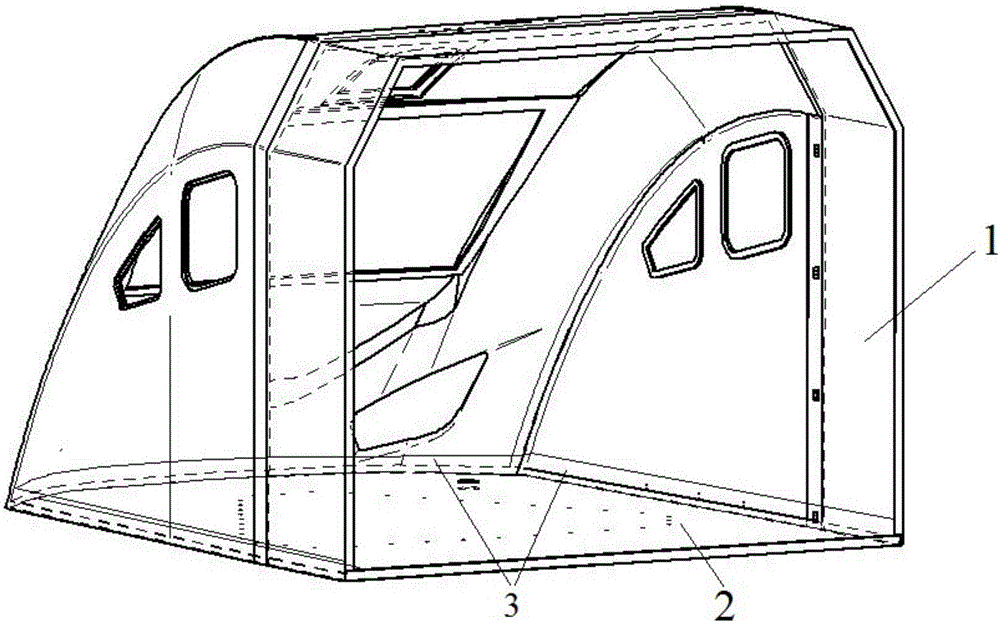
本實用新型涉及高速軌道交通設備,特別的,涉及一種纖維增強泡沫夾芯結構復合材料機車駕駛艙。
背景技術:
:在高速軌道交通領域,復合材料正成為越來越重要的一類材料,除用作內部設備和裝飾材料外,在承重結構上的應用也越來越廣泛,用復合材料做成的構件,重量輕、強度高、剛性大,是一種理想的結構件。復合材料產品制造多數是成型件,制造出的產品,不需進行機械加工,生產效率高,制造成本低。復合材料在軌道交通車輛中廣泛應用,對減輕車廂重量,降低噪聲、振動,提高安全性、舒適性,減少維修等均有重要作用。目前,機車駕駛艙的艙體結構均為金屬制造,這種結構的缺點是:重量過重、易受環(huán)境影響而腐蝕、成形過程中受焊接影響易導致變形。而復合材料的機車駕駛艙艙體結構尚未見報道。復合材料已逐漸成為鐵路車輛的主要用材,并且隨著客貨運列車向高速化、重載化、舒適化、安全化方向的發(fā)展而起著越來越重要的作用,在機車車輛不同結構區(qū)域用復合材料替代原有金屬結構是一個不斷探索的過程。中國專利201510579742.9公開了一種碳纖維復合材料車體,該方案也只是提到將碳纖維復合材料用于車體,其碳纖維復合材料中碳纖維具體如何分布以及能達到什么技術性能要求均未提及,且機車兩端的駕駛艙比機車中間的車廂在防火、隔熱、隔音、及抗高速沖擊方面的要求均要高,因此,需要一種專門針對機車駕駛艙的方案來解決這個問題,在減輕車體重量、降低成本的同時,又能滿足機車駕駛艙的各項性能要求。技術實現要素:本實用新型目的在于提供一種纖維增強泡沫夾芯結構復合材料機車駕駛艙,以解決
背景技術:
中提出的問題。為實現上述目的,本實用新型提供了一種纖維增強泡沫夾芯結構復合材料機車駕駛艙,包括前頂1與底板2,底板通過補強層3粘接在前頂的底部,粘接成一體的前頂與底板構成駕駛艙艙體,所述前頂與底板均包括上蒙皮4、下蒙皮5及泡沫芯材6,所述上蒙皮、下蒙皮及補強層均采用纖維增強復合材料,上蒙皮、下蒙皮及補強層中的樹脂均為阻燃環(huán)氧樹脂,上蒙皮、下蒙皮及補強層中的增強織物均為鋪疊在一起的多層,前頂及底板中的增強織物均采用碳纖維織物、玻璃纖維織物及碳纖維-玻璃纖維混編織物中的一種或幾種,且前頂與底板中上蒙皮與下蒙皮厚度均在3mm~8mm之間。進一步的,所述上蒙皮及下蒙皮中的增強織物的鋪疊層數等于8~12層,補強層中的增強織物為鋪疊層數不少于6層的多軸碳纖維織物,且上蒙皮、下蒙皮及補強層中的織物面密度均在350g/㎡~650g/㎡之間。進一步的,所述上蒙皮、下蒙皮及補強層中的織物均由面密度為400g/㎡、方向為(0°,90°)以及面密度為600g/㎡、方向為(+45°,-45°)的兩種多軸織物交替鋪疊構成,上蒙皮中各層織物的鋪層依次為(0°,90°)/(+45°,-45°)/(0°,90°)/(+45°,-45°)/(0°,90°)/(+45°,-45°)/(0°,90°)/(+45°,-45°)/(0°,90°)/(+45°,-45°);下蒙皮中各層織物的鋪層依次為(+45°,-45°)/(0°,90°)/(+45°,-45°)/(0°,90°)/(+45°,-45°)/(0°,90°)/(+45°,-45°)/(0°,90°)/(+45°,-45°)/(0°,90°)。