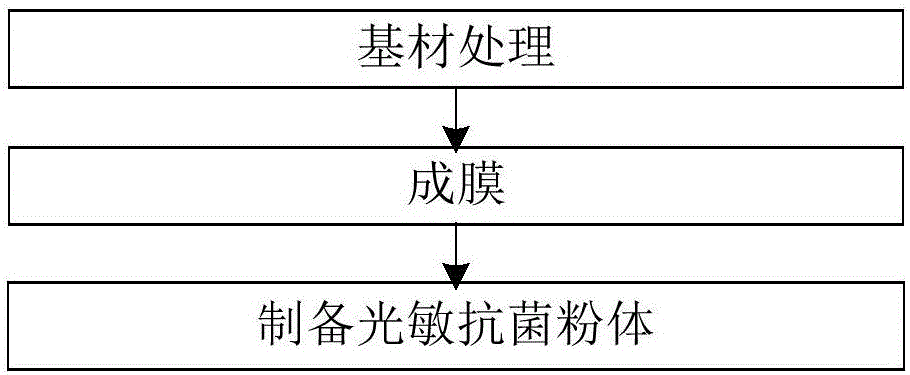
本發(fā)明涉及基于超材料的波導裝置。
背景技術:
:相關技術中的波導裝置存在轉化效率低的技術問題。技術實現(xiàn)要素:本發(fā)明旨在提供基于超材料的波導裝置,以解決上述技術問題。本發(fā)明的實施例中提供了基于超材料的波導裝置,包括波導導管和分隔片;所述波導導管內部設置有分隔片,所述分隔片沿所述波導導管的內部斜向下設置,將所述波導導管分隔成為兩個部分。本發(fā)明的上述實施例提供的基于超材料的波導裝置的結構設置合理,從而解決了上述技術問題。附圖說明此處的附圖被并入說明書中并構成本說明書的一部分,示出了符合本發(fā)明的實施例,并與說明書一起用于解釋本發(fā)明的原理。圖1是本發(fā)明的結構示意圖。圖2是根據一示例性實施例示出的基于超材料的波導裝置的防腐抗菌膜的制備方法的工藝流程圖。具體實施方式這里將詳細地對示例性實施例進行說明,其示例表示在附圖中。下面的描述涉及附圖時,除非另有表示,不同附圖中的相同數字表示相同或相似的要素。以下示例性實施例中所描述的實施方式并不代表與本發(fā)明相一致的所有實施方式。相反,它們僅是與如所附權利要求書中所詳述的、本發(fā)明的一些方面相一致的裝置和方法的例子。在本申請的描述中,需要說明的是,除非另有規(guī)定和限定,術語“安裝”、“相連”、“連接”應做廣義理解,例如,可以是機械連接或電連接,也可以是兩個元件內部的連通,可以是直接相連,也可以通過中間媒介間接相連,對于本領域的普通技術人員而言,可以根據具體情況理解上述術語的具體含義。結合以下實施例對本發(fā)明作進一步描述。應用場景1圖1是根據一示例性實施例示出的基于超材料的波導裝置9,如圖1所示,包括波導導管10和分隔片20;所述波導導管10內部設置有分隔片20,所述分隔片20沿所述波導導管10的內部斜向下設置,將所述波導導管10分隔成為兩個部分。本發(fā)明的上述實施例提供的基于超材料的波導裝置的結構設置合理,從而解決了上述技術問題。優(yōu)選地,所述分隔片20由超導材料制成。優(yōu)選地,所述分隔片20與波導導管10的中心軸的方向形成的角度為0~90°。優(yōu)選地,所述分隔片20與波導導管10的中心軸的方向形成的角度為45°。優(yōu)選地,所述波導裝置9的外表面涂刷有防腐抗菌膜;圖2是根據一示例性實施例示出的基于超材料的波導裝置的防腐抗菌膜的制備方法的工藝流程圖。參照圖2,所述防腐抗菌膜的制備方法包括以下步驟:S1,基材的處理:將鋁或鋁合金經過500#~800#的水磨砂紙打磨光亮,分別用乙醇和自來水清洗,依次經過除油和酸洗處理,取出然后用蒸餾水沖洗,置于40℃下烘干;其中,所述除油溶液的配方為:氫氧化鈉、環(huán)己烷、碳酸氫鈉、脂肪醇聚氧乙烯醚、乳化劑、苯并三氮唑、除油液溫度為50~60℃、除油時間為30~45s;所述酸性溶液的配方為:70%~80%硫酸10份、70%~90%硝酸1份、50%高錳酸鉀3份、1%單乙醇胺、活化溫度為50~60℃、活化時間為20~30s;酸性溶液的目的是除去鋁合金表面的氧化膜、氧化皮、銹蝕產物,并改變鋁合金表面狀態(tài);S2,成膜:將經過步驟S1處理過的基材試樣浸入處理液中40s,置于紅外燈下烘烤2min;再重復浸漬30s,置于紅外燈下烘烤1min;其中,所述處理液配置如下:在適量的蒸餾水中加入適量的氯氧化鋯、偏鈦酸制成溶液A,在溶液A中依次加入硫酸、羥基亞乙基二膦酸和氨基三亞甲基膦酸,制成制成溶液B,在溶液B中加超純水水定容至1000ml,用氨水調節(jié)溶液pH值至7.5~8.5;S3,制備光敏抗菌油漆膜:A.