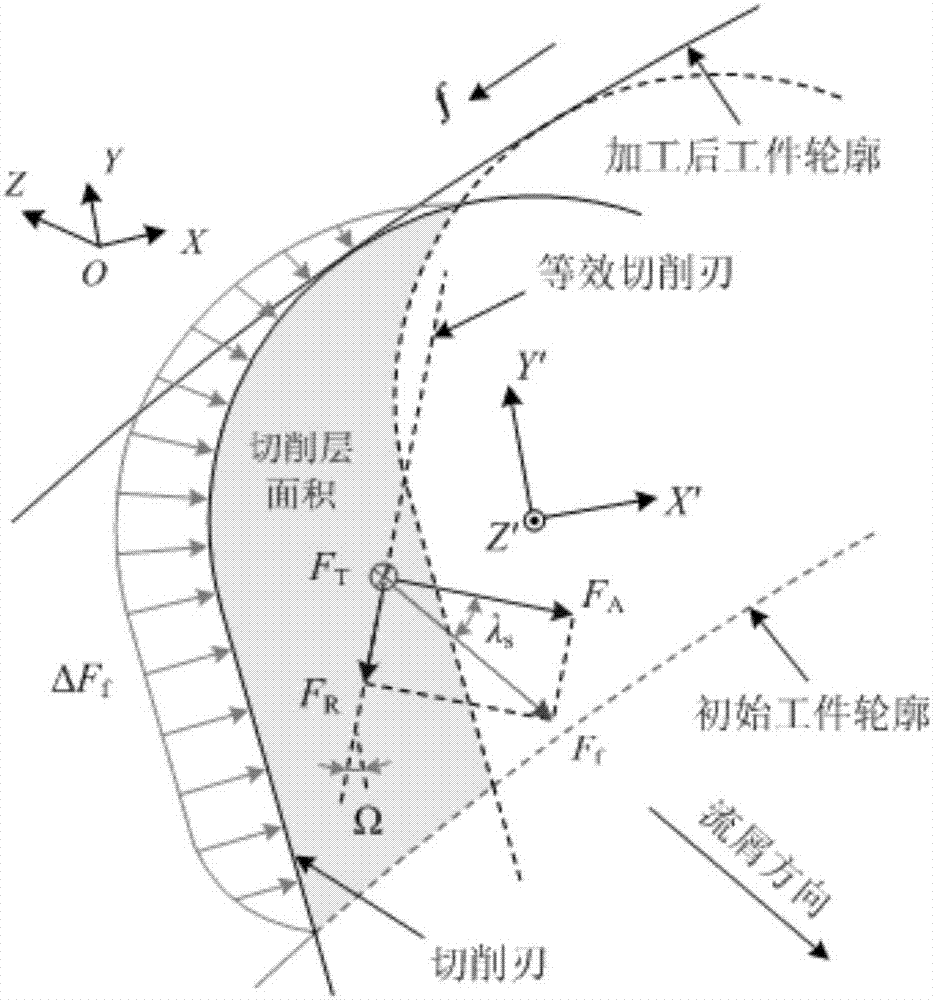
本發(fā)明涉及一種控制曲線車削加工切削力突變的方法,屬于曲線車削加工工藝領(lǐng)域。
背景技術(shù):
:曲線車削加工是兵器、車輛等工業(yè)領(lǐng)域常見的加工工藝,如彈體外圓車削、中凸變橢圓活塞型面車削等。由于工件輪廓曲線曲率變化,切削力容易出現(xiàn)大幅度變化,對刀具和工件造成切削載荷沖擊,加劇刀片磨損、破損,甚至引起刀具折斷,影響零件加工質(zhì)量,降低生產(chǎn)效率?,F(xiàn)有技術(shù)面對彈體外圓車削和內(nèi)孔鏜削加工時,切削力在實際加工過程中會產(chǎn)生突變,通常采用過小的刀具進給量以避免產(chǎn)生切削力突變,這種切削用量選擇方式趨于保守,使得能耗過大、加工成本偏高,成為制約難加工材料切削技術(shù)發(fā)展的瓶頸;即使采用切削力建模技術(shù),也僅僅針對直線切削,面向彈體外圓、變橢圓型面等變曲線曲率車削加工時也不具備適用性。因此,建立曲線車削加工切削力模型,研究切削力變化規(guī)律,對實現(xiàn)高效優(yōu)質(zhì)生產(chǎn)具有重要意義。技術(shù)實現(xiàn)要素:本發(fā)明的技術(shù)解決問題:為克服現(xiàn)有技術(shù)的不足,提供一種控制曲線車削加工切削力突變的方法,通過建曲線切削狀態(tài)下的切削力模型,判斷切削力在實際加工過程中產(chǎn)生突變的位置,進而調(diào)整刀具在切削力突變處的進給量,高效完成曲線車削加工。本發(fā)明的技術(shù)解決方案:一種控制曲線車削加工切削力突變的方法具體步驟為:(1)建立坐標系按照右手定則在工件上建立世界坐標系:以工件軸線和端面的交點為原點o,x軸與工件軸線重合并指向工件外側(cè),oyz平面與工件端面重合,建立世界坐標系oxyz;按照右手定則在刀具上建立移動坐標系:以刀尖圓弧圓心為原點o',x'軸與x軸平行且方向一致,o'x'y'平面與刀具前刀面重合,建立刀具上的移動坐標系o'x'y'z';(2)確定切削層面積任意前后兩次進刀時,切削刃與工件輪廓曲線相交圍成切削層區(qū)域abcd,其中兩次進刀切削刃中的圓弧刃部分交點為a,切削刃中的直線刃部分與工件輪廓曲線交點分別為b和c,圓弧刃與直線刃切點為d,基于格林運算法則計算切削層區(qū)域abcd面積(3)確定等效切削刃方向角ω等效切削刃方向角ω可由刃傾角λs和摩擦力方向角β表示為:ω=β-λs,其中刃傾角λs為由加工條件決定的定值,β由切削層區(qū)域中微元上的摩擦力矢量確定;(4)在世界坐標系oxyz上采集直線切削狀態(tài)下的切削力fx1、fy1和fz1;(5)直線切削力變換通過空間矩陣變換,將采集的直線切削力[fx1,fy1,fz1]變換為移動坐標系o'x'y'上的切削力(6)標定剪應(yīng)力τs、法向摩擦角βn、流屑角η和法向剪切角(7)計算切向、徑向和軸向切削力系數(shù)kt、kr和ka其中,γn為法向前角;(8)在移動坐標系o'x'y'z'上計算曲線切削狀態(tài)時的切削力ft3、fr3和fa3(9)在世界坐標系oxyz上計算曲線切削狀態(tài)時的切削力fx3、fy3、fz3(10)根據(jù)步驟9計算得到的切削力,判斷實際加工過程中切削力在刀具及工件上產(chǎn)生突變的位置,進而調(diào)整刀具在切削力突變位置處的進給量,使切削力在此處變化趨于穩(wěn)定。