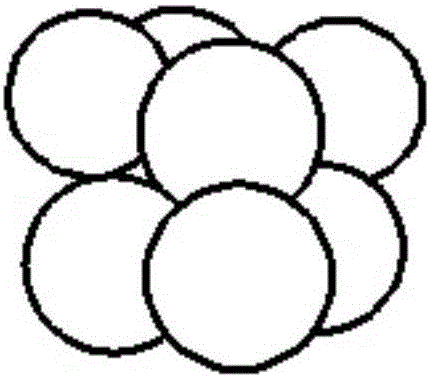
本發(fā)明涉及一種金屬3D打印球形粉末的緊密堆積的配粉方法,主要用于快速成型過程中粉末的配比,用于提高成形件的精度,降低誤差,屬于快速成型領域。
背景技術:當今的市場環(huán)境正在發(fā)生著巨大的變化,一方面表現(xiàn)為消費者需求日趨個性化和多樣化;另一方面則是產(chǎn)品制造商們都著眼于全球市場的激烈競爭。面對這樣一個迅速變化且無法預料的買方市場,制造商們不但要很快地設計出符合人們消費需求的產(chǎn)品,而且必須很快地生產(chǎn)制造出來,才能搶占市場。傳統(tǒng)的大批量生產(chǎn)模式對市場的響應遲緩,無法快速響應市場需求。為此,近十幾年來工業(yè)化國家一直在努力地研發(fā)新型的制造技術,提高制造業(yè)發(fā)展水平,以便在激烈的全球競爭中占有一席之地。得益于計算機、微電子、信息、自動化、新材料和現(xiàn)代企業(yè)管理技術的發(fā)展與進步,產(chǎn)品設計、加工制造、質量檢測、生產(chǎn)管理和企業(yè)經(jīng)營都發(fā)生了重大變革,產(chǎn)生了一批新的制造技術和制造模式,制造工程與科學取得了前所未有的發(fā)展??焖俪尚图夹g就是在這種背景下逐步形成并得以發(fā)展的??焖俪尚图夹g的發(fā)展,使得產(chǎn)品設計、制造的周期大大縮短,提高了產(chǎn)品設計、制造的一次成功率,降低產(chǎn)品開發(fā)成本,從而給制造業(yè)帶來了根本性的變化??焖俪尚图夹g(RP)是一種集成了計算機輔助設計及制造技術、逆向工程技術、分層制造技術(SFF)、材料去除成形(MPR)、材料增加成形(MAP)技術而產(chǎn)生的新型產(chǎn)品制造技術。通俗地說,快速成型技術就是利用三維CAD的數(shù)據(jù),通過快速成型機,將一層層的材料堆積成實體原型。在市場競爭日益激烈的情況下,產(chǎn)品創(chuàng)新和上市速度以及制造技術的柔性必然成為企業(yè)的核心競爭力。快速成型技術和虛擬現(xiàn)實技術一起,都是產(chǎn)品數(shù)字化開發(fā)的重要手段和有力工具,同時也已經(jīng)成為先進制造技術群不可分割的組成部分,在制造業(yè)獲得越來越廣泛的應用。與傳統(tǒng)的制造過程相比,采用激光快速成型和激光快速制模技術后,可以將產(chǎn)品試制和批量生產(chǎn)的模具準備工作并行作業(yè),明顯縮短新產(chǎn)品設計和試制周期,并節(jié)省產(chǎn)品開發(fā)費用。其中激光快速成型技術中應用比較廣泛的為選區(qū)激光熔化,選區(qū)激光熔化(SLM-SelectiveLaserMelting)是一種金屬件直接成型方法,是快速成型技術的最新發(fā)展。該技術基于快速成型的最基本思想,用逐層添加方式根據(jù)CAD數(shù)據(jù)直接成型具有特定幾何形狀的零件,成型過程中金屬粉末完全熔化,產(chǎn)生冶金結合。該技術突破了傳統(tǒng)加工方法去除成型的概念,采用添加材料的方法成型零件,最大程度的減少了材料的浪費;成型過程幾乎不受零件復雜程度的限制,因而具有很大的柔性,特別適合于單件小批量產(chǎn)品的制造。雖然快速成型技術原理上可以成型許多復雜形狀的金屬零件,但是其在實際加工過程中仍存在致密度不夠、尺寸精度低、表面質量差等問題。