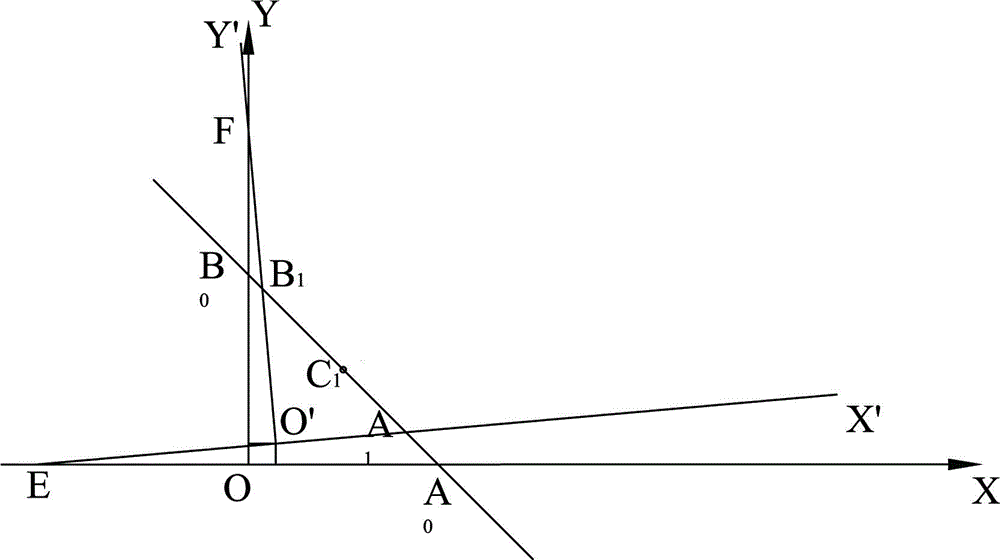
本發(fā)明屬于工業(yè)測量領域,尤其涉及一種矩形工件位置和角度測量方法,適用于大尺寸矩形工件的位置和角度的非接觸式測量。
背景技術:
:在機床切割領域,對大尺寸的薄鋼板進行激光切割時,必須要對放置到切割平臺上的工件進行定位,使工件相對于機床及激光切割頭處于正確的位置,特別是工件的邊部要被利用為成品零件的邊部時,對工件的定位精度要求較高,否則會導致切割零件尺寸誤差。工件定位傳統(tǒng)的方法是利用機械夾具對工件進行裝夾,配合百分表、劃線法進行找正調(diào)整,方能使工件的定位基準面分別與機床的工作臺面和工作臺的進給方向x、y保持平行。這種方法需要較長的調(diào)整時間,效率低下,不適用于快速在線作業(yè)。另一種方法是,利用機械擋塊來限定工件位置,用拍打機構(gòu)使工件和擋塊壓靠對齊。這種方法需要對擋塊的位置進行標定,一旦機床的工件坐標原點變化,就要重新調(diào)整擋塊位置,重新進行標定。而且在長期拍打下,擋塊的松動也會帶來工件定位誤差。因此,一套可以在線自動測量工件擺放的實際位置和角度,并傳輸?shù)接嬎銠C系統(tǒng)進行工件坐標系自動修正的系統(tǒng),對于現(xiàn)代化高速高精度生產(chǎn)是必不可少的。比較常見的做法是采用CCD相機和圖像處理技術來測量,如中國專利CN200410015617.7提出了一種工件定位光電測控系統(tǒng),包括計算機系統(tǒng),圖像信號攝取裝置,該圖像信號攝取裝置分別攝取標準工件與待加工工件的位置圖像信號,并傳輸?shù)接嬎銠C系統(tǒng)中,將待加工工件的位置圖像信號與標準工件的位置圖像信號比較產(chǎn)生誤差值,計算機系統(tǒng)根據(jù)該誤差值控制伺服電機移動待加工工件達到預定位置。這種方法測量靈活、范圍較大、測量過程快捷,具有很多優(yōu)點,而且隨著高分辨率高性能CCD相機的出現(xiàn)和計算機圖像處理技術的發(fā)展,測量精度也在逐步提升。 但缺點是,測量精度易受光照等條件的干擾,需要有相機和光源的安裝條件,系統(tǒng)結(jié)構(gòu)較為復雜,成本也較高。本發(fā)明針對這種情況,提出一種安裝簡便、測量迅速,且安裝、維護要求較低的測量系統(tǒng)和方法。技術實現(xiàn)要素:本發(fā)明的目的在于提供一種矩形工件位置和角度測量方法,可自動對工件位置和角度進行在線測量,并能根據(jù)測量結(jié)果自動生成誤差補償數(shù)據(jù)反饋到數(shù)控系統(tǒng),調(diào)整工件坐標系后進行切割加工,以保證工件的加工尺寸精度及批量工件的尺寸一致性,大大增強數(shù)控機床的智能化程度。