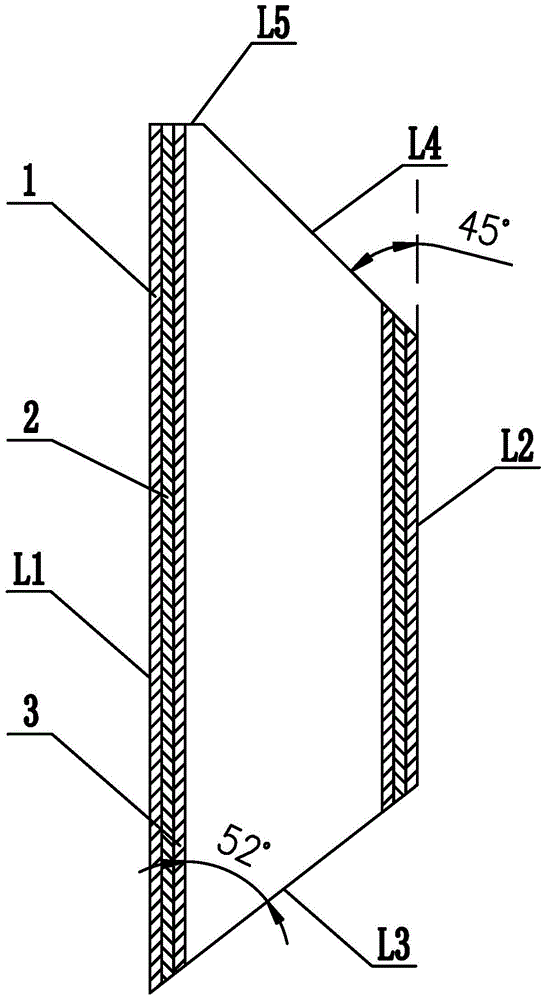
本發(fā)明屬于管件成型技術(shù)領(lǐng)域,具體涉及一種稀有金屬薄壁彎頭的冷成型方法。
背景技術(shù):稀有金屬例如鈦、鋯、鉭、鎳等,由于這些材料在石油、化工、制藥等行業(yè)中較為苛刻的工況條件下,能夠表現(xiàn)出很好的耐蝕,耐高溫強(qiáng)度,良好的導(dǎo)熱性等特點(diǎn)而被廣泛的應(yīng)用。但是這些材料價(jià)格卻相對(duì)較高,對(duì)于不承受壓力只要求耐蝕的管件,材料成本是人們主要考慮的問(wèn)題,在保證管件強(qiáng)度的前提下,盡量使用壁厚較薄的材料制備。在彎頭冷成型過(guò)程中,工件與模具之間的摩擦力,以及在“R”區(qū)的變形力都很大。公稱(chēng)直徑在DN15mm~DN100mm范圍內(nèi)的90°彎頭,使用壁厚大于1.5mm,且徑厚比小于15的稀有金屬管坯,利用冷成型模具(包括鋼球)可以直接成型。這是因?yàn)楣芘鞅诤褫^厚,具有一定的剛度,且在變形最大的內(nèi)弧側(cè)和外弧側(cè)利用壁厚增厚和減薄,從而抵抗摩擦力和變形力,使彎頭達(dá)到要求尺寸。當(dāng)使用壁厚為0.4mm~1.5mm,且徑厚比大于等于15的稀有金屬管坯,利用冷成型模具(包括鋼球)將很難成型。這是因?yàn)椋阂?、管坯較薄,其本身的剛度不能夠抵抗摩擦力和變形力,如果不用任何工裝輔助成型,在沖頭下壓力的作用下管坯極易出現(xiàn)褶皺甚至材料堆積的現(xiàn)象;二、管坯壁厚為0.4mm~1.5mm,而模具孔與沖頭外徑之間的間隙約為0.3mm~0.8mm,沖頭與模具孔同心度如果稍有偏差,將極易出現(xiàn)部分管坯無(wú)法接觸到?jīng)_頭下壓面,即壓偏現(xiàn)象,一旦出現(xiàn)壓偏該彎頭將無(wú)法成型,同時(shí)還會(huì)損傷模具。
技術(shù)實(shí)現(xiàn)要素:本發(fā)明所要解決的技術(shù)問(wèn)題在于針對(duì)上述現(xiàn)有技術(shù)的不足,提供一種稀有金屬薄壁彎頭的冷成型方法。該方法能夠有效地解決稀有金屬薄壁彎頭成型難度大,尤其是壁厚為0.4mm~1.5mm的彎頭成型難度更大的問(wèn)題。采用該方法只需使用普通的彎頭成型模具,即可得到壁厚為0.4mm~1.5mm的稀有金屬薄壁彎頭,具有產(chǎn)品質(zhì)量高,成品率高達(dá)98%的顯著特點(diǎn)。為解決上述技術(shù)問(wèn)題,本發(fā)明采用的技術(shù)方案是:一種稀有金屬薄壁彎頭的冷成型方法,其特征在于,包括以下步驟:步驟一、根據(jù)所要成型的薄壁彎頭的材質(zhì)和尺寸選擇稀有金屬管并對(duì)所述稀有金屬管進(jìn)行切割,得到管坯,然后根據(jù)所述管坯的尺寸選擇外套鋼管和內(nèi)襯鋼管;所述管坯、外套鋼管和內(nèi)襯鋼管的長(zhǎng)度均相同;步驟二、將步驟一中所述外套鋼管、管坯和內(nèi)襯鋼管按照由外至內(nèi)的順序套裝在一起,得到復(fù)合管,然后在所述復(fù)合管的兩端進(jìn)行點(diǎn)焊使外套鋼管、管坯和內(nèi)襯鋼管三者固定在一起;步驟三、在步驟二中點(diǎn)焊后的復(fù)合管的一端進(jìn)行整體切割形成第一斜面,在點(diǎn)焊后的復(fù)合管的另一端進(jìn)行部分切割形成平臺(tái)和第二斜面,得到異形復(fù)合管;所述異