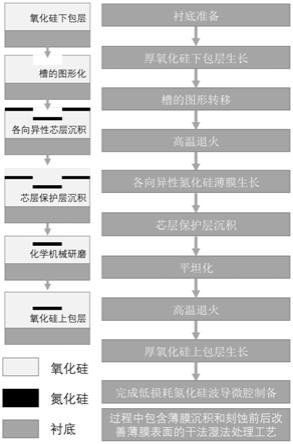
1.本發(fā)明涉及一種低損耗氮化硅波導(dǎo)的制備方法,屬于硅基光子器件制備技術(shù)領(lǐng)域。
背景技術(shù):2.氮化硅材料的折射率高于二氧化硅,且氧化硅和氮化硅的薄膜方法與cmos平臺(tái)兼容。在硅基平臺(tái)上,氮化硅是極為理想的芯層材料;而氧化硅良好的光電特性,以及極低的光損耗,使得其稱(chēng)為包層材料的最佳選擇。在硅基光子學(xué)快速發(fā)展的今天,芯層為氮化硅的低損耗的波導(dǎo)、微腔、光柵等等結(jié)構(gòu)可以為光子學(xué)設(shè)計(jì)提供巨大的方法和技術(shù)支撐。
3.盡管如此,現(xiàn)有的氮化硅波導(dǎo)方法依然有三個(gè)缺點(diǎn):首先,氮化硅由于其材料特性,其對(duì)光的損耗,要高于氧化硅材料;其次,傳統(tǒng)的氮化硅波導(dǎo)加工方法步驟,會(huì)用到刻蝕方法刻蝕氮化硅芯層,刻蝕會(huì)引入很大的側(cè)壁粗糙度,從而導(dǎo)致?lián)p耗增加;第三,現(xiàn)有的氮化硅波導(dǎo)大多在300nm
–
500nm,不僅由于應(yīng)力的問(wèn)題影響加工,同時(shí),更厚的氮化硅波導(dǎo)更容易受到側(cè)壁粗糙度的影響,從而有更大的損耗。
技術(shù)實(shí)現(xiàn)要素:4.本發(fā)明的主要目的是提供一種低損耗氮化硅波導(dǎo)的制備方法,能夠?qū)崿F(xiàn)低損耗氮化硅波導(dǎo)的制備,降低氮化硅波導(dǎo)的損耗。本發(fā)明所述氮化硅波導(dǎo)包括但不限于條形波導(dǎo)、脊型波導(dǎo)等結(jié)構(gòu),而是包含任何氮化硅材質(zhì)的可以實(shí)現(xiàn)導(dǎo)引光波功能的結(jié)構(gòu)。本發(fā)明通過(guò)氮化硅芯層定義光波導(dǎo),使得光的能量主要在氧化硅中傳播,從而能夠利用氧化硅超低光損耗的特性。通過(guò)各向異性薄膜沉積填槽,配合平坦化的方式形成氮化硅芯層,避免對(duì)氮化硅芯層的刻蝕和直接研磨,從而避免芯層表面粗糙度和損傷帶來(lái)的損耗。通過(guò)較薄的氮化硅芯層在實(shí)現(xiàn)對(duì)光的弱束縛的同時(shí),也使得氮化硅的側(cè)壁本身較小,從而進(jìn)一步降低側(cè)壁粗糙度對(duì)光損耗的影響。所述較薄的氮化硅芯層指比現(xiàn)有技術(shù)氮化硅波導(dǎo)薄。本發(fā)明可以兼容弱束縛光波導(dǎo)結(jié)構(gòu),實(shí)現(xiàn)進(jìn)一步低損耗的氮化硅光波導(dǎo)制備。
5.本發(fā)明的目的是通過(guò)以下技術(shù)方案實(shí)現(xiàn):
6.本發(fā)明公開(kāi)的一種低損耗氮化硅波導(dǎo)的制備方法,包括如下步驟:
7.步驟一:準(zhǔn)備晶圓襯底,并對(duì)襯底進(jìn)行清洗;
8.步驟二:在襯底上進(jìn)行厚的氧化硅下包層生長(zhǎng);
9.步驟三:使用光刻和刻蝕的方法完成圖形轉(zhuǎn)移,在下包層上形成槽,完成波導(dǎo)的圖形定義;
10.步驟四:對(duì)波導(dǎo)進(jìn)行高溫退火,實(shí)現(xiàn)氧化硅的回流;
11.步驟五:使用各向異性沉積方法進(jìn)行各項(xiàng)異性的氮化硅薄膜生長(zhǎng);
12.步驟六:使用化學(xué)氣相沉積方法進(jìn)行芯層保護(hù)層氧化硅薄膜生長(zhǎng);
13.步驟七:使用化學(xué)機(jī)械平坦化方法進(jìn)行化學(xué)機(jī)械研磨平坦化晶圓,去除高處的氮化硅薄膜;