的計算方法為:采用b樣條曲線法將切削刃和工件輪廓曲線分別參數(shù)化表示為和其中n(u)和n(t)為遞推公式,均可表示為式中,n表示b樣條曲線上離散點對應(yīng)的參數(shù)值,i表示第i個離散點,k表示b樣條曲線的冪次,px、py分別為切削刃在世界坐標系oxyz中x方向和y方向上的b樣條曲線控制點;qx、qy分別為加工前工件輪廓曲線在世界坐標系oxyz中x方向和y方向上的b樣條曲線控制點;其中j和j+1分別為前后兩次進刀。通過得到剪應(yīng)力τs、法向摩擦角βn、流屑角η和法向剪切角其中ftn、frn和fan分別為ft、fr和fa在法平面投影,as為剪切面積,f為進給量,ap為切削深度,為剪力在法平面上的投影與切削平面之間夾角,ξn為切削合力在法平面上的投影與切削平面之間夾角,ξλ為切削合力f與法平面之間的夾角,βa為摩擦角,βn為法向摩擦角。步驟5中其中γo為刀具前角。步驟3中摩擦力方向角β計算方法為將切削層區(qū)域abcd分為由圓弧刃圍成的第一區(qū)域和由直線刃圍成的第二區(qū)域,δam,1和δam,2分別表示第一區(qū)域和第二區(qū)域中的第m個微元面積,δβm,1和δβm,2分別表示第一區(qū)域和第二區(qū)域中第m個微元對應(yīng)的摩擦角。式中cj+1,θ(u)和cj+1,r(u)分別為微元的極角和極徑,可分別表示為:同理可得δam,2;微元摩擦角同理可得δβm,2。在步驟9和步驟10之間還可以對建模進行試驗驗證,在世界坐標系oxyz上采集曲線切削狀態(tài)下的切削力,作為切削力試驗值,將切削力試驗值與步驟9獲得的切削力預(yù)測值進行比對,如果切削力幅值偏差在10%以內(nèi),則說明建模正確;如果切削力幅值偏差大于10%,則重新檢驗并標定剪應(yīng)力τs、法向摩擦角βn、流屑角η和法向剪切角直至將切削力幅值偏差控制在10%以內(nèi)。本發(fā)明與現(xiàn)有技術(shù)相比具有如下有益效果:(1)本發(fā)明采用b樣條曲線法將切削刃和工件輪廓曲線參數(shù)化處理,建立包含關(guān)鍵幾何參數(shù)的統(tǒng)一計算模型,解析切削力模型系數(shù)和力矢量、速度矢量、流屑矢量之間的約束關(guān)系,提出切削力模型系數(shù)標定方法,進而確定切削力模型系數(shù),通過建立的切削力模型,可以判斷切削力在實際曲線加工過程中產(chǎn)生突變的位置,進而調(diào)整刀具在切削力突變處的進給量,使切削力在此處變化趨于穩(wěn)定,相對于現(xiàn)有對直線切削建模技術(shù)的應(yīng)用,可以高效完成曲線車削加工;(2)本發(fā)明中基于格林運算法則計算單連通區(qū)域內(nèi)的切削層面積,基于極坐標微元法計算等效切削刃方向角采用極坐標微元法,有效避免了因出現(xiàn)不規(guī)則幾何接觸區(qū)域而產(chǎn)生的解析困難問題。附圖說明圖1為本發(fā)明世界坐標系oxyz示意圖;圖2為本發(fā)明移動坐標系o'x'y'z'示意圖;圖3為本發(fā)明切削層面積示意圖;圖4為本發(fā)明等效切削刃方向角示意圖;圖5為本發(fā)明切削力采集標定示意圖;圖6為本發(fā)明法向摩擦角標定結(jié)果及其擬合曲線;圖7為本發(fā)明法向剪切角標定結(jié)果及其擬合曲線;圖8為本發(fā)明剪應(yīng)力標定結(jié)果及其擬合曲線;圖9為本發(fā)明切向力系數(shù)標定結(jié)果及其擬合曲線;圖10為本發(fā)明徑向力系數(shù)標定結(jié)果及其擬合曲線;圖11為本發(fā)明軸向力系數(shù)標定結(jié)果及其擬合曲線;圖12為本發(fā)明曲線車削工件輪廓示意圖;圖13為本發(fā)明切削層面積的變化曲線;圖14為本發(fā)明等效切削刃方向角變化曲線;圖15為本發(fā)明在x方向上切削力預(yù)測值與試驗值的比對示意圖;圖16為本發(fā)明在y方向上切削力預(yù)測值與試驗值的比對示意圖;圖17為本發(fā)明在z方向上切削力預(yù)測值與試驗值的比對示意圖。