而上述問題產(chǎn)生的一個重要原因就是打印所用粉末存在著缺陷與不足。3D打印中,相當重要的環(huán)節(jié)就是金屬粉末的的配比問題,金屬粉末的配比問題嚴重影響3D打印成型件的收縮率、尺寸精度和形狀精度,從而影響打印精度。由于現(xiàn)今國內外還沒有一套完整的理論和數(shù)據(jù)指導金屬粉末的配比研究,一些粉末往往在鋪粉過程不能實現(xiàn)很好的致密堆積從而致使打印產(chǎn)品精度不高,性能下降。粉末的問題嚴重限制了3D打印技術的應用,因此我們發(fā)明了一種基于金屬3D打印球形粉末的緊密堆積的配粉方法從而指導配粉工作更好的進行。
技術實現(xiàn)要素:本發(fā)明的目的是指導金屬打印機所用粉末的篩分配粉工作,彌補配粉領域理論分析相關研究的不足,并有效的指導金屬3D打印機的打印工作提高實物打印的打印精度,降低誤差。本發(fā)明公布了一種基于金屬3D打印球形粉末的緊密堆積的配粉方法,其特征在于,包括以下步驟:步驟1,采用金屬晶體堆積模型中的面心立方結構得到單粒徑球的堆積模型;步驟2,以面心立方結構為基本結構在空隙中進行5種粒徑球的填充,1次球粒徑為100μm,依次填充粒徑為41.4μm的2次球,粒徑為22.5μm的3次球,粒徑為11.7μm的4次球,粒徑為11.6μm的5次球;1次球的基本結構系統(tǒng)的孔隙率為0.2594,填入2次球后系統(tǒng)孔隙率變?yōu)?.2070,繼續(xù)填入3次球后系統(tǒng)孔隙率變?yōu)?.1900,繼續(xù)填入4次球后孔隙率變?yōu)?.1580,繼續(xù)填入5次球后孔隙率變?yōu)?.1490;各次球的個數(shù)之比為1:1:2:8:8;步驟3,以步驟2中填充好的5種粒徑球的結構為基本結構利用matlab進行多個基本結構的計算;具體方式為,選擇第一個5種粒徑球填充的結構,即1次球100μm,2次球41.4μm,3次球22.5μm,4次球11.7μm,5次球11.6μm;由于3D打印金屬粉末粒徑處于1μm-100μm之間,且精度在1μm范圍;然后以1次球1μm之差選擇第二個5種粒徑球的填充結構,即為1次球99μm,2次球40.986μm,3次球22.275μm,4次球11.583μm,5次球11.484μm;然后繼續(xù)以1次球1μm之差選擇第三個5粒徑填充的結構直到最后一個填充結構的1次球粒徑為1μm則結束;為了得到更加精確的數(shù)值,球粒徑的數(shù)值在計算過程中保留三位有效數(shù)字,最后得到的數(shù)值由matlab中的fix函數(shù)截尾取整;步驟4,由于粉末冶金中氣霧化金屬粉末的粒徑是以一個類高斯分布形式存在的,因此,在matlab中定義從1次球粒徑為1μm到一次球粒徑為100μm的5粒徑填充結構的1次球個數(shù)遵循一個高斯分布,該高斯分布由公式確定,其中X表示粒徑的數(shù)值,Y表示對應粒徑的個數(shù);步驟5,通過步驟4后在matlab中已確定了粒徑從1μm到100μm的各個球的個數(shù)和體積,在matlab中利用作圖命令,做出該粒徑范圍的頻度分布曲線,以及累計體積分布曲線;根據(jù)得到的分布曲線得到各個粒徑范圍的顆粒的體積分數(shù),從而得到配粉數(shù)據(jù)表格。具體細節(jié)如下:在步驟1中單粒徑理想球的堆積模型分為立方體排列、正斜方體排列1、面心立方排列/菱面體排列、正斜方體排列2、菱形四面體排列、菱面體堆積/六方最密堆積等六種。