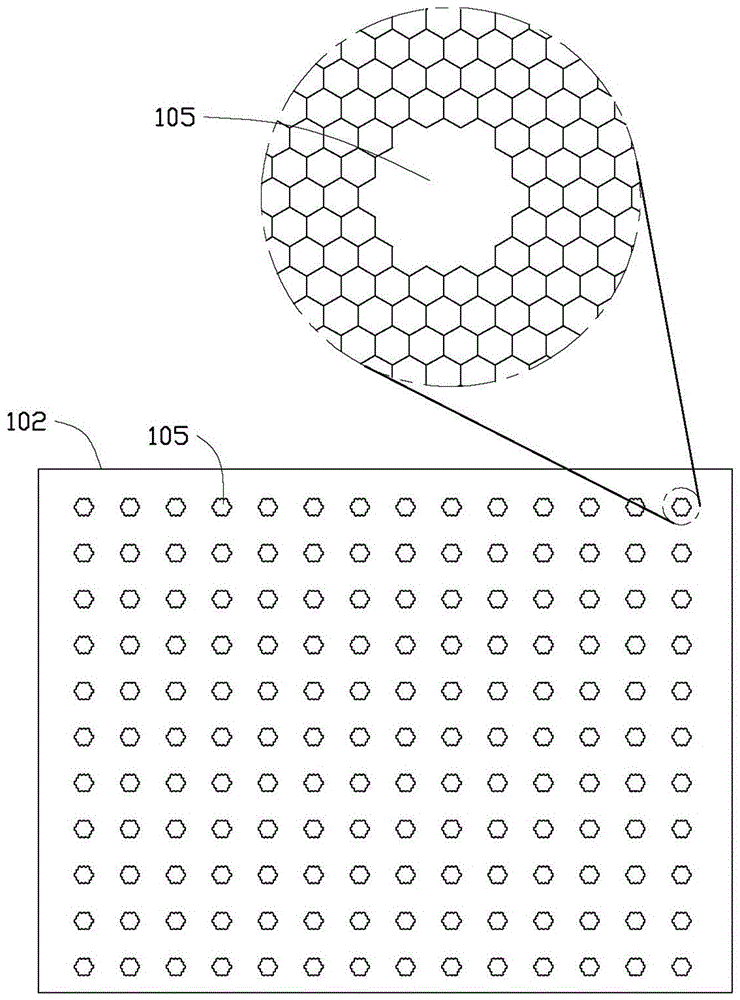
本發(fā)明涉及一種具有微構造的外延結構體。
背景技術:以GaN以及InGaN,AlGaN為主的氮化物形成的具有微構造的外延結構體是近年來備受關注的半導體結構,其連續(xù)可變的直接帶隙,優(yōu)異的物理化學穩(wěn)定性,高飽和電子遷移率等特性,使之成為激光器,發(fā)光二極管等光電子器件和微電子器件的優(yōu)選半導體結構。由于GaN等本身生長技術的限制,現今大面積的GaN半導體層大多生長在藍寶石等其他基底上。由于氮化鎵和藍寶石基底的晶格常數不同,從而導致氮化鎵外延層存在較多位錯缺陷。現有技術提供一種改善上述不足的方法,其采用非平整的藍寶石基底外延生長氮化鎵。然而,現有技術通常采用光刻等微電子工藝在藍寶石基底表面形成溝槽從而構成非平整外延生長面。該方法不但工藝復雜,成本較高,而且會對藍寶石基底外延生長面造成污染,從而影響外延結構的質量。
技術實現要素:綜上所述,確有必要提供一種位錯缺陷較少,且外延層與襯底之間的應力較小的高質量的具有微構造的外延結構體。一種具有微構造的外延結構體,其包括一外延層及一石墨烯層,所述外延層一表面具有多個凹槽及多個凸起以形成一圖案化表面,所述石墨烯層具有多個開口,所述石墨烯層設置于該外延層的圖案化的表面,并嵌入該外延層的多個凹槽中,所述外延層的多個凸起由所述石墨烯層的多個開口露出,所述石墨烯層為具有多個開口的連續(xù)的整體結構體,所述石墨烯層的厚度為一個碳原子厚度。一種具有微構造的外延結構體,其包括層疊設置的一外延層及一具有多個開口的圖案化的單層石墨烯薄膜,外延層的部分滲透所述石墨烯薄膜的多個開口露出,所述開口的尺寸為10納米~120微米,所述圖案化的單層石墨烯薄膜的占空比為1:4~4:1,所述石墨烯層為具有多個開口的連續(xù)的整體結構體,所述石墨烯層的厚度為一個碳原子厚度。與現有技術相比,本發(fā)明提供的具有微構造的外延結構體采用具有多個開口石墨烯層作為掩膜的方式生長外延層,大大降低了具有微構造的外延結構體的制備成本,并且所述石墨烯層具有良好的導電性,使得所述具有微構造的外延結構體具有廣泛用途。附圖說明圖1為本發(fā)明第一實施例提供的具有微構造的外延結構體的制備方法的工藝流程圖。圖2為圖1中采用的第一種圖案化石墨烯層的示意圖。圖3為圖1中采用的第二種圖案化石墨烯層的示意圖。圖4為圖1中采用的第三種圖案化石墨烯層的示意圖。圖5為圖1中采用的第四種圖案化石墨烯層的示意圖。圖6為本發(fā)明第一實施例中采用的碳納米管膜的掃描電鏡照片。圖7為圖6中的碳納米管膜中的碳納米管片段的結構示意圖。圖8為本發(fā)明采用的多層交叉設置的碳納米管膜的掃描電鏡照片。圖9為圖1中外延層的生長過程的示意圖。圖10為本發(fā)明第一實施例提供的具有微構造的外延結構體的示意圖。圖11為圖10所示的具有微構造的外延結構體沿線XI-XI的剖面示意圖。圖12為本發(fā)明第二實施例提供的具有微構造的外延結構體的分解示意圖。圖13為圖12所示的具有微構造的外延結構體整合示意圖。圖14為本發(fā)明第四實施例提供的具有微構造的外延結構體的制備方法的工藝流程圖。主要元件符號說明具有微構造的外延結構體10,20基底100外延生長面101石墨烯層102第一石墨烯層202第二石墨烯層302凹槽1043凸起1045外延層104第一外延層204第二外延層304開口105緩沖層1041外延晶粒1042外延薄膜1044碳納米管片段143碳納米管145如下具體實施方式將結合上述附圖進一步說明本發(fā)明。具體實施方式以下將結合附圖詳細說明本發(fā)明實施例提供的具有微構造的外延結構體及其制備方法。為了便于理解本發(fā)明的技術方案,本發(fā)明首先介紹一種具有微構造的外延結構體的制備方法。請參照圖1,本發(fā)明第一實施例提供一種具有微構造的外延結構體10的制備方法,具體包括一下步驟:S11:提供一基底100,且該基底100具有一外延生長面101;S12:在基底100的外延生長面101生長一緩沖層1041;S13:在所述緩沖層1041的遠離基底100的表面設置一圖案化的石墨烯層102;S14:在設置有石墨烯層102的緩沖層1041表面生長一外延層104;S15,去除所述基底100,得到所述具有微構造的外延結構體10。在步驟S11中,所述基底100提供了生長所述外延層104的外延生長面101。所述基底100的外延生長面101是分子平滑的表面,且去除了氧或碳等雜質。所述基底100可以為單層或多層結構。當所述基底100為單層結構時,該基底100可以為一單晶結構體,且具有一晶面作為外延層104的外延生長面101。