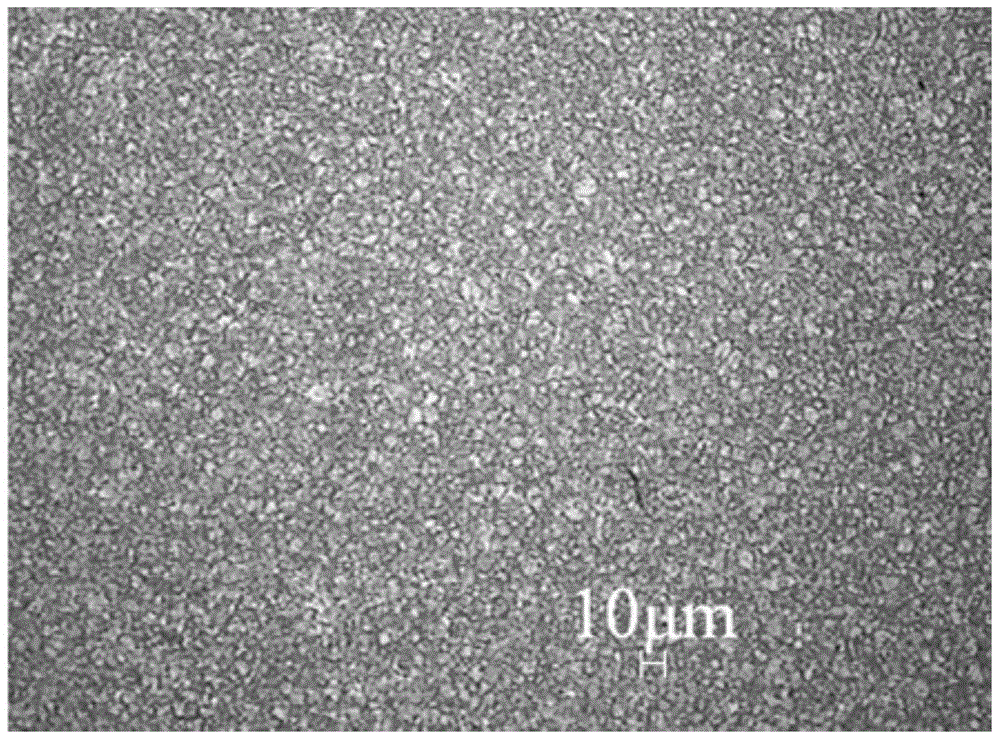
本發(fā)明涉及一種銅鎢觸頭材料的制備方法,屬于金屬基復(fù)合材料領(lǐng)域。
背景技術(shù):由于鎢的熔點高,耐電弧侵蝕性強,而銅具有優(yōu)良的導(dǎo)電導(dǎo)熱性能,銅鎢材料兼具有良好的耐電弧侵蝕性及導(dǎo)電導(dǎo)熱性,因而銅鎢觸頭材料被作為弧觸頭廣泛地應(yīng)用于SF6高壓斷路器上,起接通和分斷電流的作用。由于在接通和分斷電流過程中,一方面所產(chǎn)生的電弧全部由弧觸頭來承受,觸頭要受到電弧的侵蝕、高溫和熱應(yīng)力的作用,另一方面因動、靜觸頭相互沖擊摩擦,觸頭還要受到機械應(yīng)力的作用,觸頭的失效主要為電弧侵蝕和高溫機械摩擦損蝕交互作用所致,因此銅鎢觸頭不僅要具有良好的耐電弧侵蝕性還要具有足夠高的高溫機械強度。對此,銅鎢觸頭應(yīng)相應(yīng)地具備如下性能:①具有鎢顆粒均勻地分布于銅基體上的組織結(jié)構(gòu),具備這樣的組織才能使觸頭獲得良好的耐電弧侵蝕性,②觸頭的鎢骨架具有足夠高的高溫機械強度,而要獲得這樣的性能,就必需使鎢骨架中相互接觸的鎢顆粒燒結(jié)成為一體,使得各鎢顆粒連續(xù)成一個整體鎢骨架,這樣才能形成一個在高溫下耐沖擊磨損的觸頭基體。目前,銅鎢觸頭材料制造工藝有:①1800℃以上高溫預(yù)燒鎢骨架,然后滲銅,制造工藝為:鎢粉→成型→預(yù)燒鎢骨架→熔滲,使用這種工藝可以得到各鎢顆粒連續(xù)成一個整體的鎢骨架,觸頭具有優(yōu)良的耐電弧侵蝕性和高的高溫機械強度,但制備設(shè)備昂貴,能源消耗高;②1450℃以下低溫活化燒結(jié)鎢骨架,然后滲銅,制造工藝為:鎢粉+微量的金屬元素→混合→成型→預(yù)燒鎢骨架→熔滲,添加微量的金屬元素多為鎳、鈷、鐵中的一種,但因微量的金屬元素難于分布均勻,鎢骨架的燒結(jié)效果較差,觸頭的高溫機械強度低,高溫下抗沖擊磨損的性能低,從而降低了開關(guān)運行的可靠性。公開號為CN101279365A的發(fā)明專利,公開了一種高抗電弧燒蝕的鎢銅電觸頭材料的制備方法,該方法按以下步驟進行:首先按比例稱量銅粉、鎢粉以及稀土單質(zhì)鑭或鈰;然后將20~40%的銅粉、鎢粉及全部稀土單質(zhì)鑭或鈰放在高能球磨機中進行機械合金化;再次將余下的銅粉、鎢粉及添加的鎳粉和乙醇進行共同機械混合;在模具中壓制成型;最后將壓坯裝入高溫保護氣氛燒結(jié)爐中采用熔滲技術(shù)燒結(jié)成型即得到高抗電弧燒蝕的鎢銅電觸頭。