制備抗菌粉體:稱取10g脲胺、10g碳酸氫銨、5g氯化銨和15g分散劑十六烷基三甲基溴化銨,加入1000ml超純水,搖晃1~2min,加入5gNaCl,搖晃30min,加入1mol/LNaOH溶液調節(jié)pH值至8.5~9.5,采用經過拉伸的長頸滴管滴加AgNO3溶液,搖晃30min,標記為溶液A;B.將步驟A中制得的溶液A中加入10mlTiO2溶液,再加入10ml磷酸鋯,于50~60℃水浴,得到溶液B;C.將溶液A和溶液B按照2:1的比例混合,配置得到溶液C;在溶液C中加入3g二氧化硅碳納米管,置于磁力攪拌器上70~80℃攪拌1~2h,逐滴加入正硅酸乙酯,攪拌2~3h,加入20ml無水乙醇攪拌30min,將上述溶液置于40Gy193Irγ射線下照射30min后,置于0.5~30KPa負壓下抽濾,將濾料放入馬弗爐中1000~1200℃煅燒1~3h,取出冷卻研磨,過1200目篩即得;S4,將經過S2處理的基材涂刷上經過S3制備而成的光敏抗菌油漆即可。實驗測試:(1)點滴試驗:鹽霧試驗:腐蝕液用NaCl溶液,濃度為90~100mg/mL,pH值為6.5~9.5,鹽霧沉降量為3.0ml/100cm3.h;連續(xù)噴霧168h為一個周期,測量基材表面的腐蝕率。168h鹽霧腐蝕后,采用本發(fā)明方法制備的復合膜體系沒有出現(xiàn)起泡或者脫漆的現(xiàn)象;連續(xù)進行2個周期后,出現(xiàn)了非常輕微的直徑不超過0.5mm的起泡點,基材表面的腐蝕率小于0.5%;試驗進行4個周期后,復合膜體系的表面出現(xiàn)了直徑不超過0.8mm的起泡點,基材表面的腐蝕率小于5%。因此,在成膜的表面涂刷了光敏抗菌油漆后組成的復合膜體系大大的提高了漆膜的耐腐蝕性能,復合膜體系的起泡和剝離現(xiàn)象得到有效的抑制,表現(xiàn)出非常優(yōu)異的耐腐蝕性能,試驗進行5個周期后,基材表面的腐蝕率才達到10%。(2)抗菌性能測試:檢測該復合膜對大腸桿菌、霉菌和金黃色葡萄球菌的抑菌效果。結果如表1、表2、表3所示。表1復合膜對大腸桿菌的抑菌率及6個月后在30min時的抑菌率接觸時間(min)抑菌率0020100%30100%50100%60100%6個月后30min100%表2復合膜對霉菌的抑菌率及6個月后在30min時的抑菌率接觸時間(min)抑菌率0020100%30100%50100%6099.9%6個月后30min99%表3復合膜對金黃色葡萄球菌的抑菌率及6個月后在30min時的抑菌率接觸時間(min)抑菌率0020100%3098%5099%6095%6個月后30min99%試驗表明,20分鐘時,該復合膜對大腸桿菌、霉菌和金黃色葡萄球菌的抑菌率已經達到100%,表現(xiàn)出優(yōu)異的抗菌性能;在經過長達6個月的自然環(huán)境暴曬后,30min內對上述細菌的抑菌率均在99%以上,因此,根據本發(fā)明的實施例所提供的方法制備而成的復合膜具有優(yōu)異的持久抑菌效果。結果表明,利用本發(fā)明提供的方法制備而成的復合膜體系具有優(yōu)異的抗腐蝕和抑菌的性能。經過含有鈦鋯處理液處理過的基材和光敏抗菌油漆之間的協(xié)同作用,使得鋁或者鋁合金表面得到非常好的保護。