所述單層結構的基底100的材料可以為SOI(silicononinsulator,絕緣基底上的硅)、LiGaO2、LiAlO2、Al2O3、Si、GaAs、GaN、GaSb、InN、InP、InAs、InSb、AlP、AlAs、AlSb、AlN、GaP、SiC、SiGe、GaMnAs、GaAlAs、GaInAs、GaAlN、GaInN、AlInN、GaAsP、InGaN、AlGaInN、AlGaInP、GaP:Zn或GaP:N等。當所述基底100為多層結構時,其需要包括至少一層上述單晶結構體,且該單晶結構體具有一晶面作為外延層104的外延生長面101。所述基底100的材料可以根據所要生長的外延層104來選擇,優(yōu)選地,使所述基底100與外延層104具有相近的晶格常數以及熱膨脹系數。所述基底100的厚度、大小和形狀不限,可以根據實際需要選擇。所述基底100不限于上述列舉的材料,只要具有支持外延層104生長的外延生長面101的基底100均屬于本發(fā)明的保護范圍。本實施例中,所述基底100的材料為Al2O3。步驟S12中,所述緩沖層1041的生長方法可以分別通過分子束外延法(MBE)、化學束外延法(CBE)、減壓外延法、低溫外延法、選擇外延法、液相沉積外延法(LPE)、金屬有機氣相外延法(MOVPE)、超真空化學氣相沉積法(UHVCVD)、氫化物氣相外延法(HVPE)、以及金屬有機化學氣相沉積法(MOCVD)等中的一種或多種實現。所述緩沖層1041的材料可以為Si、GaAs、GaN、GaSb、InN、InP、InAs、InSb、AlP、AlAs、AlSb、AlN、GaP、SiC、SiGe、GaMnAs、GaAlAs、GaInAs、GaAlN、GaInN、AlInN、GaAsP、InGaN、AlGaInN、AlGaInP、GaP:Zn或GaP:N。當緩沖層1041根據所要生長的外延層的材料選取,所述緩沖層1041的材料能夠減少所述外延層生長過程中的晶格失配,降低生長的的位錯密度即可。所述緩沖層1041的材料可與基底100的材料相同或不同。本實施例中,采用MOCVD工藝進行外延生長緩沖層1041。其中,采用高純氨氣(NH3)作為氮的源氣,采用氫氣(H2)作載氣,采用三甲基鎵(TMGa)或三乙基鎵(TEGa)、三甲基銦(TMIn)、三甲基鋁(TMAl)作為Ga源、In源和Al源。所述緩沖層1041的生長具體包括以下步驟:首先,將藍寶石基底100置入反應室,加熱到1100℃~1200℃,并通入H2、N2或其混合氣體作為載氣,高溫烘烤200秒~1000秒。其次,繼續(xù)同入載氣,并降溫到500℃~650℃,通入三甲基鎵或三乙基鎵以及氨氣,低溫生長GaN層,所述低溫GaN層作為繼續(xù)生長外延層104的緩沖層1041,其厚度10納米~50納米。在步驟S13中,所述石墨烯層102可以由石墨烯粉末或石墨烯薄膜構成。所述石墨烯粉末為分散的石墨烯顆粒,所述石墨烯薄膜為一連續(xù)的單層碳原子層,即單層石墨烯。當所述石墨烯層102包括石墨烯粉末時,所述石墨烯粉末需要經過溶液分散、涂覆以及刻蝕等圖案化工藝形成圖案化的整體結構。當所述石墨烯層102包括多個石墨烯薄膜時,該多個石墨烯薄膜可以層疊設置或共面設置。所述石墨烯薄膜可以經過切割或刻蝕等工藝處理形成圖案化結構。所述單層石墨烯有著非常獨特的性能。首先,單層石墨烯幾乎完全透明,大約只吸收2.3%的可見光,并可透過大部分紅外線;其次,單層石墨烯厚度僅約為0.34nm,比表面積的理論值為2630m2·g-1,而實測石墨烯的抗拉強度為125GPa,楊氏模量達到了1.0TPa;再次,石墨烯薄膜的熱導率實測值為5300W·m-1·K-1,其載流子遷移率的理論值為2×105cm2·V-1·s-1,而其電阻率只有1×10-6Ω·cm,約為銅的2/3;最后,在室溫下即能觀測到石墨烯薄膜具有量子霍爾效應和無散射傳輸現象。本實施例中,所述石墨烯層102為一純石墨烯結構,即僅包括石墨烯材料。所述石墨烯層102的厚度為1納米~100微米,比如1納米、10納米、200納米,1微米或10微米。可以理解,當所述石墨烯層102為單層石墨烯時,所述石墨烯層102為一個碳原子厚度。優(yōu)選地,所述石墨烯層102為一圖案化結構。當所述石墨烯層102設置在所述緩沖層1041的遠離基板100的表面時,使所述緩沖層1041的遠離基板100的表面通過所述石墨烯層102部分暴露出來,以便于在該所述緩沖層1041暴露出來的部分表面上生長半導體外延層104,即所述石墨烯層102起掩模作用。如圖2~圖4所示,所述“圖案化結構”指所述石墨烯層102為一具有多個開口105的連續(xù)整體結構。當所述石墨烯層102設置在所述緩沖層1041的遠離基板100的表面時,使所述所述緩沖層1041的遠離基板100的表面對應開口105的部分暴露出來。所述多個開口105的形狀不限,可以為圓形、方形、三角形、菱形或矩形等。同一個石墨烯層102的多個開口105的形狀可以相同或不同。所述多個開口105從所述石墨烯層102的厚度方向貫穿所述石墨烯層102。所述開口105可以為如圖2所示的微孔或者如圖3所示的條形的間隙。