所述泡沫芯材采用PET泡沫、酚醛泡沫、PMI泡沫、PVC泡沫中的任意一種。進一步的,所述前頂底部邊緣設有與底板邊緣配合的橫截面呈L形的卡接邊11,L形卡接邊為前頂與底板的粘接處,且整個底板被包圍在前頂的殼體內,補強層貼粘在駕駛艙內前頂與底板接合的縫隙處并將縫隙覆蓋,補強層上部與前頂下蒙皮貼粘,補強層的下部與底板上蒙皮貼粘。進一步的,所述前頂的上蒙皮最外層的增強織物設置或替換為斜紋碳纖維織物。所述前頂及底板分別為通過模具一體成型的結構,且前頂上開設有沿厚度方向貫穿上蒙皮、泡沫芯材及下蒙皮的窗孔與燈孔,窗孔與燈孔內裝設有便于安裝窗框與燈框的飛邊。用于制作前頂與底板的模具在鋪設上蒙皮或下蒙皮前涂覆有透明膠衣,透明膠衣固化后的厚度不超過0.6mm。優(yōu)選的,所述透明膠衣固化后的厚度為0.25mm~0.6mm。所述底板上設有用于與外部裝置固連的金屬預埋件7,金屬預埋件一端預埋在底板下蒙皮與泡沫芯材之間,另一端穿過底板下蒙皮伸至底板外。根據所述纖維增強泡沫夾芯結構復合材料機車駕駛艙,本實用新型還提供了一種纖維增強泡沫夾芯結構復合材料機車駕駛艙的制備方法,包括以下步驟:1)機車駕駛艙前頂制備1-a.前頂模具準備;將模具表面清潔干凈,然后在模具表面擦拭脫模劑,晾干備用;1-b.刷涂膠衣;將調配好的透明膠衣均勻的刷涂在模具上,膠衣固化后的厚度≤0.6mm;1-c.鋪層與配膠;膠衣固化后,按照上蒙皮/泡沫芯材/下蒙皮的順序鋪放原材料,調配阻燃環(huán)氧樹脂膠;1-d.成型;采用VARI(真空輔助成型)工藝注膠整體成型;1-e.固化和脫模;駕駛艙前頂蒙皮凝膠后,拆卸前頂模具,將機車駕駛艙前頂取出。2)機車駕駛艙底板制備2-a.底板模具準備;將模具表面清潔干凈,然后在模具表面擦拭脫模劑,晾干備用;2-b.刷涂膠衣;將調配好的透明膠衣均勻的刷涂在模具上,膠衣固化后的厚度≤0.6mm;2-c.鋪層與配膠;膠衣固化后,按照下蒙皮/泡沫芯材/上蒙皮的順序鋪放原材料,調配阻燃環(huán)氧樹脂膠;2-d.成型;采用VARI(真空輔助成型)工藝注膠整體成型;2-e.固化和脫模;駕駛艙底板蒙皮凝膠后,拆卸底板模具,將機車駕駛艙底板取出。3)前頂與底板粘結與補強3-a.前頂與底板的粘接先將駕駛艙前頂與底板分別放置在前頂模具與底板模具內,然后在前頂與底板的接合處(即底板邊緣與前頂L形卡接邊處)分別刷涂膩子,一方面對駕駛艙的前頂和底板起初步粘結作用,另一方面將前頂與底板之間的縫隙填充,再將底板模具和前頂模具固定在一起,將前頂和底板接縫處擠出的膩子清理干凈。3-b.