應用場景2圖1是根據一示例性實施例示出的基于超材料的波導裝置9,如圖1所示,包括波導導管10和分隔片20;所述波導導管10內部設置有分隔片20,所述分隔片20沿所述波導導管10的內部斜向下設置,將所述波導導管10分隔成為兩個部分。本發(fā)明的上述實施例提供的基于超材料的波導裝置的結構設置合理,從而解決了上述技術問題。優(yōu)選地,所述分隔片20由超導材料制成。優(yōu)選地,所述分隔片20與波導導管10的中心軸的方向形成的角度為0~90°。優(yōu)選地,所述分隔片20與波導導管10的中心軸的方向形成的角度為45°。優(yōu)選地,所述波導裝置9的外表面涂刷有防腐抗菌膜;圖2是根據一示例性實施例示出的基于超材料的波導裝置的防腐抗菌膜的制備方法的工藝流程圖。參照圖2,所述防腐抗菌膜的制備方法包括以下步驟:S1,基材的處理:將鋁或鋁合金經過500#~800#的水磨砂紙打磨光亮,分別用乙醇和自來水清洗,依次經過除油和酸洗處理,取出然后用蒸餾水沖洗,置于40℃下烘干;其中,所述除油溶液的配方為:氫氧化鈉、環(huán)己烷、碳酸氫鈉、脂肪醇聚氧乙烯醚、乳化劑、苯并三氮唑、除油液溫度為50~60℃、除油時間為30~45s;所述酸性溶液的配方為:70%~80%硫酸10份、70%~90%硝酸1份、50%高錳酸鉀3份、1%單乙醇胺、活化溫度為50~60℃、活化時間為20~30s;酸性溶液的目的是除去鋁合金表面的氧化膜、氧化皮、銹蝕產物,并改變鋁合金表面狀態(tài);S2,成膜:將經過步驟S1處理過的基材試樣浸入處理液中40s,置于紅外燈下烘烤2min;再重復浸漬30s,置于紅外燈下烘烤1min;其中,所述處理液配置如下:在適量的蒸餾水中加入適量的氯氧化鋯、偏鈦酸制成溶液A,在溶液A中依次加入硫酸、羥基亞乙基二膦酸和氨基三亞甲基膦酸,制成制成溶液B,在溶液B中加超純水水定容至1000ml,用氨水調節(jié)溶液pH值至7.5~8.5;S3,制備光敏抗菌油漆膜:A.制備抗菌粉體:稱取10g脲胺、10g碳酸氫銨、5g氯化銨和15g分散劑十六烷基三甲基溴化銨,加入1000ml超純水,搖晃1~2min,加入5gNaCl,搖晃30min,加入1mol/LNaOH溶液調節(jié)pH值至8.5~9.5,采用經過拉伸的長頸滴管滴加AgNO3溶液,搖晃30min,標記為溶液A;B.將步驟A中制得的溶液A中加入10mlTiO2溶液,再加入10ml磷酸鋯,于50~60℃水浴,得到溶液B;C.將溶液A和溶液B按照2:1的比例混合,配置得到溶液C;在溶液C中加入3g二氧化硅碳納米管,置于磁力攪拌器上70~80℃攪拌1~2h,逐滴加入正硅酸乙酯,攪拌2~3h,加入20ml無水乙醇攪拌30min,將上述溶液置于40Gy193Irγ射線下照射30min后,置于0.5~30KPa負壓下抽濾,將濾料放入馬弗爐中1000~1200℃煅燒1~3h,取出冷卻研磨,過1200目篩即得;S4,將經過S2處理的基材涂刷上經過S3制備而成的光敏抗菌油漆即可。實驗測試:(1)點滴試驗:鹽霧試驗:腐蝕液用NaCl溶液,濃度為90~100mg/mL,pH值為6.5~9.5,鹽霧沉降量為3.0ml/100cm3.h;連續(xù)噴霧168h為一個周期,測量基材表面的腐蝕率。168h鹽霧腐蝕后,采用本發(fā)明方法制備的復合膜體系沒有出現(xiàn)起泡或者脫漆的現(xiàn)象;連續(xù)進行2個周期后,出現(xiàn)了非常輕微的直徑不超過0.5mm的起泡點,基材表面的腐蝕率小于0.5%;試驗進行4個周期后,復合膜體系的表面出現(xiàn)了直徑不超過0.8mm的起泡點,基材表面的腐蝕率小于5%。