所述開口105為微孔時其孔徑(平均孔徑)范圍為10納米~500微米,所述開口105為間隙時其寬度(平均寬度)范圍為10納米~500微米。以下稱為“所述開口105的尺寸”是指孔徑或間隙寬度的尺寸范圍。所述石墨烯層102中的微孔和間隙可以同時存在并且兩者尺寸可以在上述尺寸范圍內不同。所述開口105的尺寸可以為10納米~300微米,比如10納米、1微米、10微米、80微米或120微米等。所述開口105的尺寸越小,有利于在生長外延層的過程中減少位錯等缺陷的產生,以獲得高質量的半導體外延層104。優(yōu)選地,所述開口105的尺寸為10納米~10微米。進一步地,所述石墨烯層102的占空比為1:100~100:1,如1:10、1:2、1:4、4:1、2:1或10:1。優(yōu)選地,所述占空比為1:4~4:1。所謂“占空比”指該石墨烯層102設置于所述緩沖層1041的遠離基板100的表面后,該緩沖層1041的遠離基板100的表面被石墨烯層102占據的部分與通過開口105暴露的部分的面積比。本實施例中,所述開口105在所述石墨烯層102中均勻分布。所述“圖案化結構”也可以為設置于基底100表面的多個間隔設置的圖案,且相鄰兩個圖案之間形成多個開口105。當所述石墨烯層102設置在所述緩沖層1041的遠離基板100的表面時,使所述緩沖層1041的遠離基板100的表面對應開口105的部分暴露出來。如圖5所示,所述石墨烯層102為多個平行且間隔設置的石墨烯條帶,相鄰的石墨烯條帶之間為所述開口105。所述石墨烯層102可以直接生長在所述緩沖層1041的遠離基板100的表面或先制備石墨烯后再轉移至所述緩沖層1041的遠離基板100的表面。所述石墨烯粉末可以通過液相剝離法、插層剝離法、剖開碳納米管法、溶劑熱法、有機合成法等方法中的一種或多種制備。所述石墨烯薄膜可以通過化學氣相沉積(CVD)法、機械剝離法、靜電沉積法、碳化硅(SiC)熱解法、外延生長法等方法中的一種或多種制備。本實施例中,參見圖5,所述石墨烯層102為多個間隔設置的條形石墨烯層102,且每個條形石墨烯為多個石墨烯粉末組成的整體結構,其制備方法具體包括以下步驟。首先,制備一石墨烯粉末溶液。所述石墨烯粉末可以通過液相剝離法、插層剝離法、剖開碳納米管法、溶劑熱法、有機合成法等方法制備。所述石墨烯粉末溶液的溶劑可以為水、乙醇、N-甲基吡咯烷酮、四氫呋喃以及2-氮甲基乙酰胺中的一種或多種。所述石墨烯粉末溶液的濃度為1毫克/毫升~3毫克/毫升。其次,在緩沖層1041的遠離基板100的表面形成連續(xù)的石墨烯涂層。本實施例,將石墨烯粉末溶液滴到緩沖層1041的遠離基板100的表面,并進行甩膜旋涂處理,從而得到連續(xù)的石墨烯涂層。所述甩膜旋涂的轉速為3000轉/分鐘~5000轉/分鐘,所述甩膜旋涂的時間為1分鐘~2分鐘。最后,將該連續(xù)的石墨烯涂層圖案化。所述將該連續(xù)的石墨烯涂層圖案化方法包括光催化二氧化鈦切割法、離子束刻蝕法、原子力顯微鏡刻蝕法、以及等離子體刻蝕法中的一種或多種。本實施例中,通過光催化二氧化鈦切割連續(xù)的石墨烯涂層,具體包括以下步驟:(a)制備一圖案化的金屬鈦層;(b)將該圖案化的金屬鈦層加熱氧化得到一圖案化的二氧化鈦層;(c)將該圖案化的二氧化鈦層與連續(xù)的石墨烯涂層接觸,并采用紫外光照射該圖案化的二氧化鈦層;以及(d)去除圖案化的二氧化鈦層??梢岳斫猓摲椒ㄖ?,得到的石墨烯層102的圖案與所述二氧化鈦層的圖案相互嚙合,即所述連續(xù)的石墨烯涂層與二氧化鈦層對應的地方被去除。所述步驟(a)中,所述圖案化的金屬鈦層可以通過掩模蒸鍍法或光刻曝光法制備形成在一石英基底表面。所述石英基底的厚度為300微米~1000微米,所述金屬鈦層的厚度為3納米~10納米。本實施例中,所述石英基底的厚度為500微米,所述金屬鈦層的厚度為4納米。所述圖案化的金屬鈦層為一具有多個間隔設置的條形開口的連續(xù)金屬鈦層。所述步驟(b)中,將圖案化的金屬鈦層在500℃~600℃條件下加熱1小時~2小時。所述步驟(c)中,所述紫外光的波長為200納米~500納米,所述紫外光照射的氣氛為空氣或氧氣,所述紫外光照射的環(huán)境濕度為40%~75%,所述紫外光照射的時間為30分鐘~90分鐘。由于二氧化鈦為光催化半導體材料,在紫外光照射下會產生電子與空穴的分離。該電子與空穴分別被二氧化鈦表面的Ti(IV)和晶格氧所捕獲,從而具有很強的氧化還原能力。被捕獲的電子與空穴很容易氧化還原空氣中的氧氣和水而形成O2和H2O2等活性物質,該活性物質可以將石墨烯分解。所述步驟(d)中,通過將石英基底移開去除圖案化的二氧化鈦層??梢岳斫?,所述步驟(a)中,還可以通過將金屬鈦直接沉積在一圖案化的碳納米管結構表面。該碳納米管結構可以為碳納米管膜,碳納米管線或其組合。當該碳納米管結構為多個碳納米管線時,該多個碳納米管線可以平行間隔或交叉設置,由于碳納米管線之間具有微孔或間隙,所以該多個碳納米管線形成一圖案化結構。