前頂與底板的補強膩子固化后,在補強區(qū)域手糊6層以上增強織物,用真空袋壓成型。4)機車駕駛艙艙體的后固化前頂與底板的補強層凝膠后,將整個艙體和模具置入烘箱,開始加熱升溫,保持80℃恒溫5個小時,停止加熱,模具溫度降到50℃時,可以拆模,將機車駕駛艙艙體取出。所述機車駕駛艙的制備方法中,步驟1與步驟2的工藝過程可分別同時進行。步驟1與步驟2中所用的阻燃環(huán)氧樹脂的粘度為100~300mPa﹒s步驟3中的膩子可采用與步驟1與步驟2相同的阻燃環(huán)氧樹脂再加填料調配制成。有益效果:本實用新型提出一種纖維增強泡沫芯材結構復合材料機車駕駛艙及其制備方法,機車駕駛艙艙體采用了纖維增強泡沫芯材結構,相對于金屬結構的機車駕駛艙艙體,具有顯著減重效果(減重量達60%),可有效節(jié)省能源,對于纖維增強復合材料在機車駕駛艙上的應用有著極其重要的意義,具有很大的發(fā)展空間和廣闊的市場應用前景;使用復合材料制備機車駕駛艙艙體,對于提高復合材料在鐵路車輛上的應用水平,促進鐵路事業(yè)的持續(xù)發(fā)展也有著重要意義。本實用新型的機車駕駛艙制備方法使用真空輔助成型(VARI)工藝制備駕駛艙艙體,成本低,易于整體化成型,簡化了繁瑣的零部件裝配過程。除了上面所描述的目的、特征和優(yōu)點之外,本實用新型還有其它的目的、特征和優(yōu)點。下面將參照圖,對本實用新型作進一步詳細的說明。附圖說明構成本申請的一部分的附圖用來提供對本實用新型的進一步理解,本實用新型的示意性實施例及其說明用于解釋本實用新型,并不構成對本實用新型的不當限定。在附圖中:圖1是本實用新型優(yōu)選實施例的機車駕駛艙立體結構圖;圖2是本實用新型優(yōu)選實施例的機車駕駛艙仰視圖;圖3是本實用新型優(yōu)選實施例的前頂仰視圖;圖4是本實用新型圖3中的I處局部放大視圖;圖5是本實用新型優(yōu)選實施例的底板剖面圖;圖6是本實用新型優(yōu)選實施例的前頂剖面圖;圖7是本實用新型優(yōu)選實施例的窗孔及燈孔示意圖;圖8是本實用新型圖7中的B-B剖視圖。圖中:1-前頂,11-卡接邊,12-窗孔,13-燈孔,14-飛邊,2-底板,3-補強層,4-上蒙皮,5-下蒙皮,6-泡沫芯材,7-金屬預埋件。具體實施方式以下接合附圖對本實用新型的實施例進行詳細說明,但是本實用新型可以根據權利要求限定和覆蓋的多種不同方式實施。參見圖1~圖6的一種纖維增強泡沫夾芯結構復合材料機車駕駛艙,包括分別前頂1與底板2,底板2通過補強層3粘接在前頂1的底部,粘接成一體的前頂1與底板2構成駕駛艙艙體,前頂與底板均包括上蒙皮4、下蒙皮5及泡沫芯材6,上蒙皮、下蒙皮及補強層均采用纖維增強復合材料,上蒙皮、下蒙皮及補強層中的樹脂均為阻燃環(huán)氧樹脂,上蒙皮、下蒙皮及補強層中的增強織物均為鋪疊在一起的10層,前頂中的增強織物采用多軸碳纖維織物、多軸玻璃纖維織物及碳纖維-玻璃纖維混編織物中的一種或幾種,底板中的增強織物采用碳纖維織物、玻璃纖維織物及碳纖維-玻璃纖維混編織物中的一種或幾種,且前頂與底板中上蒙皮與下蒙皮厚度均在3mm~8mm之間。