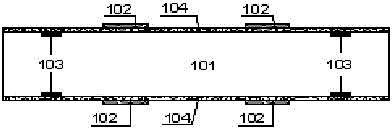
本發(fā)明涉及晶閘管技術(shù)領(lǐng)域,更具體的說(shuō)涉及一種平面工藝的晶閘管、用于制造晶閘管的芯片及其制作方法。
背景技術(shù):電力半導(dǎo)體器件晶閘管,主要包括外殼、芯片、框架三部分,其核心部分在于芯片,芯片的陽(yáng)極焊接在框架上,芯片的門極和陰極分別通過(guò)導(dǎo)線連接到框架相應(yīng)的管腳上,外殼起到保護(hù)芯片的作用。晶閘管芯片的制造方法按工藝分類可以分為:臺(tái)面工藝和平面工藝,臺(tái)面工藝又分為雙臺(tái)面工藝和單臺(tái)面工藝;1.雙臺(tái)面工藝:由于雙臺(tái)面工藝不采用隔離擴(kuò)散,工藝相對(duì)簡(jiǎn)單。但是:①該結(jié)構(gòu)的硅片在生產(chǎn)制造過(guò)程中容易破碎;②臺(tái)面的鈍化保護(hù)(半絕緣多晶硅SIPOS+玻璃鈍化+低溫氧化物L(fēng)TO)所需成本較高及工藝控制難度較大;③硅片在使用砂輪劃切的情況下其劃切效率極低,且容易造成芯片破損。④芯片在封裝制造過(guò)程中,粘片空洞率較大導(dǎo)致芯片可靠性降低,焊錫溢出至背面溝槽內(nèi)導(dǎo)致反向電壓失效,產(chǎn)品合格率降低。2.單臺(tái)面工藝:?jiǎn)闻_(tái)面工藝采用對(duì)通隔離技術(shù)形成隔離保護(hù)墻,隔離保護(hù)墻與芯片陽(yáng)極相連,與陰極共用槽型臺(tái)面實(shí)現(xiàn)正反向耐壓。與此同時(shí),隔離墻也是隔離相鄰芯片的公共區(qū)域和劃切區(qū)域,使得芯片在制造及封裝過(guò)程中有效克服雙面刻槽腐蝕法的缺點(diǎn)。3.平面工藝:與單臺(tái)面工藝類似,平面工藝也采用對(duì)通隔離技術(shù)形成隔離保護(hù)墻,N型高阻區(qū)和場(chǎng)限環(huán)將隔離保護(hù)墻與P型主結(jié)隔離開(kāi)(即結(jié)終端結(jié)構(gòu)),以實(shí)現(xiàn)正反向耐壓。通常在結(jié)終端處表面刻蝕一個(gè)較淺的鈍化槽,鈍化槽內(nèi)采用SIPOS+LTO(或氮化硅薄膜)+聚酰亞胺多層鈍化工藝,有效確保產(chǎn)品良好的可靠性和一致性。上述單臺(tái)面工藝和平面工藝都需要隔離保護(hù)墻對(duì)芯片進(jìn)行保護(hù),目前,實(shí)現(xiàn)半導(dǎo)體功率器件對(duì)通隔離的方法有以下兩種:濃硼隔離擴(kuò)散法、激光穿孔法。但兩種方法各自都存在不足之處:⑴濃硼隔離擴(kuò)散法:①由于硼在硅中的雜質(zhì)擴(kuò)散系數(shù)很慢(擴(kuò)散溫度為1200~1300℃條件下:硼擴(kuò)散系數(shù)約為1*10-11cm2/S,而鋁擴(kuò)散系數(shù)約為8*10-11cm2/S),硅片的厚度只能限制在250μm以下,這使得采用濃硼隔離擴(kuò)散的器件只能實(shí)現(xiàn)1200V以下的耐壓。②濃硼隔離擴(kuò)散的擴(kuò)散溫度較高,一般在1250℃~1300℃,擴(kuò)散時(shí)間需要120-200小時(shí)。過(guò)高的擴(kuò)散溫度及過(guò)長(zhǎng)的擴(kuò)散時(shí)間使得產(chǎn)品的少子壽命縮短,還會(huì)造成擴(kuò)散缺陷的增多,致使產(chǎn)品的穩(wěn)定性、可靠性降低,漏電流增大。同時(shí)還造成生產(chǎn)周期過(guò)長(zhǎng)、耗能高。③濃硼隔離擴(kuò)散造成對(duì)通隔離區(qū)雜質(zhì)濃度偏高(一般表面濃度R□≤10),PN結(jié)耗盡層寬度降低,導(dǎo)致產(chǎn)品的反向阻斷電壓降低。④濃硼隔離擴(kuò)散的橫向擴(kuò)散較大,通常為擴(kuò)散深度的80%,減小了芯片的有效面積,降低了產(chǎn)品的通態(tài)電流。⑵激光穿孔法:利用紫外激光束以一定的間距在芯片周圍的隔離墻上垂直穿孔(激光孔直徑可以調(diào)節(jié)),達(dá)到加快隔離墻形成速度的目的。但是,該方法也有以下不足:①單片硅片激光穿孔造型最少需要30分鐘,特別是芯片版面較小的產(chǎn)品所需時(shí)間更長(zhǎng)(達(dá)到1.5小時(shí)),批量生產(chǎn)難度較大。后續(xù)經(jīng)過(guò)拋光等工序加工,容易造成碎片,產(chǎn)品合格率低。②激光孔的直徑通常較小(直徑一般為30-100μm),孔內(nèi)殘留的硅渣很難去除,容易造成污染,影響產(chǎn)品性能。③由于隔離墻上設(shè)有垂直的激光孔,后續(xù)玻璃鈍化保護(hù)時(shí),玻璃填覆在激光孔內(nèi),芯片劃切時(shí)容易造成玻璃膜裂紋,降低產(chǎn)品的合格率和可靠性。