當該碳納米管結構為碳納米管膜時,由于碳納米管膜中的碳納米管之間具有微孔或間隙,所以該碳納米管膜形成一圖案化結構。由于金屬鈦層直接沉積在碳納米管膜中的碳納米管表面,所以也形成一圖案化結構。所述步驟(b)中,還可以通過給碳納米管通入電流的方式加熱氧化碳納米管表面的金屬鈦。所述步驟(c)中,與碳納米管對應位置的石墨烯被分解去除形成開口105。即,得到的石墨烯層102的圖案與所述碳納米管結構的圖案相互嚙合。由于碳納米管的直徑僅為0.5納米~50納米,所以可以制備出幾十納米尺寸的開口105。通過選擇碳納米管的直徑可以控制石墨烯層102的開口105的尺寸。該碳納米管結構為一自支撐結構。所謂“自支撐”指該碳納米管結構不需要大面積的載體支撐,而只要相對兩邊提供支撐力即能整體上懸空而保持自身狀態(tài),即將該碳納米管結構置于(或固定于)間隔特定距離設置的兩個支撐體上時,位于兩個支撐體之間的碳納米管結構能夠懸空保持自身狀態(tài)。所述步驟(d)中,由于該碳納米管結構為一自支撐結構,所以通過將碳納米管結構移開,可以方便的去除圖案化的二氧化鈦層。例如,首先,將多個平行間隔設置的碳納米管線表面沉積金屬鈦;然后,通過加熱將金屬鈦氧化形成二氧化鈦;其次,將該多個平行間隔設置的碳納米管線設置于連續(xù)的石墨烯涂層表面,并采用紫外光照射該多個平行間隔設置的碳納米管線;最后,將多個平行間隔設置的碳納米管線去除得到具有多個條形開口的石墨烯層102。所述碳納米管膜可以為一從碳納米管陣列中拉取獲得自支撐結構。參見圖6和圖7,具體地,所述碳納米管膜包括多個連續(xù)且定向延伸的碳納米管片段143。該多個碳納米管片段143通過范德華力首尾相連。每一碳納米管片段143包括多個相互平行的碳納米管145,該多個相互平行的碳納米管145通過范德華力緊密結合。該碳納米管片段143具有任意的長度、厚度、均勻性及形狀。所述碳納米管膜可通過從一碳納米管陣列中選定部分碳納米管后直接拉取獲得。所述碳納米管膜的厚度為1納米~100微米,寬度與拉取出該碳納米管膜的碳納米管陣列的尺寸有關,長度不限。所述碳納米管膜中相鄰的碳納米管之間存在微孔或間隙,且該微孔的孔徑或間隙的尺寸小于10微米。優(yōu)選地,所述碳納米管膜的厚度為100納米~10微米。該碳納米管膜中的碳納米管145沿同一方向擇優(yōu)取向延伸。所述碳納米管膜及其制備方法具體請參見申請人于2007年2月9日申請的,于2010年5月26日公告的第CN101239712B號中國公開專利“碳納米管膜結構及其制備方法”。為節(jié)省篇幅,僅引用于此,但上述申請所有技術揭露也應視為本發(fā)明申請技術揭露的一部分。請參閱圖8,當多層碳納米管膜層疊設置時,相鄰兩層碳納米管膜中的碳納米管的延伸方向形成一交叉角度α,且α大于等于0度小于等于90度(0°≤α≤90°)。所述石墨烯層102還可以為一包括石墨烯以及添加材料的復合結構。所述添加材料包括碳納米管、碳化硅、氮化硼、氮化硅、二氧化硅、無定形碳等中的一種或多種。所述添加材料還可以包括金屬碳化物、金屬氧化物及金屬氮化物等中的一種或多種。所述添加材料可以通過化學氣相沉積(CVD)、物理氣相沉積(PVD)、磁控濺射等方法形成于石墨烯的表面??梢岳斫猓緦嵤├?,也可以先對緩沖層1041的遠離基板100的表面進行表面處理形成石墨烯浸潤區(qū)域與石墨烯不浸潤區(qū)域,然后涂敷石墨烯層直接形成圖案化的石墨烯層102。所述表面處理的方法為自組裝分子法、臭氧處理法、氧等離子處理法、氬等離子處理法、紫外光照法、以及蒸鍍法中的一種或多種。所述石墨烯層102還可以為一包括石墨烯以及添加材料的復合結構。所述添加材料包括碳納米管、碳化硅、氮化硼、氮化硅、二氧化硅、無定形碳等中的一種或多種。所述添加材料還可以包括金屬碳化物、金屬氧化物及金屬氮化物等中的一種或多種。所述添加材料可以通過化學氣相沉積(CVD)、物理氣相沉積(PVD)、磁控濺射等方法形成于石墨烯的表面。以上內容可知,所述石墨烯層102起著生長半導體外延層104的掩模作用。所謂“掩模”是指該石墨烯層102用于遮擋所述緩沖層1041的部分表面,且暴露部分緩沖層1041的表面,從而使得半導體外延層104僅從所述緩沖層1041的表面的暴露的部分生長。由于石墨烯層102具有多個開口105,所以該石墨烯層102形成一圖案化的掩模。由于所述石墨烯層102在所述緩沖層1041的遠離基板100的表面形成多個開口105,從而使得所述緩沖層1041的遠離基板100的表面上具有一圖案化的掩模??梢岳斫?,相對于光刻等微電子工藝,通過設置石墨烯層102作為掩模進行外延生長的方法工藝簡單、成本低廉,不易在基底100的外延生長面101引入污染,而且綠色環(huán)保。可以理解,所述基底100、緩沖層1041和石墨烯層102共同構成了用于生長異質外延結構的襯底。該襯底可用于生長外延層104,如半導體外延層、金屬外延層或合金外延層。