下面通過實施例1~實施例3及對比例1、對比例2來闡述本實用新型的技術效果:實施例1~實施例3中,前頂1底部邊緣設有與底板邊緣配合的橫截面呈L形的卡接邊11,L形卡接邊位置處為前頂與底板的粘接處,且整個底板2被包圍在前頂1的殼體內,補強層3貼粘在駕駛艙內前頂與底板接合的縫隙處并將縫隙覆蓋,補強層上部與前頂下蒙皮貼粘,補強層的下部與底板上蒙皮貼粘,且實施例1~實施例3中,補強層呈折彎式結構,補強層的折彎角等于補強位置處前頂與底板之間的夾角。實施例1~實施例3中,前頂的上蒙皮及下蒙皮均采用多軸織物時,上蒙皮中各層織物的鋪層依次為(0°,90°)/(+45°,-45°)/(0°,90°)/(+45°,-45°)/(0°,90°)/(+45°,-45°)/(0°,90°)/(+45°,-45°)/(0°,90°)/(+45°,-45°);下蒙皮中各層織物的鋪層依次為(+45°,-45°)/(0°,90°)/(+45°,-45°)/(0°,90°)/(+45°,-45°)/(0°,90°)/(+45°,-45°)/(0°,90°)/(+45°,-45°)/(0°,90°)。實施例1~實施例3中,前頂上蒙皮中最外一層織物(即第一層織物)均用斜紋碳纖維織物代替。實施例1~實施例3中,前頂及底板中各層織物的面密度均在350g/㎡~650g/㎡之間。實施例1~實施例3中,補強層為6層多軸碳纖維織物,補強層中的織物均由面密度為400g/㎡、方向為(0°,90°)以及面密度為600g/㎡、方向為(+45°,-45°)的兩種多軸織物交替鋪疊構成,補強層中各層織物的鋪層依次為(0°,90°)/(+45°,-45°)/(0°,90°)/(+45°,-45°)/(0°,90°)/(+45°,-45°),參見圖1,補強層貼粘在駕駛艙內前頂與底板接合的縫隙處并將全部縫隙覆蓋,參見圖4,補強層上部與前頂下蒙皮貼粘,補強層的下部與底板上蒙皮貼粘,補強層的總寬度為200~300mm,折彎后上部與下部各占一半寬度并分別與前頂及底板貼粘在一起。參見圖7與圖8,前頂上開設有沿厚度方向貫穿上蒙皮、泡沫芯材及下蒙皮的窗孔12與燈孔13,窗孔與燈孔內裝設有便于安裝窗框與燈框的飛邊14,本實施例中,飛邊呈法蘭邊結構并向駕駛艙內凸起,同時駕駛艙外側(即上蒙皮一側)內凹,以方便安裝窗框與燈框,飛邊用于擋住窗框與燈框并對窗框與燈框起支撐定位作用。實施例1:上蒙皮與下蒙皮的厚度為3mm。纖維增強泡沫夾芯結構復合材料機車駕駛艙實施例1的制備方法:1)機車駕駛艙艙體前頂制備將前頂模具表面清潔干凈,然后在駕駛艙前頂模具表面擦拭3遍脫模劑,晾干之后,將調配好的透明膠衣均勻的刷涂在前頂模具上,控制膠衣厚度在0.4mm左右,膠衣凝膠固化后,先鋪設一層斜紋碳纖維織物,然后依次鋪放9層多軸碳纖維織物/PET泡沫/10層多軸碳纖維織物,調配阻燃環(huán)氧樹脂,通過VARI工藝注膠,室溫固化24小時后,拆卸前頂模具,將機車駕駛艙的前頂取出。