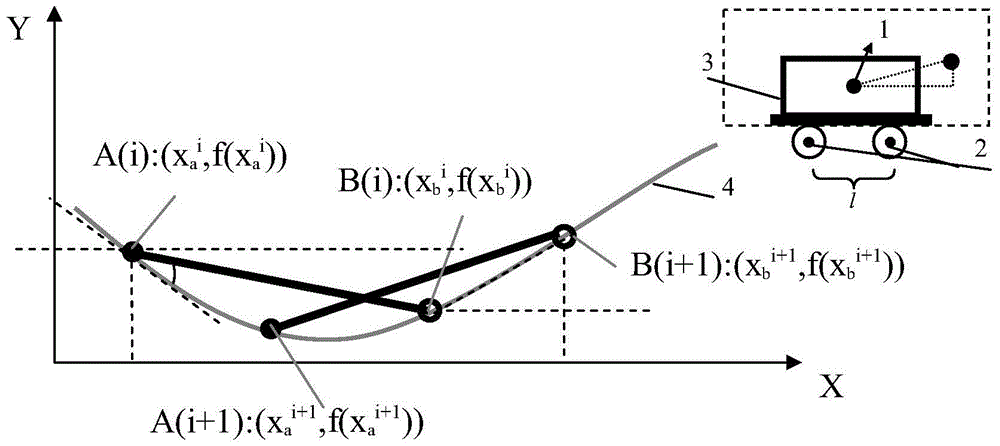
本發(fā)明涉及道路交通領(lǐng)域中各類公路、鐵路、橋梁和隧道等工程結(jié)構(gòu)表面線形檢測方法,具體涉及一種基于剛性載體運行軌跡解析算法的線形檢測方法及裝置。
背景技術(shù):公路、鐵路路基的變形監(jiān)測,橋梁和隧道的變形監(jiān)測對于保證交通工程的結(jié)構(gòu)安全至關(guān)重要。公路、鐵路中軟土地路基很容易發(fā)生沉降、錯差等變形問題。普通的檢測手段無法滿足高精度的長距離引測。橋梁結(jié)構(gòu)在外力作用下會產(chǎn)生變形,而各種病害如裂縫、預(yù)應(yīng)力損失等最終也導(dǎo)致橋梁線形發(fā)生變化,線形位移是判斷橋梁安全的最重要而且直觀的參考指標(biāo)。隧道在長期的運營及使用過程中,最關(guān)心的安全問題就是防止隧道坍塌,及時快速把握隧道沿線走向及圍巖條件較差區(qū)域的環(huán)向變形是確保隧道運營安全的重要工作。道路交通領(lǐng)域的變形監(jiān)測對精度要求必須符合相應(yīng)的國家評定標(biāo)準(zhǔn)。例如對于目前常見的斜拉索橋中,如果主跨分別為鋼箱架加勁梁,預(yù)應(yīng)力混凝土梁和鋼桁架加勁梁,跨中撓度最大允許變形為跨徑的1/400,1/500和1/800。如果跨徑為500m,則上述橋梁跨中撓度最大允許值分別為1.25m,1m和0.625m。然而每年觀測數(shù)據(jù)顯示,對于有下?lián)献冃乌厔莸拇笮蜆蛄褐骺缈缰邢聯(lián)厦磕曛挥?-3毫米,中小型橋梁跨中下?lián)仙踔林挥?-2毫米。據(jù)此,對線形測量系統(tǒng)的精度要求在毫米量級。公路、鐵路、橋梁和隧道線形檢測常規(guī)方法主要采用光學(xué)儀器通過建立水準(zhǔn)控制網(wǎng)進(jìn)行測量,長期監(jiān)測主要采用連通管測試系統(tǒng)、激光測量系統(tǒng)、光電圖像式測量系統(tǒng)以及GPS法等新型測試方法。水準(zhǔn)控制網(wǎng)的建立工程復(fù)雜,耗時長,受環(huán)境影響較大。連通管測試系統(tǒng)通過測量各測點與基準(zhǔn)點的液面壓力差來得到各測點的撓度值。不僅需要預(yù)鋪水管,而且在使用過程中存在著響應(yīng)時間慢,施工及維護(hù)成本高等缺點。激光測量系統(tǒng)和光電圖像式測量系統(tǒng)主要是通過光學(xué)系統(tǒng)捕捉光斑或成像的位置變化得出光源的相對位置變化。這兩種測量系統(tǒng)都必須在橋上安裝固定設(shè)備作為參考點,當(dāng)設(shè)備移動后無法獲得最初的測量基準(zhǔn)狀態(tài),無法滿足長期測量要求,而且不同氣候條件對測量有影響。GPS技術(shù)接收導(dǎo)航衛(wèi)星的載波相位差分?jǐn)?shù)據(jù)實時測定站點的三維坐標(biāo),是一種新型的實時測量技術(shù)。GPS受外界大氣影響小,可以在暴風(fēng)雨中進(jìn)行監(jiān)測,可以實現(xiàn)三維坐標(biāo)的自動監(jiān)測。然而該技術(shù)存在著垂直高程精度較差、無法達(dá)到毫米精度的缺點,且成本高,無法大規(guī)模開展應(yīng)用。此外進(jìn)行多點精確測量方式時,要求每點靜止測試時間較長,測試慢。