技術(shù)實(shí)現(xiàn)要素:本發(fā)明的目的在于:提供一種用于構(gòu)成平面晶閘管的芯片,通過(guò)兩種采用蒸發(fā)金屬鋁膜實(shí)現(xiàn)對(duì)通隔離的方法來(lái)制造該晶閘管芯片,進(jìn)而利用該晶閘管芯片來(lái)生產(chǎn)一種成本低、生產(chǎn)周期短、耗能及污染少性能優(yōu)越、穩(wěn)定可靠的平面晶閘管。為了達(dá)到上述目的,本發(fā)明的一個(gè)技術(shù)方案是提供一種用于制造平面晶閘管的芯片;該芯片用于制造單向晶閘管時(shí),包含:位于芯片中間的N型長(zhǎng)基區(qū)N1,設(shè)置在N型長(zhǎng)基區(qū)N1下側(cè)的第一P型短基區(qū)P1,設(shè)置在N型長(zhǎng)基區(qū)N1上側(cè)的第二P型短基區(qū)P2;設(shè)置在第二P型短基區(qū)P2上的第一擴(kuò)磷區(qū)域N2,設(shè)置在第一擴(kuò)磷區(qū)域N2上的陰極;設(shè)置在第二P型短基區(qū)P2上的門極;設(shè)置在第一P型短基區(qū)P1上的陽(yáng)極;設(shè)置在N型長(zhǎng)基區(qū)N1周邊的隔離墻,設(shè)置在第二P型短基區(qū)P2與隔離墻之間的場(chǎng)限環(huán),其特征在于:所述隔離墻由蒸發(fā)金屬鋁擴(kuò)散形成。該芯片用于制造雙向晶閘管芯片時(shí),進(jìn)一步在所述第一P型短基區(qū)P1上還設(shè)置有第三擴(kuò)磷區(qū)域N4;則所述陽(yáng)極設(shè)置在所述第一P型短基區(qū)P1和所述第三擴(kuò)磷區(qū)域N4上;在所述第二P型短基區(qū)P2上還設(shè)置有第二擴(kuò)磷區(qū)域N3;則所述門極設(shè)置在所述第二擴(kuò)磷區(qū)域N3上,而所述陰極設(shè)置在所述第一擴(kuò)磷區(qū)域N2和所述第二P型短基區(qū)P2上。該芯片用于制造單向晶閘管或雙向晶閘管芯片時(shí),在所述隔離墻上設(shè)置有劃切區(qū)域;在所述門極與陰極之間,所述劃切區(qū)域與陰極之間,和所述劃切區(qū)域與門極之間,都設(shè)置有氧化層、鈍化薄膜及聚酰亞胺薄膜。本發(fā)明的另一個(gè)技術(shù)方案是提供一種用于制造平面晶閘管的芯片的制作方法,所述芯片用于制造單向晶閘管時(shí),包含:位于芯片中間的N型長(zhǎng)基區(qū)N1,設(shè)置在N型長(zhǎng)基區(qū)N1下側(cè)的第一P型短基區(qū)P1,設(shè)置在N型長(zhǎng)基區(qū)N1上側(cè)的第二P型短基區(qū)P2;設(shè)置在第二P型短基區(qū)P2上的第一擴(kuò)磷區(qū)域N2,設(shè)置在第一擴(kuò)磷區(qū)域N2上的陰極;設(shè)置在第二P型短基區(qū)P2上的門極;設(shè)置在第一P型短基區(qū)P1上的陽(yáng)極;設(shè)置在N型長(zhǎng)基區(qū)N1周邊的隔離墻,設(shè)置在第二P型短基區(qū)P2與隔離墻之間的場(chǎng)限環(huán),其特征在于:所述芯片的隔離墻是經(jīng)過(guò)第一方法或第二方法形成的,其中,所述第一方法包含以下步驟:硅片雙面經(jīng)過(guò)噴砂、光刻腐蝕對(duì)版標(biāo)記、蒸發(fā)金屬鋁后,進(jìn)行反刻金屬鋁以保留對(duì)應(yīng)隔離墻位置上的金屬鋁,再進(jìn)行真空合金后,經(jīng)過(guò)對(duì)通隔離擴(kuò)散形成所述的隔離墻;所述第二方法包含以下步驟:硅片雙面經(jīng)過(guò)氧化、光刻隔離窗口、沉積多晶硅薄膜及蒸發(fā)金屬鋁后,進(jìn)行金屬鋁反刻以保留隔離窗口上的金屬鋁,再通過(guò)對(duì)通隔離擴(kuò)散形成所述的隔離墻。所述第一方法中,雙面蒸發(fā)金屬鋁膜的厚度為0.2~1.0μm;反刻金屬鋁膜后,保留在對(duì)應(yīng)隔離墻位置上的金屬鋁寬度為80~200μm;真空合金時(shí),合金溫度480~520℃,合金時(shí)間20~40分鐘;對(duì)通隔離擴(kuò)散時(shí),擴(kuò)散溫度1200~1280℃,擴(kuò)散時(shí)間20~60小時(shí),以實(shí)現(xiàn)硅片厚度為200-500μm的對(duì)通隔離;擴(kuò)散氣氛:氮?dú)馀c氧氣比例5:1~10:1,其中,氮?dú)饬髁?~6L/min,氧氣流量0.2~0.6L/min,升溫速率3~5℃/min、降溫速率1~3℃/min;形成的隔離墻厚度為100~300μm。所述第二方法中,在硅片雙面形成的氧化層的厚度≥1.0μm;雙面光刻隔離窗口時(shí),所述隔離窗口的寬度為80-200μm,并腐凈隔離窗口內(nèi)的氧化層;在硅片兩側(cè)的表面及硅片兩側(cè)的隔離窗口內(nèi)沉積多晶硅薄膜,所述多晶硅薄膜的厚度為0.3-2.0μm;雙面蒸發(fā)金屬鋁,使得鋁膜厚度為0.2~1.0μm;反刻金屬鋁,只保留所述隔離窗口上的金屬鋁膜寬度為80~200μm;對(duì)通隔離擴(kuò)散時(shí),擴(kuò)散溫度1200~1280℃,擴(kuò)散時(shí)間20~60小時(shí),以實(shí)現(xiàn)硅片厚度為200-500μm的對(duì)通隔離;擴(kuò)散氣氛:氮?dú)馀c氧氣比例5:1~10:1,其中氮?dú)饬髁?~6L/min,氧氣流量0.2~0.6L/min,升溫速率3~5℃/min、降溫速率1~3℃/min;形成的隔離墻厚度為100~300μm;所述第二方法中還包含在對(duì)通隔離擴(kuò)散后進(jìn)行的表面腐蝕,以去除隔離窗口內(nèi)的鋁硅合金層。