2)機車駕駛艙艙體底板制備將底板模具表面清潔干凈,然后在底板模具表面擦拭3遍脫模劑,晾干之后,將調配好的透明膠衣均勻的刷涂在底板模具上,控制膠衣厚度在0.4mm左右,膠衣凝膠后,依次鋪放10層碳纖維織物/金屬預埋件/PET泡沫/10層碳纖維織物,調配阻燃環(huán)氧樹脂,通過VARI工藝注膠,室溫固化24小時后,拆卸底板模具,將機車駕駛艙的底板取出。3)駕駛艙艙體前頂與底板粘結與補強先分別將駕駛艙前頂與底板放置到前頂模具與底板模具內,然后在前頂與底板的接合處分別刷涂膩子,再將底板模具和前頂模具固定在一起,將前頂和底板接縫處擠出的膩子清理干凈,膩子固化后,手糊6層多軸碳纖維織物,用真空袋壓工藝成型。4)機車駕駛艙艙體的后固化前頂與底板的補強層凝膠后,將整個艙體和兩個模具的接合體置入烘箱,開始加熱升溫,保持80℃恒溫5個小時,停止加熱,模具溫度降到50℃時,開始拆模,將機車駕駛艙艙體取出。實施例2:上蒙皮與下蒙皮的厚度為6mm。纖維增強泡沫夾芯結構復合材料機車駕駛艙實施例2的制備方法:1)機車駕駛艙艙體前頂制備將前頂模具表面清潔干凈,然后在前頂模具表面擦拭3遍脫模劑,晾干之后,將調配好的透明膠衣均勻的刷涂在模具上,控制膠衣厚度在0.4mm左右,膠衣凝膠固化后,先鋪設一層斜紋碳纖維織物,然后依次鋪放9層多軸玻璃纖維織物/酚醛泡沫/10層多軸玻璃纖維織物,調配阻燃環(huán)氧樹脂,通過VARI工藝注膠,室溫固化24小時后,拆卸模具,將機車駕駛艙的前頂取出。2)機車駕駛艙艙體底板制備將底板模具表面清潔干凈,然后在底板模具表面擦拭3遍脫模劑,晾干之后,將調配好的透明膠衣均勻的刷涂在模具上,控制膠衣厚度在0.3mm左右,膠衣凝膠固化后,依次鋪放10層玻璃纖維織物/金屬預埋件/酚醛泡沫/10層玻璃纖維織物,調配阻燃環(huán)氧樹脂,通過VARI工藝注膠,室溫固化24小時后,拆卸底板模具,將機車駕駛艙的底板取出。3)駕駛艙艙體前頂與底板粘結與補強先分別將駕駛艙前頂與底板放置到前頂模具與底板模具內,然后在前頂與底板的接合處分別刷涂膩子,再將底板模具和前頂模具固定在一起,將前頂和底板接縫處擠出的膩子清理干凈,膩子固化后,手糊6層多軸玻璃纖維織物,用真空袋壓工藝成型。4)機車駕駛艙艙體的后固化前頂與底板的補強層凝膠后,將整個艙體和兩個模具的接合體置入烘箱,開始加熱升溫,保持80℃恒溫5個小時,停止加熱,模具溫度降到50℃時,開始拆模,將機車駕駛艙艙體取出。實施例3:上蒙皮與下蒙皮的厚度為8mm。纖維增強泡沫夾芯結構復合材料機車駕駛艙的制備方法實施例3:1)機車駕駛艙艙體前頂制備將前頂模具表面清潔干凈,然后在前頂模具表面擦拭3遍脫模劑,晾干之后,將調配好的透明膠衣均勻的刷涂在前頂模具上,控制膠衣厚度在0.5mm左右,膠衣凝膠固化后,先鋪設一層斜紋碳纖維織物,然后依次鋪放9層碳纖維-玻璃纖維混編織物/PMI泡沫/10層碳纖維-玻璃纖維混編織物,調配阻燃環(huán)氧樹脂,通過VARI工藝注膠,室溫固化24小時后,拆卸前頂模具,將機車駕駛艙的前頂取出。