因此,在成膜的表面涂刷了光敏抗菌油漆后組成的復合膜體系大大的提高了漆膜的耐腐蝕性能,復合膜體系的起泡和剝離現(xiàn)象得到有效的抑制,表現(xiàn)出非常優(yōu)異的耐腐蝕性能,試驗進行5個周期后,基材表面的腐蝕率才達到10%。(2)抗菌性能測試:檢測該復合膜對大腸桿菌、霉菌和金黃色葡萄球菌的抑菌效果。結果如表1、表2、表3所示。表1復合膜對大腸桿菌的抑菌率及6個月后在30min時的抑菌率表2復合膜對霉菌的抑菌率及6個月后在30min時的抑菌率接觸時間(min)抑菌率0020100%3099%5099%6099%6個月后30min99%表3復合膜對金黃色葡萄球菌的抑菌率及6個月后在30min時的抑菌率接觸時間(min)抑菌率0020100%3097%5097%6096%6個月后30min96%試驗表明,20分鐘時,該復合膜對大腸桿菌、霉菌和金黃色葡萄球菌的抑菌率已經達到100%,表現(xiàn)出優(yōu)異的抗菌性能;在經過長達6個月的自然環(huán)境暴曬后,30min內對上述細菌的抑菌率均在96%以上,因此,根據本發(fā)明的實施例所提供的方法制備而成的復合膜具有優(yōu)異的持久抑菌效果。結果表明,利用本發(fā)明提供的方法制備而成的復合膜體系具有優(yōu)異的抗腐蝕和抑菌的性能。經過含有鈦鋯處理液處理過的基材和光敏抗菌油漆之間的協(xié)同作用,使得鋁或者鋁合金表面得到非常好的保護。應用場景3圖1是根據一示例性實施例示出的基于超材料的波導裝置9,如圖1所示,包括波導導管10和分隔片20;所述波導導管10內部設置有分隔片20,所述分隔片20沿所述波導導管10的內部斜向下設置,將所述波導導管10分隔成為兩個部分。本發(fā)明的上述實施例提供的基于超材料的波導裝置的結構設置合理,從而解決了上述技術問題。優(yōu)選地,所述分隔片20由超導材料制成。優(yōu)選地,所述分隔片20與波導導管10的中心軸的方向形成的角度為0~90°。優(yōu)選地,所述分隔片20與波導導管10的中心軸的方向形成的角度為45°。優(yōu)選地,所述波導裝置9的外表面涂刷有防腐抗菌膜;圖2是根據一示例性實施例示出的基于超材料的波導裝置的防腐抗菌膜的制備方法的工藝流程圖。參照圖2,所述防腐抗菌膜的制備方法包括以下步驟:S1,基材的處理:將鋁或鋁合金經過500#~800#的水磨砂紙打磨光亮,分別用乙醇和自來水清洗,依次經過除油和酸洗處理,取出然后用蒸餾水沖洗,置于40℃下烘干;其中,所述除油溶液的配方為:氫氧化鈉、環(huán)己烷、碳酸氫鈉、脂肪醇聚氧乙烯醚、乳化劑、苯并三氮唑、除油液溫度為50~60℃、除油時間為30~45s;所述酸性溶液的配方為:70%~80%硫酸10份、70%~90%硝酸1份、50%高錳酸鉀3份、1%單乙醇胺、活化溫度為50~60℃、活化時間為20~30s;酸性溶液的目的是除去鋁合金表面的氧化膜、氧化皮、銹蝕產物,并改變鋁合金表面狀態(tài);S2,成膜:將經過步驟S1處理過的基材試樣浸入處理液中40s,置于紅外燈下烘烤2min;再重復浸漬30s,置于紅外燈下烘烤1min;其中,所述處理液配置如下:在適量的蒸餾水中加入適量的氯氧化鋯、偏鈦酸制成溶液A,在溶液A中依次加入硫酸、羥基亞乙基二膦酸和氨基三亞甲基膦酸,制成制成溶液B,在溶液B中加超純水水定容至1000ml,用氨水調節(jié)溶液pH值至7.5~8.5;S3,制備光敏抗菌油漆膜:A.