通過(guò)蒸發(fā)金屬鋁擴(kuò)散形成所述芯片中的隔離墻后,該芯片中的其他部分進(jìn)一步通過(guò)以下步驟形成:光刻硼窗口、硼擴(kuò)散、光刻K區(qū)、磷擴(kuò)散、正面刻槽、光刻鈍化窗口、鈍化保護(hù)、光刻引線、雙面金屬化、金屬反刻、合金、聚酰亞胺形成、光刻焊線窗口、亞胺化、芯片測(cè)試、硅片劃切。所述芯片用于制造雙向晶閘管時(shí),該芯片中進(jìn)一步包含設(shè)置在所述第一P型短基區(qū)P1上的第三擴(kuò)磷區(qū)域N4,和設(shè)置在所述第二P型短基區(qū)P2上的第二擴(kuò)磷區(qū)域N3;則,該芯片上在進(jìn)行光刻K區(qū)的步驟時(shí),是在硅片的正面形成所述第一擴(kuò)磷區(qū)域N2和第二擴(kuò)磷區(qū)域N3,還在硅片的背面形成所述第三擴(kuò)磷區(qū)域N4。本發(fā)明的又一個(gè)技術(shù)方案是提供一種平面晶閘管,其設(shè)置有上述任意一種實(shí)施結(jié)構(gòu)的芯片,所述芯片的陽(yáng)極焊接在框架上,所述芯片的門極和陰極分別通過(guò)導(dǎo)線連接到框架相應(yīng)的管腳上,所述晶閘管還設(shè)置有保護(hù)該芯片的外殼;其中,所述芯片中設(shè)置有經(jīng)過(guò)蒸發(fā)金屬鋁擴(kuò)散形成的隔離墻;所述經(jīng)過(guò)蒸發(fā)金屬鋁擴(kuò)散形成的隔離墻,是指在硅片雙面經(jīng)過(guò)噴砂、光刻腐蝕對(duì)版標(biāo)記、蒸發(fā)金屬鋁后,進(jìn)行金屬鋁反刻以保留對(duì)應(yīng)隔離墻位置上的金屬鋁,再進(jìn)行真空合金后,經(jīng)過(guò)對(duì)通隔離擴(kuò)散后所形成的隔離墻;或者,所述經(jīng)過(guò)蒸發(fā)金屬鋁擴(kuò)散形成的隔離墻,是指在硅片雙面經(jīng)過(guò)氧化、光刻隔離窗口、沉積多晶硅薄膜及蒸發(fā)金屬鋁后,進(jìn)行金屬鋁反刻以保留隔離窗口上的金屬鋁,再通過(guò)對(duì)通隔離擴(kuò)散形成所形成的隔離墻。與現(xiàn)有技術(shù)相比,本發(fā)明所述平面晶閘管,用于制造平面晶閘管的芯片及其制作方法,其優(yōu)點(diǎn)在于:本發(fā)明的晶閘管包含外殼、芯片、框架三部分,其中的芯片包含N型長(zhǎng)基區(qū)N1,P型短基區(qū)P1、P2,隔離墻,擴(kuò)磷區(qū)域N2(或擴(kuò)磷區(qū)域N2、N3、N4),場(chǎng)限環(huán)等。尤其所述的隔離墻是由蒸發(fā)金屬鋁擴(kuò)散而成:一種優(yōu)選方案中,硅片表面噴砂后蒸發(fā)金屬鋁,經(jīng)反刻、真空合金,對(duì)通隔離擴(kuò)散后形成隔離墻。另一種優(yōu)選方案中,硅片經(jīng)氧化、光刻隔離窗口后,沉積多晶硅薄膜,蒸發(fā)寬度與隔離窗口寬度一致的金屬鋁,進(jìn)行對(duì)通隔離擴(kuò)散后形成隔離墻。上述兩種方法對(duì)于平面工藝的單向晶閘管芯片、雙向晶閘管芯片都適用。單向與雙向晶閘管的區(qū)別在于光刻K區(qū)(即,擴(kuò)磷區(qū)域)時(shí)所使用的K區(qū)版,根據(jù)產(chǎn)品參數(shù)要求設(shè)計(jì)不同的K區(qū)版即可實(shí)現(xiàn)單向、雙向晶閘管。本發(fā)明由于采用金屬鋁作為雜質(zhì)源進(jìn)行擴(kuò)散,消除了由于硼擴(kuò)散速率慢、擴(kuò)散深度淺(只能實(shí)現(xiàn)硅片厚度250μm以下的對(duì)通隔離)的弊端。鋁擴(kuò)散可以實(shí)現(xiàn)硅片厚度200-500μm的對(duì)通隔離,耐壓可以提高到2000V以上,高溫漏電小,性能穩(wěn)定,鋁的橫向擴(kuò)散寬度為擴(kuò)散深度的40%(硼的橫向擴(kuò)散寬度為擴(kuò)散深度的80%),提高芯片面積的利用率,提高產(chǎn)品的電流能力。除此之外,還具有以下優(yōu)點(diǎn):生產(chǎn)成本低、生產(chǎn)周期短、耗能及污染少等,采用本發(fā)明生產(chǎn)的晶閘管性能優(yōu)越、穩(wěn)定可靠。附圖說(shuō)明圖1A~圖1F是本發(fā)明所述制造方法中,與第一種采用蒸發(fā)金屬鋁實(shí)現(xiàn)對(duì)通隔離方案中各個(gè)主要步驟相對(duì)應(yīng)的晶閘管芯片結(jié)構(gòu)示意圖;圖1G~圖1J是四個(gè)不同實(shí)施例中,相鄰芯片上金屬鋁膜的外形示意圖;圖2A~圖2D是本發(fā)明所述制造方法中,與第二種采用蒸發(fā)金屬鋁實(shí)現(xiàn)對(duì)通隔離方案中各個(gè)主要步驟相對(duì)應(yīng)的晶閘管芯片結(jié)構(gòu)示意圖;圖3是本發(fā)明所述晶閘管芯片的制造方法中,第一種采用蒸發(fā)金屬鋁實(shí)現(xiàn)對(duì)通隔離方案的工藝流程示意圖;圖4是本發(fā)明所述晶閘管芯片的制造方法中,第二種采用蒸發(fā)金屬鋁實(shí)現(xiàn)對(duì)通隔離方案的工藝流程示意圖;圖5是本發(fā)明一個(gè)優(yōu)選實(shí)施例中單向晶閘管芯片的結(jié)構(gòu)示意圖;圖6是本發(fā)明另一個(gè)優(yōu)選實(shí)施例中雙向晶閘管芯片的結(jié)構(gòu)示意圖。