但是該方法存在如下問題:①添加的0.05~0.15%微量活化燒結(jié)元素鎳,在機械混合過程中難于均勻分散;②加入的2.4~17.6%比例的銅粉要比添加的鎳多得多,在機械混合過程中由于銅粉的阻礙作用鎢顆粒捕捉到鎳的幾率大為降低;③機械混合后,難于避免地存在有銅的富集。因此在后續(xù)熔滲燒結(jié)時,鎢骨架的活化燒結(jié)效果會大打折扣,鎢骨架中相互接觸的鎢顆粒不能燒結(jié)成為一體,因此所制得的銅鎢的高溫機械強度也會大為降低,鎢顆粒的彌散程度也不夠高。
技術(shù)實現(xiàn)要素:本發(fā)明要解決的技術(shù)問題是提供一種銅鎢觸頭材料的制備方法。該方法可實現(xiàn)在球磨的同時實現(xiàn)鎳的自動添加,而且使鎳均勻的分布于鎢粉中,制得的銅鎢觸頭金相組織均勻,具有優(yōu)良的耐電弧侵蝕性和高的高溫機械強度。本發(fā)明所述的銅鎢觸頭材料的制備方法,其特征在于:取鎢粉、高純鎳球和水置于球磨機中進行球磨,所得球磨后的鎢粉經(jīng)干燥、退火、成型、預(yù)燒結(jié)、熔滲處理,得到銅鎢觸頭材料;其中:所述高純鎳球與鎢粉的重量比為4~10:1;所述水的用量按每1kg鎢粉末加入120~150ml水計算;所述球磨的時間為12~48h。本發(fā)明將鎢粉與高純鎳球和水按特定配比置于球磨機中進行球磨特定時間,一方面,球磨過程中,由高純鎳球上因球磨損耗的鎳可以作為添加物直接添加到鎢粉中,實現(xiàn)球磨和加入添加物同時進行,而且申請人經(jīng)過大量實驗驗證發(fā)現(xiàn),當(dāng)球磨時間限定在上述范圍內(nèi)時,所得觸頭材料中的鎳恰好占鎢粉總重量的0.1~1.0%;另一方面,因鎢顆粒的硬度比高純鎳球高得多,鎢粉與鎳球得到充分的接觸和研磨,由高純鎳球上因球磨損耗的鎳可以均勻地覆著到鎢顆粒的表面,從而達到有效提高鎢骨架燒結(jié)效果的目的;因此,采用本發(fā)明所述方法可以制造得到具有優(yōu)良的耐電弧侵蝕性和高的高溫機械強度的銅鎢觸頭材料。上述技術(shù)方案中,所述的高純鎳球為高純度的鎳球,為了盡量少地引入雜質(zhì),優(yōu)選是采用鎳含量≥99.9%的鎳球。通常情況下,采用直徑為φ6~φ30mm的高純鎳球。上述技術(shù)方案中,銅片在熔滲步驟中放入,所述鎢粉和銅片的用量及配比可根據(jù)要制備的銅鎢觸頭材料來計算。上述技術(shù)方案中,所述鎢粉的粒度與現(xiàn)有技術(shù)相同,在本發(fā)明中,優(yōu)選采用平均粒度為2~9μm的鎢粉。