計算得到的六種排列方式的孔隙率分別為,一、正方系:立方堆積0.4764、正斜方體堆積0.3954、面心立方排列/菱面體排列0.2594。二、斜方系:正斜方體堆積0.3954、契行四面體堆積0.6981、菱面體堆積/六方最密堆積0.2594。最終得出結論:對于單粒徑的球形顆粒堆積,處于面心立方或六方最密堆積時可獲得最大的堆積密度。在步驟2中,由于要選擇更小的球填入到基本排列模型中去,而面心立方方中存在規(guī)則和易計算的正四面體間隙和正八面體間隙因此選擇的模型是六種空間堆積中的面心立方密堆模型。面心立方密堆的模型中存在八面體間隙和四面體間隙。所以可以計算其中可以填充的最大的球的半徑。根據(jù)Horsfieled填充理論,設基本的均一球體為1次球,其半徑為r1;填入四角孔的最大球體為2次球,其半徑為r2;填入三角孔的最大球體為3次球,其半徑為r3;其后再填入更小的4次球,其半徑為r4;5次球,其半徑為r5。經(jīng)過計算母球,八面體間隙、四面體間隙以及更小的孔可以填充的球的半徑之比為:r2=0.414r1,r3=0.225r1,r4=0.117r1,r5=0.116r1。在填入多次球之后得到的模型的孔隙率分別為:一次球0.2594,二次球0.2070,三次球0.1900,四次球0.1580,五次球0.1490。在步驟3中,利用matlab編程時是以一個多粒徑堆積的最密堆積模型為基礎的,選擇一個確定大小的模型作為第一個模型,然后選擇第二個模型,第二個模型的最大顆粒與第一個模型的最大顆粒相差1μm,然后依次相差1μm選出第三個,第四個等等無數(shù)個模型。最后利用matlab里的循環(huán)語句,依次計算各個粒徑的球形顆粒的具體個數(shù)以及所占體積,得到近似下的連續(xù)粒徑分布的頻度分布曲線。在得到了連續(xù)的頻度分布曲線之后發(fā)現(xiàn),連續(xù)粒徑分布的球體中大球所占體積最大,且隨著粒徑的減小,所占體積迅速降低。雖然這是理論上最密的堆積模型但是考慮到實際氣霧化制粉的工藝中得到的原始粉末都遵循高斯分布的規(guī)律,因此考慮的粉末的利用率和金屬3D打印機鋪粉的工藝過程對此連續(xù)粒徑的頻度曲線進行了適當?shù)恼{整。并最終得到的曲線既符合最密堆積的模型規(guī)律又基本遵循了高斯分布的規(guī)律。本發(fā)明的優(yōu)點和意義是:1、相比先前研究者的關于連續(xù)粒徑的堆積模型,本模型具有確切的計算數(shù)據(jù)支持并非只是經(jīng)驗的選取粒徑之比,且利用的是matlab循環(huán)計算,比只是公式推導圖像擬合等方法,更準確。2、運用此種堆積模型能夠得到的粉末的孔隙率理論上可以達到0.149,這要比市面上目前所用金屬粉末的松裝密度的0.4左右小很多,極大的提高了粉末的松裝密度。3、擴大3D打印技術在某些因打印精度而受到限制的領域,使3D打印技術得到更廣泛的應用。附圖說明圖1為本發(fā)明一種基于金屬3D打印球形粉末的理想最密堆積模型的建立方法的流程圖。圖2A-2F為單粒徑堆積的六種堆積模型示意圖。圖2A為立方堆積,圖2B為正斜方體堆積,圖2C為面心立方堆積,圖2D為正斜方體堆積,圖2E為楔形四面體堆積,圖2F為六方堆積。