為達到上述目的,本發(fā)明的技術方案是:一種矩形工件位置和角度測量方法,其特征是,包括,1)采用一個二維形狀測量傳感器,安裝在激光切割頭上,激光切割頭安裝于三軸數(shù)控機床的Z軸,傳感器隨激光切割頭在切割范圍內(nèi)X軸或Y軸方向平面移動,傳感器的光線豎直向下照射在鋼板的邊部,光線與X軸方向成一角度θ,獲取鋼板邊沿輪廓;在傳感器安裝好后,對傳感器的安裝位置進行標定,即傳感器中心點和激光切割頭的噴嘴中心點的相對位置,這樣就可以通過數(shù)控機床Z軸的移動來精確控制傳感器光線的照射位置;2)第一次測量將待切割的矩形片料在數(shù)控機床切割工位上放置好,控制傳感器位于矩形片料角度上方,觸發(fā)傳感器進行第一次測量,得到矩形片料的左邊沿和右邊沿位置值;3)平移掃描測量矩形片料長邊激光切割頭攜帶傳感器沿X軸方向平移,移動過程中以一定時間間隔或距離間隔觸發(fā)多次測量,對矩形片料的長邊邊沿位置進行采樣,同時實時記錄采樣時的數(shù)控機床X軸坐標位置;4)利用測量得到的矩形片料長邊邊沿數(shù)據(jù)樣本,用二點直線法或最小二乘法擬合直線,計算矩形片料長邊和X軸的偏角;5)利用步驟2)測量得到的矩形片料左右邊沿位置值,與理論左右邊沿位置值進行對比,推算矩形片料在X、Y軸方向的偏移量;6)將步驟4)計算得到的偏角和步驟5)得到的X、Y偏移值傳輸給數(shù)控機床控制系統(tǒng),對數(shù)控機床的理論工件坐標系進行補償;7)數(shù)控機床控制系統(tǒng)使用補償后的工件坐標系開始激光切割加工。進一步,所述傳感器的光線與X軸方向成角度θ為30~60度,優(yōu)選θ為45度。在激光切割領域,待切割的片料多為規(guī)則的矩形。矩形料的工件坐標系原點一般設定在片料的角點,X、Y軸分別和構(gòu)成該角點的兩條直角邊重合。搬運裝置將矩形料放置到切割工位,實際的放置位置和角度存在偏差,尤其是在缺乏定位裝置的情況下。本發(fā)明采用一個二維形狀測量傳感器,這種傳感器通過向物體發(fā)射出具有一定寬度的激光線束,并通過CCD感應器接受反射回來的激光,來檢測物體的截面輪廓形狀尺寸,如高度、寬度、邊沿位置、轉(zhuǎn)折點位置等。本發(fā)明所述的二維形狀測量傳感器安裝在激光切割頭上,可以隨激光切割頭在切割范圍內(nèi)X或Y軸方向平面移動。傳感器的光線豎直向下與X軸方向成角度θ,照射在鋼板的邊部,獲取邊沿輪廓,可以檢測邊沿位置,測量精度非常高。在傳感器安裝好后,對傳感器的安裝位置進行標定,即傳感器中心點和激光切割頭的噴嘴中心點的相對位置。這樣就可以通過數(shù)控機床Z軸的移動來精確控制傳感器光線的照射位置。在理想的工件擺放情況下,數(shù)控機床初始設定的工件坐標系是與矩形片料的零件坐標系重合的,即坐標系原點在矩形片料的角點,坐標系X、Y軸與矩形片料的兩條直邊重合。但由于搬運裝置的重復定位精度等因素影響,實際擺放好的矩形片料與設定的工件坐標系成一定的偏角,并且片料的角點也偏離了設定的工件坐標系原點。本發(fā)明的目的是在線自動測量該偏角和在X、Y軸方向上的偏移量。本發(fā)明的有益效果:本發(fā)明方法測量過程簡潔、快速、自動化程度高,對安裝條件和環(huán)境光線的要求低,非常適合矩形工件的位置和角度的高精度測量,在加工前可協(xié)助操作者進行工件的找正,自動完成工件坐標系的設定,從而降低了對上料搬運裝置的定位精度要求,簡化工裝夾具,節(jié)省夾具費用,縮短輔助時間,提高加工效率。