14.步驟八:進(jìn)行高溫退火改善氮化硅的形貌和光學(xué)損耗;
15.步驟九:生長(zhǎng)厚的氧化硅薄膜,完成上包層,完成低損耗的氮化硅波導(dǎo)的制備。
16.本發(fā)明公開(kāi)的一種低損耗氮化硅波導(dǎo)的制備方法,還包含薄膜沉積和刻蝕前后改善薄膜表面的干法濕法處理方法。
17.本發(fā)明公開(kāi)的一種低損耗氮化硅波導(dǎo)的制備方法,通過(guò)氮化硅芯層定義光波導(dǎo),使得光的能量主要在氧化硅中傳播,從而能夠利用氧化硅超低光損耗的特性。通過(guò)各向異性薄膜沉積填槽,配合平坦化的方式形成氮化硅芯層,避免對(duì)氮化硅芯層的刻蝕和直接研磨,從而避免芯層表面粗糙度和損傷帶來(lái)的損耗。通過(guò)較薄的氮化硅芯層在實(shí)現(xiàn)對(duì)光的弱束縛的同時(shí),也使得氮化硅的側(cè)壁本身較小,從而進(jìn)一步降低側(cè)壁粗糙度對(duì)光損耗的影響。所述較薄的氮化硅芯層指比現(xiàn)有技術(shù)氮化硅波導(dǎo)薄。本發(fā)明能夠兼容弱束縛光波導(dǎo)結(jié)構(gòu),實(shí)現(xiàn)進(jìn)一步低損耗的氮化硅光波導(dǎo)制備。
18.本發(fā)明還包含薄膜沉積和刻蝕前后改善薄膜表面的干法濕法處理方法。
19.所述的下包層、上包層不限于二氧化硅薄膜,或?yàn)槠渌凵渎氏鄬?duì)較低的材料,所述折射率相對(duì)較低的材料不限于二氧化硅薄膜、石英、玻璃。所述下包層、上包層成膜手段生長(zhǎng)包括使用干氧或濕氧熱氧化、化學(xué)氣相沉積、濺射、蒸發(fā)。
20.所述的芯層不限于氮化硅,或?yàn)槠渌凵渎氏鄬?duì)較高的材料,所述折射率相對(duì)較高的材料包括氮化硅、氮化鋁、鋁鎵砷、碳化硅,所述的芯層成膜手段生長(zhǎng)包括化學(xué)氣相沉積、分子束外延、濺射、蒸發(fā)。
21.所述下包層、上包層的氧化硅薄膜,其厚度較厚;所述芯層氮化硅薄膜,其典型厚度為百納米級(jí)。
22.所述襯底不限于硅襯底,還包括但不限于soi、藍(lán)寶石的其他襯底。
23.所述的光刻刻蝕包含波導(dǎo)版圖的制備;晶圓涂膠;圖形轉(zhuǎn)移;反應(yīng)離子刻蝕;所述圖形轉(zhuǎn)移包含但不限于接近式、接觸式、步進(jìn)式曝光、納米壓印、自組裝。
24.側(cè)壁氮化硅生長(zhǎng)速率緩慢,幾乎能夠忽略,所述各向異性的氮化硅沉積方法實(shí)現(xiàn)方法包括襯底偏壓、沉積-刻蝕循環(huán)方法,或基于側(cè)壁與平面薄膜生長(zhǎng)速率不同、結(jié)合濕法腐蝕回刻實(shí)現(xiàn)。
25.所述平坦化方法,去除高處的氮化硅薄膜,停在氧化硅下包層上面,槽底部的氮化硅不受平坦化的影響。
26.1、本發(fā)明公開(kāi)的一種低損耗氮化硅波導(dǎo)的制備方法,通過(guò)使用氧化硅回流方法將槽側(cè)壁粗糙度降低到亞納米量級(jí),再引入各向異性薄膜沉積技術(shù)填槽,配合化學(xué)機(jī)械平坦化,規(guī)避了對(duì)波導(dǎo)芯層的刻蝕。從而減小芯層等離子體損傷和側(cè)壁粗糙度。
27.2、本發(fā)明公開(kāi)的一種低損耗氮化硅波導(dǎo)的制備方法,在沒(méi)有增加方法復(fù)雜度的情況下,避免芯層刻蝕引入的波導(dǎo)側(cè)壁粗糙度損耗。同時(shí),使用弱束縛波導(dǎo),在通過(guò)氮化硅定義波導(dǎo)芯層的同時(shí),光的大部分能量在氧化硅中傳播,同樣能夠顯著降低波導(dǎo)損耗,有效地實(shí)現(xiàn)與cmos方法平臺(tái)兼容的低損耗氮化硅波導(dǎo)的制備。
