳化三鉻(Cr3C2)的含量,以保有較低的內(nèi)應(yīng)力??椉唽?dǎo)向組件在高速磨耗的行為上,因快速磨擦?xí)a(chǎn)生熱及熱累積,熱累積會(huì)造成深切凹口(depthofcutnotching),因此如何將產(chǎn)生的熱快速傳導(dǎo)出去,避免熱累積產(chǎn)生,將可提高織紗導(dǎo)向組件的壽命。本發(fā)明的涂覆復(fù)合金屬碳化物陶瓷電鍍層之織紗導(dǎo)向組件1,其熱傳導(dǎo)系數(shù)為185W/(m·K)以上,相對(duì)于鋁的熱傳導(dǎo)系數(shù)為237W/(m·K)、鐵為80.4W/(m·K)、玻璃為1.38W/(m·K)、硅晶圓為157W/(m·K)、金為318W/(m·K)、鉆石為2300W/(m·K)、不銹鋼為18W/(m·K);本發(fā)明的涂覆復(fù)合金屬碳化物陶瓷電鍍層之織紗導(dǎo)向組件1的熱傳導(dǎo)系數(shù)雖比金為低,相當(dāng)于鋁材質(zhì)的熱傳導(dǎo)系數(shù),但遠(yuǎn)高于不銹鋼的熱傳導(dǎo)系數(shù),因此本發(fā)明的涂覆復(fù)合金屬碳化物陶瓷電鍍層的織紗導(dǎo)向組件1的耐用壽命高于傳統(tǒng)不銹鋼制的織紗導(dǎo)向組件。對(duì)于不同的應(yīng)用,可在碳化鉻陶瓷電鍍液中添加第一群組金屬鹽,第一群組金屬鹽為鈷鹽,選自于硝酸鈷(Co(NO3)2·6H2O)、硫酸鈷(CoSO4·7H2O)、氯化鈷(CoCl2)或氯酸鈷(Co(ClO3)2)之一或其組合;配方如表2;經(jīng)電鍍形成的復(fù)合金屬碳化物陶瓷電鍍層3,系為非晶相碳化鉻鈷結(jié)構(gòu)附著在該組件基材2表面之全部或一部分,非晶相碳化鉻鈷結(jié)構(gòu)至少包括鈷元素與六碳化二十三鉻鈷((Co,Cr)23C6)或三碳化七鉻鈷((Co,Cr)7C3)之一或其組合;表2、碳化鉻陶瓷電鍍液組成表對(duì)于不同的應(yīng)用,可在碳化鉻陶瓷電鍍液中添加第二群組金屬鹽,第一群組金屬鹽為鐵鹽,選自于硫酸亞鐵(FeSO4)、硫酸亞鐵銨((NH4)2Fe(SO4)2.6H2O)或氯化亞鐵(FeCl2)之一或其組合;配方如表3;經(jīng)電鍍形成的復(fù)合金屬碳化物陶瓷電鍍層3,系為非晶相碳化鉻鐵結(jié)構(gòu)附著在該組件基材2表面之全部或一部分,非晶相碳化鉻鐵結(jié)構(gòu)至少包括鐵元素與六碳化二十三鉻鐵((Fe,Cr)23C6)或三碳化七鉻鐵((Fe,Cr)7C3)之一或其組合;表3、碳化鉻陶瓷電鍍液組成表下述實(shí)施例為本發(fā)明的涂覆復(fù)合金屬碳化物陶瓷電鍍層的織紗導(dǎo)向組件的各種實(shí)施例,但實(shí)際上本發(fā)明不以此為限。<第一組實(shí)施例>如圖2,為本組實(shí)施例的涂覆復(fù)合金屬碳化物陶瓷電鍍層之織紗導(dǎo)向組件1的示意圖,在本組實(shí)施例的碳化鉻陶瓷電鍍液系使用表1之配方,但不以此為限。