形復(fù)合管沿復(fù)合管中軸線(xiàn)和所述平臺(tái)的中心線(xiàn)的截面為五邊形,所述五邊形包括平行設(shè)置的左邊L1和右邊L2,用于連接左邊L1下端和右邊L2下端的第一斜邊L3,與左邊L1垂直的直邊L5,和用于連接直邊L5和右邊L2上端的第二斜邊L4,所述第一斜邊L3與左邊L1的夾角為52°,第二斜邊L4與右邊L2的延長(zhǎng)線(xiàn)的夾角為45°,所述左邊L1的長(zhǎng)度大于右邊L2的長(zhǎng)度;步驟四、對(duì)步驟三中所述異形復(fù)合管位于第一斜面和第二斜面的端部均進(jìn)行間斷焊形成焊點(diǎn),并對(duì)異形復(fù)合管位于所述平臺(tái)的端部進(jìn)行滿(mǎn)焊形成焊縫,然后在所述焊縫上機(jī)加工出一個(gè)平面;步驟五、將步驟四中機(jī)加工后的異形復(fù)合管置于彎頭成型模具的模腔內(nèi),使異形復(fù)合管的短邊位于模腔的內(nèi)彎部一側(cè),長(zhǎng)邊位于模腔的外彎部一側(cè),并使焊縫朝上放置,對(duì)異形復(fù)合管進(jìn)行冷成型,得到復(fù)合彎頭;步驟六、按照所要成型的薄壁彎頭尺寸對(duì)步驟五中所述復(fù)合彎頭進(jìn)行機(jī)械加工去除復(fù)合彎頭兩端多余部分,然后酸洗去除外套鋼管和內(nèi)襯鋼管,得到壁厚為0.4mm~1.5mm的稀有金屬薄壁彎頭。上述的一種稀有金屬薄壁彎頭的冷成型方法,其特征在于,步驟一中所述稀有金屬管為純鈦管、純鋯管、純鎳管或純鉭管。上述的一種稀有金屬薄壁彎頭的冷成型方法,其特征在于,步驟一中所述外套鋼管的內(nèi)徑比管坯的外徑大0.2mm~1mm,外套鋼管內(nèi)表面的粗糙度不大于6.3μm,外套鋼管的壁厚為1mm~1.5mm。上述的一種稀有金屬薄壁彎頭的冷成型方法,其特征在于,步驟一中所述內(nèi)襯鋼管的外徑比管坯的內(nèi)徑小0.2mm~1mm,內(nèi)襯鋼管外表面的粗糙度不大于6.3μm,內(nèi)襯鋼管的壁厚為1mm~1.5mm。上述的一種稀有金屬薄壁彎頭的冷成型方法,其特征在于,步驟三中所述直邊L5的長(zhǎng)度為外套鋼管直徑的1/5。上述的一種稀有金屬薄壁彎頭的冷成型方法,其特征在于,步驟四中機(jī)加工的深度不大于焊縫厚度的1/2。上述的一種稀有金屬薄壁彎頭的冷成型方法,其特征在于,步驟五中冷成型過(guò)程中對(duì)異形復(fù)合管進(jìn)行通球整形。本發(fā)明與現(xiàn)有技術(shù)相比具有以下優(yōu)點(diǎn):1、本發(fā)明能夠有效地解決稀有金屬薄壁彎頭成型難度大,尤其是壁厚為0.4mm~1.5mm的彎頭成型難度更大的問(wèn)題。采用本發(fā)明的冷成型方法,只需使用普通的彎頭成型模具,即可得到壁厚為0.4mm~1.5mm的稀有金屬薄壁彎頭,具有產(chǎn)品質(zhì)量高,成品率高達(dá)98%的顯著特點(diǎn)。2、本發(fā)明在彎頭成型前,用內(nèi)、外兩根鋼管將稀有金屬管坯夾在中間,使得管坯在成型過(guò)程中受到內(nèi)、外鋼管的夾持作用,并充分利用內(nèi)鋼管的剛度和外鋼管的保護(hù),同時(shí)增加了管坯的壁厚,增大了受力面積,最終得到壁厚為0.4mm~1.5mm的薄壁彎頭,從而有效控制成品彎頭出現(xiàn)外弧開(kāi)裂和內(nèi)弧起皺現(xiàn)象,避免了壓偏現(xiàn)象的發(fā)生,保護(hù)成品薄壁彎頭的表面不受損傷,同時(shí)對(duì)模具也起到了一定的保護(hù)作用。