該襯底也可用于生長同質外延層,從而得到一同質外延結構。步驟S14中,所述外延層104的生長方法可以分別通過分子束外延法(MBE)、化學束外延法(CBE)、減壓外延法、低溫外延法、選擇外延法、液相沉積外延法(LPE)、金屬有機氣相外延法(MOVPE)、超真空化學氣相沉積法(UHVCVD)、氫化物氣相外延法(HVPE)、以及金屬有機化學氣相沉積法(MOCVD)等中的一種或多種實現,所述外延層104的材料可以與緩沖層1041的材料相同或者不同。所述外延層104的生長的厚度可以根據需要制備。具體地,所述外延層104的生長的厚度可以為0.5納米~1毫米。例如,所述外延層104的生長的厚度可以為100納米~500微米,或200納米~200微米,或500納米~100微米。所述外延層104的材料為半導體材料,如Si、GaAs、GaN、GaSb、InN、InP、InAs、InSb、AlP、AlAs、AlSb、AlN、GaP、SiC、SiGe、GaMnAs、GaAlAs、GaInAs、GaAlN、GaInN、AlInN、GaAsP、InGaN、AlGaInN、AlGaInP、GaP:Zn或GaP:N??梢岳斫?,所述外延層104的材料也可以為金屬或合金等其他材料,只要保證所述材料可用上述生長方法如MBE、CBE、MOVPE等方法生長即可。本實施例中,生長所述外延層104時采用的所述石墨烯層102為一圖案化的單層石墨烯薄膜。所述外延層104的制備方法為,在生長完緩沖層1041的工藝條件下,將設置有石墨烯層102及緩沖層1041的基底100的溫度保持在1000℃~1100℃,持續(xù)通入氨氣和載氣,同時通入三甲基鎵或三乙基鎵,在高溫下生長出高質量的外延層104。具體的,參見圖9所述外延層104的制備方法包括以下步驟:S141:沿著基本垂直于所述緩沖層1041表面的方向成核并外延生長形成多個外延晶粒1042;S142:所述多個外延晶粒1042沿著基本平行于所述緩沖層1041表面的方向外延生長形成一連續(xù)的外延薄膜1044;S143:所述外延薄膜1044沿著基本垂直于所述緩沖層1041表面的方向外延生長形成一外延層104。在步驟S141,由于石墨烯層102設置于所述緩沖層1041表面,因此外延晶粒僅從所述緩沖層1041暴露的部分生長,即外延晶粒從石墨烯層102的開口105處生長出來。在步驟S142中,通過控制生長條件使所述多個外延晶粒1042沿著基本平行于所述基底100的外延生長面101的方向同質外延生長并連成一體將所述石墨烯層102覆蓋。即,該步驟中所述多個外延晶粒1042進行側向外延生長直接合攏,并最終形成多個凹槽1043將石墨烯層102包圍。所述凹槽1043的形狀與石墨烯層102的圖案有關。步驟S143中,由于所述石墨烯層102的存在,使得外延晶粒1042與基底100之間的晶格位錯在形成連續(xù)的外延薄膜1044的過程中停止生長。因此,該步驟的外延層104相當于在沒有缺陷的外延薄膜1044表面進行同質外延生長。步驟S15中,所述基底100的去除方法可為激光照射法、腐蝕法或溫差自剝離法。所述去除方法可根據基底100以及外延層104材料的不同進行選擇。本實施例中,所述基底100的去除方法為激光照射法。具體的,所述去除方法包括以下步驟:S151,將所述基底100中未生長外延層104的表面進行拋光并清洗;S152,將經過表面清洗的基底100放置于一平臺(圖未示)上,并利用激光對所述基底100與外延層104進行掃描照射;S153,將經激光照射后的基底100浸入溶液中去除所述基底100,形成所述具有微構造的外延結構體10。在步驟S151中,所述拋光方法可為機械拋光法或化學拋光法,使所述基底100的表面平整光滑,以減少后續(xù)激光照射中激光的散射。所述清洗可用鹽酸、硫酸等沖洗所述基底100的表面,從而去除表面的金屬雜質以及油污等。在步驟S152中,所述激光從基底100拋光后的表面入射,且入射方向基本垂直于所述基底100拋光后的表面,即基本垂直于所述基底100與外延層104的界面。所述激光的波長不限,可根據緩沖層1041以及基底100的材料選擇。具體的,所述激光的能量小于基底100的帶隙能量,而大于緩沖層1041的帶隙能量,從而激光能夠穿過基底100到達緩沖層1041,在緩沖層1041與基底100的界面處進行激光剝離。所述界面處的緩沖層1041對激光產生強烈的吸收,從而使得界面處的緩沖層1041溫度快速升高而分解。本實施例中所述外延層104為GaN,其帶隙能量為3.3ev;基底100為藍寶石,其帶隙能量為9.9ev;所述激光器為KrF激光器,發(fā)出的激光波長為248nm,其能量為5ev,脈沖寬度為20~40ns,能量密度為400~600mJ/cm2,光斑形狀為方形,其聚焦尺寸為0.5mm×0.5mm;掃描位置從所述基底100的邊緣位置開始,掃描步長為0.5mm/s。