上述技術(shù)除了存在各自不同的應(yīng)用局限外,還由于通過為數(shù)不多的測點來擬合檢測對象的撓度線形,因此均存在線形不連續(xù)的問題。既有專利(公開號:CN201210116750.6)中,提出了采用光纖陀螺線形測量系統(tǒng)測量橋梁的線形和剛性曲線的方法,并且提到了多種減小誤差的方法,但是該專利僅采用對數(shù)據(jù)的分析達(dá)到減小誤差的目的。既有專利(申請?zhí)枺篊N201210455343.8)中,提出了一種動態(tài)校正方法,該方法對測試系統(tǒng)中的光纖陀螺施加預(yù)先定義的角速度交變調(diào)制信號,通過將包含調(diào)制信號的角速度數(shù)據(jù)與預(yù)先定義的角速度調(diào)制信號數(shù)據(jù)進(jìn)行對比,得到修正系數(shù),并未考慮載體運動的方向與實際待測工程結(jié)構(gòu)表面之間的關(guān)系。既有專利(申請?zhí)枺篊N201210455270.2)中,提出了一種靜態(tài)校正方法,該方法在被測路段放置靜態(tài)標(biāo)定橋,通過系統(tǒng)測得標(biāo)定橋的橋高與實際橋高進(jìn)行對比,得到縱坐標(biāo)修正系數(shù),利用該系數(shù)修正整體線形曲線,并未提到載體本身結(jié)構(gòu)尺寸大小對待測工程結(jié)構(gòu)表面曲線測量是有影響的,當(dāng)載體不能視為質(zhì)點時,此方法會帶來較大誤差。
技術(shù)實現(xiàn)要素:本發(fā)明要解決的技術(shù)問題是:提供一種基于剛性載體運行軌跡解析算法的線形檢測方法及裝置,能夠提高整體線形檢測精度。本發(fā)明為解決上述技術(shù)問題所采取的技術(shù)方案為:一種基于剛性載體運行軌跡解析算法的線形檢測方法,其特征在于:它包括以下步驟:S1、將一個剛性輪式檢測車沿著待測工程結(jié)構(gòu)表面運行,實時檢測剛性輪式檢測車的傾斜角度θi、前輪運行路程Δsb和后輪運行路程Δsa;S2、定義前輪和后輪與待測工程結(jié)構(gòu)表面的接觸點分別為B點和A點,B點和A點之間的距離為l,視剛性輪式檢測車的運動方向與B、A兩點的連線成割線關(guān)系,定義γi為剛性輪式檢測車的傾斜角度從開始到i-1時刻夾角的積分;B點和A點的運行軌跡解析算法如下:①,②,③,④,其中C1、C2為中間變量,⑤,⑥,⑦,式中為i時刻A、B兩點坐標(biāo);為i+1時刻A、B兩點坐標(biāo);θi為i時刻的AB連線和i+1時刻的AB連線之間的夾角;S3、視剛性輪式檢測車與待測工程結(jié)構(gòu)表面的接觸點的運動軌跡無限逼近待測工程結(jié)構(gòu)表面線形,即得到待測工程結(jié)構(gòu)表面線形。一種用于實現(xiàn)上述基于剛性載體運行軌跡解析算法的線形檢測方法的檢測裝置,其特征在于:它包括一個剛性輪式檢測車,剛性輪式檢測車下方設(shè)置前輪和后輪,前輪與后輪之間的距離為定值,在剛性輪式檢測車上設(shè)有角度傳感器,前輪和后輪分別設(shè)有里程儀。按上述裝置,所述的里程儀為光電編碼器。按上述裝置,所述的角度傳感器為光纖陀螺。