在以矩形片料為加工對象的機床切割、刻字等領 域具有良好的推廣應用價值。附圖說明圖1本發(fā)明采用二維形狀測量傳感器對矩形片料邊部進行測量的示意圖;圖2為本發(fā)明在測量過程中傳感器光線與測量對象的幾何關系圖;圖3為本發(fā)明計算X、Y偏移值的幾何示意圖。具體實施方式下面結(jié)合具體實施例,進一步闡述本發(fā)明。應理解,這些實施例僅用于說明本發(fā)明而不用于限制本發(fā)明的范圍。此外應理解,在閱讀了本發(fā)明表述的內(nèi)容之后,本領域技術人員可以對本發(fā)明作各種改動或修改,這些等價形式同樣落于本申請所附權利要求書所限定的范圍。如圖1所示,矩形片料1放置在切割平臺上,二維形狀測量傳感器的探頭2安裝在其上方,可以隨激光切割頭在切割范圍內(nèi)X或Y軸方向平面移動。探頭2的安裝使其線狀光與X軸方向成一角度θ—45°。探頭2發(fā)出具有一定寬度的激光照射矩形片料1的邊部,其連接的傳感器控制器3負責測量處理和結(jié)果輸出。測量得到的輪廓圖如圖1所示,A、B分別表示輪廓的左邊沿點和右邊沿點。C為傳感器的中心點。A和B相對于C的位置即為邊沿點的位置值,可以從傳感器中直接讀取,傳輸?shù)接嬎銠C系統(tǒng)。圖2為在測量過程中,傳感器光線與測量對象的幾何關系圖。圖中,坐標系XOY為機床初始設定的工件坐標系,其X、Y軸與機床坐標系的X、Y軸平行。圖中坐標系X′O′Y′為矩形片料的零件坐標系,其原點O′為矩形片料的角點,X′、Y′軸與片料的兩條直邊重合。在理想的工件擺放情況下,初始設定的工件坐標系XOY與零件坐標系X′O′Y′重合。但由于實際擺放中不可避免的誤差,零件坐標系X′O′Y′與初始設定的工件坐標系XOY存在一定的偏差。本發(fā)明的目的就是要在線自動測量實際零件坐標系X′O′Y′相對于初始設定的工件坐標系XOY的位置關系,即坐標系偏移(Δx,Δy)和偏角δ。以便數(shù)控系統(tǒng)可以補償工件坐標系,使調(diào)整后的工件坐標系與實際零件坐標系重合。結(jié)合圖2,本發(fā)明實施例的自動測量過程如下:1)切割頭攜帶傳感器在測量起始位置待機。該測量起始位置由機床事先設定,其要使激光照射在鋼板的角部,可以同時獲得截面輪廓的左邊沿和右邊沿。傳感器光線與X軸負方向成θ角,一般設定為45°角,實際數(shù)值要進行標定后獲得。C1為該位置的傳感器中心點,A0和B0分別為光線與坐標系XOY的交點。傳感器光線相對于坐標系XOY的位置固定,即A0C1、B0C1為固定的已知值,分別表示為L0和R0;2)第一次測量當待切割的矩形片料在機床切割工位上放置好后,系統(tǒng)觸發(fā)傳感器對片料角部進行第一次測量,同時獲取左邊沿位置L1和右邊沿位置R1,也就是圖2中所示的A1C1、B1C1;3)平移測量切割頭攜帶傳感器沿X方向平移,移動過程中以一定時間間隔或距離間隔觸發(fā)多次測量,對矩形片料的單個長邊進行掃描。