在掃描的過程中,所述GaN緩沖層1041開始分解為Ga和N2??梢岳斫?,所述脈沖寬度、能量密度、光斑形狀、聚焦尺寸以及掃描步長可根據實際需求進行調整;可根據緩沖層1041對特定波長的激光具有較強的吸收作用選擇相應波長的激光。由于所述GaN緩沖層1041對上述波長的激光具有很強的吸收作用,因此,所述緩沖層1041的溫度快速升高而分解;而所述外延層104對上述波長的激光吸收較弱或不吸收,因此所述外延層104并不會被所述激光所破壞。可以理解,對于不同的緩沖層1041可以選擇不同波長的激光,使緩沖層1041對激光具有很強的吸收作用。所述激光照射的過程在一真空環(huán)境或保護性氣體環(huán)境進行以防止在激光照射的過程中石墨烯層102被氧化而破壞。所述保護性氣體可以為氮氣、氦氣或氬氣等惰性氣體。在步驟S153中,可將激光照射后的基底100及外延層104浸入一酸性溶液中,以去除GaN分解后的Ga,從而實現基底100與外延層104的剝離,形成所述具有微構造的外延結構體10。所述溶液可為鹽酸、硫酸、硝酸等可溶解Ga的溶劑。由于緩沖層1041的存在,一方面,所述緩沖層1041設置在石墨烯層102與基底100之間,將所述石墨烯層102與基底100隔離開,因此在剝離基底100的過程中,所述石墨烯層102不會直接吸附于基底100上而從外延層104中剝離;另一方面,在激光照射緩沖層1041的過程中,所述緩沖層1041受熱分解并經溶液溶解后,石墨烯層102會與所述緩沖層1041脫離,從而使得所述石墨烯層102保留于凹槽1043中。進一步的,在緩沖層1041受熱分解的過程中,緩沖層1041分解產生的氣體受熱膨脹,會將石墨烯層102推離所述緩沖層1041與基底100,從而使得石墨烯層102更容易與緩沖層1041分離。由于石墨烯層102的存在,使外延層104與緩沖層1041之間的接觸面積減小,從而減小了生長過程中外延層104與緩沖層1041之間的應力。因此,在激光照射去除基底100的過程中,使得緩沖層1041及基底100的剝離更加的容易,也減小了對外延層104的損傷。所述S15步驟結束后得到一具有微構造的外延結構體10,其包括一外延層104及一石墨烯層102,所述外延層104一表面具有多個凹槽1043,所述石墨烯層102設置于該外延層104的圖案化的表面,并嵌入該外延層104的多個凹槽1043。如圖10及圖11所示,本發(fā)明進一步提供一種由上述方法制備的具有微構造的外延結構體10,所述具有微構造的外延結構體10包括一外延層104及一石墨烯層102,所述外延層104一表面具有多個凹槽1043及多個凸起1045以形成一圖案化表面,所述石墨烯層102為具有多個開口105的連續(xù)的整體結構體,所述石墨烯層102設置于該外延層104的圖案化的表面,并嵌入該外延層104的多個凹槽1043中,所述外延層104的多個凸起1045由所述石墨烯層102的多個開口105露出。所述具有微構造的外延結構體10是指所述外延層104表面具有由多個凹槽1043和多個凸起1045間隔形成的微結構,所述微結構是在外延層104生長過程中,外延層104從石墨烯層102中的開口位置生長,之后圍繞石墨烯層102進行側向外延生長所形成,將基底100剝離后,在所述外延層104的表面形成多個凹槽1043和多個凸起1045。本實施例提供的具有微構造的外延結構體,由于所述石墨烯層102直接暴露于外延層104的表面,因此所述石墨烯層102可以直接作為具有微構造的外延結構體10的大面積電極,從而可以改善具有微構造的外延結構體10中的電場分布及電流走向,進而提高具有微構造的外延結構體10的工作效率。本發(fā)明第二實施例提供另一種具有微構造的外延結構體10的制備方法,具體包括以下步驟:S21,提供一基底100,且該基底100具有一支持外延層104生長的外延生長面101;S22,在基底100的外延生長面101生長一緩沖層1041;S23,在所述緩沖層1041的遠離基底100的表面平鋪一石墨烯層102;S24,在設置有石墨烯層102的緩沖層1041表面生長外延層104;S25,將基底浸入腐蝕溶液中,剝離所述基底100,得到所述具有微構造的外延結構體10。本發(fā)明第二實施例的具有微構造的外延結構體10的制備方法與第一實施例的制備方法基本相同,其區(qū)別在于,本實施例中所述基底100的材料為SiC,外延生長面101上生長的緩沖層1041為AlN或TiN,外延層104為GaN,并且所述去除方法為腐蝕法。本發(fā)明第二實施例中采用單層石墨烯薄膜制備石墨烯層202制備石墨烯層102,其制備方法包括以下步驟。具體的,在步驟S23中,該石墨烯層102的制備方法包括以下步驟:首先,制備一單層石墨烯薄膜。本實施例中,采用CVD法制備單層石墨烯薄膜,具體包括以下步驟:(a1)提供一襯底;(b1)在襯底上沉積金屬催化劑層;(c1)對金屬催化劑層進行退火處理;以及(d1)在碳源氣氛中生長單層石墨烯薄膜。