以本發(fā)明的電鍍方法在綜片11的組件基材2表面的全部形成復(fù)合金屬碳化物陶瓷電鍍層3,制成綜片11,所形成的復(fù)合金屬碳化物陶瓷電鍍層3系經(jīng)由電鍍形成非晶相碳化鉻結(jié)構(gòu),附著在組件基材2表面,復(fù)合金屬碳化物陶瓷電鍍層3成份系由主要包含鉻元素32、碳元素31、氧元素等所組成,即復(fù)合金屬碳化物陶瓷電鍍層3由鉻元素32、碳元素31形成非晶相碳化鉻結(jié)構(gòu),至少包括六碳化二十三鉻(Cr23C6)或三碳化七鉻(Cr7C3)之一或其組合。請(qǐng)參見圖9,為本組實(shí)施例第I實(shí)施例復(fù)合金屬碳化物陶瓷電鍍層的XPS(電子能譜儀)分析照片。表4為本組實(shí)施例的各實(shí)施例的操作條件與結(jié)果表注,因綜片面積不足,摩擦系數(shù)系在相同組件基材與相同電鍍條件的試片上,電鍍厚度為30μm以上依據(jù)ASTMD3702-94以300牛頓荷重試驗(yàn);熱傳導(dǎo)系數(shù)系在厚度為表中厚度的試片上,系依據(jù)ASTMC177試驗(yàn)量測(cè)表面兩點(diǎn)距離的熱傳導(dǎo)系數(shù)。在本第一組實(shí)施例,對(duì)于第I組樣品進(jìn)行抽樣及測(cè)試結(jié)果的范圍如下表5,在此特別說(shuō)明,表5為第I組抽樣樣品的測(cè)試結(jié)果,其測(cè)試結(jié)果為非限制性的。表5、第I組抽樣樣品的測(cè)試結(jié)果<第二組實(shí)施例>如圖3,為本組實(shí)施例的涂覆復(fù)合金屬碳化物陶瓷電鍍層的織紗導(dǎo)向組件1的示意圖,系以停經(jīng)片15為實(shí)施例,在本組實(shí)施例的碳化鉻陶瓷電鍍液系使用表1的配方,在此不再重復(fù)列出。本組實(shí)施例的涂覆復(fù)合金屬碳化物陶瓷電鍍層3之織紗導(dǎo)向組件1,系經(jīng)由電鍍形成復(fù)合金屬碳化物陶瓷電鍍層3附著在組件基材2上,制成停經(jīng)片15,所形成的復(fù)合金屬碳化物陶瓷電鍍層3系經(jīng)由電鍍形成非晶相碳化鉻結(jié)構(gòu),附著在組件基材2表面,復(fù)合金屬碳化物陶瓷電鍍層3成份系由主要包含鉻元素32、碳元素31、氧元素等所組成,即復(fù)合金屬碳化物陶瓷電鍍層3由鉻元素32、碳元素31形成非晶相碳化鉻結(jié)構(gòu)。表6為本組實(shí)施例的各實(shí)施例的操作條件與結(jié)果表注,因停經(jīng)片面積不足,摩擦系數(shù)系在相同組件基材與相同電鍍條件的試片上,電鍍厚度為30μm以上依據(jù)ASTMD3702-94以300牛頓荷重試驗(yàn);熱傳導(dǎo)系數(shù)系在厚度為表中厚度的試片上,系依據(jù)ASTMC177試驗(yàn)量測(cè)表面兩點(diǎn)距離的熱傳導(dǎo)系數(shù)。<第三組實(shí)施例>如圖4,為本組實(shí)施例的涂覆復(fù)合金屬碳化物陶瓷電鍍層的織紗導(dǎo)向組件1的示意圖,系以紡針16為實(shí)施例,在本組實(shí)施例的碳化鉻陶瓷電鍍液系使用表1之配方,在此不再重復(fù)列出。本組實(shí)施例之涂覆復(fù)合金屬碳化物陶瓷電鍍層3之織紗導(dǎo)向組件1,系經(jīng)由電鍍形成復(fù)合金屬碳化物陶瓷電鍍層3附著在組件基材2上,制成紡針16,所形成的復(fù)合金屬碳化物陶瓷電鍍層3系經(jīng)由電鍍形成非晶相碳化鉻結(jié)構(gòu),附著在組件基材2表面,復(fù)合金屬碳化物陶瓷電鍍層3成份系由主要包含鉻元素32、碳元素31、氧元素等所組成,即復(fù)合金屬碳化物陶瓷電鍍層3由鉻元素32、碳元素31形成非晶相碳化鉻結(jié)構(gòu)。