具體實施方式下面結(jié)合附圖對本發(fā)明作進一步詳細的描述。一種控制曲線車削加工切削力突變的方法,具體步驟為:(1)建立坐標系如圖1所示,按照右手定則在工件上建立世界坐標系:以工件軸線和端面的交點為原點o,x軸與工件軸線重合并指向工件外側(cè),oyz平面與工件端面重合,建立世界坐標系oxyz;如圖2所示,按照右手定則在刀具上建立移動坐標系:以刀尖圓弧圓心為原點o',x'軸與x軸平行且方向一致,o'x'y'平面與刀具前刀面重合,建立刀具上的移動坐標系o'x'y'z';(2)確定切削層面積任意前后兩次進刀時,切削刃與工件輪廓曲線相交圍成切削層區(qū)域abcd,如圖3所示,其中兩次進刀切削刃中的圓弧刃部分交點為a,切削刃中的直線刃部分與工件輪廓曲線交點分別為b和c,圓弧刃與直線刃切點為d,基于格林運算法則計算切削層區(qū)域abcd面積具體計算方法為:采用b樣條曲線法將切削刃和工件輪廓曲線分別參數(shù)化表示為和其中n(u)和n(t)為遞推公式,均可表示為式中,n表示b樣條曲線上離散點對應(yīng)的參數(shù)值,i表示第i個離散點,k表示b樣條曲線的冪次,px、py分別為切削刃在世界坐標系oxyz中x方向和y方向上的b樣條曲線控制點;qx、qy分別為加工前工件輪廓曲線在世界坐標系oxyz中x方向和y方向上的b樣條曲線控制點;則其中j和j+1分別為前后兩次進刀。(3)確定等效切削刃方向角ω等效切削刃方向角ω可由刃傾角λs和摩擦力方向角β表示為:ω=β-λs,其中刃傾角λs為由加工條件決定的定值,β由切削層區(qū)域中微元上的摩擦力矢量確定,如圖4所示,將切削層區(qū)域abcd分為由圓弧刃圍成的第一區(qū)域和由直線刃圍成的第二區(qū)域,δam,1和δam,2分別表示第一區(qū)域和第二區(qū)域中的第m個微元面積,δβm,1和δβm,2分別表示第一區(qū)域和第二區(qū)域中第m個微元對應(yīng)的摩擦角;式中cj+1,θ(u)和cj+1,r(u)分別為微元的極角和極徑,可分別表示為:同理可得δam,2;微元摩擦角同理可得δβm,2。(4)在世界坐標系oxyz上采集直線切削狀態(tài)下的切削力fx1、fy1和fz1;(5)直線切削力變換通過空間矩陣變換,將采集的直線切削力[fx1,fy1,fz1]變換為移動坐標系o'x'y'上的切削力其中γo為刀具前角。(6)標定剪應(yīng)力τs、法向摩擦角βn、流屑角η和法向剪切角通過得到剪應(yīng)力τs、法向摩擦角βn、流屑角η和法向剪切角其中ftn、frn和fan分別為ft、fr和fa在法平面投影,as為剪切面積,f為進給量,ap為切削深度,為剪力在法平面上的投影與切削平面之間夾角,ξn為切削合力在法平面上的投影與切削平面之間夾角,ξλ為切削合力f與法平面之間的夾角,βa為摩擦角,βn為法向摩擦角。