3、本發(fā)明方法新穎,可靠實(shí)用,工藝先進(jìn),特別適用于價(jià)格較高的稀有金屬材料制壁厚為0.4mm~1.5mm的薄壁彎頭的中小批量生產(chǎn),既能大大降低使用該彎頭設(shè)備的生產(chǎn)成本,又能保持設(shè)備整體的耐蝕性,顯著提高企業(yè)的經(jīng)濟(jì)效益。下面結(jié)合附圖和實(shí)施例,對(duì)本發(fā)明技術(shù)方案做進(jìn)一步的詳細(xì)說(shuō)明。附圖說(shuō)明圖1為本發(fā)明的異形復(fù)合管的立體結(jié)構(gòu)示意圖。圖2為本發(fā)明的異形復(fù)合管沿中軸線(xiàn)和平臺(tái)的中心線(xiàn)的截面示意圖。圖3為本發(fā)明在焊縫上機(jī)加工出平面的異形復(fù)合管的結(jié)構(gòu)示意圖。圖4為本發(fā)明異形復(fù)合管置于模具模腔中的位置關(guān)系示意圖。附圖標(biāo)記說(shuō)明:1—外套鋼管;2—管坯;3—內(nèi)襯鋼管;4—焊點(diǎn);5—焊縫;6—第一斜面;7—平臺(tái);8—第二斜面。具體實(shí)施方式實(shí)施例1本實(shí)施例所要成型的薄壁彎頭的材質(zhì)為純鉭,規(guī)格為DN20Ⅰ-0.4-Ta190E(L),成型方法具體為:步驟一、選擇外徑為25mm,壁厚為0.5mm的Ta1純鉭管并進(jìn)行切割,得到長(zhǎng)度為95mm,外徑為25mm,壁厚為0.5mm的管坯2,選擇長(zhǎng)度為95mm,外徑為28mm,壁厚為1mm的外套鋼管1,長(zhǎng)度為95mm,外徑為23.8mm,壁厚為1.5mm的內(nèi)襯鋼管3;所述外套鋼管1內(nèi)表面的粗糙度不大于6.3μm;所述內(nèi)襯鋼管3外表面的粗糙度不大于6.3μm;步驟二、將步驟一中所述外套鋼管1、管坯2和內(nèi)襯鋼管3按照由外至內(nèi)的順序套裝在一起,得到復(fù)合管,然后在所述復(fù)合管的兩端分別點(diǎn)焊3~4個(gè)點(diǎn)使外套鋼管1、管坯2和內(nèi)襯鋼管3三者固定在一起;步驟三、在步驟二中點(diǎn)焊后的復(fù)合管的一端進(jìn)行整體切割形成第一斜面6,在點(diǎn)焊后的復(fù)合管的另一端進(jìn)行部分切割形成平臺(tái)7和第二斜面8,得到異形復(fù)合管;如圖1所示,所述異形復(fù)合管沿復(fù)合管中軸線(xiàn)和所述平臺(tái)7的中心線(xiàn)的截面為五邊形,所述五邊形包括平行設(shè)置的左邊L1和右邊L2,用于連接左邊L1下端和右邊L2下端的第一斜邊L3,與左邊L1垂直的直邊L5,和用于連接直邊L5和右邊L2上端的第二斜邊L4,所述第一斜邊L3與左邊L1的夾角為52°,第二斜邊L4與右邊L2的延長(zhǎng)線(xiàn)的夾角為45°,所述左邊L1的長(zhǎng)度大于右邊L2的長(zhǎng)度,所述直邊L5的長(zhǎng)度為5.6mm;步驟四、對(duì)步驟三中所述異形復(fù)合管位于第一斜面6和第二斜面8的端部均進(jìn)行間斷焊形成焊點(diǎn)4,并對(duì)異形復(fù)合管位于所述平臺(tái)7的端部進(jìn)行滿(mǎn)焊形成厚度為1.5mm的焊縫5,然后在所述焊縫5上機(jī)加工出一個(gè)平面,機(