表7為本組實(shí)施例之各實(shí)施例之操作條件與結(jié)果表注,因紡針面積不足,摩擦系數(shù)系在相同組件基材與相同電鍍條件的試片上,電鍍厚度為30μm以上依據(jù)ASTMD3702-94以300牛頓荷重試驗(yàn);熱傳導(dǎo)系數(shù)系在厚度為表中厚度的試片上,系依據(jù)ASTMC177試驗(yàn)量測(cè)表面兩點(diǎn)距離的熱傳導(dǎo)系數(shù)。<第四組實(shí)施例>如圖5,系本組實(shí)施例的涂覆復(fù)合金屬碳化物陶瓷電鍍層的織紗導(dǎo)向組件1的示意圖,系以鋼筘14為實(shí)施例,在本組實(shí)施例的碳化鉻陶瓷電鍍液系使用表2之配方,在此不再重復(fù)列出。本組實(shí)施例的涂覆復(fù)合金屬碳化物陶瓷電鍍層3的織紗導(dǎo)向組件1,系經(jīng)由電鍍形成復(fù)合金屬碳化物陶瓷電鍍層3附著在鋼筘14的鋼絲的組件基材2上,所形成的復(fù)合金屬碳化物陶瓷電鍍層3系經(jīng)由電鍍形成非晶相碳化鉻結(jié)構(gòu),附著在組件基材2表面,復(fù)合金屬碳化物陶瓷電鍍層3成份系由主要包含鉻元素32、碳元素31、鈷元素33、氧元素等所組成,即復(fù)合金屬碳化物陶瓷電鍍層3由鉻元素32、碳元素31、鈷元素33形成非晶相碳化鉻結(jié)構(gòu)。非晶相碳化鉻鈷結(jié)構(gòu)包括鈷元素與六碳化二十三鉻鈷((Co,Cr)23C6)或三碳化七鉻鈷((Co,Cr)7C3)。表8中,實(shí)施例I的SEM(掃描式電子顯微鏡)表面形貌照片參見圖10。表8為本組實(shí)施例之各實(shí)施例之操作條件與結(jié)果表注,因鋼筘面積不足,摩擦系數(shù)系在相同組件基材與相同電鍍條件的試片上,電鍍厚度為30μm以上依據(jù)ASTMD3702-94以300牛頓荷重試驗(yàn);熱傳導(dǎo)系數(shù)系在厚度為表中厚度的試片上,系依據(jù)ASTMC177試驗(yàn)量測(cè)表面兩點(diǎn)距離的熱傳導(dǎo)系數(shù)。<第五組實(shí)施例>如圖6,為本組實(shí)施例的涂覆復(fù)合金屬碳化物陶瓷電鍍層的織紗導(dǎo)向組件1的示意圖,系以筘片12為實(shí)施例,在本組實(shí)施例的碳化鉻陶瓷電鍍液系使用表2的配方,在此不再重復(fù)列出。本組實(shí)施例的涂覆復(fù)合金屬碳化物陶瓷電鍍層3的織紗導(dǎo)向組件1,系經(jīng)由電鍍形成復(fù)合金屬碳化物陶瓷電鍍層3附著在筘片12的組件基材2上,所形成的復(fù)合金屬碳化物陶瓷電鍍層3系經(jīng)由電鍍形成非晶相碳化鉻結(jié)構(gòu),附著在組件基材2表面,復(fù)合金屬碳化物陶瓷電鍍層3成份系由主要包含鉻元素32、碳元素31、鈷元素33、氧元素等所組成,即復(fù)合金屬碳化物陶瓷電鍍層3由鉻元素32、碳元素31、鈷元素33形成非晶相碳化鉻結(jié)構(gòu)。非晶相碳化鉻鈷結(jié)構(gòu)包括鈷元素與六碳化二十三鉻鈷((Co,Cr)23C6)或三碳化七鉻鈷((Co,Cr)7C3)。