上述技術(shù)方案中,對球磨后的鎢粉進行干燥、退火、成型、預(yù)燒結(jié)和熔滲處理的工藝與現(xiàn)有技術(shù)相同,在本發(fā)明中,所述干燥、退火、成型、預(yù)燒結(jié)和熔滲處理的工藝參數(shù)優(yōu)選為:干燥是將球磨后的鎢粉置于80~150℃條件下烘干2~4h;退火是將干燥后的鎢粉置于氫氣或氨分解氣氣氛下、溫度為700~850℃的條件下,保溫1~3h;成型是將退火后的鎢粉置于鋼模中壓制成壓坯,成型壓力為2~4T/cm2;如果有必要,還可以加入現(xiàn)有技術(shù)中常規(guī)用量的成型劑(如石蠟等);預(yù)燒結(jié)是將壓坯置于氫氣或氨分解氣氣氛下、溫度1300~1450℃的條件下,保溫1~2h;熔滲是將銅片和預(yù)燒結(jié)后的壓坯置于氫氣或氨分解氣氣氛下、溫度1150~1250℃的條件下,保溫1~2h。與現(xiàn)有技術(shù)相比,本發(fā)明的特點在于:1、采用特殊的球磨工藝不僅使鎳的添加與球磨同時進行,而且加入的鎳可以均勻地覆著到鎢顆粒的表面,有效地提高了鎢骨架的活化燒結(jié)效果從而獲得性能良好的鎢骨架,將所得鎢骨架與銅片經(jīng)熔滲處理后所得的銅鎢觸頭材料具有鎢顆粒均勻地分布于銅基體上的組織結(jié)構(gòu),因此觸頭具有優(yōu)良的耐電弧侵蝕性和高的高溫機械強度(由于球磨時不加入銅粉,所以壓坯不存在銅富集,預(yù)燒結(jié)和熔滲后觸頭可以獲得鎢顆粒均勻地分布于銅基體上的組織結(jié)構(gòu),均勻彌散的高熔點鎢相大大提高了觸頭耐電弧侵蝕的能力。鎳均勻地覆著到鎢顆粒的表面,有效地提高了鎢骨架的活化燒結(jié)效果,使得鎢顆粒燒結(jié)成為一體,鎢骨架成為高強度骨架,可以耐受高溫機械磨損),所得觸頭材料應(yīng)用于SF6高壓斷路器上,完全可以經(jīng)受得住電弧侵蝕和高溫機械摩擦損蝕的交互作用,可以提高觸頭的使用壽命和斷路器運行的可靠性;2、與高溫預(yù)燒結(jié)相比,本發(fā)明技術(shù)采用常規(guī)設(shè)備即可實現(xiàn),造價低,電能消耗低。附圖說明圖1為本發(fā)明實施例3中經(jīng)預(yù)燒結(jié)處理得到的鎢骨架的SEM圖;圖2為本發(fā)明實施例3制備得到的觸頭材料的金相組織圖。具體實施方式下面結(jié)合具體實施例對本發(fā)明作進一步的詳述,以更好地理解本發(fā)明的內(nèi)容,但本發(fā)明并不限于以下實施例。