所述步驟(a1)中,所述襯底可以為銅箔或Si/SiO2。本實施例中,所述襯底為Si/SiO2。所述Si層的厚度為300微米~1000微米,所述SiO2層的厚度為100納米~500納米。優(yōu)選地,所述Si層的厚度為600微米,所述SiO2層的厚度為300納米。所述步驟(b1)中,所述金屬催化劑層的材料包括鎳、鐵、金等,所述金屬催化劑層的厚度為100納米~800納米。所述金屬催化劑層可以通過化學氣相沉積(CVD)、物理氣相沉積(PVD)、磁控濺射或電子束蒸鍍等方法制備。本實施例中,采用電子束蒸鍍法在SiO2層表面沉積一厚度為500納米的金屬鎳。所述步驟(c1)中,所述退火溫度為900℃~1000℃;所述退火的氣氛為氬氣和氫氣混合氣體,其中氬氣的流量為600sccm,氫氣的流量為500sccm;所述退火時間為10分鐘~20分鐘。所述步驟(d1)中,所述生長溫度為900℃~1000℃;所述碳源氣為甲烷;所述生長時間為5分鐘~10分鐘。其次,將該單層石墨烯薄膜轉移至所述緩沖層1041的遠離基底100的表面。本實施例中,具體包括以下步驟:(a2)在單層石墨烯薄膜表面涂覆有機膠體或聚合物作為支撐體;(b2)對涂覆有機膠體或聚合物的單層石墨烯薄膜烘烤堅膜;(c2)將堅膜后的單層石墨烯薄膜以及Si/SiO2襯底一起浸泡在去離子水中使金屬催化劑層和SiO2層分離;(d2)將分離后的支撐體/單層石墨烯薄膜/金屬催化劑層復合結構去除金屬催化劑層;(e2)將支撐體/單層石墨烯薄膜復合結構設置在外延生長面101,并加熱使單層石墨烯薄膜與所述緩沖層1041牢固結合;以及(f2)去除支撐體。所述步驟(a2)中,所述支撐體的材料為聚甲基丙烯酸甲酯(PMMA)、聚二甲基硅氧烷、光刻正膠9912、光刻膠AZ5206中的一種或多種。所述步驟(b2)中,所述烘烤的溫度為100℃~185℃。所述步驟(c2)中,浸泡在去離子水中之后,對所述金屬催化劑層和SiO2層進行超聲處理。所述步驟(d2)中,通過化學液腐蝕去除金屬催化劑層,該化學液可以為硝酸、鹽酸、氯化鐵(FeCl3)、硝酸鐵(Fe(NO3)3)等。所述步驟(f2)中,去除支撐體的方法為先用丙酮和乙醇浸泡,然后在保護氣體中加熱到約400℃。最后,將該單層石墨烯薄膜圖案化。所述將該單層石墨烯薄膜圖案化方法包括光催化二氧化鈦切割法、離子束刻蝕法、原子力顯微鏡刻蝕法、以及等離子體刻蝕法中的一種或多種。本實施例中,先將一陽極氧化鋁模板(AnodicAluminumOxideTemplate)設置于該單層石墨烯薄膜表面,然后通過等離子體刻蝕法將該單層石墨烯薄膜圖案化。其中,所述陽極氧化鋁模板具有多個成陣列排布的微孔,與陽極氧化鋁模板微孔對應處的單層石墨烯薄膜被等離子體刻蝕去除,從而得到的石墨烯層102為一具有多個微孔的連續(xù)單層石墨烯薄膜。在步驟S24中,將所述生長有外延層104的基底100浸入到相應的腐蝕溶液中,使得所述緩沖層1041在溶液中溶解,從而實現基底100的分離。所述溶液可根據緩沖層1041以及外延層104的材料進行選擇,即所述溶液可溶解緩沖層1041而不能溶解外延層104。所述溶液可為NaOH溶液、KOH溶液、NH4OH溶液等,本實施例中,所述溶液為KOH溶液。所述KOH溶液的質量濃度可為30%~50%,浸入時間為2分鐘~10分鐘,使得KOH溶液浸入到外延層104的凹槽1043中,逐漸腐蝕掉AlN緩沖層,使得SiC基底脫落。由于石墨烯層102與凹槽1043部分接觸,石墨烯具有較強的吸附作用,因此在緩沖層1041腐蝕的過程中,所述AlN逐漸在KOH溶液中溶解而從石墨烯層102表面脫離,從而使所述石墨烯層102吸附于凹槽1043中,得到所述具有微構造的外延結構體10??梢岳斫猓鼍彌_層1041以及溶液的材料不限于以上所舉,只要保證溶液能夠溶解緩沖層1041而不能溶解外延層104即可。如當所述緩沖層為TiN時,所述溶液可為硝酸。進一步的,所述腐蝕法中,也可以直接將基底100溶解去除,從而在溶解的過程中,所述緩沖層1041以及基底100能夠同時被溶解,使得石墨烯層102暴露于外延層104的表面??梢岳斫猓绻苯訉⒒?00溶解去除,也可以省去生長緩沖層的步驟。所述腐蝕法中,由于石墨烯層102的存在,石墨烯層102與緩沖層1041之間存在多個凹槽或間隙,從而能夠使相應的溶液均勻的分散到緩沖層1041中將緩沖層1041溶解而實現快速的剝離,能夠更好保持所述具有微構造的外延結構體的剝離表面的平整和光滑。請參閱圖12及13,為本發(fā)明第二實施例制備獲得的具有微構造的外延結構體10,其包括:一外延層104及一石墨烯層102。本發(fā)明第二實施例中的具有微構造的外延結構體10與第一實施例的其區(qū)別在于,本發(fā)明第二實施例的石墨烯層102為一圖案化的單層石墨烯薄膜。