圖中:硅片101,光刻膠102,對(duì)版標(biāo)記103,金屬鋁膜104,隔離墻105;硅片201,氧化層202,多晶硅薄膜203,金屬鋁膜204,隔離墻205;單向晶閘管中:N型長(zhǎng)基區(qū)N1·901,第一P型短基區(qū)P1·902,第二P型短基區(qū)P2·903,擴(kuò)磷區(qū)域N2·904,隔離墻905,場(chǎng)限環(huán)906,門極907,陰極908,陽(yáng)極909,氧化層910,劃切區(qū)域911,鈍化薄膜912,聚酰亞胺薄膜913;雙向晶閘管中:N型長(zhǎng)基區(qū)N1·1001,第一P型短基區(qū)P1·1002,第二P型短基區(qū)P2·1003,第一擴(kuò)磷區(qū)域N2·1004,第二擴(kuò)磷區(qū)域N3·1005,第三擴(kuò)磷區(qū)域N4·1006,隔離墻1007,場(chǎng)限環(huán)1008,門極1009,陰極1010,陽(yáng)極1011,氧化層1012,鈍化薄膜1013,聚酰亞胺薄膜1014,劃切區(qū)域1015。具體實(shí)施方式下面結(jié)合附圖和具體實(shí)施方式對(duì)本發(fā)明作進(jìn)一步說(shuō)明。實(shí)施例1本實(shí)施例中的晶閘管為平面工藝的單向晶閘管,主要包含外殼、芯片、框架三部分,其核心部分在于芯片,芯片的陽(yáng)極焊接在框架上,芯片的門極和陰極分別通過(guò)導(dǎo)線連接到框架相應(yīng)的管腳上,外殼起到保護(hù)芯片的作用。晶閘管芯片(芯片結(jié)構(gòu)見(jiàn)附圖5)為平面工藝單向晶閘管芯片,包括:N型長(zhǎng)基區(qū)N1·901、第一P型短基區(qū)P1·902、第二P型短基區(qū)P2·903、擴(kuò)磷區(qū)域N2·904、隔離墻905、場(chǎng)限環(huán)906、門極907、陰極908、陽(yáng)極909、氧化層910、劃切區(qū)域911、鈍化薄膜912、聚酰亞胺薄膜913。芯片中間為N型長(zhǎng)基區(qū)N1·901,上下兩側(cè)分別為第一P型短基區(qū)P1·902、第二P型短基區(qū)P2·903。N型長(zhǎng)基區(qū)N1·901周邊均有隔離墻905保護(hù):隔離墻由蒸發(fā)金屬鋁擴(kuò)散而成(其實(shí)現(xiàn)步驟在下文中將具體描述)。劃切區(qū)域911設(shè)在隔離墻905的正上方,擴(kuò)磷區(qū)域N2·904設(shè)在第二P型短基區(qū)P2·903上,陰極908設(shè)在擴(kuò)磷區(qū)域N2·904上,門極907設(shè)在第二P型短基區(qū)P2·903上,陽(yáng)極909設(shè)在第一P型短基區(qū)P1·902上,場(chǎng)限環(huán)906設(shè)在隔離墻905與第二P型短基區(qū)P2·903之間,劃切區(qū)域911、門極907、陰極908之間均有鈍化薄膜912、聚酰亞胺薄膜913鈍化保護(hù)。這種結(jié)構(gòu)除了隔離墻是由蒸發(fā)金屬鋁擴(kuò)散而成之外,其余部分與原來(lái)的平面工藝單向晶閘管芯片相同。上述平面工藝單向晶閘管芯片制造方法:參見(jiàn)附圖3,該制造方法包括硅片來(lái)料檢驗(yàn)501、雙面噴砂及清洗502、光刻腐蝕對(duì)版標(biāo)記503、雙面蒸鋁504、反刻金屬鋁505、真空合金506、對(duì)通隔離擴(kuò)散507、雙面拋光508、氧化509、光刻硼窗口510、硼擴(kuò)散511、光刻K區(qū)512、磷擴(kuò)散513、光刻鈍化窗口514、鈍化保護(hù)515、光刻引線孔516、雙面金屬化517、金屬反刻518、合金519、聚酰亞胺520、光刻焊線窗口521、亞胺化522、芯片測(cè)試523、硅片劃切524。硅片來(lái)料檢驗(yàn)501:選取<111>區(qū)熔硅片,電阻率50-60,硅片厚度300±5μm。雙面噴砂清洗502:使用噴砂機(jī)將硅片雙面噴砂,噴砂去除量為0.5-1.0μm,噴砂后用活性劑清洗沖水即可。雙面噴砂工步的目的在于破壞硅片表面硅原子的晶格結(jié)構(gòu),有助于后續(xù)工步中金屬鋁與硅更好的結(jié)合。光刻腐蝕對(duì)版標(biāo)記503:具體請(qǐng)參見(jiàn)附圖1A~圖1B所示,在硅片兩面分別涂覆光刻膠102,通過(guò)掩膜版對(duì)硅片101上的光刻膠102進(jìn)行曝光,將掩膜版上的標(biāo)記圖形(正方形、長(zhǎng)方形、矩形、圓等圖形均可)復(fù)制到硅片101上,通過(guò)顯影液顯影后將標(biāo)記圖形內(nèi)的光刻膠102去除干凈(即圖形內(nèi)的硅裸露在表面),用硅微腐蝕液對(duì)標(biāo)記圖形進(jìn)行腐蝕,腐蝕深度一般為30-40μm,腐蝕后去膠、清洗。雙面蒸鋁504:即,雙面蒸發(fā)金屬鋁(蒸發(fā)方式可以采用電子束蒸發(fā)、濺射)鋁膜厚度一般為0.2~1.0μm。