實施例1:稱取20kg平均粒度2μm的鎢粉,將鎢粉、200kg的φ6~φ30mm組合(其中的重量比為φ6mm:φ10mm:φ20mm:φ30mm=3:5:1:1)的高純鎳球、3000ml去離子水一起放入100升的滾筒球磨機內(nèi)進行球磨(轉(zhuǎn)速為45轉(zhuǎn)/分),球磨時間24小時,取出粉料于150℃下烘干2小時,將烘干的粉末置于氫氣氣氛中700℃下退火2小時(經(jīng)檢測,所得粉末材料中的鎳含量為0.55%),用2T/cm2的壓力在鋼模中將退火后的粉末壓成壓坯,將壓坯置于石墨舟中,在氫氣氣氛中1300℃下燒結(jié)1小時得到鎢骨架,將鎢骨架坯置于石墨舟中并加入相應(yīng)質(zhì)量銅片(為鎢骨架重量的57%),在氫氣氣氛中1200℃下熔滲2小時,由此可制得銅鎢70觸頭。實施例2:稱取20kg平均粒度9μm的鎢粉,將鎢粉、80kg的φ20mm的高純鎳球、2400ml去離子水一起放入50升的滾筒球磨機內(nèi)進行球磨(轉(zhuǎn)速為50轉(zhuǎn)/分),球磨時間12小時,取出粉料于80℃下烘干4小時,將烘干的粉末置于氫氣氣氛中850℃下退火1小時(經(jīng)檢測,所得粉末材料中的鎳含量為0.15%),用4T/cm2的壓力在鋼模中將退火后的粉末壓成壓坯,將壓坯置于石墨舟中,在氨分解氣氣氛中1450℃下燒結(jié)1小時得到鎢骨架,將鎢骨架坯置于石墨舟中并加入相應(yīng)質(zhì)量銅片(為鎢骨架重量的24%),在氨分解氣氣氛中1250℃下熔滲1小時,由此可制得銅鎢85觸頭。實施例3:稱取20kg平均粒度為6μm的鎢粉,將鎢粉、160kg的φ10mm的高純鎳球、2600ml去離子水一起放入100升的滾筒球磨機內(nèi)進行球磨(轉(zhuǎn)速為45轉(zhuǎn)/分),球磨時間48小時,取出粉料于100℃下烘干3小時,將烘干的粉末置于氨分解氣氣氛中800℃下退火1.5小時(經(jīng)檢測,所得粉末材料中的鎳含量為0.96%),用3T/cm2的壓力在鋼模中將退火后的粉末壓成壓坯,將壓坯置于石墨舟中,在氫氣氣氛中1400℃下燒結(jié)2小時得到鎢骨架(如圖1所示),將鎢骨架坯置于石墨舟中并加入相應(yīng)質(zhì)量銅片(為鎢骨架重量的31%),在氫氣氣氛中1250℃下熔滲1小時,由此可制得銅鎢80觸頭,所得觸頭材料的金相組織結(jié)構(gòu)圖如圖2所示。對實施例1~3制得的觸頭材料進行性能檢測,并與現(xiàn)有常規(guī)熔滲法制得的銅鎢80觸頭材料的性能進行對比,結(jié)果如下述表1所示:表1:實施例材料相對密度,%高溫抗拉強度,MPa實施例1銅鎢7099.6/實施例2銅鎢8599.7/實施例3銅鎢8099.6185現(xiàn)有熔滲法產(chǎn)品銅鎢8099.1~99.4125~150