本發(fā)明第三實施例提供一種具有微構造的外延結構體10的制備方法,具體包括一下步驟:S31,提供一基底100,且該基底100具有一支持外延層104生長的外延生長面101;S32,在基底100的外延生長面101生長一緩沖層1041;S33,在所述緩沖層1041的遠離基底100的表面平鋪一石墨烯層102;S34,在設置有石墨烯層102的緩沖層1041表面生長外延層104;S35,對所述生長有外延層104的基底100降溫,剝離所述基底100,得到所述具有微構造的外延結構體10。本發(fā)明第三實施例的具有微構造的外延結構體10的制備方法與第一實施例的半導體層的制備方法基本相同,其區(qū)別在于,在步驟S33中,直接將石墨烯粉末分散在緩沖層1041表面。在步驟S35中,所述剝離方法為溫差分離法。所述溫差分離法為在高溫生長GaN完成之后,將所述高溫的基底100的溫度在2min~20min的時間內,快速的降低到200℃以下,利用外延層104與基底100之間的由于熱膨脹系數的不同而產生的應力將二者分離。可以理解,該方法中也可以通過給石墨烯層102通入電流的方式加熱外延層104與基底100,再降溫從而實現剝離。在剝離基底100的過程中,所述石墨烯層102吸附于凹槽1043中而不會脫落。這是因為一方面所述石墨烯層102為一整體結構,其與凹槽1043之間存在接觸;另一方面,所述石墨烯層102嵌入外延層104中,凹槽1043將石墨烯層102半包圍起來;第三,所述基底100可沿著平行于外延層104圖案化表面的方向剝離,使得石墨烯層102保留于凹槽1043中。進一步的,在所述外延層104從基底100上分離之后,可包括一在外延層104的表面繼續(xù)側向生長外延層的步驟。所述進一步生長外延層的步驟可以減少在基底100分離的過程中,外延層104上產生裂紋。如圖14所示,本發(fā)明第四實施例提供一種具有微構造的外延結構體20的制備方法,主要包括以下步驟:S41,提供一基底100,且該基底100具有一支持外延層204生長的外延生長面101;S42,在基底100的外延生長面101生長一緩沖層1041;S43,在所述緩沖層1041的遠離基底100的表面平鋪一第一石墨烯層202;S44,在設置有第一石墨烯層202的緩沖層1041表面生長第一外延層204;S45,在所述第一外延層204遠離基底100的表面進一步設置一第二石墨烯層302;S46,在所述第一外延層204遠離基底100的表面進一步生長一第二外延層304;S47,剝離所述基底100,得到所述具有微構造的外延結構體20。本發(fā)明第四實施例提供的具有微構造的外延結構體10的制備方法與第一實施例基本相同,其不同在于,在所述第一外延層204遠離緩沖層1041的表面進一步鋪設一第二石墨烯層302的步驟S45,以及進一步生長一第二外延層304的步驟S46。所述第二石墨烯層302與第一外延層204接觸設置,并且所述第二外延層304覆蓋所述第二石墨烯層302生長,將第二石墨烯層302夾持于第一外延層204以及第二外延層304之間,并使第二石墨烯層302嵌入所述第二外延層304中。由于第二石墨烯層302的存在,所述第二外延層304靠近第一外延層204的表面形成多個凹槽1043,所述第二石墨烯層302設置于該凹槽1043內。所述多個凹槽1043在第二外延層304的表面形成一“圖案化”的結構,且所述第二外延層304的圖案化表面與圖案化第二石墨烯層302中的圖案基本相同。所述第二石墨烯層302與第二外延層304分別與所述第一石墨烯層202以及第一外延層204的結構基本相同,所述第二外延層304的材料可以與第一外延層204相同或不同??梢岳斫猓€可以在所述第二外延層304的表面繼續(xù)設置石墨烯層,并進一步生長外延層,從而形成具有多個外延層以及多個石墨烯層的復合結構。所述多個外延層的材料可以相同也可以不同,且多個石墨烯層可以作為不同的電極,使所述具有微構造的外延結構體可以方便的應用于不同的電子器件。本發(fā)明采用一石墨烯層作為掩模設置于所述基底外延生長面生長外延層具有以下有以效果:第一,所述石墨烯層可直接鋪設或轉移在基底的外延生長面,相對于現有技術通過沉積后再光刻等工藝形成掩模,本發(fā)明工藝簡單,成本低廉,有利于量產。第二,所述石墨烯層為圖案化結構,其厚度、開口尺寸均可達到納米級,所述襯底用來生長外延層時形成的異質外延晶粒具有更小的尺寸,有利于減少位錯缺陷的產生,以獲得高質量的異質外延層。第三,所述石墨烯層的開口尺寸為納米級,所述外延層從與納米級開口對應的暴露的外延生長面生長,使得生長的外延層與基底之間的接觸面積減小,減小了生長過程中外延層與襯底之間的應力,從而可以生長厚度較大的異質外延層,可進一步提高異質外延層的質量;同時,由于石墨烯層具有多個開口,減小了外延層與緩沖層之間的接觸面積,因此,在剝離基底的過程中,使得基底的剝離更加的容易,也減小了對外延層的損傷。另外,本領域技術人員還可在本發(fā)明精神內作其它變化,當然這些依據本發(fā)明精神所作的變化,都應包含在本發(fā)明所要求保護的范圍內。