參見(jiàn)圖1C,用電子束蒸發(fā)臺(tái)在硅片雙面蒸發(fā)金屬鋁,例如,鋁膜厚度為0.2~1.0μm。反刻金屬鋁505:參見(jiàn)圖1D~圖1E所示,利用光刻技術(shù),保留隔離墻上面的金屬鋁,用鋁腐蝕液腐凈其他區(qū)域內(nèi)的金屬鋁,鋁膜寬度一般為80-200μm。金屬鋁膜的形狀:如圖1H所示,相鄰芯片共用連續(xù)金屬鋁膜(鋁膜寬度為80-200μm);也可以如附圖1G所示,每個(gè)芯片使用單獨(dú)的金屬鋁膜,鋁膜與鋁膜的間距為100-500μm(間距可以根據(jù)擴(kuò)散深度進(jìn)行調(diào)節(jié));也可以如附圖1I所示,相鄰芯片共用不連續(xù)的金屬鋁膜,單個(gè)鋁膜外形有多種(如正方形、長(zhǎng)方形等),鋁膜與鋁膜的間距為100-500μm(間距可以根據(jù)擴(kuò)散深度進(jìn)行調(diào)節(jié)),也可以如附圖1J所示,每個(gè)芯片使用單獨(dú)的不連續(xù)金屬鋁膜,單個(gè)鋁膜外形有多種(如正方形、長(zhǎng)方形等),鋁膜與鋁膜的間距為50-500μm(間距可以根據(jù)擴(kuò)散深度進(jìn)行調(diào)節(jié))真空合金506:例如,合金溫度480~520℃,合金時(shí)間20~40分鐘;真空合金工步的目的在于將金屬鋁和硅在合金溫度下形成一層良好、均勻的鋁硅熔融物,使得擴(kuò)散形成的隔離墻具有均勻的擴(kuò)散深度、擴(kuò)散寬度。對(duì)通隔離擴(kuò)散507:擴(kuò)散溫度1200~1280℃,擴(kuò)散時(shí)間20~60小時(shí),可以實(shí)現(xiàn)硅片厚度為200-500μm的對(duì)通隔離。擴(kuò)散氣氛:氮?dú)馀c氧氣比例5:1~10:1氧氣可以將鋁蒸汽(高溫條件下)氧化為Al2O3,Al2O3是一種無(wú)效的雜質(zhì)擴(kuò)散源、不會(huì)在裸硅表面形成P型區(qū),O2可以在裸硅表面生長(zhǎng)氧化層用于阻擋爐管內(nèi)或硅片表面其他雜質(zhì)的擴(kuò)散;通常氮?dú)饬髁?~6L/min,氧氣流量0.2~0.6L/min,升溫速率3~5℃/min、降溫速率1~3℃/min。一個(gè)優(yōu)選的實(shí)施例中,擴(kuò)散溫度1275℃,擴(kuò)散時(shí)間35小時(shí),擴(kuò)散氣氛:N2流量為6L/min、O2流量為0.6L/min,升溫速率4℃/min、降溫速率2℃/min。高溫?cái)U(kuò)散后形成寬度為100-150μm的隔離墻,擴(kuò)散后R□約為200-500□。雙面拋光508:將對(duì)通隔離擴(kuò)散后的硅片進(jìn)行雙面拋光,去除表面鋁硅合金層,拋光去除量為15-20μm。至此,晶閘管芯片中通過(guò)蒸發(fā)金屬鋁膜擴(kuò)散形成隔離墻105后的結(jié)構(gòu),請(qǐng)參見(jiàn)圖1F所示。氧化509:氧化溫度1100~1200℃,氧化時(shí)間6-8h,得到的氧化層厚度一般為1.5μm。光刻硼窗口510:利用光刻技術(shù),將P型短基區(qū)及場(chǎng)限環(huán)內(nèi)的氧化層腐蝕干凈。硼擴(kuò)散511:用離子注入機(jī)注入硼(注入劑量:1E14~1E15),然后進(jìn)行高溫?cái)U(kuò)散,擴(kuò)散溫度1200~1280℃,擴(kuò)散時(shí)間20-30小時(shí),硼R□為20-60□,硼結(jié)深為30-50μm。即,形成了圖5中所示的第一P型短基區(qū)P1·902和第二P型短基區(qū)P2·903。光刻K區(qū)512:在硅片正面光刻擴(kuò)磷區(qū)域。磷擴(kuò)散513:采用三氯氧磷(POCl3)液態(tài)源擴(kuò)散,預(yù)擴(kuò)溫度1050~1150℃,預(yù)擴(kuò)時(shí)間60-90分鐘,源溫15-20℃,磷再擴(kuò)溫度1150~1200℃,時(shí)間4-5小時(shí),R□為0.3-1.00□,擴(kuò)散結(jié)深為10-20μm。即,形成了圖5中所示的擴(kuò)磷區(qū)域N2·904。光刻鈍化窗口514、鈍化保護(hù)515:將鈍化窗口內(nèi)氧化層腐蝕干凈,然后在窗口內(nèi)沉積SIPOS薄膜及氮化硅薄膜(或LTO薄膜),進(jìn)行鈍化保護(hù)。光刻引線孔516:刻出需要進(jìn)行金屬化的區(qū)域,并將區(qū)域內(nèi)的鈍化保護(hù)層腐蝕干凈。雙面金屬化517:在硅片正背面分別蒸發(fā)鈦-鎳-銀,鈦蒸發(fā)厚度要求1200-1600埃,鎳蒸發(fā)厚度要求4500-5500埃,銀蒸發(fā)厚度要求1.4-1.7μm。即,在對(duì)應(yīng)位置形成了圖5中所示的門極907、陰極908和陽(yáng)極909。金屬反刻518:是對(duì)不需要金屬層覆蓋的區(qū)域進(jìn)行光刻。光刻后腐蝕去除上述區(qū)域內(nèi)的金屬層,然后進(jìn)行剝離去膠。合金519:真空合金,加強(qiáng)金屬與硅的結(jié)合力。