圖3為面心立方堆積空隙中的四面體間隙示意圖圖4為面心立方堆積空隙中正八面體間隙示意圖圖5A為面心立方堆積中的四角孔示意圖圖5B為2次球填入四角孔中的示意圖圖6A為面心立方堆積中的三角孔示意圖圖6B為3次球填入三角孔中的示意圖圖7A為2次球與一次球形成的四面體間隙示意圖圖7B為4次球填入圖7A中的間隙示意圖圖8為5次球填入3次球與4次球之間的示意圖圖9A為金屬粉末的粒徑頻度分布曲線圖9B為金屬粉末的體積累計分布曲線圖10A德國進口金屬粉末的測定得到的頻度分布曲線圖10B德國進口金屬粉末的測定得到的體積累計分布曲線具體實施方式為使本發(fā)明方法和優(yōu)點、特征更明顯易懂下文特舉出較佳實例并配合所附圖例進行詳細說明如下:在步驟1中由附圖1可以得到最大堆積密度的堆積方式為面心立方堆積和六方最密堆積,兩種堆積方式的孔隙率都為0.2594。在步驟2中選擇的基本填充模式是面心立方堆積模型。因為考慮到面心立方堆積模型的晶胞結構較簡單且每個晶胞中均勻的分布著四面體間隙和八面體間隙,一次球與八面體間隙與四面體間隙與4次球與5次球的相對個數(shù)之比為:1:1:2:8:8。1次球2次球3次球4次球5次球的粒徑之比為1:0.414:0.225:0.117:0.116.在步驟3中利用matlab編程的思想是:以一個多粒徑堆積的最密堆積模型為基礎,選擇一個確定大小的模型作為第一個模型,然后選擇第二個模型,第二個模型的最大顆粒與第一個模型的最大顆粒相差1μm,然后依次相差1μm選出第三個,第四個等等無數(shù)個模型。最后利用matlab里的循環(huán)語句,依次計算各個粒徑的球形顆粒的具體個數(shù)以及所占體積,得到近似下的連續(xù)粒徑分布的頻度分布曲線。具體我們以不銹鋼粉末為例:選取的不銹鋼粉末的粒徑分布為1μm—100μm,考慮到氣霧化制粉過程中得到的粉末基本遵循高斯曲線且金屬3D打印所需粉末粒徑相對較小,因此進行了方案的設計。在方案中,把程序之初各個粒徑的粉末的1次球的個數(shù)給定一個近似符合高斯曲線的初值,即選擇的一次球的個數(shù)遵循公式:其中y表示一次球的個數(shù),x表示粒徑的數(shù)值。然后進行計算得到了顆粒的頻度分布曲線和體積累計分布曲線,如圖9A和圖9B所示。將圖9A、9B分別與10A實際測試金屬3D打印所用金屬粉末的頻度分布曲線、10B實際測試金屬3D打印所用金屬粉末的體積累計分布曲線相比較,發(fā)現(xiàn)其基本規(guī)律相同。根據(jù)圖9B所得的體積累計分布曲線可得1—100μm的不銹鋼的配粉數(shù)據(jù)如下:得到上表所示的數(shù)據(jù)以后,可以根據(jù)此數(shù)據(jù)進行篩分配粉。本發(fā)明得到了一種適用于金屬3D打印球形粉末的緊密堆積的配粉方法,此種方法得到的粉末不僅符合最密度堆積的模型而且總體數(shù)據(jù)基本符合高斯分布,與實際所用粉末的粒度分布數(shù)據(jù)也基本接近。因此可以作為以后進行金屬粉末配粉工作的理論依據(jù)。相比先前研究者的關于連續(xù)粒徑的堆積模型,本方法中的模型具有確切的計算數(shù)據(jù)支持并非只是經(jīng)驗的選取粒徑之比,且利用的是matlab循環(huán)計算,比只是公式推導圖像擬合等方法,更準確。運用此種堆積模型能夠得到的粉末的孔隙率理論上可以達到0.149,這要比市面上目前所用金屬粉末的松裝密度的0.4左右小很多,極大的提高了粉末的松裝密度。提高了鋪粉致密度之后將會減小3D打印實物模型的收縮比,提高打印的尺寸精度和形狀精度,從而使得成型件的精度,密度和質量都達到最佳。同時擴大3D打印技術在某些因打印精度而受到限制的領域,使3D打印技術得到更廣泛的應用。