制備抗菌粉體:稱取10g脲胺、10g碳酸氫銨、5g氯化銨和15g分散劑十六烷基三甲基溴化銨,加入1000ml超純水,搖晃1~2min,加入5gNaCl,搖晃30min,加入1mol/LNaOH溶液調節(jié)pH值至8.5~9.5,采用經過拉伸的長頸滴管滴加AgNO3溶液,搖晃30min,標記為溶液A;B.將步驟A中制得的溶液A中加入10mlTiO2溶液,再加入10ml磷酸鋯,于50~60℃水浴,得到溶液B;C.將溶液A和溶液B按照2:1的比例混合,配置得到溶液C;在溶液C中加入3g二氧化硅碳納米管,置于磁力攪拌器上70~80℃攪拌1~2h,逐滴加入正硅酸乙酯,攪拌2~3h,加入20ml無水乙醇攪拌30min,將上述溶液置于40Gy193Irγ射線下照射30min后,置于0.5~30KPa負壓下抽濾,將濾料放入馬弗爐中1000~1200℃煅燒1~3h,取出冷卻研磨,過1200目篩即得;S4,將經過S2處理的基材涂刷上經過S3制備而成的光敏抗菌油漆即可。實驗測試:(1)點滴試驗:鹽霧試驗:腐蝕液用NaCl溶液,濃度為90~100mg/mL,pH值為6.5~9.5,鹽霧沉降量為3.0ml/100cm3.h;連續(xù)噴霧168h為一個周期,測量基材表面的腐蝕率。168h鹽霧腐蝕后,采用本發(fā)明方法制備的復合膜體系沒有出現(xiàn)起泡或者脫漆的現(xiàn)象;連續(xù)進行2個周期后,出現(xiàn)了非常輕微的直徑不超過0.5mm的起泡點,基材表面的腐蝕率小于0.5%;試驗進行4個周期后,復合膜體系的表面出現(xiàn)了直徑不超過0.8mm的起泡點,基材表面的腐蝕率小于5%。因此,在成膜的表面涂刷了光敏抗菌油漆后組成的復合膜體系大大的提高了漆膜的耐腐蝕性能,復合膜體系的起泡和剝離現(xiàn)象得到有效的抑制,表現(xiàn)出非常優(yōu)異的耐腐蝕性能,試驗進行5個周期后,基材表面的腐蝕率才達到10%。(2)抗菌性能測試:檢測該復合膜對大腸桿菌、霉菌和金黃色葡萄球菌的抑菌效果。結果如表1、表2、表3所示。表1復合膜對大腸桿菌的抑菌率及6個月后在30min時的抑菌率表2復合膜對霉菌的抑菌率及6個月后在30min時的抑菌率接觸時間(min)抑菌率0020100%3099%5099%6099%6個月后30min99%表3復合膜對金黃色葡萄球菌的抑菌率及6個月后在30min時的抑菌率接觸時間(min)抑菌率0020100%3099%5099%6099%6個月后30min99%試驗表明,20分鐘時,該復合膜對大腸桿菌、霉菌和金黃色葡萄球菌的抑菌率已經達到100%,表現(xiàn)出優(yōu)異的抗菌性能;在經過長達6個月的自然環(huán)境暴曬后,30min內對上述細菌的抑菌率均在98%以上,因此,根據本發(fā)明的實施例所提供的方法制備而成的復合膜具有優(yōu)異的持久抑菌效果。結果表明,利用本發(fā)明提供的方法制備而成的復合膜體系具有優(yōu)異的抗腐蝕和抑菌的性能。經過含有鈦鋯處理液處理過的基材和光敏抗菌油漆之間的協(xié)同作用,使得鋁或者鋁合金表面得到非常好的保護。應用場景4圖1是根據一示例性實施例示出的基于超材料的波導裝置9,如圖1所示,包括波導導管10和分隔片20;所述波導導管10內部設置有分隔片20,所述分隔片20沿所述波導導管10的內部斜向下設置,將所述波導導管10分隔成為兩個部分。