表9為本組實(shí)施例之各實(shí)施例之操作條件與結(jié)果表注,因筘片面積不足,摩擦系數(shù)系在相同組件基材與相同電鍍條件的試片上,電鍍厚度為30μm以上依據(jù)ASTMD3702-94以300牛頓荷重試驗(yàn);熱傳導(dǎo)系數(shù)系在厚度為表中厚度的試片上,系依據(jù)ASTMC177試驗(yàn)量測(cè)表面兩點(diǎn)距離的熱傳導(dǎo)系數(shù)。<第六組實(shí)施例>如圖7,為本組實(shí)施例的涂覆復(fù)合金屬碳化物陶瓷電鍍層的織紗導(dǎo)向組件1的示意圖,系以申克片13為實(shí)施例,在本組實(shí)施例的碳化鉻陶瓷電鍍液系使用表3的配方,在此不再重復(fù)列出。本組實(shí)施例的涂覆復(fù)合金屬碳化物陶瓷電鍍層3的織紗導(dǎo)向組件1,系經(jīng)由電鍍形成復(fù)合金屬碳化物陶瓷電鍍層3附著在申克片13的組件基材2上,所形成的復(fù)合金屬碳化物陶瓷電鍍層3系經(jīng)由電鍍形成非晶相碳化鉻結(jié)構(gòu),附著在組件基材2表面,復(fù)合金屬碳化物陶瓷電鍍層3成份系由主要包含鉻元素32、碳元素31、鐵元素34、氧元素等所組成,即復(fù)合金屬碳化物陶瓷電鍍層3由鉻元素32、碳元素31、鐵元素34形成非晶相碳化鉻結(jié)構(gòu)。非晶相碳化鉻鈷結(jié)構(gòu)包括鐵元素與六碳化二十三鉻鐵((Fe,Cr)23C6)或三碳化七鉻鐵((Fe,Cr)7C3)。表10中,實(shí)施例II的SEM(掃描式電子顯微鏡)表面形貌照片參見圖式附件11圖。表10為本組實(shí)施例之各實(shí)施例之操作條件與結(jié)果表實(shí)施例申克片I申克片II組件基材高碳鋼不銹鋼復(fù)合金屬碳化物陶瓷電鍍層厚度2.0μm1.2μm碳元素含量12At%15At%鉻元素含量35At%34At%鐵元素含量32At%31At%摩擦系數(shù)0.430.44熱傳導(dǎo)系數(shù)190190表面硬度(維氏硬度試驗(yàn)ASTMB578)850Hv875Hv注,因申克片面積不足,摩擦系數(shù)系在相同組件基材與相同電鍍條件的試片上,電鍍厚度為30μm以上依據(jù)ASTMD3702-94以300牛頓荷重試驗(yàn);熱傳導(dǎo)系數(shù)系在厚度為表中厚度的試片上,系依據(jù)ASTMC177試驗(yàn)量測(cè)表面兩點(diǎn)距離的熱傳導(dǎo)系數(shù)。最后應(yīng)說(shuō)明的是:以上各實(shí)施例僅用以說(shuō)明本發(fā)明的技術(shù)方案,而非對(duì)其限制;盡管參照前述各實(shí)施例對(duì)本發(fā)明進(jìn)行了詳細(xì)的說(shuō)明,本領(lǐng)域的普通技術(shù)人員應(yīng)當(dāng)理解:其依然可以對(duì)前述各實(shí)施例所記載的技術(shù)方案進(jìn)行修改,或者對(duì)其中部分或者全部技術(shù)特征進(jìn)行等同替換;而這些修改或者替換,并不使相應(yīng)技術(shù)方案的本質(zhì)脫離本發(fā)明各實(shí)施例技術(shù)方案的范圍。當(dāng)前第1頁(yè)1 2 3