(7)計算切向、徑向和軸向切削力系數(shù)kt、kr和ka其中,γn為法向前角;(8)在移動坐標系o'x'y'z'上計算曲線切削狀態(tài)時的切削力ft3、fr3和fa3(9)在世界坐標系oxyz上計算曲線切削狀態(tài)時的切削力fx3、fy3、fz3(10)在世界坐標系oxyz上采集曲線切削狀態(tài)下的切削力,作為切削力試驗值,將切削力試驗值與步驟9獲得的切削力預(yù)測值進行比對,如果切削力幅值偏差在10%以內(nèi),則說明建模正確;如果切削力幅值偏差大于10%,則重新檢驗并標定剪應(yīng)力τs、法向摩擦角βn、流屑角η和法向剪切角直至將切削力幅值偏差控制在10%以內(nèi);(11)根據(jù)步驟9計算得到的切削力,判斷實際加工過程中切削力在刀具及工件上產(chǎn)生突變的位置,進而調(diào)整刀具在切削力突變位置處的進給量,使切削力在此處變化趨于穩(wěn)定。實施例試驗在數(shù)控精密車削中心進行,由測力儀在世界坐標系oxyz上采集直線切削狀態(tài)下的切削力fx1、fy1和fz1,采樣頻率10khz,試件材料選用58simn高強度鋼,刀具前角為0°,后角為5°,主偏角為93°,副偏角為52°,刀尖圓弧半徑為0.8mm。1、進行切削力模型系數(shù)標定試驗切削力模型系數(shù)標定試驗的因素及水平設(shè)計如表1所示,將采集的切削力表示成切削層面積的函數(shù),如圖5所示,根據(jù)上文的標定方法對切削力模型系數(shù)進行標定,以雙指數(shù)函數(shù)對切削力模型系數(shù)進行擬合,其中a表示切削層面積,b、c、d、b和c表示雙指數(shù)函數(shù)的系數(shù),擬合系數(shù)如表2所示,標定結(jié)果如圖6-8和擬合曲線如圖9-11所示。表1標定試驗設(shè)計的因素及水平表2雙指數(shù)函數(shù)的擬合系數(shù)βnφnτsktkrkab18.726-18.735-1987.34880.8-787.78c0.5173-0.5172-2388.21202.6-152.52d0.0960.6892931.452772.71202.5407.18b0.00580.0058-0.07730.03970.0155c0.2937-0.5172-472.160.00210.40032、進行曲線車削試驗曲線車削試驗工件輪廓如圖12所示,試驗過程中切削層面積和等效切削刃方向角變化如圖13和圖14所示,切削力預(yù)測值與試驗值對比如圖15-17所示。通過圖15-17可以看出,在x、y、z三方向上切削力預(yù)測值與試驗值的幅值大小偏差在10%以內(nèi),變化趨勢保持一致,驗證了曲線車削中該切削力建模方法的有效性。在此基礎(chǔ)上,判斷實際加工過程中切削力在刀具及工件上產(chǎn)生突變的位置,進而調(diào)整刀具在切削力突變位置處的進給量,使切削力在此處變化趨于穩(wěn)定。本發(fā)明采用b樣條曲線法將切削刃和工件輪廓曲線參數(shù)化處理,建立包含關(guān)鍵幾何參數(shù)的統(tǒng)一計算模型,解析切削力模型系數(shù)和力矢量、速度矢量、流屑矢量之間的約束關(guān)系,提出切削力模型系數(shù)標定方法,進而確定切削力模型系數(shù),通過建立的切削力模型,可以判斷切削力在實際曲線加工過程中產(chǎn)生突變的位置,進而調(diào)整刀具在切削力突變處的進給量,使切削力在此處變化趨于穩(wěn)定,相對于現(xiàn)有對直線切削建模技術(shù)的應(yīng)用,可以高效完成曲線車削加工。本發(fā)明說明書中未作詳細描述的內(nèi)容屬于本領(lǐng)域?qū)I(yè)技術(shù)人員的公知技術(shù)。當前第1頁12