28.3、本發(fā)明公開(kāi)的一種低損耗氮化硅波導(dǎo)的制備方法,使用與cmos平臺(tái)兼容的方法,利用各向異性填槽和化學(xué)機(jī)械研磨方法,避免對(duì)波導(dǎo)芯層的刻蝕和直接研磨,從而避免芯層表面粗糙度和損傷帶來(lái)的損耗。本發(fā)明能夠兼容弱束縛光波導(dǎo)結(jié)構(gòu),實(shí)現(xiàn)進(jìn)一步低損耗的氮化硅光波導(dǎo)制備。
29.4、本發(fā)明公開(kāi)的一種低損耗氮化硅波導(dǎo)的制備方法,通過(guò)行高溫退火改善氮化硅的形貌和光學(xué)損耗。
附圖說(shuō)明
30.圖1為低損耗氮化硅波導(dǎo)的制備方法的具體實(shí)施方法流程示意圖及方法步驟說(shuō)明;
31.圖2為本發(fā)明的一個(gè)實(shí)例,波導(dǎo)結(jié)構(gòu)示意。圖中標(biāo)號(hào):1-襯底,2-氧化硅下包層,3-氧化硅上包層,4-氮化硅芯層,5-定義波導(dǎo)的凹槽。
具體實(shí)施方式
32.下面結(jié)合附圖2對(duì)本發(fā)明做進(jìn)一步說(shuō)明。
33.實(shí)施例1:
34.如圖1和圖2所示,本實(shí)施例公開(kāi)的一種低損耗氮化硅波導(dǎo)的制備方法,包括:
35.步驟1,首先進(jìn)行襯底準(zhǔn)備,對(duì)應(yīng)圖2襯底1,對(duì)襯底進(jìn)行爐前清洗。步驟2,在襯底上進(jìn)行15μm氧化硅薄膜生長(zhǎng),使用濕氧氧化方法,對(duì)應(yīng)圖2氧化硅下包層2。步驟3,使用設(shè)計(jì)好的版圖進(jìn)行波導(dǎo)結(jié)構(gòu)的光刻刻蝕方法,完成圖形轉(zhuǎn)移,形成定義波導(dǎo)所需的槽,槽深500nm,對(duì)應(yīng)圖2定義波導(dǎo)的凹槽5。步驟4,進(jìn)行大約1200℃的3小時(shí)高溫退火。步驟5,使用帶襯底偏壓的hdpcvd方法,進(jìn)行各向異性的氮化硅芯層薄膜生長(zhǎng)。芯層厚度為110nm。然后使用濕法處理掉側(cè)壁較薄的氮化硅,使得氮化硅薄膜剩余100nm。步驟6,使用pecvd生長(zhǎng)氧化硅薄膜,400nm,作為化學(xué)機(jī)械研磨時(shí)候芯層的保護(hù)層。步驟7,使用化學(xué)機(jī)械研磨對(duì)晶圓進(jìn)行平坦化,剩余的氮化硅芯層對(duì)應(yīng)圖2氮化硅芯層4。步驟8,進(jìn)行3小時(shí)高溫退火。步驟9,使用pecvd方法進(jìn)行15um的氧化硅上包層生長(zhǎng),對(duì)應(yīng)圖2氧化硅上包層3。完成低損耗氮化硅波導(dǎo)的制備。
36.根據(jù)散射損耗與粗糙度的關(guān)系式:
[0037][0038]
其中,α代表了波導(dǎo)散射損耗,κ=0.48,n為波導(dǎo)有效折射率,k為真空波數(shù),d為波導(dǎo)寬度一半,σ為波導(dǎo)頂面和側(cè)壁粗糙度,可以看出損耗隨著粗糙度的平方的減小而減小。
[0039]
以上所述,僅為本發(fā)明中的具體實(shí)施方式,但本發(fā)明的保護(hù)范圍并不局限于此,任何熟悉該技術(shù)的人在本發(fā)明所揭露的技術(shù)范圍內(nèi),所做的任何修改、等同替換、改進(jìn)等,均應(yīng)包含在本發(fā)明的保護(hù)范圍之內(nèi)。因此,本發(fā)明的保護(hù)范圍應(yīng)該以權(quán)利要求書(shū)的保護(hù)范圍為準(zhǔn)。