jī)加工的深度為0.5mm;步驟五、將步驟四中機(jī)加工后的異形復(fù)合管置于彎頭成型模具的模腔內(nèi),使異形復(fù)合管的短邊位于模腔的內(nèi)彎部一側(cè),長(zhǎng)邊位于模腔的外彎部一側(cè),并使焊縫5朝上放置,對(duì)異形復(fù)合管進(jìn)行冷成型,冷成型過(guò)程中對(duì)異形復(fù)合管進(jìn)行通球整形,得到復(fù)合彎頭;步驟六、按照所要成型的薄壁彎頭尺寸對(duì)步驟五中所述復(fù)合彎頭進(jìn)行機(jī)械加工去除復(fù)合彎頭兩端多余部分,然后酸洗去除外套鋼管1和內(nèi)襯鋼管3,得到公稱(chēng)直徑為DN20mm,壁厚為0.4mm的成品彎頭。本實(shí)施例成型的成品彎頭內(nèi)外表面能夠保持原始管坯的表面粗糙度,外觀質(zhì)量好,成品率達(dá)到98%。實(shí)施例2本實(shí)施例所要成型的薄壁彎頭的材質(zhì)為純鈦,規(guī)格為DN25Ⅱ-0.8-TA190E(L),成型方法具體為:步驟一、選擇外徑為32mm,壁厚為0.8mm的TA1純鈦管并進(jìn)行切割,得到長(zhǎng)度為95mm,外徑為32mm,壁厚為0.8mm的管坯2,選擇長(zhǎng)度為95mm,外徑為35.2mm,壁厚為1.5mm的外套鋼管1,長(zhǎng)度為95mm,外徑為30mm,壁厚為1.5mm的內(nèi)襯鋼管3;所述外套鋼管1內(nèi)表面的粗糙度不大于6.3μm;所述內(nèi)襯鋼管3外表面的粗糙度不大于6.3μm;步驟二、將步驟一中所述外套鋼管1、管坯2和內(nèi)襯鋼管3按照由外至內(nèi)的順序套裝在一起,得到復(fù)合管,然后在所述復(fù)合管的兩端分別點(diǎn)焊3~4個(gè)點(diǎn)使外套鋼管1、管坯2和內(nèi)襯鋼管3三者固定在一起;步驟三、在步驟二中點(diǎn)焊后的復(fù)合管的一端進(jìn)行整體切割形成第一斜面6,在點(diǎn)焊后的復(fù)合管的另一端進(jìn)行部分切割形成平臺(tái)7和第二斜面8,得到異形復(fù)合管;如圖1所示,所述異形復(fù)合管沿復(fù)合管中軸線(xiàn)和所述平臺(tái)7的中心線(xiàn)的截面為五邊形,所述五邊形包括平行設(shè)置的左邊L1和右邊L2,用于連接左邊L1下端和右邊L2下端的第一斜邊L3,與左邊L1垂直的直邊L5,和用于連接直邊L5和右邊L2上端的第二斜邊L4,所述第一斜邊L3與左邊L1的夾角為52°,第二斜邊L4與右邊L2的延長(zhǎng)線(xiàn)的夾角為45°,所述左邊L1的長(zhǎng)度大于右邊L2的長(zhǎng)度;所述直邊L5的長(zhǎng)度為7.2mm;步驟四、對(duì)步驟三中所述異形復(fù)合管位于第一斜面6和第二斜面8的端部均進(jìn)行間斷焊形成焊點(diǎn)4,并對(duì)異形復(fù)合管位于所述平臺(tái)7的端部進(jìn)行滿(mǎn)焊形成厚度為2mm的焊縫5,然后在所述焊縫5上機(jī)加工出一個(gè)平面,機(jī)加工的深度為1mm;步驟五、將步驟四中機(jī)加工后的異形復(fù)合管置于彎頭成型模具的模腔內(nèi),使異形復(fù)合管的短邊位于模腔的內(nèi)彎部一側(cè),長(zhǎng)邊位于模腔的外彎部一側(cè),并使焊縫5朝上放置,對(duì)異形復(fù)合管進(jìn)行冷成型,得到復(fù)合彎頭;步驟六、按照所要成型的薄壁彎頭尺寸對(duì)步驟五中所述復(fù)合彎頭進(jìn)行機(jī)械加工去除復(fù)合彎頭兩端多余部分,然后酸洗去除外套鋼管1和內(nèi)襯鋼管3,得到公稱(chēng)直徑為DN25mm,壁厚為0.8mm的成品彎頭。