本發(fā)明的有益效果為:以前輪和后輪與待測工程結(jié)構(gòu)表面的接觸點的運動來無限逼近待測工程結(jié)構(gòu)表面線形,更好地把握了剛性輪式檢測車與待測曲線的位置關(guān)系;客觀采用了割線AB傾斜角的變化決定角度傳感器的輸出,無需考慮割線AB是否能近似為切線的問題,更能夠真實的反映待測工程結(jié)構(gòu)表面的二維曲線,尤其是在測量小尺寸的待測工程結(jié)構(gòu)時,與待測工程結(jié)構(gòu)尺寸相比,剛性輪式檢測車前后輪的間距不可忽略,剛性輪式檢測車不可被近似為質(zhì)點,本發(fā)明方法更能準(zhǔn)確地描述待測工程結(jié)構(gòu)表面線形。附圖說明圖1是本發(fā)明一實施例的方法流程圖;圖2是本發(fā)明涉及到的剛性輪式檢測車的線形檢測圖;圖3是用于檢驗運動軌跡解析算法的一個梯形鋼制模型線形曲線;圖4是采用通用算法所測得的結(jié)構(gòu)表面線形曲線與基準(zhǔn)線形的比較;圖5是采用本發(fā)明方法推演出的結(jié)構(gòu)表面線形曲線與基準(zhǔn)線形的比較;圖中:1-角度傳感器,2-前、后輪里程儀,3-剛性輪式檢測車,4-待測工程結(jié)構(gòu)表面線形曲線。具體實施方式下面結(jié)合具體實例對本發(fā)明做進(jìn)一步說明。一種基于剛性載體運行軌跡解析算法的線形檢測方法,如圖1所示,包括以下步驟:S1、將一個剛性輪式檢測車沿著待測工程結(jié)構(gòu)表面運行,實時檢測剛性輪式檢測車的傾斜角度θi、前輪運行路程Δsb和后輪運行路程Δsa;S2、定義前輪和后輪與待測工程結(jié)構(gòu)表面的接觸點分別為B點和A點,B點和A點之間的距離為l,視剛性輪式檢測車的運動方向與B、A兩點的連線分別成割線關(guān)系,定義γi為剛性輪式檢測車的傾斜角度從開始到i-1時刻夾角的積分;B點和A點的運行軌跡解析算法如下:①,②,③,④,其中C1、C2為中間變量,⑤,⑥,⑦,式中為i時刻A、B兩點坐標(biāo);為i+1時刻A、B兩點坐標(biāo);θi為i時刻的AB連線和i+1時刻的AB連線之間的夾角;S3、視剛性輪式檢測車與待測工程結(jié)構(gòu)表面的接觸點的運動軌跡無限逼近待測工程結(jié)構(gòu)表面線形,即得到待測工程結(jié)構(gòu)表面線形。用于實現(xiàn)上述線形檢測方法的檢測裝置,如圖2所示,包括一個剛性輪式檢測車3,剛性輪式檢測車3下方設(shè)置前輪和后輪,前輪與后輪之間的距離為定值,在剛性輪式檢測車上設(shè)有角度傳感器1(本實施例中為光纖陀螺),前輪和后輪分別設(shè)有里程儀2(本實施例中為光電編碼器)。為了對比本發(fā)明的優(yōu)點,選取一個梯形鋼制模型,采用傳統(tǒng)水準(zhǔn)測量方法測得的線形曲線為f(x),如圖3所示;將剛性輪式檢測車近似為一個質(zhì)點,采用通用算法測得的線形曲線與基準(zhǔn)線形f(x)進(jìn)行對比,如圖4所示;采用本發(fā)明方法,視剛性輪式檢測車運動方向與工程結(jié)構(gòu)表面接觸點間成割線關(guān)系,所推演的線形曲線與基準(zhǔn)線形f(x)的比較如圖5所示。綜合比較圖4和圖5,可見本發(fā)明方法擁有更高的準(zhǔn)確度。以上實施例僅用于說明本發(fā)明的計算思想和特點,其目的在于使本領(lǐng)域內(nèi)的技術(shù)人員能夠了解本發(fā)明的內(nèi)容并據(jù)以實施,本發(fā)明的保護(hù)范圍不限于上述實施例。所以,凡依據(jù)本發(fā)明所揭示的原理、設(shè)計思路所作的等同變化或修飾,均在本發(fā)明的保護(hù)范圍之內(nèi)。