依次獲得N組左邊沿位置值Li及對應測量位置的X坐標值xi,i=1,2……,N;4)計算機系統(tǒng)利用測量值計算偏角δ、以及偏移Δx和Δy;5)將Δx、Δy和δ傳輸給數(shù)控系統(tǒng),對工件坐標系進行補償;6)數(shù)控系統(tǒng)開始切割加工過程。上述步驟4)中偏角δ的計算,一種最簡便的方法是兩點直線法,只需要取矩形片料長邊上兩個位置的邊部測量值,連接兩次測量的邊沿點A1和A2而形成的直線A1A2,認為是矩形片料的長邊即X′軸??梢赃@樣判斷的前提條件是矩形片料長邊的平直度較好,且A1和A2之間的距離盡可能大。結(jié)合圖2,在三角形ΔA1A2D中,由三角函數(shù)關系可推導,tanδ=A1DA2D=(A1C1-A2C2)sinθC1C2-(A1C1-A2C2)cosθ=(L2-L1)sinθ(x2-x1)-(L2-L1)cosθ]]>從而,δ=tan-1(L2-L1)sinθ(x2-x1)-(L2-L1)cosθ]]>式中,L1和L2分別為兩次測量的傳感器的左邊沿位置讀數(shù),x1和x2分別為兩次測量的實時數(shù)控機床X軸坐標值,θ為傳感器光線相對于X軸的安裝角度。進一步,如果矩形片料長邊的平直度較差,兩點直線法的測量誤差可能較大,也可以采用多點測量、然后用最小二乘法來擬合長邊,使測量結(jié)果盡可能精確。假設擬合直線表示為直線方程y=a0+a1x,式中有兩個待定參數(shù),a0代表截距,a1代表斜率。對于等精度測量所得到的N組數(shù)據(jù)(xi,yi),i=1,2……,N,xi值被認為是準確的,所有的誤差只聯(lián)系著yi。我們以左邊沿讀數(shù)L1在Y方向的投影作為Lisinθ作為直線的yi,以N次測量的實時機床坐標值為xi,計算最小二乘法擬合的直線方程的斜率:a1=N(Σi=1nxiyi)-(Σi=1nxi)(Σi=1nyi)N(Σi=1nxi2)-(Σi=1nxi)2=N(Σi=1nxiLi)-(Σi=1nxi)(Σi=1nLi)N(Σi=1nxi2)-(Σi=1nxi)2sinθ]]>根據(jù)直線斜率與傾斜角的關系得出:δ=tan-1a1接下來計算偏移Δx和Δy。結(jié)合圖3的幾何關系進行三角函數(shù)變換,可以如下推導,及Δy=O′Esinδ=(A1E-O′A1)sinδ=(sinθsinδA0A1-A1B1cos(θ+δ))sinδ=(C1A0-C1A1)sinθ-(A1C1+B1C1)sinδcos(θ+δ)=(L0-L1)sinθ-(L1+R1)sinδcos(θ+δ)]]>根據(jù)以上計算公式,計算機系統(tǒng)將計算得到的Δx、Δy和δ傳輸給數(shù)控機床控制系統(tǒng),補償理論工件坐標系,找正零件后進行加工作業(yè),確保零件 的加工尺寸精度。本發(fā)明整個測量過程簡潔、快速、自動化程度高,對安裝條件和環(huán)境光線的要求低,降低了對上料搬運裝置的定位精度要求,節(jié)省夾具費用,縮短輔助時間,提高加工效率。在以矩形片料為加工對象的機床切割、刻字等領域具有良好的推廣應用價值。當前第1頁1 2 3