本實(shí)施例成型的成品彎頭內(nèi)外表面能夠保持原始管坯的表面粗糙度,外觀質(zhì)量好,成品率達(dá)到98%。實(shí)施例3本實(shí)施例所要成型的薄壁彎頭的材質(zhì)為純鎳,規(guī)格為DN32Ⅱ-1-N690E(L),成型方法具體為:步驟一、選擇外徑為38mm,壁厚為1mm的純鎳管并進(jìn)行切割,得到長(zhǎng)度為105mm,外徑為38mm,壁厚為1mm的管坯2,選擇長(zhǎng)度為105mm,外徑為41.2mm,壁厚為1.2mm的外套鋼管1,長(zhǎng)度為105mm,外徑為35mm,壁厚為1mm的內(nèi)襯鋼管3;所述外套鋼管1內(nèi)表面的粗糙度不大于6.3μm;所述內(nèi)襯鋼管3外表面的粗糙度不大于6.3μm;步驟二、將步驟一中所述外套鋼管1、管坯2和內(nèi)襯鋼管3按照由外至內(nèi)的順序套裝在一起,得到復(fù)合管,然后在所述復(fù)合管的兩端分別點(diǎn)焊3~4個(gè)點(diǎn)使外套鋼管1、管坯2和內(nèi)襯鋼管3三者固定在一起;步驟三、在步驟二中點(diǎn)焊后的復(fù)合管的一端進(jìn)行整體切割形成第一斜面6,在點(diǎn)焊后的復(fù)合管的另一端進(jìn)行部分切割形成平臺(tái)7和第二斜面8,得到異形復(fù)合管;如圖1所示,所述異形復(fù)合管沿復(fù)合管中軸線(xiàn)和所述平臺(tái)7的中心線(xiàn)的截面為五邊形,所述五邊形包括平行設(shè)置的左邊L1和右邊L2,用于連接左邊L1下端和右邊L2下端的第一斜邊L3,與左邊L1垂直的直邊L5,和用于連接直邊L5和右邊L2上端的第二斜邊L4,所述第一斜邊L3與左邊L1的夾角為52°,第二斜邊L4與右邊L2的延長(zhǎng)線(xiàn)的夾角為45°,所述左邊L1的長(zhǎng)度大于右邊L2的長(zhǎng)度;所述直邊L5的長(zhǎng)度為8.4mm;步驟四、對(duì)步驟三中所述異形復(fù)合管位于第一斜面6和第二斜面8的端部均進(jìn)行間斷焊形成焊點(diǎn)4,并對(duì)異形復(fù)合管位于所述平臺(tái)7的端部進(jìn)行滿(mǎn)焊形成厚度為1.5mm的焊縫5,然后在所述焊縫5上機(jī)加工出一個(gè)平面,機(jī)加工的深度為0.6mm;步驟五、將步驟四中機(jī)加工后的異形復(fù)合管置于彎頭成型模具的模腔內(nèi),使異形復(fù)合管的短邊位于模腔的內(nèi)彎部一側(cè),長(zhǎng)邊位于模腔的外彎部一側(cè),并使焊縫5朝上放置,對(duì)異形復(fù)合管進(jìn)行冷成型,冷成型過(guò)程中對(duì)異形復(fù)合管進(jìn)行通球整形,得到復(fù)合彎頭;步驟六、按照所要成型的薄壁彎頭尺寸對(duì)步驟五中所述復(fù)合彎頭進(jìn)行機(jī)械加工去除復(fù)合彎頭兩端多余部分,然后酸洗去除外套鋼管1和內(nèi)襯鋼管3,得到公稱(chēng)直徑為DN32mm,壁厚為1mm的成品彎頭。本實(shí)施例成型的成品彎頭內(nèi)外表面能夠保持原始管坯的表面粗糙度,外觀質(zhì)量好,成品率達(dá)到98%。