聚酰亞胺520、光刻焊線窗口521、亞胺化522:在硅片表面涂覆聚酰亞胺,通過(guò)光刻技術(shù)將焊線窗口內(nèi)的聚酰亞胺顯影去除,在100~150℃烘箱內(nèi)烘1小時(shí)實(shí)現(xiàn)聚酰亞胺的亞胺化。然后對(duì)芯片進(jìn)行測(cè)試523)、硅片劃切524)成互相分離的晶閘管芯片。將劃切后的芯片進(jìn)行粘片、鍵合、包封、電鍍、切筋、成品測(cè)試,最終的產(chǎn)品即為平面晶閘管。采用本發(fā)明的平面晶閘管產(chǎn)品電參數(shù)、電性能明顯提高,各項(xiàng)指標(biāo)均達(dá)到設(shè)計(jì)要求。以16A/1400V(版面為3.9*3.9mm2)為例,申請(qǐng)人已做到:通態(tài)平均電流IT(AV)=16A,正反向峰值電壓VDRM=VRRM=1400-1600V,通態(tài)峰值電壓VTM≤1.3V@IT=5A,門極觸發(fā)電壓VGT=0.8-1.2V,門極觸發(fā)電流IGT=10-30mA,高溫漏電流(125℃)IDRM/IRRM=0.1-0.3mA。實(shí)施例2本實(shí)施例中的晶閘管為平面工藝的雙向晶閘管,主要包含外殼、芯片、框架三部分,其核心部分在于芯片,芯片的陽(yáng)極焊接在框架上,芯片的門極和陰極分別通過(guò)導(dǎo)線連接到框架相應(yīng)的管腳上,外殼起到保護(hù)芯片的作用。晶閘管芯片的芯片結(jié)構(gòu)見(jiàn)附圖6,為一個(gè)平面工藝雙向晶閘管芯片,包括:N型長(zhǎng)基區(qū)N1·1001、第一P型短基區(qū)P1·1002、第二P型短基區(qū)P2·1003、第一擴(kuò)磷區(qū)域N2·1004、門極下的第二擴(kuò)磷區(qū)域N3·1005、第一P型短基區(qū)P1·1002上的第三擴(kuò)磷區(qū)域N4·1006、隔離墻1007、場(chǎng)限環(huán)1008、門極1009、陰極1010、陽(yáng)極1011、氧化層1012、鈍化薄膜1013、聚酰亞胺薄膜1014、劃切區(qū)域1015。芯片中間為N型長(zhǎng)基區(qū)N1·1001,上下兩側(cè)分別為第一P型短基區(qū)P1·1002、第二P型短基區(qū)P2·1003。N型長(zhǎng)基區(qū)N1·1001周邊均有隔離墻1007保護(hù):隔離墻由蒸發(fā)金屬鋁擴(kuò)散而成(實(shí)現(xiàn)步驟將在下文中具體描述)。隔離墻1007與第二P型短基區(qū)P2·1003之間設(shè)有場(chǎng)限環(huán)1008。第三擴(kuò)磷區(qū)域N4·1006設(shè)在第一P型短基區(qū)P1·1002上,第一擴(kuò)磷區(qū)域N2·1004及第二擴(kuò)磷區(qū)域N3·1005設(shè)在第二P型短基區(qū)P2·1003上。門極1009設(shè)在第二擴(kuò)磷區(qū)域N3·1005上,陰極1010設(shè)在第一擴(kuò)磷區(qū)域N2·1004及第二P型短基區(qū)P2·1003之上,陽(yáng)極1011設(shè)在第一P型短基區(qū)P1·1002及第一擴(kuò)磷區(qū)域N2·1004之上,劃切區(qū)域1015設(shè)在隔離墻1007之上,門極1009、陰極1010、劃切區(qū)域1015之間均有鈍化薄膜1013、聚酰亞胺薄膜1014鈍化保護(hù)。這種結(jié)構(gòu)除了隔離墻是由蒸發(fā)金屬鋁擴(kuò)散而成之外,其余部分與原來(lái)的平面工藝雙向晶閘管芯片相同。上述平面工藝雙向晶閘管芯片的制造方法,除了在光刻K區(qū)步驟中,雙面需要同時(shí)光刻擴(kuò)磷區(qū)域外,其余步驟同實(shí)施例1。上述雙向晶閘管芯片中隔離墻的制作方法,簡(jiǎn)述如下:硅片來(lái)料檢驗(yàn)后,雙面噴砂及清洗。雙面光刻對(duì)版標(biāo)記及腐蝕對(duì)版標(biāo)記,便于后續(xù)光刻對(duì)版,見(jiàn)附圖1A~圖1B。雙面蒸發(fā)金屬鋁(蒸發(fā)方式可以采用電子束蒸發(fā)、濺射),鋁膜厚度一般為0.2~1.0μm,見(jiàn)附圖1C。反刻金屬鋁膜,只保留所需的金屬鋁膜(鋁膜寬度為80-200μm),見(jiàn)附圖1D~圖1E。真空合金:合金溫度480~520℃,合金時(shí)間20~40分鐘。對(duì)通隔離擴(kuò)散:擴(kuò)散溫度1200~1280℃,擴(kuò)散時(shí)間20~60小時(shí),可以實(shí)現(xiàn)硅片厚度為200-500μm的對(duì)通隔離。擴(kuò)散氣氛:氮?dú)馀c氧氣比例5:1~10:1(通常氮?dú)饬髁?~6L/min,氧氣流量0.2~0.6L/min),升溫速率3~5℃/min、降溫速率1~3℃/min,見(jiàn)附圖1F。并且,上述平面工藝雙向晶閘管芯片的生產(chǎn)方法,除了在光刻K區(qū)步驟中,雙面需要同時(shí)光刻相應(yīng)的擴(kuò)磷區(qū)域外,其余步驟同實(shí)施例1。實(shí)施例3本實(shí)施例中的晶閘管為平面工藝的單向晶閘管,主要包含外殼、芯片、框架三部分,其核心部分在于芯片,芯片的陽(yáng)極焊接在框架上,芯片的門極和陰極分別通過(guò)導(dǎo)線連接到框架相應(yīng)的管腳上,外殼起到保護(hù)芯片的作用。