2)機車駕駛艙艙體底板制備將底板模具表面清潔干凈,然后在底板模具表面擦拭3遍脫模劑,晾干之后,將調配好的透明膠衣均勻的刷涂在底板模具上,控制膠衣厚度在0.4mm左右,膠衣凝膠固化后,依次鋪放10層碳纖維-玻璃纖維混編織物/金屬預埋件/PMI泡沫/10層碳纖維-玻璃纖維混編織物,調配阻燃環(huán)氧樹脂,通過VARI工藝注膠,室溫固化24小時后,拆卸模具,將機車駕駛艙的底板取出。3)駕駛艙艙體前頂與底板粘結與補強先分別將駕駛艙前頂與底板放置到前頂模具與底板模具內,然后在前頂與底板的接合處分別刷涂膩子,再將底板模具和前頂模具固定在一起,將前頂和底板接縫處擠出的膩子清理干凈。膩子固化后,手糊6層碳纖維織物,用真空袋壓工藝成型。4)機車駕駛艙艙體的后固化前頂與底板的補強層凝膠后,將整個艙體和兩個模具的結合體置入烘箱,開始加熱升溫,保持80℃恒溫5個小時,停止加熱,模具溫度降到50℃時,開始拆模,將機車駕駛艙艙體取出。實施例1~實施例3中采用的阻燃環(huán)氧樹脂的粘度均為300mPa·s。對比例1對比例1中上蒙皮與下蒙皮的厚度為2.5mm,其余各條件與參數與實施例1相同。對比例2對比例2中上蒙皮與下蒙皮的厚度為8.5mm;其余各條件與參數與實施例2相同。分別對實施例1~實施例3及對比例1、對比例2先后進行稱重測試、隔音測試、以及用重量為1kg、速度為320km/h的鋁塊對駕駛艙進行高速沖擊,再進行點燃測試,得到各實施例與對比例的效果對比如表一。表一減重量隔聲量抗高速沖擊性能上下蒙皮厚度實施例163%38dB未穿透3mm實施例260.5%42dB未穿透6mm實施例358%45dB未穿透8mm對比例164%36dB穿透2.5mm對比例257%46dB未穿透8.5mm本實用新型的實施例1~實施例3及對比例1、對比例2中機車復合材料駕駛艙的尺寸為:長3960mm、寬3098mm、高2510mm,實施例1~實施例3所制試件各附件裝配完后整體的重量均為2500~2600kg,相對現有的金屬駕駛艙重量約減輕60%,且采用本實用新型的纖維增強泡沫夾芯結構復合材料機車駕駛艙經實驗檢測后,阻燃等級符合DIN5510-2:2009防火等級S3等級要求,隔熱性能、隔聲性能符合TB/T3107-2011《鐵道客車單元式組合車窗》標準要求,抗高速沖擊性能符合UICCODE651-2002《軌道車輛司機室》標準要求。以上所述僅為本實用新型的優(yōu)選實施例而已,并不用于限制本實用新型,對于本領域的技術人員來說,本實用新型可以有各種更改和變化。凡在本實用新型的精神和原則之內,所作的任何修改、等同替換、改進等,均應包含在本實用新型的保護范圍之內。當前第1頁1 2 3