實(shí)施例4本實(shí)施例所要成型的薄壁彎頭的材質(zhì)為純鋯,規(guī)格為DN40Ⅱ-1.5-R6070290E(L),成型方法具體為:步驟一、選擇外徑為45mm,壁厚為1.5mm的純鋯管并進(jìn)行切割,得到長(zhǎng)度為150mm,外徑為45mm,壁厚為1.5mm的管坯2,選擇長(zhǎng)度為150mm,外徑為49mm,壁厚為1.5mm的外套鋼管1,長(zhǎng)度為150mm,外徑為41mm,壁厚為1.2mm的內(nèi)襯鋼管3;所述外套鋼管1內(nèi)表面的粗糙度不大于6.3μm;所述內(nèi)襯鋼管3外表面的粗糙度不大于6.3μm;步驟二、將步驟一中所述外套鋼管1、管坯2和內(nèi)襯鋼管3按照由外至內(nèi)的順序套裝在一起,得到復(fù)合管,然后在所述復(fù)合管的兩端分別點(diǎn)焊3~4個(gè)點(diǎn)使外套鋼管1、管坯2和內(nèi)襯鋼管3三者固定在一起;步驟三、在步驟二中點(diǎn)焊后的復(fù)合管的一端進(jìn)行整體切割形成第一斜面6,在點(diǎn)焊后的復(fù)合管的另一端進(jìn)行部分切割形成平臺(tái)7和第二斜面8,得到異形復(fù)合管;如圖1所示,所述異形復(fù)合管沿復(fù)合管中軸線(xiàn)和所述平臺(tái)7的中心線(xiàn)的截面為五邊形,所述五邊形包括平行設(shè)置的左邊L1和右邊L2,用于連接左邊L1下端和右邊L2下端的第一斜邊L3,與左邊L1垂直的直邊L5,和用于連接直邊L5和右邊L2上端的第二斜邊L4,所述第一斜邊L3與左邊L1的夾角為52°,第二斜邊L4與右邊L2的延長(zhǎng)線(xiàn)的夾角為45°,所述左邊L1的長(zhǎng)度大于右邊L2的長(zhǎng)度;所述直邊L5的長(zhǎng)度為9.8mm;步驟四、對(duì)步驟三中所述異形復(fù)合管位于第一斜面6和第二斜面8的端部均進(jìn)行間斷焊形成焊點(diǎn)4,并對(duì)異形復(fù)合管位于所述平臺(tái)7的端部進(jìn)行滿(mǎn)焊形成厚度為1.8mm的焊縫5,然后在所述焊縫5上機(jī)加工出一個(gè)平面,機(jī)加工的深度為0.8mm;步驟五、將步驟四中機(jī)加工后的異形復(fù)合管置于彎頭成型模具的模腔內(nèi),使異形復(fù)合管的短邊位于模腔的內(nèi)彎部一側(cè),長(zhǎng)邊位于模腔的外彎部一側(cè),并使焊縫5朝上放置,對(duì)異形復(fù)合管進(jìn)行冷成型,冷成型過(guò)程中對(duì)異形復(fù)合管進(jìn)行通球整形,得到復(fù)合彎頭;步驟六、按照所要成型的薄壁彎頭尺寸對(duì)步驟五中所述復(fù)合彎頭進(jìn)行機(jī)械加工去除復(fù)合彎頭兩端多余部分,然后酸洗去除外套鋼管1和內(nèi)襯鋼管3,得到公稱(chēng)直徑為DN40mm,壁厚為1.5mm的成品彎頭。本實(shí)施例成型的成品彎頭內(nèi)外表面能夠保持原始管坯的表面粗糙度,外觀質(zhì)量好,成品率達(dá)到98%。以上所述,僅是本發(fā)明的較佳實(shí)施例,并非對(duì)本發(fā)明做任何限制,凡是根據(jù)發(fā)明技術(shù)實(shí)質(zhì)對(duì)以上實(shí)施例所作的任何簡(jiǎn)單修改、變更以及等效結(jié)構(gòu)變化,均仍屬于本發(fā)明技術(shù)方案的保護(hù)范圍內(nèi)。