本發(fā)明的上述實施例提供的基于超材料的波導裝置的結構設置合理,從而解決了上述技術問題。優(yōu)選地,所述分隔片20由超導材料制成。優(yōu)選地,所述分隔片20與波導導管10的中心軸的方向形成的角度為0~90°。優(yōu)選地,所述分隔片20與波導導管10的中心軸的方向形成的角度為45°。優(yōu)選地,所述波導裝置9的外表面涂刷有防腐抗菌膜;圖2是根據一示例性實施例示出的基于超材料的波導裝置的防腐抗菌膜的制備方法的工藝流程圖。參照圖2,所述防腐抗菌膜的制備方法包括以下步驟:S1,基材的處理:將鋁或鋁合金經過500#~800#的水磨砂紙打磨光亮,分別用乙醇和自來水清洗,依次經過除油和酸洗處理,取出然后用蒸餾水沖洗,置于40℃下烘干;其中,所述除油溶液的配方為:氫氧化鈉、環(huán)己烷、碳酸氫鈉、脂肪醇聚氧乙烯醚、乳化劑、苯并三氮唑、除油液溫度為50~60℃、除油時間為30~45s;所述酸性溶液的配方為:70%~80%硫酸10份、70%~90%硝酸1份、50%高錳酸鉀3份、1%單乙醇胺、活化溫度為50~60℃、活化時間為20~30s;酸性溶液的目的是除去鋁合金表面的氧化膜、氧化皮、銹蝕產物,并改變鋁合金表面狀態(tài);S2,成膜:將經過步驟S1處理過的基材試樣浸入處理液中40s,置于紅外燈下烘烤2min;再重復浸漬30s,置于紅外燈下烘烤1min;其中,所述處理液配置如下:在適量的蒸餾水中加入適量的氯氧化鋯、偏鈦酸制成溶液A,在溶液A中依次加入硫酸、羥基亞乙基二膦酸和氨基三亞甲基膦酸,制成制成溶液B,在溶液B中加超純水水定容至1000ml,用氨水調節(jié)溶液pH值至7.5~8.5;S3,制備光敏抗菌油漆膜:A.制備抗菌粉體:稱取10g脲胺、10g碳酸氫銨、5g氯化銨和15g分散劑十六烷基三甲基溴化銨,加入1000ml超純水,搖晃1~2min,加入5gNaCl,搖晃30min,加入1mol/LNaOH溶液調節(jié)pH值至8.5~9.5,采用經過拉伸的長頸滴管滴加AgNO3溶液,搖晃30min,標記為溶液A;B.將步驟A中制得的溶液A中加入10mlTiO2溶液,再加入10ml磷酸鋯,于50~60℃水浴,得到溶液B;C.將溶液A和溶液B按照2:1的比例混合,配置得到溶液C;在溶液C中加入3g二氧化硅碳納米管,置于磁力攪拌器上70~80℃攪拌1~2h,逐滴加入正硅酸乙酯,攪拌2~3h,加入20ml無水乙醇攪拌30min,將上述溶液置于40Gy193Irγ射線下照射30min后,置于0.5~30KPa負壓下抽濾,將濾料放入馬弗爐中1000~1200℃煅燒1~3h,取出冷卻研磨,過1200目篩即得;S4,將經過S2處理的基材涂刷上經過S3制備而成的光敏抗菌油漆即可。實驗測試:(1)點滴試驗:鹽霧試驗:腐蝕液用NaCl溶液,濃度為90~100mg/mL,pH值為6.5~9.5,鹽霧沉降量為3.0ml/100cm3.h;連續(xù)噴霧168h為一個周期,測量基材表面的腐蝕率。168h鹽霧腐蝕后,采用本發(fā)明方法制備的復合膜體系沒有出現(xiàn)起泡或者脫漆的現(xiàn)象;連續(xù)進行2個周期后,出現(xiàn)了非常輕微的直徑不超過0.5mm的起泡點,基材表面的腐蝕率小于0.5%;試驗進行4個周期后,復合膜體系的表面出現(xiàn)了直徑不超過0.8mm的起泡點,基材表面的腐蝕率小于5%。