晶閘管芯片(芯片結(jié)構(gòu)見(jiàn)附圖5)為平面工藝單向晶閘管芯片,包括:N型長(zhǎng)基區(qū)N1·901、第一P型短基區(qū)P1·902、第二P型短基區(qū)P2·903、擴(kuò)磷區(qū)域N2·904、隔離墻905、場(chǎng)限環(huán)906、門極907、陰極908、陽(yáng)極909、氧化層910、劃切區(qū)域911、鈍化薄膜912、聚酰亞胺薄膜913。這種結(jié)構(gòu)除了隔離墻是由蒸發(fā)金屬鋁擴(kuò)散而成之外,其余部分與原來(lái)的平面工藝單向晶閘管芯片相同。而與實(shí)施例1的不同點(diǎn)則在于隔離墻的形成方法不同。上述平面工藝單向晶閘管芯片制造方法:參見(jiàn)附圖4,該制造方法包括硅片來(lái)料檢驗(yàn)601、清洗及氧化602、光刻隔離窗口603、多晶硅沉積604、雙面蒸鋁605、光刻鋁窗口606、對(duì)通隔離擴(kuò)散607、表面腐蝕608、二次氧化609、光刻硼窗口610、硼擴(kuò)散611、光刻K區(qū)612、磷擴(kuò)散613、光刻鈍化窗口614、鈍化保護(hù)615、光刻引線孔616、雙面金屬化617、金屬反刻618、合金619、聚酰亞胺620、光刻焊線窗口621、亞胺化622、芯片測(cè)試623、硅片劃切624。硅片來(lái)料檢驗(yàn)601:選取<111>區(qū)熔硅片,電阻率50-60,硅片厚度300±5μm。清洗氧化602:采用干氧、濕氧交替氧化,氧化溫度1150~1200℃,時(shí)間5-8小時(shí)。在硅片201兩面形成的氧化層202厚度一般大于≥1.0μm,可以保護(hù)芯片圖形內(nèi)部不受其他雜質(zhì)的影響。光刻隔離窗口603:在硅片201兩面進(jìn)行光刻,將隔離窗口內(nèi)的氧化層腐蝕干凈,隔離窗口寬度一般為80-200μm,腐蝕完隔離窗口內(nèi)氧化層進(jìn)行去膠,亦見(jiàn)圖2A。多晶硅沉積604:LPCVD法沉積多晶硅薄膜,薄膜厚度一般為:0.3~2.0μm;其作用是在高溫條件下(蒸發(fā)金屬鋁后)形成一層均勻的鋁雜質(zhì)源薄膜,使得隔離墻的擴(kuò)散深度、寬度均勻、一致。雙面蒸鋁605:用電子束蒸發(fā)臺(tái)在硅片雙面蒸發(fā)金屬鋁,鋁膜厚度為0.2~1.0μm,見(jiàn)附圖2B。光刻鋁窗口606:利用光刻技術(shù),保留隔離窗口上面的金屬鋁,用鋁腐蝕液腐凈其他區(qū)域內(nèi)的金屬鋁,鋁膜寬度同隔離窗口寬度一致,見(jiàn)圖2C。金屬鋁膜的形狀:如圖1H所示,相鄰芯片共用連續(xù)金屬鋁膜(鋁膜寬度為80-200μm);也可以如附圖1G所示,每個(gè)芯片使用單獨(dú)的金屬鋁膜,鋁膜與鋁膜的間距為100-500μm(間距可以根據(jù)擴(kuò)散深度進(jìn)行調(diào)節(jié));也可以如附圖1I所示,相鄰芯片共用不連續(xù)的金屬鋁膜,單個(gè)鋁膜外形有多種(如正方形、長(zhǎng)方形等),鋁膜與鋁膜的間距為100-500μm(間距可以根據(jù)擴(kuò)散深度進(jìn)行調(diào)節(jié))。也可以如附圖1J所示,每個(gè)芯片使用單獨(dú)的不連續(xù)金屬鋁膜,單個(gè)鋁膜外形有多種(如正方形、長(zhǎng)方形等),鋁膜與鋁膜的間距為50-500μm(間距可以根據(jù)擴(kuò)散深度進(jìn)行調(diào)節(jié))。對(duì)通隔離擴(kuò)散607:擴(kuò)散溫度1200~1280℃,擴(kuò)散時(shí)間20~60小時(shí),可以實(shí)現(xiàn)硅片厚度為200-500μm的對(duì)通隔離。擴(kuò)散氣氛:氮?dú)馀c氧氣比例5:1~10:1(通常氮?dú)饬髁?~6L/min,氧氣流量0.2~0.6L/min),升溫速率3~5℃/min、降溫速率1~3℃/min,見(jiàn)附圖2D。一個(gè)優(yōu)選的實(shí)施例中,擴(kuò)散溫度1275℃,擴(kuò)散時(shí)間60小時(shí),擴(kuò)散氣氛:N2流量為6L/min、O2流量為0.6L/min,升溫速率4℃/min、降溫速率2℃/min。高溫?cái)U(kuò)散后形成寬度為100-150μm的隔離墻,擴(kuò)散后R□約為200-500□。表面腐蝕608:用硅腐蝕液將隔離窗口內(nèi)的鋁硅合金層腐蝕干凈。步驟609至步驟624與實(shí)施例1中的步驟509至步驟524完全相同,最終形成本實(shí)施例所述的晶閘管。實(shí)施例4本實(shí)施例中的晶閘管為平面工藝的雙向晶閘管,主要包含外殼、芯片、框架三部分,其核心部分在于芯片,芯片的陽(yáng)極焊接在框架上,芯片的門極和陰極分別通過(guò)導(dǎo)線連接到框架相應(yīng)的管腳上,外殼起到保護(hù)芯片的作用。晶閘管芯片(芯片結(jié)構(gòu)見(jiàn)附圖6)為平面工藝雙向晶閘管芯片,包括:N型長(zhǎng)基區(qū)N1·1001、第一P型短基區(qū)P1·1002、第二P型短基區(qū)P2·1003、第一擴(kuò)磷區(qū)域N2·1004、門極下第二擴(kuò)磷區(qū)域N3·1005、P1上第三擴(kuò)磷區(qū)域N4·1006、隔離墻1007、場(chǎng)限環(huán)1008、門極1009、陰極1010、陽(yáng)極1011、氧化層1012、鈍化薄膜1013、聚酰亞胺薄膜1014、劃切區(qū)域1015。