因此,在成膜的表面涂刷了光敏抗菌油漆后組成的復合膜體系大大的提高了漆膜的耐腐蝕性能,復合膜體系的起泡和剝離現(xiàn)象得到有效的抑制,表現(xiàn)出非常優(yōu)異的耐腐蝕性能,試驗進行5個周期后,基材表面的腐蝕率才達到10%。(2)抗菌性能測試:檢測該復合膜對大腸桿菌、霉菌和金黃色葡萄球菌的抑菌效果。結果如表1、表2、表3所示。表1復合膜對大腸桿菌的抑菌率及6個月后在30min時的抑菌率表2復合膜對霉菌的抑菌率及6個月后在30min時的抑菌率接觸時間(min)抑菌率0020100%3099%5099%6099%6個月后30min99%表3復合膜對金黃色葡萄球菌的抑菌率及6個月后在30min時的抑菌率接觸時間(min)抑菌率0020100%30100%50100%60100%6個月后30min99%試驗表明,20分鐘時,該復合膜對大腸桿菌、霉菌和金黃色葡萄球菌的抑菌率已經達到100%,表現(xiàn)出優(yōu)異的抗菌性能;在經過長達6個月的自然環(huán)境暴曬后,30min內對上述細菌的抑菌率均在99%以上,因此,根據本發(fā)明的實施例所提供的方法制備而成的復合膜具有優(yōu)異的持久抑菌效果。結果表明,利用本發(fā)明提供的方法制備而成的復合膜體系具有優(yōu)異的抗腐蝕和抑菌的性能。經過含有鈦鋯處理液處理過的基材和光敏抗菌油漆之間的協(xié)同作用,使得鋁或者鋁合金表面得到非常好的保護。應用場景5圖1是根據一示例性實施例示出的基于超材料的波導裝置9,如圖1所示,包括波導導管10和分隔片20;所述波導導管10內部設置有分隔片20,所述分隔片20沿所述波導導管10的內部斜向下設置,將所述波導導管10分隔成為兩個部分。本發(fā)明的上述實施例提供的基于超材料的波導裝置的結構設置合理,從而解決了上述技術問題。優(yōu)選地,所述分隔片20由超導材料制成。優(yōu)選地,所述分隔片20與波導導管10的中心軸的方向形成的角度為0~90°。優(yōu)選地,所述分隔片20與波導導管10的中心軸的方向形成的角度為45°。優(yōu)選地,所述波導裝置9的外表面涂刷有防腐抗菌膜;圖2是根據一示例性實施例示出的基于超材料的波導裝置的防腐抗菌膜的制備方法的工藝流程圖。參照圖2,所述防腐抗菌膜的制備方法包括以下步驟:S1,基材的處理:將鋁或鋁合金經過500#~800#的水磨砂紙打磨光亮,分別用乙醇和自來水清洗,依次經過除油和酸洗處理,取出然后用蒸餾水沖洗,置于40℃下烘干;其中,所述除油溶液的配方為:氫氧化鈉、環(huán)己烷、碳酸氫鈉、脂肪醇聚氧乙烯醚、乳化劑、苯并三氮唑、除油液溫度為50~60℃、除油時間為30~45s;所述酸性溶液的配方為:70%~80%硫酸10份、70%~90%硝酸1份、50%高錳酸鉀3份、1%單乙醇胺、活化溫度為50~60℃、活化時間為20~30s;酸性溶液的目的是除去鋁合金表面的氧化膜、氧化皮、銹蝕產物,并改變鋁合金表面狀態(tài);S2,成膜:將經過步驟S1處理過的基材試樣浸入處理液中40s,置于紅外燈下烘烤2min;再重復浸漬30s,置于紅外燈下烘烤1min;其中,所述處理液配置如下:在適量的蒸餾水中加入適量的氯氧化鋯、偏鈦酸制成溶液A,在溶液A中依次加入硫酸、羥基亞乙基二膦酸和氨基三亞甲基膦酸,制成制成溶液B,在溶液B中加超純水水定容至1000ml,用氨水調節(jié)溶液pH值至7.5~8.5;S3,制備光敏抗菌油漆膜:A.制備抗菌粉體:稱取10g脲胺、10g碳酸氫銨、5g氯化銨和15g分散劑十六烷基三甲基溴化銨,加入1000ml超純水,搖晃1~2min,加入5gNaCl,搖晃30min,加入1mol/LNaOH溶液調節(jié)pH值至8.5~9.5,采用經過拉伸的長頸滴管滴加AgNO3溶液,搖晃30min,標記為溶液A;B.將步驟A中制得的溶液A中加入10mlTiO2溶液,再加入10ml磷酸鋯,于50~60℃水浴,得到溶液B;C.將溶液A和溶液B按照2:1的比例混合,配置得到溶液C;在溶液C中加入3g二氧化硅碳納米管,置于磁力攪拌器上70~80℃攪拌1~2h,逐滴加入正硅酸乙酯,攪拌2~3h,加入20ml無水乙醇攪拌30min,將上述溶液置于40Gy193Irγ射線下照射30min后,置于0.5~30KPa負壓下抽濾,將濾料放入馬弗爐中1000~1200℃煅燒1~3h,取出冷卻研磨,過1200目篩即得;S4,將經過S2處理的基材涂刷上經過S3制備而成的光敏抗菌油漆即可。實驗測試:(1)點滴試驗:鹽霧試驗:腐蝕液用NaCl溶液,濃度為90~100mg/mL,pH值為6.5~9.5,鹽霧沉降量為3.0ml/100cm3.h;連續(xù)噴霧168h為一個周期,測量基材表面的腐蝕率。168h鹽霧腐蝕后,采用本發(fā)明方法制備的復合膜體系沒有出現(xiàn)起泡或者脫漆的現(xiàn)象;連續(xù)進行2個周期后,出現(xiàn)了非常輕微的直徑不超過0.5mm的起泡點,基材表面的腐蝕率小于0.5%;試驗進行4個周期后,復合膜體系的表面出現(xiàn)了直徑不超過0.8mm的起泡點,基材表面的腐蝕率小于5%。因此,在成膜的表面涂刷了光敏抗菌油漆后組成的復合膜體系大大的提高了漆膜的耐腐蝕性能,復合膜體系的起泡和剝離現(xiàn)象得到有效的抑制,表現(xiàn)出非常優(yōu)異的耐腐蝕性能,試驗進行5個周期后,基材表面的腐蝕率才達到10%。(2)抗菌性能測試:檢測該復合膜對大腸桿菌、霉菌和金黃色葡萄球菌的抑菌效果。結果如表1、表2、表3所示。表1復合膜對大腸桿菌的抑菌率及6個月后在30min時的抑菌率表2復合膜對霉菌的抑菌率及6個月后在30min時的抑菌率接觸時間(min)抑菌率0020100%30100%50100%60100%6個月后30min100%表3復合膜對金黃色葡萄球菌的抑菌率及6個月后在30min時的抑菌率接觸時間(min)抑菌率0020100%3099%5099%6099%6個月后30min99%試驗表明,20分鐘時,該復合膜對大腸桿菌、霉菌和金黃色葡萄球菌的抑菌率已經達到100%,表現(xiàn)出優(yōu)異的抗菌性能;在經過長達6個月的自然環(huán)境暴曬后,30min內對上述細菌的抑菌率均在96%以上,因此,根據本發(fā)明的實施例所提供的方法制備而成的復合膜具有優(yōu)異的持久抑菌效果。結果表明,利用本發(fā)明提供的方法制備而成的復合膜體系具有優(yōu)異的抗腐蝕和抑菌的性能。經過含有鈦鋯處理液處理過的基材和光敏抗菌油漆之間的協(xié)同作用,使得鋁或者鋁合金表面得到非常好的保護。最后應當說明的是,以上實施例僅用以說明本發(fā)明的技術方案,而非對本發(fā)明保護范圍的限制,盡管參照較佳實施例對本發(fā)明作了詳細地說明,本領域的普通技術人員應當理解,可以對本發(fā)明的技術方案進行修改或者等同替換,而不脫離本發(fā)明技術方案的實質和范圍。當前第1頁1 2 3