這種結(jié)構(gòu)除了隔離墻是由蒸發(fā)金屬鋁擴(kuò)散而成之外,其余部分與原來(lái)的平面工藝雙向晶閘管芯片相同。與實(shí)施例2的不同點(diǎn)則在于隔離墻的形成方法不同。上述雙向晶閘管芯片中隔離墻使用了實(shí)施例3所示的制作方法,簡(jiǎn)述如下:硅片清洗、氧化(氧化層厚度≥1.0μm)。雙面光刻隔離環(huán)(隔離環(huán)寬度為80-200μm),腐凈隔離環(huán)內(nèi)的氧化層,見(jiàn)附圖2A。LPCVD法沉積多晶硅薄膜:多晶硅薄膜厚度為0.3-2.0μm。雙面蒸發(fā)金屬鋁,鋁膜厚度一般為0.2~1.0μm,見(jiàn)附圖2B。反刻金屬鋁,只保留所需的金屬鋁膜,見(jiàn)附圖2C。對(duì)通隔離擴(kuò)散:擴(kuò)散溫度1200~1280℃,擴(kuò)散時(shí)間20~60小時(shí),可以實(shí)現(xiàn)硅片厚度為200-500μm的對(duì)通隔離。擴(kuò)散氣氛:氮?dú)馀c氧氣比例5:1~10:1(通常氮?dú)饬髁?~6L/min,氧氣流量0.2~0.6L/min),升溫速率3~5℃/min、降溫速率1~3℃/min,見(jiàn)附圖2D。上述平面工藝雙向晶閘管芯片的制造方法,除了在光刻K區(qū)步驟中,雙面需要同時(shí)光刻擴(kuò)磷區(qū)域外,其余步驟同實(shí)施例3。盡管本發(fā)明的內(nèi)容已經(jīng)通過(guò)上述優(yōu)選實(shí)施例作了詳細(xì)介紹,但應(yīng)當(dāng)認(rèn)識(shí)到上述的描述不應(yīng)被認(rèn)為是對(duì)本發(fā)明的限制。在本領(lǐng)域技術(shù)人員閱讀了上述內(nèi)容后,對(duì)于本發(fā)明的多種修改和替代都將是顯而易見(jiàn)的。比方說(shuō),本發(fā)明的保護(hù)范圍不受實(shí)施例中具體參數(shù)的限制,如:①金屬鋁膜厚度小于0.2μm(或大于1.0μm),寬度小于80μm(或大于200μm),也可以實(shí)施本發(fā)明,但實(shí)際效果以鋁膜厚度0.2~1.0μm、寬度80-200μm為最佳。如果有人為實(shí)施本發(fā)明,故意采用上述方法,也應(yīng)落入本發(fā)明的保護(hù)范圍。②金屬鋁膜的排布方法:如圖1H所示,相鄰芯片共用連續(xù)金屬鋁膜(鋁膜寬度為80-200μm);也可以如附圖1G所示,每個(gè)芯片使用單獨(dú)的金屬鋁膜,鋁膜與鋁膜的間距為100-500μm(間距可以根據(jù)擴(kuò)散深度進(jìn)行調(diào)節(jié));也可以如附圖1I所示,相鄰芯片共用不連續(xù)的金屬鋁膜,單個(gè)鋁膜外形有多種(如正方形、長(zhǎng)方形等),鋁膜與鋁膜的間距為100-500μm(間距可以根據(jù)擴(kuò)散深度進(jìn)行調(diào)節(jié));也可以如附圖1J所示,每個(gè)芯片使用單獨(dú)的不連續(xù)金屬鋁膜,單個(gè)鋁膜外形有多種(如正方形、長(zhǎng)方形等),鋁膜與鋁膜的間距為50-500μm(間距可以根據(jù)擴(kuò)散深度進(jìn)行調(diào)節(jié))。如果有人為實(shí)施本發(fā)明,故意采用其他形狀的鋁膜排布方法,也應(yīng)落入本發(fā)明的保護(hù)范圍。③多晶硅薄膜厚度小于0.3μm(或大于2.0μm),也可以實(shí)施本發(fā)明,但實(shí)際效果以多晶硅薄膜厚度0.3~2.0μm為最佳。如果有人為實(shí)施本發(fā)明,故意采用上述方法,也應(yīng)落入本發(fā)明的保護(hù)范圍。④為了達(dá)到破壞硅片表面硅原子的晶格結(jié)構(gòu)的目的,也可以采用激光造損、離子注入等其他方式實(shí)施本發(fā)明,但實(shí)際效果以噴砂的方法最為經(jīng)濟(jì)、實(shí)用。如果有人為實(shí)施本發(fā)明,故意采用上述方法,也應(yīng)落入本發(fā)明的保護(hù)范圍。⑤真空合金溫度低于480℃(或高于520℃)、時(shí)間少于20分鐘(或長(zhǎng)于40分鐘),也可以實(shí)施本發(fā)明,但實(shí)際效果以真空合金溫度480~520℃、合金時(shí)間20~40分鐘為最佳。如果有人為實(shí)施本發(fā)明,故意采用上述方法,也應(yīng)落入本發(fā)明的保護(hù)范圍。⑥高溫?cái)U(kuò)散時(shí),氮?dú)馀c氧氣比例低于5:1(或高于10:1)也可以實(shí)施本發(fā)明,但實(shí)際效果以氮?dú)馀c氧氣比例5:1~10:1為最佳。如果有人為實(shí)施本發(fā)明,故意采用上述方法,也應(yīng)落入本發(fā)明的保護(hù)范圍。⑦氧化層厚度小于1.0μm,也可實(shí)施本發(fā)明,但實(shí)際效果以氧化層厚度大于1.0μm為最佳。如果有人為實(shí)施本發(fā)明,故意采用上述方法,也應(yīng)落入本發(fā)明的保護(hù)范圍。